Search results for: user
Category
Announcements
CMMS
Compliance & Control
Enterprise Asset Management
Facility Management
Fleet
Operations & Maintenance
Product Updates
Uncategorized
CMMS
The Importance of User-Friendly CMMS Interface
Introduction CMMS is a powerful software solution that simplifies and improves the management of maintenance tasks, equipment, and facilities. It enables companies to transition from traditional paper-based systems to a digital platform that provides comprehensive control, tracking, and optimization of maintenance operations. While a CMMS system is an extremely powerful maintenance management tool, its effectiveness […]
Make your work easier.
Try for free.
Book a demo
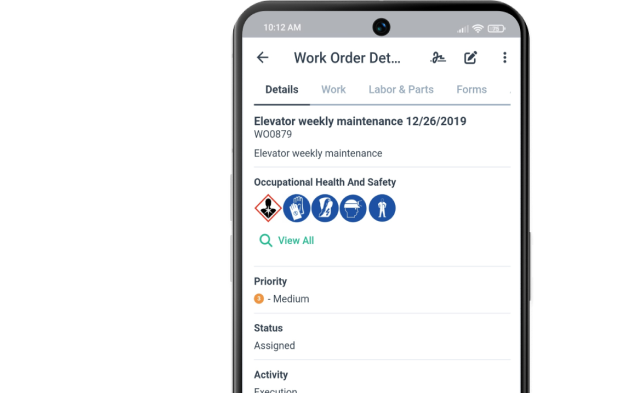