Get a Free WorkTrek Demo
Let's show you how WorkTrek can help you optimize your maintenance operation.
Try for freeKey Takeaways:
- Root cause analysis turns reactive maintenance into proactive maintenance.
- Many companies experience data collection challenges.
- CMMS automates asset management and organizes asset data in one place.
- Digital checklists save time and increase technicians’ efficiency.
Costly downtime, premature equipment replacements, and lost profits are too familiar outcomes of poor asset maintenance.
But there’s another hidden cost—constant pressure on your team to keep things running.
To avoid this and ensure your assets work as hard as possible, efficient maintenance is the key.
In this article, we’ll explore five best practices for keeping your assets in peak condition while streamlining your maintenance efforts.
Let’s get started.
Collect As Much Data as Possible
Efficient asset maintenance begins with good data.
The more detailed and accurate asset data you collect, the better your maintenance strategy will be.
Asset data includes everything from basic information like the make, model, and serial number to detailed maintenance history, usage patterns, and real-time sensor data.
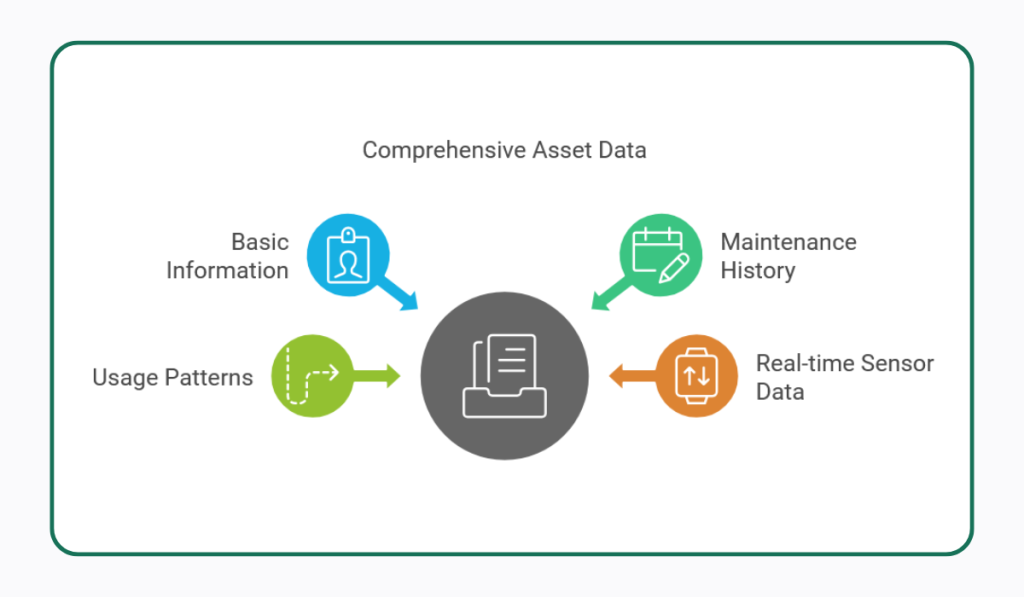
However, the real power of this data is in what it allows you to do.
For example, a detailed maintenance history for each asset lets you quickly identify recurring issues and estimate how frequently each asset requires attention.
If a specific pump fails every six months, you can schedule maintenance before another breakdown.
This way, you can achieve three key things:
- plan your workload more effectively,
- allocate resources properly, and
- avoid unexpected downtime.
Detailed data shows you exactly what’s needed for each maintenance task.
If you know the time it takes to replace a part, the materials required, the tools needed, and even the technician’s PPE, you can plan maintenance tasks down to the smallest detail.
This detailed planning reduces errors, minimizes downtime, and ensures technicians have the necessary tools and parts when needed.
Data isn’t just useful for scheduling maintenance, though. It is also important for managing costs.
For instance, if you track labor and parts expenses over time through reports like the one below, you can clearly understand your maintenance costs and make better budgeting decisions.
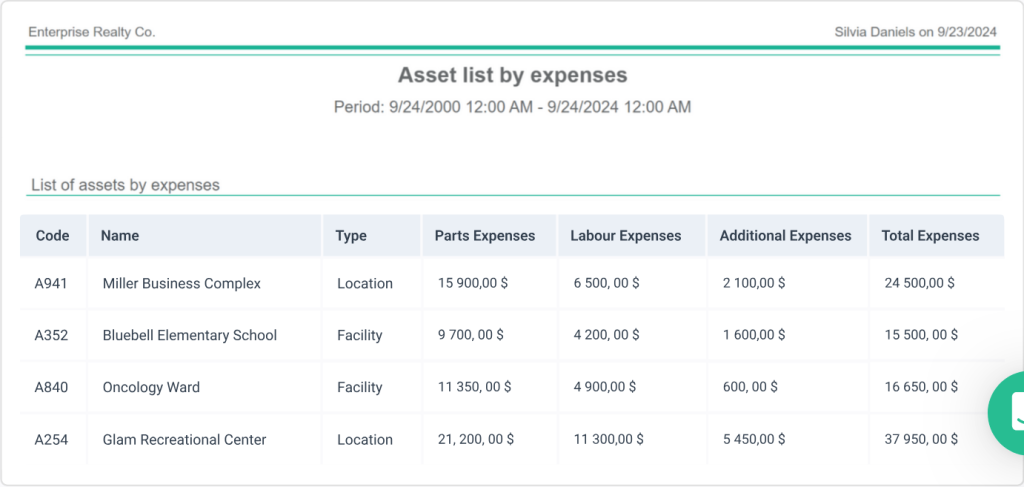
If a particular asset demands frequent repairs and incurs high labor and spare parts costs, you can present this data to management to justify replacing it.
Moreover, knowing the expenses associated with planned and unplanned downtime allows you to learn which assets need attention first.
However, managing all this asset data seems challenging for many companies.
Many maintenance teams need help with data accuracy, analysis time, and knowing what actions to take based on the information they have.
A recent study by Augury confirms this, revealing that 39% of organizations cite data accuracy as a major obstacle, and 36% say the time it takes to analyze data is a barrier.
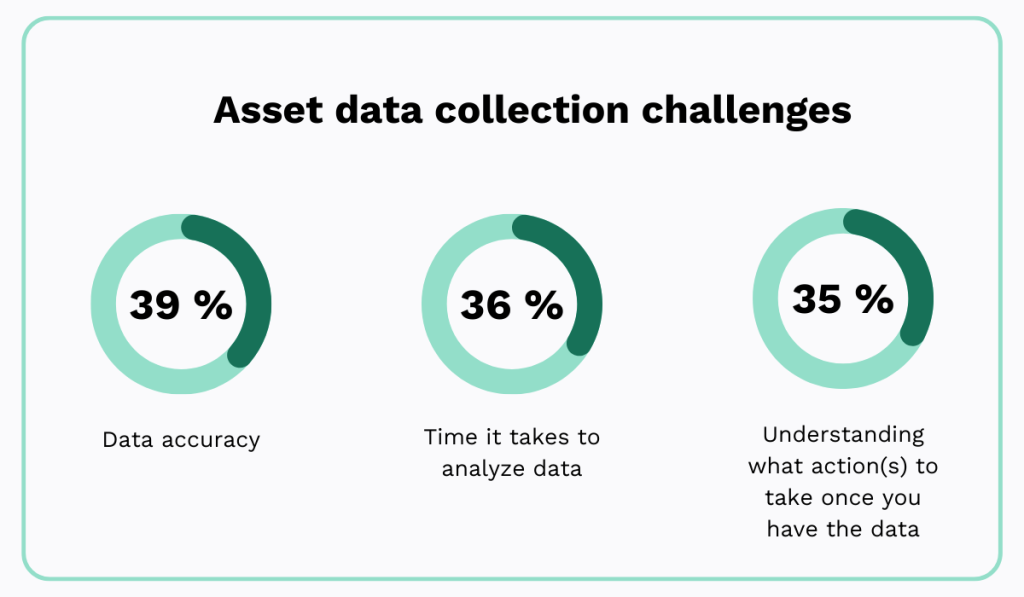
If you struggle with the same, adopting specialized software is best.
But—more on that later.
Conduct Root Cause Analysis (RCA)
You have probably heard of the famous root cause analysis (RCA), but do your teams regularly conduct it?
They certainly should as this is another best practice for efficient asset maintenance.
Rather than addressing symptoms, RCA uncovers root causes, enabling long-term solutions and preventing recurring failures.
RCA’s ultimate goal is to move from reactive to proactive maintenance, reducing downtime and improving asset reliability along the way.
RCA has a few steps you need to follow, and here they are briefly explained:
Identify the issue | Recognize and document recurring problems or asset failures |
Collect data | Gather all relevant asset data (maintenance logs, sensor readings, performance history) |
Analyze the data | Identify patterns that reveal the root cause (you can use 5 Whys, Pareto charts, fishbone diagrams, and other tools and methods) |
Develop solutions | Based on the root cause, develop and implement corrective actions (e.g., part replacement) or preventive measures (better maintenance scheduling) |
Monitor | Track the asset to ensure the issue is resolved and to prevent future issues |
For example, if a motor repeatedly fails after a specific period of operation, analyzing maintenance records and performance data could reveal that overheating is a recurring issue due to poor ventilation.
By addressing this root cause, you can significantly reduce future failures.
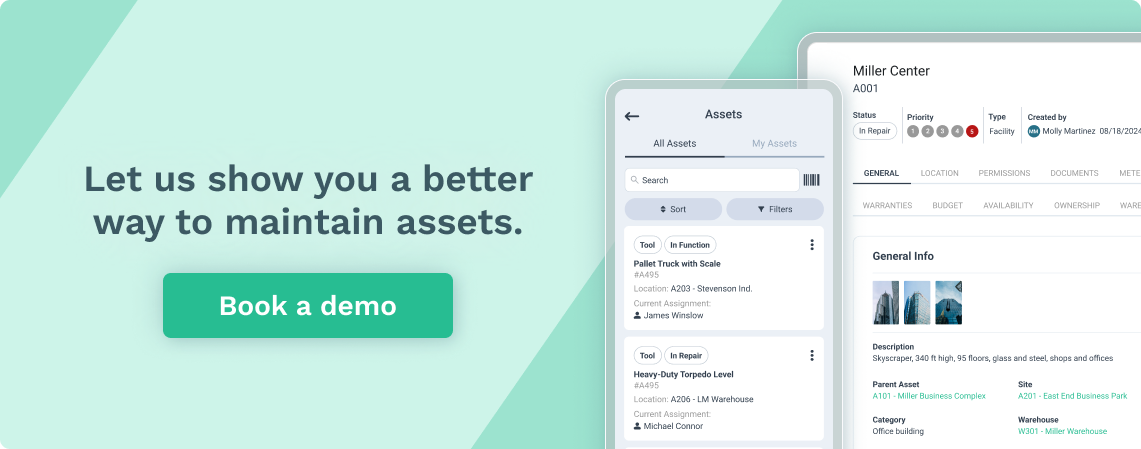
While RCA sounds excellent in theory, many maintenance teams struggle to apply it in practice.
They are often so focused on immediate fixes that they rarely have time to investigate root causes.
According to the same study by Augury, 74% of companies claim to use preventive maintenance (PM), but much of it is still reactive and manual.
Moreover, 37% of respondents wait for machines to break.
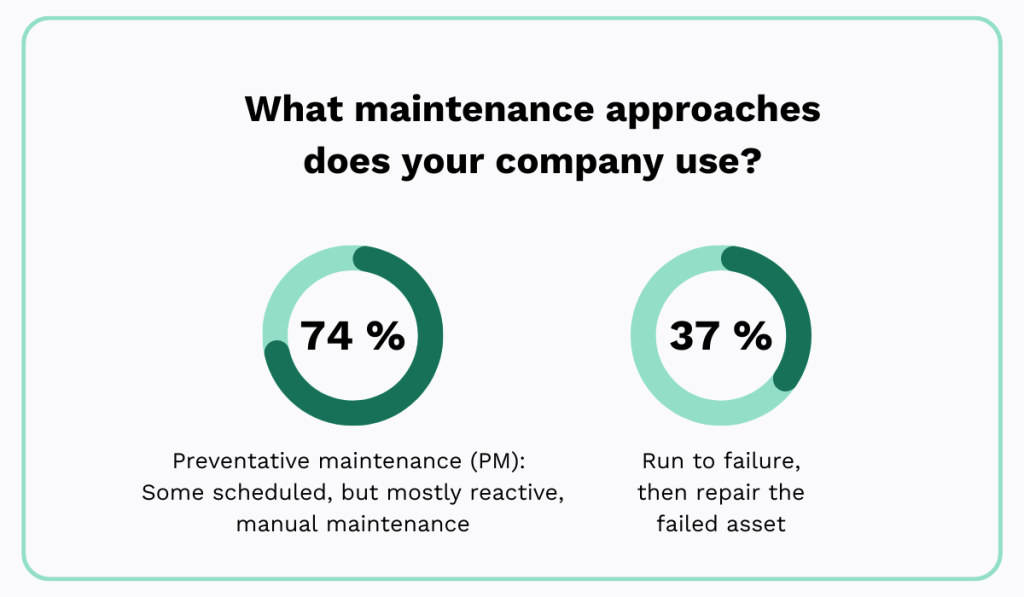
Data collection is another reason why companies struggle with this.
Naturally, successful RCA requires accurate, up-to-date data, as Tim Davison, Asset CARE Planner at Molson Coors (formerly MillerCoors), explains:
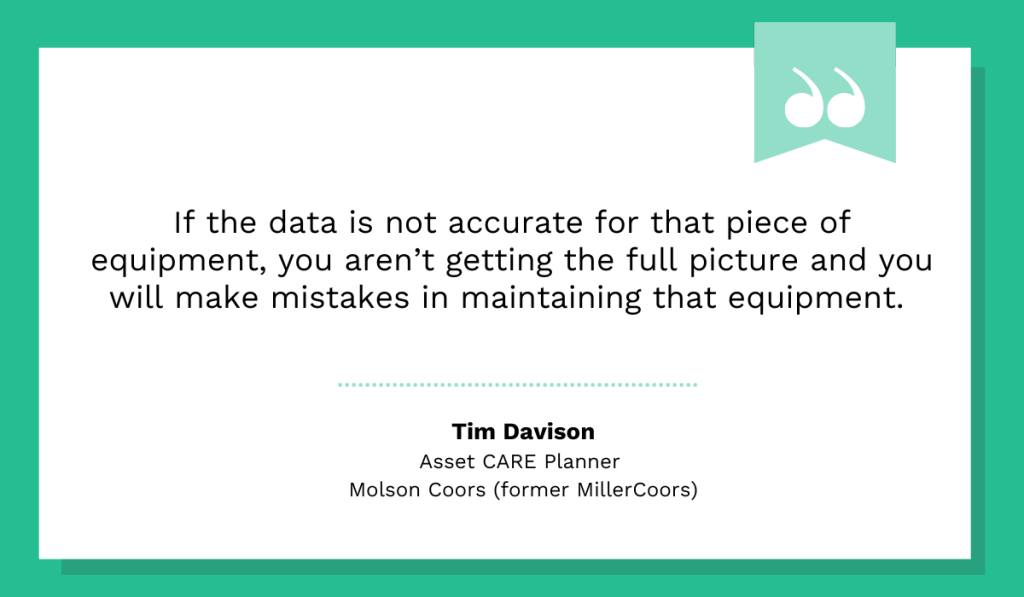
He continues that maintenance planners need data to prepare better maintenance plans.
Overall, if the necessary data isn’t readily available, it’s difficult to conduct any analysis, let alone the RCA.
Luckily, a smart way to get the data you need is by automating asset maintenance with a CMMS.
Automate Your Asset Maintenance
Automating asset maintenance with a software solution like CMMS can improve your maintenance processes and overall asset management.
CMMS automates workflows, and triggers maintenance tasks, preventive maintenance schedules, and approval processes.
Instead of relying on manual tasks that cause delays or missed maintenance windows, the system sends automatic alerts when inspecting or servicing a machine.
Take WorkTrek as an example.
This solution transforms your workflows from manual, time-consuming processes to a faster, more efficient system, and customers recognize this:
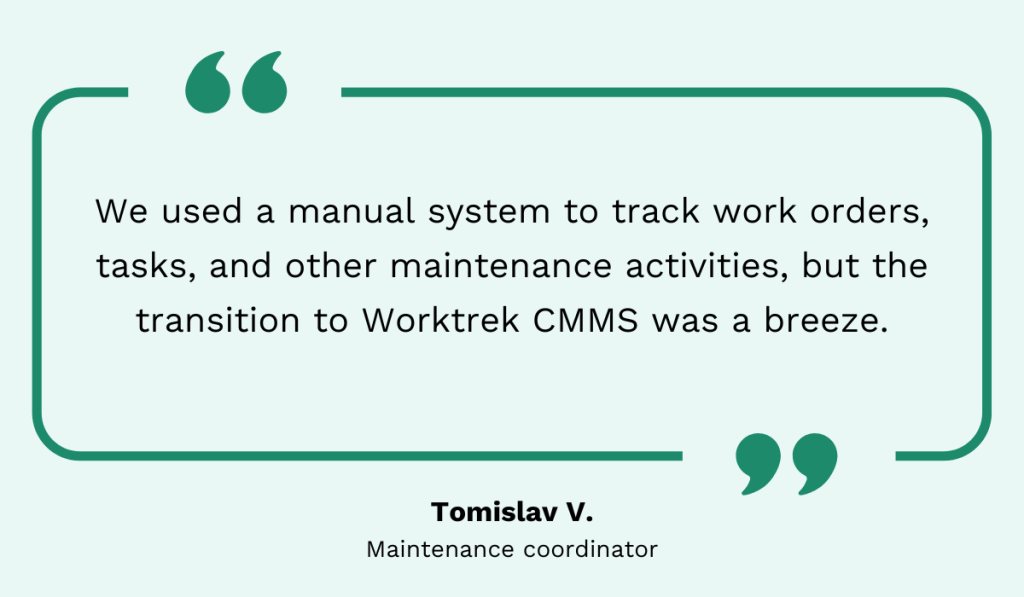
Our user also mentions that the system’s design is intuitive, allowing them to create and assign work orders with little effort quickly.
Let’s see how WorkTrek achieves this.
For starters, all your asset data is stored in one place. You can access historical data, maintenance logs, and spare parts lists.
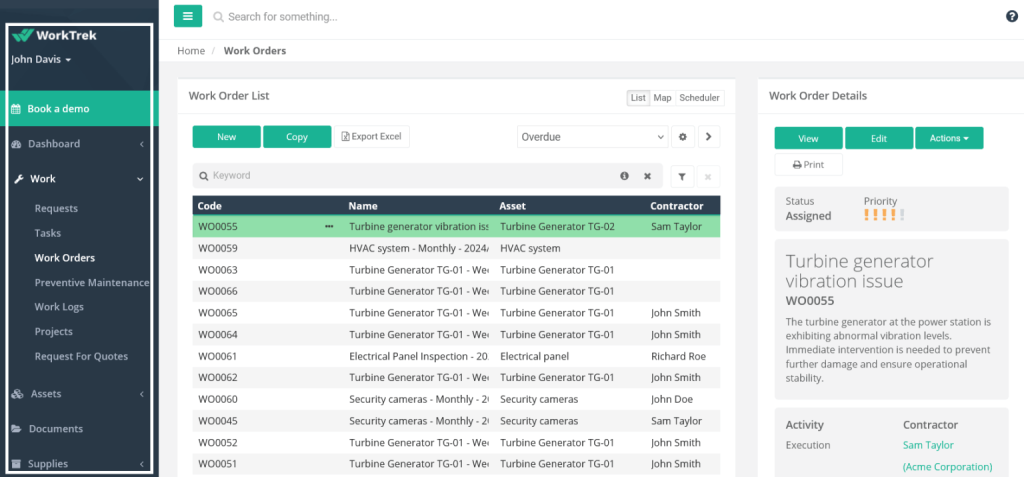
Next, when it comes to maintenance scheduling, WorkTrek allows you to view the schedule in a calendar format, which makes everything more organized.
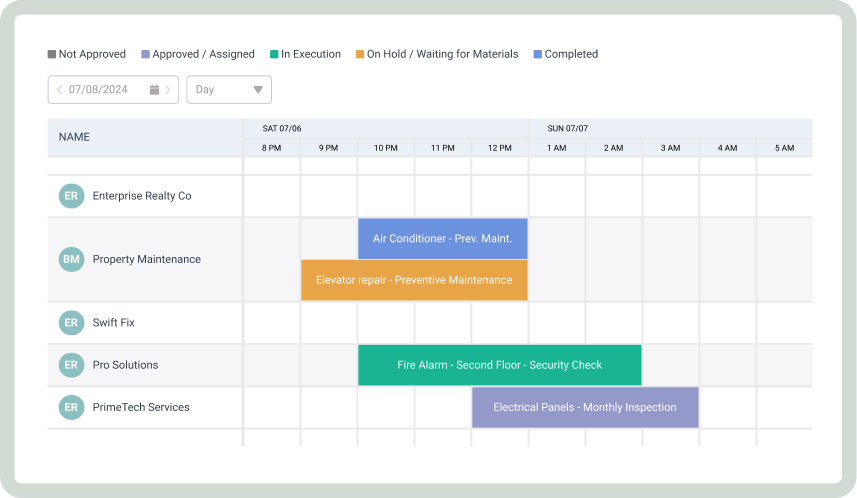
Additionally, the system helps you track asset locations and usage.
With a map-based interface, you can visualize where assets are, who uses them, and what condition they’re in.
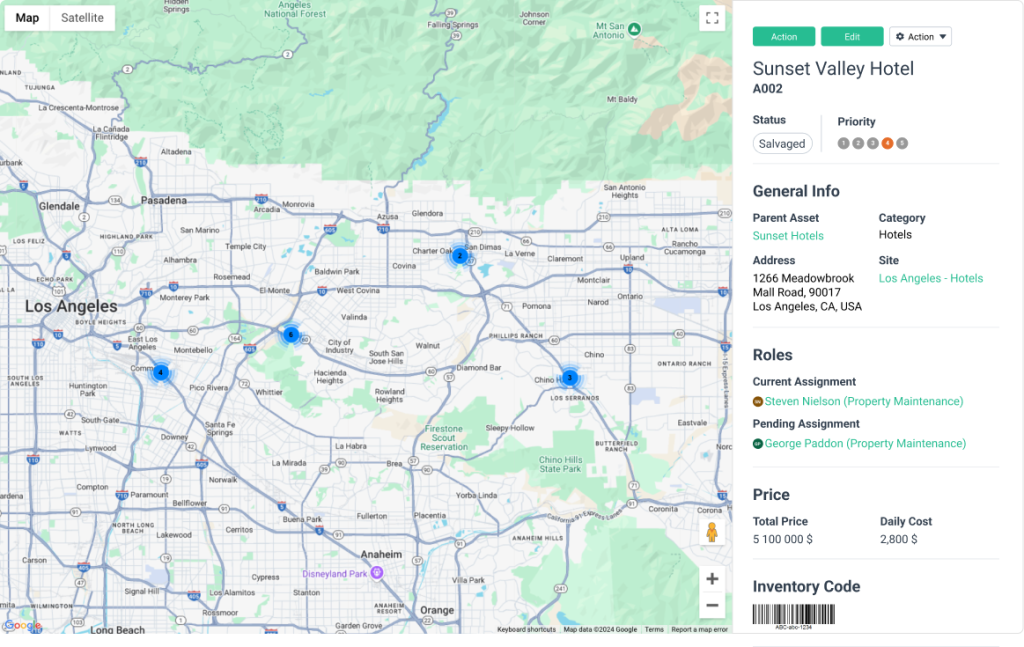
Meter readings can even track asset performance over time, allowing you to schedule maintenance based on real usage data.
And for assets that need simple weekly or monthly checks, you can schedule that easily, too.
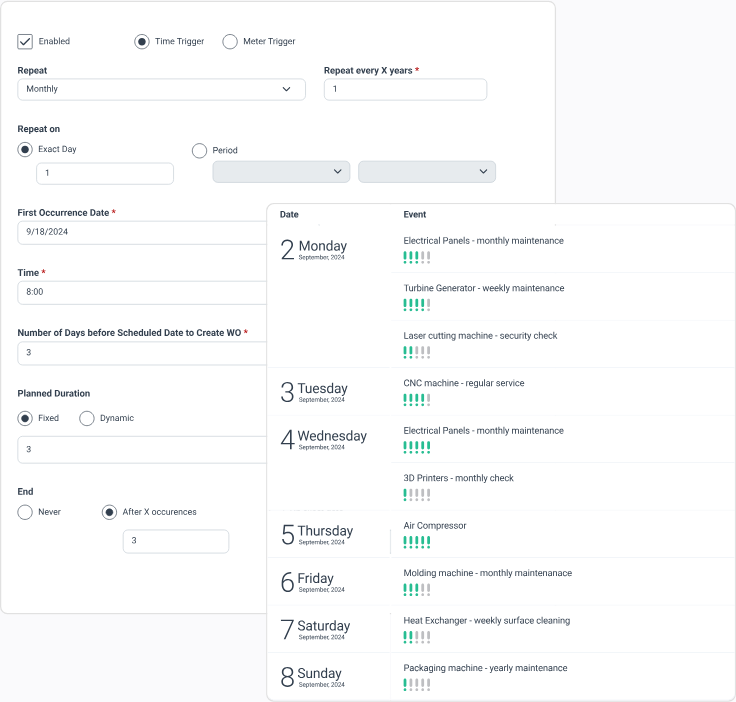
Technicians also benefit from this automation.
While on-site, they can scan asset barcodes or QR codes with their smartphones to access information such as repair history or instructions.
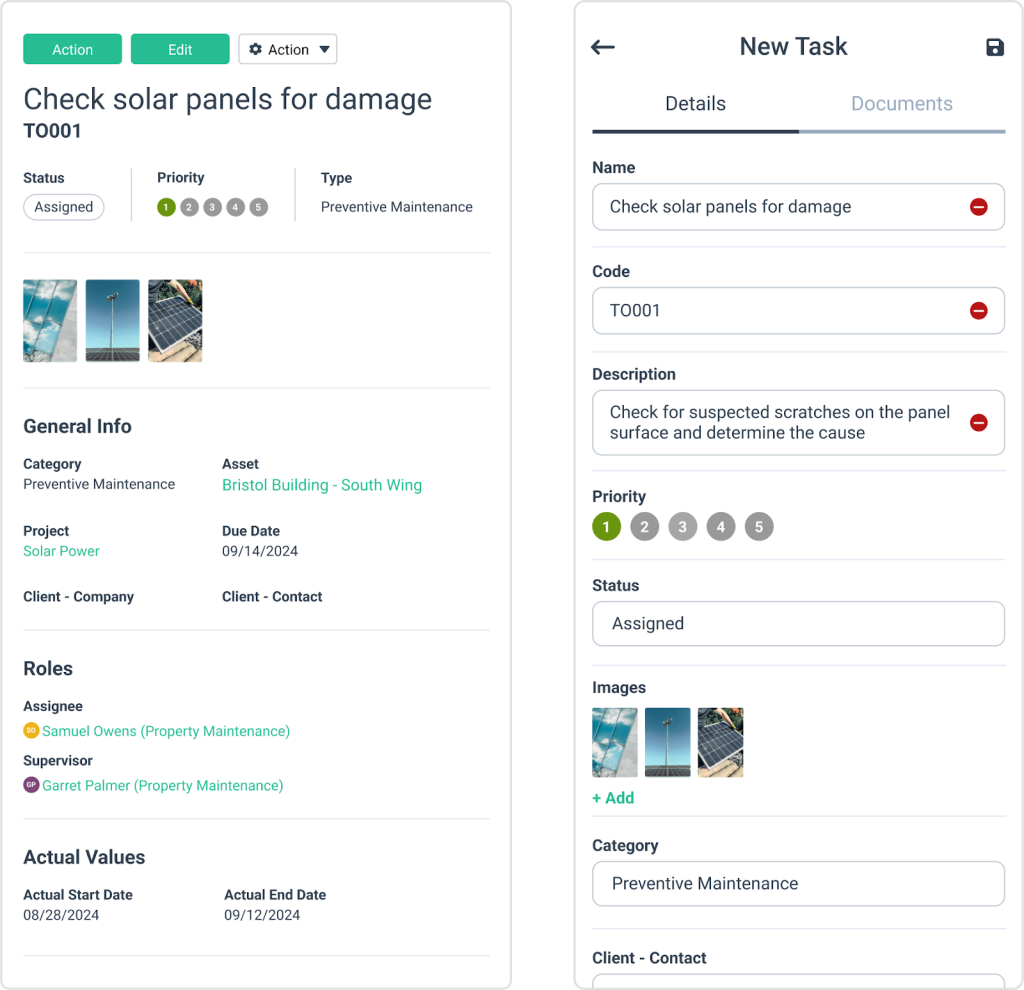
All these automated features save significant time and money.
Office staff can avoid manual scheduling, and technicians can complete tasks more efficiently.
These time savings translate directly into cost savings.
Standardize Maintenance Processes
Standardizing your maintenance processes is just as crucial as automating them, and a CMMS is the perfect tool to help you achieve both.
Creating standard operating procedures (SOPs) for frequent, high-risk, or complex tasks ensures that every maintenance activity is performed consistently.
One of the best ways to standardize maintenance is by using checklists.
With CMMS like WorkTrek, you can create digital checklists for every work order, outlining the necessary steps, schedules, and responsibilities for each task.
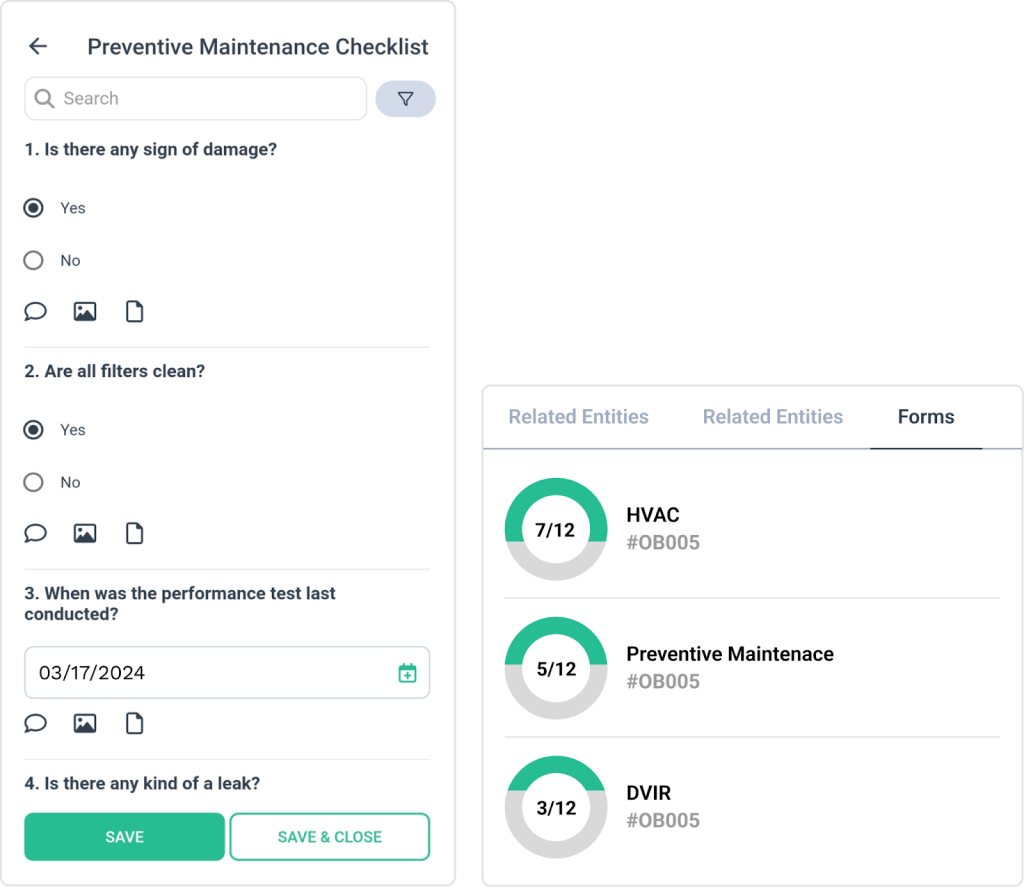
This standardizes the maintenance process and ensures that all work is done consistently, no matter who performs the task.
We don’t need to overemphasize how much time this saves.
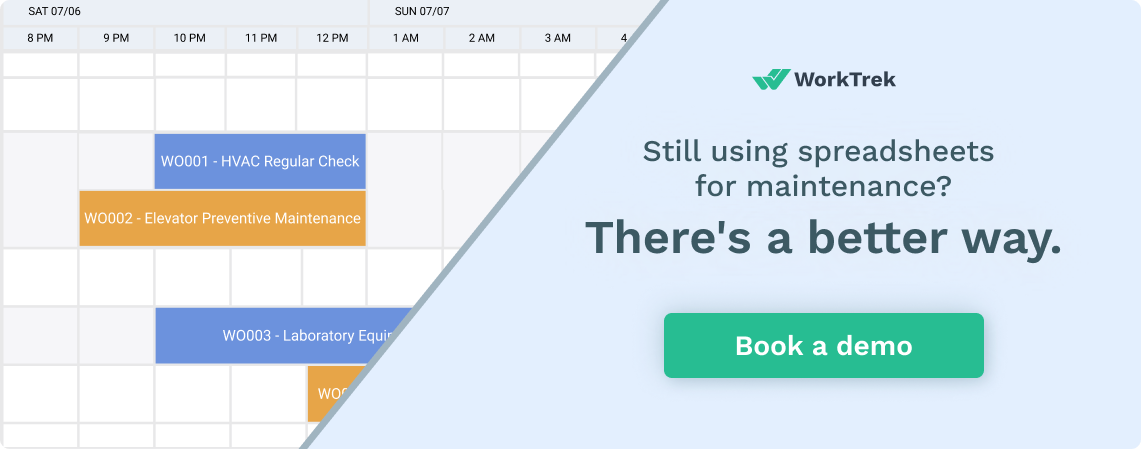
Siu Loon Khuu from the Swiss railway company BLS explains it well by describing how digital checklists increased the efficiency of their asset maintenance:
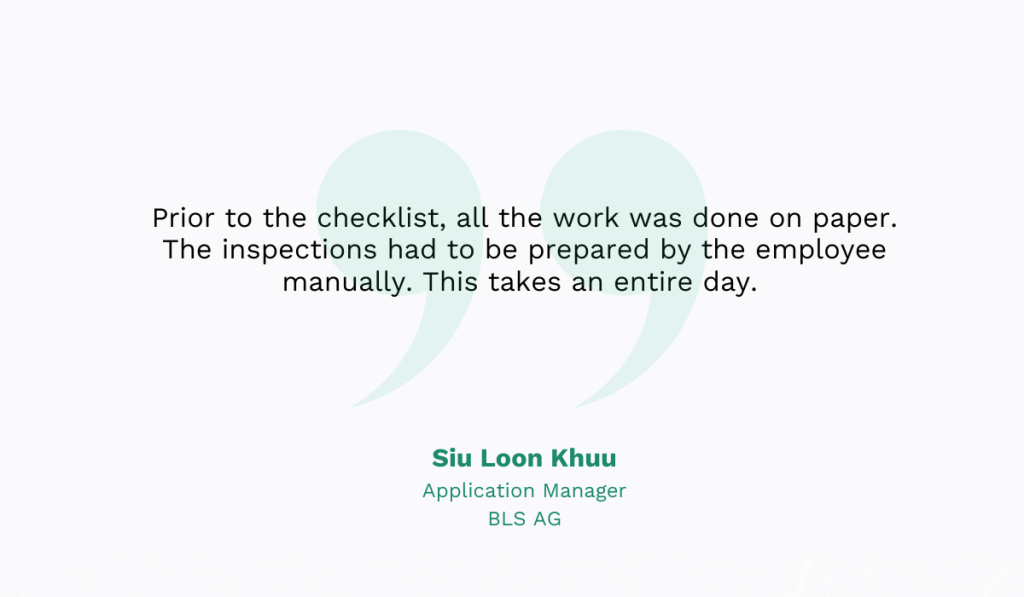
Preparing inspections took one day, and transferring the results in Excel manually took another.
Apart from saving all this time, he explained that such digital checklists simplify the technicians’ work and provide compliance documentation which is so important in the railway industry.
Another big plus is that digital checklists, like those from WorkTrek, automatically generate follow-up work orders for failed inspections or flagged issues.
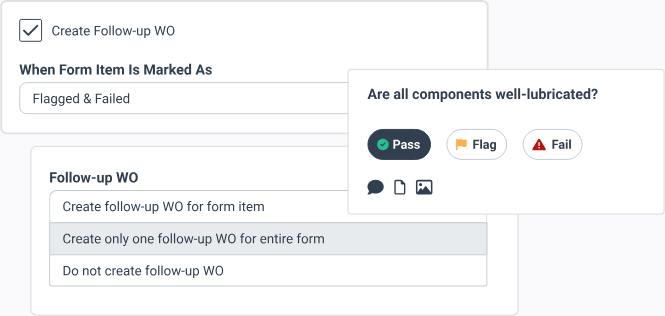
This is where standardization and automation work in tandem.
But the benefits don’t stop at saving time.
Standardizing maintenance processes can also significantly impact the technicians’ safety.
The right CMMS will allow you to predefine hazards and risks for every asset, set requirements for necessary personal protective equipment (PPE), and establish lockout/tagout procedures for each piece.
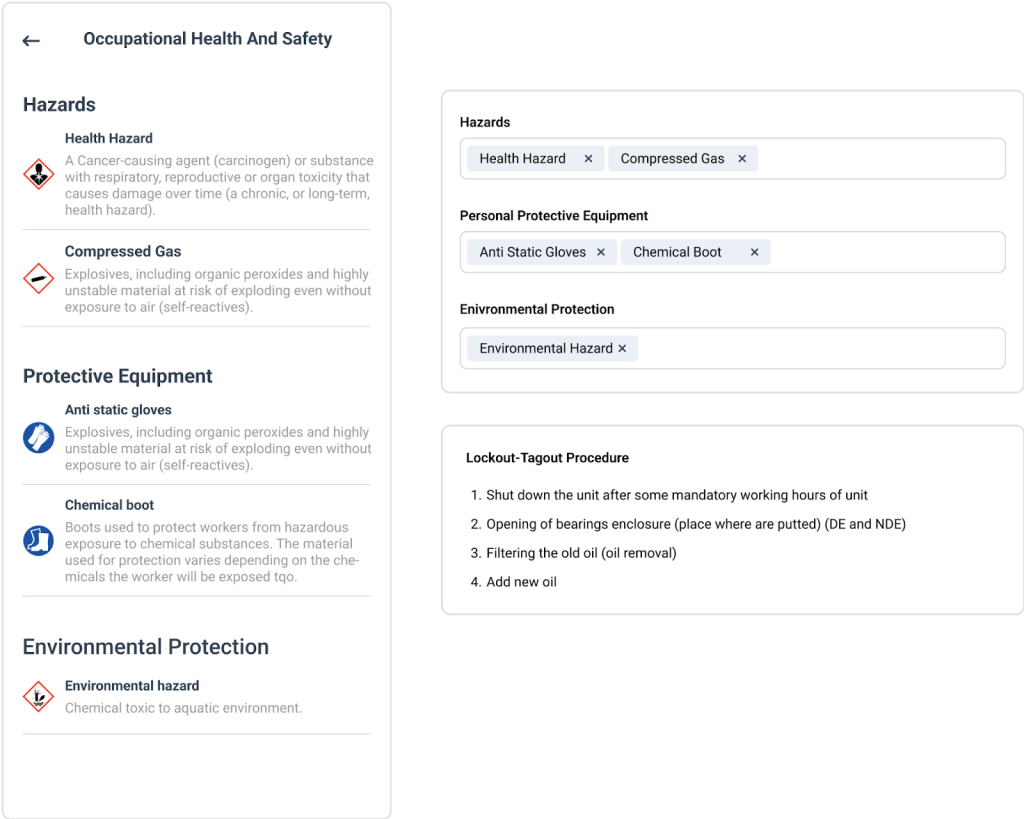
When this information is in your CMMS, technicians can access it anytime and follow the correct safety procedures.
That’s a big plus since you can rest assured that you did everything possible to keep your team safe.
Lastly, standardized procedures make training, evaluating, and certifying your maintenance team much easier.
When everyone follows the same processes, you can provide clear training materials, ensure all your technicians are updated with the required standards, and assess performance more effectively.
Track Asset Maintenance KPIs
How will you know if all these best practices are yielding results in your maintenance strategy?
By tracking asset maintenance KPIs.
After all, you can only improve what you measure.
To ensure you’re getting the most out of your maintenance, you should track the following KPIs:
- Work order resolution time to track how long it takes to complete work orders.
- Maintenance backlog to measure the number of unresolved maintenance tasks.
- Overtime, indicating whether the maintenance team is overburdened.
- Percentage of planned maintenance (PMP) to track how much of your maintenance work is planned rather than reactive.
Monitoring these KPIs helps identify bottlenecks, inefficiencies, and opportunities for improvement.
These lead metrics translate into lag (asset) metrics, which you can also track.
KPI | What it tracks | What it means |
---|---|---|
Mean time between failures (MTBF) | the average time between asset failures | a higher MTBF means your assets are more reliable |
Mean time to repair (MTTR) | the average time it takes to repair a failed asset | the lower the MTTR, the quicker you can get back to production |
Overall equipment effectiveness (OEE) | combines availability, performance, and quality to measure the effectiveness of your assets | a higher OEE means better asset use and fewer issues |
Equipment downtime | how much time an asset is down due to failures or maintenance | high downtime means frequent breakdowns or inefficient maintenance practices |
The key is doing it regularly.
Only by consistently tracking these KPIs can you ensure that you’re always improving your processes and making the best use of your resources.
They did that at Molson Coors (formerly MillerCoors) in the early 2000s.
Bobby McCall, the maintenance manager for packaging operations, explained at the time how tracking and adjusting the preventive maintenance frequencies helped them improve.
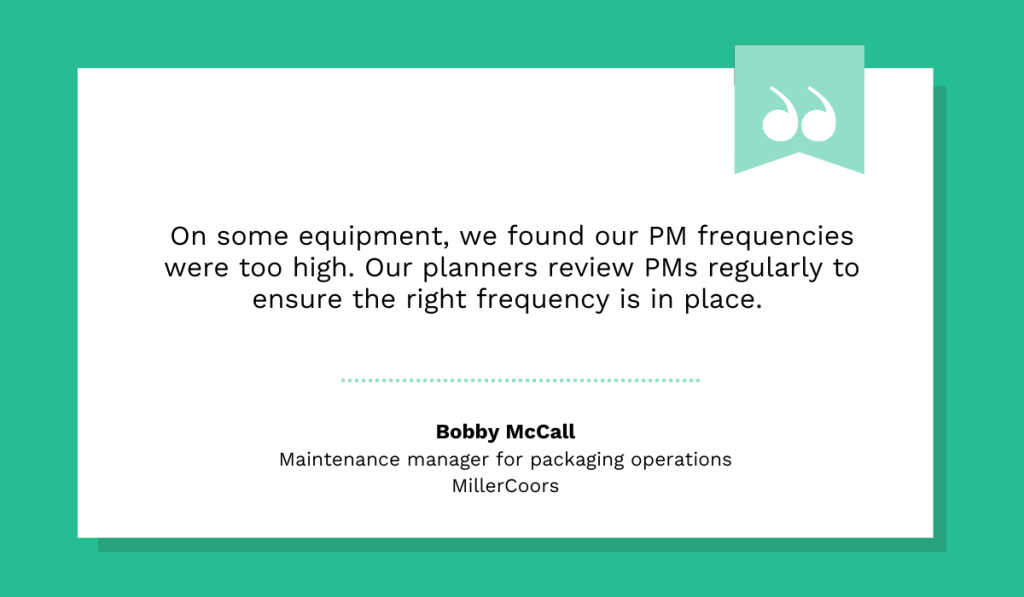
Their goal was to focus on the work that needed to be done and to optimize time and resources.
Of course, by reviewing maintenance regularly, Molson Coors achieved significant improvements.
For example, planned and scheduled maintenance now makes up over 60% of their maintenance workload, compared to less than 30% in the past.
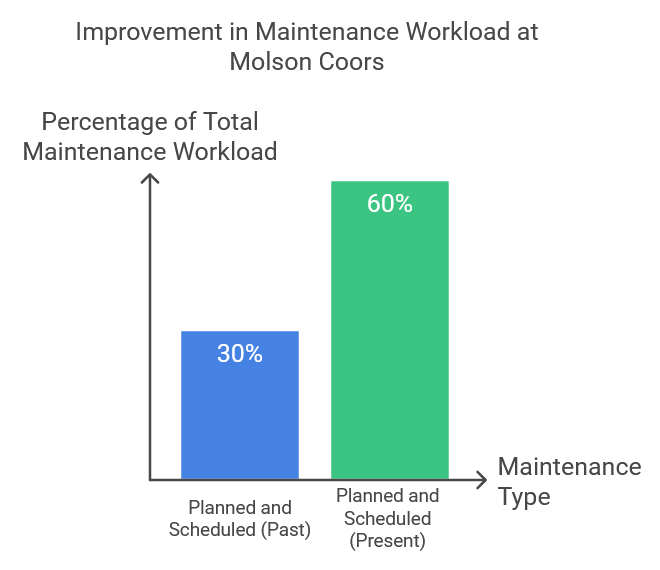
They also increased their preventive maintenance completion rates, with forklift maintenance rising from 31% to 82% in under 18 months.
All in all, these changes led to cost savings, improved reliability, better decision-making, and greater operational stability.
This proves that tracking the right KPIs can make all the difference in achieving more efficient asset maintenance.
Conclusion
Adopting these five best practices for asset maintenance will undoubtedly transform your operations, drive efficiency, reduce costs, and improve asset reliability.
The benefits are clear: extended asset lifespans, reduced breakdowns, and lower operational costs.
To replicate this success, ensure your team adopts these best practices and begins implementing them today.