Get a Free WorkTrek Demo
Let's show you how WorkTrek can help you optimize your maintenance operation.
Try for freeDesigning effective maintenance shop layouts can enhance efficiency and productivity. This guide covers linear, U-shaped, and Cellular layouts and offers key considerations and best practices for creating an optimal workspace for your needs.
Listen to this Article
Choosing the Right Layout for Your Maintenance Shop
Selecting the ideal configuration for your maintenance shop can significantly impact your team’s productivity and efficiency.
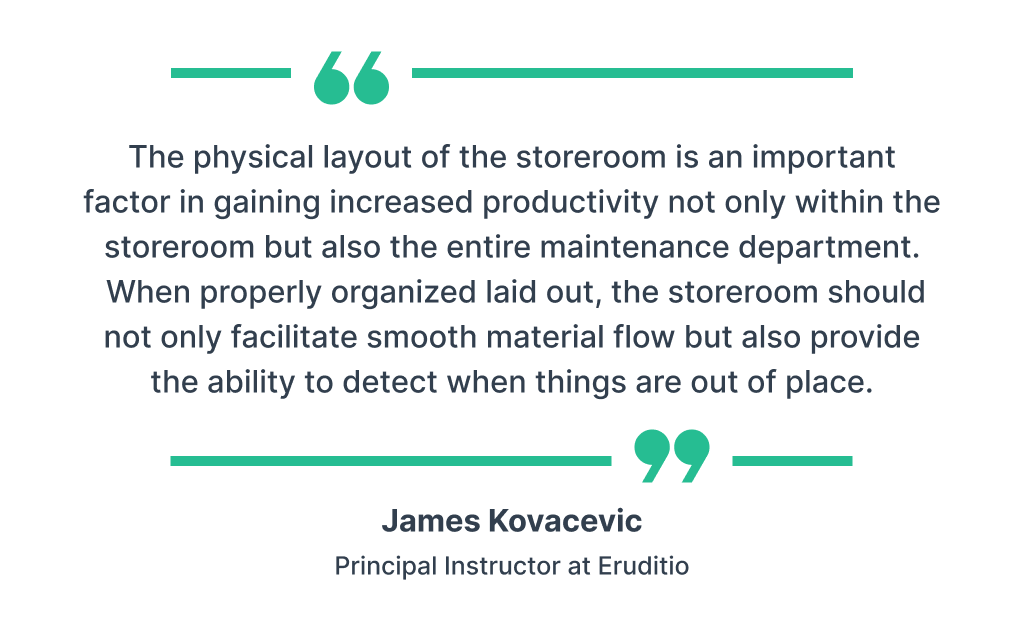
Illustration: WorkTrek / Quote: HP Reliability
Customize this setup based on your industry’s particular demands and the nature of the tasks at hand. A practical layout maximizes space utilization, facilitates workflow management, and promotes a safe working environment.
Layout Types
Various layouts are utilized in maintenance shops, each offering distinct benefits. This segment will delve into three widespread arrangements: linear, U-shaped, and Cellular configurations.
Comprehending their strengths and limitations lets you choose a design that effectively complements your facility’s maintenance operations.
Choosing an appropriate layout entails assessing several factors, such as available space within your shop, equipment being operated by staff members, and routine tasks performed there.
A closer look at individual layouts’ specifics is instrumental in pinpointing which one best suits your organization.
1. Linear Layout
A linear layout suits maintenance shops that carry out tasks in sequence well. It fosters a direct and efficient workflow, letting maintenance personnel proceed from one task to the subsequent ones without retracing their steps.

Source: International Journal of Advanced Robotic Systems
The arrangement of workstations in a straight line helps utilize vertical space optimally while keeping tools and equipment within easy reach.
Such an arrangement is especially beneficial for shops dealing with repetitive tasks that need an uninterrupted pathway for conducting maintenance work efficiently.
2. U-Shaped Layout
A U-shaped configuration is ideal for small to medium maintenance shops. It offers a compact and efficient design. Tools and equipment are placed in a central position, making them easily accessible from various locations within the shop.
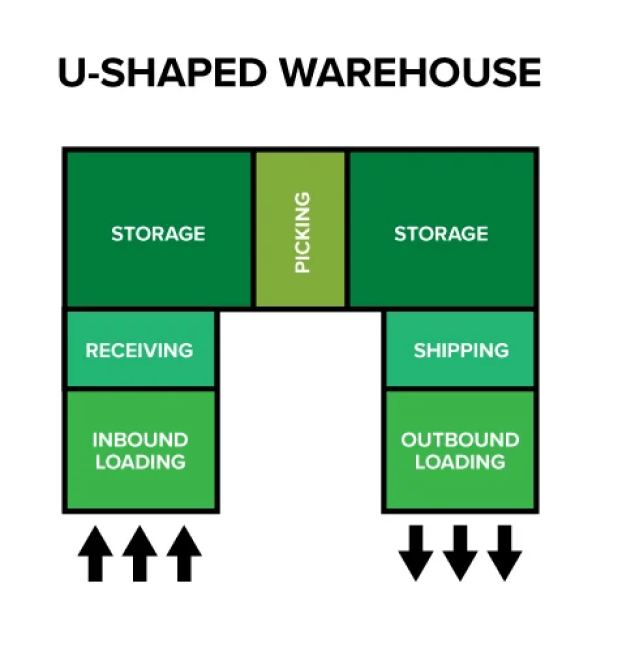
Source: Webstaurant Store
This arrangement enables staff to transition swiftly between workstations, increasing flexibility and quick response capabilities.
This layout enhances teamwork by promoting improved communication among personnel. With tools and equipment readily available at a moment’s notice for everyone involved in maintenance activities, efficiency is heightened, leading to less downtime and an uptick in overall productivity.
3. Cellular Layout
The design of a cellular layout is particularly tailored to meet the unique needs of maintenance shops. It ensures that specific tasks and equipment are accommodated for maximum operational agility.
This configuration reduces extraneous movement and improves the efficiency of work processes by assembling related operations into dedicated cells within the workspace.
By strategically arranging workstations and machinery into distinct zones, workers can concentrate on tasks with fewer disturbances. This organization fosters an environment where maintenance activities can be carried out more smoothly and proficiently.
Considerations for Maintenance Shop Layouts
Creating a practical shop layout requires addressing several critical factors that influence the functionality and productivity of your business operations.
Focusing on efficient space utilization, streamlining workflow processes, and implementing safety protocols can significantly bolster a work environment that promotes proficient task execution by staff.
Optimizing available space can ensure your shop has ample capacity for housing all essential tools, equipment, and inventory without appearing overcrowded. Efficient organization minimizes the time spent searching and enhances overall orderliness.
Refine Workflows
Refining workflow efficiency involves structuring a floor plan conducive to seamless activity transitions. Situating storage centrally and categorizing components according to how often they are used helps reduce unnecessary movement while improving item reachability.
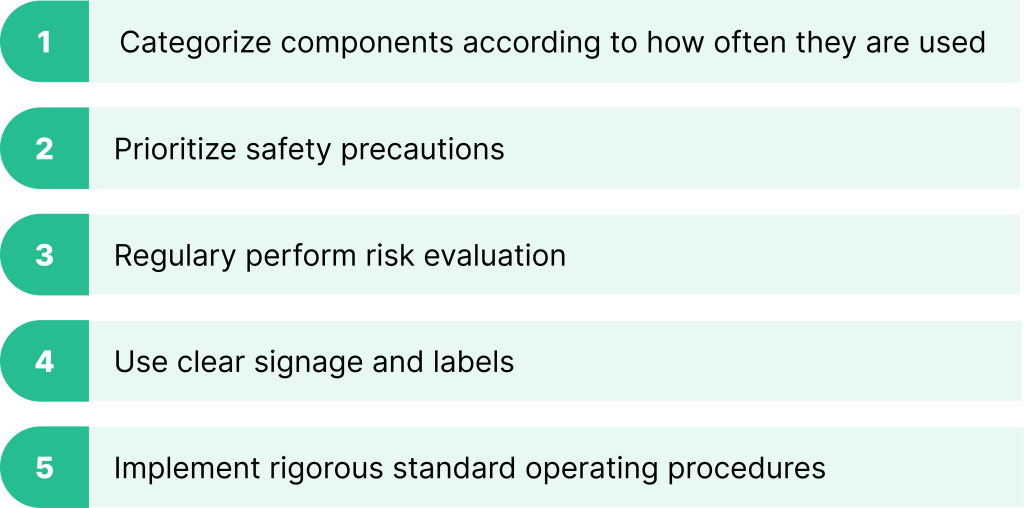
Source: WorkTrek
Finally, prioritizing safety precautions is critical in safeguarding employees and maintaining a secure operational setting.
Thorough risk evaluations should be performed regularly to reduce potential risks. Clear signage and labels should be maintained throughout the premises, and rigorous standard operating procedures should be implemented.
Space Utilization
Leveraging vertical space offers a practical approach to boosting storage efficiency while preserving essential ground areas.
High-density storage options like stackable bins and modular cabinets can significantly improve the capacity within constrained storage zones.
Assessing cubic space’s three-dimensional aspects lets you maximize your available storage region.
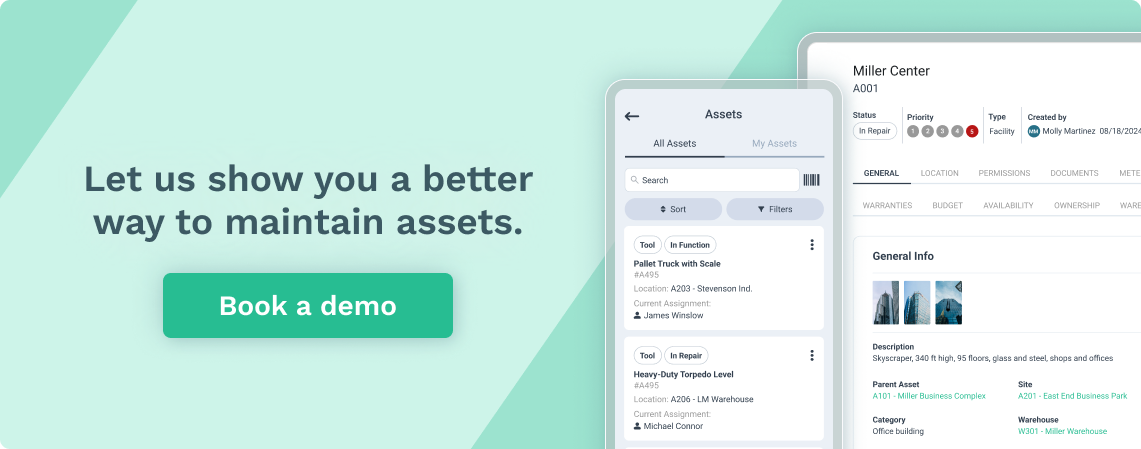
Implementing streamlined modular storage solutions helps arrange inventory in a well-ordered fashion, facilitating the process for staff members when they need to find and retrieve tools and equipment for maintenance tasks.
Workflow Efficiency
Create an efficient workflow. This can lead to a logical arrangement that facilitates the smooth transition from receiving parts to dispatching them after task completion.
A centralized stock room is beneficial for efficiency as it simplifies access and reduces travel time within the shop. This setup aids staff in quickly locating and obtaining essential tools and components required for maintenance.
The strategic organization of specialized equipment can significantly streamline shop operations.
Stock Position
Positioning items regularly near the stock room’s entrance reduces unnecessary movement throughout the space, leading to considerable time savings.
Inviting employee input about workflow can help pinpoint areas for improvement and cultivate an environment committed to ongoing refinement.
Safety Measures
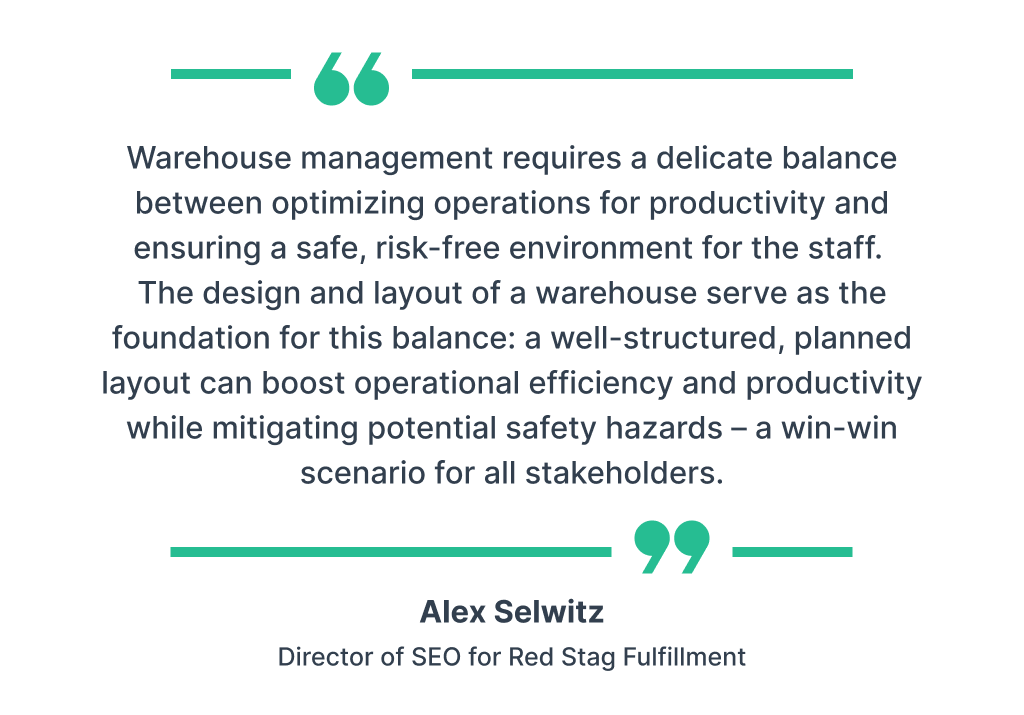
Illustration: WorkTrek / Quote: Safeopedia
Safety should not be ignored. Before determining the final storage setup, it’s crucial to perform an in-depth risk assessment to uncover potential dangers and allow for the integration of necessary precautions.
Maintaining clear identification and proper organization through signage helps staff quickly find equipment and tools while informing them about potential safety hazards.
The application of cautionary labels on cabinets containing hazardous materials and prominent 5S directional signs dramatically improves security within the storage area.
Organizing Workstations and Storage Solutions
Focus on creating an organized working environment. Such an environment enables maintenance staff to carry out their duties more efficiently, reducing unnecessary operational halts and boosting overall productivity.
Discussions will center on organizing tools, managing spare parts inventory effectively, and strategically positioning specialized equipment within the shop.
The arrangement of tools so that they are readily identifiable and accessible by maintenance personnel can significantly streamline tasks. Implementing uniform labeling systems and consistent inventory tracking strategies increases this aspect’s efficacy.
Spare Parts Management
Manage spare parts through orderly storage practices. Implementing technological advancements such as barcoding systems helps preserve the ready availability of necessary components.
Routine audits support keeping precise records of all items stored within the inventory.
Access to Protective Gear
Lastly, thoughtful space allocation for specialized machinery improves workflow dynamics while ensuring essential personal protective gear remains easily accessible for staff members in various upkeep activities throughout the shop.
Tool Organization
Just like in your garage, organize tools in the storeroom so they are easy to find. Clear inventory and clearly labeled tools allow staff to identify and access the necessary tools quickly.
Adopting uniform inventory tracking methods simplifies the inclusion of new items while maintaining record accuracy.
Utilizing storage solutions such as small parts bins and adaptable systems enables efficient use of storage space by organizing tools to reduce time spent searching for them.
By adopting labeling best practices and standardization, you maintain an orderly shop environment, translating into less time spent looking for equipment and more time dedicated to carrying out maintenance tasks.
Barcodes

Source: WorkTrek
Integrating a barcoding system diminishes the likelihood of retrieving an incorrect part, streamlining the inventory process and ensuring that the right parts are readily available. To achieve optimal results, this should be paired with proficient management techniques.
Ordering Spare Parts
Position items needed frequently nearest to the retrieval area. This reduces the time required to search for components.
Implementing a robust spare parts system featuring organized storage solutions and a well-structured method of tracking inventory data guarantees quick accessibility and neat organization.
Conducting regular audits helps keep inventory records precise, which assists in managing large quantities of spare parts linked with work orders without causing any disarray.
Continuously evaluating and refining your inventory procedures permits adjustments that align with operational shifts while preventing outdated methods from impeding efficiency levels.
Specialized Equipment Placement
If you are using specialized equipment, place them strategically within the workplace. This allows maintenance technicians easy access to the equipment.
By categorizing bearings and related parts according to type and size, coupled with clear identification of Bill of Materials (BOMs), the selection is expedited, minimizing the required inventory.
Correct equipment labeling and deliberate placement result in more streamlined maintenance activities and an orderly shop environment.
Training Maintenance Personnel
Frequent training workshops help employees become well-acquainted with the protocols and are reminded of optimal methods. Random inspections pinpoint areas that require enhancement and remedy any deficiencies in understanding or execution.
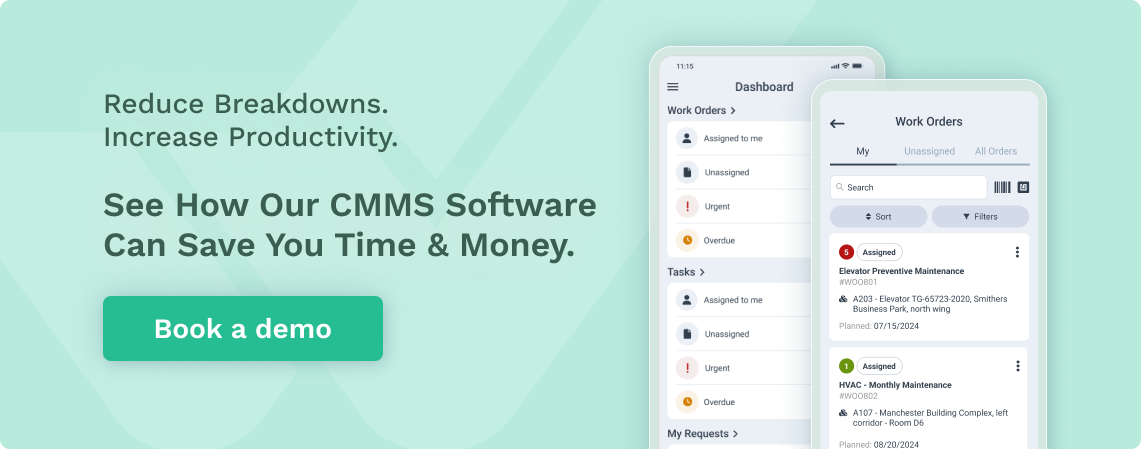
Maintaining a steady education schedule fosters a culture of perpetual advancement and compliance with established norms. This approach boosts efficiency while securing safe and effective operational performance, diminishing the likelihood of mistakes and mishaps.
Enhancing Inventory Management and Control
Implementing a secured storage area alongside inventory management software substantially improves stock oversight and regulation. This segment focuses on computerized systems that handle inventories, periodic cycle counting practices, and administering vital spare parts.
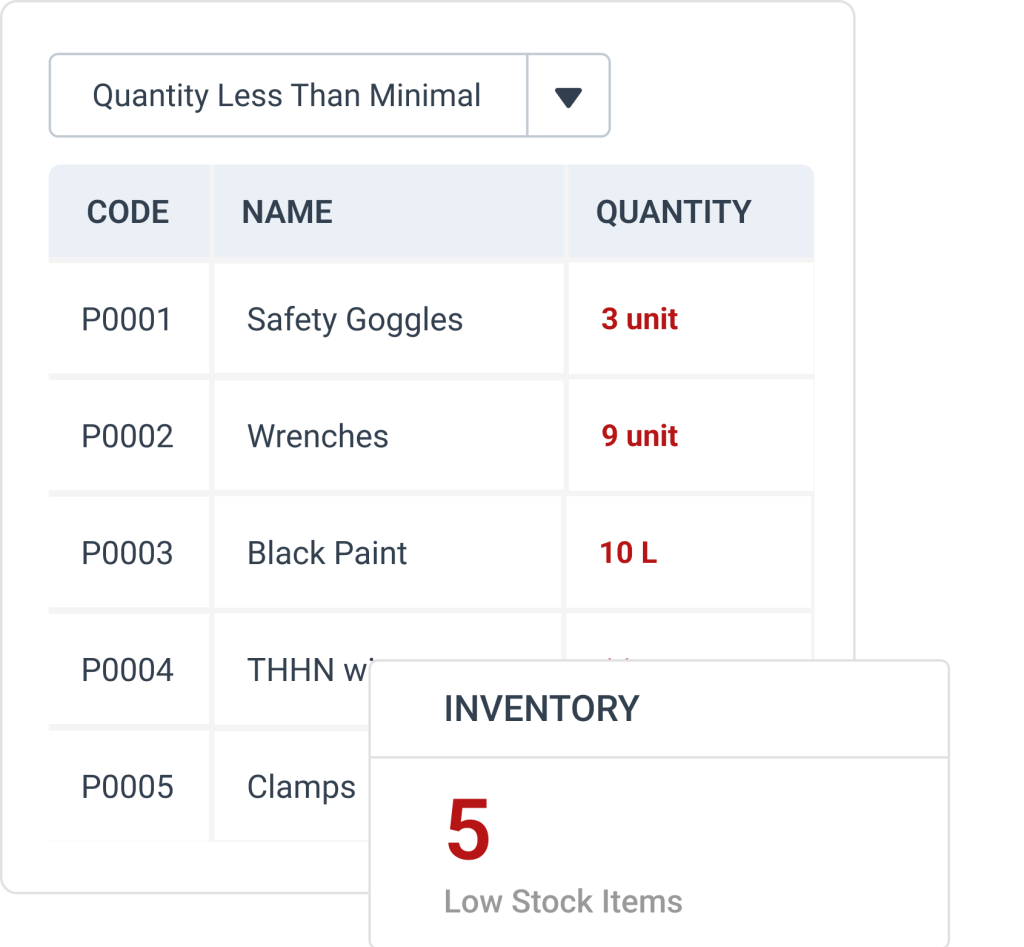
CMMS systems like WorkTrek, designated for handling inventory, provide instantaneous updates regarding stock levels and their allocation, facilitating strategic decisions while avoiding excesses or shortages in supply.
Source: WorkTrek
Regular cycle counts help promptly identify discrepancies in inventory records, ensuring accuracy in record-keeping and consistent control over inventory scheduling.
The organization of critical spares by how frequently they’re used, coupled with routine audits, helps guarantee the accessibility of necessary components when required without delay.
Digital Inventory Systems
Modern maintenance shops heavily rely on digital inventory systems for effective operation. These centralized systems facilitate the immediate tracking of inventory movements and stock quantities, which supports decision-making in managing inventories adeptly.
Most organizations integrate an inventory module within their Computerized Maintenance Management System (CMMS) to bolster management efficiency and oversight.

Source: WorkTrek
Adopting methods such as barcode scanning coupled with consistent updates is essential to maintaining accurate stock levels.
These practices help ensure that purchasing personnel receive prompt alerts when the quantity of items dips below pre-established minimums to trigger restocking activities.
Cycle Counting
Cycle counting can help keep inventory records accurate. Its objective is to identify and rectify any inconsistencies within the inventory, guaranteeing that the information accurately reflects the current status.
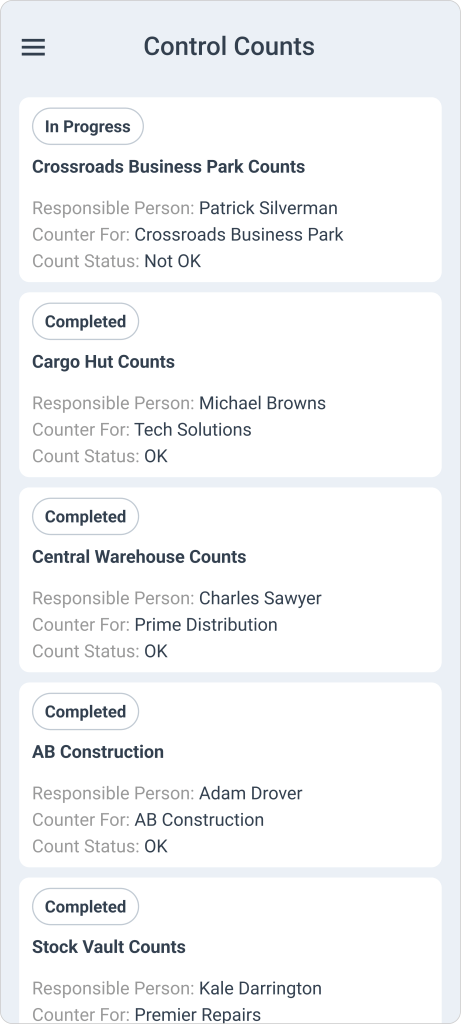
Source: WorkTrek
The rate at which cycle counts are performed should align with the significance and cost of specific items, meaning those more vital components may be counted more regularly.
This method ensures that a company’s inventory remains correct by consistently verifying and refreshing data on stock levels. Such diligence fosters streamlined maintenance operations by relying on dependable record-keeping for effective resource management.
Managing Critical Spares
Managing critical spare parts should be a high priority on your list. You should also keep accurate counts and log all items.
Before maintenance personnel can remove an item, it must be accurately logged into the stock system for precise inventory control and record-keeping. A CMMS system can automate this process.
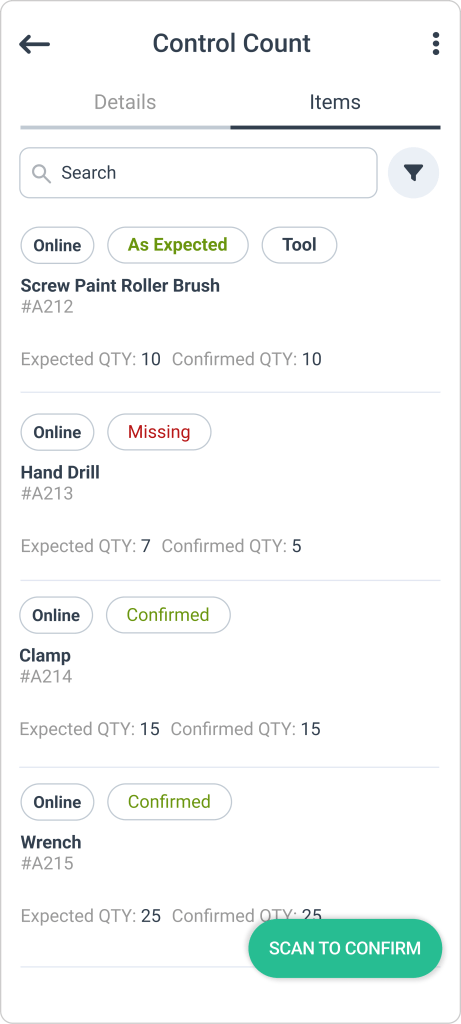
Source: WorkTrek
Preparing necessary parts for scheduled preventive maintenance enables the maintenance team to operate more effectively while diminishing the likelihood of equipment failure.
Continuous Improvement
Establish a culture that promotes ongoing enhancement of the process.
- Establish specific Standard Operating Procedures (SOPs) to meet your shop’s unique needs.
- Ensuring that all maintenance personnel receive thorough training, guaranteeing uniformity in procedure execution.
- Routinely assessing and refreshing SOPs to ensure their continued efficacy and alignment with changing operational demands.
- Listen to feedback from maintenance team members and implement suggestions.
Motivating team members to take an active role in pinpointing areas for advancement and applying upgrades to improve operational effectiveness.
Summary
In summary, the design of the maintenance shop is key to utilizing the space, workflow, and safety. A strategic layout that uses every inch and has workstations alongside storage solutions will give your maintenance team a safe and productive environment.
Following standard operating procedures and maintaining organization through regular upkeep, incremental improvements, and monitoring will keep your maintenance standards high.
Remember that a streamlined maintenance shop is an ongoing process—regular reviews are needed as new requirements or best practices change. Having a culture of continuous improvement and involving your maintenance team in this will help them work together to manage the workshop area safely, putting any business on the road to long-term success.