Get a Free WorkTrek Demo
Let's show you how WorkTrek can help you optimize your maintenance operation.
Try for freeKey Takeaways:
- Among organizations that use EAM software, 98% rely on it to generate reports.
- 62% of companies have implemented a CMMS.
- CMMS solutions can automate preventive maintenance scheduling.
You’ve probably heard of CMMS and EAM systems if you own or manage physical assets.
These terms are often used interchangeably when referring to software for asset management, maintenance planning, and maximizing asset ROI.
However, they’re not the same.
In fact, not knowing the difference and picking the wrong one could easily translate to missed opportunities, wasted money, or various operational disruptions down the line.
Therefore, this article will discuss the key differences between CMMS and EAM systems.
This will help you choose the solution that best aligns with your organization’s needs and goals.
What Is a CMMS?
CMMS (Computerized Maintenance Management System) is software designed to help you maintain your assets more efficiently by automating various upkeep processes.
Think of a CMMS as a centralized hub for all your maintenance-related activities.
It enables you to issue and track work orders, access detailed asset information, generate reports, and view current and historical data—all in one place.
Here are some typical CMMS features:
Work Order Management | Create, assign, track, and analyze maintenance tasks from a single platform. |
Compliance Management | Define, access, and manage health and safety procedures, linking them to specific assets and work orders. |
Inventory Management | Easily track inventory levels, manage spare parts and materials, and never miss a reorder with automated alerts. |
Invoicing | Generate invoices directly from work orders in just a few clicks. |
Analytics & Reporting | Gain insights through automated reports, key performance indicators, and customizable dashboards. |
Mobile Functionality | Access all CMMS features on the go. |
One of the most valuable features of a CMMS is preventive maintenance management.
This feature automates upkeep schedules based on either time (e.g., daily, weekly, monthly) or usage metrics (e.g., runtime, mileage, temperature, pressure), as shown below.

Based on these triggers, the system automatically generates work orders with all the necessary details and sends timely alerts for an upcoming service or inspection.
This proactive approach ensures that assets are maintained at the right time, reducing unplanned downtime and extending their lifespan.
As Baron Brown, Senior Project Engineer at FST Technical Services, a provider of life cycle testing, inspection, certification & engineering solutions, puts it:

Essentially, a CMMS helps ensure that key equipment upkeep is always done on time, addressing minor problems before they escalate, says Brown.
That’s likely why many companies are adopting this technology across their operations.
According to a 2024 survey by the Institution of Mechanical Engineers, 62% of organizations use a CMMS—up from 49% the year before.

And it’s easy to see why.
As companies grow and their maintenance needs become more complex, traditional manual processes can no longer keep up.
Tracking tasks, planning maintenance activities, and monitoring progress through paper logs and spreadsheets only introduces errors and disruptions.
A CMMS is the most effective way to tackle inefficiencies, making maintenance more streamlined, organized, and data-driven.
What Is EAM?
Enterprise Asset Management (EAM) software helps you manage and optimize the entire lifecycle of your physical assets, such as equipment, machinery, and infrastructure.
Here are some typical features you can expect in such a system:
Maintenance Management | Preventive maintenance scheduling, predictive maintenance using sensors or condition data, and work order management. |
Inventory & Spare Parts Management | Parts usage and availability tracking, reorder alerts, and supplier integration. |
Labor & Resource Management | Maintenance team scheduling, timesheet tracking. |
Reporting & Analytics | Dashboards for asset performance, compliance, and audit reports. |
Financial Management | A comprehensive financial view of your asset portfolio and future expenses forecasting. |
You’ll notice that many CMMS and EAM features overlap, including preventive maintenance, work order management, and maintenance cost tracking.
However, EAM software is designed to offer a more holistic approach to asset management, covering all phases of an asset’s lifecycle.
This entails everything from planning and procurement to operation, maintenance, and eventual disposal.
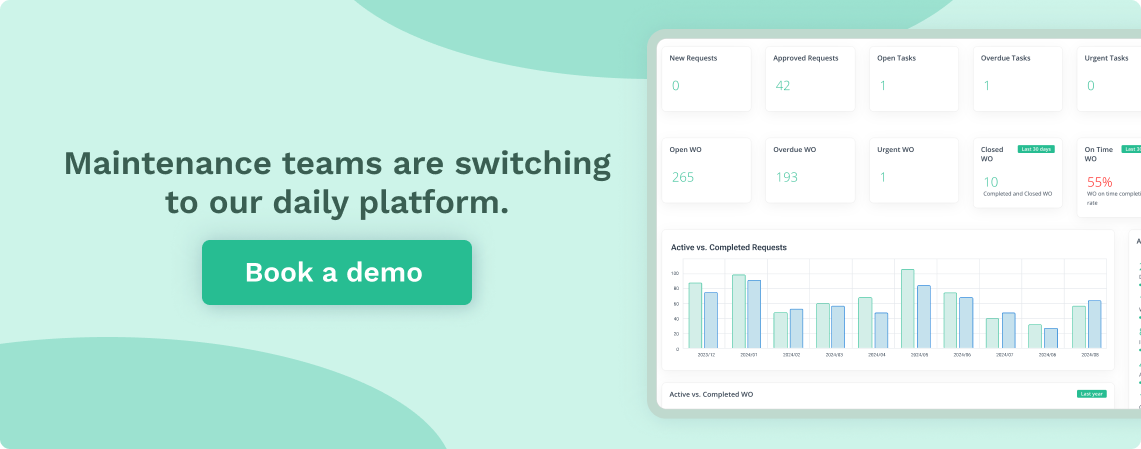
In essence, all asset-related information is centralized and accessible from anywhere.
Alan Salton, Managing Director at Panorama Consulting Group, a consulting firm specializing in digital transformation, sums up the whole purpose of EAMs:

These solutions are key to gaining control over your assets, from ensuring compliance to helping you understand your Overall Equipment Effectiveness (OEE).
In terms of specific use cases, companies leverage EAM software for a wide variety of tasks.
According to a 2025 survey by Brightly, the top three include generating reports, physical asset tracking, and maintenance management.
Overall, EAM and CMMS solutions share many similarities. Both were developed to help organizations maximize the value of their assets.
This is why confusion between the two is so common.
Still, to gauge which system is right for your business, it’s important to fully understand how they differ from each other.
Therefore, let’s break down the key differences between EAM and CMMS.
CMMS vs EAM: A Comparison
The key difference between CMMS and EAM software lies in their scope and focus.
CMMS solutions are designed to optimize upkeep operations: managing WOs, ensuring timely maintenance, tracking spare parts, and measuring upkeep effectiveness.
EAM systems, on the other hand, have a broader scope.
They include everything a CMMS does but go further by managing the entire asset lifecycle, including procurement, financial tracking, and more.
But the differences go beyond just focus.
To help you see the distinctions between these two types of software, we’ve broken down the key differences in the table below:
Category | CMMS | EAM |
Focus | Primarily maintenance operations: tracking WOs, managing preventive maintenance, and scheduling repairs. | Broader scope: covers asset planning, acquisition, usage, maintenance, and disposal; integrates with finance, inventory, HR, and more. |
User Base | Maintenance teams, technicians, and facility managers. | A broader audience, including maintenance, operations, finance, and executive leadership. |
Implementation | Quicker to implement and doesn’t involve extensive training. | More complex rollouts require cross-departmental input, data migration, training, and phased implementation. |
Cost | Lower overall cost due to narrower scope and fewer features. | Higher cost due to expanded capabilities like financial integration and strategic planning. |
Pros | Easy to implement and use, cost-effective, ideal for small to mid-sized organizations, and helps reduce unplanned downtime. | Highly versatile, provides a detailed view of each asset across its lifecycle, supports advanced analytics, and integrates across departments and enterprise systems (ERP, HRMS). |
Cons | Limited to maintenance tasks, may not integrate well with other enterprise systems, fewer use cases. | Greater complexity, higher cost, and potentially excessive for organizations with basic maintenance needs. |
As you can see, CMMS and EAM systems differ in more ways than it might seem at first glance.
However, Tim Shope, Industry Leader at the controls systems provider, Hargrove Controls & Automation, maintains that these tools should be seen as complementary rather than different:

In other words, while each system has unique strengths, weaknesses, and ideal use cases, they deliver the best results when used in tandem.
But what if implementing both systems isn’t feasible for your organization?
Let’s discuss how to choose the right solution for your specific needs.
Which Is Right For Your Business?
When choosing between an EAM system and a CMMS, start by asking yourself a few key questions:
- What’s the primary goal—just maintenance or full asset lifecycle management?
- Do you need integration with other enterprise systems (e.g., ERP, finance)?
- How many assets are you managing, and how complex are they?
- What level of reporting and analytics do you require?
- Do you have the time to commit to implementation?
- How tech-savvy is your team?
- What’s your budget?
Answering these questions will help clarify your organization’s needs and readiness for implementation.
From there, it becomes much easier to identify the right system.
Now, here’s a simple rule of thumb:
EAM systems are generally better suited for larger, asset-heavy organizations.
Such companies often have complex asset management requirements and a greater need for integration across business functions, both of which an EAM system can easily address.
They typically have the budget to support the software investment and associated training.
However, if your primary focus is maintenance, EAM software might be overkill.
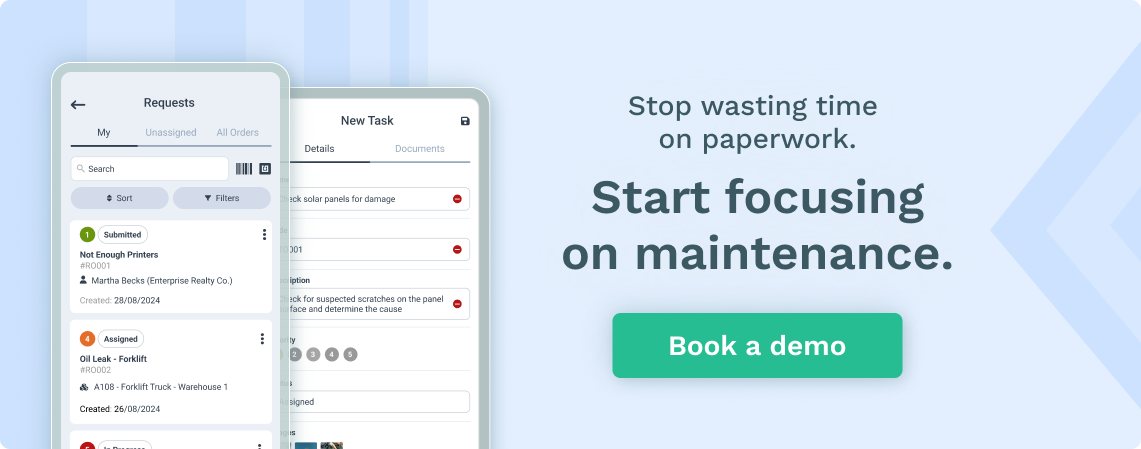
The survey by the Institution of Mechanical Engineers we mentioned earlier found that only 22% of maintenance professionals currently use EAM systems—down from 39% the year before.

One possible reason for this decline is the growing popularity of CMMS platforms, which are purpose-built for maintenance and often offer stronger features.
So, who should choose a CMMS?
Typically, a CMMS is used by small to mid-sized organizations that want to automate workflows, implement proactive maintenance, and minimize downtime—all in a simple, cost-effective way.
Take our own CMMS solution, WorkTrek, for example.
It replaces outdated tools like spreadsheets with a centralized, easy-to-use system used by maintenance professionals across industries.
As a result, mistakes are minimized, and maintenance efficiency is significantly improved.
Just ask Matjaž Valenčič, Operations and Maintenance Manager at interEnergo, an international Ljubljana-based energy company.
He has firsthand experience with WorkTrek:

If Matjaž’s story sounds familiar, then a CMMS like WorkTrek might be what you’re looking for.
It’s simpler and more affordable than an EAM system, yet powerful enough to transform your maintenance operations.
But don’t just take our word for it.
Instead, take advantage of WorkTrek’s free trial and explore all its features firsthand.
That way, you and your team can see how well it fits into your daily operations and decide based on experience.
Because, at the end of the day, whether you choose an EAM or a CMMS, the right solution should align with your needs and work for you—not the other way around.
Conclusion
Choosing between CMMS and EAM software isn’t just a technology decision.
It’s an opportunity to eliminate outdated workflows, streamline operations, reduce stress, and boost your asset ROI.
So, take the time to research your options thoroughly.
Don’t forget to ask for free trials or demos, read real user reviews, and see these tools in action.
The more informed you are, the more confident you’ll be in selecting the right solution for your team.