Get a Free WorkTrek Demo
Let's show you how WorkTrek can help you optimize your maintenance operation.
Try for freeIntroduction
It’s no secret that maintenance departments are often overloaded and tedious. Manual processes simply cannot keep up with today’s rapidly evolving and increasingly technology-driven organizations. That’s why many companies, large and small, are turning to computerized maintenance management software (CMMS) to streamline processes, increase efficiency, and reduce maintenance costs. While a CMMS is a very useful tool for maintenance managers, it can become less effective if common mistakes are ignored.
Preventative Maintenance Mistakes You Shouldn’t Ignore
Preventative maintenance: Companies continue to invest in tools that help them perform routine maintenance to improve equipment performance, reliability and cost-effectiveness. In order for equipment to maintain optimal performance and avoid unnecessary breakdowns, it is important to perform routine maintenance to improve equipment reliability. It’s important to have maintenance management tools like CMMS software to help you plan and manage preventive maintenance and monitor performance.
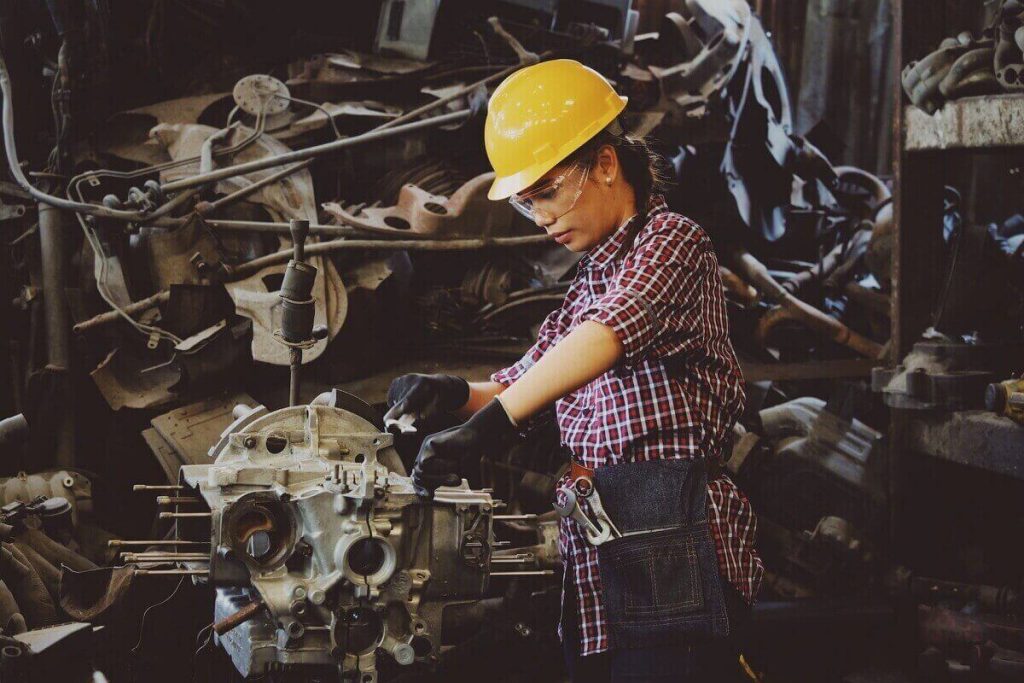
Establish maintenance standards
If standard procedures and schedules for preventive maintenance or performance measurements are not established, equipment can fail quickly. Repairs can cost more than ongoing preventive maintenance and can cause significant disruption to business operations.
Set appropriate scheduled maintenance frequency to optimize equipment performance, reliability and longevity. Since every business’s maintenance needs are different, you’ll want to develop a preventive maintenance program that’s right for your business.
Unable to track PM information
Missing important information from your PM plan can lead to major disasters. If you don’t track
all the important information for all your devices, you’ll have limited visibility into your device’s performance. Tracking the percentage of PM tasks completed, the number of downtimes that occurred, or the number of times certain equipment had to be repaired is valuable information for improving your preventive maintenance program.
No preventive maintenance checklist
Forgetting to perform certain maintenance tasks can result in significant downtime. Creating a checklist and attaching it to a work order ensures that all tasks are completed to the required specifications. You should also obtain the signature of the person responsible for tasks that could be hazardous if omitted.
Eliminate equipment from PM plans
Ignoring equipment that is located elsewhere or does not seem important enough when setting up a PM plan can have a significant impact on your business. PM should plan for all equipment, support and infrastructure resources. Failure to include plant support equipment in the PM program can result in downtime and significant operational disruption.
Instructions not clearly defined
Working in reactive mode may result in directives being omitted or poorly defined. PM tasks should be clearly explained and contain as much detail as possible. For example, what is the condition of the equipment, what issues need to be looked for, and what should they do if the equipment is not in ideal condition. Ensuring they have access to all historical repair information, manuals, drawings or other additional information will speed up the repair process.
Buy spare parts before you need them
If parts sit on the shelf for a long time and you don’t have the right parts in stock, it can cost you a lot of money. For proper inventory management, you need to create a plan to inspect all spare parts and create a classification, such as critical and non-critical. The categories you set today may change at any time. Review repair history and identify hard-to-find or very expensive parts so you can find the right part when you really need it. Eliminate parts that are no longer used because you no longer own the equipment and it takes up a lot of warehouse space.
Poor communication among employees
One of the main issues in maintenance management is getting your team to engage, accept and encourage less enthusiastic team members. A preventive maintenance program is the first step to operating your facility more efficiently, minimizing downtime and reducing maintenance costs.
What good is a preventive maintenance program if your team doesn’t fully understand the program and isn’t trained to perform the procedures and tasks necessary for the program to be successful?
Whether it’s training employees how to use new technology to track planned repairs, or training them on what, when and how to do something, a properly informed and trained workforce will ensure the success of your preventive maintenance program?
The effectiveness of your PM program is not tracked
Neglecting the effectiveness of a PM program is a recipe for disaster. To fully understand whether your preventive maintenance program is meeting or falling short of expectations, you must measure it.
Properly tracking your PM program can improve return on investment (ROI).
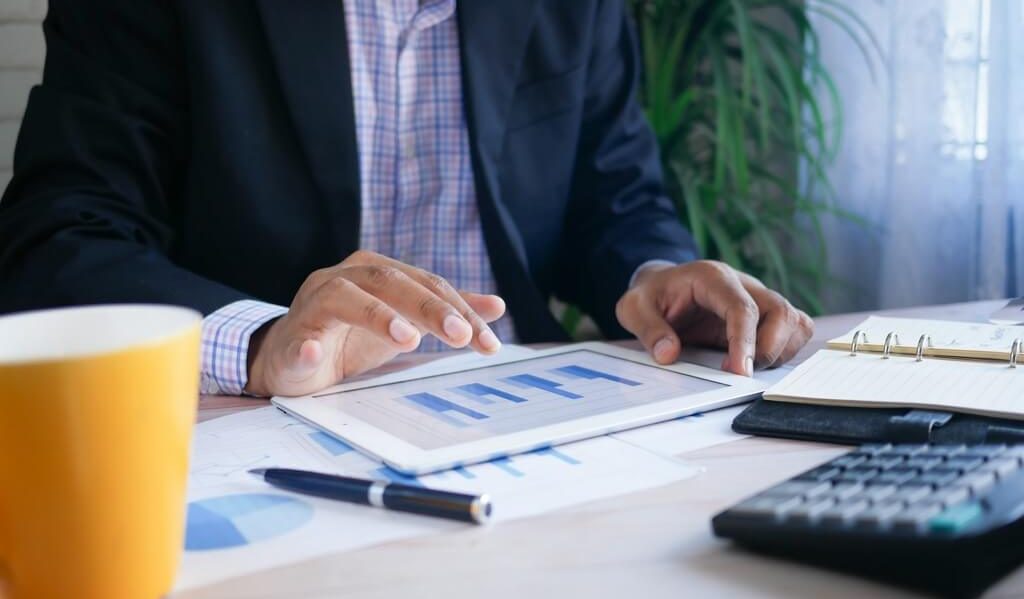
5 Mistakes to Avoid When Buying CMMS Software
Use these five points to ask questions now that will contribute to the success of your CMMS implementation later.
Scalability: Scalability means that the CMMS software can accommodate changes in size or volume as your needs change. This could mean something as simple as adding user licenses, or it could mean something more complex like adding advanced features or upgrading to meet new business needs.
Compatibility: Maintenance managers often need to share maintenance data with their organization’s systems of record. CMMS software’s compatibility with external applications means you don’t have to worry about manually reformatting large amounts of data to meet the needs of other systems.
Customization and modifications: It’s important to be able to customize certain things so that your CMMS software meets your business needs. Make sure you can customize the layout, add custom fields, create nested fields, and link custom prompts to suit your needs.
Mobile devices: If you haven’t started using mobile devices in your maintenance work, you probably will soon. Look for CMMS software with an adaptive interface so that your maintenance team can easily access it no matter what device they use (desktop, tablet, or mobile phone).
Data accessibility: When properly integrated, a modern CMMS can use data from virtually any source to power its alerts, alerts, and reports. Make sure your CMMS software can track the data your users need and create custom reports based on the information you and company managers need to know.
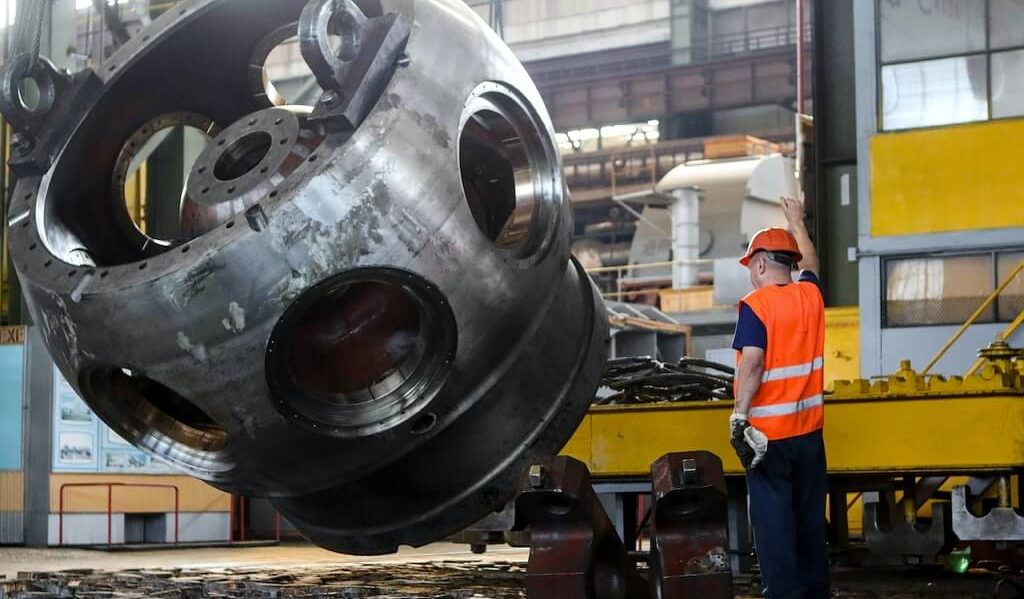
The Most Common Mistakes When Investing in CMMS
Roles and benefits
For many managers, the misconceptions and mistakes surrounding CMMS don’t start with choosing the wrong software. They often start with a fundamental misunderstanding of the purpose and role of a CMMS.
The biggest misconception is the belief that a CMMS or other technology can solve problems that are actually underlying process or leadership issues. For example, if a company has no real direction in terms of maintenance capabilities—how it wants to do things, what its maintenance philosophy is—adding a tool on top of that isn’t going to solve the problem. This is a leadership challenge that needs to be addressed.
This misunderstanding occurs because managers have not kept pace with advances in CMMS features, functionality, and potential benefits to their departments.
They view a CMMS as a tool that helps them track work orders, maintain asset history, and manage inventory. But when you look at the overall scope of what they want to accomplish as a facilities plan, the system should have more capabilities to automate the process and enable the team to collect data as efficiently as possible so they can drive business decisions.
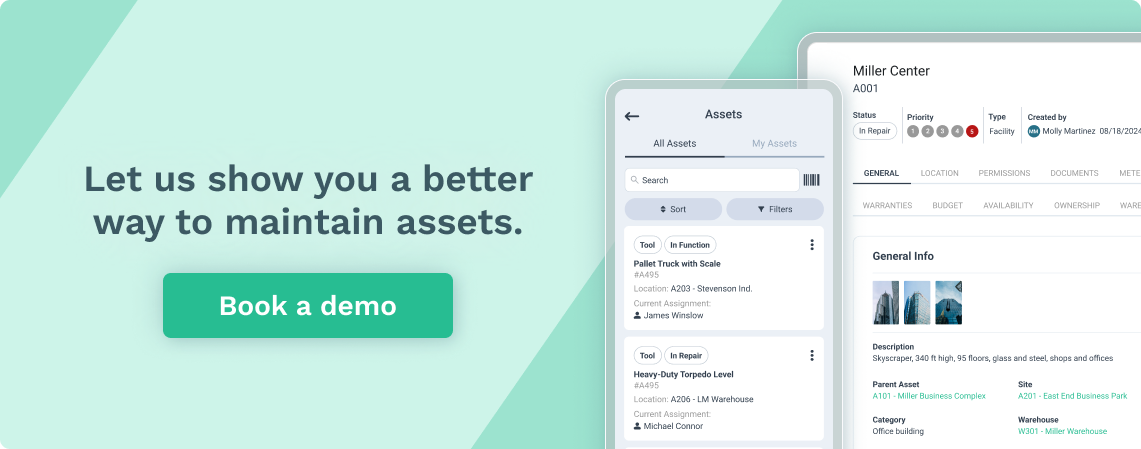
Perhaps the easiest misconception to understand is that a CMMS is a business tool and not just designed to help you manage your daily life. CMMS are typically limited to supporting work order management. It will do that, but it also needs to do more.
Make a Choice
These incorrect assumptions about the role and feature of a CMMS lay the foundation for errors. These errors initially occur when selecting a CMMS.
They start shopping before they know what they want. There are many great products out there, and managers may end up choosing a product or software that excels in some areas but lacks some key features they really need. Advise to customers is to discuss what they want the system to do now and in the future before purchasing. Set a vision, develop an action plan, and use it to formulate your specifications and requirements.
Managers who understand what a CMMS should do for their departments have a better chance of selecting software that meets those needs. Those who don’t often end up with substandard products.
We encounter some issues when companies are unhappy with the CMMS they choose. People go back to the first misconception that a CMMS solves process or leadership problems. If an organization does not clearly define its needs or search for a CMMS, there is a risk of not getting one that meets its actual goals.
Managers who don’t understand their department’s needs before starting the CMMS process may make the mistake of relying on a software vendor to fill gaps in needs and expectations.
The second mistake is to simply say they need a CMMS and then ask for a product demo. Vendors will come in and talk about the power of all these different products and show them all the bells and whistles and the amazing things their software can do. But again, if you don’t have the process in place and don’t understand your needs, it will be difficult to decide on a solution. Ultimately, the choice is based on who delivers the best demo, not the software they actually need.
Data Input, Data Output
A key function of a selected CMMS is to provide managers with critical information about asset health and technician productivity. This information can help managers make decisions on everything from staffing and engineering priorities to budgeting and resource allocation. Unfortunately, mistakes early in the CMMS process can have consequences that impact this functionality.
For example, when determining departmental needs, managers often make mistakes in the way the CMMS captures, stores, and accesses maintenance activity data. The result is that the database fails to provide managers with the information they need.
You need standardized terminology. „What do we call our places? How do we label our assets? Make sure you define this criterion. So how much of the data set we have now meets this standard? How accurate is this information?“
Managers also make the mistake of not identifying goals and requirements early in the CMMS process.
This is something we see all the time, even in very mature organizations that have deployed a CMMS and been using it for a long time. They sometimes default to generating data from CMMS reports that can simply be pulled from the machine, rather than reports that actually help them manage the data.
It comes back to the issue of planning and establishing clear goals and outcomes that the company hopes to achieve with its maintenance program, and deciding how to measure those outcomes, whether that’s customer satisfaction or renovation completion rates.
Perhaps the most costly mistake managers make when selecting and implementing a new or updated CMMS is underestimating the time and effort required to do the hard work early on, and the problems this decision creates for everyone involved in the process.
You need to know what you’re looking for, what decision you want to make, how the data affects it, and how to configure the software. This becomes one of the requirements in your requirements statement and doesn’t begin until your process is understood.
Before purchasing software, an organization should define what it wants from the software.
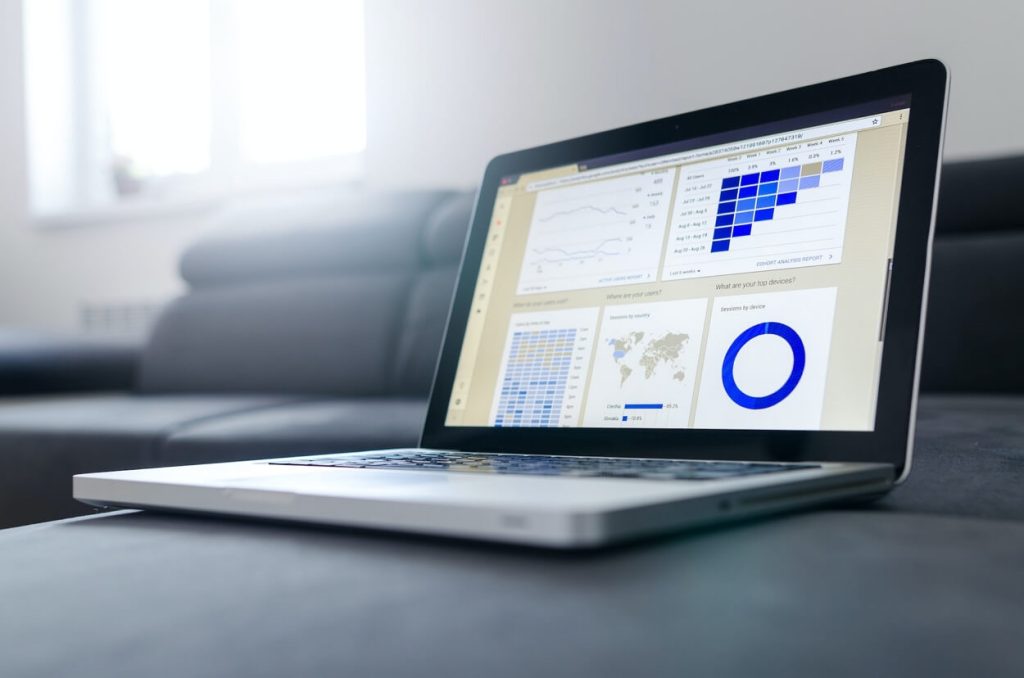
Common Mistakes in CMMS Implementation
By identifying and avoiding these mistakes, companies can ensure successful integration of a CMMS into their operations.
Insufficient planning
One of the most common mistakes when implementing a CMMS is starting the journey without clearly defined goals and objectives. This can create risks by causing companies to invest time and resources without a clear endpoint. To avoid this, companies need to explain what they hope to achieve with a CMMS, such as reducing costs, improving asset performance, or increasing maintenance efficiency.
Implementing a CMMS requires significant resources, and organizations that don’t devote enough resources to the project may find themselves overwhelmed. To avoid this mistake, a careful resource allocation plan should be developed. This includes budget allocations, human resources, and timelines.
Not all organizations are equally prepared for CMMS implementation. Failure to assess a company’s readiness for this technological change can lead to resistance and inefficiency. A proper readiness assessment should consider factors such as employee training, IT infrastructure, and change management strategies.
Ignoring data accuracy
Accurate data forms the basis for the operation of a Computerized Maintenance Management System (CMMS). Neglecting data cleansing and validation before migrating data to a CMMS can lead to poor decisions and wasted resources. Therefore, regular data cleaning and validation protocols must be established to maintain data integrity.
In addition to cleaning existing data, it is also important to integrate accurate data sources into the CMMS. This includes data collected by devices, sensors, and other Internet of Things (IoT) devices. Accurate data is critical for real-time monitoring and predictive maintenance.
Data is dynamic and requires ongoing maintenance to ensure its accuracy. Failure to establish regular data maintenance procedures is a major danger. To prevent data degradation, companies should implement data governance practices, define ownership, and establish a data maintenance plan.
Consider user training
The effective use of a CMMS system depends largely on the users who interact with it. Neglecting user training may prove to be a serious mistake. Therefore, companies must design comprehensive training programs that provide employees with the skills they need to effectively navigate and use a CMMS.
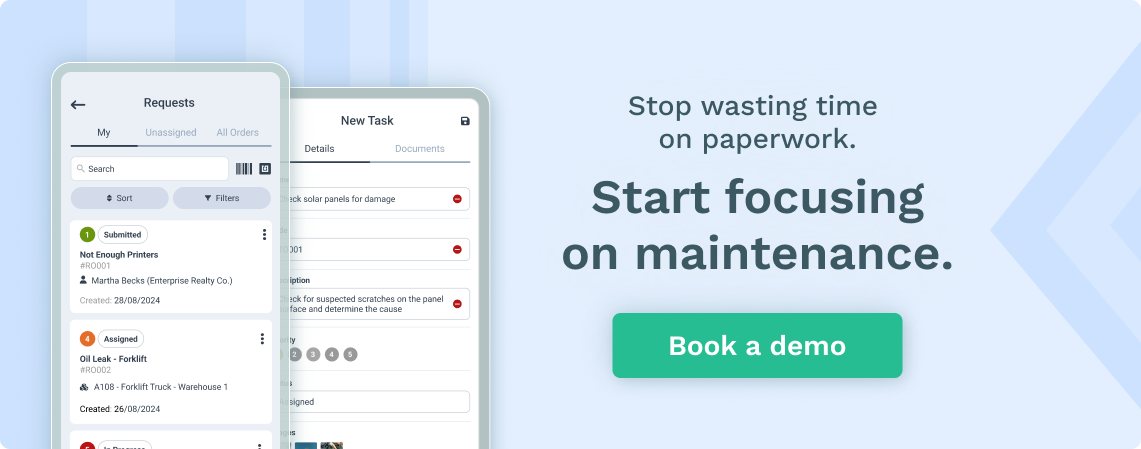
Another important aspect that is often overlooked is user engagement. It is important to encourage employees to provide feedback on the usability of the CMMS and make suggestions for improvements. This ongoing commitment can lead to a more user-friendly system that meets the needs of the organization.
Best CMMS systems often evolve, and as new features and updates are rolled out, employees may require additional training. To avoid this mistake, companies should provide ongoing training and support to ensure users are familiar with the system and stay up to date.
Ignore change management
Resistance to change can be a significant barrier to implementing a CMMS. Employees may resist adopting a new system because they fear change or feel uncomfortable. It is critical to recognize this resistance and address it through effective change management strategies.
Implementing an effective change management strategy requires clear communication, involving employees in decisions and addressing their concerns. Changes should be introduced gradually, with a focus on demonstrating the benefits of a CMMS to employees.
To ensure a smooth transition, it is important to align the CMMS system with the culture and values of the organization. Ignoring this consistency can lead to a sense of disharmony among employees. Therefore, it is important to ensure that the CMMS supports the overall mission and goals of the organization.
Choosing the wrong CMMS solution
Choosing a CMMS solution that isn’t right for your company’s specific needs can be a costly mistake. Therefore, companies must conduct a thorough needs analysis and evaluate potential CMMS options to find the most suitable solution.
The supplier selection process is equally important. Choosing an unreliable or inappropriate CMMS provider can lead to problems down the road. Therefore, thorough due diligence and background checks are crucial when choosing a trustworthy provider.
As businesses change and grow over time, they should choose CMMS software that is adaptable and scalable. Systems that fail to evolve as business needs change may become obsolete, resulting in further investment and trouble.
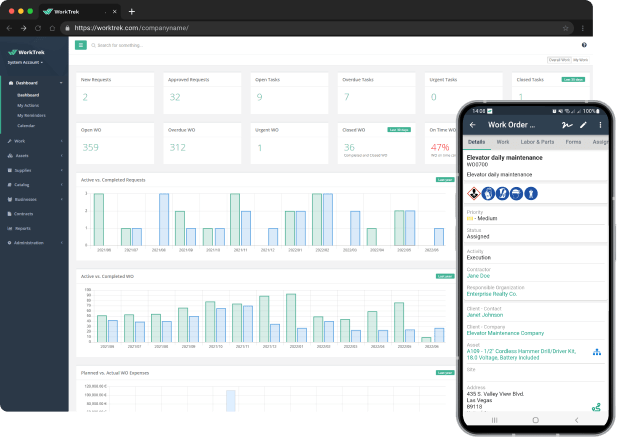
Common Mistakes Companies Often Make when Using a CMMS
Improper use of CMMS software
When used correctly, a CMMS system is an extremely valuable tool. Using a CMMS can have a positive impact on asset management and maintenance planning and reduce costs. But if staff do not use it correctly due to negligence or lack of knowledge, various problems can arise.
We often see errors caused by CMMS users, such as forgetting to enter data, entering inconsistent data, or not performing ongoing inventory maintenance checks recommended by the CMMS system.
These seemingly small user errors can lead to larger problems that cost the company time and money, especially in a tightly coupled CMMS. Always remember that a CMMS system is not just about the software itself, but also about how users provide data to the system and use the information provided.
Implementation and training compromises
Another common mistake is entrusting CMMS system setup to someone with little or no maintenance knowledge or CMMS implementation experience. This task should be assigned to an individual or team with a high level of knowledge that enables them to evaluate the entire asset inventory and configure the correct support for each asset.
Lack of proper CMMS training and preparation for all maintenance team members can also lead to many problems. If team members don’t receive clear instructions, they’re likely to use their own methods when using the software, resulting in a confusing and confusing inventory of asset data.
Task management error
Some supervisors may not be able to assign specific roles to each member of the maintenance management team, or may not properly define the expectations and requirements for these roles. Make sure these definitions are clearly spelled out in your CMMS to avoid confusion about who does what when, which can lead to costly mistakes.
In addition, it is important to ensure that middle and senior managers understand and are able to use the CMMS. This ensures that asset management tasks are properly delegated and each team member is accountable for their role in the process.
Lack of implementation time and resources
The more assets you have, the more resources and time you have to devote to maintenance. Maintenance management should be an ongoing process, which means team members must devote significant time each month, week, or even day to ensure smooth operations. In this way, organizations can help ensure that all maintenance objectives are met, helping to drive rather than hinder the organization’s success.
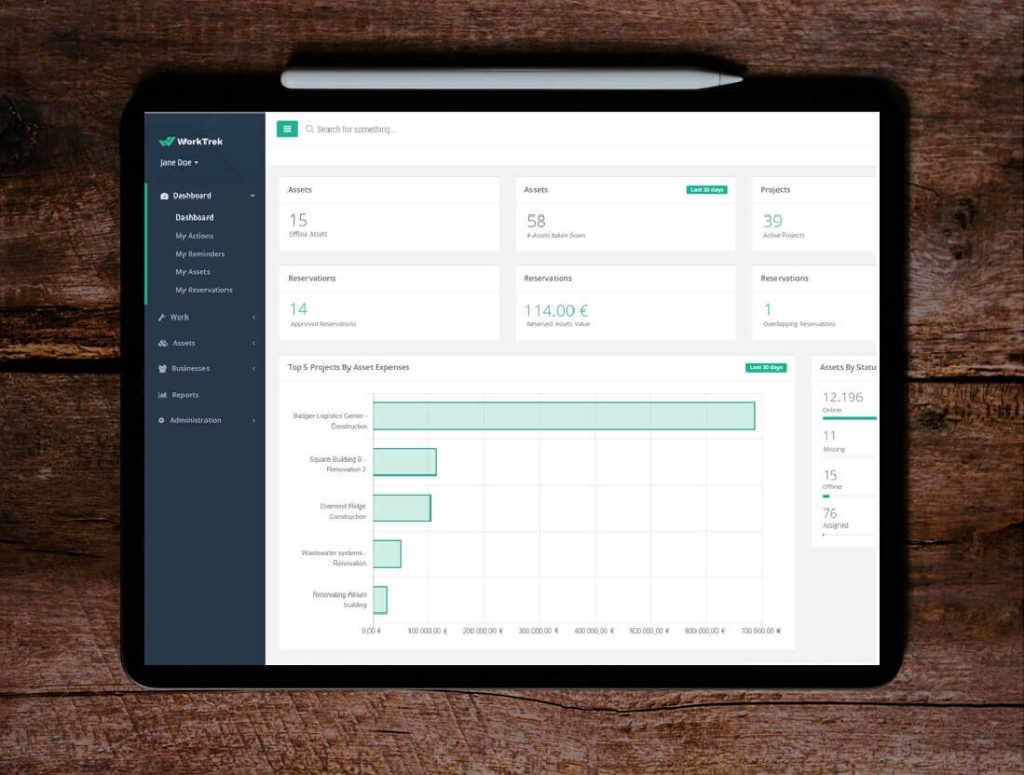
Conclusion
CMMS errors can hinder the successful implementation and use of the system and result in missed opportunities for efficiency gains and cost savings. By avoiding these common mistakes, companies can avoid pitfalls and realize the true potential of a CMMS in asset maintenance. With WorkTrek CMMS, companies can overcome these challenges and benefit from optimized maintenance processes, increased equipment reliability and overall efficiency.