Get a Free WorkTrek Demo
Let's show you how WorkTrek can help you optimize your maintenance operation.
Try for freeYou are probably wondering, how to reduce downtime with CMMS? There is no time for downtime. In this context, the old adage “time is money” is even more relevant. The efficient and effective operation of your facility depends on the maintenance management and services you provide. Introducing the latest technology to your facility and team requires a steep learning curve, but the benefits in terms of reduced troubleshooting are especially huge.
What Is Downtime?
Downtime is an unplanned stop in production. It disrupts operations and can have a significant impact on profits. If not activated, it can negatively impact labor efficiency, inventory planning, cycle times, and lead times.
Since planned outages such as software and hardware upgrades and preventive maintenance are part of regular operations, they are not usually considered “downtime”.
What Does CMMS Mean?
The CMMS (meaning Computer Aided Maintenance Management) improves the management of service by improving the sharing of information and by facilitating the daily life of technicians in their tasks.
The CMMS will help you manage your service. For example by improving the management of what already exists. That is to say, improve the availability of the equipment and the team by creating schedules for example.
In addition to availability management, you can extend the life of the equipment and improve safety through preventive management.
Finally, it is also possible to manage the history and costs of your service, by tracing and archiving its various actions, but also by controlling the various costs related to it.
To sum up, computer-assisted maintenance management will allow you to manage your entire service to improve and optimize its results and monitoring.
What Is CMMS Used For?
CMMS works by tracking and managing data related to maintenance activities. This data can be used to improve the quality of an organization’s services.
Using a CMMS has many benefits, including:
Improving the quality of service: By monitoring and managing data relating to maintenance activities, CMMS can help organizations improve the quality of their services. This improvement in service quality can lead to greater customer satisfaction.
Reduced downtime: By streamlining and optimizing an organization’s maintenance operations, CMMS can help reduce downtime. This reduction in downtime can lead to increased productivity and lower costs.
Increased productivity: By reducing downtime and improving the quality of a company’s services, CMMS can help increase productivity. This increased productivity can lead to increased profits
Reduced maintenance costs: By streamlining and optimizing an organization’s maintenance operations, CMMS can help reduce maintenance costs. This reduction in costs can lead to increased profits.
Accurate Industrial Maintenance Tracking: CMMS can help organizations track their maintenance activities accurately. This accurate tracking can help improve decision-making and enable better planning.
To be more precise, let us take as a concrete case the technical services (of a company or a municipality).
In this case, CMMS software allows you to:
- Manage teams and stock
- Manage staff (availability, cost)
- Manage interventions (plan, execute)
- Manage the transmission of information
- Manage the budget (labor, stocks, purchase…)
Downtime Type
Not all downtime is terrible. In other words, sometimes companies use downtime as a means to an end. Extend the useful life of assets or otherwise help businesses increase productivity.
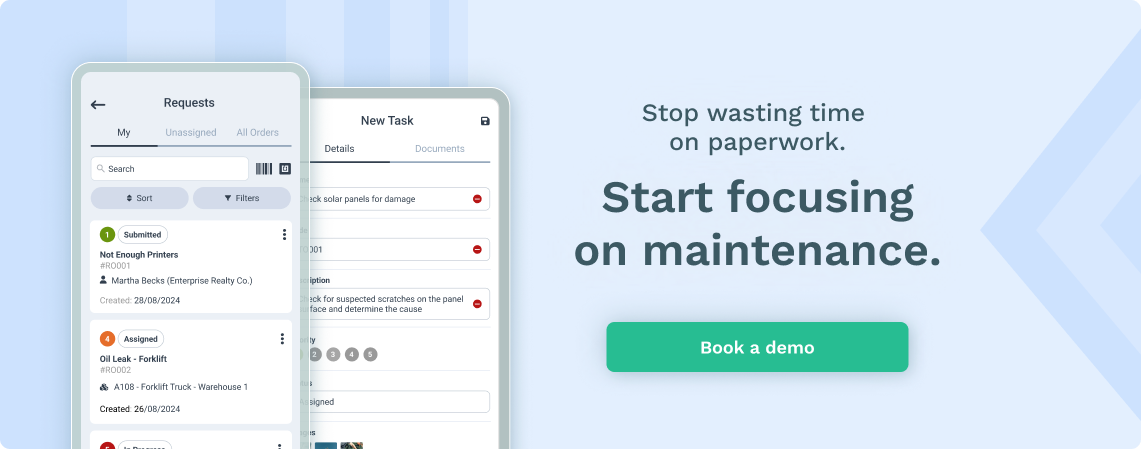
We can distinguish between two types of downtime based on the expectation that the downtime will occur and its cause. Each element is described in detail below.
Planned Downtime
As the name suggests, planned downtime is calculated in advance and incorporated into the regular operations of a company. It can also be called “quiet time”.
For example, if the last worker shuts down a production facility for a day and all machines are shut down, it is a planned downtime. The device rests overnight and restarts in the morning.
However, planned downtime also includes times when you intend to shut down equipment. This includes situations where machine components require oil changes, repairs, inspections, etc.
So sometimes this downtime can do a lot of good for a company. On the one hand, the service life of the system can be extended, directly increasing productivity.
Unexpected Downtime
This downtime is the flip side of the coin – downtime that doesn’t add value to the business. Of course, since this was a sudden outage, meaning the company didn’t anticipate or plan for it, there were unavoidable costs.
Equipment failures fall into this category. Furthermore, unplanned downtime means not only costs associated with damaged machinery but costs as well. In most cases, these are allegations of personal injury and environmental incidents.
What Are The Causes Of Unplanned Downtime?
You can think of disruptions as the result of your assets sliding down the KPI curve. This means there are many points along the way where you can spot early warning signs, plan quick and easy fixes, and avoid downtime altogether.
What you need is a series of planned inspections and tasks that allow the maintenance department to regularly spot and fix small problems before they have had enough time and oversight to develop into major problems.
What you need is a preventive maintenance plan, and we can accept that fact and say that one of the causes of unplanned downtime is a lack of preventive maintenance.
But that’s not the only reason for downtime. In fact, the best PM programs in the world are no match for crippling operator errors. It doesn’t matter how perfectly the production line runs if the operators can’t get it right. You can have a perfectly tuned engine and manual transmission, but it won’t last long if the driver is constantly changing gears without using the clutch.
Here’s another cause of downtime: operator error.
Other reasons include poor quality MRO inventory and poor or non-existent standard operating procedures for maintenance technicians. Assets fail when teams use bad parts and misuse parts.
Preventive Maintenance Can Save You A Lot Of Trouble!
First of all, the CMMS is the ideal tool for planning preventive maintenance operations. And this, in an efficient way and avoid unforeseen breakdowns. By maintaining your equipment regularly, you significantly reduce the risk of downtime. In addition, you prolong their lifespan. No more unexpected breakdowns, you can say goodbye to moments of stress and panic!
That’s not all! By planning your interventions with the CMMS, you also avoid many unnecessary costs. With a solid preventive maintenance plan, you reduce the risk of breakdowns or production stoppages. This is what can have a significant impact on your bottom line. As you will have understood, the CMMS is the ideal ally to optimize the management of your maintenance.
Of course, the safety of all users is also a priority. So don’t forget to take this crucial aspect into account in your maintenance planning. In short, CMMS is the secret to reducing downtime and maintenance costs while ensuring the safety of your equipment and employees.
Strategies for using preventive maintenance:
Create a preventive maintenance plan – A regular preventive maintenance program forms the backbone of any preventive maintenance program. However, this schedule should not be developed in isolation but should take into account various factors that affect the overall performance and life of the equipment. By creating a preventive maintenance plan, you can create a clear schedule for maintenance activities, ensuring that all required tasks are performed at the correct time. Not only does this help prevent equipment failure and downtime, it also extends the life and performance of the equipment.
Implement predictive maintenance – While preventive maintenance helps mitigate potential issues before they fail, it may not be enough to completely reduce downtime. This is where predictive maintenance (PdM) comes into play.
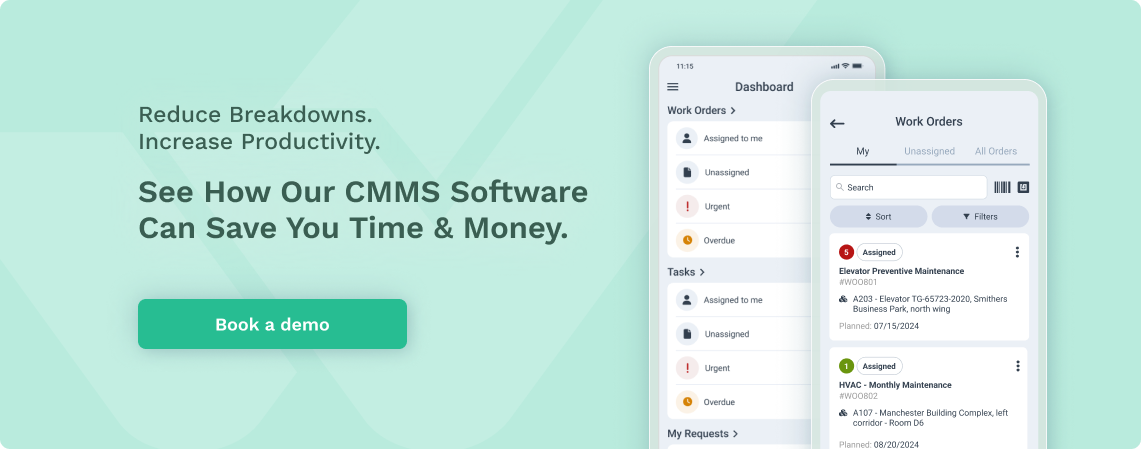
By implementing predictive maintenance, you can ensure that maintenance is only performed when needed, reducing unnecessary downtime and the costs associated with unnecessary maintenance.
Train your maintenance team – To minimize downtime, a well-trained maintenance team is essential. They are the first line of defense against equipment failure, and the faster they can identify and fix problems, the less downtime you will have. A well-trained maintenance team can significantly reduce the time it takes to resolve issues and get your operations back on track, reducing downtime.
Using CMMS (Computerized Maintenance Management System) – Computerized Maintenance Management Systems help companies streamline maintenance processes and minimize downtime. They help with all aspects of maintenance such as: work order management, asset tracking, and preventative maintenance planning. Implementing a CMMS can significantly reduce downtime by streamlining maintenance processes and improving communication and coordination within maintenance teams and other departments.
Regularly review and update your maintenance plan – Over time, even the best maintenance plan can become obsolete. Regularly reviewing and updating your maintenance plan is essential to ensure it remains effective and downtime is minimized. By regularly reviewing and updating your maintenance plan, you can ensure that it is effective in minimizing downtime as your operation evolves and grows.
Corrective Maintenance: An Essential Solution To Solve Problems
Sometimes, despite preventive maintenance, equipment fails, for one reason or another. In this case, too, the CMMS allows you to manage corrective maintenance interventions effectively. When a piece of equipment breaks down, you can quickly open a maintenance request in your CMMS tool, like on WorkTrek for example. The software allows you to follow the progress of the intervention, and its degree of urgency, and to make sure that the repairs are carried out within the time allowed. And hope, we know instantly when the breakdown is repaired!
By using the CMMS to manage corrective maintenance interventions, you have control of your budget and you reduce, again, the downtime of your equipment, whatever it may be. Whether you call on a service provider or your maintenance agent directs the repair, the follow-up is done on your CMMS software.
In addition, the CMMS allows you to track maintenance costs. You can easily see how much you spend on maintenance and identify which equipment needs the most maintenance. By using this information, you can make informed decisions about future investments and ensure that you allocate the necessary resources to the equipment that needs them most. And yes, we know, money is the sinews of war!
How Can A CMMS Help You Reduce Downtime?
One of the biggest challenges of modern maintenance management is data. You need to find ways to capture them, keep them safe and up-to-date, share them, and turn them into actionable insights.
This is all very difficult, basically impossible, with paper and spreadsheets. Because you’re relying on everyone to manually enter data, you’re bound to make mistakes. Even if you can get perfect data, you can’t share it directly. They might have all the correct numbers, but if they’re stuck on a piece of paper or a spreadsheet in the office, they’re useless to the team.
Modern CMMS solutions make your life easier. All your data is stored in a central database, so you can be sure it is correct and accessible. Everyone works with the same data sets, and everyone has instant access from any internet-connected device.
This software solution allows you to set up, schedule, and track PMs. Once you have enough data, you can use automatically generated reports to calculate key metrics and KPIs, giving insight into how your team handles errors and how to improve.
No Downtime
Achieving zero downtime is the ultimate goal in many industries, especially manufacturing. While avoiding downtime due to unavoidable events may not be realistic, organizations can significantly reduce downtime with CMMS through proactive strategies and the use of advanced technology. Here are some steps to help minimize downtime:
- Implement preventive maintenance – To minimize unplanned breakdowns, a sound preventative maintenance strategy is essential. This includes scheduling maintenance tasks based on how long the equipment is running or at intervals to ensure machines are repaired before potential failures occur.
- Use predictive maintenance – Predictive maintenance uses technologies such as IoT and artificial intelligence to monitor equipment performance in real-time and predict when downtime is likely to occur. By identifying potential problems early, repairs can be scheduled during off-peak hours to avoid production disruptions.
- Use condition-based maintenance – This includes monitoring the physical condition of the facility to determine what maintenance needs to be done. Condition monitoring tools such as vibration analysis, thermal imaging, and oil analysis can provide real-time insight into machine health.
- Invest in maintenance management software – Maintenance management software like Cryoto’s CMMS can dramatically improve maintenance planning, track asset performance, manage spare parts inventory, and provide insightful reporting that can help reduce downtime.
- Maintain a well-managed parts inventory – Having the spare parts you need when you need them is crucial. An efficient parts management system ensures parts are available for scheduled maintenance or unexpected repairs, preventing extended downtime.
- Provide regular training – Equipment operators should be well-trained to recognize early signs of potential problems. Trained personnel can help spot problems before they lead to equipment failure.
- Regularly review and improve your maintenance processes – To approach zero downtime, a continuous improvement approach is essential. Review your maintenance procedures regularly, learn from your mistakes, and make necessary adjustments.
Remember that balance is important when striving for zero downtime. Excessive maintenance is costly and counterproductive. The goal should be to simplify the maintenance process and minimize downtime without incurring excessive costs. Implementing predictive and preventive maintenance strategies based on real-time data and analytics is critical.
In conclusion, CMMS is a valuable tool for reducing downtime and maintenance costs. Planning preventive maintenance operations and managing corrective maintenance interventions, it allows you to reduce your maintenance costs. By following these, you can improve your business performance and save money.