Get a Free WorkTrek Demo
Let's show you how WorkTrek can help you optimize your maintenance operation.
Try for freeKey Takeaways:
- 78% of manufacturers have experienced downtime due to a lack of spare parts.
- Maintenance technicians reveal that trial and error often replace formal training.
- Proper asset maintenance depends on communication across multiple departments.
- Using IoT sensors to monitor asset behavior helps plan maintenance.
Asset maintenance can be challenging.
It is a complex process involving tasks such as tracking spare parts, managing unplanned downtime, and coordinating between maintenance and operations.
However, there are proven ways to improve that process and reduce asset downtime, save costs, and extend the assets’ lifespan at the same time.
Take a few minutes to learn how to reap these benefits yourself.
Maintain an Updated Asset List
To optimize asset performance, you must first know what assets you have, where they are located, how they are functioning, and their lifecycle stage.
In other words, you need to maintain an asset list with all the details about each asset, including:
- expenses
- warranties
- serial numbers
- asset locations
- OEM recommendations
- maintenance history records
If you can track this asset information, you’re already ahead in avoiding operational inefficiencies.
Naturally, the key here is ensuring this detailed asset list is always up-to-date.
That’s why it’s necessary to regularly audit your inventory and update asset information, such as when it was last serviced, which parts may be nearing the end of their lifespan, and where each asset is located.
With this level of detail, you can prioritize maintenance tasks and allocate resources more effectively, so you don’t waste time or money unnecessarily.
But the real challenge arises from managing this data, especially if it’s done manually.
Paper records and spreadsheets become inefficient and error-prone as asset numbers grow.
The solution is to digitalize this process and use a computerized maintenance management system (CMMS).
Rodrigo Pires, Maintenance Coordinator at Vale, a global mining company, agrees:
One such robust and structured solution is our CMMS software—WorkTrek.
With WorkTrek, you can track complete asset metadata, including physical location, custom fields, warranty, maintenance history, expenses, and more.
And you can do it all through a single platform available on desktop, tablet, and mobile devices.
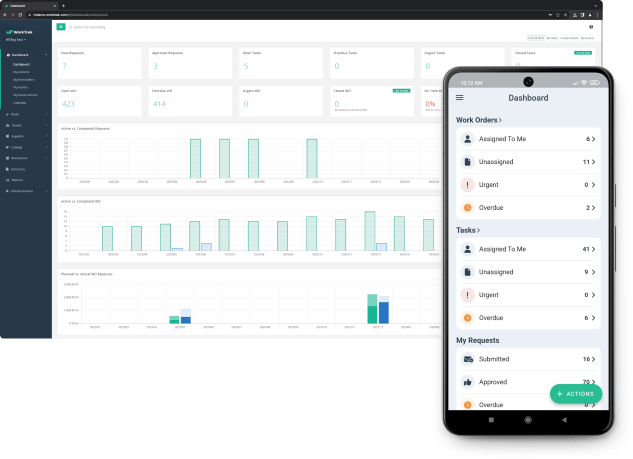
You can also organize assets by location and create unlimited asset hierarchies.
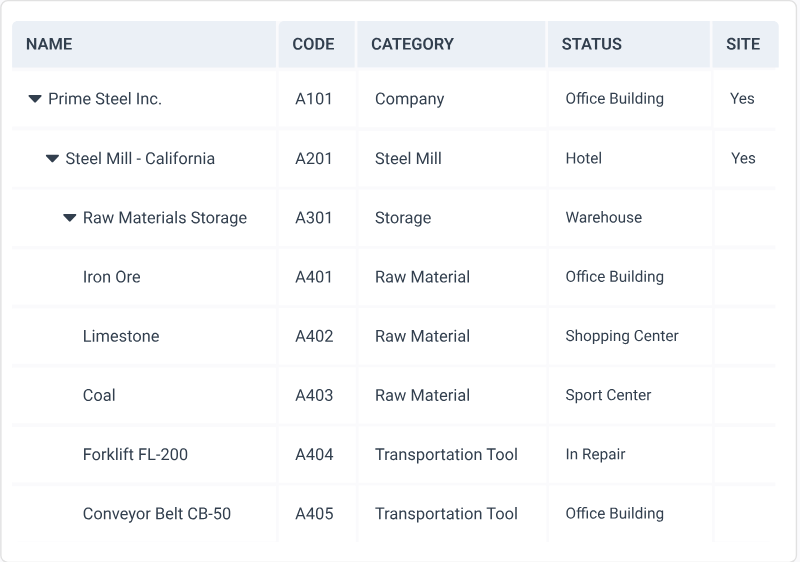
This ensures that every detail about every asset is right where it needs to be.
Say you have a critical piece of equipment nearing the end of its warranty period.
Since you have this information at your fingertips, you can plan for any repairs or parts replacements before the warranty expires.
On top of that, with WorkTrek, you can use barcode or QR code labels for easier asset identification.
A technician in the field can scan the code with their mobile device, instantly pulling up all the asset details, related work orders, and tasks.
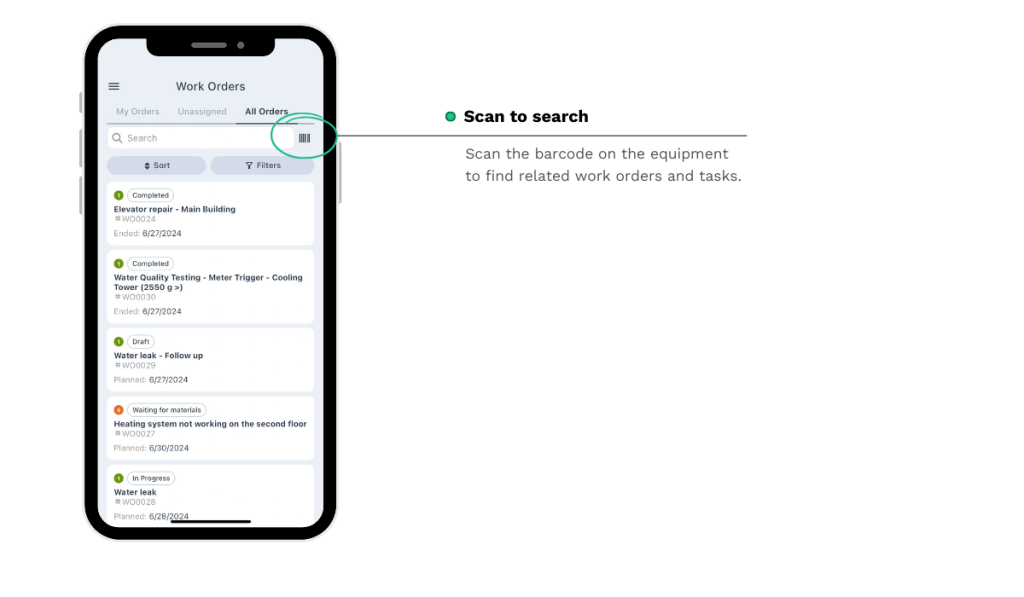
This way, maintenance technicians have the most accurate and up-to-date information.
In short, the first key step to better maintenance is having an organized, real-time view of your assets.
And the easiest way to get it is with a robust CMMS.
Centralize Spare Parts Inventory Management
There is no more disruptive scenario than when equipment breaks down, and you don’t have a spare part readily available.
This leads to very costly downtime, as confirmed by research.
According to Siemens, the cost of a lost hour now ranges from $39,000 in factories producing fast-moving consumer goods to more than $2,000,000 per hour in the automotive industry.
And this happens primarily due to a lack of spares.
One study from 2022 found that 78% of manufacturers had experienced a shutdown or line stoppage precisely due to that reason.
Conversely, overstocking spare parts is also a problem because it ties up capital, consumes space, and risks obsolescence.
The key is finding the right balance.
To be able to do that, you first need to centralize spare parts inventory management.
You can achieve that with a CMMS.
With a good system, you can track spare parts by assigning barcodes or QR codes to each part.
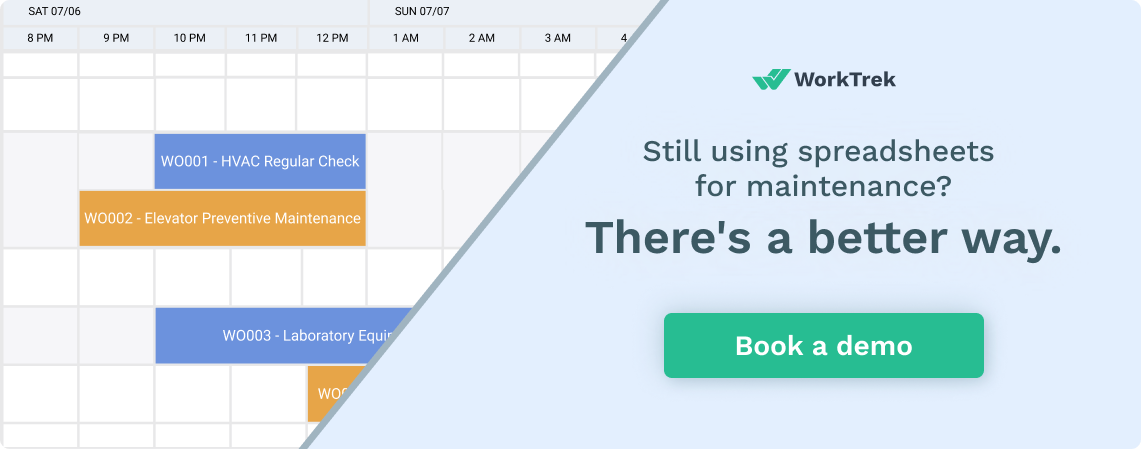
You can also automate stock replenishment and set reorder thresholds to avoid stockouts and overstocking.
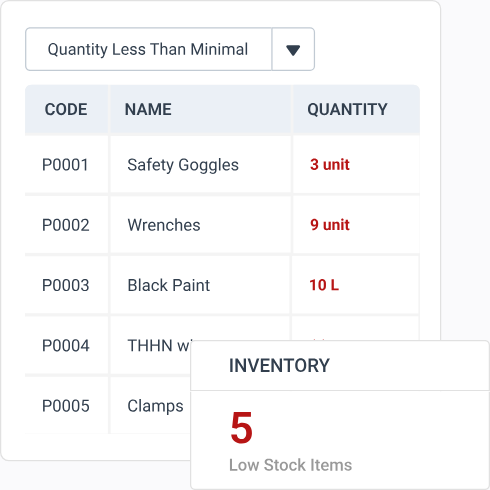
WorkTrek, for example, has all these abilities and provides an efficient way to manage spare parts inventory, so you always have what you need on hand.
It also allows you to transfer inventory between warehouses using your phone, making inventory management even more accessible and convenient.
Establish Clear Communication Protocols Between Teams
Effective communication is essential for a streamlined maintenance process.
Delays, prolonged downtime, and inefficiencies often result from poor inter-team communication.
And it happens more often than we’d like to admit.
Let’s start with the maintenance and operations teams who rely on each other.
Timely and accurate reporting of equipment failures by operations teams is crucial for maintenance teams to respond effectively.
Owe Forsberg, IDCON’s VP, summarizes what maintenance wants from operations:

He adds a process that should be used, too: sending a work request that becomes a work order if approved.
But it’s a two-way street.
Operations also depend on maintenance to plan work.
They need clear schedules to adjust production timelines and minimize disruptions.
Michael Dearden, an experienced maintenance manager, shared how he ensured cordial relationships and good communication between maintenance and operations across three refineries where he worked:
He also explains that in the rare event of a major breakdown, it is essential to keep everyone fully informed with constant updates on progress and provide “realistic” completion times.
However, communication isn’t just about maintenance and operations.
Procurement and finance play a role, too.
Spare parts management is a great example of how important cross-departmental communication is.
Phillip Slater, founder of SparePartsKnowHow.com and spare parts management specialist, explains that:
- maintenance needs to provide quality forecasts and data on needs,
- procurement needs to purchase goods in a manner consistent with inventory goals,
- finance needs to understand that not all inventory is bad.
When these teams fail to communicate, it’s a recipe for delays and costly mistakes.
So, what’s the solution?
First, assign unique IDs to all assets to ensure everyone speaks the same language when identifying equipment.
Second, a standardized failure reporting system should be created with clear categories like downtime type, recurrence, and performance impact.
And don’t forget to train your teams to follow these protocols consistently.
Here’s another tip from Valentin Espinosa, Engineering and Maintenance Manager at CarbonFree:
Communication between ops and the maintenance team does not happen via email. The best option is a face-to-face conversation to present and discuss facts, strategy and how to proceed, oriented on gaining an agreement.
Face-to-face communication and quick communication channels can make all the difference in relationships between teams, especially maintenance and operations.
So, if you want to improve your maintenance process, change the way your teams communicate.
Or remind someone in upper management about it.
Conduct Regular Maintenance Training
One thing that often comes up in conversations about maintenance is the need for proper training.
Many maintenance professionals report that training is often limited or absent.
For example, one Reddit user from a steel fabrication factory shared his frustration:
When something goes down, they want it back up ASAP so there’s not a lot of opportunities to learn slowly, four supervisors are cracking the whip with a fire lit under my feet to “just get it running. I always remind them I’ve had no formal training other than electrical and if they’d like me to do things quicker, they should push for training.
He pointed to a common problem: workers are expected to deliver immediate fixes without the time or resources to learn the right way.
The demand to ‘just get it running’ frequently results in frustration and inefficiencies.
Another professional echoed this sentiment:
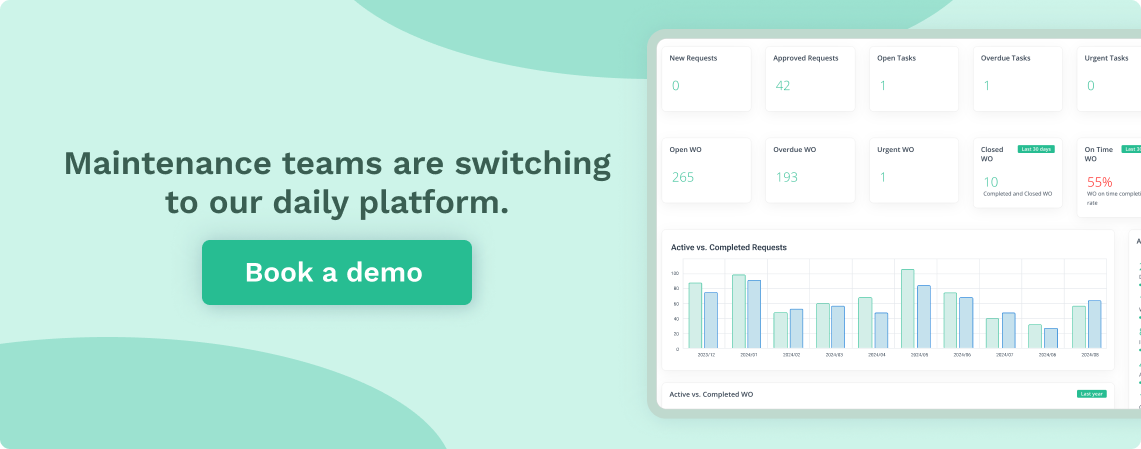

This disconnect between workers and leadership only makes the problem worse.
Many maintenance staff feel unsupported, with no formal training programs to develop their skills.
For some, trial and error becomes the default training method, which isn’t just inefficient but also risky, as another worker bluntly put it:
Been in the industry since 2010. The only time I see training taking place is to cover the company from a potential lawsuit or if the maintenance techs are part of a good union.
Even supervisors aren’t immune to this lack of training, as one shared:
All these experiences from maintenance professionals underscore the importance of proper training for all staff levels to ensure they are equipped to handle their challenges.
So, invest in comprehensive training programs that combine classroom learning with practical, on-the-job experience, as one maintenance professional suggests.
Teach core skills like preventive maintenance, troubleshooting, and using diagnostic tools.
On top of that, refresher courses should be offered to keep knowledge up-to-date and ensure compliance with safety standards.
Investing in maintenance training benefits not only the workers but also the entire company, leading to better asset management, fewer errors, and improved overall performance.
Identify Trends In Asset Behavior
Your assets hold the answers to their maintenance needs—they show you when and what type of maintenance is required.
By analyzing patterns in asset performance, you can predict failures, optimize maintenance schedules, and extend equipment life.
The key is to use historical data and tools like IoT sensors to track vital asset metrics such as temperature, vibration, and error codes.
You can uncover trends and make data-driven decisions that boost efficiency with analytics tools.
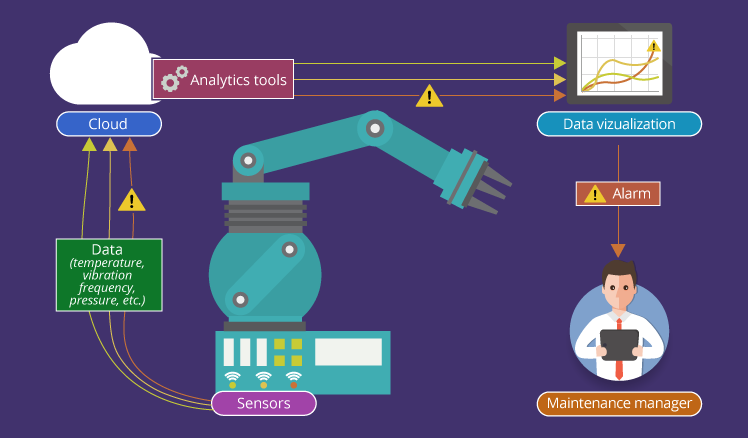
Take Fastenal, an American industrial supply company, as an example.
They faced the challenge of improving machine uptime, utilization, and quality but needed more real-time data and actionable insights.
To solve this, they turned to MachineMetrics, an automated machine monitoring and manufacturing analytics solution.
The system collected data from machine controls and operators, including key metrics like:
- Machine performance
- Asset status tracking
- Utilization rates
- Fault detection
- Downtime
Fastenal then displayed real-time dashboards on the production floor, giving managers immediate insights into performance metrics and any underperforming jobs.
This solution allowed Fastenal to track asset performance, identify production bottlenecks, and measure the impact of process improvements.
As a result, the company saw significant benefits:
This example shows the power of leveraging asset data to identify trends.
Fastenal didn’t just react to problems but anticipated and solved them before they escalated because data gave them the power to do so.
And you can do the same.
By monitoring asset behavior and making data-driven adjustments, your team can plan maintenance based on failure predictions.
The goal is clear; listen to what your assets are telling you.
When you do, you’re not just maintaining assets but maximizing their potential.
Conclusion
We hope this article has given you ideas on improving your asset maintenance process.
From improving communication and training to using sensors, there are a lot of things you can do. You can also help yourself with a reliable CMMS to increase your overall efficiency.
So apply these strategies today. The key to better maintenance is in your hands!