Get a Free WorkTrek Demo
Let's show you how WorkTrek can help you optimize your maintenance operation.
Try for freeWhat is lean inventory management? It offers a solution that minimizes excess inventory and streamlines inventory control operations. This approach helps organizations reduce holding costs, improve cash flow, and ensure that the right amount of stock is available at the right time.
In an increasingly competitive business environment, companies constantly seek ways to minimize waste, reduce costs, and maximize efficiency.
Illustration: WorkTrek / Data: Plataine
One key challenge they face is managing inventory effectively without overstocking or running out of critical supplies.
By adopting lean principles, companies can better align their inventory levels with actual demand, eliminate waste, and enhance operational efficiency.
Listen to an Audio Version of this Article
Understanding Lean Inventory Management Systems
Illustration: WorkTrek / Quote: NetSuite
Lean inventory management is a strategy for enhancing efficiency and minimizing waste in inventory maintenance.
It emerged from Japan and centered on removing ‘Muda,’ which translates to waste, as part of refining manufacturing processes.
This strategy, which takes its cues from the groundbreaking Toyota Production System, has significantly altered companies’ methods for managing their inventory.
At its core, lean inventory management prioritizes reducing excess stock while improving efficiency in the supply chain.
Simplifying procedures and eliminating superfluous stages within operations ensures resources are utilized more effectively, leading to quicker workflows and diminished expenses.
Origins of Lean Inventory
Taiichi Ohno, as part of the Toyota Production System, substantially shaped the core of lean inventory management. He is often called the father of the lean manufacturing movement.
His singular focus on minimizing waste and enhancing operational efficacy was the foundation of lean manufacturing principles.
Illustration: WorkTrek / Data: Southern States TOYOTA lift
James Womack and Dan Jones later played crucial roles in advancing and disseminating these ideas well beyond their initial scope within the automotive sector.
Through their efforts, a diverse array of industries globally have embraced lean inventory methods, revolutionizing their approaches to managing inventory.
Core Principles of Lean Inventory Management
Lean inventory management is grounded in five essential principles:
- Value:
- Organizations must understand customer value expectations through direct engagement and then align pricing and manufacturing practices to deliver optimal value while eliminating waste to meet customer needs.
- Value stream:
- Map and analyze the entire product lifecycle to identify and eliminate non-value-adding activities. If a process doesn’t enhance customer value, it should be removed from the value stream.
- Flow
- Organizations should maintain a steady production flow matching demand, using just-in-time principles to avoid waste from inventory imbalances that disrupt manufacturing efficiency.
- Pull
- Pull systems trigger production only when demand exists, requiring accurate forecasting to maintain steady manufacturing while avoiding excess inventory costs and waste.
- Perfection
- Continuous analysis of performance metrics enables organizations to streamline processes, reduce waste, and enhance customer value, recognizing that improvement is an ongoing journey.
Source: WorkTrek
Strategies for Implementing Lean Inventory Management
Implementing lean inventory management involves a strategic plan that understands inventory movement and aligns production schedules with real customer demands. To adopt lean practices, create a detailed blueprint with specific qualitative and quantitative objectives. Also, make sure you have the resources needed for the transition.
Developing a comprehensive plan to implement lean principles includes setting clear goals and timelines to guide the transition to more efficient lean operations. This strategy aims to streamline processes by eliminating unnecessary steps, resulting in faster workflows and improved operational efficiency.
Just-in-Time (JIT) Inventory
The Just-in-Time (JIT) method of inventory management focuses on acquiring materials only as they are needed for production or sale.
This strategy ensures supply is synchronized with demand while maintaining low operational costs.
Source: WorkTrek
Advantages of implementing JIT in inventory management include:
- Reducing unnecessary levels of excess inventory
- Tailoring production to reflect actual customer demand
- Reducing the requirement for holding surplus stock
- Cutting down on the need for extensive storage space
According to lean manufacturing principles, efficient inventory management requires keeping the right amount of raw materials on hand.
The key to implementing lean inventory management principles is to reduce excess inventory.
Source: WorkTrek
This approach allows for flexible adjustment to changes in consumer demand. Industry leaders, such as global eCommerce companies and brands like Starbucks, utilize JIT systems to manage their resources effectively, thereby reducing waste and minimizing costs related to storage.
One of the challenges in JIT is managing supplier relationships. You need good supplier partnerships to make JIT work.
Demand Forecasting Techniques
Precise demand forecasting is a cornerstone of lean inventory management. This can ensure businesses can anticipate stock requirements while avoiding outdated inventory.
One key strategy is to leverage past sales data. This can help you recognize market trends and account for seasonal fluctuations.
For instance, giants like Amazon implement sophisticated predictive algorithms in their inventory management practices that pinpoint customer needs precisely, optimizing their stock levels and curbing unnecessary waste.
Sales data and demand forecasting techniques can help you fine-tune your inventory management processes.
Continuous Improvement Processes
Like any process that you implement, lean management requires continuous improvement.
Illustration: WorkTrek / Data: Wever
One successful approach is using key performance indicators, such as inventory turnover rates and service level measurements, to refine and iterate on your process continuously.
Based on our experience, companies that integrate lean inventory principles perpetually tweak their methods to pinpoint and eliminate inefficiencies.
Benefits of Lean Inventory Management Systems
Think of lean inventory management as keeping your kitchen organized. You wouldn’t buy 50 loaves of bread at once – they’d go bad before you could use them. Instead, you buy what you need when you need it. That’s what lean inventory is all about.
When businesses use lean inventory, they save money, work smarter, and keep customers happy. It’s about having just enough – not too much, not too little. Like a well-organized kitchen, everything has its place and purpose.
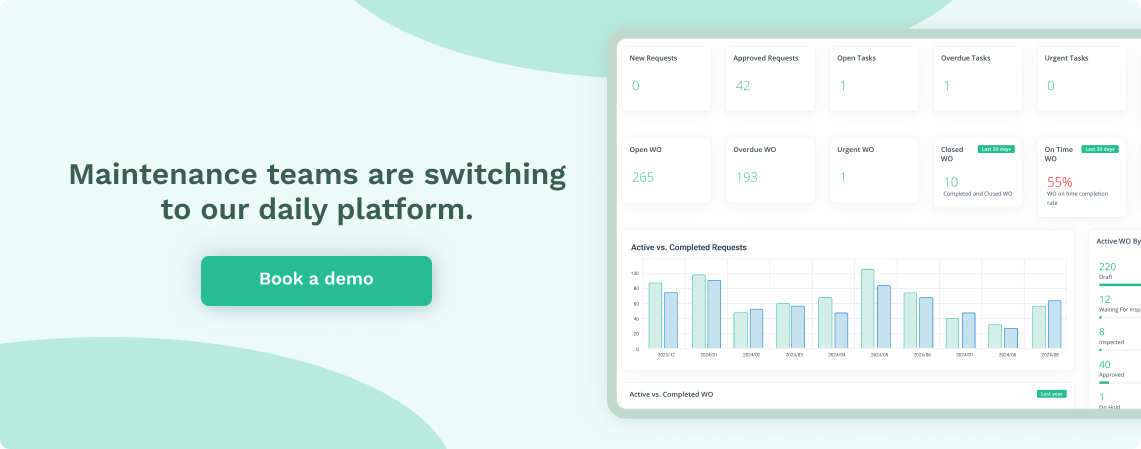
Let’s look at the top 10 ways lean inventory helps businesses work better and save money.
1. Reduced Carrying Costs
Think of carrying costs like paying rent for your stuff. The more inventory you keep, the more you pay to store it. It’s that simple. Lean inventory means keeping fewer things on your shelves.
Illustration: WorkTrek / Data: Sprintzeal
You spend less on warehouse space, insurance, and utilities when you store less. Many businesses save up to 30% on these costs in their first year of going lean.
2. Better Cash Flow
Too much inventory is like keeping all your money in a storage room instead of your bank account. When you own less inventory, you have more cash for other things.
It’s like cleaning out your garage sale—when you sell things you don’t need, you suddenly have extra money to spend on leamore important things.
3. Better Quality Control
When you have fewer items to check, spotting problems is easier. It’s like trying to find a bad apple – checking a small basket is much easier than a huge bin.
Problems get fixed faster because you’re dealing with smaller batches. This means fewer unhappy customers and fewer returns.
4. Getting More Done
Lean inventory is like having a clean, organized desk. When everything has its place, you can work faster and better.
Workers don’t waste time hunting for things. They know where everything is and can get their job done more quickly.
5. Using Space Better
Good inventory management helps you use your space wisely. It’s like organizing your closet – when you do it right, you’re amazed at how much space you have.
Source: WorkTrek
Many companies find they can fit the same amount of stuff in a much smaller space. Some save up to 40% of their warehouse space by organizing better.
6. Quick Response to Changes
When you keep less inventory, it’s easier to change direction when necessary. It’s like driving a small car instead of a big truck—you can turn much faster.
Illustration: WorkTrek / Quote: Manutan
If customers suddenly want something different, you can adapt quickly. You won’t be stuck with piles of stuff nobody wants anymore.
7. Less Waste
Keeping less inventory means less stuff gets old, expired, or damaged. It’s like buying enough groceries for the week instead of filling your fridge until things spoil.
Companies usually throw away much less when they use lean inventory. This saves money and is better for the environment.
8. Happier Customers
When you manage inventory well, customers get what they want faster. It’s like a restaurant that always has fresh ingredients ready to cook.
Customers are happier because they don’t have to wait as long for their orders. They can count on getting their stuff on time.
9. Lower Labor Costs
With lean inventory, workers spend less time moving things around. It’s like having a clean kitchen—you can cook faster when you’re not constantly shuffling things around to find what you need.
Companies often save 10-20% on labor costs because workers can do their jobs more efficiently. They spend less time searching for things and more time getting work done.
10. Better Relationships with Suppliers
Ordering smaller amounts more often helps you work better with your suppliers. It’s like going to the grocery store twice a week instead of once a month – the store can better predict your needs.
Suppliers like steady, regular orders better than big, random ones. This often leads to better service and sometimes even better prices.
Illustration: WorkTrek
Challenges in Adopting Lean Inventory Management Systems
Making big changes in a company’s work is never easy – especially regarding inventory. It’s like trying to change your eating habits or start a new exercise routine. You know it’s good for you, but doing it can be tricky.
Many companies want to switch to lean inventory but encounter obstacles. These problems are typical and happen to most businesses. Understanding these common challenges is the first step to solving them. It’s like having a map of the potholes in the road—when you know they’re there, you can plan how to avoid them.
Let’s look at the main reasons companies struggle with this change.
1. Old Habits Die Hard
Illustration: WorkTrek / Data: itefy
People get comfortable doing things their way. It’s like switching from paper maps to a GPS – even when the new way is better, some folks want to stick to what they know.
Many workers have been doing inventory the same way for years. They might resist or quietly return to their old ways when you ask them to change.
2. Fear of Running Out
Companies worry about not having enough products when customers want them. It’s like being afraid to let your gas tank go below half-full – you keep extra “just in case.”
This fear makes managers keep extra stock around, even when they don’t need it. They’d rather have too much than risk running out.
3. Unreliable Suppliers
When suppliers are late or inconsistent, keeping less inventory is hard. It’s like trying to plan meals when you don’t know if the grocery store will have what you need.
Companies often keep extra stock to protect themselves from supplier problems. This extra “safety stock” goes against lean principles.
4. Poor Technology
Many companies use outdated systems to track their inventory. It’s like trying to run a modern kitchen with a 20-year-old stove – things don’t work as well as they should.
Illustration: WorkTrek / Data: Limble
Without good technology, it’s hard to know precisely what you have and what you need. This makes companies keep extra “just to be safe.”
5. Lack of Training
Workers need good training to understand lean methods. It’s like getting a new smartphone – if nobody shows you how to use it, you’ll only use the basic features.
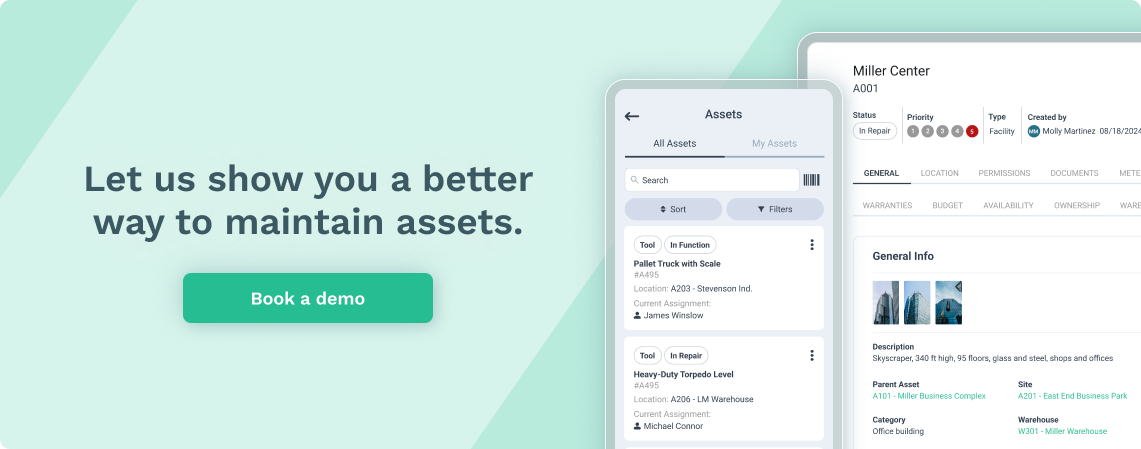
Many companies don’t spend enough time training their workers. People who don’t understand the new system are likelier to make mistakes.
6. Rushing the Change
Some companies try to change everything at once. It’s like trying to learn how to juggle by starting with five balls—it’s too much and too fast.
Big changes need time. When companies rush, people become overwhelmed and frustrated, often leading to failure.
7. Poor Communication
Leaders sometimes don’t explain why they’re making changes. It’s like parents telling kids to eat vegetables without explaining why they’re healthy.
Workers who don’t understand the benefits of lean inventory are less likely to support the change. Good communication helps everyone work toward the same goal.
Making big changes in how you handle inventory isn’t easy. However, understanding these common problems helps companies avoid them. The key is to take it slow, train people well, and ensure everyone understands why the changes matter.
Would you like me to expand on any of these challenges or share some tips for overcoming them?
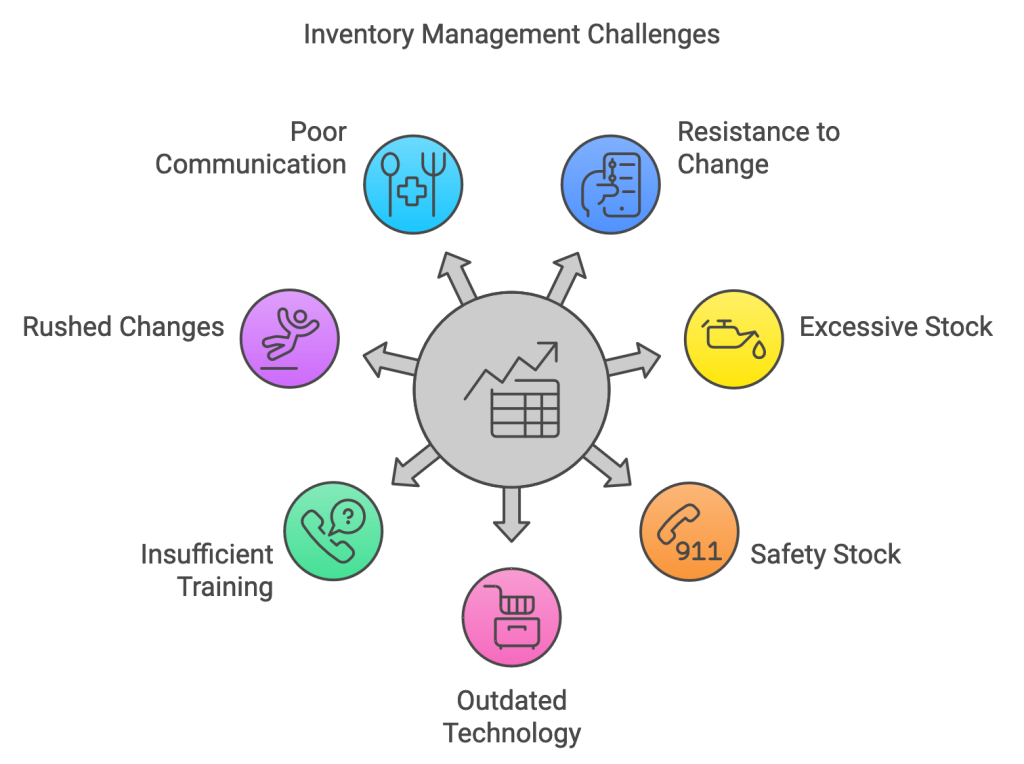
Source: WorkTrek
Tools and Techniques for Lean Inventory Management
To implement lean inventory management, you need real visibility that can only be achieved with precise inventory records.
Integrating tools such as barcodes with ERP software can improve inventory tracking accuracy.
Source: WorkTrek
Implementing CMMS software like WorkTrek can help you easily track your inventory and set low stock alerts.
The deployment of these instruments enhances effective inventory management by adhering to lean principles, ultimately reducing unnecessary excesses and enhancing operational productivity.
Kanban Systems
Kanban systems employ visual aids to oversee workflow processes, signal work status, and efficiently regulate inventory amounts.
These systems use boards with visible representations of tasks that permit teams to track their progress and maintain a steady delivery rhythm.
Source: WorkTrek
Implementing Kanban systems can result in decreased surplus inventory, heightened efficiency, and an agile supply chain.
This makes them indispensable resources within the practice of lean inventory management.
Value Stream Mapping
Lean inventory management utilizes value stream mapping as a powerful instrument for detailing the various stages of the production process.
This approach aids in illustrating material and information trajectories, shedding light on their progression through each manufacturing phase.
Source: WorkTrek
By delineating every task, companies can pinpoint specific segments prone to inefficiency, paving the way for strategic enhancement initiatives.
Adopting value stream mapping fosters shorter lead times, bolsters productivity, and augments quality standards across all aspects of production.
Cycle Counting
Instituting a cycle counting program bolsters the precision of inventory records, thereby facilitating superior inventory management. It enables expeditious pinpointing and rectification of discrepancies in stock data.
Illustration: WorkTrek / Quote: NetSuite
Frequent partial counts within the inventory ensure sustained high levels of accuracy, circumventing the necessity for interruptive complete audits.
Such a strategy augments inventory management efficiency and aligns with lean inventory management principles.
Real-World Examples of Lean Inventory Management
Implementations of lean inventory management in actual business settings demonstrate its value across many industries. The success stories from diverse sectors exemplify adopting lean practices that enhance efficiency and minimize waste.
Businesses ranging from car makers to major retailers have effectively utilized lean inventory management strategies, enabling them to trim their inventory levels, refine their processes, and boost customer satisfaction.
Manufacturing Industry
Zara employs a just-in-time production strategy to swiftly adapt to changing fashion trends. This strategy helps mitigate inventory risks and shorten lead times, sustaining a lean supply chain by keeping inventory levels tightly matched with actual demand.
How does Zara do this?
- Just-In-Time (JIT) Production:Zara employs JIT manufacturing to produce items in response to current demand, minimizing overproduction and excess inventory. This approach allows the company to adapt swiftly to changing fashion trends and customer preferences.
- Vertical Integration: Zara maintains tight oversight over inventory levels by controlling various stages of its supply chain—from design and production to distribution. This integration enables rapid adjustments to production schedules based on real-time sales data, ensuring supply aligns closely with demand.
- Frequent Inventory Replenishment: Zara delivers new products to its stores in small batches twice a week. This practice keeps inventory levels low and reduces the risk of overstocking while also creating a sense of scarcity that encourages prompt purchases.
- Responsive Design and Production: The company can design, produce, and distribute a new garment to stores within four to five weeks. This rapid turnaround allows Zara to respond promptly to emerging trends, reducing the need for large inventories of unsold items.
- Advanced Information Systems: Zara utilizes sophisticated IT systems to monitor sales and inventory in real-time. Store managers input sales data daily, which informs production and distribution decisions and ensures that inventory levels are optimized across all locations.
As Zara has proven, the emphasis of lean inventory practices on minimizing waste and enhancing process efficiency can result in marked gains regarding operational effectiveness and cost savings.
Summary
Lean inventory management is the foundation for streamlining inventory processes, reducing waste, and increasing efficiency overall.
Knowing the beginning, the basics, and the tactics allows companies to adopt lean. The benefits are many: cost savings, higher customer satisfaction, and environmental sustainability.
As you implement lean inventory in your business, you need to recognize and actively pursue continuous improvement opportunities while improving demand forecasting and supplier partnerships.
These are key to long-term success and staying ahead of the game in the ever-changing business landscape. Commit to lean inventory management and watch your operations improve.