Get a Free WorkTrek Demo
Let's show you how WorkTrek can help you optimize your maintenance operation.
Try for freeHave you ever wondered how solid your maintenance practices really are?
Is your equipment properly maintained, and are your technicians consistently following safety procedures?
These are the types of crucial questions a good maintenance audit can answer.
While some industries require mandatory audits by regulatory bodies, each company can benefit from an internal, voluntary audit.
If you’d like to start conducting these audits more regularly, this article is for you.
We’ll walk you through the key steps of effective maintenance audits to ensure you’re truly getting value from the process.
1. Defining Audit Scope and Objectives
Before starting the audit, the first step is to clearly define its scope and objectives.
This might seem obvious, but without it, you’re just looking for a haystack without knowing which needle to look for.
So, plan what you’ll audit first. If you manage three different facilities or two different production lines, you might audit the maintenance on just one.
Prioritize what’s most impactful. For example, assets that are the largest contributors to product output pose the greatest safety risks or are the most costly to maintain.
By focusing on these, you’ll get the most value from your audit.
Also, think about what aspects of your maintenance program you want to focus on.
This could include everything from maintenance planning and scheduling, work order management, safety practices, and predictive maintenance.
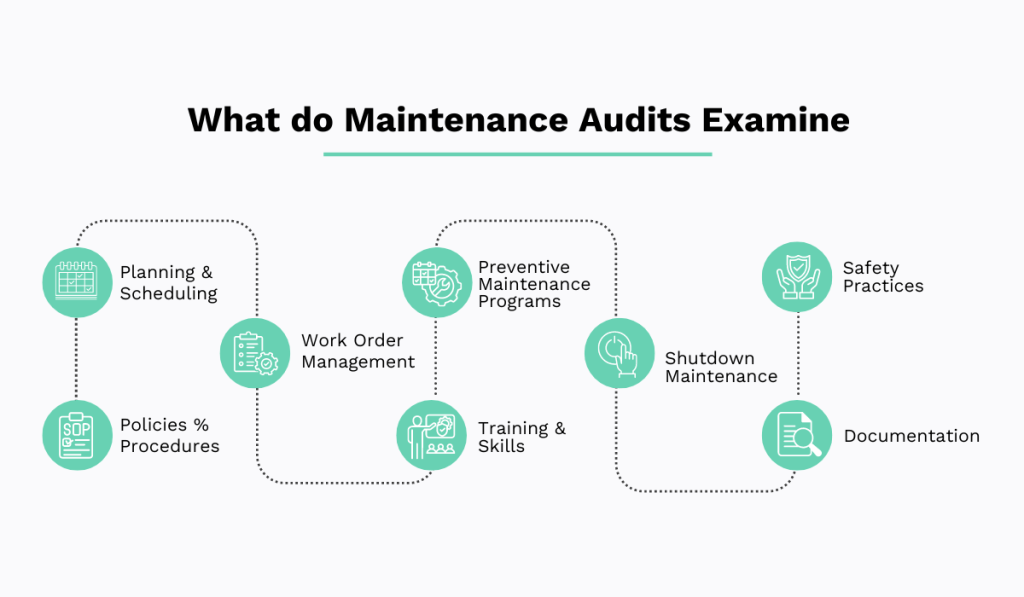
Your maintenance audit might cover all these aspects, or it could narrow down to just one.
Once you’ve determined what you’re auditing, decide why you’re auditing it.
Maybe you’ve noticed that maintenance is taking longer than planned and want to dig into why that’s happening to reduce it.
Or perhaps you want to reduce unplanned downtime.
Whichever objectives you choose, make them specific, measurable, achievable, relevant, and time-bound (SMART).
This ensures they’re not just vague goals but targets you can hit.
So, think about a specific objective like:
Cut asset downtime by 10% over the next three months by improving preventive maintenance scheduling and inventory management.
Next, define the metrics and KPIs to benchmark your audit against.
This could include:
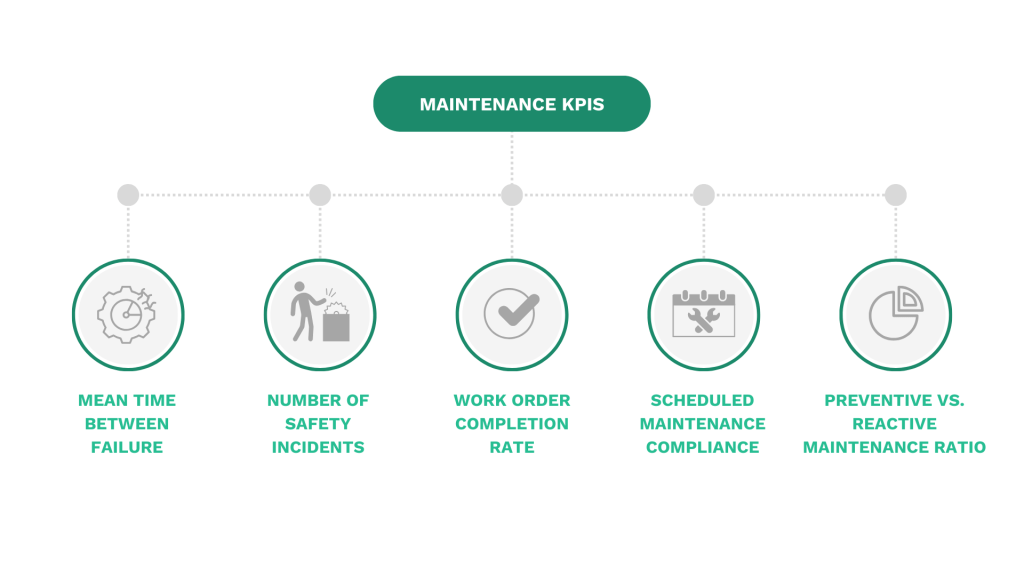
Of course, metrics should align with your objectives.
With so many moving parts, it’s easy to oversee something. But if you compile everything into a maintenance audit checklist, you will ensure this doesn’t happen.
Below is a simple maintenance audit checklist:
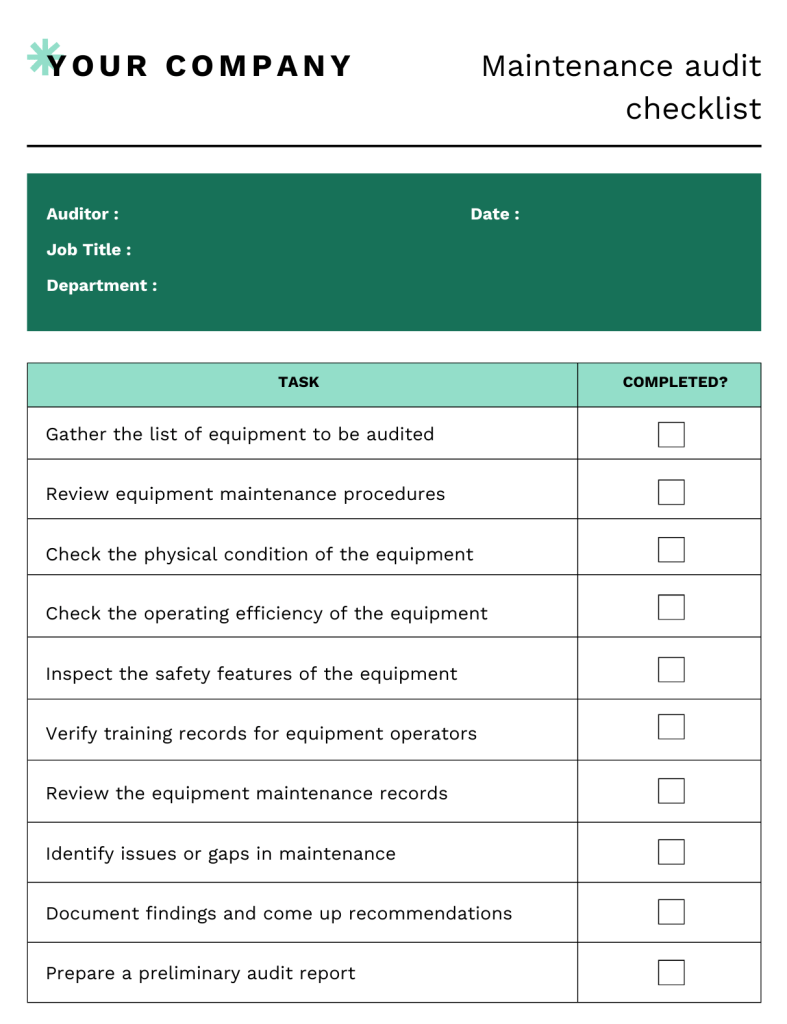
Finally, think about the right people for the job.
Does the audit scope call for a team of people, or is it just you?
Do you need to include maintenance technicians, engineers, and other managers to help you out?
If multiple people are involved, a designated audit manager should be appointed to oversee the process and ensure everything runs smoothly.
Doing all this will lay the groundwork for a thorough and effective audit.
2. Reviewing Documentation on Past Maintenance
After you’ve set your audit’s scope and objectives, review your past maintenance documentation.
Go over previous work orders and parts replacement history to see what you can learn.
That’s a lot of information to gather, but if you’re already using a computerized maintenance management system (CMMS) like WorkTrek, this step becomes much easier.
With solutions like WorkTrek, you can track who completed a task, when it was done, how long it took, and which parts were used.
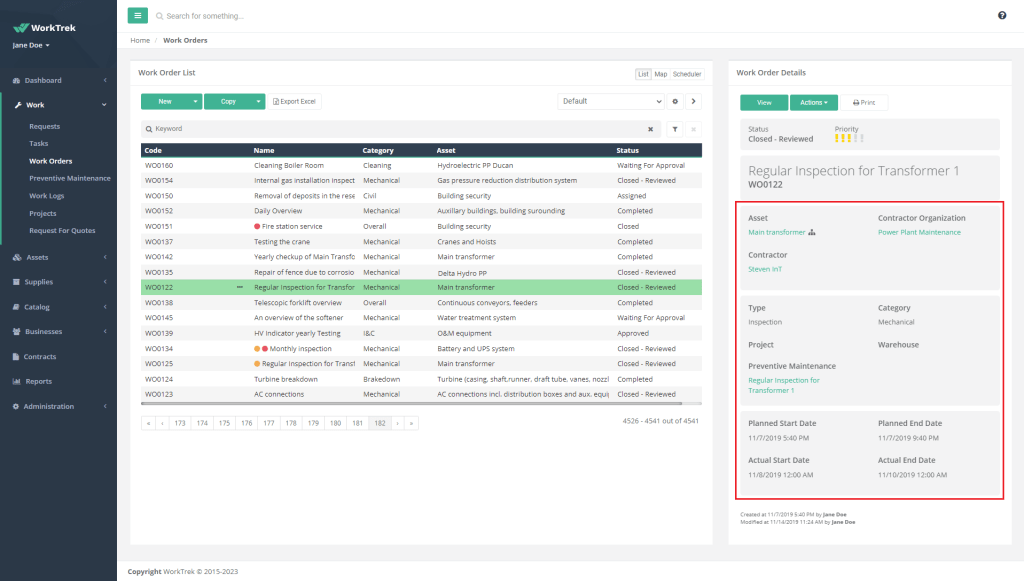
You can also store all your documents in one place, and generate reports in just a few clicks.
Below is just a small part of the reports that WorkTrek generates for you:
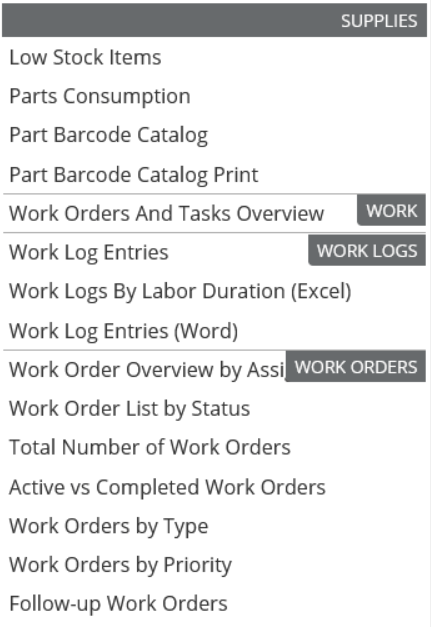
Thanks to historical data, you can see if certain pieces of equipment break down more often.
This might mean it’s time to replace them, or it could indicate they are not correctly maintained.
You might also discover that problems arise more often after certain technicians perform maintenance.
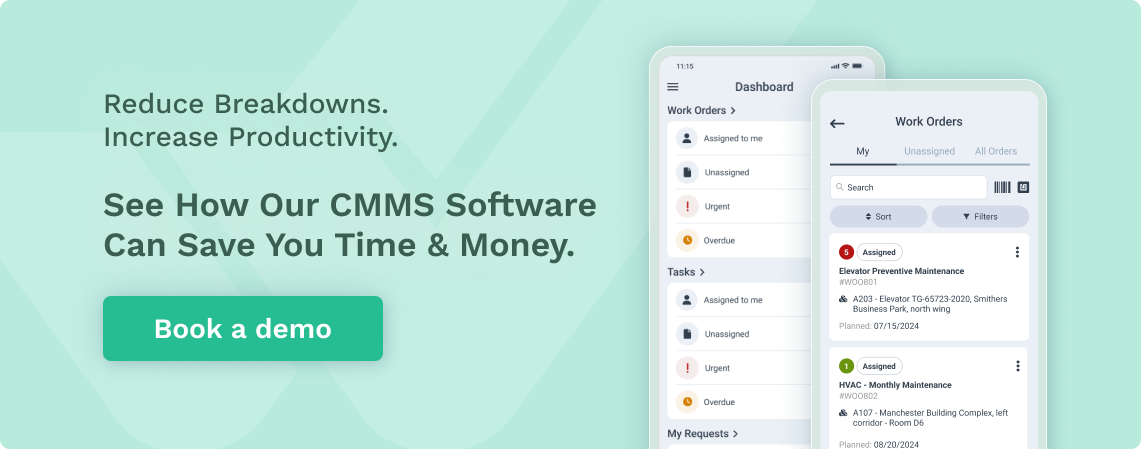
This could suggest a need for better training or clearer maintenance procedures.
Another thing you can do is compare the costs of similar work orders over time.
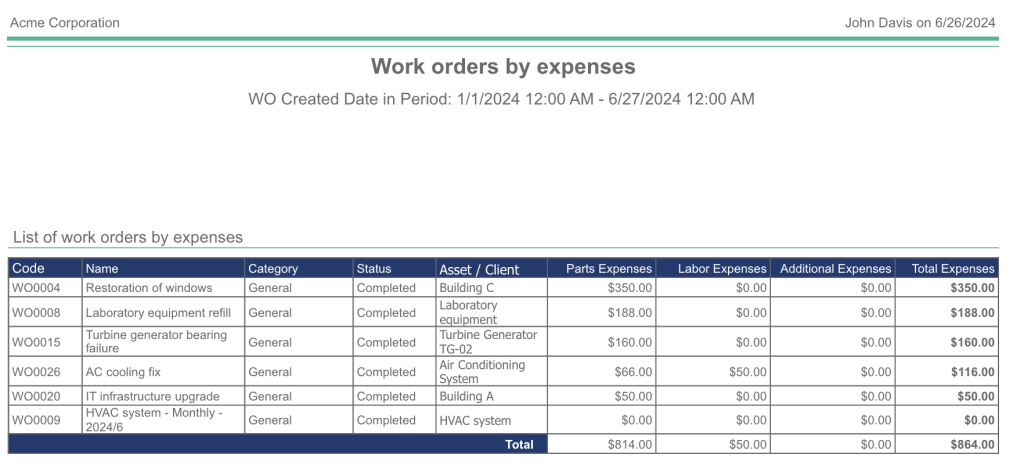
If the same maintenance job costs way more now than it did a few months ago, there are some inefficiencies to fix.
You can also check if the maintenance steps in your logs match the procedures you’ve set for each piece of equipment.
This is a good way to see if your team is following the standard operating procedures.
At this point, you should also categorize your findings into two main groups:
This helps you evaluate how well your maintenance planning is working.
For example, a high number of unplanned maintenance tasks might signal that your planning process needs improvement.
Finally, use past maintenance documentation to check if you’re meeting all the necessary regulations and standards—safety, environmental, or regulations specific to your industry.
The data shows if maintenance tasks are performed at industry-standard intervals and if all necessary checklists have been completed and signed off.
Going through all these records might feel daunting, but it’s a crucial step to understand how well your maintenance program is working and where it needs improvement.
And if you’ve got a good CMMS, it’s not nearly as tough as it sounds.
3. Examining the Equipment in Use
Don’t limit your audit to reviewing documents and records in an office.
It’s as important to visit the facility or shop floor and inspect the actual machines and their conditions.
This way, you gather firsthand information and verify the accuracy of the documentation.
Paul Hardiman, director of Quality Partner Limited and an expert in IATF auditor training, agrees:
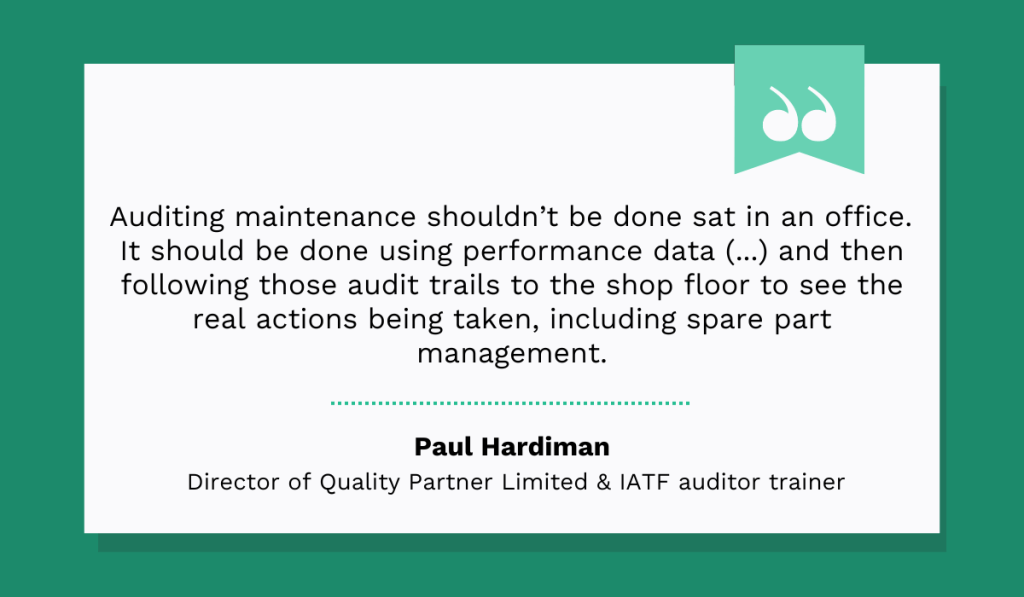
So, at this point, you physically check the equipment.
You’re looking for any signs of wear and tear, damage, or malfunction.
This means closely examining components like bearings, belts, electrical connections, and the overall structural integrity of the machines.
Specialized tools can help you measure factors like temperature, pressure, and vibration levels to clearly understand how well the equipment is performing.
As you inspect the equipment, you’ll want to compare what you see to your maintenance records.
Is the equipment in the condition it should be, based on what’s been reported?
For instance, you might print out a list of current work requests (which is very easy to do with WorkTrek) and then head out to see if the maintenance was carried out as reported.
Below is one such report.
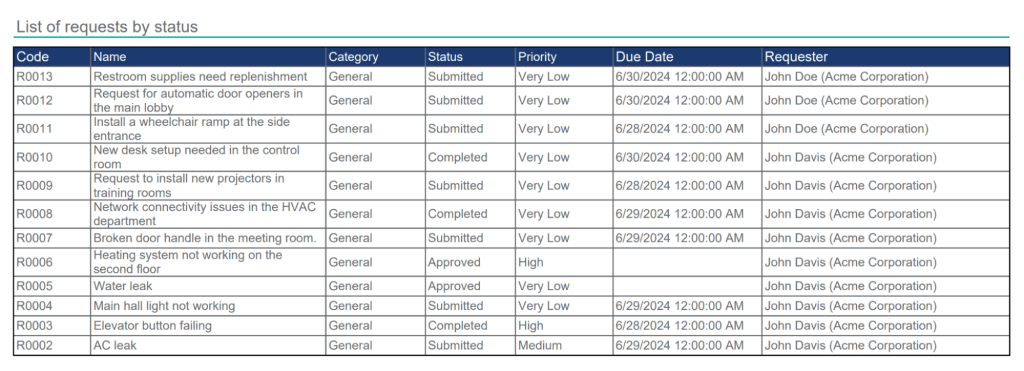
Now, check the code R0003.
It shows a high-priority maintenance task: fixing a failing elevator button.
The system says the job’s done, so you go to the elevator and test the button yourself.
Simple checks like this one confirm whether your team is doing the work recorded in the system.
In summary, get out into the field, see the equipment firsthand, and ensure everything aligns with the maintenance records.
4. Checking the Backup Inventory
Once you’ve inspected the equipment, check your spare parts inventory.
By now, you have a better idea of which backup items are most needed, so you should check if those parts are available in the inventory.
Having replacement parts on hand is critical for both unexpected breakdowns and preventive maintenance.
If a machine breaks down and you don’t have the parts to fix it immediately, production grinds to a halt, leading to delays and extra costs.
Take a look at one audit by Paul Hardiman that describes such a case:
If you watched the video, you saw what happened when a robotic arm didn’t arrive as planned.
The machine was down for 16 hours, which disrupted the entire production line.
All because the backup inventory wasn’t handled properly.
Or, learn from the experience of Jan Barraclough, a maintenance manager who found himself in a tough spot when working at a plant with two process trains.
The plant had multiple pump failures, and when he checked the stock levels, he discovered they were running dangerously low:
Checking stock levels, I discovered we had six belts left on site. I also made a few calls and discovered that we had no spare pulleys (either pump or motor) or taper locks and nothing on order.
![]()
This led to him trying to get parts delivered quickly to solve this mess. Of course, this urgency cost a lot more than it would have if the parts had been ordered on time.
Some parts even took up to six months to arrive, dangerously increasing the chances of another breakdown the facility wouldn’t be ready for.
Again, having a good CMMS can make a huge difference here.
With WorkTrek, for example, you can keep an accurate list of all your spare parts, and it’s easy to compare that list with your actual inventory.
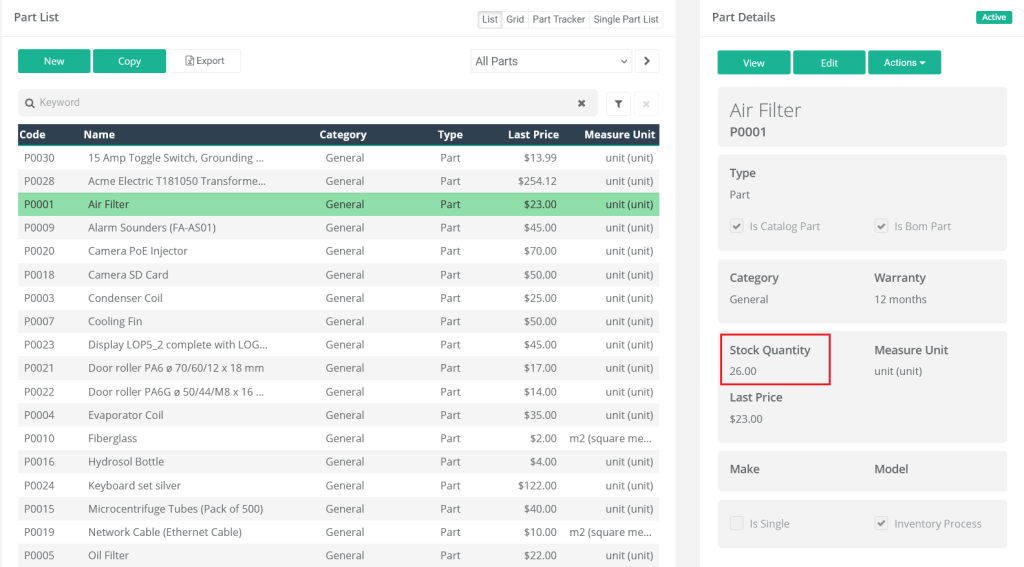
This way, you can quickly spot if something’s missing or if there’s a problem with how parts are being managed.
The key takeaway from this step?
Never miss it.
If there are inefficiencies in your backup inventory, it’s an area you should improve to avoid costly downtime in the future.
5. Creating a Report With Findings
The audit is only useful if it results in actionable steps. Without a clear report, all that effort won’t lead to any changes.
So, create a report that summarizes your findings, highlights areas for improvement, and suggests actionable steps which could include:
- replacing outdated equipment
- reporting issues to upper management
- providing additional training for technicians
One of the key parts of creating your report is deciding what to tackle first.
You can do this by attributing a risk rating to each finding:
- High-priority recommendations for urgent issues that could threaten safety, reliability, or compliance.
- Medium-priority recommendations for problems that affect efficiency or cost but aren’t immediate threats.
- Low-priority recommendations for minor issues or improvements that can wait until later.
For example, look at the audit conducted by the Office of the Auditor General (OAG) on the Facilities Maintenance program for Fairfax County Public Schools.
Below is the risk rating summary for their findings:
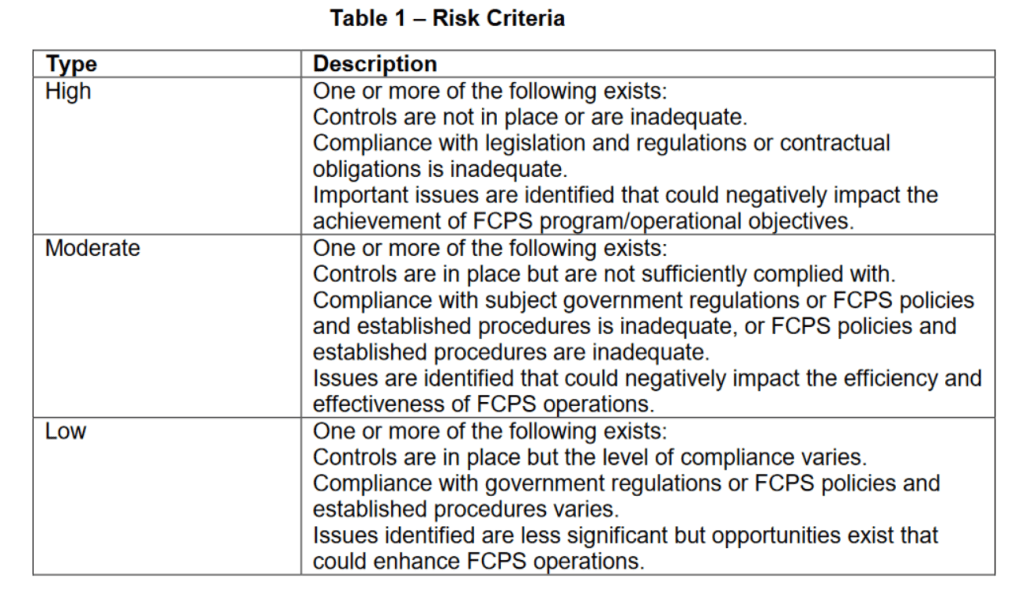
They identified five moderate-risk findings and provided detailed recommendations for each.
One big risk was insufficient funding for maintenance priorities and a deferred maintenance backlog.
To fix it, they recommended developing a backlog reduction spending plan and elevating concerns to the leadership team to secure additional funding.
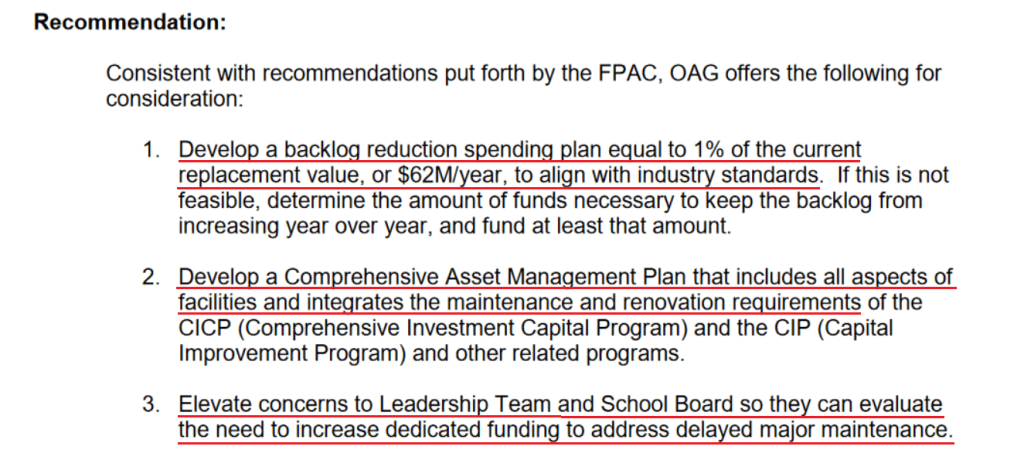
These recommendations were then shared with the management.
Let’s conclude with an excellent example of what happens when you actually accept audit recommendations.
Wärtsilä Power Plants, a supplier of flexible baseload power plants from Finland, audited the Limbe power plant in Cameroon.
They discovered major corrosion and maintenance issues that had cut the plant’s output to just 40%.
Wärtsilä recommended a total power plant rehabilitation, including repairs to engines, alternators, and radiators, and technical training for the staff.
The Limbe power plant implemented them.
In just seven months, the plant got back to its full capacity of 80 MW and saved money through reduced fuel and lube oil consumption.
This is a perfect example of what happens when you turn what you’ve learned from a good audit into action.
Conclusion
With these five steps, you’ll get your maintenance audit right.
It might seem like a lot of work, but these steps can really make a big difference in how well your facility runs.
By defining what to audit, reviewing past maintenance records, inspecting equipment, checking your spare parts, and putting together a detailed report, you’re setting yourself up for better maintenance practices.
The key is to keep doing these audits regularly—whether that’s every year, every six months, or even more often.
This way, you can track your progress, see improvements, and stay on top of your maintenance, which is why maintenance audits were invented.