Get a Free WorkTrek Demo
Let's show you how WorkTrek can help you optimize your maintenance operation.
Try for freeDo you feel like you’re constantly putting out fires, with one machine breakdown after another?
You’re not alone.
Many maintenance managers are stuck in reactive mode, dealing with unexpected maintenance issues that can destroy the day’s plans.
But what if you could get ahead of the chaos and prevent costly breakdowns before they happen?
You can—when you start scheduling your maintenance.
Instead of waiting for something to break, you set a timetable for regular check-ups, repairs, and maintenance.
Today, we will show you why this is your best defense against downtime, how to make it work, and which tools make your maintenance schedule organized and effective.
Let’s jump in.
Maintenance Scheduling Explained
While maintenance planning involves deciding what needs to be done, scheduling ensures those tasks get done.
It’s about implementing a maintenance plan and ensuring the right people do your equipment inspections, preventive maintenance, and corrective repairs on time.
As such, maintenance scheduling answers two key questions:
- Who will perform the tasks?
- When will they do it?
Getting these answers right keeps your machines in top condition, prevents unexpected breakdowns, and extends your equipment’s life.
A good schedule also maximizes the use of your resources—especially labor.
It reduces the chances of workers waiting around for tasks or being double-booked, leading to wasted time and reduced productivity.
Now—who should handle maintenance scheduling?
Big plants and facilities with more complex needs often have a dedicated scheduler.
This person’s job is to ensure that maintenance tasks are scheduled efficiently, considering the availability of resources, their effect on operations, and the importance of each task.
In smaller operations, this role might be handled by a maintenance supervisor or the maintenance planner (although that’s not ideal as planners should focus on planning future tasks).
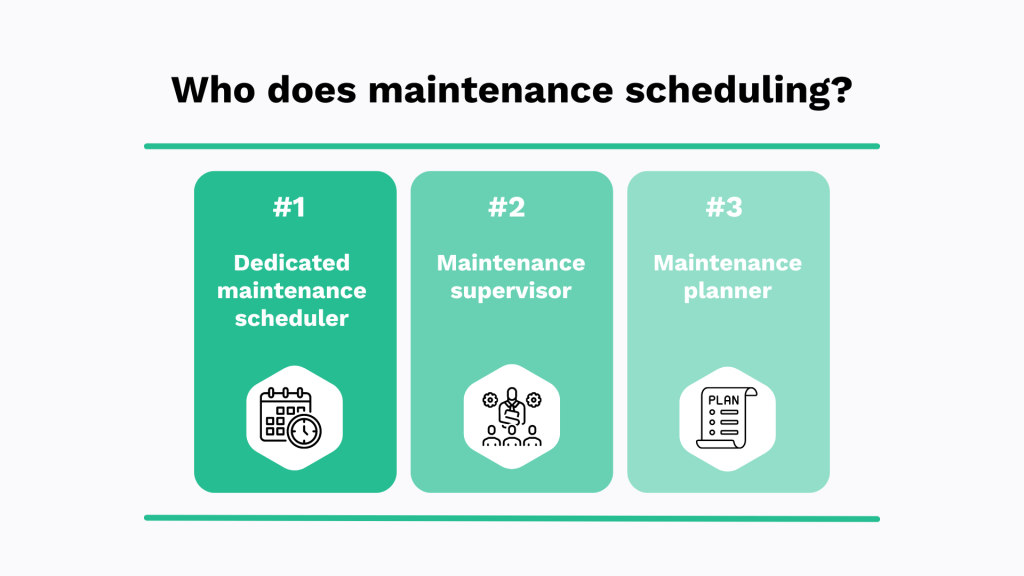
Regardless of who’s responsible, they must have hands-on experience with maintenance work.
They need to know how to prioritize tasks, estimate how long each job will take, and understand what skills are needed.
This is the only way to ensure the schedule is realistic and that the right people are assigned to the right tasks.
To keep everything running smoothly, it’s also important for the scheduler to work closely with the technicians.
They do the work, and their insights can help fine-tune the schedule.
Why Should You Schedule Maintenance
You might think that scheduling maintenance is just about putting some tasks on a calendar.
But in reality, maintenance scheduling is one of the most crucial things you can do to keep your plant or facility running smoothly.
Let’s break down why it’s so important.
Less Downtime
Have you ever been in the middle of a production run, and suddenly, a key piece of equipment broke down?
It’s unexpected, inconvenient, and expensive.
This is what happens when maintenance isn’t properly planned and scheduled.
But regular maintenance scheduling helps keep your equipment in top shape.
The healthier your equipment is, the fewer surprise breakdowns you have to deal with, which means less unplanned downtime.
Let’s look at what happens when you don’t schedule maintenance.
One Reddit user sums it up perfectly:
If you do not schedule maintenance on your machine, your machine will schedule it for you… Penny wise, pound foolish is a great expression.
In other words, if you’re not proactive about scheduling maintenance, your equipment will eventually force your hand—usually at the worst possible time.
When that happens, the costs can skyrocket.
Research by Senseye and Siemens shows that for large manufacturers across many industrial sectors, the cost of unplanned downtime can easily exceed $100,000 per hour and reach millions.
Alexander Hill, Global Head of Business Development at Senseye, puts this into perspective:
Unplanned downtime is the curse of the industrial sector. When expensive production lines and machinery fall silent, organizations stop earning, and those investments start costing rather than making money.
Unplanned downtime is not just an immediate financial hit, and it puts your entire production schedule at risk.
In 2022, a survey by Plant Services and Augury found that 36% of corporate respondents and 44% of frontline workers rank unexpected machine downtime as the biggest risk to meeting production targets.
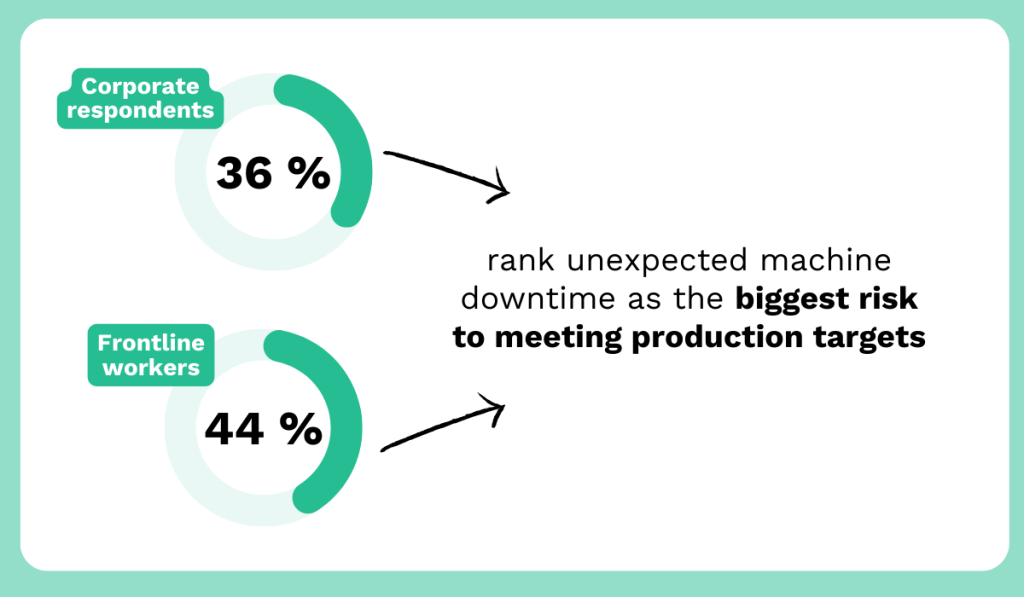
When equipment fails unexpectedly, it can mean the difference between hitting your production goals or falling short.
So schedule regular maintenance to keep equipment in good condition and prevent this.
Safety
When you think about safety in your facility, what comes to mind?
Probably things like protective gear, safety protocols, and training programs.
Have you considered how much a well-planned maintenance schedule contributes to safety?
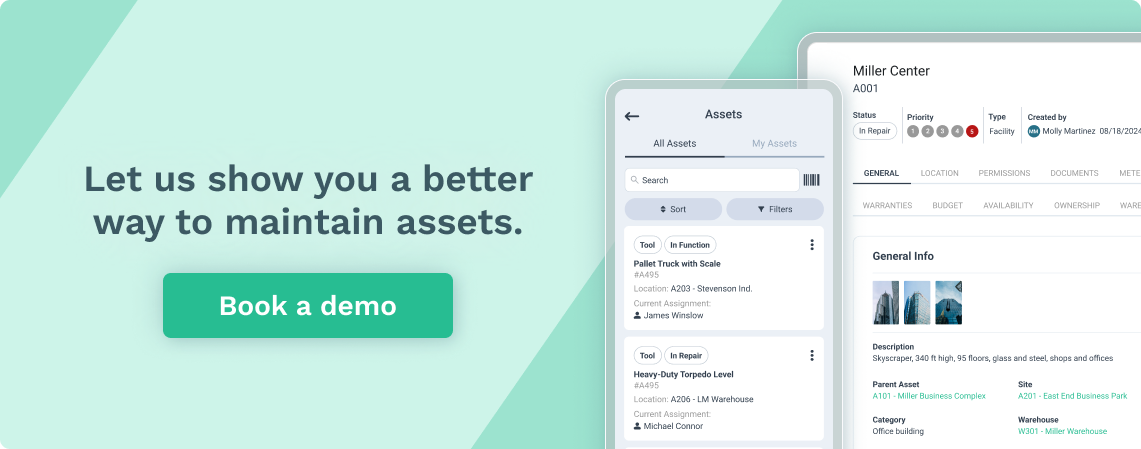
When equipment is regularly maintained, it’s less likely to malfunction and put your workers at risk.
On the flip side, if you don’t plan and schedule maintenance, you’re forced into a reactive mode.
And that’s where things get dangerous.
Chris Allmond, Head of Engineering Consultancy Services at RS Integrated Supply, and an asset management expert, agrees:
Reactive maintenance is the lowest level. (…) It is also very unsafe because people are often working under pressure from operations managers to get things up and running again, so they don’t step back and evaluate the inherent risks in conducting the activity. They just dive in, and that’s when people can get hurt.
And when accidents happen, they’re often serious.
The headlines are filled with reports from OSHA about injuries and fatalities in plants and facilities, many of which are due to poorly maintained equipment that breaks down or technicians rushing under pressure to get machines back to work.
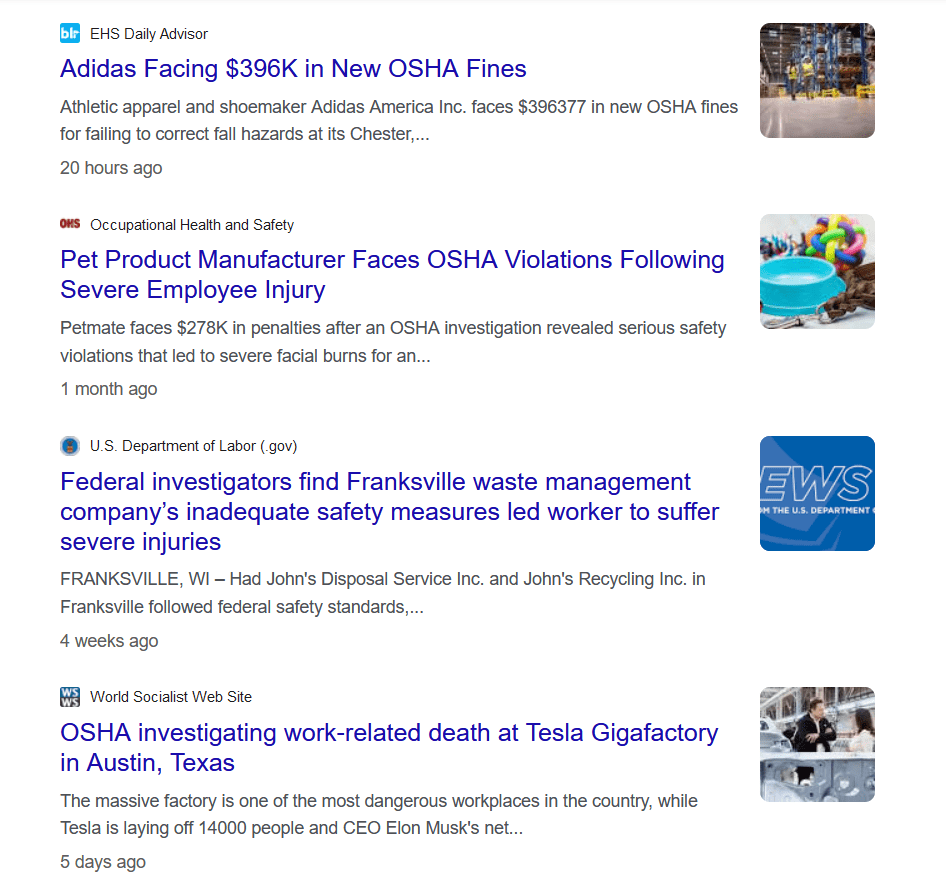
This widespread issue affects all sectors, from manufacturing to aviation.
One of the most tragic examples of this happened in 1979 with the crash of American Airlines Flight 191.
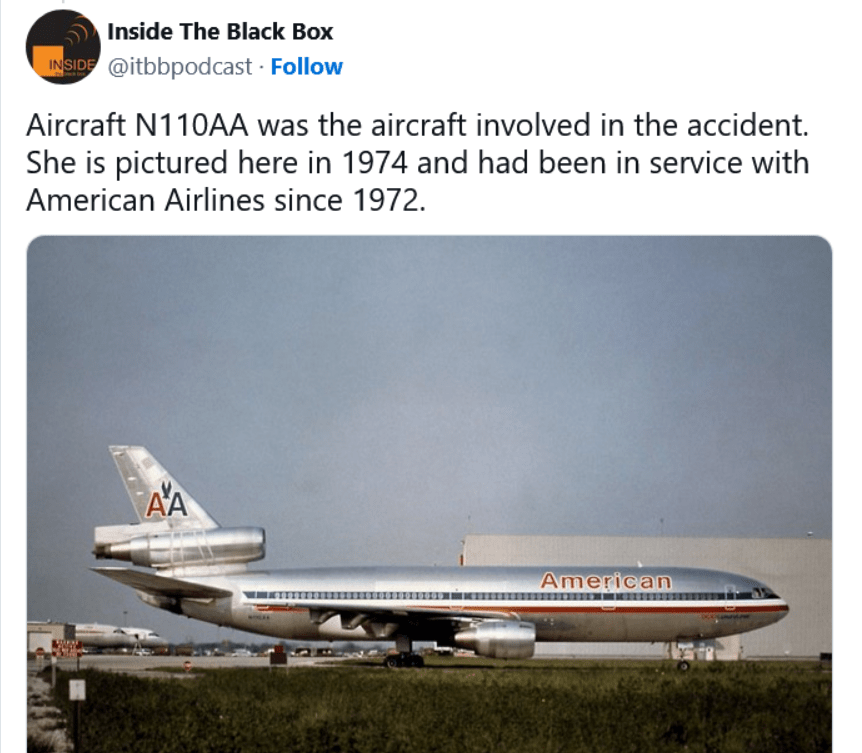
The disaster, which claimed the lives of all 271 passengers and crew on board, as well as two people on the ground, was directly linked to a maintenance decision made in haste.
In an attempt to save time, American Airlines’ maintenance engineers removed the engine and pylon from the wing of a McDonnell Douglas DC-10 as a single unit, contradicting the manufacturer’s guidance that each component should be removed separately.
This shortcut led to catastrophic consequences.
The lesson here is clear: skipping or rushing maintenance is risky—even deadly.
However, when you schedule regular maintenance, you protect your equipment and everyone in your facility.
Scheduling maintenance is really just taking proactive steps to prevent accidents before they happen, rather than reacting to them after the fact.
Saved Money
Safety can also protect your bottom line.
When you prevent accidents, you also avoid hefty safety fines.
This is just one way how scheduling maintenance can save you money, but the savings don’t stop here.
Unplanned downtime and emergency repairs are some of the biggest hidden costs in any operation.
These emergency fixes typically cost much more than regular, planned maintenance.
Frank Briganti, Director of Program Execution at CACI, has seen this firsthand:
The cost of emergency repairs is usually 2-3 times larger than the cost of properly maintaining equipment. Equipment never seems to fail at the beginning of the month; it waits until you are behind schedule or have a big financial commitment to deal with.
By scheduling maintenance, you can plan your labor resources more effectively and address minor issues before they become big problems.
This reduces the need for emergency repairs and the associated overtime costs, keeping your budget under control.
You also save money on energy.
Properly calibrated and lubricated machinery operates more efficiently, consuming less energy and resources.
This means lower operational costs, improved energy efficiency, and even a smaller environmental footprint.
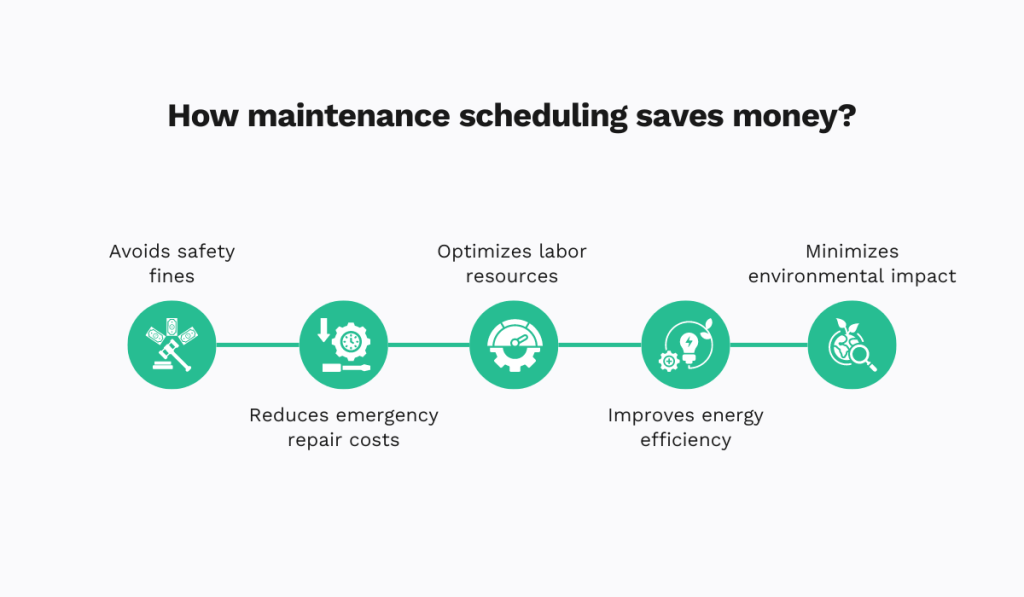
All these translate into significant cost savings over time.
But if that’s not the case, the story is completely different.
What to Be Aware of When Scheduling Maintenance
Scheduling maintenance is more than just picking a date on the calendar.
Several potential pitfalls can throw your plans off course, and many companies struggle with these issues.
In fact, a 2021 report by Plan Engineering found that 20% of companies cite poor scheduling—rarely followed through—as a key challenge in improving facility maintenance.
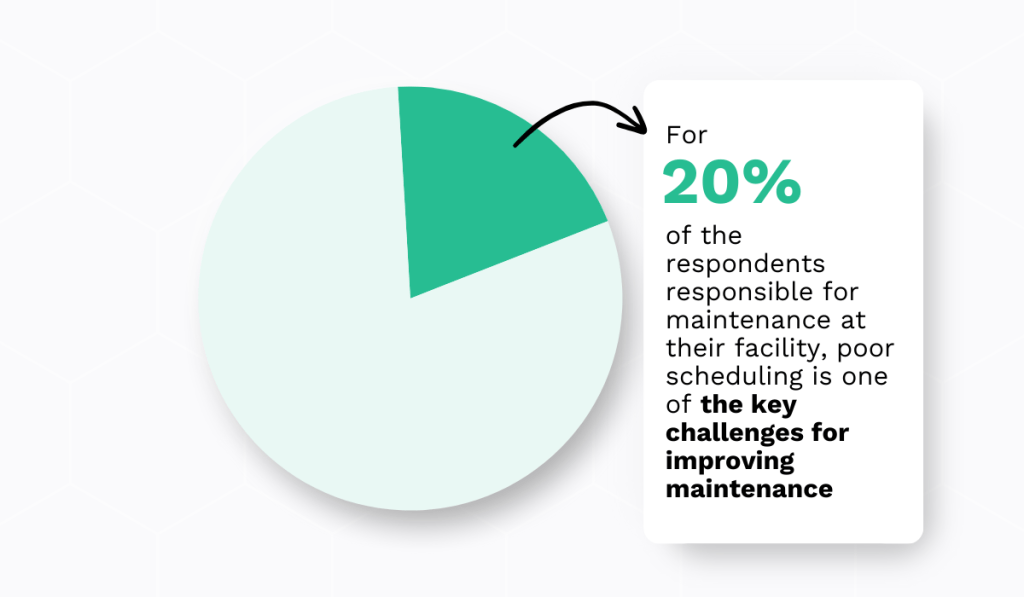
This happens because of maintenance, repair, and operations (MRO) inventory.
Managing that is one of the biggest challenges in maintenance scheduling.
It includes everything from machine oil and lubricants to spare parts like motors and gears, and safety equipment such as masks, earplugs, and hard hats.
If you’re not closely monitoring your inventory, you might schedule maintenance only to discover that you’re missing a critical part, material, or a piece of protective equipment.
For instance, if you schedule maintenance for a production line but realize the needed robotic arm isn’t in stock, you’re looking at costly downtime.
As one industrial maintenance technician on Reddit put it:
Part is $2000 and takes 8 weeks. That downtime would cost like a half million dollars.
Stockpiling MRO inventory might seem like a solution, but it comes with its risks.
Buying and storing excess inventory ties up capital that could be better used elsewhere in your business.
Additionally, some items may become obsolete if they sit on the shelf for too long.
So, it’s all about finding that balance—ensuring you have what you need without overstocking.
Poor coordination and communication can also be a problem in scheduling maintenance.
If maintenance isn’t properly communicated and coordinated, you could end up with situations where a technician is assigned multiple tasks simultaneously or in different locations, with no realistic way to complete them all.
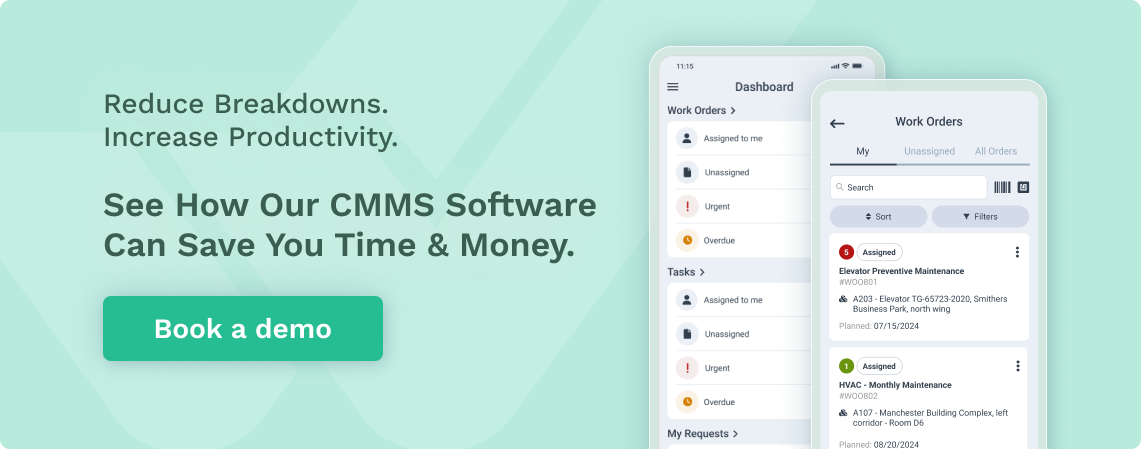
This can lead to:
- Rushed jobs,
- Missed deadlines,
- Poor maintenance outcomes.
Communication between the maintenance team and other departments, like production and procurement, can be challenging.
But doing it right is crucial for maintenance scheduling, as it ensures you have the necessary parts and can align maintenance schedules with production needs.
One way to align different departments with maintenance is through regular meetings.
That’s what they do at Simmons Foods, as Tim Newman, their Maintenance Manager, explains:

Finally, it’s essential to have accurate records of all maintenance activities.
Without them, you risk scheduling maintenance too late or missing it which can, again, cause equipment failures and unplanned downtime.
Good record-keeping helps track past repairs, forecast future needs, and comply with regulations.
However, manually managing all this information can be overwhelming, which brings us to the benefits of using digital tools for scheduling maintenance.
Improving Maintenance Scheduling with CMMS
When it comes to boosting your maintenance scheduling process, a computerized maintenance management system (CMMS) can really make a difference.
This type of software takes a lot of the manual work off your plate.
It automates scheduling, keeps track of what’s been done, and provides fresh data to help you stay on top of maintenance tasks.
Take our WorkTrek, for example.
Its work order management features make it easy to assign and monitor maintenance tasks, ensuring they’re completed on time.
WorkTrek’s easy-to-use calendar interface lets you view and schedule activities by specific dates, days of the week, or set time intervals.
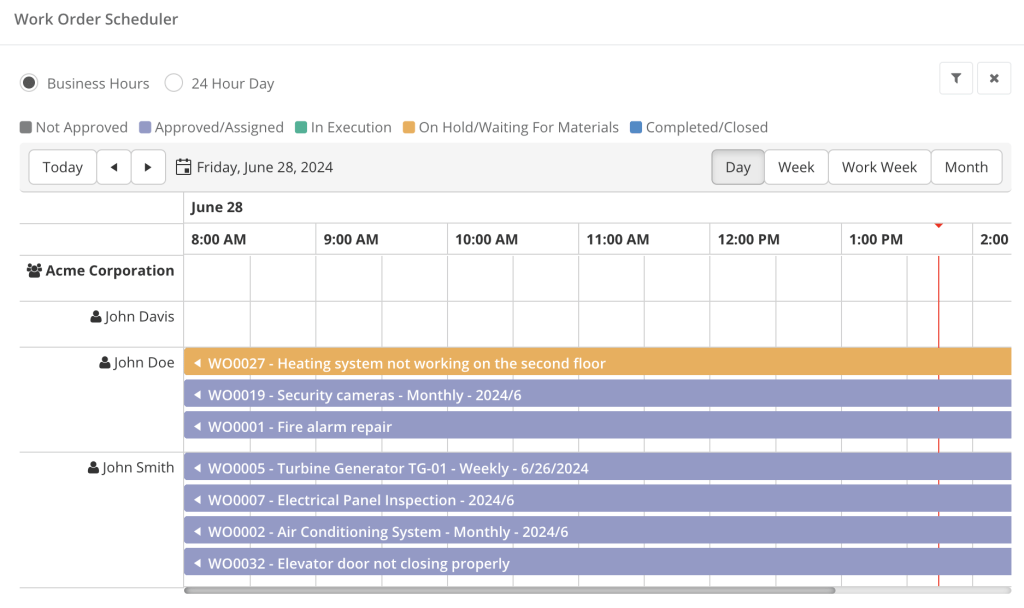
This makes organizing even the most complex maintenance schedules straightforward.
Our CMMS also lets you prioritize tasks based on factors like equipment criticality, safety concerns, or operational impact.
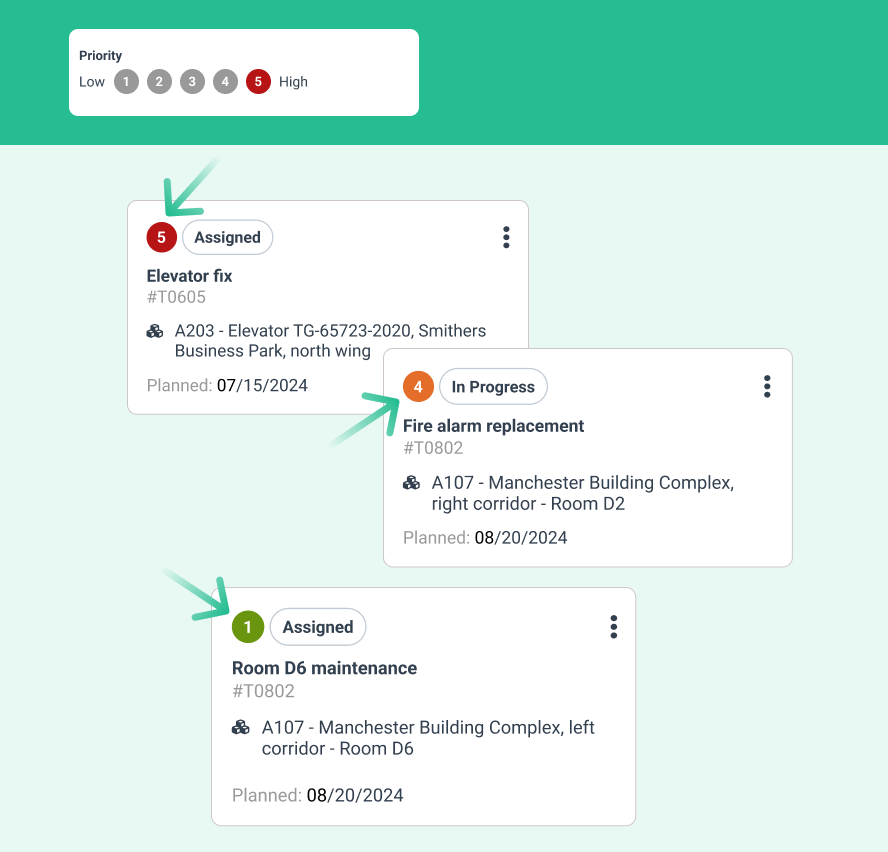
This way, your technicians always work on what’s most important, which helps reduce the risk of unexpected breakdowns or safety issues.
Handling recurring maintenance tasks—like inspections, lubrication, or filter replacements—is a breeze with WorkTrek, too.
With just a few clicks, you can set up recurring schedules so these routine tasks never get overlooked.
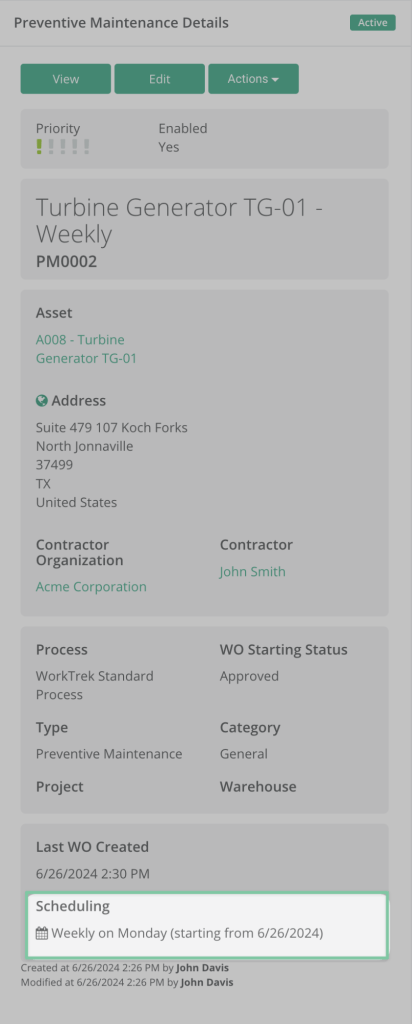
Plus, having access to all previous maintenance data makes it easier to determine when specific equipment needs checking again and what personal protective equipment (PPE) or procedures are required.
This historical data is crucial for accurate scheduling.
By reviewing past work orders, you can see how long similar tasks took and use that information to create more realistic schedules.
Your technicians can also add notes if something didn’t go as planned or if a task took longer than expected.
This feedback lets you adjust future schedules to be even more accurate.
Overall, this level of visibility and control over maintenance is why people like Damir Fabijanković, Service Manager at METUS, choose WorkTrek:
WorkTrek application helped us greatly in better visibility, control, and organization of work. With the WorkTrek mobile application, our technicians have a clearer division of work tasks, which improves their efficiency.
In short, a good CMMS will automate maintenance scheduling and make it more precise and reliable.
Conclusion
After planning, maintenance scheduling is the next logical step.
When done right, it helps you avoid downtime, save money, and keep your facility safe.
To get the most out of your scheduling, make sure your maintenance scheduler stays on top of inventory, communicates with technicians and other departments, and uses past maintenance data to create accurate schedules.
And don’t forget—providing your scheduler with the right tool will make the whole process smoother and more efficient.