Get a Free WorkTrek Demo
Let's show you how WorkTrek can help you optimize your maintenance operation.
Try for freeKey Takeaways
- An organized asset inventory with spare parts on hand reduces repair downtime.
- Preventive maintenance can cut downtime (surpassing $500,000 per hour).
- A CMMS simplifies maintenance scheduling and management.
- Keeping technicians informed and setting realistic timelines prevents rushed inspections.
Effective maintenance isn’t just about keeping machines running—it’s about keeping your entire operation on track.
Equipment failures can spiral into dangerous situations with surging costs without a solid maintenance plan.
But here’s the good news: by adopting a few smart maintenance practices, you can avoid breakdowns, reduce costly downtime, and make maintenance a smooth, integrated part of your production process.
So here are five best maintenance practices that every manufacturing operation should have:
1. Develop a Comprehensive Asset Inventory
A well-organized asset inventory is the backbone of any effective maintenance plan. It’s a go-to guide for every piece of equipment you rely on.
Each inventory entry should include item details, from equipment specifications, maintenance history, location, and OEM recommendations to user manuals.
Source: WorkTrek
By having this information readily accessible, your maintenance team has a clear picture of what’s in the facility, what requires regular care, and what might be nearing the end of its lifecycle.
This enables planners to anticipate needs accurately, and technicians can conduct repairs quickly and precisely.
A detailed inventory also tracks important performance metrics, such as mean time between failures (MTBF).
This data reveals how often breakdowns occur, helping you predict maintenance needs and plan replacements before issues arise.
Additionally, centralizing this data lets you easily track maintenance costs over time.
Source: WorkTrek
This can help you identify high-cost or high-risk equipment and make more informed budgeting and cost-control decisions.
Another critical component of a comprehensive inventory is having essential spare parts on hand.
Maintenance Engineer Willys Juma highlights how important this can be for minimizing downtime:
Illustration: WorkTrek / Quote: Linkedin
If you follow his advice, you’ll be ready when a part breaks down, and you won’t have to wait for shipments or deal with extra downtime.
Handling this level of information, however, becomes challenging without digital tools.
While it’s possible to keep this inventory in spreadsheets, it becomes harder to stay organized the more assets you have.
Asset management software or a computerized maintenance management system (CMMS) becomes invaluable here.
These systems make it easy to update your asset records, access critical information quickly, and have all your asset information in one place.
Source: WorkTrek
As you’ll see later, a CMMS like this can be a game-changer for your maintenance.
All in all, a solid inventory foundation with the right digital tools sets your team up for success and ensures your facility is always ready to respond.
2. Do More Preventive Maintenance
Preventive maintenance is a proactive way to keep equipment running by handling small issues before they become big.
This maintenance type reduces unexpected breakdowns, extends equipment life, and cuts repair costs.
Why is this so important?
The financial impact of downtime speaks for itself.
Siemens’ True Cost of Downtime report found that unplanned downtime in automotive manufacturing can cost over $2 million—per hour!
In the Oil & Gas sector, an hour of downtime costs nearly $500,000.
Illustration: WorkTrek / Data: Siemens
With stakes this high, it’s clear why a solid preventive maintenance strategy is critical for keeping production on track and preventing revenue loss.
And many maintenance professionals recognize these benefits.
One survey revealed that companies moving towards preventive maintenance experience 52.7 % less unplanned downtime.
Illustration: WorkTrek / Data: NCBI
So, how do you set up an effective preventive maintenance program?
Start by creating a risk-based priority system.
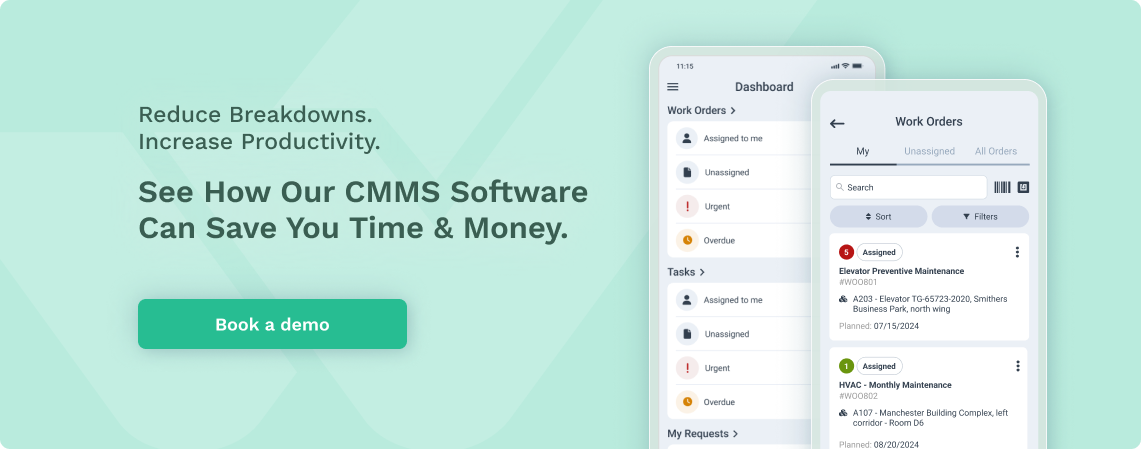
Identify which machines are most critical to your production and schedule preventive maintenance around them.
Trey Eckert, Sales Director at M&S Reliability Group and a former maintenance planner, explains how to determine which assets are the most critical:
Illustration: WorkTrek / Quote: Linkedin
Essentially, focus on the equipment without backups first, so you’re covered where it counts most.
But let’s be real—implementing preventive maintenance isn’t always a walk in the park.
It takes careful planning, diligent scheduling, and a dedicated team to handle it all.
But this is where a CMMS (computerized maintenance management system) can simplify things.
3. Help Yourself with CMMS
When managing maintenance, a CMMS can be one of the best investments for your operation.
A good computerized maintenance management system not only keeps all your asset information organized but also automates tasks like scheduling, tracking work orders, and monitoring inventory levels.
By having all this information in one place, you can see at a glance what’s been done, what’s due next, and what’s running low in stock.
Source: WorkTrek
Let’s take an example from our own CMMS, WorkTrek.
Instead of juggling spreadsheets or hand-written logs, WorkTrek lets you directly set up recurring maintenance tasks, assign them to technicians, and even send mobile notifications to keep everyone in the loop.
For field technicians, these notifications mean they’re updated the minute they’re assigned a work order.
Source: WorkTrek
But that’s not all.
With a few clicks, WorkTrek allows technicians to attach photos of their inspections, review equipment manuals, and check asset specifications on their mobile devices.
Source: WorkTrek
When something urgent comes up, employees can quickly submit service requests through the app or request portal.
Then, you can instantly create work orders and assign tasks, making it easy to prioritize requests and send technicians where needed most.
Source: WorkTrek
One standout feature is WorkTrek’s ability to integrate with meters.
For example, if your water meter reaches a certain level, you can input that information into the system, and WorkTrek can automatically create a work order for an inspection or repair.
Source: WorkTrek
This kind of automation ensures that maintenance happens exactly when needed, so you avoid all those costly breakdowns and unplanned downtime.
In short, a good CMMS like WorkTrek gives you more options than spreadsheets ever could, helping you keep equipment running smoothly without the chaos of manual tracking.
Think of it as an extra set of hands that keeps everything organized and ready when needed.
However, even with this fantastic tool, planning, and scheduling maintenance requires thoughtfulness to minimize disruption to production.
That leads us to our next best practice.
4. Plan for Maintenance During Slow Times
To minimize disruptions to production, schedule maintenance during low-demand times—like overnight shifts or weekends.
It’s no wonder why banks or phone providers schedule app maintenance late at night.
They choose off-peak times to affect as few users as possible.
The same principle applies to manufacturing: performing maintenance during slow periods lets you keep productivity steady without impacting operations.
After all, maintenance is costly—not just in resources but in time.
In fact, 31% of facilities report they spend 30 hours or more each week on scheduled maintenance.
Illustration: WorkTrek / Data: Plant Engineering
Imagine if all those hours were taken out of production time—it would dramatically impact output every week.
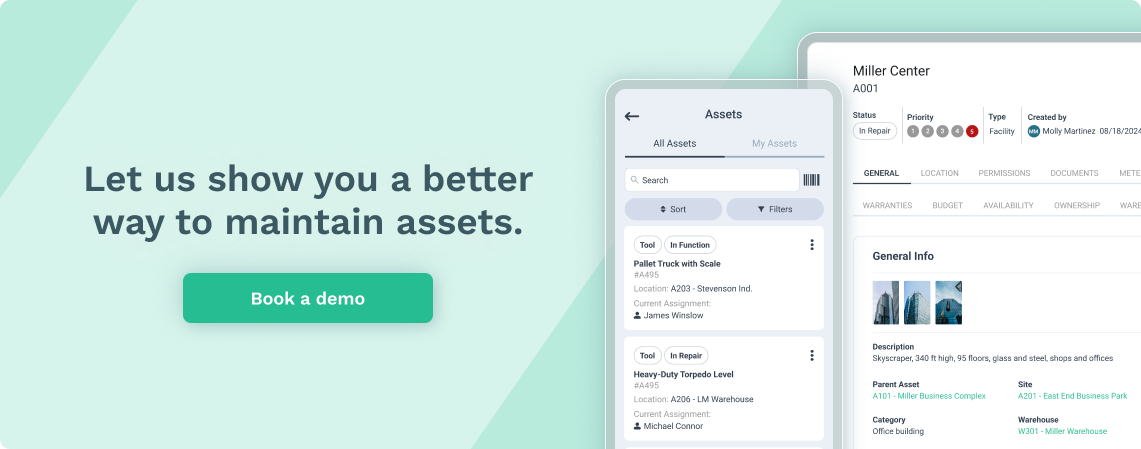
Instead, you avoid interruptions by timing maintenance around low-demand periods and maintain a consistent production flow.
You need strong coordination between the maintenance and production departments to make this possible.
To make this coordination smoother, Sachin Fatangare, Head of Quality & EHS at Ingersoll Rand, suggests using a centralized scheduling system:
Illustration: WorkTrek / Quote: Linkedin
But for that, you first need a tool that can access isolated production data from systems such as SCADA, PLC, and BMS.
Luckily, many modern CMMS have this ability.
By pulling real-time data on production cycles and asset conditions, a CMMS can help you identify ideal maintenance windows with minimal disruption to operations.
With these insights, planning maintenance around production flow becomes a straightforward, data-driven process.
5. Keep Your Maintenance Staff Informed
A maintenance plan is only as good as the team that carries it out.
For maintenance to be effective, your technicians need clear, up-to-date information on every relevant detail—from recent equipment changes and new safety protocols to troubleshooting best practices.
When staff is well-informed, they perform tasks more accurately and efficiently, reducing the risk of downtime and costly errors.
On top of that, they can follow safety and compliance guidelines.
According to a recent survey, 81% of manufacturing companies cite staff training as their top strategy for compliance, while 69% emphasize building a safety-focused culture.
Illustration: WorkTrek / Data: Limble
Clear communication supports these goals, helping staff follow procedures to stay compliant and avoid costly mistakes, creating a safer, regulation-ready work environment.
Regular training and open communication also empower technicians to address maintenance needs proactively.
With a solid understanding of equipment updates and specific failure points, they can spot issues before they escalate.
However, for proactive maintenance to succeed, management must also set realistic timeframes.
However, this is often not the case, as Preston Powell, a diesel mechanic, notes:
“They preach faster, faster, then they miss putting oil in the engine… and it blows up.”
Rushing maintenance tasks may seem efficient but can lead to expensive repairs and unexpected downtime.
Another experienced technician, Paul Orme, highlights the dangers of prioritizing speed over thoroughness:
Illustration: WorkTrek / Quote: Linkedin
Rushing technicians may save time in the short term, but it can compromise equipment reliability and lead to preventable breakdowns later on.
The takeaway?
Equip your team with knowledge, prioritize training, and set practical expectations.
Only then can technicians complete tasks safely and thoroughly and catch potential issues before they fail.
Open communication and realistic timelines from management foster a culture where quality maintenance is achievable, leading to reliable production and fewer unexpected costs.
And that’s what every manufacturer wants, and there are no two ways about it!
Conclusion
Stakes are high in manufacturing.
That’s why a successful manufacturing maintenance strategy requires proactive planning, coordination, and consistent communication.
From implementing an efficient CMMS to prioritizing staff training, each practice works together to keep operations smooth and equipment running at peak performance.
By adopting them, you’ll be well on your way to building a resilient maintenance strategy that supports long-term success in your manufacturing facility.
So, make these five best practices a part of your operations.