Get a Free WorkTrek Demo
Let's show you how WorkTrek can help you optimize your maintenance operation.
Try for freePoor work order tracking can cause significant issues, like missing deadlines, losing track of tasks, and overspending.
To address these issues, the first thing to know is that there’s no one-size-fits-all solution.
While some businesses have complex workflows requiring sophisticated tracking, others may only need simple methods for a small number of work orders.
The key is finding what works best for you.
This post will help you do that by reviewing six different methods of tracking work orders.
Paper-Based Work Order Tracking
A paper-based method is the most basic and accessible way of tracking work orders.
It may also be the most cost-effective method since it requires no setup costs, though this comes with a caveat.
According to some sources, paper documents are generally 141x more expensive than digital ones.
However, the scenario is likely reversed when you’re handling a small number of work orders that can be easily created and stored manually.
So, again, it will be important to assess your individual needs and situation.
This method works best for very small businesses, solopreneurs, and one-off tasks.
Managers who use it typically rely on pre-made paper forms to create and assign work orders.
They fill them out, place them in a shared location like a tray box, or hand them over directly to technicians. Upon completion, they store them for future reference.

Pretty straightforward, right?
That’s also perhaps the biggest benefit of this method. There’s no learning curve, software setup, or extensive training required.
Both technicians and managers can adopt this system right away.
They also don’t have to worry about making difficult-to-fix mistakes, which can be common with complex software.
For example, adding a wrong entry to one paper form doesn’t affect other work orders or disrupt the system.
However, one drawback of this method is a potential lack of efficiency, especially regarding data retrieval and communication between the parties.
Each party must exchange and process the forms on time to ensure smooth workflow.
You’ll also need a safe place to store them.
So, ensure you have file cabinets or similar storage ready and start systematically archiving orders.
Whiteboards or Corkboards
Whiteboards or corkboards fix one of the drawbacks of paper forms: lack of visibility and oversight.
They provide a visual, centralized space for displaying all work orders, making it easier to track which tasks are being worked on and by whom.
This helps managers evenly spread the work across technicians and ensure all orders are handled.
Specialized boards with pre-made tables and templates can be handy, as they ensure you never forget to add any important details to your work orders.

Alternatively, you can find options that combine whiteboards with corkboards to leverage the best of both worlds.
For example, you can add paperwork orders to the corkboard and use the whiteboard to jot down others on the fly.

Just like paper forms, whiteboards, and corkboards are straightforward, simple, and accessible to use.
They provide quick updates, let everyone easily track order statuses, and delegate tasks.
However, they’ll only work for teams that are in the same physical location.
If your team is largely in the field, other methods mentioned below will likely be more useful.
With this in mind, boards can work for maintenance teams in:
- manufacturing
- facilities management
- retail stores and warehouses (for daily task assignments)
Even if you don’t use them to track work orders, whiteboards can still be very useful.
For instance, they can be amazing tools for brainstorming sessions and visualizing maintenance workflows.

This can help you determine the best general structure for managing and organizing work orders, making daily management easier even if it relies on another method.
Spreadsheets (Excel or Google Sheets)
The two methods we’ve mentioned so far are extremely easy to use but have significant data drawbacks.
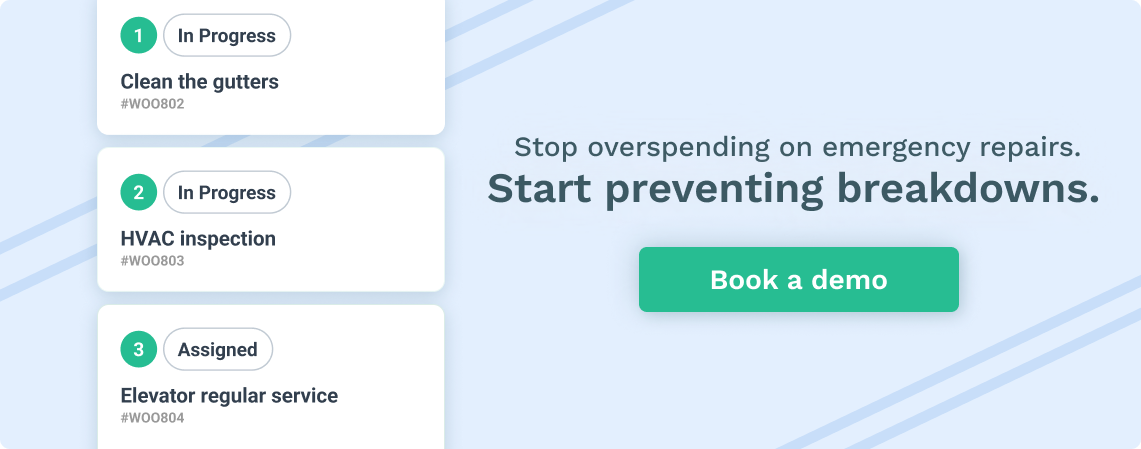
Both methods make data easily lost and difficult to access or share.
Spreadsheets fix these issues while offering almost the same level of simplicity. You can easily customize them and leverage ready-made templates for recurring orders.
In fact, we already prepared one for you. You can download it for free and use it.

Unlike paper forms or boards, spreadsheets can be easily shared.
If you’re using local spreadsheet files, you can share them via email or a file-sharing service like Dropbox.
Cloud platforms, like Google Drive, are even more convenient because they allow you to add users and provide direct access.

Also, spreadsheets let multiple users collaborate and edit data. This can, however, be both a pro and a con, so make sure you establish editing guidelines upfront.
Admittedly, spreadsheets are somewhat more complex than the good old pen and paper, but most modern workers can quickly master them.
Pair that with the fact that spreadsheets also offer advanced features, like sorting, filtering, and basic automation, and it becomes evident they’re much more suitable for contemporary businesses.
As Greg Christensen, the Vice President of ProjectHub.com, says, spreadsheets are the first step to true digitization.
This is especially important for small to medium-sized businesses needing a more structured approach.
Even simple automation, like SUM, AVERAGE, and VLOOKUP functions, can help reduce errors in more complex work orders.

Manual calculations can be reduced to a minimum, making decision-making quicker and less prone to errors.
It’s also easier to track simple KPIs, such as completion rates or costs, using a spreadsheet rather than paper or a whiteboard.
Project Management Systems
While spreadsheets can work for smaller teams with simple work orders, they won’t be the best choice for those managing multiple ongoing orders simultaneously.
This is often the case in marketing, software development, and consulting industries. Managers typically manage several complex projects involving many different team members simultaneously.
Such projects usually require continuous work progress monitoring, visualization, and clear accountability, which spreadsheets don’t provide.
Project management systems (PM systems), like Trello, Asana, or Monday.com, will prove more useful in these cases.

As you can see above, project management systems have many useful features.
They range from tools for tracking due dates and statuses to collaboration features that let entire teams communicate in a single interface.
For example, compare that to managing work orders in spreadsheets and then using several other tools just to get feedback from various team members. The process becomes much more complicated and time-consuming.
Even simpler project management tools like Trello can make work order tracking significantly easier.
They allow you to collaborate with different team members, visualize work orders, and share any necessary files all in one place:
More robust systems also offer integrations, automation, and reporting functionalities.
Here are a few examples:
- Integration: By integrating your PM system with a CRM like Salesforce, you can automatically enrich work orders with ready-to-go customer data.
- Automation: Work orders can automatically get assigned to the right person, flagged for review, and more.
- Reporting: Automatically-generated reports offer quick insights into project progress, team performance, and upcoming deadlines.
As you probably realize by now, project management tools can range from very simple to very complex.
The key here is to choose the level of complexity that matches your needs. That way, you’ll avoid overwhelming team members while ensuring you can adequately address all your needs.
Accounting Systems
Accounting systems like Xero or Quickbooks are not meant to track work orders.
Still, many businesses use them as workarounds.
In some cases, teams just don’t want to deal with adopting new software and the challenges that come with it.
For many businesses, though, tracking work orders alongside financial data is extremely beneficial.
This includes:
- Service-based businesses who bill per task, like electricians or plumbers.
- Companies that need detailed cost tracking for labor and materials.
- Businesses aiming for seamless financial audits and compliance.
The biggest benefit of using accounting systems to track work orders is that it simplifies invoicing, billing, and cost tracking.
Storing both work orders and financial data in one system can reduce errors, improve accuracy, and save time spent on duplicating data.
It can also help you improve budget planning and enable better, data-driven decisions.

The issue, however, is that most accounting systems don’t offer a straightforward way to create or track work orders.
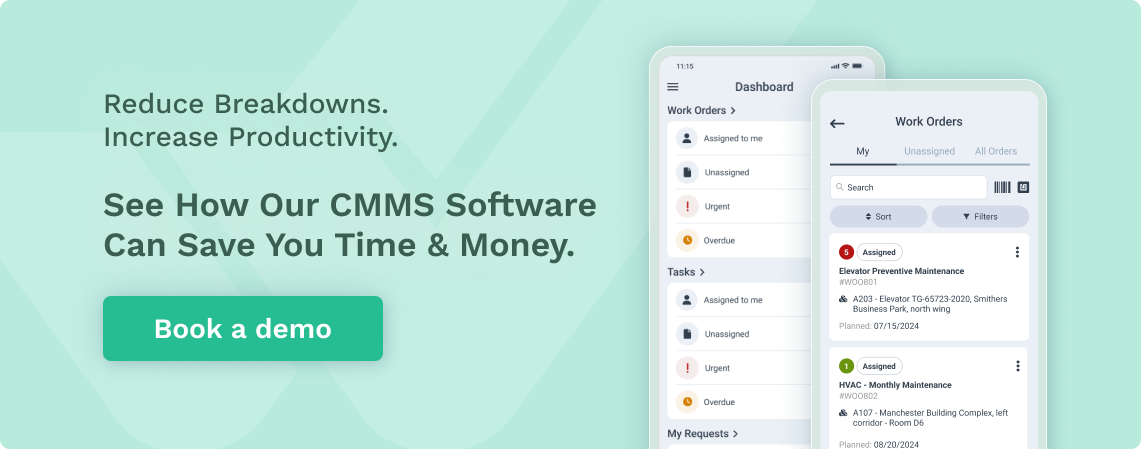
With most, you’ll have to settle for makeshift alternatives.
For example, with QuickBooks, you could try customizing Sales Orders or using Estimates.
You can tag the estimates you use for work order purposes as ‘Work Orders,’ as shown below.

Of course, the problem here is that it becomes difficult to distinguish work orders from actual sales orders or estimates, which can quickly create a messy situation.
Many teams prefer to integrate accounting systems with other specialized software for tracking work orders.

This integration allows you to associate work orders with financial data without creating chaos.
The disadvantage is that you’ll still need another software. So, it’s best to prepare for training and some potential work disruptions in advance.
Also, choosing software that integrates with your existing accounting systems is important.
Most systems have a publicly available list of possible integrations on their websites:

If you don’t see your desired app on the list, try contacting either software provider to check if integration is still possible.
Specialized Work Order Management Software
This list wouldn’t be complete without specialized work order management tools.
They’re the most obvious but also the best choice for most businesses.
As Zapier puts it, having a drawer full of sharp knives is better than one blunt cleaver.
Since specialized software is designed for specific tasks, it often performs exceptionally well.
This typically leads to higher productivity, easier adoption, and less downtime.
These advanced tools are often industry-specific, enabling comprehensive work order management.
This is essential for large enterprises with complex workflows and high work order volumes.
Most specialized software includes everything you’ll need to manage work orders effectively, from scheduling and real-time updates to inventory management and analytics.
As an example, consider the WorkTrek dashboard:

It offers a quick overview of the most important metrics, like open, urgent, and closed work orders.
By clicking Work, you can get more details about each, create new work orders, or manage existing ones.
This includes assigning them to different team members, describing the work orders, adding due dates, and more:

Finally, cloud-based solutions like WorkTrek also facilitate remote access and team collaboration.
There’s no need to switch between multiple different apps.
Users can collaborate and communicate through the same interface, usually by leaving comments and tagging others with @mentions.

Like project management systems, some work order software solutions offer several work order views for easier management.
For example, alongside lists, WorkTrek displays maps:

This way, users see the list of active work orders and their geolocation. This comes in handy when managing multiple facilities across cities or states.
Specialized systems work best for companies that need more, whether detailed reporting, parts and labor management or preventive maintenance capabilities.
They’re also typically the best fit for manufacturing, healthcare, and construction industries, where precision and scalability are essential.
Conclusion
Effective work order tracking is all about matching your method to your business’s needs.
For businesses with simple workflows or a limited number of work orders, straightforward methods like paper forms can be practical and efficient.
On the other hand, specialized work order management software is the best choice for more complex operations.
The key takeaway: there’s no universal approach. Choose what works best for you.
By finding the right method, you’ll not only track work orders but also set your team up for success and smoother operations.