Get a Free WorkTrek Demo
Let's show you how WorkTrek can help you optimize your maintenance operation.
Try for freeWe all know maintenance is vital, no matter your industry.
When done right, it can save money, reduce unplanned downtime, and even extend the lifespan of valuable assets.
But what happens when maintenance goes wrong?
In this article, we’re answering that question by outlining six of the worst maintenance disasters ever.
We’ll unpack the chain of events, explore the costly consequences, and reveal exactly what maintenance mistakes were made.
So, read on because each story has a unique lesson and is packed with insights that can help you improve your own maintenance game and the safety of your operations.
The Deepwater Horizon Oil Spill
In 2010, the BP Deepwater Horizon rig in the Gulf of Mexico exploded, killing eleven people and injuring 17 others.
Below, you can see fireboat response crews attempting to extinguish the blaze aboard the oil rig.
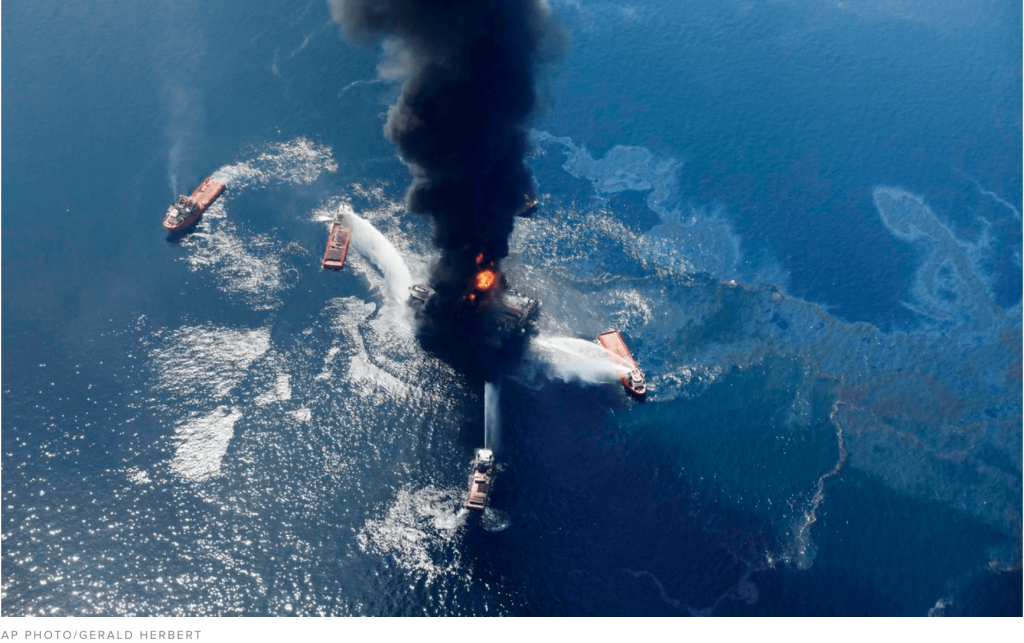
To this day, this remains the world’s largest marine oil spill, releasing an estimated 4.9 million barrels of crude oil—equivalent to 779 million liters, or over 300 Olympic swimming pools.
The accident stemmed from a “well integrity failure,” which led to losing control over the well’s pressure.
The blowout preventer (BOP), a device designed to seal the well in such an event automatically failed to activate, too.
This allowed high-pressure oil and gas to escape, which ultimately caused a series of explosions on the rig.
But what exactly caused this failure?
In short, lack of proactive maintenance and lapses in safety procedures.
An independent federal agency (CSB) investigating industrial chemical accidents found that BP hadn’t performed regular inspections or testing to identify latent failures of the BOP’s emergency systems.
So, is it surprising that his vital piece of equipment malfunctioned?
Not at all.
According to an article by Vysus Group, back then, “the industry was habitually very reactive to maintenance issues because it could afford to be.“
But throwing money at problems doesn’t cut it, especially when maintaining such dangerous machinery.
Simply reacting to equipment failures only heightens the risk of unforeseen damage, which impacts production, cost, and, most importantly, safety.
On the other hand, research shows that predictive and preventive maintenance strategies can greatly reduce downtime and severe asset damage.
With fewer breakdowns, safety improves, too.
Sure, some accidents may be unavoidable, but with a vigilant maintenance plan, the risk of such devastating events can certainly be reduced.
The Phillips Disaster of 1989
In 1989, a catastrophic explosion rocked the Phillips Petroleum plant in Pasadena, Texas, claiming 23 lives and injuring 314.
Below, you can see the area affected by the explosion.
What exactly went wrong?
To cut costs, Phillips had subcontracted maintenance work on their polyethylene reactor to Fish Engineering and Construction, who had a questionable safety record even before this disaster.
For example, in one earlier incident, a Fish employee opened gas piping without properly isolating the line, leading to a deadly explosion that killed one worker and injured four others.
On the day of the accident, it was, yet again, a Fish employee who failed to secure a valve on the polyethylene reactor properly.
As a result, 85,000 pounds of highly flammable ethylene-isobutane gas was released into the plant.
Within two minutes, the massive gas cloud ignited, detonating with the force of two-and-a-half tons of dynamite—a blast so powerful it registered 3.5 on the Richter Scale.
A subsequent OSHA investigation found that both Phillips and Fish were responsible for this disaster.
As per their report:
At the conclusion of the investigation (April 19, 1990), OSHA issued 566 willful and 9 serious violations with a combined total proposed penalty of $5,666,200 to Phillips 66 Company and 181 willful and 12 serious violations with a combined total proposed penalty of $729,600 to Fish Engineering and Construction, Inc., a maintenance contractor on the site.
Yes, it was a Fish employee who made the mistake. Still, it was also revealed that Phillips lacked adequate standard operating procedures (SOPs), which contributed to the overall unsafe work culture.
Unfortunately, Kristen Panella, founder of 2SAFE Consulting, a full-service provider for companies’ environmental health and safety needs, says it’s quite common for companies to neglect SOPs development and training:
No. 1 [safety challenge] is lack of knowledge.
I’ll give you a good example. I was at a facility, and a gentleman was in a forklift. It lifted him up, and he had to go into the racks and grab whatever the product was, go back on the forklift and come back down. He was not wearing fall protection. I said, “You’re 20 feet in the air. Why aren’t you wearing fall protection?” He said, “You’re the first person to say anything about that.”
This is a big problem because these procedures are created to protect workers, particularly those working in high-risk environments with hazardous machinery and materials.
And if they’re not properly implemented, the consequences can be dire.
The Phillips incident serves as clear proof.
The Morbi Bridge Collapse
Now, here’s a more recent story to remind us that maintenance disasters aren’t just a part of history.
On October 30, 2022, a pedestrian suspension bridge over the Machchhu River in Morbi, Gujarat, India, collapsed, leading to the tragic deaths of at least 141 people and injuries to over 180 others.
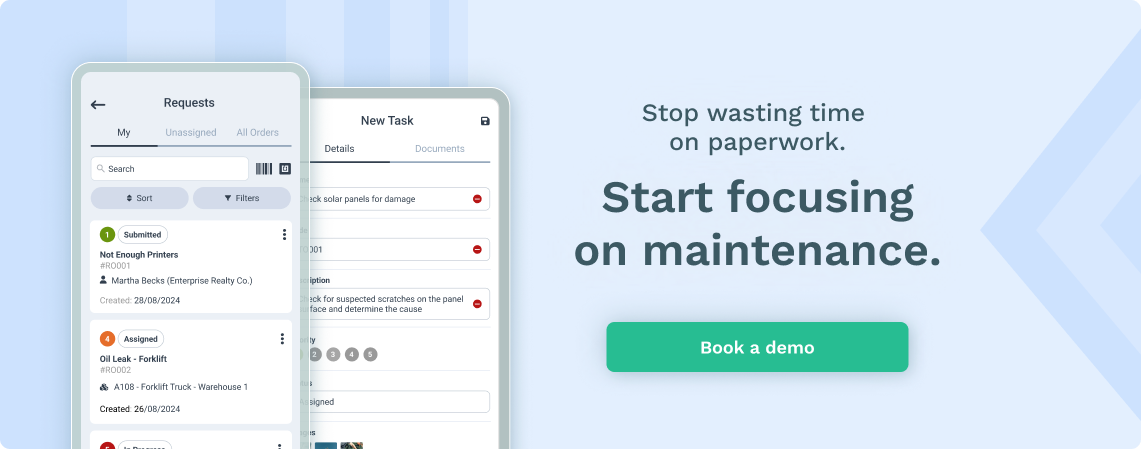
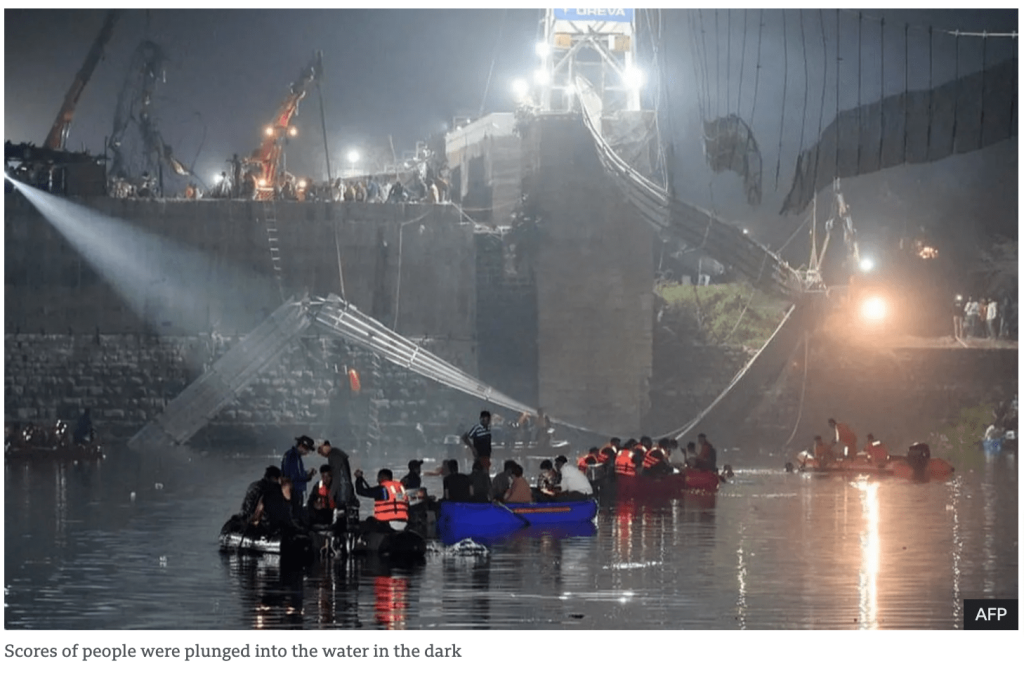
This 137-year-old bridge had just reopened after being repaired—so what happened?
The answer is a frustrating mix of neglect and unqualified handling.
As it turns out, while the bridge’s flooring was replaced, the original aging cables were not.
However, according to Chief Justice Sunita Agarwal, even the flooring wasn’t done properly:
When you are repairing a heritage structure, you need to ensure that the same material is used. You cannot change the material. What happened in Morbi? The old wooden planks were changed with Aluminum.
Therefore, given that the cables were rusted, with broken anchors and loose bolts, they just couldn’t withstand all that added weight.
Here’s where it gets even more unsettling: the company responsible for the bridge’s maintenance is best known for manufacturing clocks.
Not exactly someone you’d expect to be able to handle complex infrastructure projects, right?
The lesson here is clear: hire the right people for the job.
But the story also highlights a larger, more pressing issue within the maintenance industry: a shortage of skilled labor.
A recent survey by ABB reveals that 43% of companies currently face challenges in recruiting maintenance staff.
This is naturally causing serious issues.
From increased unplanned downtime to project delays, keeping your operations running smoothly is extremely hard without skilled maintenance personnel.
Nevertheless, relying on unskilled replacements shouldn’t be our go-to solution.
To keep operations safe and efficient, we must properly address this skills crisis and invest more in high-quality training and upskilling programs.
That’s the only way to equip new generations with the knowledge necessary to prevent the next Morbi bridge incident.
The Romeoville Refinery Explosion of 1984
Shortly before 6 p.m. on July 23, 1984, a set of explosions at the Union Oil Co. refinery in Romeoville, Illinois, killed 17 workers and launched a 34-ton tower into a nearby field.
According to the Chicago Tribune, a second explosion was so intense that debris struck an airplane flying 1,500 feet above the plant.
Here’s a clip of the news report about the accident:
Who would have thought it all began with a small crack in a circular weld?
An operator attempted to close the main inlet valve to stop gas from leaking from the crack, but the crack only grew bigger, releasing flammable gas that ignited within moments.
The vessel, in service since 1970, had undergone numerous repairs and modifications before the incident.
All these years of pressure and repairs had finally taken a toll.
A repair weld connecting a replacement section to the original structure caused numerous tiny cracks throughout the vessel.
Over time, hydrogen started to seep in, quietly expanding those tiny cracks.
The court later found that the refinery had failed to adequately inspect for cracks near field welds or pressure vessels exposed to hydrogen.
Even when they did inspect, the checks were largely visual rather than using more effective techniques like magnetic particle testing, liquid dye penetrant testing, or angle beam ultrasonic testing.
This catastrophe is a stark reminder of why proper condition monitoring is crucial in preventive maintenance.
With a set of appropriate condition-monitoring techniques and processes, we can get insight into assets’ true conditions, which allows us to schedule maintenance before any major problems happen.
According to Bently Nevada, 90% of equipment failures are not time-based anyway.
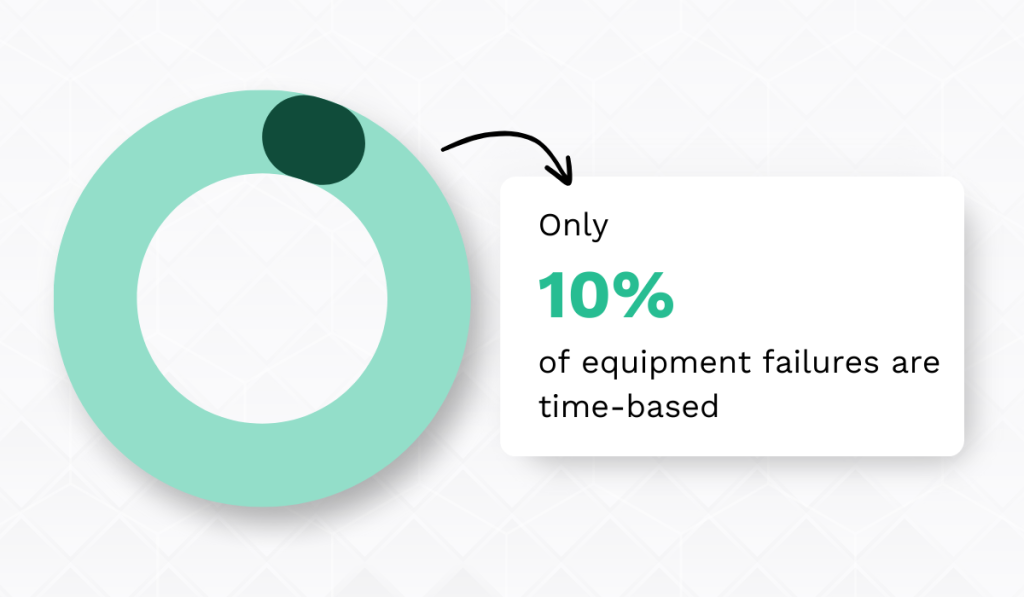
This means that relying on maintenance schedules based solely on predetermined time intervals, without considering a machine’s actual health, is ineffective.
Unfortunately, they had to learn this the hard way at Union Oil.
The China Airlines Flight 611 Crash
China Airlines Flight 611 on May 25, 2002, was supposed to be just another routine trip from Taiwan to Hong Kong.
But 20 minutes after takeoff, the Boeing 747-209B operating the route suddenly disintegrated midair, scattering debris into the Taiwan Strait.
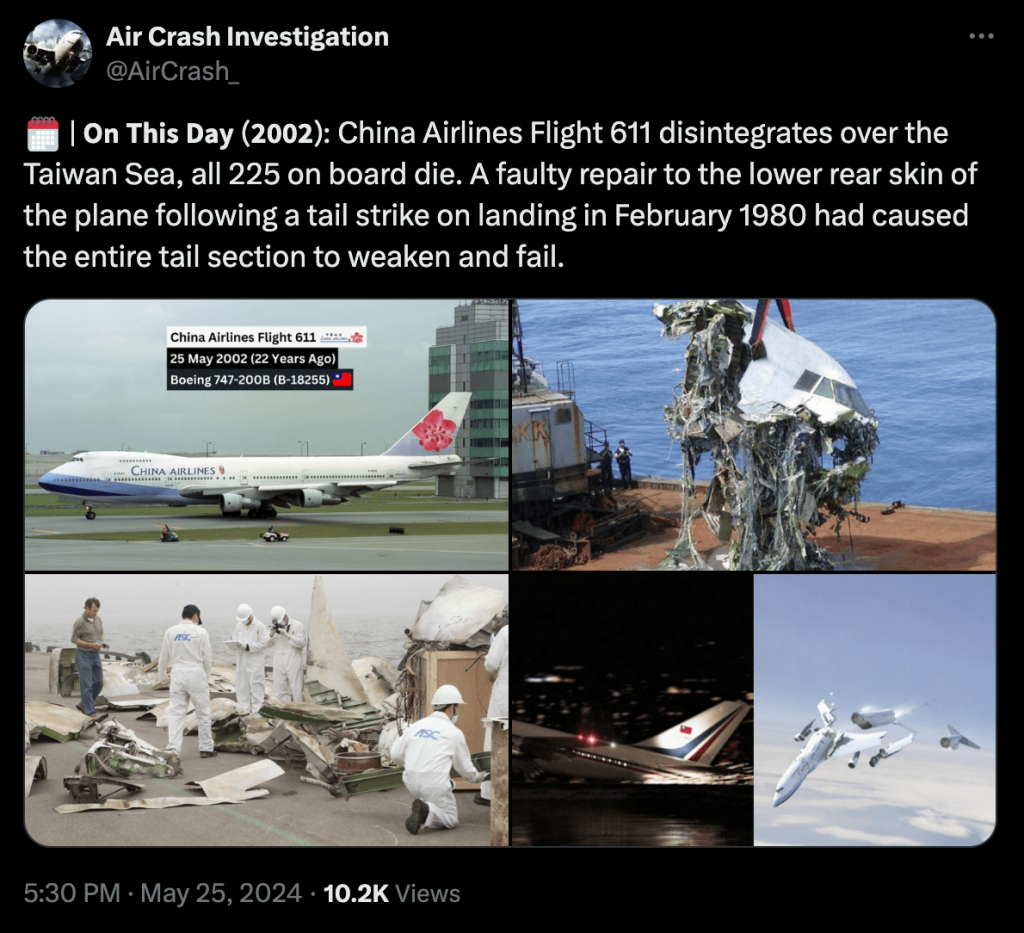
All 225 people aboard lost their lives, leaving investigators scrambling to understand what went wrong with a plane that, on the surface, seemed in working order.
What they discovered was a ticking time bomb that had been quietly waiting to go off for over two decades.
In February 1980, the same aircraft scraped its tail against the runway while landing in Hong Kong during a flight from Stockholm to Taipei.
The aircraft was depressurized, ferried to Taiwan, and repaired by a China Airlines team.
However, the repair did not comply with the Boeing Structural Repair Manual (SRM).
The SRM specified that repairs should either replace the damaged skin entirely or cut out the damaged area and install a reinforcing doubler plate to restore structural integrity.
Instead, the China Airlines team applied a doubler plate over the damaged area without removing the skin.
To make matters worse, the installed doubler plate was too small, meaning the repair offered no protection against crack propagation in regions beyond the doubler’s reach.
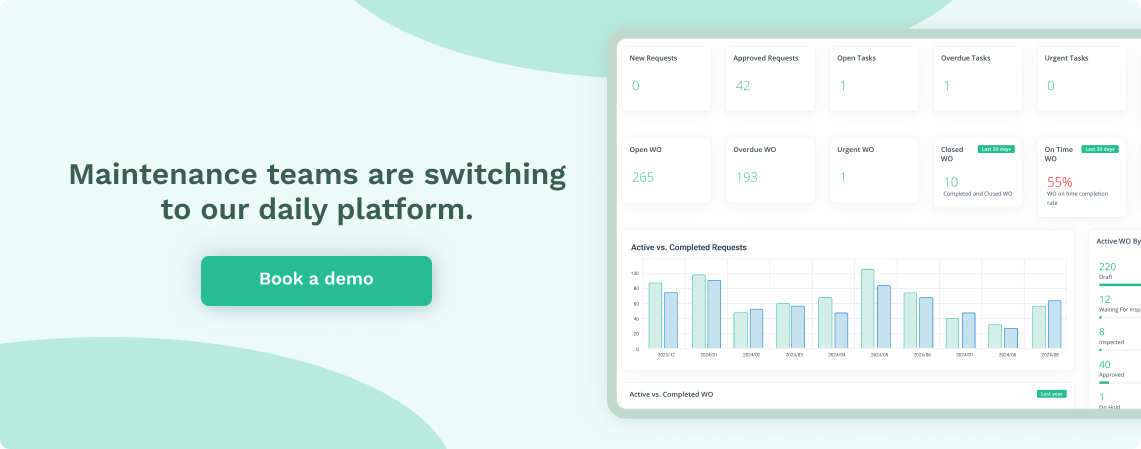
Over time, with repeated pressurization and depressurization during flight cycles, cracks began to form around these exposed areas until the hull catastrophically failed in midair 22 years later.
You can learn more about the incident on the official YouTube channel of Mayday: Air Disaster. This dramatic non-fiction series investigates high-profile air disasters:
It’s also important to note that the plane was about 22 years old and approaching retirement age.
In general, aging aircraft is a big challenge for the aerospace industry, as airlines often keep older planes in service longer than they should to meet demand.
McKinsey analysis indicates that aircraft retirement rates will be approximately 24% lower from 2024 through 2026 compared to 2010–2019.

The problem is that older planes require far more care, and skipping steps or rushing repairs is a gamble no airline can afford to take.
Flight 611’s fate shows the heavy price of cutting corners.
In aviation, there’s no room for compromise—only absolute precision and adherence to safety standards can keep passengers safe in the skies.
The Valero McKee Refinery Propane Fire
On February 16, 2007, a propane fire erupted at the Valero McKee Refinery in Sunray, Texas, north of Amarillo.
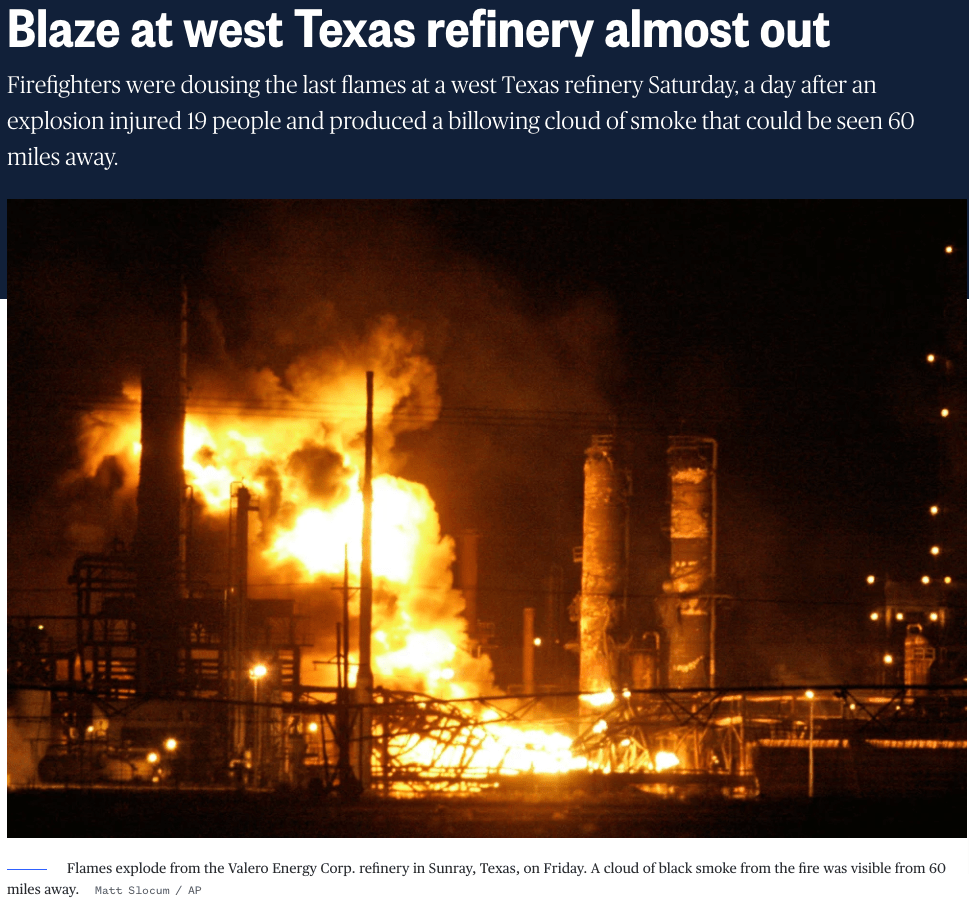
As a result, three workers sustained severe burns, and the refinery had to be shut down.
The trouble started in the refinery’s propane deasphalting unit, where high-pressure propane separates gas oil from asphalt.
Propane leaked from a weakened piping elbow damaged by ice, which had been out of service since the early 1990s.
The problem was that the refinery operators never thoroughly evaluated how to decommission this idle piping properly.
Instead of removing or freeze-protecting it, they simply closed off valves, inadvertently creating a “dead leg”—a section of piping with no flow.
This was a big mistake.
Over time, water seeped past the closed valve, pooling at a low point in the piping.
During a cold snap in early February 2007, the water froze, expanded, and cracked the elbow (shown below).
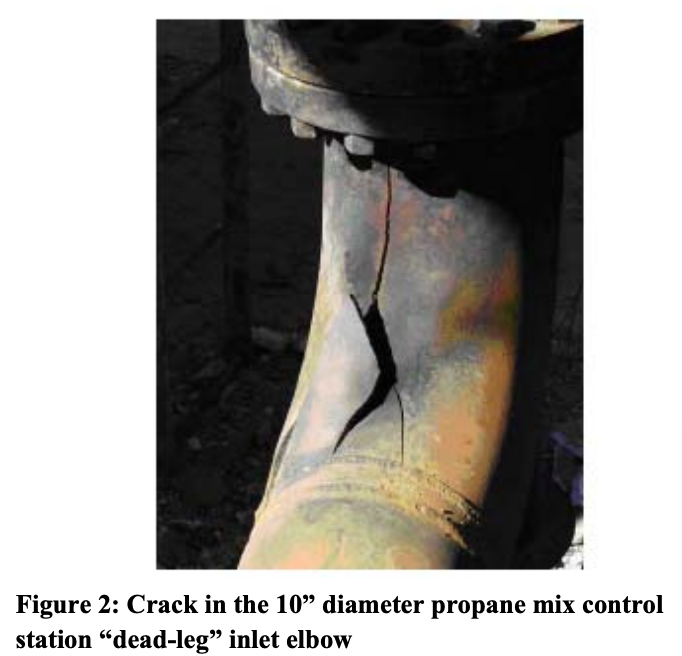
Then, on February 16, as temperatures rose, the ice melted, and high-pressure liquid propane surged through the leaking valve and escaped through the fractured elbow.
Within seconds, an estimated 4,500 pounds of propane per minute poured into the air, forming a massive flammable vapor cloud that drifted toward the boiler house.
Investigators believe the vapor later met an ignition source, triggering a powerful explosion.
In the video below, you’ll find a 3-D animation reconstructing the accident sequence, shedding light on the disastrous chain of events.
This incident illustrates how even infrequently used equipment can pose significant risks if not properly maintained.
Had the refinery implemented an effective program to identify and freeze-protect inactive piping and equipment, this tragedy could have been prevented.
But, unfortunately, it’s easy to forget about idle assets until it’s too late.
Conclusion
Reflecting on these tragic stories, it’s clear that the importance of maintenance should never be underestimated.
By sticking to standard procedures, prioritizing regular inspections, and proper condition monitoring, we can prevent many risks before they arise.
However, when we skip these steps, the results can be devastating: wasted money, damaged equipment and infrastructure, and, worst of all, lives in harm’s way.
The stakes couldn’t be higher.
So, let’s commit to learning from these accidents and do our best to ensure that the same mistakes are never made again.