What is the Economic Life of Assets?
Economic life represents the optimal period when an asset provides the most significant net financial benefit to an organization, balancing acquisition costs, operating expenses, maintenance costs, and performance degradation against its productive value. This period typically ends when the total cost of ownership exceeds the asset’s contribution to revenue or when a replacement would be more economically advantageous.
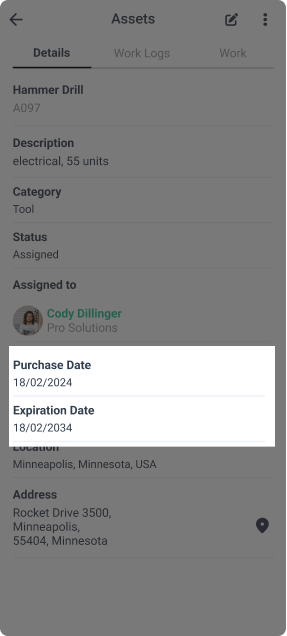
From a maintenance perspective, economic life factors include the increasing frequency and cost of repairs as equipment ages, declining performance efficiency, higher energy consumption, and growing reliability risks. It also considers technological obsolescence, where newer equipment might offer significant operational advantages or cost savings that justify replacement before physical deterioration necessitates it.
The calculation of economic life involves analyzing the point where the combined costs of maintenance, operation, and depreciation reach their lowest average annual total. This intersection helps maintenance organizations make informed decisions about equipment replacement timing and optimize their maintenance strategies by preventing premature replacement and costly asset overretention.
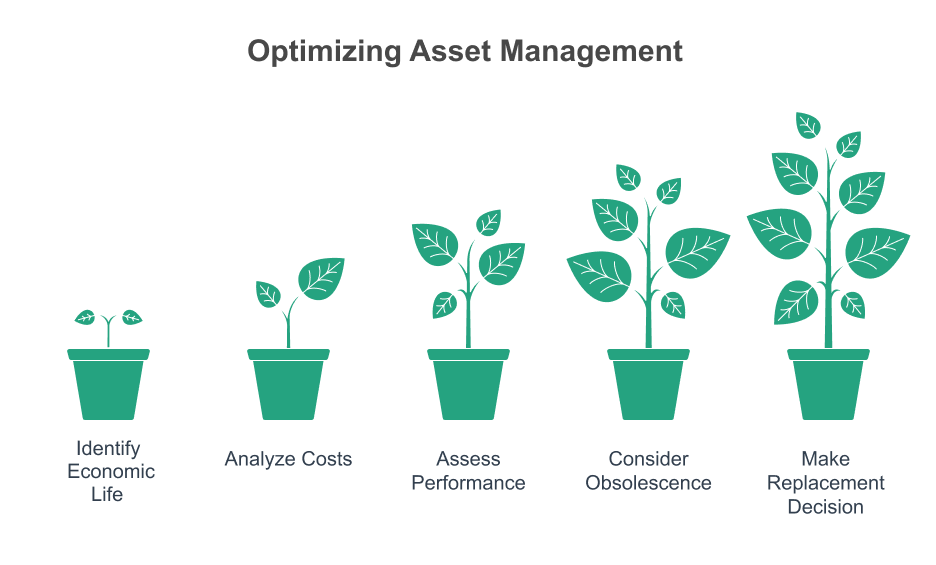
Organizations use this metric to develop maintenance strategies, plan capital expenditures, and establish equipment replacement cycles. It’s particularly crucial for budget planning and resource allocation, as it helps predict when significant capital investments will be needed and allow for proper financial planning.
For practical application, maintenance organizations track key performance indicators throughout an asset’s lifecycle to identify when actual costs begin to deviate from the projected economic life calculations. This allows for adjustment of maintenance strategies or acceleration of replacement plans when necessary.
Assess the Economic Life of an Asset
Assessing an asset’s economic life requires a comprehensive analytical approach focused on both financial and operational data. Organizations should continuously track and analyze operating costs, maintenance expenses, reliability metrics, and performance data to establish clear replacement decision points.
Use Key Performance Indicators
Key financial indicators include total maintenance costs, repair frequency, downtime costs, energy consumption, and spare parts expenses. These should be measured against the asset’s productivity, output quality, and contribution to revenue. Annual trending of these metrics helps identify degradation patterns and cost acceleration points that signal the approach to the end of economic life.
Use Reliability Metrics
Performance analysis must incorporate reliability metrics like Mean Time Between Failures (MTBF), Overall Equipment Effectiveness (OEE), and maintenance labor hours per operating hour. When these metrics show consistent decline despite regular maintenance, it often indicates deteriorating economic value. Organizations should also evaluate technological advancements that might make current equipment obsolete or significantly less efficient than newer alternatives.
Organizations need to establish a standardized replacement analysis process. This should include calculating the Equivalent Annual Cost (EAC) for both existing equipment and potential replacements. The EAC comparison helps determine optimal replacement timing by showing when maintaining existing equipment becomes more expensive than investing in new equipment.
Review Market Conditions
Market conditions also play a crucial role. Organizations should consider factors like equipment resale value, availability of replacement parts, vendor support, and industry technological trends. Equipment that’s becoming obsolete may warrant earlier replacement due to increasing support costs and declining vendor commitment.
Assess Risks
Risk assessment is essential in the decision-making process. This includes evaluating the impact of potential failures on safety, environmental compliance, production schedules, and customer commitments. Higher risk exposure might justify earlier replacement even if pure financial metrics suggest continued operation.
The most effective approach combines these analyses into a structured decision-making framework that weighs financial, operational, and risk factors to determine optimal replacement timing. Regular review and adjustment of this framework ensures it remains aligned with organizational objectives and market conditions.
Get a Free WorkTrek Demo
Let's show you how WorkTrek can help you optimize your maintenance operation.
Try for free