What is Enterprise Resource Planning?
In maintenance organizations, Enterprise Resource Management (ERM) software is an integrated system that helps manage and coordinate an organization’s resources, including assets, personnel, finances, and inventory. ERM software provides a centralized platform where maintenance teams can track operations, schedule tasks, manage budgets, and streamline workflows, promoting efficiency and accountability across the organization.
ERM software is handy for maintenance organizations because it ensures seamless coordination between asset management and operations departments. It offers modules facilitating work order management, preventive maintenance scheduling, asset tracking, and inventory control.
For instance, it ensures technicians have the right repair tools and parts, reducing downtime. Integration with Computerized Maintenance Management Systems (CMMS) is common, enabling teams to align maintenance plans with other business processes, such as procurement and finance.
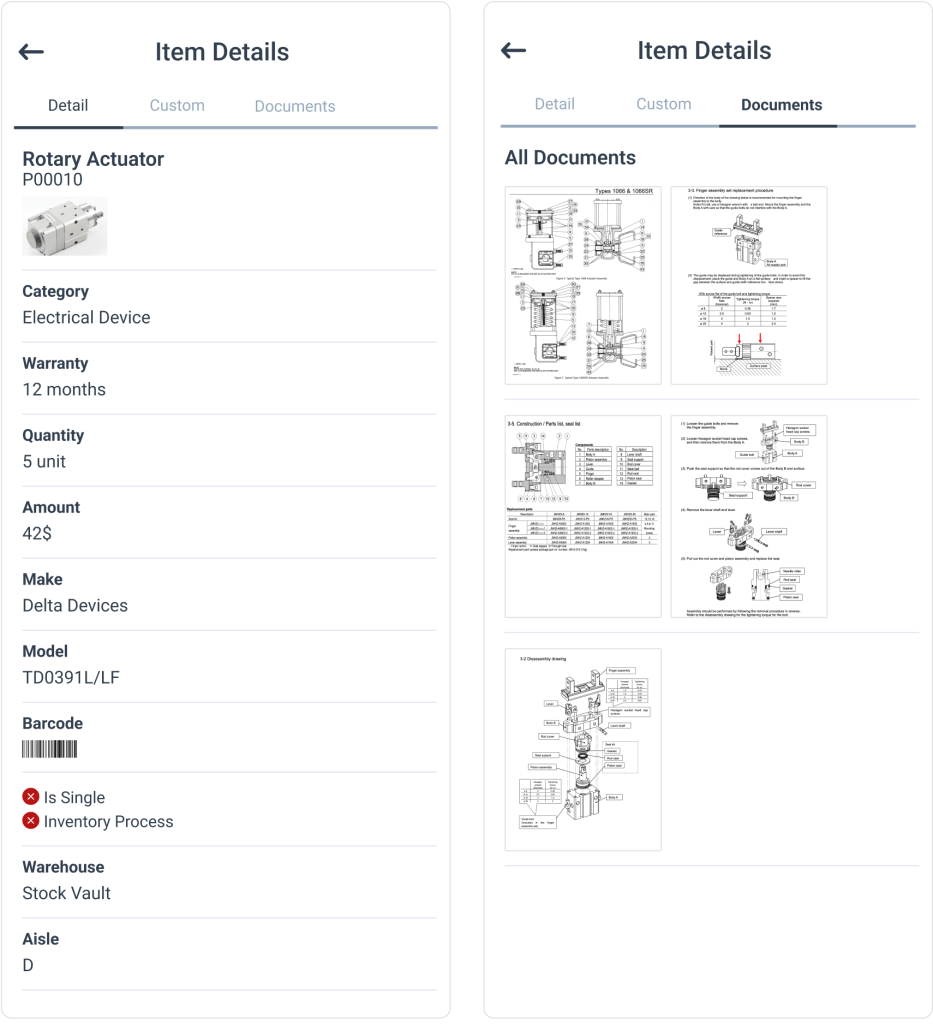
A key feature of ERM software is the ability to provide real-time visibility into resource allocation and asset performance. Managers can monitor equipment availability and utilization, track maintenance costs, and ensure compliance with safety regulations.
This visibility enables data-driven decision-making, allowing organizations to adjust schedules, manage budgets, and allocate resources more effectively.
ERM software also supports predictive and preventive maintenance by generating automated alerts based on asset conditions or predefined service intervals. By ensuring timely maintenance activities, the system helps extend asset lifecycles and avoid unexpected failures.
In addition, ERM software simplifies reporting and compliance, making it easier for organizations to meet regulatory requirements and audit standards. With historical data readily accessible, maintenance teams can generate reports on asset performance, maintenance costs, and resource usage.
Tips for Selecting an ERP Software
Here are key tips for selecting ERP software for maintenance operations:
- Assess specific organizational needs and pain points before evaluating solutions
- Ensure mobile functionality for technicians in the field
- Verify integration capabilities with existing systems (CMMS, accounting, etc.)
- Compare vendor support services, training programs, and implementation assistance
- Evaluate customization options to match workflows
- Check scalability to accommodate future growth
- Review security features and compliance with industry standards
- Consider the total cost of ownership, including maintenance, upgrades, and training.
- Test user interface simplicity and adoption requirements
- Validate reporting capabilities align with KPI tracking needs
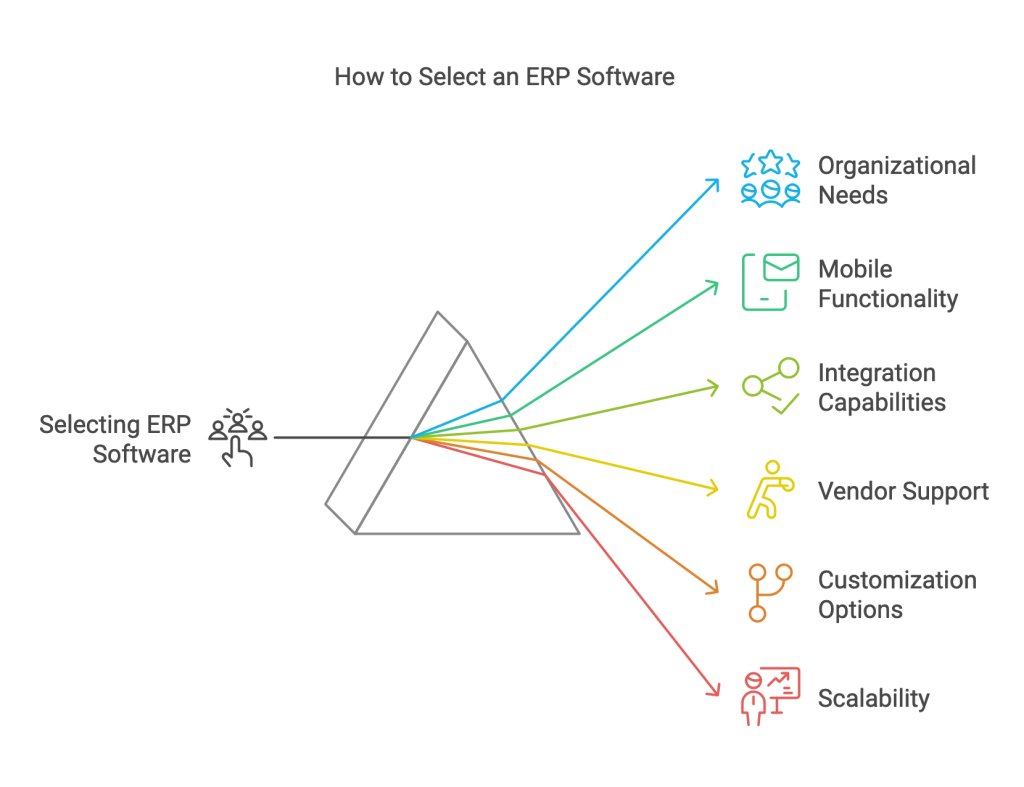
Focus on vendors with proven experience in maintenance operations and request demos with real-world scenarios relevant to your organization.
Get a Free WorkTrek Demo
Let's show you how WorkTrek can help you optimize your maintenance operation.
Try for free