What is an Equipment Maintenance Log?
An equipment maintenance log is a detailed, structured record that tracks all maintenance activities performed on a piece of equipment throughout its lifecycle. It provides a chronological history of inspections, repairs, part replacements, upgrades, and routine servicing, serving as a critical tool for monitoring asset health and performance. Maintenance organizations use these logs to ensure equipment remains in optimal working condition, helping to prevent unexpected breakdowns and extend asset life.
Each entry in the maintenance log typically includes important details such as the date of service, type of maintenance performed, parts used, technician responsible, and the equipment’s current condition. In some cases, logs also document downtime, repair costs, and future maintenance recommendations. Maintenance logs can be kept manually or, more commonly, maintained within Computerized Maintenance Management Systems (CMMS) like WorkTrek for easier tracking and reporting.
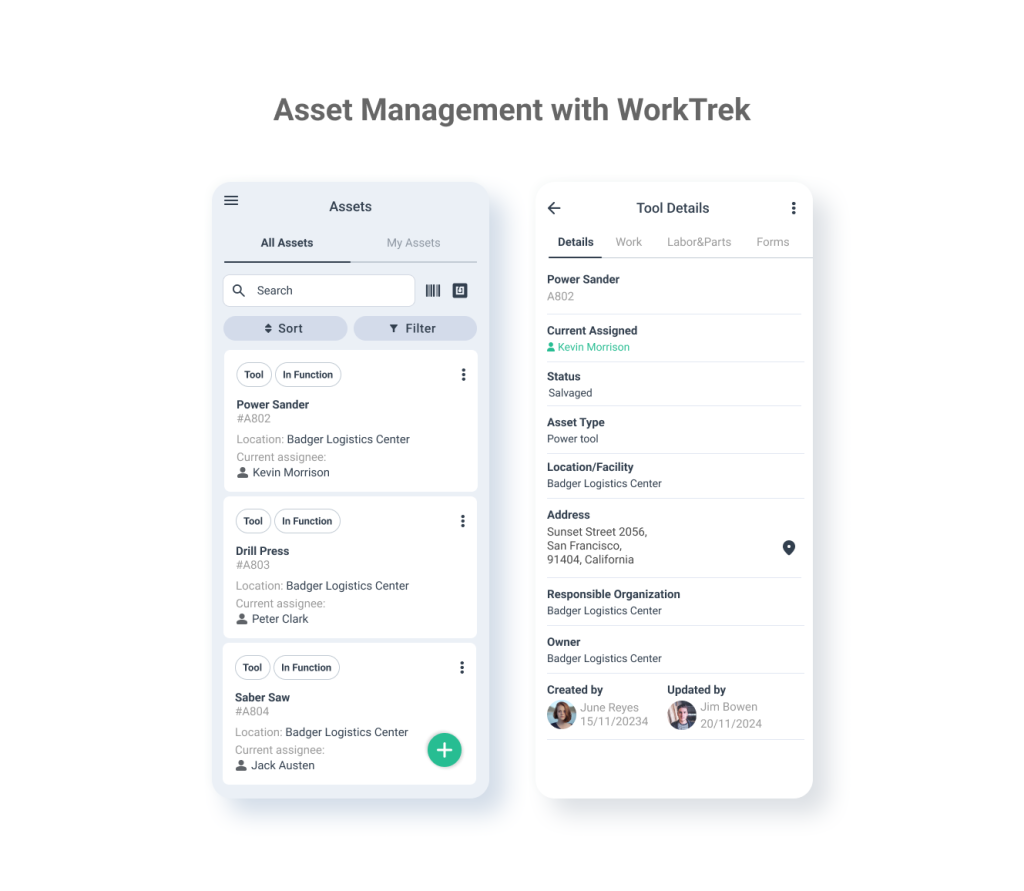
The primary purpose of an equipment maintenance log is to enhance visibility into an asset’s service history. This helps maintenance teams make data-driven decisions about when to schedule preventive maintenance or determine if an asset is nearing the end of its useful life. Accurate logs also support predictive maintenance by enabling trend analysis to identify patterns in wear and failure.
In addition to improving maintenance planning, maintenance logs ensure regulatory compliance. Many industries require organizations to maintain complete records of asset maintenance activities. This documentation proves that proper inspections and servicing have been carried out, helping to avoid fines or legal issues.
Equipment maintenance logs also promote accountability and transparency by assigning responsibility for each maintenance task and tracking the results.
Type of Equipment Maintenance Log
Below are the main types of Equipment Maintenance Logs that organizations use to ensure systematic tracking of maintenance activities:
1. Preventive Maintenance Log
- Records scheduled routine maintenance tasks aimed at preventing equipment breakdowns. It includes dates, tasks performed, and who completed the maintenance.
2. Corrective Maintenance Log
- Documents any repair activities taken in response to equipment malfunctions or unexpected failures. This log includes the nature of the issue, resolution steps, parts replaced, and time taken for repairs.
3. Predictive Maintenance Log
- This log type captures maintenance actions based on data-driven insights or condition monitoring. It details sensor readings, anomalies observed, and actions taken to address potential future failures.
4. Inspection Log
- Regular inspections of equipment are recorded to assess its condition. It includes observations, potential issues identified, and recommendations for future actions.
5. Usage-Based Maintenance Log
- Focuses on tracking maintenance triggered by specific equipment usage metrics, like run hours or cycles. It includes log entries detailing when maintenance was performed relative to usage thresholds.
6. Calibration Log
- This log details calibration activities for equipment that requires precise measurements. It includes the calibration date, reference standards, and any adjustments made.
7. Parts Replacement Log
- Tracks the replacement of components or spare parts, including the parts replaced, their condition, dates, and associated costs. This is particularly useful for monitoring wear and planning for future replacements.
8. Downtime Log
- This record includes incidents in which equipment was unavailable or non-operational. It includes the cause of downtime, duration, corrective measures taken, and its impact on productivity.
9. Safety and Compliance Log
- Focuses on documenting safety checks and compliance-related maintenance activities. This log ensures that equipment meets regulatory standards and remains safe for operation.
10. Lubrication Log
- Specifically, it records lubrication activities, including the type of lubricant used, equipment components serviced, and the frequency of lubrication, which is crucial for machinery requiring regular lubrication.
11. Environmental Impact Log
- Captures maintenance activities that aim to mitigate the environmental impact, such as filter replacements, leak repairs, and emission monitoring. This is critical for equipment with potential environmental hazards.
12. Maintenance Request Log
- Tracks maintenance requests submitted by operators or users. It includes details of reported issues, priority levels, and actions taken to address the requests.
Benefits of Equipment logs
Equipment maintenance logs provide essential benefits across multiple areas:
Regulatory Compliance
Maintains documented proof of inspections, repairs, and safety checks required by OSHA and industry regulations. Includes calibration records, safety certifications, and audit trails that protect organizations legally.
Asset Management
Records equipment specifications, warranty information, and complete maintenance history. It also enables tracking parts replacement, operating hours, and performance metrics, helping predict equipment lifespan and optimal replacement timing.
Cost Control
Monitors repair expenses, parts usage, and labor hours. Identifies equipment with excessive maintenance costs and highlights opportunities for cost reduction. Supports budget planning and ROI analysis for equipment investments.
Efficiency
Schedules preventive maintenance to minimize unexpected breakdowns. Streamlines work order management and resource allocation. Reduces equipment downtime through systematic maintenance tracking.
Performance Tracking
Documents equipment reliability metrics, failure patterns, and maintenance effectiveness. Includes downtime analysis, mean time between failures, and repair response times. Helps optimize maintenance strategies and equipment utilization.
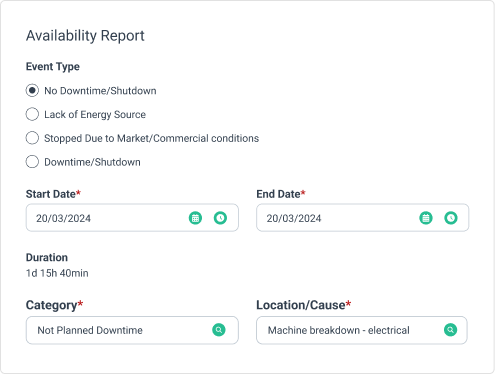
Decision Support
Provides data-driven insights for equipment replacement, maintenance scheduling, and resource allocation. Historical trends guide strategic planning and maintenance policy development. Supports continuous improvement initiatives.
Training
Serves as a knowledge base for maintenance procedures and troubleshooting guides—documents best practices, joint issues, and successful repair strategies. Facilitates technician training and standardizes maintenance procedures.
How to Create a Maintenance Log
To create an equipment maintenance log, follow these core steps:
Equipment Identification
- Equipment name, model, serial number
- Location and department
- Installation date and warranty details
- Technical specifications
- Manufacturer contact information
Maintenance Schedule
- Preventive maintenance intervals
- Required inspections
- Calibration schedules
- Safety check requirements
Maintenance Record Fields
- Date and time of maintenance
- Type of maintenance (preventive/corrective)
- Technician name/ID
- Work performed
- Parts used and costs
- Labor hours
- Equipment downtime
- Next maintenance due date
Format Recommendations
- Use standardized templates
- Include clear section headers
- Maintain consistent date formats
- Number entries sequentially
- Add signature/verification fields
- Include equipment status indicators
- Attach relevant photos/documents
- Add space for notes/observations
Digital logs should use searchable fields and backup capabilities. Paper logs need durability and organized filing systems. Both should follow company naming conventions and documentation standards.
Get a Free WorkTrek Demo
Let's show you how WorkTrek can help you optimize your maintenance operation.
Try for free