What is Gap Analysis?
Gap analysis in maintenance refers to comparing current maintenance practices and performance against industry standards, best practices, or organizational goals to identify areas for improvement.
The “gap” represents the difference between the organization’s current level and its desired level regarding maintenance efficiency, effectiveness, and asset reliability.
It involves measuring, documenting, and analyzing the disparity between existing maintenance practices and optimal or target maintenance standards to identify improvement areas.
How to Use Gap Analysis
This evaluation typically examines several key areas:
- Resource Management: The difference between available maintenance resources (personnel, tools, parts) and what’s needed for optimal operation. For instance, a facility might have 5 maintenance technicians but require 7 to meet preventive maintenance schedules effectively.
- Process Efficiency: The variance between current maintenance procedures and industry best practices or organizational goals. This could include comparing the current mean time between failures (MTBF) of 30 days against an industry standard of 45 days.
- Skill Sets: The disparity between existing staff capabilities and required competencies for maintaining modern equipment. For example, maintenance teams might need additional training in predictive maintenance technologies they currently don’t use.
- Technology Implementation: The difference between current maintenance management systems and available technological solutions that could improve efficiency. This might involve comparing paper-based work orders against the capabilities of a computerized maintenance management system (CMMS).
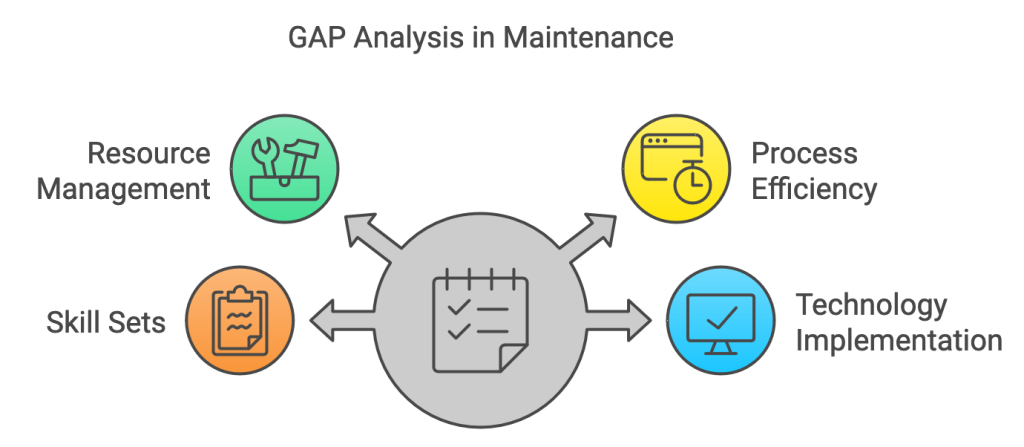
How to Maintenance Managers use Gap Analysis?
Maintenance managers use gap analysis in several interconnected ways to drive improvements and optimize their maintenance programs. Let’s explore each major application:
Strategic Planning
Strategic Planning and Goal Setting Maintenance managers begin by using gap analysis to understand their current maintenance program’s effectiveness clearly. They gather data on key performance indicators like equipment uptime, maintenance costs, labor utilization, and emergency repair frequency.
They identify specific areas needing improvement by comparing these metrics against industry benchmarks and organizational goals.
For example, if a manufacturing facility’s preventive maintenance completion rate is 65% but industry standards suggest 85%, this reveals a 20% performance gap requiring attention.
Resource Allocation
Resource Allocation and Budgeting Gap analysis helps maintenance managers make data-driven cases for additional resources. By quantifying gaps between current and desired performance levels, they can better justify budget requests to upper management.
For instance, if gap analysis reveals that equipment downtime is 25% higher than industry standards due to delayed repairs, managers can demonstrate how investing in additional maintenance technicians or spare parts inventory would close this gap and improve productivity.
Training
Maintenance managers can identify specific skill deficiencies within their teams through gap analysis. They assess their staff’s capabilities against the skills required to maintain modern equipment and implement new maintenance strategies.
For example, suppose a facility is moving toward condition-based maintenance, but the analysis shows staff lack expertise in vibration analysis and thermography. In that case, managers can develop targeted training programs to build these competencies.
Process Improvement
Maintenance managers examine their current workflows and procedures against best practices to identify inefficiencies and improvement opportunities. They might discover that their work order system takes an average of 48 hours to process requests while best-in-class facilities complete this in 24 hours.
This insight allows them to redesign workflows, implement automation, or adjust staffing patterns to close the gap.
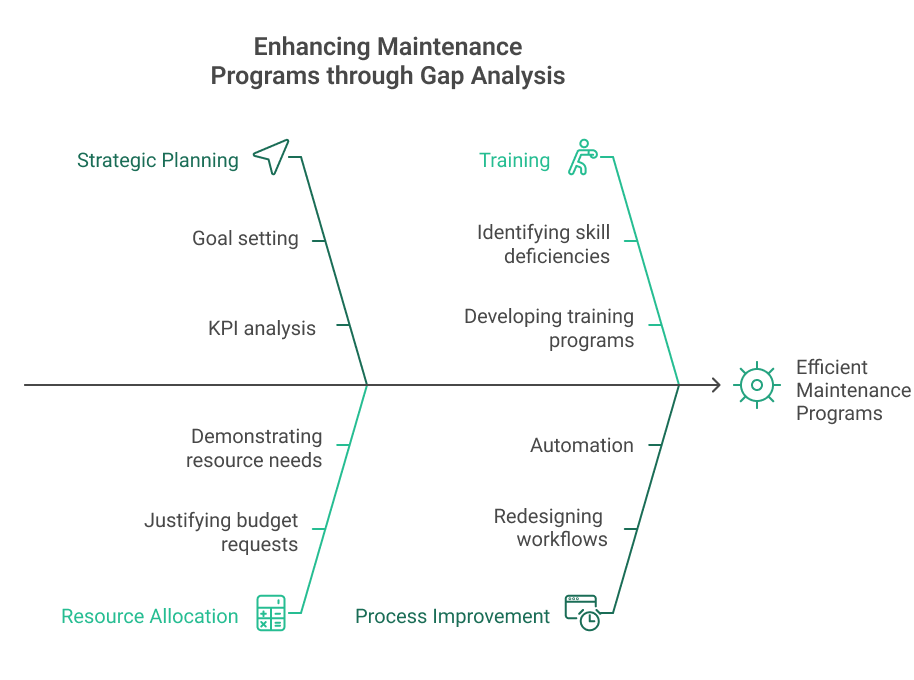
Technology and CMMS Implementation
Implementing a CMMS like WorkTrek can greatly benefit maintenance managers. CMMS can help maintenance managers make informed decisions about their maintenance.
They might find that their manual data collection methods result in 15% data error rates, while automated systems could reduce this to 2%. This analysis helps justify investments in computerized maintenance management systems (CMMS) or condition monitoring equipment.
Monitor Performance
Maintenance managers use gap analysis as an ongoing tool for tracking progress toward goals. They establish baseline measurements, set improvement targets, and regularly measure progress. This continuous monitoring allows them to:
- Adjust strategies if improvement efforts aren’t closing gaps as expected
- Celebrate and reinforce successful gap closures
- Identify new gaps that emerge as technology and industry standards evolve
Risk Management
Through gap analysis, maintenance managers can identify potential risks in their maintenance programs. They examine areas where performance gaps might lead to safety issues, production delays, or equipment failures. This allows them to prioritize improvements based on risk levels and potential impact on operations.
Pros and Cons of GAP Analysis for Maintenance Teams
Advantages:
Data-driven Decision Making
Gap analysis provides maintenance managers with concrete, quantifiable data to support their decisions. Instead of relying on intuition or anecdotal evidence, managers can point to specific metrics showing the difference between current and desired performance.
For example, when a maintenance manager needs to justify hiring additional technicians, they can demonstrate how current staffing levels result in 30% longer repair times than industry standards.
Strategic Focus
Maintenance managers can prioritize their improvement efforts more effectively by systematically identifying and measuring gaps between current and desired states. This helps them focus resources on the areas with the most significant impact.
For instance, if gap analysis reveals that outdated preventive maintenance schedules account for 60% of unexpected breakdowns. In comparison, parts inventory issues account for only 10%, so managers know where to concentrate their improvement efforts first.
Clear Communication
Tool Gap analysis is an excellent communication tool when working with upper management and maintenance staff. The visual and numerical representation of performance gaps helps maintenance managers clearly articulate needs and justify resource requests.
When presenting to senior leadership, showing that current maintenance software leads to 25% longer work order processing times than modern systems makes a compelling case for upgrading technology.
Objective Performance
Assessment The methodology provides an objective framework for assessing maintenance performance. Rather than subjective impressions, gap analysis uses measurable criteria to evaluate the maintenance organization’s performance.
This objectivity helps reduce bias in decision-making and creates a more fair basis for implementing changes.
Disadvantages:
Resource Intensive
Conducting a thorough gap analysis requires significant time and effort to gather accurate data, analyze performance metrics, and develop improvement plans. Many maintenance organizations struggle to allocate the necessary resources while managing daily operations. The process often requires dedicated staff time that could be spent on immediate maintenance needs.
Data Quality Challenges
The effectiveness of gap analysis heavily depends on the quality and availability of maintenance data. Many organizations face challenges with incomplete or inaccurate maintenance records, making it difficult to establish reliable baseline measurements. The gap analysis may lead to flawed conclusions or misguided improvement efforts without good data.
Complexity in Implementation
While identifying gaps might be straightforward, developing and implementing solutions to close those gaps can be complex and challenging. For example, a gap analysis might reveal the need for advanced predictive maintenance capabilities, but implementing such programs requires significant changes in technology, processes, and staff skills that can be difficult to coordinate.
Risk of Analysis Paralysis
Sometimes, maintenance managers can become too focused on gathering and analyzing data, leading to delayed action. The desire for perfect information before making changes can result in missed opportunities for immediate improvements. This is particularly problematic in maintenance environments where quick responses to problems are often necessary.
Resistance to Change
Gap analysis often reveals the need for significant changes in maintenance practices, which can lead to resistance from staff members who are uncomfortable with existing procedures. Even when the analysis clearly shows the benefits of new approaches, overcoming this resistance requires careful change management and additional time and resources.
External Factors
Gap analysis might not fully account for external factors beyond the maintenance organization’s control, such as budget constraints, corporate policies, or union agreements. This can lead to frustration when identified gaps cannot be addressed due to these external limitations.
Benchmark Relevancy
Finding relevant benchmarks for comparison can be challenging, especially for specialized industries or unique maintenance environments. Using inappropriate benchmarks can lead to unrealistic goals or misguided improvement efforts.
For instance, comparing the performance of a small maintenance shop to that of a large automated facility might set unrealistic expectations.
Get a Free WorkTrek Demo
Let's show you how WorkTrek can help you optimize your maintenance operation.
Try for free