What is Industry 4.0?
The term Industry 4.0 represents a significant shift in how manufacturing and production systems operate in today’s digital world. Industry 4.0 refers to the fourth industrial revolution that focuses on interconnectivity, automation, machine learning, and real-time data to create smarter, more efficient manufacturing processes. This technological evolution builds upon the digital revolution (the third industrial revolution) but takes it further by blending physical production with smart digital technology.
Walking through a modern factory floor today, you’ll notice a stark difference from past facilities. Machines communicate with each other, robots work alongside humans, and production systems make decisions without human intervention.
The Fourth Industrial Revolution is changing how things are made, entire business models, and creating new opportunities across industries.
Defining Industry 4.0
Industry 4.0, also known as the Fourth Industrial Revolution or 4IR, represents the next significant advancement in manufacturing and industrial processes. It marks a significant shift in how companies produce goods by integrating digital technologies.
At its core, Industry 4.0 can be defined as integrating intelligent digital technologies into manufacturing and industrial processes. This transformation builds upon previous industrial revolutions characterized by mechanization, mass production, and early automation.
“Industry 4.0” originated in Germany as part of a strategic initiative to establish the country as a leader in advanced manufacturing solutions. Since then, it has gained global recognition as the defining framework for modern industrial development.
Key components of Industry 4.0 include:
- Cyber-physical systems
- Internet of Things (IoT) connectivity
- Industrial Internet
- Cloud computing
- Advanced analytics
- Artificial intelligence
- Smart factories
- Data Security
- Smart and autonomous systems
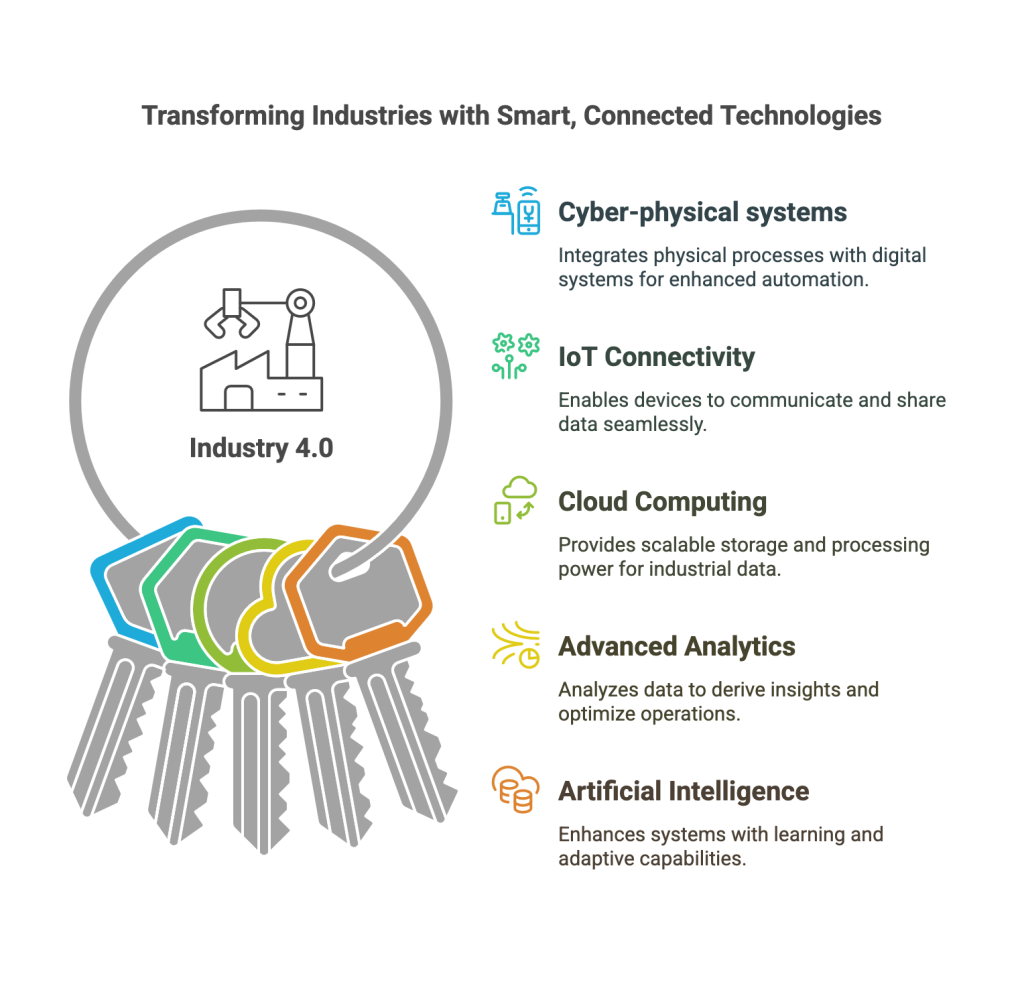
Source: WorkTrek.com
Industry 4.0 technologies enable machines, devices, sensors, and people to connect and communicate with one another. This creates networks throughout the value chain that can make decisions and control each other autonomously.
The emergence of digital industrial technology is a defining characteristic of Industry 4.0. These technologies transform traditional manufacturing practices and create smart factories where computer-based systems monitor physical operations.
Organizations implementing Industry 4.0 principles can achieve greater operational efficiency, productivity, and innovation through data-driven decision-making and autonomous systems.
Historical Context
The development of Industry 4.0 represents the latest chapter in manufacturing evolution. It builds upon three previous industrial revolutions that fundamentally transformed production methods, economic systems, and society.
First Industrial Revolution
The First Industrial Revolution began in Britain around 1760 and spread through Europe and North America until 1840. This transformation marked humanity’s shift from manual production to mechanized manufacturing processes.
Water and steam power became the driving forces behind new machinery. James Watt’s invention of the steam engine in 1769 revolutionized production capabilities and transportation.
Textile manufacturing was transformed, with innovations like the spinning jenny and power loom dramatically increasing production efficiency. Coal became the primary energy source, replacing wood and other biofuels.
This period saw the rise of factories, drawing workers from rural areas to growing industrial centers. The socioeconomic landscape changed dramatically as manufacturing moved from homes to centralized facilities.
Second Industrial Revolution
The Second Industrial Revolution, which lasted from approximately 1870 to 1914, introduced new energy sources and mass production techniques. Electricity, gas, and oil-powered new machines enabled more efficient manufacturing processes.
Steel production expanded significantly, becoming more affordable through the Bessemer process. This enabled the construction of railroads, larger ships, and skyscrapers that defined the era.
The assembly line, perfected by Henry Ford, revolutionized manufacturing by introducing standardized parts and moving production lines. This development dramatically reduced production time and costs while increasing output.
Communication technologies like the telephone and telegraph connected distant locations and accelerated business transactions. Chemical industries developed synthetic materials and new manufacturing processes.
Scientific management principles introduced by Frederick Taylor focuse
Core Components of Industry 4.0
Industry 4.0 represents a fundamental shift in manufacturing processes. Several key technologies work together to create smart factories. These technologies enable real-time decision-making, automation, and enhanced connectivity throughout production systems.
Internet of Things (IoT)
The Internet of Things forms the backbone of Industry 4.0 by connecting machines, devices, sensors, and people through network technology. IoT devices in machinery collect vast amounts of operational data in real time.
These smart sensors monitor everything from temperature and pressure to vibration and energy consumption. They enable equipment to communicate with other systems across the factory floor.
The true power of industrial IoT comes from its ability to create a digital thread throughout the manufacturing process. This connectivity allows remote monitoring, predictive maintenance, and automated responses to changing conditions.
IoT implementation helps manufacturers reduce downtime, optimize equipment performance, and increase operational efficiency. The number of connected industrial devices continues to grow exponentially each year.
Big Data and Analytics
Big Data analytics transforms the massive amounts of information IoT devices generate into actionable insights. Manufacturing operations produce terabytes of data daily that must be processed efficiently and become part of your business processes.
Advanced analytics tools use machine learning algorithms to identify patterns, anomalies, and opportunities for improvement that humans might miss. These systems can predict equipment failures before they occur, reducing costly downtime.
Real-time analytics capabilities enable instant decision-making on the factory floor. Through data-driven insights, manufacturers can optimize production schedules, improve quality control, and reduce waste.
Dashboards and visualization tools make complex data accessible to workers at all levels. This democratization of information empowers employees to make better decisions based on accurate, up-to-date information.
Autonomous Robots
Autonomous robots in Industry 4.0 go far beyond traditional industrial robots. These machines can work alongside humans safely and learn from their experiences.
Modern industrial robots feature advanced sensors and AI capabilities that allow them to adapt to changing environments. They can recognize objects, navigate complex spaces, and perform precision tasks with minimal human intervention.
Collaborative robots (cobots) represent a significant advancement in this field. Unlike traditional robots that work in isolation, cobots are designed to operate safely alongside human workers, combining human flexibility with robotic precision.
These robots handle repetitive, dangerous, or ergonomically challenging tasks while human workers focus on more complex activities requiring creativity and problem-solving. This collaboration improves both productivity and workplace safety.
Simulation
Before implementation, digital simulation creates virtual models of physical processes, products, and factory layouts. Engineers can test different scenarios in a risk-free virtual environment before making changes to actual production.
These simulations use real-time data from the factory floor to mirror physical processes with high accuracy. This digital twin technology allows manufacturers to optimize processes virtually before changing physical systems.
Virtual commissioning enables engineers to test new equipment and configurations without disrupting ongoing production, significantly reducing implementation time and costs.
Simulation tools also support worker training in a safe environment. Employees can practice complex procedures or emergency responses without safety risks or production impacts.
Horizontal and Vertical System Integration
Horizontal integration connects all departments within a company—from product development to manufacturing, logistics, and service—creating seamless information flow across the entire value chain.
Vertical integration links all levels of the organization, from the factory floor to executive decision-makers. Operational data moves upward, while strategic decisions flow downward through connected systems.
This comprehensive integration extends beyond company boundaries to include suppliers and customers. The result is a fully transparent ecosystem where all stakeholders can access relevant information.
Industry 4.0 workplaces require flexible systems that can adapt quickly to changing requirements. Integrated systems enable faster response to market changes and customer demands.
Cybersecurity
As connectivity increases, cybersecurity becomes critical for protecting sensitive manufacturing data and preventing operational disruptions. Industry 4.0 implementations must incorporate robust security measures.
Manufacturing systems face unique cybersecurity challenges compared to traditional IT environments. Industrial control systems often run legacy software with limited security features.
Advanced threat detection systems use AI to identify suspicious activities and potential breaches. These systems continuously monitor network traffic for anomalies that might indicate a security incident.
Manufacturers implement multiple layers of protection, including firewalls, encryption, and access controls. Regular security assessments and employee training are essential components of comprehensive security programs.
Security by design principles ensures that new systems incorporate protection from the beginning rather than as an afterthought. This proactive approach reduces vulnerabilities throughout the production ecosystem.
The Cloud
Cloud computing provides the computational power and storage capacity needed for Industry 4.0 applications. Cloud platforms enable manufacturers to process massive datasets without maintaining extensive on-site IT infrastructure.
Cloud services’ scalability allows companies to adjust resources as needed, paying only for what they use. This flexibility makes advanced technologies accessible to smaller manufacturers.
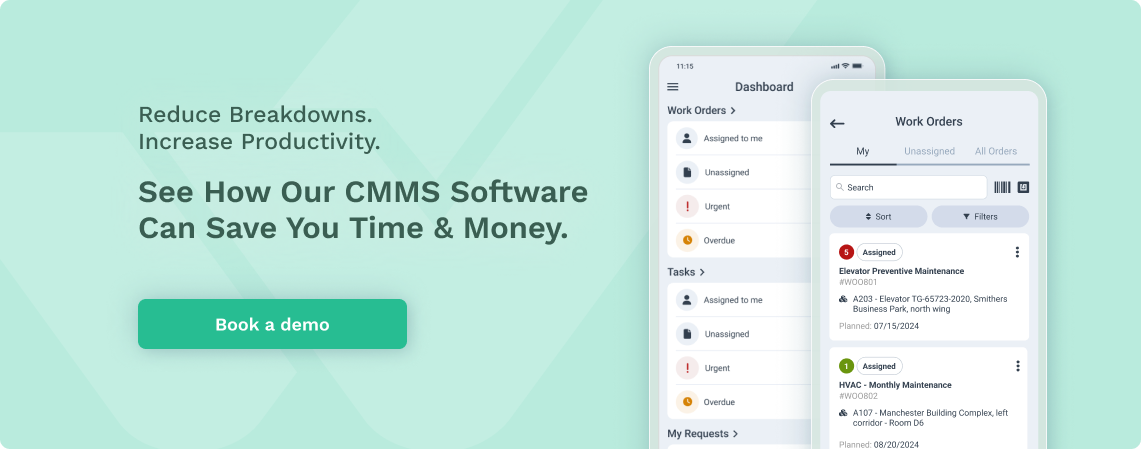
Cloud platforms facilitate collaboration across geographic boundaries. Teams can collaborate on designs, share data, and solve problems regardless of location.
Edge computing complements cloud services by processing time-sensitive data closer to its source. This hybrid approach reduces latency for critical operations while leveraging cloud capabilities for intensive analytics.
Additive Manufacturing
Additive manufacturing, commonly known as 3D printing, creates objects by adding material layer by layer based on digital models. This technology enables the production of complex shapes that would be impossible with traditional manufacturing methods.
The Impact of Industry 4.0
Industry 4.0 is profoundly transforming our world. Integrating smart technologies and automated systems reshapes manufacturing processes, economic structures, workforce requirements, and social dynamics.
On Manufacturing
Industry 4.0 has dramatically changed how products are made. Smart factories now use connected machines that can communicate with each other and make decisions without human intervention.
Predictive maintenance has made manufacturing more efficient. It prevents breakdowns before they happen, reducing downtime and saving companies money.
Customization has become easier and more affordable. Manufacturers can now produce personalized products at mass-production prices, meeting individual customer needs without significant cost increases.
Quality control has improved through automated inspection systems that use computer vision to spot defects invisible to the human eye. Fewer defective products reach customers.
Production flexibility has increased, allowing manufacturers to adapt quickly to changing market demands and customer preferences without extensive retooling.
On Economy
The economic impact of Industry 4.0 is substantial and far-reaching. New business models have emerged, including product-as-a-service offerings where companies sell outcomes rather than physical products.
Supply chains have become more resilient and transparent. Real-time tracking and analytics help businesses respond quickly to disruptions and optimize logistics operations.
Small and medium enterprises (SMEs) can now compete more effectively with larger corporations. Cloud-based solutions provide access to advanced technologies without massive capital investments.
Economic Benefits of Industry 4.0:
- Increased productivity and efficiency
- Lower operational costs
- New revenue streams through data monetization
- Enhanced global competitiveness
- Faster time-to-market for new products
However, economic disparities may widen between technology adopters and those who lag in implementation.
On Workforce
The workforce is experiencing significant changes as Industry 4.0 advances. Many routine and repetitive jobs are being automated while new roles focused on technology management and data analysis are being created.
Workers need skills that are different from those in the past. Technical knowledge, digital literacy, and the ability to work alongside robots and AI systems have become essential in the modern workplace.
Continuous learning has become necessary for career stability. Workers must regularly update their skills to remain relevant in a rapidly evolving job market.
Remote work opportunities have expanded as digital connectivity allows many tasks to be performed from anywhere. This has changed traditional working arrangements and office structures.
The demand for STEM professionals has increased dramatically, creating opportunities for those with the right educational background but challenges for others.
On Society
Society is adapting to the widespread changes brought by Industry 4.0. Consumer expectations have shifted toward personalization, immediacy, and seamless experiences across physical and digital worlds.
Privacy concerns have grown as more data is collected through connected devices and systems. Questions about who owns this data and how it should be protected remain central to public discourse.
Urban environments are evolving into smart cities where infrastructure, services, and citizens are connected through digital networks. This improves efficiency but raises questions about surveillance and control.
The digital divide between technology-rich and technology-poor communities presents significant social challenges. Access to high-speed internet and digital literacy have become essential for full social participation.
Environmental impacts can be positive through resource optimization and waste reduction, but increased electronic consumption creates new sustainability challenges.
Challenges and Considerations
The widespread adoption of Industry 4.0 faces several significant hurdles that organizations must overcome to fully realize its benefits. These challenges range from security concerns to workforce readiness and technical integration issues.
Data Privacy and Security
As factories become more connected, they face increased cybersecurity threats. Smart manufacturing relies on vast networks of sensors and devices that create multiple potential entry points for attackers.
Organizations must implement robust security protocols to protect both operational technology (OT) and information technology (IT) systems. This includes:
- Regular security audits
- Advanced encryption methods
- Multi-factor authentication
- Continuous monitoring systems
Data privacy concerns also grow as companies collect more information about processes, products, and workers. Compliance with regulations like GDPR becomes increasingly complex in highly connected environments.
Security breaches can result in costly production downtime, intellectual property theft, or safety risks in critical manufacturing environments.
Skilled Labor Shortage
The transition to Industry 4.0 creates a significant workforce skills gap. Traditional manufacturing skills must now be combined with digital competencies.
Workers need training in:
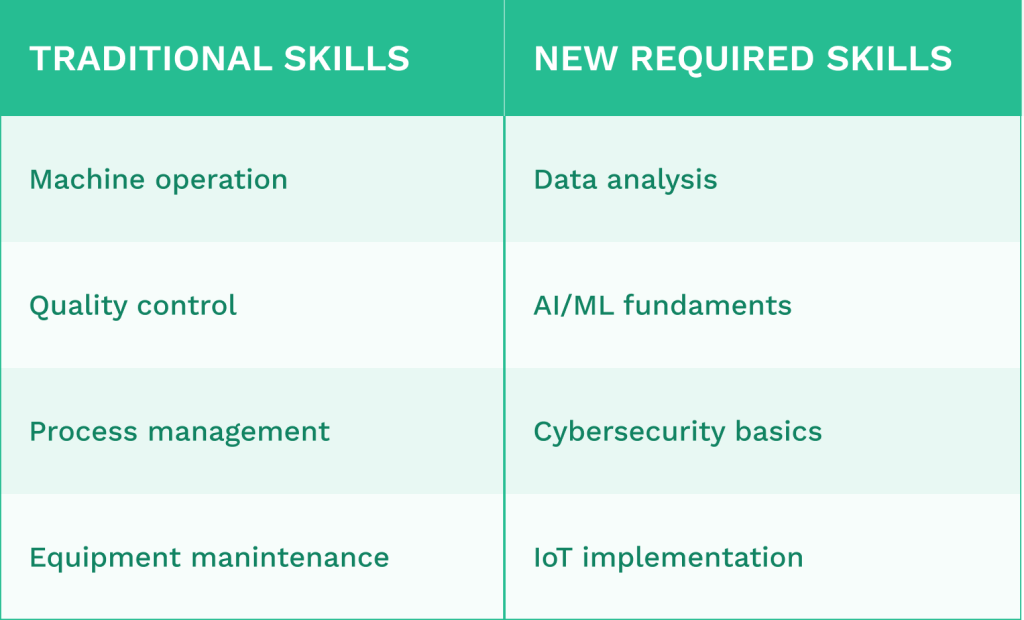
Companies often struggle to find qualified personnel who understand manufacturing processes and digital technologies. This shortage can slow implementation and limit the effectiveness of Industry 4.0 initiatives.
Retraining existing workers requires substantial time and financial investment. Organizations must develop comprehensive training programs and potentially partner with educational institutions to build talent pipelines.
Interoperability and System Integration
Interoperability challenges present significant technical hurdles for Industry 4.0 implementation. Many manufacturing environments contain legacy equipment that is not designed for digital connectivity.
These older systems often use proprietary protocols that are difficult to communicate with newer technologies. Creating a unified system requires extensive integration work and sometimes custom solutions.
Standardization remains an ongoing challenge. Vendors, technologies, and platforms may use different communication protocols, data formats, and interfaces.
Integration complexity increases with:
- Multiple equipment generations on the factory floor
- Various vendor systems that need to communicate
- Different data formats and storage solutions
- Proprietary control systems
Addressing these challenges requires thoughtful architecture planning and, potentially, middleware solutions to bridge technological gaps.
Initial Investment
Cost constraints represent a significant barrier, particularly for small and medium enterprises. The initial investment for Industry 4.0 technologies can be substantial.
Expenses typically include:
- Hardware (sensors, controllers, robotics)
- Software platforms and licenses
- Integration services
- Training and workforce development
- Consulting expertise
Companies often struggle with ROI calculations for these investments, as benefits may take time to materialize. Determining which technologies to prioritize requires careful strategic planning.
Many organizations adopt a phased approach, first implementing technologies with the clearest financial benefits before expanding to more comprehensive solutions. This helps manage costs while still moving toward digital transformation.
Financial assistance programs, including government grants and tax incentives, can help offset some expenses, particularly for smaller manufacturers.
Strategic Implementation
Implementing Industry 4.0 requires careful planning, adequate resources, and organizational alignment. Companies, governments, educational institutions, and cross-industry partnerships play critical roles in successful digital transformation initiatives.
Companies’ Roadmap to Adoption
The journey toward Industry 4.0 implementation typically begins with a comprehensive assessment of current capabilities and technological gaps. Companies should develop a clear strategic roadmap that aligns with business objectives rather than pursuing technology for its own sake.
Successful organizations often start with pilot projects in high-impact areas before scaling across operations. This phased approach allows for learning and adjustment while minimizing disruption and risk.
Key components of an effective implementation strategy include:
- Leadership commitment and clear vision from top management
- Prioritization of initiatives based on business value and feasibility
- Cross-functional teams that combine IT and operational technology expertise
- Budget allocation for both technology investment and workforce development
Companies should establish metrics to measure progress and ROI, focusing on operational improvements and new business capabilities rather than just technology deployment.
Government Policy and Support
Governments worldwide are creating policies and incentives to accelerate Industry 4.0 adoption. These include tax incentives for technology investments, grants for research and development, and the creation of innovation hubs.
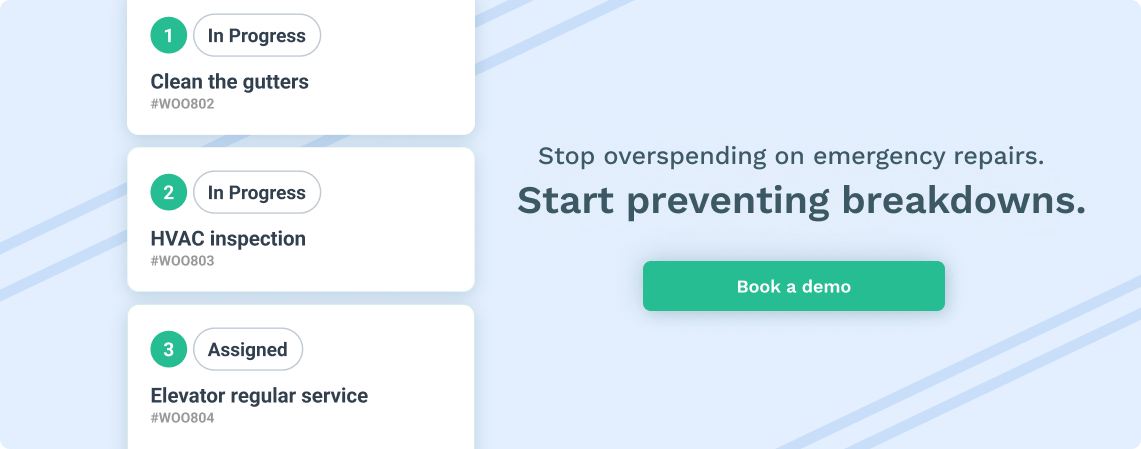
Many countries have established national manufacturing strategies that prioritize digital transformation. These initiatives often focus on:
- Developing digital infrastructure (high-speed networks, data centers)
- Creating regulatory frameworks that address data privacy and cybersecurity
- Supporting small and medium enterprises that may lack resources
- Promoting standards and interoperability across technologies
Public-private partnerships have proven effective in creating test beds where companies can experiment with new technologies in low-risk environments. These collaborative ecosystems help bridge the gap between policy goals and practical implementation.
Education and Training
The workforce transformation required for Industry 4.0 demands significant changes in education and training approaches. Technical skills in data analytics, automation, and cybersecurity are in high demand.
Educational institutions are responding by:
- Updating engineering and technical curricula to include digital technologies
- Creating specialized degree programs in areas like industrial IoT and advanced manufacturing
- Developing continuing education and certificate programs for working professionals
- Incorporating hands-on learning with actual industrial equipment and software
Companies are complementing these efforts through internal training programs, mentoring systems, and partnerships with educational providers. This digital transformation requires technical skills and capabilities in change management, systems thinking, and cross-functional collaboration.
Collaboration Across Industries
Industry 4.0 implementation benefits greatly from cross-industry collaboration that pools knowledge, resources, and best practices. Industrial consortia bring together manufacturers, technology providers, and research institutions to tackle common challenges.
Effective collaboration takes several forms:
- Technology standardization efforts that ensure interoperability
- Shared research facilities that reduce the cost of experimentation
- Knowledge exchange platforms where companies share implementation experiences
- Joint venture initiatives for specific technology development
The Fourth Industrial Revolution blurs traditional industry boundaries, creating opportunities for new partnerships. For example, automotive manufacturers collaborate with tech companies on autonomous vehicles, while energy providers partner with equipment makers on predictive maintenance solutions.
These collaborative ecosystems accelerate innovation while distributing both risks and rewards among participants.
Future Trends and Predictions
Industry 4.0 continues to evolve rapidly as we move into 2025 and beyond. Several key trends are emerging that will shape the future of industrial transformation.
The global Industry 4.0 market is projected to reach a value of $279.75 billion by 2028, growing at an impressive 16.3% annually. This remarkable growth indicates the increasing adoption of innovative manufacturing technologies worldwide.
AI and Machine Learning are becoming central to industrial automation. These technologies will continue to enhance predictive maintenance, quality control, and process optimization across manufacturing sectors.
Industrial IoT (IIoT) and improved connectivity represent another major trend. As more devices connect, factories will generate unprecedented amounts of data that can be leveraged for better decision-making.
Factory digitalization and automation are accelerating. Companies are implementing digital solutions and automation technologies to improve efficiency and reduce operational costs.
Data analytics capabilities will become more sophisticated. Organizations will increasingly rely on advanced analytics to extract meaningful insights from the vast amounts of data that connected systems generate.
Emerging technologies to watch include:
- Augmented reality for maintenance and training
- Digital twins for virtual modeling
- Edge computing for faster processing
- 5G networks for enhanced connectivity
- Quantum computing applications
Cybersecurity will remain a critical concern as systems become more interconnected. Companies must balance innovation with robust security measures to protect sensitive industrial data and infrastructure.
How are Industry 4.0 Technologies changing Maintenance and manufacturing
Industry 4.0 technologies are dramatically transforming how manufacturing and maintenance operations function. Smart factories and highly automated environments are being created where machines, systems, and people all connect seamlessly.
These technologies significantly boost productivity and efficiency in manufacturing operations. Companies implementing these solutions report reduced downtime, higher-quality products, and faster production cycles.
Industry 4.0 has introduced predictive approaches that replace traditional reactive maintenance methods. Sensors and IoT devices continuously monitor equipment health, allowing teams to address issues before failures occur.
Key Technologies Transforming Manufacturing & Maintenance:
- Internet of Things (IoT) sensors for real-time monitoring
- Cloud computing for data storage and processing
- Artificial Intelligence for predictive analytics
- Digital twins for virtual equipment modeling
- Robotics and automation for repetitive tasks
- Smart Enterprise Resource Planning Systems
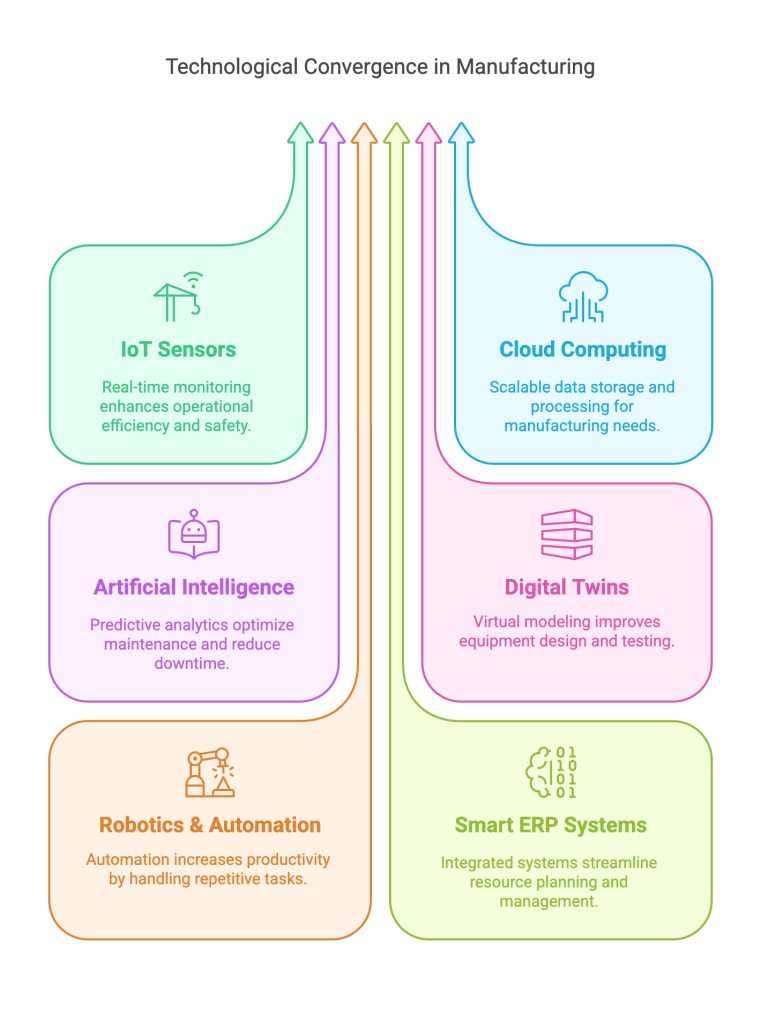
Source: WorkTrek.com
Integrating robotics and AI with IT and OT systems creates more efficient manufacturing processes. This convergence enables factories to optimize operations using real-time data.
Maintenance teams now use mobile devices to access equipment information instantly. Technicians can view repair histories, diagrams, and step-by-step instructions while working on machinery.
The digitization of manufacturing enables better decision-making through data analytics. Companies can identify inefficiencies and implement targeted improvements with greater precision.
Get a Free WorkTrek Demo
Let's show you how WorkTrek can help you optimize your maintenance operation.
Try for free