What is Infrared Thermography?
Infrared thermography (IRT) is a non-destructive testing technique that measures and visualizes the infrared radiation emitted by objects. All objects with a temperature above absolute zero emit infrared radiation, a type of electromagnetic radiation, as a function of their temperature.
Thermography uses specialized cameras with infrared detectors to capture this radiation and convert it into a visible thermal image or thermogram, where different colors or shades represent different temperature levels.
Infrared technology plays a crucial role in capturing the thermal energy emitted by objects, enabling applications such as surveillance, preventive maintenance, and identifying subsurface defects.
Using thermal imaging cameras allows for the visualization of temperature variations across an object’s surface without making physical contact.
Principles of Infrared Thermography
Infrared thermography operates on the principle that all objects emit infrared radiation as a function of their temperature. This radiation is invisible to the naked eye but can be detected and measured using specialized equipment.
The amount of infrared radiation an object emits increases with its temperature, allowing for precise temperature measurement and visualization of temperature differences across surfaces.
Infrared thermography leverages this principle to create thermal images, where different colors or shades represent varying temperatures. This non-contact method is invaluable for identifying temperature anomalies, indicating potential issues in various applications from electrical and mechanical systems to building inspections.
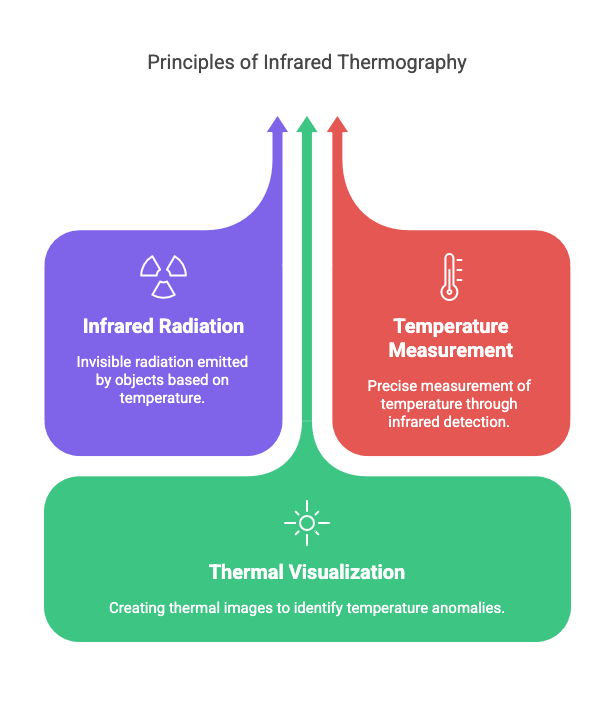
Source: WorkTrek.com
Temperature Measurement
Temperature measurement is a cornerstone of infrared thermography. It involves capturing the infrared radiation emitted by an object and converting it into a temperature value. The process begins with data acquisition, where an infrared camera detects the radiation emitted by the target object. This data is then processed to filter out noise and enhance accuracy.
The final step is temperature calculation, where the processed data is translated into temperature values. This allows for identifying temperature differences within an object or between multiple objects.
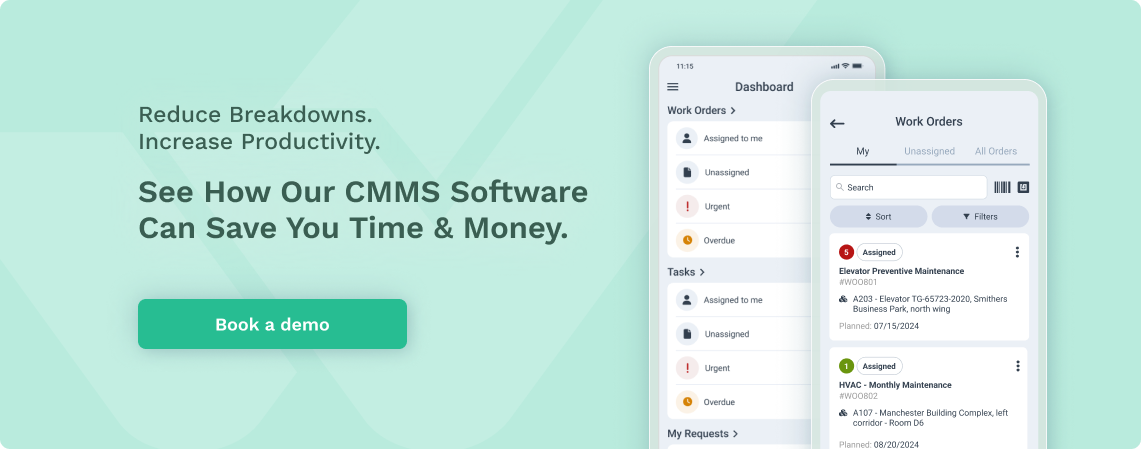
Accurate temperature measurement is crucial for diagnosing issues, ensuring safety, and optimizing application performance.
Thermal Imaging Devices
Thermal imaging devices, commonly known as thermal cameras, are essential tools in infrared thermography. These devices detect infrared radiation and convert it into thermal images, visually representing temperature distribution. Thermal imaging devices come in various forms, including handheld cameras, fixed systems, and drone-mounted units, each suited for different applications.
Handheld thermal imaging cameras offer flexibility and portability, making them ideal for on-the-spot inspections. Fixed systems provide continuous monitoring, which is crucial for critical infrastructure. Drone-mounted thermal imagers are perfect for surveying large or hard-to-reach areas.
Thanks to their ability to detect temperature differences and visualize thermal patterns, these devices are widely used across industries such as predictive maintenance, quality control, and research.
Types of Infrared Thermography
Based on Operating Principles
- Passive Thermography: Examines temperature differences naturally present in the target object without applying any external heating or cooling stimulus. It’s commonly used for monitoring operational equipment, electrical installations, or building envelopes under normal conditions.
- Active Thermography: Involves applying an external energy source (heat, cool air, vibration) to create thermal contrasts that might not be visible under steady-state conditions. After applying the stimulus, the thermal response is monitored over time. Subtypes include:
- Pulse Thermography: A brief thermal pulse is applied, and the temperature decay is monitored
- Lock-in Thermography: Applies periodic heating at a specific frequency to detect subsurface defects
- Step Heating Thermography: Continuous heating is applied, and the temperature rise is monitored
Based on Wavelength Bands
- Near Infrared (NIR): 0.7-1.4 μm wavelength range
- Short-wave Infrared (SWIR): 1.4-3 μm
- Mid-wave Infrared (MWIR): 3-5 μm
- Long-wave Infrared (LWIR): 8-14 μm
Based on Equipment Types: Thermal Imaging Camera
- Fixed/Mounted Systems: Permanently installed for continuous monitoring
- Portable Handheld Cameras: For flexible, on-demand inspections. Infrared thermal imaging cameras generate images based on infrared radiation, making them distinct from conventional cameras. A thermal imager detects infrared radiation from objects and creates thermal profiles or heat maps.
- Drone-mounted systems: For surveying large areas or inaccessible locations
- Line Scanning Systems: For continuous monitoring of moving objects (e.g., production lines)
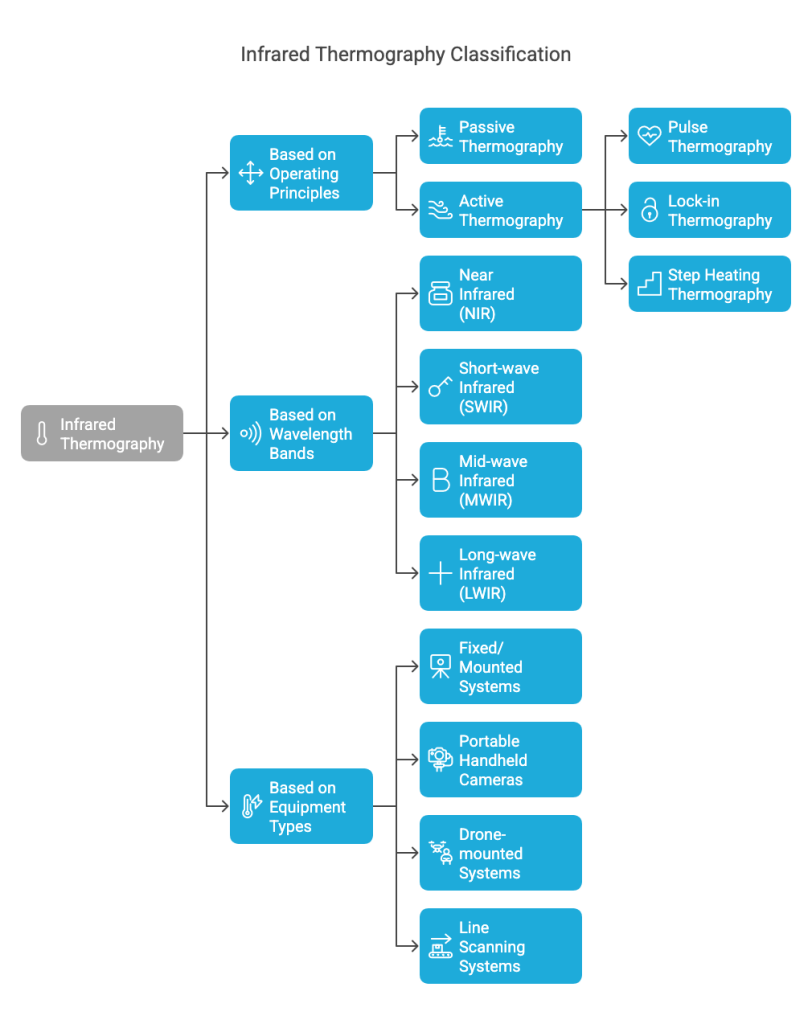
Source: WorkTrek.com
Infrared Thermography Testing Techniques
Infrared thermography is a powerful tool in nondestructive testing (NDT). This technique evaluates the integrity of materials, components, or systems without causing damage. By detecting infrared radiation and measuring temperature differences, infrared thermography can identify anomalies that may indicate defects or potential failures.
Non-Destructive Testing (NDT)
Non-destructive testing (NDT) using infrared thermography involves applying a thermal stimulus to a material or component and capturing the resulting temperature differences with an infrared camera. This data is then analyzed to detect defects such as cracks, corrosion, or delamination.
Infrared thermography NDT is widely used in the aerospace, automotive, and construction industries to ensure the safety and reliability of materials and components.
One key advantage of infrared thermography NDT is its noninvasive nature. It allows fast data acquisition and high-resolution imaging without damaging the test subject.
However, accurately interpreting thermal images requires specialized equipment and training. Despite these challenges, infrared thermography remains a valuable technique for detecting defects and evaluating the integrity of various systems, from electrical installations to structural components.
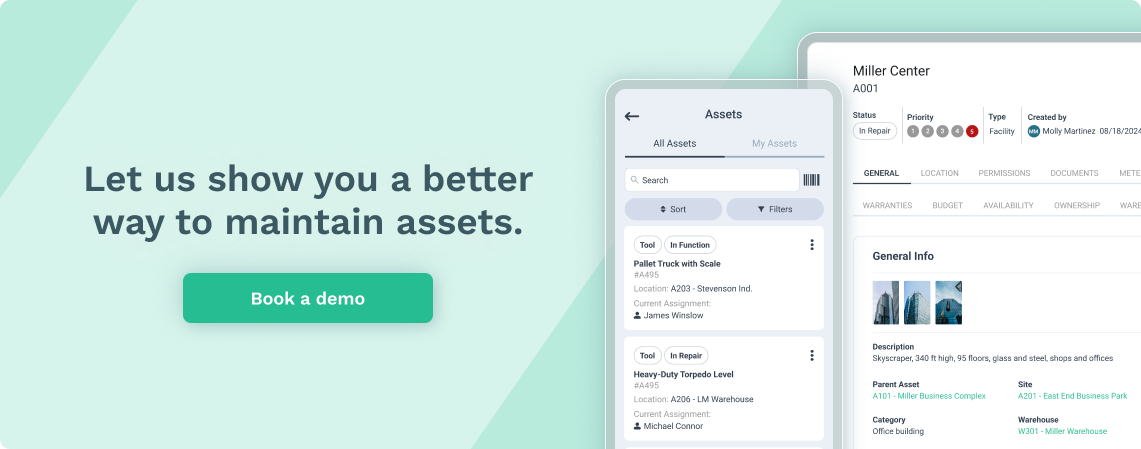
Applications in Maintenance
Electrical Maintenance
Thermography can detect overheating electrical components, loose connections, load imbalances, and other electrical faults before they cause failures. Common inspection targets include switchgear, motor control centers, transformers, circuit breakers, and high-voltage transmission lines.
Mechanical System Maintenance
It can identify friction problems, misalignments, and lubrication failures in rotating equipment. Common applications include monitoring bearings, gearboxes, motors, pumps, and conveyors to detect abnormal heating patterns.
Building Maintenance
Thermography helps identify heat loss, moisture intrusion, insulation defects, and air leakage in building envelopes. It can also detect hidden water damage, roof leaks, and heating/cooling system inefficiencies.
Preventive Maintenance Programs
Regular thermographic inspections are integrated into predictive maintenance schedules to detect developing problems before they cause failures. This often includes establishing temperature baselines for equipment and monitoring for changes over time.
Benefits of Infrared Thermography: Detecting Temperature Differences
- Non-Contact Testing: Equipment can be inspected during operation without disruption or shutdown.
- Early Fault Detection: Problems can be identified before they lead to catastrophic failures, reducing unplanned downtime.
- Safety Enhancement: Reducing the risk of electrical fires, equipment failures, and associated workplace hazards.
- Cost Savings: By preventing unexpected breakdowns and extending equipment life, thermography reduces maintenance costs and production losses.
- Wide Area Coverage: Large areas can be scanned, making inspections efficient.
- Preventive Maintenance Support: Provides objective data for condition-based maintenance programs rather than relying on fixed time intervals.
- Documentation: Creates records of equipment condition that can be compared over time to track degradation.
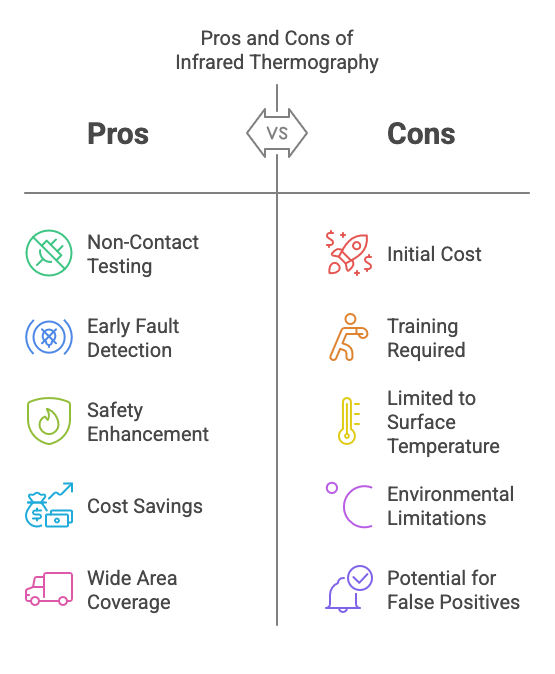
Source: WorkTrek.com
Drawbacks and Limitations
- Reference Standards: There’s sometimes a lack of standardized critical temperature thresholds for different applications and equipment types.
- Equipment Cost: Quality infrared cameras and analysis software require significant investment.
- Training Requirements: Accurate interpretation of thermograms requires specialized training and certification.
- Environmental Factors: Wind, reflections, ambient temperature, and humidity can all affect readings and must be accounted for.
- Surface Limitations: Different materials emit infrared energy differently (emissivity variations), which can complicate interpretation.
- Detection Depth: Primarily detects surface temperature; subsurface issues may only be detected indirectly through their surface effects.
- Interpretation Challenges: Thermal patterns can sometimes be ambiguous, requiring experience to diagnose the underlying issue correctly.
- Calibration Requirements: Equipment requires regular calibration to maintain accuracy.
Get a Free WorkTrek Demo
Let's show you how WorkTrek can help you optimize your maintenance operation.
Try for free