What is Inventory Management?
Inventory Management is a systematic and strategic approach to overseeing and controlling the flow of goods, materials, and resources within an organization. It encompasses the entire lifecycle of inventory items from procurement to final use or sale, including ordering, receiving, storing, tracking, maintaining, and distributing these materials.
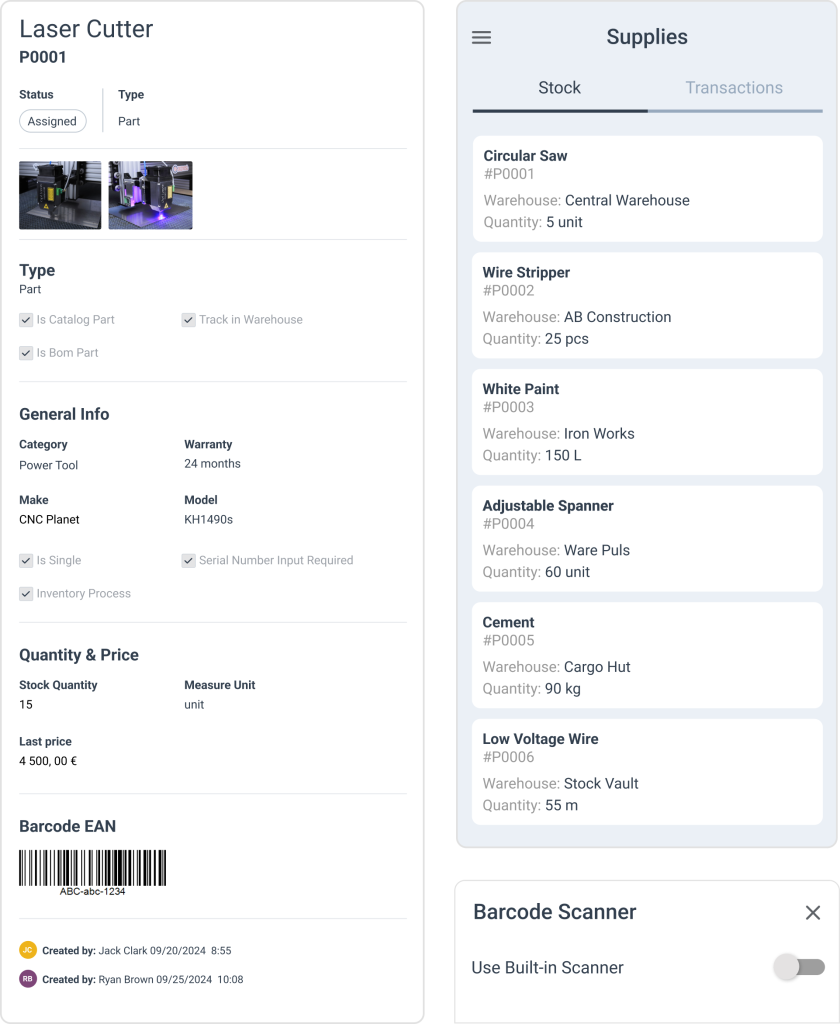
Think of it as an orchestra conductor, ensuring all pieces move harmoniously to create the desired outcome.
At its core, Inventory Management serves as the bridge between supply chain operations and an organization’s operational needs. It answers four fundamental questions:
- What items do we need?
- How much of each item should we keep?
- When should we order more?
- Where should we store everything?
Key Components of Inventory Management
Modern Inventory Management integrates several key components:
Planning and Forecasting: Using historical data, market trends, and predictive analytics to anticipate future needs and optimize stock levels. This is similar to how a weather forecaster uses multiple data points to predict tomorrow’s weather.
Stock Control: Maintaining precise records of what’s available, where it’s located, and its condition. This includes establishing minimum and maximum levels for each item, much like maintaining a fuel gauge in your car – you don’t want to run empty, but you also don’t want to overflow the tank.
Warehousing: The physical organization and storage of items to maximize space utilization while ensuring easy access and proper preservation. Think of this as organizing a library where books (inventory items) must be protected and readily accessible.
Movement Tracking: Monitoring the flow of items in and out of inventory, including documentation of all transactions and transfers. This creates a historical record, like a bank statement tracking deposits and withdrawals.
Cost Management: Balancing inventory expenses against the organization’s needs. This includes considering storage costs, ordering costs, and the opportunity cost of tied-up capital.
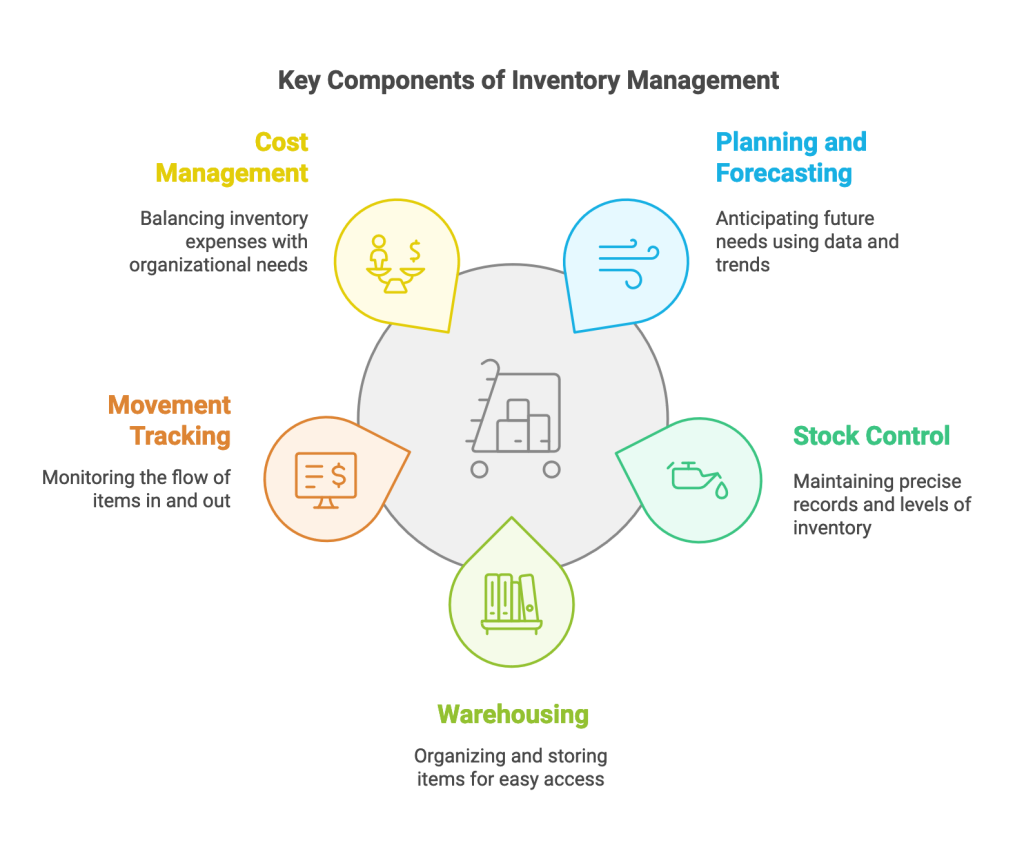
Type of Inventory Management Systems
The primary types used in maintenance organizations include perpetual inventory systems, which track stock levels in real time through automated systems and software. Periodic inventory systems involve regular manual counts at set intervals.
ABC analysis systems categorize items based on their value and criticality, with ‘A’ items being the most critical and expensive, requiring closest monitoring. Just-in-Time (JIT) inventory minimizes storage costs by ordering parts only when needed, though this requires precise timing and reliable suppliers. Min-max systems establish minimum and maximum stock levels for each item, triggering orders when inventory reaches the minimum threshold.
Best Practices for Maintenance Organizations
Successful maintenance organizations implement several key practices in their inventory management. First, they establish clear categorization systems for all parts and materials, using standardized naming conventions and location coding. They implement robust tracking systems, often using computerized maintenance management systems (CMMS) to monitor usage patterns and automate reordering processes.
Another crucial practice is setting appropriate reorder points based on lead times and critical equipment needs. Organizations should regularly analyze usage data to optimize stock levels and prevent stockouts and excess inventory. They should also maintain accurate documentation of all inventory movements and conduct regular cycle counts to verify system accuracy.
Physical organization plays a vital role, too – using proper storage methods, clear labeling, and organizing items by frequency of use or maintenance area can significantly improve efficiency. Many organizations also establish relationships with multiple suppliers to ensure supply reliability and competitive pricing.
Importance to Maintenance Organizations
Inventory management is crucial for maintenance organizations for several interconnected reasons. First, it directly impacts equipment downtime—having the right parts available when needed can mean the difference between a quick repair and an extended equipment shutdown. This downtime can have significant financial implications, especially in manufacturing or production environments.
From a financial perspective, effective inventory management helps control carrying costs while ensuring necessary parts are available. Poor inventory management can lead to either excessive capital tied up in unused inventory or costly emergency purchases and shipping charges for urgently needed items.
Moreover, proper inventory management supports maintenance planning and scheduling. Maintenance planners can schedule work more effectively and efficiently when they know exactly what parts are available. This leads to better resource utilization and more predictable maintenance operations.
Another critical aspect is the impact on maintenance technician productivity. When parts are well-organized and readily available, technicians spend less time searching for materials and more time performing actual maintenance work. This increased wrench time directly translates to improved maintenance efficiency and equipment reliability.
Proper inventory management also enhances safety. Correct replacement parts ensure that repairs are made with appropriate components, reducing the risk of equipment failure or accidents due to improper parts usage.
Get a Free WorkTrek Demo
Let's show you how WorkTrek can help you optimize your maintenance operation.
Try for free