What is Six Sigma?
Six Sigma methodology is a data-driven, statistical-based approach to process improvement and quality management that aims to reduce defects and variations in business processes to an extremely low level – specifically, 3.4 defects per million opportunities (DPMO).
The term “sigma” refers to standard deviation in statistics, which measures how much variation exists in a process. The “six” represents achieving six standard deviations between the process mean and the nearest specification limit.
To understand this better, let’s break down the core elements:
Historical Context
Motorola developed the Six Sigma process in 1986 under engineer Bill Smith. It gained widespread adoption after Jack Welch made it central to General Electric’s business strategy in 1995. Since then, it has evolved into a comprehensive management approach organizations use worldwide.
Six Sigma represents one of the most significant developments in quality management and process improvement of the past several decades.
It emerged as a response to the increasing complexity of modern manufacturing processes and the need for near-perfect quality standards in an increasingly competitive global marketplace.
The methodology’s name derives from the statistical concept of standard deviation, represented by the Greek letter sigma (σ).
In statistical terms, achieving Six Sigma quality means a process is so well-controlled that it produces only 3.4 defects per million opportunities (DPMO), translating to a remarkable 99.99966% success rate.
When first proposed, this level of quality was revolutionary, as most manufacturing processes traditionally operated at three or four-sigma levels, producing thousands of defects per million opportunities.
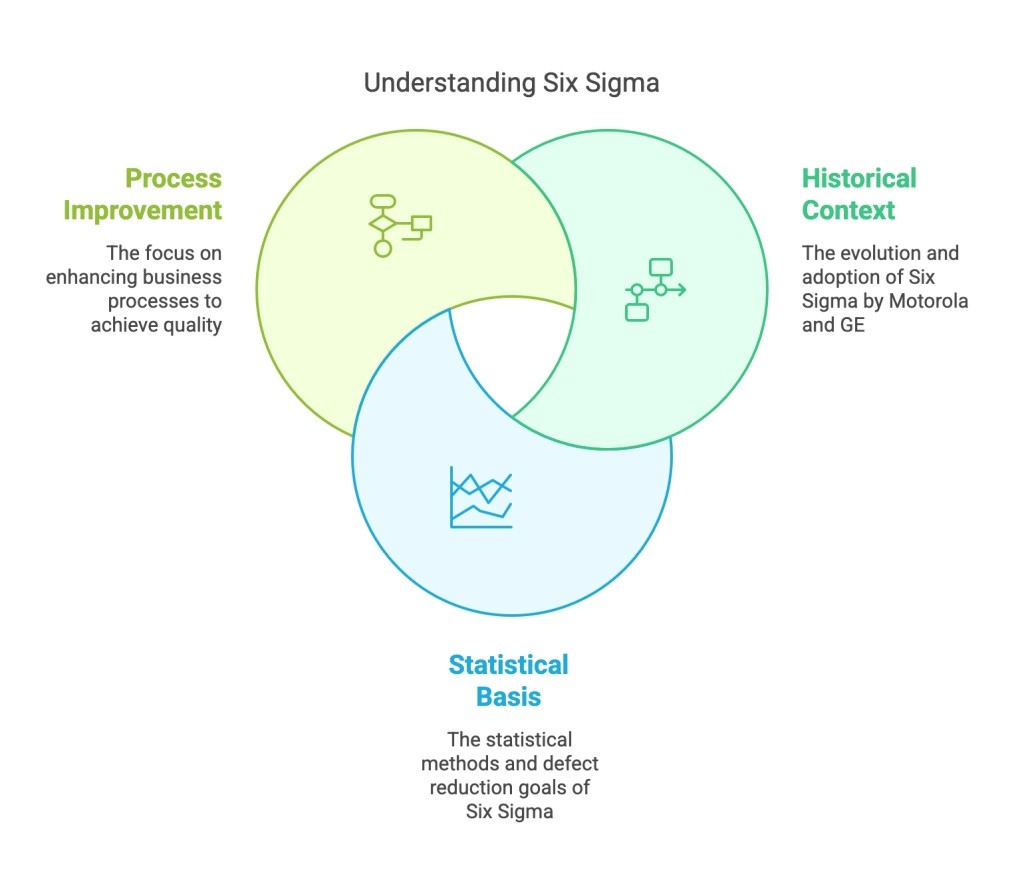
Source: Worktrek.com
Historical Development and Corporate Adoption
While Motorola laid the groundwork for Six Sigma, the methodology gained widespread recognition and adoption after Jack Welch made it the centerpiece of General Electric’s business strategy in 1995.
Under Welch’s leadership, GE demonstrated that Six Sigma could be applied beyond manufacturing to virtually any business process, from customer service to financial operations.
The success at GE led to rapid adoption across industries, with organizations like Allied Signal, Honeywell, and many others implementing their own Six Sigma programs.
This widespread adoption has led to the continuous evolution of the methodology, which incorporates elements from other quality management systems and adapts to new business challenges.
Core Philosophical Principles of Six Sigma
Six Sigma is built upon several fundamental philosophical principles that guide its implementation:
Process Focus
The methodology views all work as processes that can be defined, measured, analyzed, improved, and controlled. This process-oriented thinking applies whether the work involves manufacturing physical products or delivering services.
Data-Driven Decision Making
Six Sigma requires decisions based on verifiable data rather than assumptions or experience alone. This emphasis on quantitative analysis helps organizations make more objective decisions and measure the impact of changes.
Customer-Centric Approach
All improvements are evaluated based on their impact on customer satisfaction and value. The “voice of the customer” drives project selection and goal-setting.
Prevention Over Inspection
Six Sigma emphasizes designing quality into processes rather than trying to inspect defects out after they occur. This preventive approach is more cost-effective and reliable than reactive quality control.
Organizational Commitment
Success requires involvement at all organizational levels, from executive leadership to front-line workers. This total organizational commitment ensures a sustained focus on quality improvement.
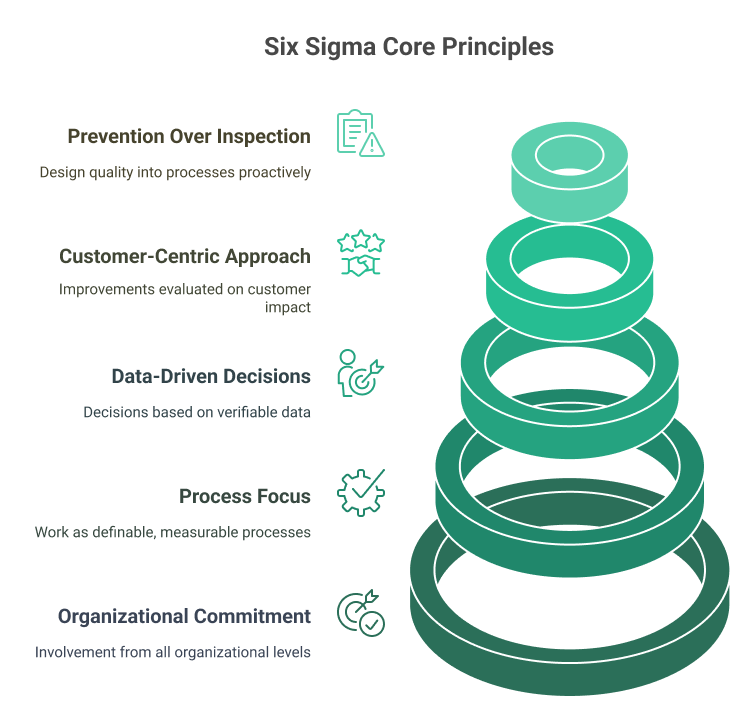
The DMAIC Improvement Cycle
The core of Six Sigma implementation is the DMAIC cycle, a structured approach to process improvement. Let’s examine each phase in detail:
Define Phase:
- Identify specific process problems and their impact on business results
- Develop a clear project charter outlining goals, scope, and timeline
- Map key stakeholders and their requirements
- Establish project team roles and responsibilities
- Create high-level process maps to understand current operations
Measure Phase:
- Develop detailed process maps showing all steps and decision points
- Identify key process input variables (KPIVs) and output measures
- Design and validate measurement systems
- Collect baseline performance data
- Calculate process capability and stability metrics
Analyze Phase:
- Apply statistical tools to identify patterns and relationships in data
- Conduct root cause analysis using techniques like fishbone diagrams
- Test hypotheses about cause-and-effect relationships
- Quantify the impact of different variables on process performance
- Prioritize improvement opportunities based on data analysis
Improve Phase:
- Generate potential solutions through structured brainstorming
- Evaluate and select the best solutions using decision matrices
- Conduct pilot tests of proposed improvements
- Implement solutions with careful change management
- Verify improvement through data collection and analysis
Control Phase:
- Develop control plans to maintain improvements
- Implement statistical process control methods
- Create standard operating procedures
- Train operators on new processes
- Monitor long-term performance and respond to variations
Statistical Foundations and Tools
The statistical underpinning of Six Sigma sets it apart from other quality improvement methodologies. Key statistical concepts and tools include:
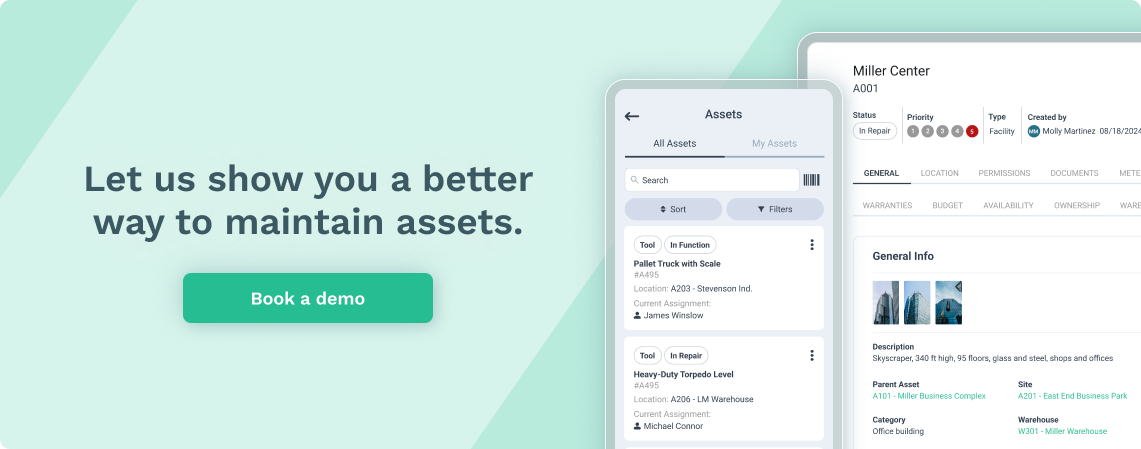
Normal Distribution and Standard Deviation
The normal distribution curve forms the theoretical basis for Six Sigma.
In a normal distribution, approximately 68% of data points fall within one standard deviation of the mean, 95% within two standard deviations, and 99.73% within three standard deviations.
Six Sigma aims to achieve six standard deviations between the process mean and specification limits, allowing for some natural drift over time.
Process Capability Indices
Cp and Cpk measurements compare process variation to specification limits, indicating how well a process can meet requirements. A process operating at Six Sigma levels will have very high capability indices, typically above 2.0.
Statistical Process Control (SPC)
Control charts monitor process performance over time, helping distinguish between normal variation and special causes requiring investigation.
Different types of control charts are used depending on the data type and process characteristics.
Design of Experiments (DOE):
DOE allows systematic investigation of process variables to optimize performance. This structured approach to experimentation is more efficient than traditional one-factor-at-a-time testing.
Regression Analysis
Various regression techniques help understand relationships between variables and predict process outcomes. Multiple regression analysis can model complex processes with many input variables.
Organizational Structure and Roles
Six Sigma implementation requires a well-defined organizational structure with clear roles and responsibilities:
Executive Leadership:
- Champions Six Sigma initiative throughout the organization
- Allocates resources and removes barriers
- Sets strategic direction and priorities
- Reviews project progress and results
- Ensures alignment with business objectives
Master Black Belts:
- Serve as technical experts and mentors
- Develop training materials and curriculum
- Coach Black Belts and Green Belts
- Provide statistical expertise
- Help select and scope projects
Black Belts:
- Lead complex improvement projects full-time
- Apply advanced statistical tools
- Coach Green Belts
- Train team members
- Report results to leadership
Green Belts:
- Lead smaller projects part-time
- Apply basic statistical tools
- Participate in Black Belt projects
- Support data collection and analysis
- Maintain regular job responsibilities
Yellow Belts:
- Participate in improvement projects
- Apply basic problem-solving tools
- Collect and analyze data
- Implement solutions
- Maintain improved processes
Implementation Challenges and Success Factors
Successfully implementing Six Sigma requires addressing several common challenges:
Cultural Resistance
Organizations must overcome resistance to change and create a culture that embraces data-driven decision-making. This often requires significant investment in training and communication.
Resource Allocation
Dedicating qualified personnel to improvement projects while maintaining regular operations can strain resources. Organizations must carefully balance these competing demands.
Project Selection
Choosing the right projects is critical for success. Projects should align with strategic objectives, have a clear business impact, and be achievable within reasonable timeframes.
Measurement Systems
Many processes lack reliable measurement systems, making it challenging to collect accurate data. Developing and validating measurement systems often requires significant effort.
Sustainability
Maintaining improvements over time requires robust control systems and ongoing monitoring. Organizations must prevent regression to old practices.
Key success factors include
Leadership Commitment
Visible and sustained support from top management for a Six Sigma project is essential for success. Leaders must demonstrate commitment through actions, not just words.
Training and Development
Comprehensive training programs ensure team members have the knowledge and skills to apply Six Sigma tools effectively. Additionally, organizations can consider Six Sigma certifications for their internal team members.
Project Management
Strong project management skills help ensure projects stay on track and deliver expected results. This includes clear scope definition, milestone tracking, and risk management.
Communication
Regular communication about project progress and results helps maintain momentum and share best practices across the organization.
Recognition and Rewards
Acknowledging and rewarding successful projects encourages continued participation and maintains motivation.
Modern Applications and Integration
Today, Six Sigma is often integrated with other improvement methodologies, particularly Lean manufacturing principles, creating Lean Six Sigma.
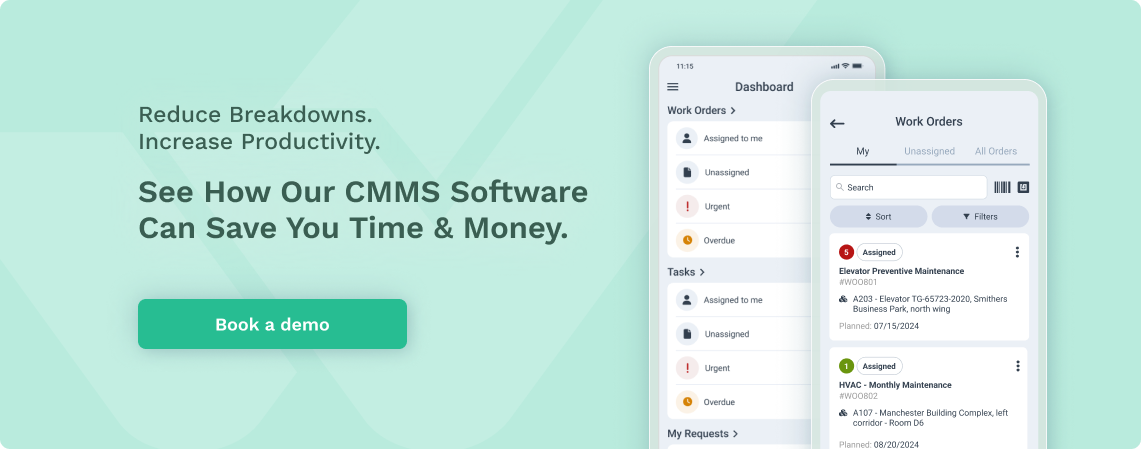
This combination brings together:
Lean Principles
- Focus on eliminating waste
- Improve flow and reduce cycle time
- Simplify processes
- Create pull systems
- Standardize work
Six Sigma Methods
- Reduce variation
- Use statistical analysis
- Measure process capability
- Design robust processes
- Control quality
This integrated approach has found applications across diverse industries:
Manufacturing
- Product quality improvement
- Process optimization
- Defect reduction
- Yield improvement
- Cost reduction
Healthcare
- Patient safety improvement
- Clinical process standardization
- Medical error reduction
- Operating room efficiency
- Length of stay reduction
Services
- Customer satisfaction improvement
- Transaction accuracy
- Response time reduction
- Service quality standardization
- Cost efficiency
Financial Services
- Risk management
- Transaction processing
- Fraud detection
- Customer service
- Compliance processes
Future Trends and Evolution
Six Sigma continues to evolve with changing business needs and technological capabilities:
Digital Transformation:
Integration with digital technologies and automation creates real-time process monitoring and adjustment opportunities.
Big Data Analytics
Advanced analytics and machine learning enhance Six Sigma’s statistical tools, enabling more sophisticated analysis of complex processes.
Agile Integration
Combining Six Sigma with Agile methodologies helps organizations balance quality improvement with speed and flexibility.
Sustainability Focus
Growing emphasis on environmental sustainability creates new applications for Six Sigma in reducing waste and improving resource efficiency.
Get a Free WorkTrek Demo
Let's show you how WorkTrek can help you optimize your maintenance operation.
Try for free