What is Total Productive Maintenance (TPM)?
Total Productive Maintenance (TPM) represents a holistic and revolutionary approach to equipment and facility management that transcends traditional maintenance paradigms. Unlike conventional maintenance strategies, which operate reactively and in isolation from core business functions, TPM seamlessly integrates maintenance activities into the organization’s operational philosophy.
This comprehensive methodology views equipment upkeep not as a separate cost center or necessary evil, but rather as a strategic investment that directly contributes to productivity, quality, cost reduction, delivery performance, safety, and employee morale.
At its core, TPM process transforms the relationship between operators and their equipment, fostering a culture of shared responsibility where everyone—from frontline machine operators to senior executives—plays an active role in maintaining optimal equipment conditions.
This collaborative approach dismantles the traditional boundaries between maintenance departments and production teams, creating a unified workforce committed to maximizing equipment effectiveness through continuous improvement initiatives.
TPM originated in Japan during the post-war industrial renaissance, evolving from preventive maintenance practices introduced by American manufacturers. The Nippon Denso Company (now Denso Corporation), a member of the Toyota group, is credited with developing the first TPM programs in the early 1960s.
The Japanese Institute of Plant Maintenance (JIPM) later formalized and propagated these practices, establishing TPM as a cornerstone of world-class manufacturing excellence.
Today, TPM principles have expanded beyond manufacturing to encompass diverse sectors, including healthcare, hospitality, transportation, and administrative services—anywhere equipment reliability and process efficiency directly impact organizational performance.
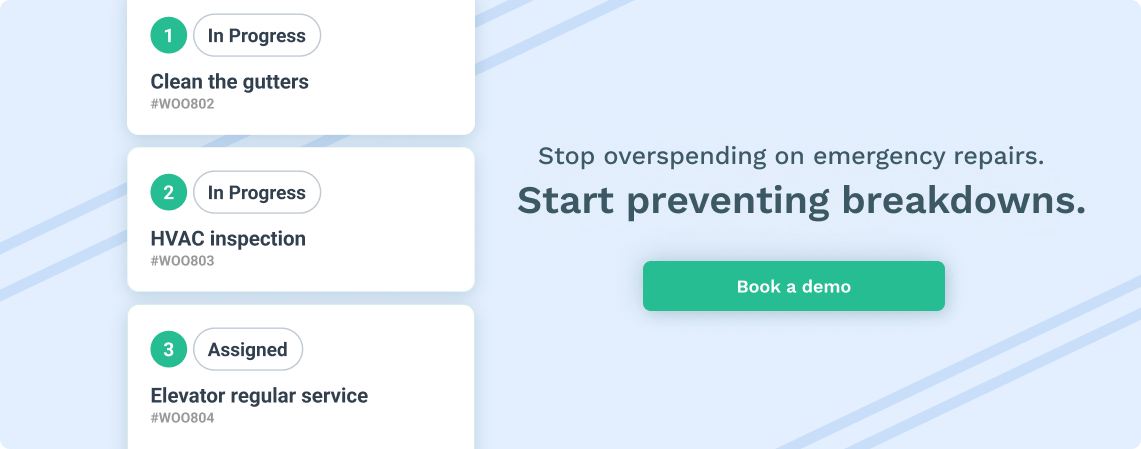
Benefits of Total Productive Maintenance (TPM)
Implementing a Total Productive Maintenance (TPM) program can bring numerous benefits to an organization. Some of the key benefits of TPM include:
- Improved Equipment Effectiveness: TPM helps maximize equipment effectiveness by reducing downtime, increasing productivity, and improving product quality. Organizations can ensure their machinery operates at peak performance by focusing on proactive maintenance techniques.
- Increased Efficiency: TPM streamlines maintenance processes, reduces waste, and improves operational efficiency. This holistic approach optimizes equipment operation, leading to smoother production flows.
- Cost Savings: TPM can help reduce maintenance costs by identifying and addressing potential issues before they become major problems. Preventive and predictive maintenance strategies minimize the need for costly emergency repairs and extend the lifespan of equipment.
- Improved Safety: TPM promotes a safe working environment by identifying and addressing potential safety hazards. Regular inspections and maintenance activities help prevent accidents and ensure compliance with safety standards.
- Increased Employee Engagement: TPM empowers employees to take ownership of their work and equipment, increasing job satisfaction and engagement. When operators are involved in maintenance tasks, they better understand their machinery and contribute to its reliability.
- Improved Quality: TPM helps enhance product quality by reducing defects and improving manufacturing processes. Organizations can produce consistent, high-quality products by maintaining equipment in optimal condition.
- Increased Customer Satisfaction: TPM improves customer satisfaction by delivering high-quality products on time. Reliable equipment and efficient processes ensure that production schedules are met, and customer expectations are exceeded.
The Eight Pillars of TPM
- Autonomous Maintenance (Jishu Hozen): Through an autonomous maintenance program, operators take ownership of routine maintenance tasks such as cleaning, lubricating, and inspecting equipment. This creates a sense of ownership and allows maintenance specialists to focus on more complex tasks.
- Planned Maintenance (Keikaku Hozen): Scheduling maintenance activities based on predicted and measured failure rates rather than waiting for equipment to fail. This includes preventive maintenance, corrective maintenance, and maintenance prevention.
- Quality Maintenance (Hinshitsu Hozen): Designing error detection and prevention into production processes. The focus is on eliminating quality defects by identifying and addressing equipment conditions that might create quality issues.
- Focused Improvement (Kobetsu Kaizen): Teams work together to achieve regular, incremental improvements in equipment operation. This often involves cross-functional teams identifying and implementing improvements to eliminate losses.
- Early Equipment Management (Shoki Kanri): Using practical knowledge and understanding of manufacturing equipment to improve new equipment design. This involves incorporating maintenance considerations into new equipment design to prevent future issues.
- Training and Education: Improving the skills of all employees involved in TPM. Operators are trained to maintain equipment and identify potential issues, while maintenance staff learn to train operators and develop more specialized technical skills.
- Safety, Health, and Environment: Creating a safe workplace and surrounding area not damaged by manufacturing processes. This includes eliminating potential health and safety risks associated with equipment and processes.
- TPM in Administration: Extending TPM principles to administrative functions. This involves applying improvement techniques to administrative processes to reduce waste and improve efficiency in non-production areas.
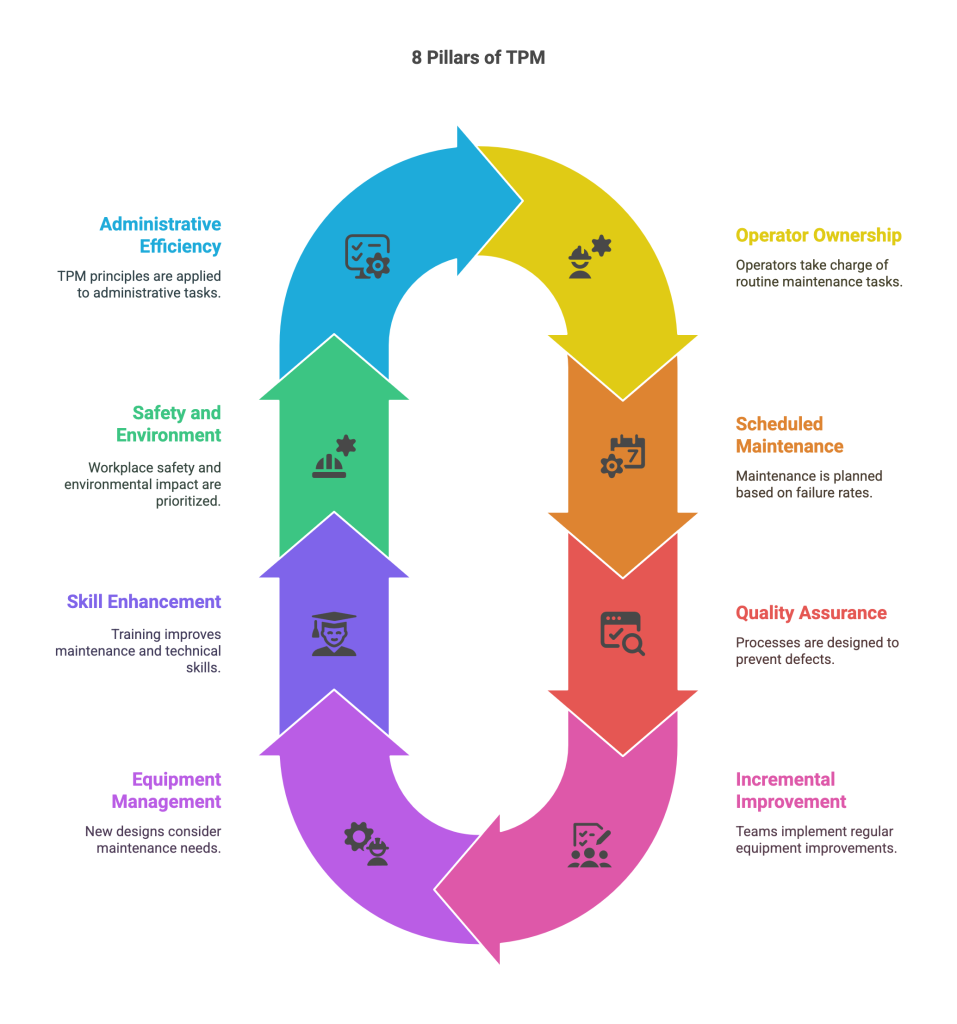
Source: WorkTrek.com
Implementing Total Productive Maintenance (TPM)
Implementing a TPM program requires careful planning, preparation, and execution. Here are the steps to implement TPM:
Preparation
- Establish a TPM Team: Assemble a cross-functional team to lead the TPM implementation effort. This team should include representatives from various departments, such as production, maintenance, quality, and engineering, to ensure a comprehensive approach.
- Define TPM Goals and Objectives: Clearly define the TPM program’s goals and objectives. These should align with the organization’s overall business objectives and focus on improving equipment effectiveness, reducing downtime, and enhancing product quality.
- Conduct a Current State Assessment: Assess the current state of maintenance processes and equipment effectiveness. This involves evaluating existing maintenance practices, identifying areas for improvement, and understanding the root causes of equipment failures.
- Develop a TPM Strategy: Develop a comprehensive TPM strategy that aligns with the organization’s goals and objectives. This strategy should outline the steps for implementing TPM, including training programs, maintenance schedules, and performance metrics.
Proactive Maintenance Techniques
- Autonomous Maintenance: Empower operators to perform routine maintenance tasks and inspections. This includes cleaning, lubricating, and checking equipment for abnormalities, fostering a sense of ownership and responsibility.
- Planned Maintenance: Schedule regular maintenance activities to prevent equipment failure. This involves creating a maintenance calendar based on predicted and measured failure rates, ensuring that maintenance tasks are performed at optimal intervals.
- Predictive Maintenance: Use condition monitoring and predictive analytics to identify potential equipment failures. Organizations can predict when equipment will likely fail by analyzing data from sensors and other monitoring tools and taking preventive action.
- Preventive Maintenance: Perform regular maintenance activities to prevent equipment failure. This includes routine inspections, adjustments, and parts replacements to ensure that equipment remains in good working condition.
Addressing Major Losses
- Identify Major Losses: Identify the major losses that are impacting equipment effectiveness. These could include breakdowns, setup and adjustment losses, idling and minor stoppages, reduced speed, defects, and rework.
- Analyze Root Causes: Analyze the root causes of major losses. This involves using tools such as root cause analysis (RCA) and failure mode and effects analysis (FMEA) to understand the underlying issues.
- Develop a Plan: Develop a plan to address major losses. This plan should include specific actions, timelines, and responsibilities to eliminate or reduce the identified losses.
- Implement the Plan: Implement the plan and monitor progress. Regularly review the effectiveness of the implemented actions and make adjustments as necessary to ensure continuous improvement.
By following these steps, organizations can successfully implement a TPM program that improves equipment effectiveness, increases efficiency, and reduces costs.
Examples of TPM Implementation
- Automotive Manufacturing: At Toyota factories, operators conduct daily equipment inspections and routine cleaning. They use visual control boards to track maintenance activities and equipment performance. When abnormalities are detected, operators might place color-coded tags on the equipment to signal the nature of the issue. This autonomous maintenance has significantly reduced unplanned downtime.
- Food and Beverage Industry: A brewery might implement TPM by training machine operators to regularly clean and sanitize filling lines, conduct basic maintenance checks, and monitor equipment performance metrics. This helps prevent contamination and reduces the risk of unexpected breakdowns during production runs.
- Electronics Manufacturing: Companies like Intel use TPM to maintain sensitive semiconductor manufacturing equipment. Operators regularly measure key parameters, perform standardized cleaning procedures, and conduct visual inspections. Maintenance specialists use condition monitoring tools to predict potential failures before they occur. This has helped improve equipment life and reduce defect rates.
- Pharmaceutical Production: TPM might involve operators monitoring critical parameters like temperature and pressure during pharmaceutical facility production. They perform scheduled equipment cleaning and follow detailed standard operating procedures for minor adjustments. This helps maintain compliance with strict quality standards while improving equipment reliability.
Participants in TPM
TPM is a company-wide initiative that involves multiple levels of the organization:
- Equipment Operators: The frontline workers who use the equipment daily become the first line of defense in equipment maintenance by performing routine checks, cleanings, and minor maintenance.
- Maintenance Technicians Provide specialized technical knowledge, perform complex repairs, and assist with training operators on basic maintenance tasks. Maintenance personnel are integral members of cross-functional teams tasked with identifying and addressing operational losses and implementing Total Productive Maintenance programs.
- Production Supervisors and Managers: Support TPM implementation by allocating time for maintenance activities, recognizing good maintenance practices, and removing barriers to implementation.
- Engineering and Design Teams: Incorporate maintenance considerations into own equipment design and modifications to improve maintainability.
- Quality Department: Collaborates on identifying how equipment conditions affect product quality and helps develop monitoring methods.
- Top Management: Provides vision, resources, and commitment to the TPM program, aligning it with overall business objectives.
- TPM Coordinator/Facilitator: Often assigned to manage the TPM implementation process, provide training, and track progress.
- Cross-functional Teams: Formed to address specific equipment issues or implement improvements, bringing together different perspectives and expertise. The maintenance team plays a crucial role in addressing issues reported by trained machine operators during autonomous maintenance practices. Maintenance teams leverage Computerized Maintenance Management Systems (CMMS) to streamline processes, track performance metrics, and promote preventive maintenance.
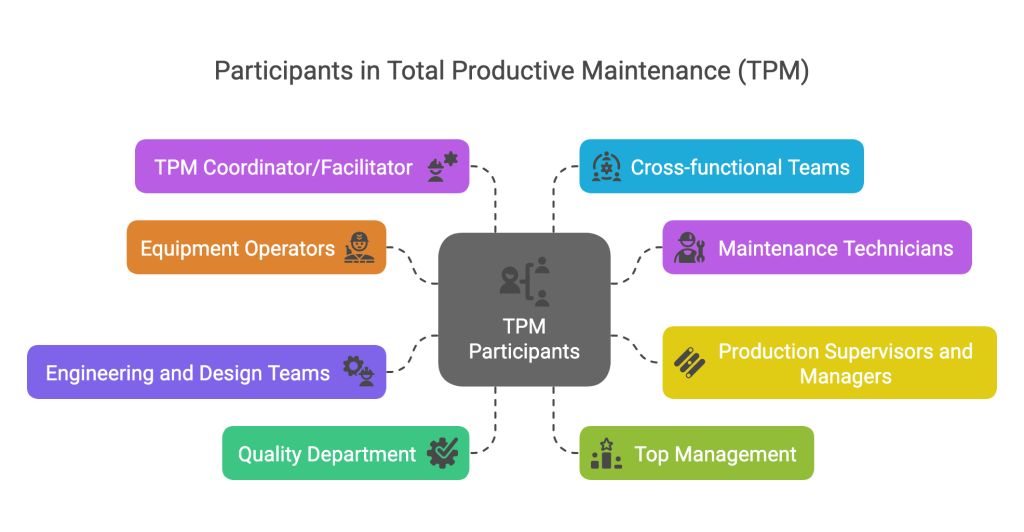
Source: WorkTrek.com
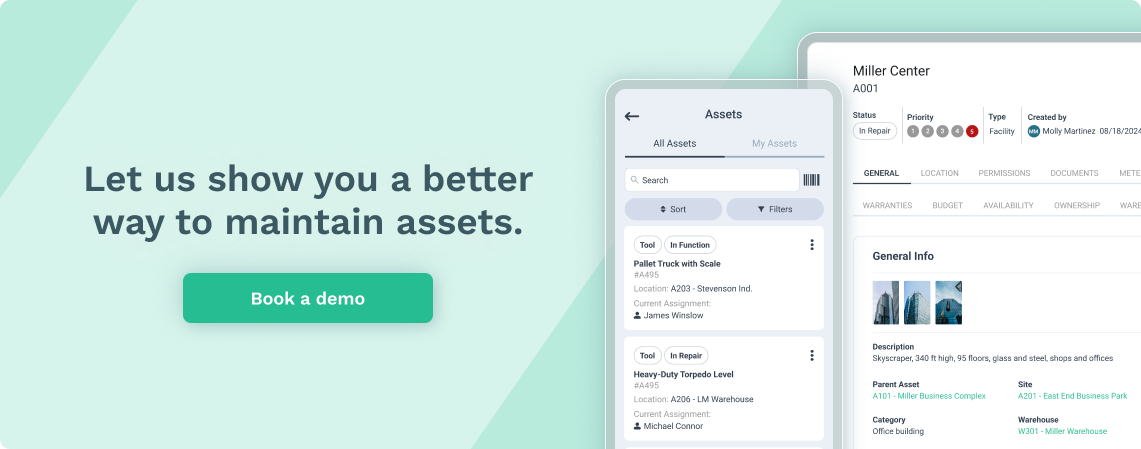
Pros and Cons of TPM
Advantages
- Reduced Equipment Downtime: Preventive and predictive maintenance approaches help catch potential issues before they cause breakdowns.
- Improved Equipment Longevity: Regular care and maintenance extend the useful life of machinery and equipment.
- Enhanced Product Quality: Well-maintained equipment produces fewer defects and more consistent products.
- Increased Productivity: Less downtime and fewer defects translate directly to higher output.
- Greater Employee Engagement: Operator involvement in equipment care creates ownership and pride in work.
- Safer Working Environment: Regular equipment inspections and maintenance help identify and address safety hazards.
- Knowledge Transfer: The system promotes knowledge sharing between maintenance specialists and operators.
- Reduced Maintenance Costs: While preventive maintenance requires investment, it typically costs less than emergency repairs and production losses from unplanned downtime.
Disadvantages
- Significant Initial Investment: Implementing TPM requires substantial resources for training, potentially new tools and monitoring equipment, and time for developing new procedures.
- Time-consuming Implementation: Full TPM implementation typically takes 3-5 years to embed in the organization’s culture fully.
- Resistance to Change: Operators may resist taking on maintenance responsibilities, while maintenance staff might feel their job security is threatened.
- Difficult to Sustain: TPM initiatives often lose momentum without ongoing management commitment.
- Challenging to Measure: Some benefits of TPM are difficult to quantify directly, making it hard to demonstrate ROI.
- Risk of Over-Maintenance: Without proper balance, there’s a risk of performing more maintenance than necessary, increasing costs without proportional benefits.
- Requires Cultural Shift: TPM demands a fundamentally different way of thinking about equipment and maintenance responsibilities, which can be challenging to establish.
- May Initially Increase Workload: During implementation, proactive and preventive maintenance may be necessary, temporarily increasing the overall workload.
I’ll add a detailed section on Quality Maintenance, which is one of the eight pillars of TPM:
Quality Maintenance (Hinshitsu Hozen) in Detail
Quality Maintenance represents a critical pillar of TPM that focuses on preventing quality defects through proactive equipment management rather than detecting defects after they occur. This approach recognizes the direct relationship between equipment condition and product quality.
Core Principles of Quality Maintenance
- Zero Defects Philosophy: Quality Maintenance operates on the premise that equipment in optimal condition should produce zero defects. Any deviation in product quality is considered a signal of equipment deterioration or improper functioning that must be addressed systematically.
- Equipment-Quality Connection: This pillar establishes connections between specific equipment conditions and the product’s quality characteristics. For example, a worn bearing might cause vibration, leading to dimensional variations in machined parts.
- Process Parameter Control: Quality Maintenance involves identifying and monitoring critical process parameters that affect product quality. When these parameters drift outside established limits, corrective action is taken before defects occur.
- Root Cause Analysis: When quality issues arise, Quality Maintenance employs rigorous analytical techniques to trace them back to specific equipment conditions rather than making process adjustments that might mask underlying equipment problems.
Implementation Steps for Quality Maintenance
- Condition-Quality Analysis: Teams analyze historical data to establish correlations between equipment conditions and quality defects. This creates a knowledge base of quality-equipment relationships.
- Critical Point Identification: The most significant equipment components affecting quality are identified and prioritized for monitoring and maintenance attention.
- Quality Control Points Establishment: Specific inspection points are established on equipment where conditions can be monitored to predict potential quality issues before they occur.
- Control Standards Development: Clear standards are created for equipment conditions, with acceptable ranges for parameters like temperature, pressure, vibration, or alignment that affect product quality.
- Checkpoint Management: Regular inspection routines are developed to monitor the critical quality control points, and operators and maintenance personnel are assigned responsibilities.
- Restoration and Improvement: When equipment deterioration is detected, restoration to optimal condition occurs promptly. Continuous improvement activities seek to extend periods between deterioration incidents.
Practical Examples of Quality Maintenance
- Injection Molding: In plastic injection molding, the temperature profile of the barrel is critical to material flow and final part quality. Quality Maintenance might involve:
- Installing temperature sensors at critical zones
- Establishing temperature variation limits based on quality correlation studies
- Creating operator checksheets for monitoring temperature patterns
- Developing preventive measures like heater inspection schedules
- Implementing automated alerts when temperatures drift from optimal ranges
- Precision Machining: In a CNC machining operation, spindle condition directly affects surface finish. Quality Maintenance practices might include:
- Regular vibration analysis of the spindle
- Checking runout measurements on a scheduled basis
- Establishing a correlation between vibration signatures and surface quality metrics
- Creating visual aids showing acceptable vs. unacceptable vibration readings
- Scheduling proactive spindle maintenance based on vibration trend analysis
- Pharmaceutical Tableting: Punch and die conditions directly affect tablet weight consistency in tablet production. Quality Maintenance strategies might include:
- Measuring punch lengths and diameters on a scheduled basis
- Creating wear limit standards based on historical quality data
- Training operators to identify early signs of punch wear
- Establishing rotation schedules for tooling based on critical wear points
- Using statistical process control to detect early signs of tool deterioration
Measuring Quality Maintenance Effectiveness
- First-Pass Yield: Tracking the percentage of products manufactured correctly the first time without rework or scrap.
- Cost of Poor Quality: Measuring direct costs (scrap, rework) and indirect costs (customer returns, warranty claims) related to quality issues.
- Equipment-Related Defect Rate: Monitoring how many defects can be traced to equipment conditions rather than other factors.
- Mean Time Between Quality Incidents: Tracking how long equipment runs between occurrences of quality-affecting deterioration.
- Predictive Success Rate: Evaluating how effectively the established condition monitoring predicts and prevents quality issues.
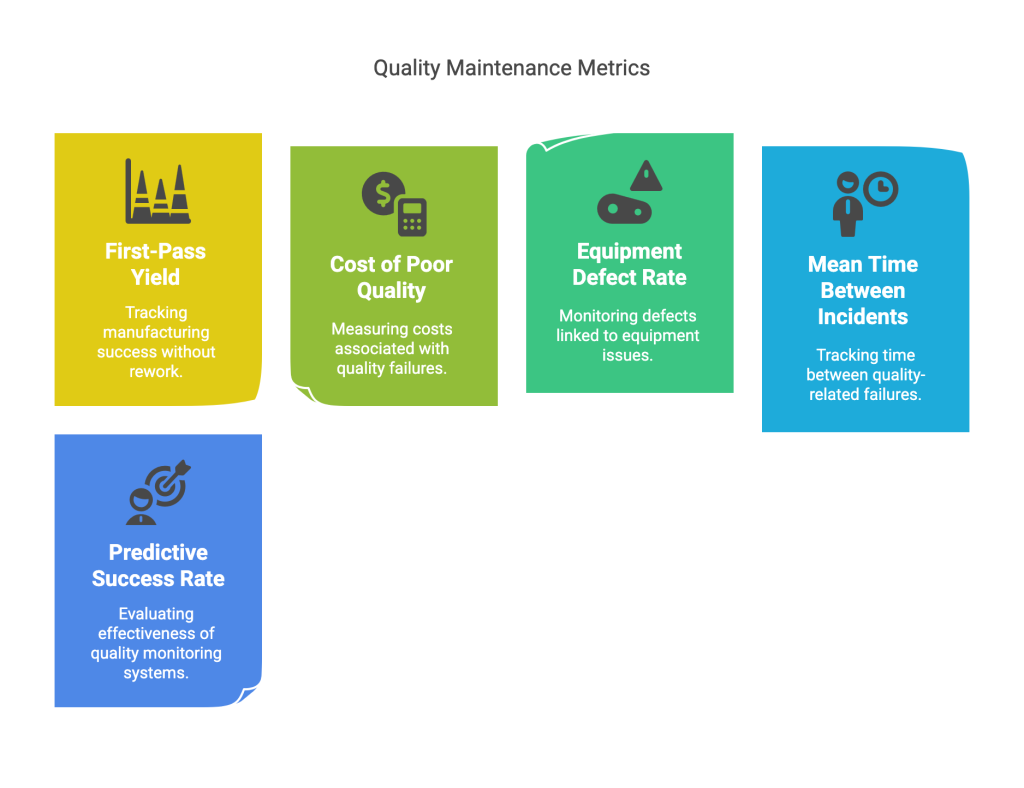
Source: WorkTrek.com
Integration with Other TPM Pillars
Quality Maintenance doesn’t exist in isolation but works synergistically with other TPM pillars:
- It relies on Autonomous Maintenance for basic equipment care that prevents quality deterioration.
- It informs Planned Maintenance by highlighting equipment components critical to quality.
- It provides feedback to Early Equipment Management to design new equipment with better stability.
- It drives Focused Improvement activities aimed at eliminating recurring quality-affecting conditions.
- It requires Training and Education to help operators understand quality-equipment relationships..
TPM represents a significant shift from traditional approaches to maintenance, but when successfully implemented, it can transform equipment performance and productivity while fostering greater collaboration between departments.
Get a Free WorkTrek Demo
Let's show you how WorkTrek can help you optimize your maintenance operation.
Try for free