What is Vibration Analysis?
Vibration analysis is a diagnostic method in modern machinery maintenance. This technique measures and interprets vibration patterns in rotating and reciprocating equipment to identify potential mechanical problems before they cause severe damage.
By monitoring the oscillatory movements of machine components, technicians can detect issues such as imbalances, misalignments, or bearing defects that might otherwise remain hidden until failure occurs.
The process is a part of predictive maintenance strategies across industries. Specialized vibration monitoring systems and sensors capture vibration frequencies from operating equipment. This allows maintenance teams to track performance over time and spot abnormal patterns.
As components age, they naturally tend to vibrate more intensely.
As mechanical components naturally vibrate more intensely with age and wear, these changes in vibration signatures provide early warning signals that help prevent unexpected downtime and extend the machine’s lifespan.
Understanding Vibration Basics
Vibration analysis requires knowledge of three key parameters that help identify machine issues. These include:
- Amplitude – The strength of vibration measured in displacement units (mils/micrometers), velocity (inches or millimeters per second), or acceleration (g’s)
- Frequency – How many vibration cycles occur per time unit, measured in Hertz (Hz)
- Phase – The timing relationship between waveforms, measured in degrees
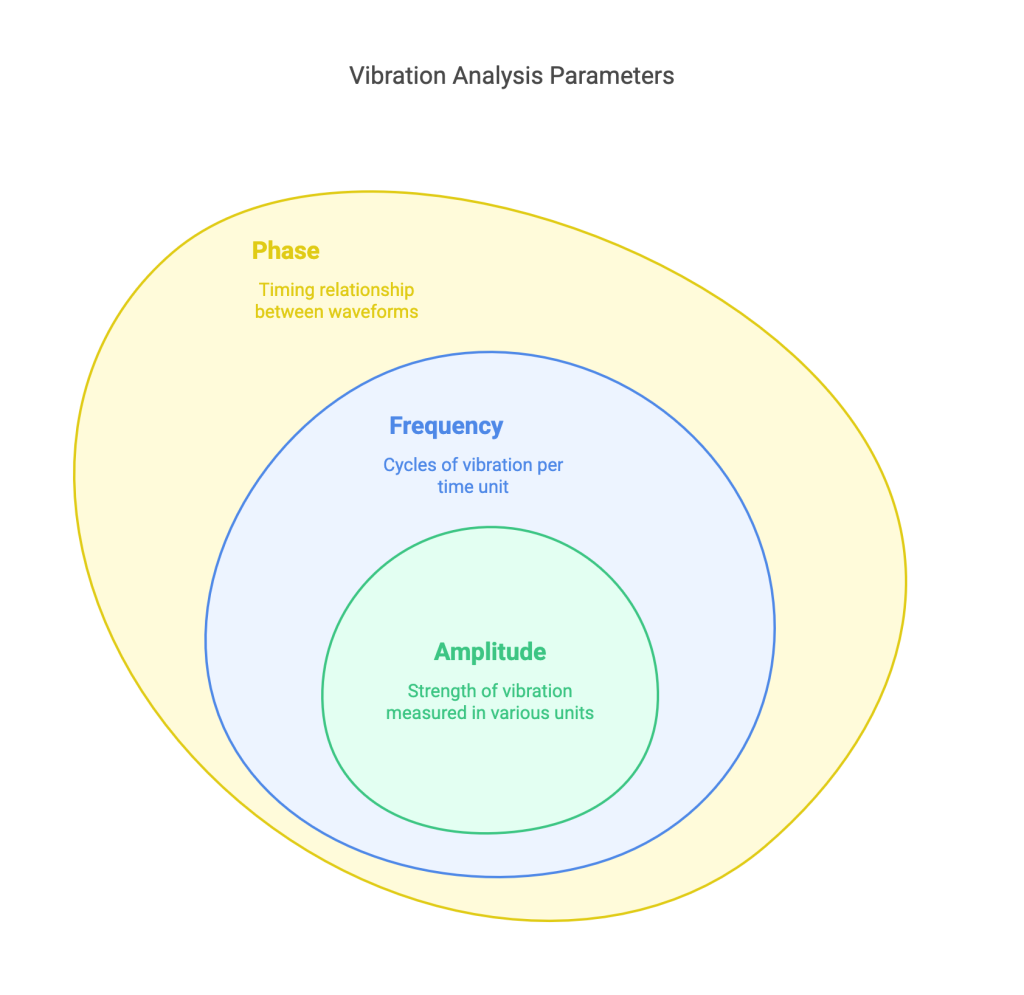
Source: Worktrek.com
Vibration analysis experts examine these parameters and waveform patterns to diagnose machine problems before they cause failures.
Vibrations fall into two main categories:
- Forced vibrations – These occur when external forces act on equipment, such as vibrations from running motors or pumps
- Natural vibrations – Also called resonance, these happen when a system vibrates at its inherent frequency
When a machine’s operating frequency matches its natural frequency, dangerous resonance can develop. This creates excessive vibration levels that may damage equipment if not addressed promptly.
Equipment monitoring professionals use specialized tools to track these parameters over time, creating baseline measurements for comparison that help detect early signs of potential failures.
How to Perform Vibration Testing and Analysis
Step 1: Collect Initial Equipment Information
Before starting any vibration measurements, gather crucial information about your machinery. Identify what sensors will work best for your specific equipment, paying attention to the required amplitude and frequency ranges.
These displacement sensors will be your primary data collection tools throughout the analysis process.
Important information to gather includes:
- Equipment specifications and design parameters
- Maintenance history and previous issues
- Normal operating speeds and load conditions
- Temperature ranges during typical operation
- Recommended measurement points
Your preparation quality directly affects your analysis results. Understanding the equipment thoroughly helps ensure accurate measurements and interpretation later in the process.
Step 2: Take Vibration Measurements
Once you’ve gathered preliminary information, it’s time to measure the vibrations in your machinery. This involves placing sensors at key measurement points to capture vibration data.
Common measurement devices include:
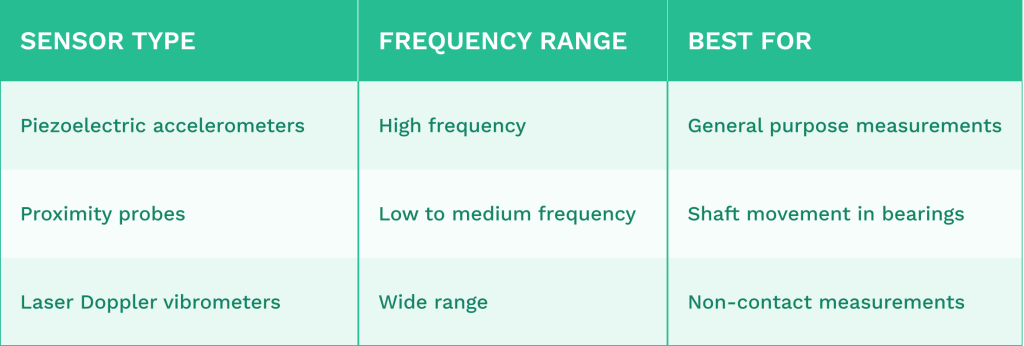
These devices capture vibration in three axes:
- Vertical (up-down)
- Horizontal (side-to-side)
- Axial (front-to-back)
For best results, take measurements under normal operating conditions. Multiple measurement points provide a complete picture of the machine’s vibration profile.
Step 3: Process the Measurement Data
After collecting vibration data, specialized software processes and analyzes the measurements. Modern analysis tools can detect patterns that might indicate developing problems in machinery.
Key analysis techniques include:
- Time domain analysis – Examines raw vibration signals over time, looking at factors like:
- Peak amplitude
- Root mean square (RMS) values
- Crest factor
- Wave pattern irregularities
- Frequency domain analysis – Converts time-based signals into frequency spectra using Fast Fourier Transform (FFT), making it easier to identify specific frequency-related issues.
- Envelope analysis – Filters and processes signals to detect early bearing failures and other high-frequency impact events.
- Modal analysis – Identifies natural frequencies and vibration patterns to detect potential structural issues.
Compare your findings with established standards and baseline measurements to identify abnormal conditions.
Step 4: Understand the Analysis Results
Proper interpretation requires understanding what different vibration patterns indicate about your machinery’s health. Analysts need to recognize specific frequency signatures associated with common mechanical problems.
Key frequency indicators to evaluate:
- Fundamental frequencies – Related to the rotation speed of components
- Harmonic patterns – Multiple frequencies showing regular intervals
- Sidebands – Secondary peaks appearing around main frequency components
These patterns help identify specific issues:
- High amplitude at 1× running speed → possible imbalance
- Elevated levels at 2× running speed → potential misalignment
- Multiple harmonics with high peaks → probable looseness
- Specific bearing defect frequencies → bearing deterioration
Comparing current results with historical data helps establish whether conditions are stable, improving, or deteriorating.
Step 5: Implement Necessary Repairs
After identifying problems through vibration analysis, establish clear thresholds for when action is required. When exceeded, these alarm levels trigger maintenance responses.
Types of alarm thresholds:
- Fixed thresholds – Based on industry standards for specific equipment types
- Trend-based alerts – Triggered by significant changes from historical patterns
- Statistical limits – Calculated using mean values and standard deviations from normal operation
When vibration levels exceed these thresholds, maintenance teams should:
- Schedule appropriate maintenance activities
- Adjust operating parameters if possible
- Order necessary replacement parts
- Plan for equipment downtime
- Document findings for future reference
The specific corrective action depends on the problem identified. For instance, imbalance might require rotor balancing, while bearing issues typically require component replacement.
Implementing these repairs before catastrophic failure saves significant downtime and emergency repair costs.
Key Advantages of Machine Vibration Monitoring
Vibration analysis serves as a powerful tool in modern maintenance strategies, delivering multiple benefits for organizations that implement it effectively:
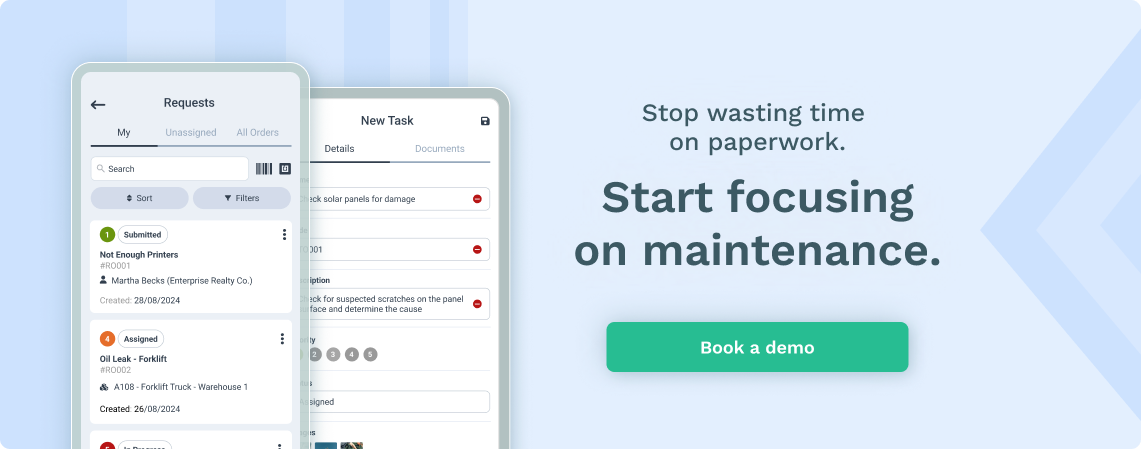
Early Problem Detection
- Identifies developing issues before human senses can detect them
- Allows maintenance teams to address problems proactively
- Prevents unexpected equipment failures
Better Maintenance Planning Vibration data helps organizations prioritize maintenance activities based on actual equipment conditions rather than fixed schedules. This increases overall safety and enables smarter resource allocation.
Cost Reduction Implementing vibration analysis brings significant financial benefits by:
- Cutting repair expenses through early intervention
- Extending equipment lifespan
- Reducing labor costs associated with emergency repairs
- Minimizing production interruptions that hurt revenue
Workplace Safety Enhancement Regular vibration monitoring creates safer working environments by preventing catastrophic equipment failures that could harm employees.
Energy Optimization Machines operating with developing faults typically consume excess energy. Vibration analysis helps identify and fix these issues, increasing efficiency and reducing operational costs.
By integrating vibration analysis into maintenance programs, companies can achieve more reliable equipment performance while reducing costs and improving safety outcomes.
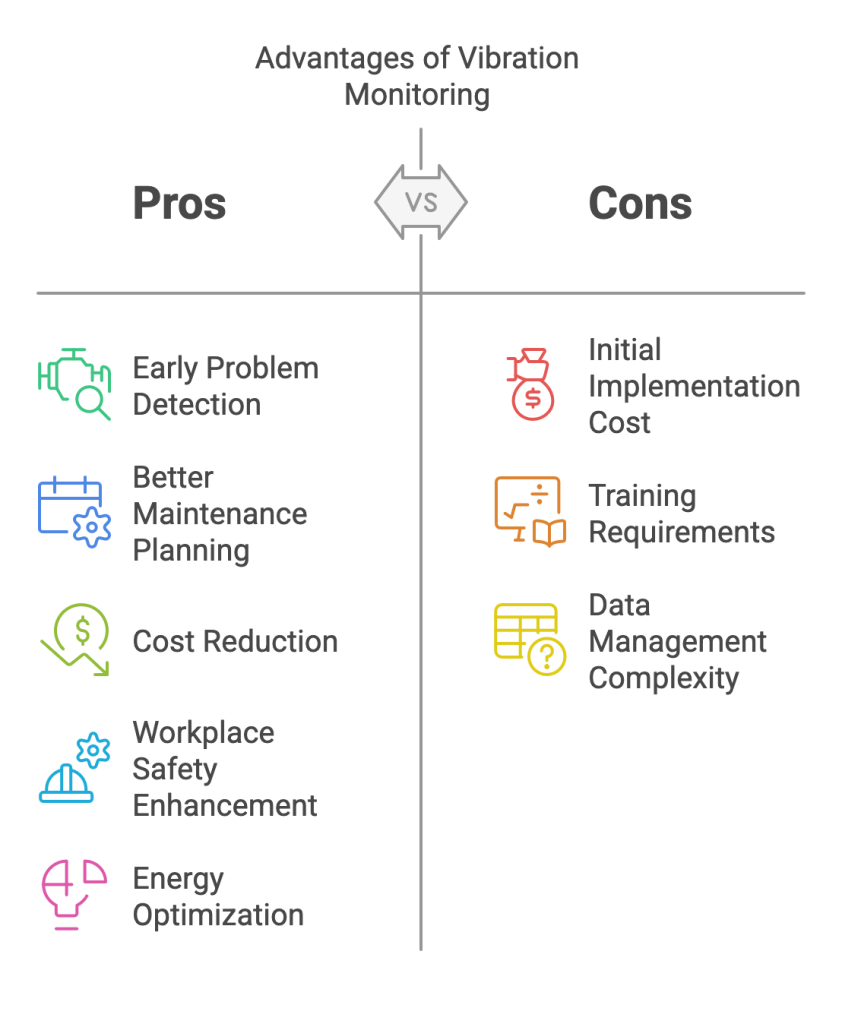
How Vibration Analysis Is Used in Industry
Vibration analysis techniques have become essential equipment monitoring and optimization tools across numerous industries. Manufacturing facilities rely on vibration analysis for monitoring motors, gearboxes, and conveyors, helping teams improve efficiency and reduce unexpected failures.
In automotive engineering, this technology helps designers test and refine:
- Engine components
- Transmission systems
- Suspension elements
These tests allow engineers to enhance performance reliability and create smoother passenger rides.
The aerospace sector depends on vibration analysis detects and identifies critical issues that could affect flight safety.
Engineers can use vibration analysis equipment to detect problems like:
- Excessive vibration
- Resonance issues
- Material fatigue points
This detection helps prevent potential failures before they occur in flight.
Wind energy companies utilize vibration monitoring to check turbine health, quickly identifying issues such as:
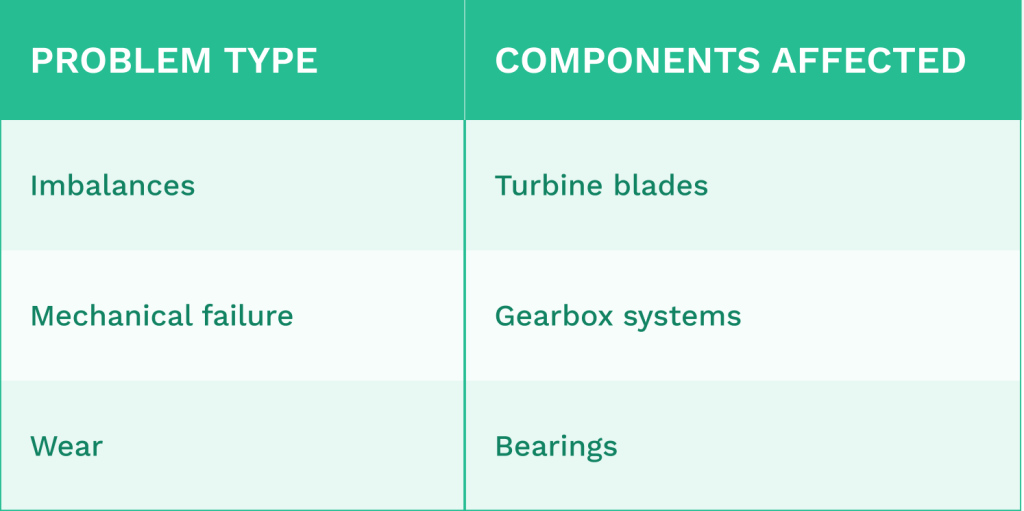
With regular vibration analysis, companies across these industries can significantly extend equipment life while improving safety and operational efficiency.
Vibration Analysis Equipment and Techniques
Vibration analysis forms the cornerstone of modern machine vibration analysis, condition monitoring, and predictive maintenance programs. This is usually part of a mathematical frequency analysis operation executed by organizations.
By examining how machines vibrate during operation, technicians can detect developing faults before they lead to catastrophic failures.
Viewing vibration amplitude and vibration parameters will help maintenance technicians conduct vibration analysis.
Here’s an overview of the most commonly used vibration analysis tools and technologies:
Vibration Data Collection Devices
Portable Vibration Analyzers
Portable vibration analyzers serve as the workhorses of many maintenance programs. These handheld devices combine sensors, data acquisition capabilities, and analytical software in one package.
Technicians use them to collect vibration readings at predetermined measurement points along a route. Modern analyzers often feature touchscreens, wireless connectivity, and the ability to perform preliminary analysis in the field.
The typical workflow involves connecting an accelerometer to the machine at specific measurement points, capturing the vibration signature, and either analyzing it immediately or transferring the data to a central database for more detailed examination.
These devices have evolved from simple meters to sophisticated computers capable of performing FFT (Fast Fourier Transform) analysis, time waveform collection, and phase measurements all in one compact unit.
Online Monitoring Systems
While portable analyzers provide periodic snapshots of machine health, online monitoring systems watch equipment continuously. These permanently installed systems use fixed sensors mounted at critical points on machinery to provide real-time vibration data.
They excel at monitoring critical assets where failures could have severe consequences or machines that experience rapid deterioration once a fault develops.
Online systems typically connect to a central network and trigger alarms when vibration levels exceed predefined thresholds. More advanced systems incorporate adaptive algorithms that learn normal vibration patterns and can detect subtle changes that might indicate emerging problems.
Sensors and Transducers
Accelerometers
Accelerometers represent the most widely used vibration sensors across industries. These devices contain a small piezoelectric crystal that generates an electrical signal proportional to the acceleration it experiences. This signal is then processed to extract vibration characteristics.
Different types of accelerometers serve specific purposes:
- General-purpose accelerometers work well for most industrial applications
- High-temperature variants withstand harsh environments
- Triaxial accelerometers measure vibration simultaneously in three perpendicular directions
- Low-frequency accelerometers detect slow-moving vibrations typical in structural applications
The mounting method significantly affects measurement accuracy. Stud mounting provides the most reliable readings compared to magnetic mounts or handheld probes.
Velocity Sensors
While accelerometers measure the rate of change in velocity, velocity sensors (or velocity transducers) directly measure the speed at which a surface moves during vibration. These sensors excel at detecting vibration in the mid-frequency range (10 Hz to 1,000 Hz) where many standard machinery faults manifest.
Velocity measurements often provide a more intuitive understanding of vibration severity for rotating equipment than acceleration readings, which is why many standards for acceptable vibration levels are expressed in terms of velocity.
Proximity Probes
Proximity probes measure displacement rather than acceleration or velocity. They’re particularly valuable for monitoring journal bearings in large rotating machinery, such as turbines and compressors.
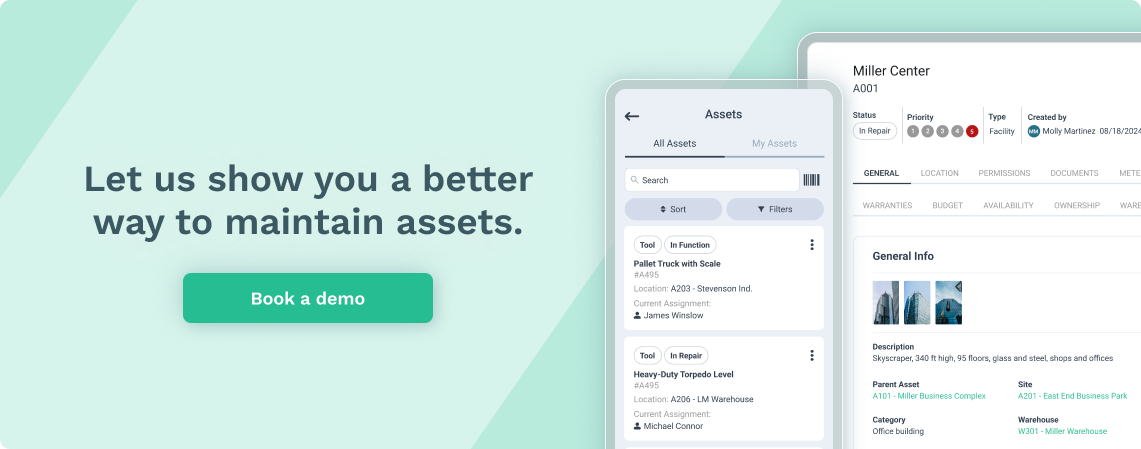
These non-contact sensors detect the actual movement of a shaft relative to its bearing, providing crucial information about clearances and dynamic behavior that other sensors cannot capture.
Analysis Software and Techniques
Spectrum Analysis Software
The heart of vibration analysis lies in transforming complex time-domain signals into frequency spectra using Fast Fourier Transform (FFT) algorithms. Spectrum analysis software presents this data in ways that help technicians identify specific fault patterns.
Modern software packages include features like:
- Automatic fault recognition that compares vibration signatures against known fault patterns
- Trending capabilities to track changes in vibration characteristics over time
- Waterfall plots that show how frequencies evolve during startup or shutdown
- Integration with computerized maintenance management systems (CMMS) to streamline workflow
Specialized Analysis Tools
Beyond basic spectrum analysis, several specialized tools help analysts extract even more information from vibration data:
Envelope Analysis (Demodulation) filters and processes signals to highlight impacts or modulations hidden in the raw data. This technique is particularly effective for detecting early-stage bearing and gear faults.
Order Tracking compensates for variations in machine speed during measurement, allowing for proper analysis of equipment that operates at variable speeds.
Operational Deflection Shape Analysis combines vibration measurements from multiple points to create an animated model showing how a machine or structure flexes during operation. This helps visualize resonance issues and identify structural weaknesses.
Modal Analysis determines a structure’s natural frequencies and mode shapes, essential for resolving resonance problems and amplifying vibration.
Integration and Implementation
Condition Monitoring Platforms
Enterprise-level condition monitoring platforms integrate vibration data with parameters like temperature, pressure, oil analysis, and process variables. This holistic approach provides a more complete picture of machine health than vibration alone could offer.
These platforms typically feature:
- Dashboards that present key performance indicators for equipment health
- Automated reporting that highlights developing issues
- Diagnostic tools that guide technicians through troubleshooting processes
- Predictive algorithms that forecast potential failure timeframes
Training and Certification
The most sophisticated vibration tools deliver limited value without properly trained analysts to interpret the results. The Vibration Institute and other organizations offer certification programs that establish standard competency levels for vibration analysts, from entry-level monitoring (Category I) to advanced analysis and program management (Category IV).
Emerging Technologies
The field continues to evolve with innovations like:
Wireless Sensors eliminate cabling challenges and make monitoring more accessible for difficult-to-reach equipment.
Machine Learning Algorithms improve fault detection by recognizing subtle patterns that might escape traditional analysis methods.
Augmented Reality Interfaces overlay vibration data onto physical equipment, helping technicians visualize problems in context.
Integration with Digital Twins allows comparison of actual vibration behavior against detailed simulation models for more accurate diagnostics.
The effectiveness of any vibration analysis program depends not just on having the right tools but on implementing a systematic approach to data collection, analysis, and follow-through.
When properly deployed, these technologies dramatically reduce unexpected failures, optimize maintenance planning, and extend equipment life.
Get a Free WorkTrek Demo
Let's show you how WorkTrek can help you optimize your maintenance operation.
Try for free