What is continuous improvement?
In maintenance organizations, continuous improvement is an ongoing effort to enhance processes, performance, and efficiency in asset management and maintenance operations. It involves systematically identifying areas where improvements can be made, implementing changes, and monitoring outcomes to ensure long-term benefits. The goal is to optimize operations, reduce downtime, lower costs, and improve asset reliability by fostering a culture of consistent progress.
Continuous improvement is typically guided by structured methodologies such as Lean, Six Sigma, or Total Productive Maintenance (TPM), which focus on eliminating waste, minimizing inefficiencies, and maximizing value. Maintenance teams apply continuous improvement principles by analyzing asset performance metrics, failure rates, and maintenance processes to identify recurring issues or bottlenecks. These insights lead to proactive changes—such as refining preventive maintenance schedules, enhancing technician training, or upgrading equipment.
Key tools for continuous improvement include Root Cause Analysis (RCA) and Key Performance Indicators (KPIs), which help teams understand failures and measure success. Maintenance organizations often adopt a Plan-Do-Check-Act (PDCA) cycle, where improvements are planned, implemented, evaluated, and adjusted based on feedback.
This iterative process ensures that even small, incremental changes lead to significant long-term improvements. Continuous improvement also encourages using predictive maintenance technologies, such as sensors and analytics, to identify problems before they lead to equipment failure. By constantly refining maintenance strategies, organizations can extend the useful life of assets, reduce unexpected breakdowns, and improve operational efficiency.

Tips for implementing continuous improvement
Maintenance organizations can effectively use continuous improvement processes to enhance operations, increase efficiency, and reduce costs. Continuous improvement is a systematic approach to identifying, analyzing, and implementing incremental changes that lead to better performance over time. Here are some ways maintenance organizations can best use continuous improvement processes:
- Establish clear goals and metrics: Maintenance organizations must establish clear, measurable goals aligning with their business objectives to implement continuous improvement. These goals should be specific, achievable, and tied to key performance indicators (KPIs) such as equipment uptime, mean time between failures (MTBF), and maintenance costs.
- Engage frontline employees: Continuous improvement relies heavily on the insights and expertise of those closest to the work. Maintenance organizations should actively engage technicians, operators, and other staff in identifying improvement opportunities and developing solutions. This can be done through regular team meetings, suggestion programs, and problem-solving workshops.
- Use structured problem-solving methods: To drive continuous improvement, maintenance organizations should use structured problem-solving methods such as Root Cause Analysis (RCA), Failure Mode and Effects Analysis (FMEA), and Plan-Do-Check-Act (PDCA). These methods provide a systematic approach to identifying the underlying causes of problems and developing effective solutions.
- Implement visual management: Visual management techniques, such as performance boards, color-coded systems, and floor markings, can help make performance visible and drive continuous improvement. Maintenance organizations can foster a culture of transparency, accountability, and collaboration by making key metrics and improvement activities visible to everyone.
- Standardize best practices: As maintenance organizations identify and implement improvements, it’s important to standardize those changes into best practices that can be consistently applied across the organization. This can be done by developing standard operating procedures (SOPs), checklists, and training programs.
- Leverage technology: Technology can be a powerful enabler of continuous improvement in maintenance. Predictive maintenance technologies, such as vibration analysis and thermal imaging, can help identify potential issues before they lead to failures. Computerized maintenance management systems (CMMS) can help track and analyze maintenance data, identify trends, and support data-driven decision-making.
- Foster a culture of learning: Continuous improvement requires a culture that values learning, experimentation, and calculated risk-taking. Maintenance organizations should encourage employees to try new ideas, learn from failures, and share knowledge. This can be supported through training programs, knowledge-sharing platforms, and recognition systems that reward improvement efforts.
- Collaborate with other functions: Maintenance doesn’t operate in a vacuum—it interacts with many other functions, such as operations, engineering, and procurement. To drive continuous improvement, maintenance organizations should collaborate closely with these functions to identify improvement opportunities, share best practices, and align goals and priorities.
Tools and Methodologies for Continous Improvement
In maintenance organizations, Lean principles help identify and eliminate common forms of waste. Technicians often waste time searching for parts, waiting for equipment to become available, or traveling between job sites.
Through value stream mapping, maintenance teams can visualize their workflow from work order creation to job completion, revealing these inefficiencies.
5S System
Consider a scenario where technicians spend excessive time locating tools. Implementing a 5S system (Sort, Set in order, Shine, Standardize, Sustain) can transform tool organization and significantly reduce search time.
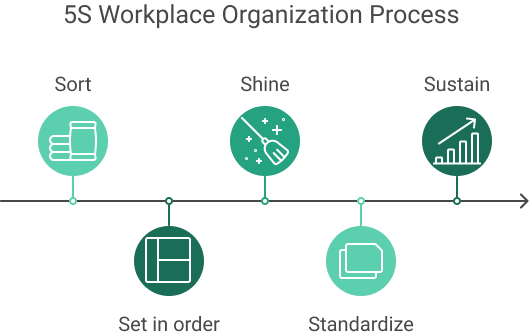
DMAIC Methodology
The DMAIC methodology from Six Sigma proves particularly valuable for improving maintenance reliability. By defining key metrics like Mean Time Between Failures (MTBF) or Mean Time To Repair (MTTR), teams can measure current performance, analyze equipment failure patterns, implement maintenance procedure improvements, and control results through standardized work practices.
For example, a facility experiencing frequent conveyor belt failures might use DMAIC to analyze failure patterns, implement preventive maintenance schedules, and track improvements in uptime.
Kaizen
Kaizen events work exceptionally well for maintenance teams because they bring operators, technicians, and engineers together to solve specific problems.
For example, a Kaizen event might focus on reducing preventive maintenance completion time by examining current procedures, identifying bottlenecks, and developing more efficient methods. These collaborative sessions often reveal insights that wouldn’t emerge from individual problem-solving efforts.
PDCA Cycle
The PDCA cycle provides a structured approach to implementing new maintenance strategies. When introducing predictive maintenance techniques, teams can plan a pilot program on critical equipment, implement it, check the results through reliability metrics, and act on those findings to refine the approach before expanding to other equipment.
Visual Boards/Kanban
Visual management transforms maintenance operations by making work visible and trackable. Maintenance teams can use visual boards to display work order status, equipment health indicators, and upcoming preventive maintenance tasks. This visibility helps supervisors allocate resources more effectively and ensures critical maintenance isn’t overlooked.
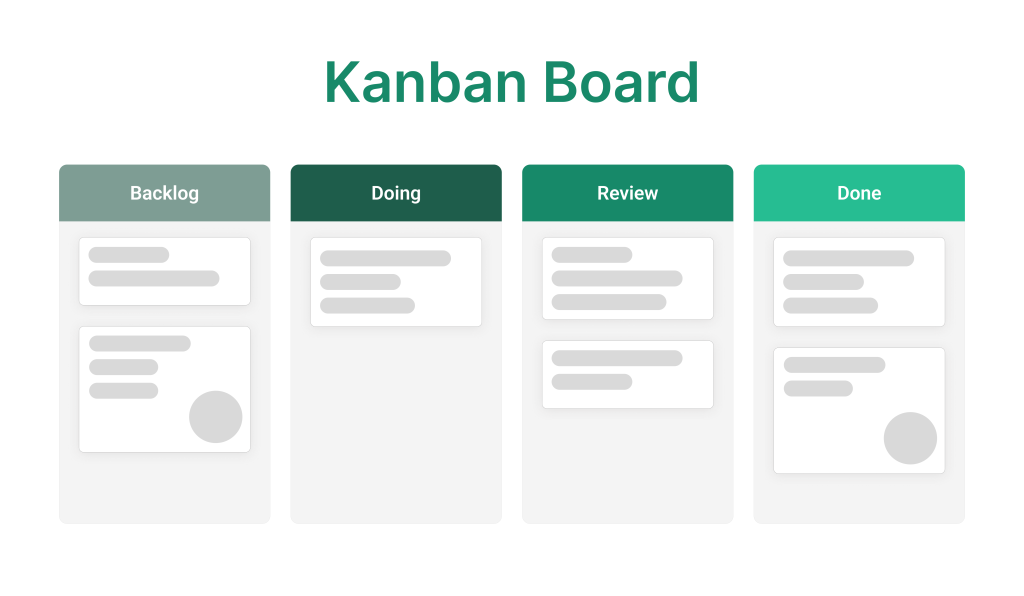
Root Cause Analysis
Root cause analysis becomes particularly powerful in maintenance contexts. When equipment fails, the 5 Whys technique helps teams dig beyond surface-level causes. Rather than simply replacing a failed bearing, teams might discover that improper lubrication procedures led to the failure, allowing them to address the underlying cause and prevent recurrence.
TPM
Total Productive Maintenance (TPM), an offshoot of TQM, specifically addresses maintenance excellence. It promotes autonomous maintenance where operators take responsibility for basic equipment care, freeing up maintenance technicians for more complex tasks. This approach also improves equipment reliability by catching issues early through regular operator inspections.
To implement these improvements effectively, maintenance organizations should start by:
- Establishing clear baseline metrics for maintenance performance
- Training staff in continuous improvement methodologies
- Creating systems for tracking and analyzing maintenance data
- Developing standard work procedures for everyday maintenance tasks
- Implementing regular review processes to assess improvement initiatives
Benefits for Maintenance Organizations
Strategic Benefits
Continuous improvement enables maintenance managers to shift from reactive firefighting to strategic planning. By systematically analyzing failure patterns and maintenance data, managers can make informed decisions about resource allocation, equipment upgrades, and preventive maintenance schedules. This strategic approach leads to better budget utilization and improved long-term reliability of assets.
Operational Efficiency
The implementation of continuous improvement methodologies streamlines daily maintenance operations in several ways. Work order completion times decrease as standardized procedures eliminate unnecessary steps and reduce variation in task performance.
The organization of tools, parts, and documentation improves, reducing the time technicians spend searching for resources. Additionally, visual management systems help managers better coordinate maintenance activities and respond quickly to emerging issues.
Cost Reduction and Resource Optimization
Through systematic analysis of maintenance practices, organizations can identify and eliminate hidden costs. Improved inventory management, for instance, reduces carrying costs and emergency parts purchases.
Better scheduling of preventive maintenance tasks optimizes labor utilization, reducing overtime expenses. The focus on root cause analysis prevents recurring failures, reducing repair costs and production losses due to equipment downtime.
Enhanced Safety and Compliance
Continuous improvement processes naturally lead to safer work environments. Organizations reduce the risk of accidents and injuries by standardizing maintenance procedures and regularly reviewing safety protocols. Documentation improvements ensure better compliance with regulatory requirements, while systematic analysis of near-misses and safety incidents helps prevent future occurrences.
Employee Development and Engagement
When maintenance organizations embrace continuous improvement, they create opportunities for professional growth among their staff. Technicians develop problem-solving skills through participation in improvement initiatives.
The emphasis on data collection and analysis helps maintenance personnel think more analytically about their work. Team-based improvement activities foster better collaboration between maintenance staff, operators, and engineering personnel.
Performance Measurement and Accountability
Continuous improvement frameworks give maintenance managers better tools for measuring and managing performance. Key Performance Indicators (KPIs) become more meaningful as data quality improves. Managers can better track metrics like Mean Time Between Failures, maintenance backlog, and preventive maintenance compliance. This enhanced visibility allows for more effective performance management and helps justify resource requests to senior management.
Cultural Transformation
Perhaps most significantly, continuous improvement creates a culture of excellence within maintenance organizations. Staff at all levels become more proactive in identifying and solving problems. The emphasis on root cause analysis leads to a deeper understanding of equipment and processes. Knowledge sharing improves as teams document their findings and solutions—this cultural shift results in more engaged employees and better maintenance outcomes.
Future Readiness
Establishing robust continuous improvement processes equips maintenance organizations to adopt new technologies and methodologies. The analytical skills and systematic approach developed through continuous improvement initiatives help organizations evaluate and implement predictive maintenance technologies, condition monitoring systems, and other advanced maintenance practices.
Get a Free WorkTrek Demo
Let's show you how WorkTrek can help you optimize your maintenance operation.
Try for free