Get a Free WorkTrek Demo
Let's show you how WorkTrek can help you optimize your maintenance operation.
Try for freeIntroduction
CMMS in Supply Chain Management refers to software that helps manage and optimize maintenance processes for the equipment and assets involved in the supply chain. It includes features such as asset tracking, preventive maintenance scheduling, work order management, and cost tracking. The goal is to ensure the reliability and efficiency of equipment, minimizing downtime and disruptions in the supply chain.
What is a CMMS?
The acronym CMMS stands for Computerized Maintenance Management System. This software package was designed to manage maintenance practices globally, on a strategic, financial, and operational level. It is today the essential software of the industrial sector. Much more than simple computer programming, it is an assistant for maintenance teams, the cornerstone of industrial efficiency.
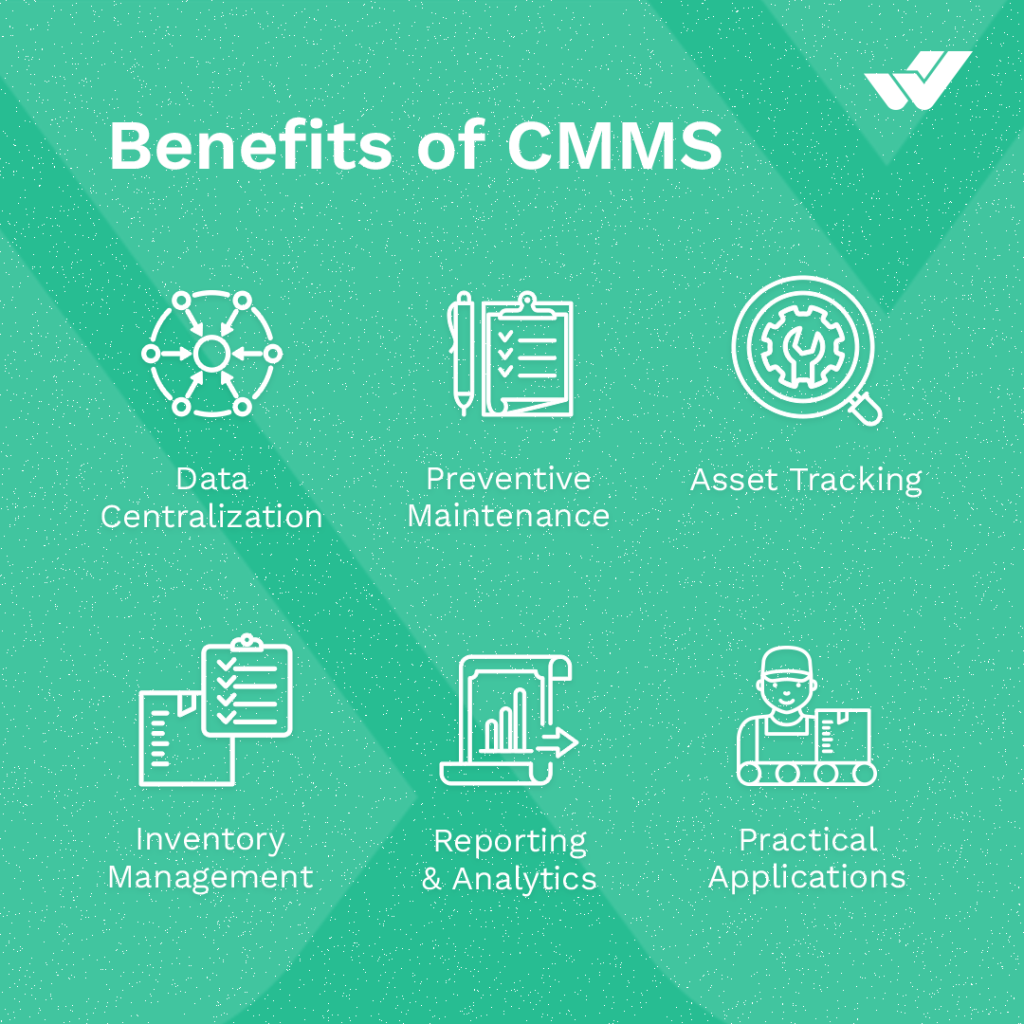
What is Supply Chain Management?
Supply Chain Management refers to the end-to-end process of planning, implementing, and controlling the flow of goods, services, and information from the point of origin to the final consumer. It involves the coordination and integration of various activities within an organization and across multiple entities in the supply chain, including suppliers, manufacturers, distributors, retailers, and customers.
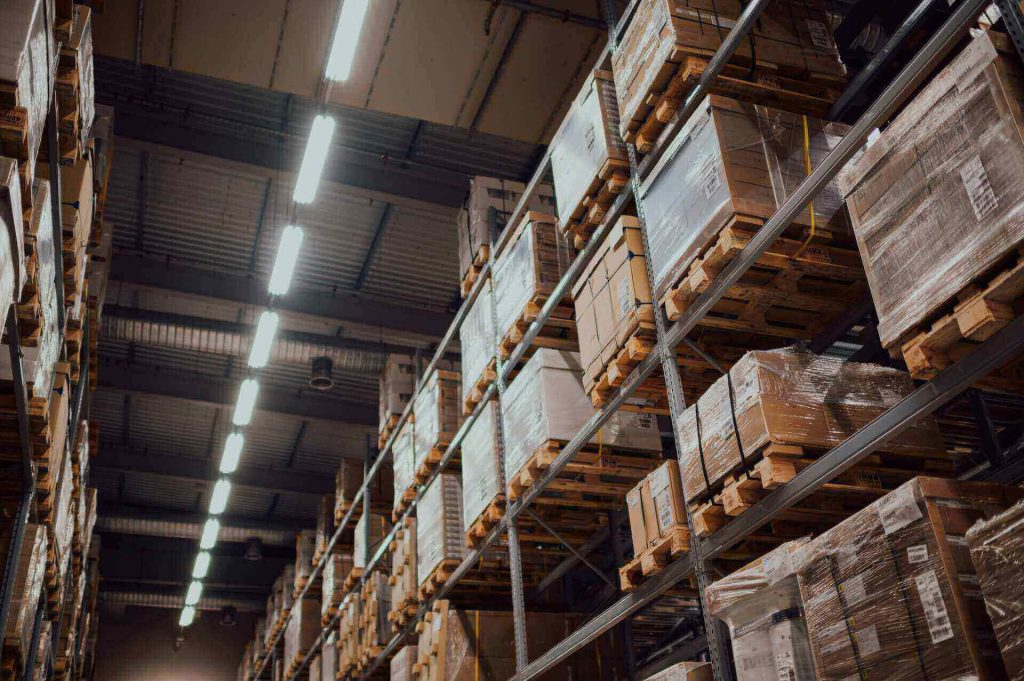
Key objectives of effective Supply Chain Management include:
- Efficiency: Minimizing waste, reducing costs, and optimizing processes to improve overall efficiency.
- Customer Satisfaction: Ensuring products are available when and where customers need them.
- Flexibility: Adapting quickly to changes in demand, market conditions, or disruptions.
- Innovation: Incorporating new technologies and best practices to enhance supply chain processes.
- Risk Management: Identifying and mitigating risks, such as supply chain disruptions, geopolitical issues, or natural disasters.
Supply Chain Management is critical for businesses to remain competitive in a global market. Effective SCM can lead to cost savings, improved customer satisfaction, and increased overall performance.
Challenges in Supply Chain Management
Here are some common challenges in supply chain management:
Supplier Relationship Management: Building and maintaining strong relationships with suppliers is crucial, but challenges such as communication barriers, quality control issues, and supply chain disruptions can strain these relationships.
Inventory Management: Balancing inventory levels to meet demand without overstocking or understocking is a constant challenge, especially when facing fluctuating demand and supply uncertainties.
Transportation Costs and Logistics: Fluctuations in fuel prices, regulatory changes, and transportation network disruptions can impact costs and logistics efficiency.
Addressing these challenges requires a holistic and proactive approach. Implementing advanced technologies, improving communication and collaboration, building strong relationships with suppliers, and regularly reviewing and updating strategies are key elements in overcoming the challenges in supply chain management.
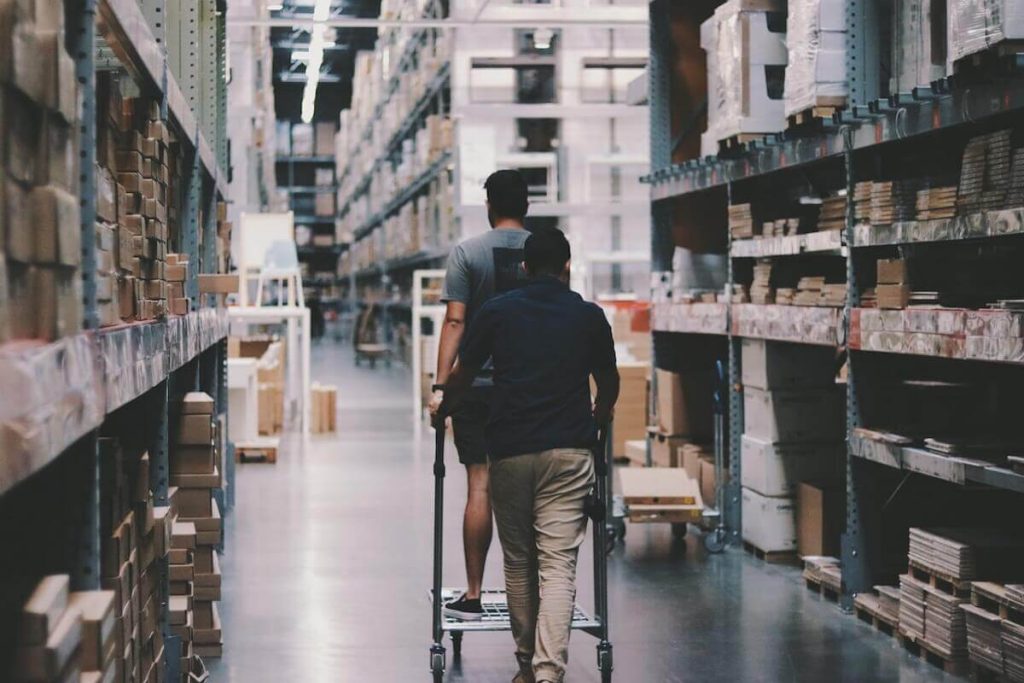
What is a Supply Chain Disruption?
A supply chain disruption is a major failure in supply chain production or distribution that negatively affects the entire process. Supply chain disruptions can lead to lower productivity, higher costs, higher customer satisfaction, and more.
Types of Supply Chain Disruptions
Many things can cause supply chain disruptions. The best way to solve these problems is to figure out what’s causing the outage and how to minimize or prevent it.
Here are some reasons why your supply chain may be affected.
Natural Disaster – Whether it’s a hurricane, earthquake, tsunami, or snowstorm, any type of natural disaster or disaster can impact or disrupt global supply chains.
Epidemic – We are still feeling the effects of the COVID-19 pandemic and the significant impact on global supply chains. This has a significant impact on supply chains due to the number of people, geographies, and global companies affected by the outbreak and other public health crises.
Product Problem – Any problems at any stage of supply chain management can cause delays in the production of the final product. These delays may impact quality and cause shipping delays.
Traffic Delays – The growing risks of driver shortages, cyberattacks, deteriorating infrastructure, and the recent COVID-19 pandemic, which has seen many countries and regions implement lockdowns to prevent the spread of the virus, have made it difficult for carriers to move goods by air, sea, or land.
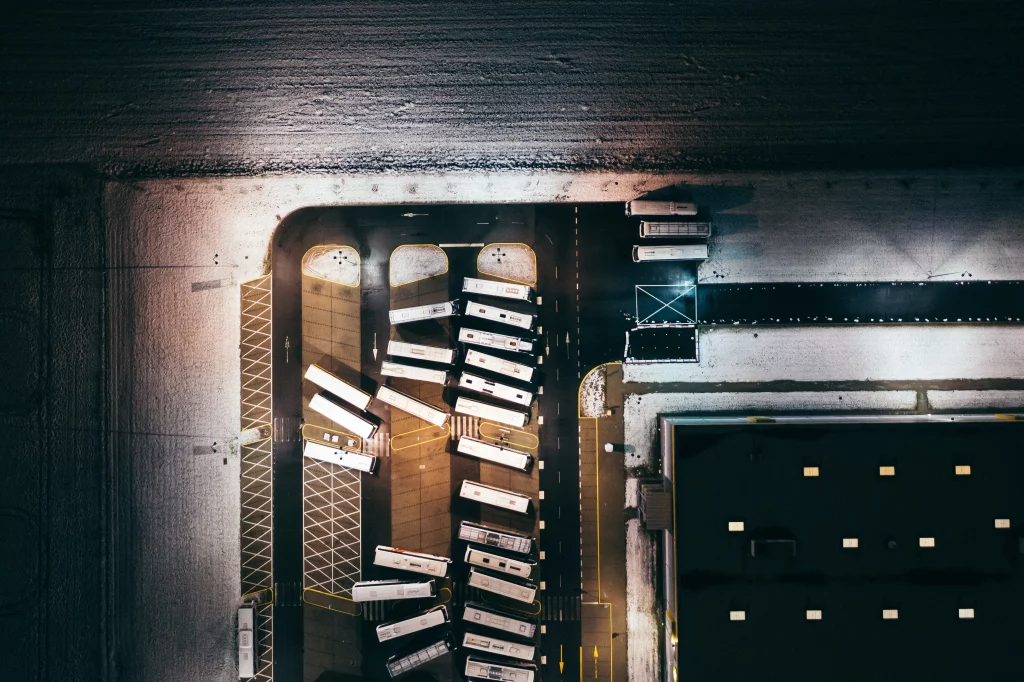
Measures to Reduce Supply Chain Disruptions
Unfortunately, things happen spontaneously and you may have little or no advance notice of supply chain disruptions. So it’s a good idea to be as prepared as possible.
By switching from spreadsheets, paper, and pencils to CMMS software, companies can more easily manage or avoid disruptions of this magnitude. Using this specialized software system along with established supply chain management technology, users can reduce errors and costs while optimizing the entire supply chain. Let’s look at some different types of supply chain management tasks and how using automated systems can help these processes run more smoothly.
Inventory management
Inventory management is critical to the supply chain. Whether you have too little or too much inventory, this can cost a lot of time and money. You must maintain a slightly higher level than all necessary inventories to create a buffer for future disruptions.
A CMMS gives you insight into your spare parts inventory. By tracking historical data in a CMMS, managers can create detailed reports to analyze and identify patterns for each inventory item. The ability to analyze patterns gives managers a deeper understanding of usage and allows them to set maximum and minimum inventory levels, reorder points, and criticality.
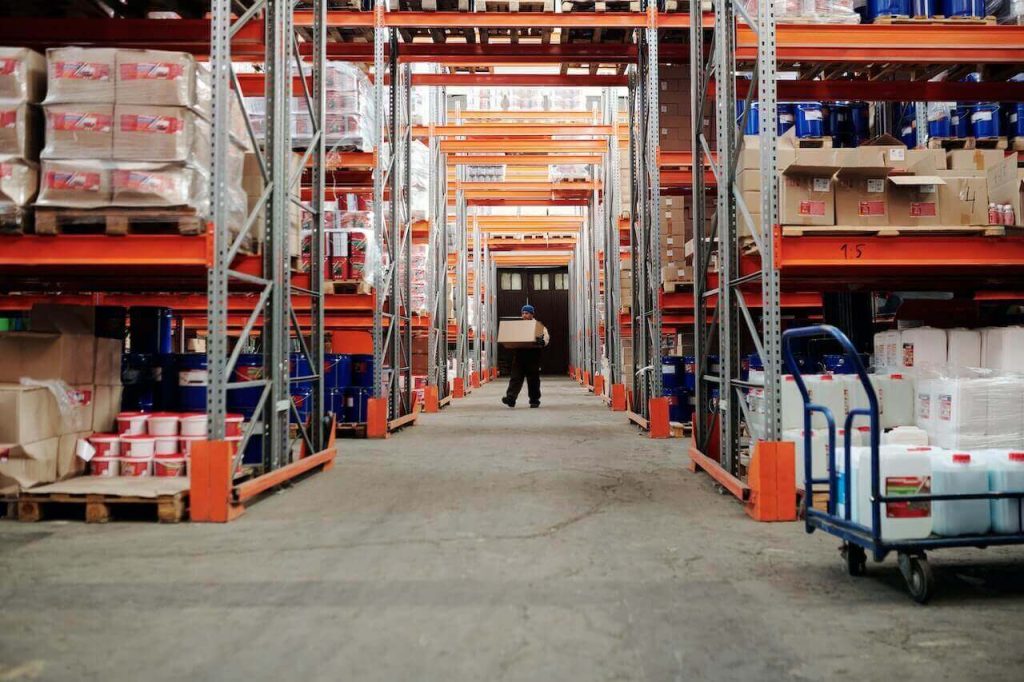
Develop a Supply Chain Contingency Plan
Since not everything goes according to plan, it is important to have contingency plans for the unexpected. Create scenarios and plan how to manage these disruptions. It may seem trivial to perform this process, but if you are prepared for any disruption that may arise, it will have less of an impact on your operations. Make sure you have an emergency budget in place to help you implement this plan.
CMMS software allows you to create, plan, execute, record, and manage all your resources. Mistakes and inefficiencies cannot be tolerated in any company. Rather than wasting valuable time managing everything with spreadsheets, paper, and pencils, minimize risk by using powerful tools like a CMMS.
The Impact of CMMS on Supply Chain Management
The implementation of a CMMS for Supply Chain Management can have several significant impacts:
Reduced Downtime – CMMS helps in scheduling preventive maintenance, reducing the likelihood of unexpected equipment failures. This, in turn, minimizes downtime and ensures a smoother flow in the supply chain.
Optimized Maintenance Processes – CMMS streamlines maintenance workflows, making it easier to create, assign, and track work orders. This optimization leads to quicker response times and more efficient maintenance activities.
Enhanced Asset Management – CMMS provides a centralized platform for tracking and managing assets, allowing for better visibility into equipment status, maintenance history, and performance. This contributes to improved decision-making in the supply chain.
Cost Savings – By reducing downtime with CMMS, optimizing maintenance, and preventing unexpected breakdowns, CMMS can result in cost savings for organizations in terms of both repair expenses and the costs associated with disrupted supply chain activities.
Efficient Inventory Management – CMMS helps in managing spare parts and inventory needed for maintenance. This ensures that the necessary supplies are available, preventing delays and interruptions in the supply chain.
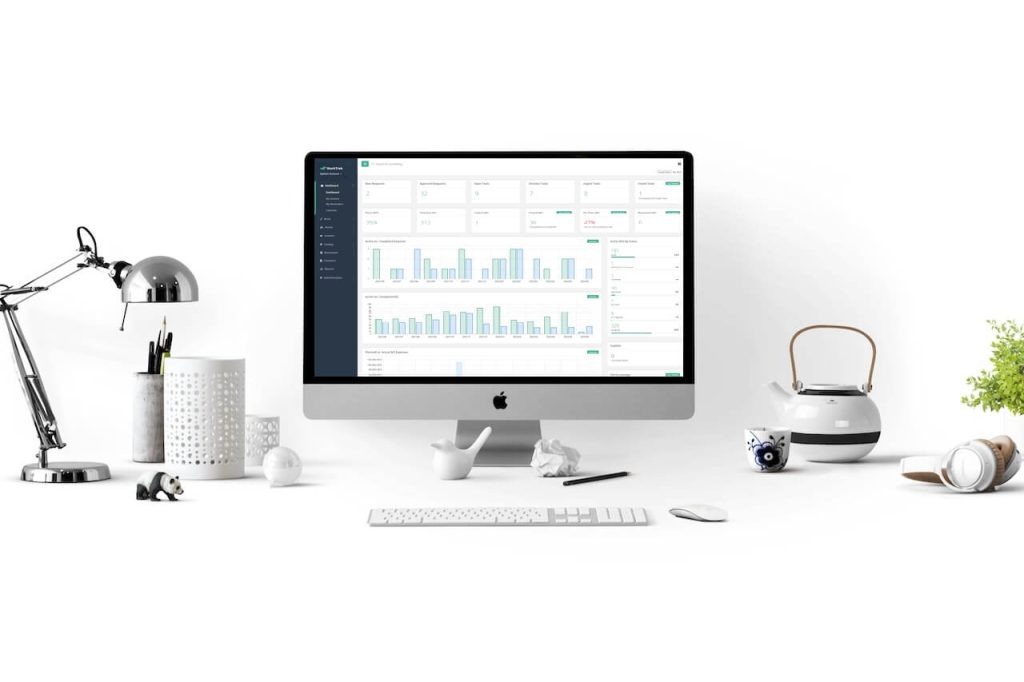
4 Ways a CMMS Helps Supply Chain Maintenance Managers Reduce Operating Costs
Plant maintenance has long been focused on being able to respond to machine failures and hopefully having the right parts in stock to minimize downtime. Over time, this situation has changed significantly; plant maintenance relies on maintenance technology to predict and prevent problems from occurring. Therefore, the life cycle of equipment, assets, and parts can be predicted.
This means supply chain managers and maintenance managers are always able to keep conveyors moving while ensuring their machines are performing at their best.
Competitive supply chain warehouse reduces corrective maintenance
The practice of forcing equipment to be brought into service to the point of needing repairs and having staff conduct regular walk-throughs to conduct manual assessments based on noise and vibration is becoming a thing of the past.
In the current competitive environment, supply chain managers must anticipate possible maintenance issues and then resolve them to prevent downtime that ultimately impacts sales and results in unfulfilled quotas.
Reduce costs through maintenance technology
Informed plant managers stay competitive in the market by understanding how technology works in their facilities. Key advantages of integrated technology include:
- Improve throughput
- Reduce production downtime and increase equipment reliability
- Improve quality and safety conditions
- Extend asset life expectancy
- Supply chain management relies on cloud-based solutions
The ability to monitor factory assets through remote sensors enables remote access to data through cloud-based applications. Therefore, when it comes to facilities management, it makes no sense to be reactive or wait until something breaks before repairing it.
CMMS software is the leading maintenance technology
Using CMMS software is beneficial because it centralizes data from safety inspections, inventory control, predictive maintenance, and preventive maintenance to facilitate measures to reduce the total cost of ownership. Field technicians and engineers can quickly identify and analyze problems to gain insight into maintenance or production operations.
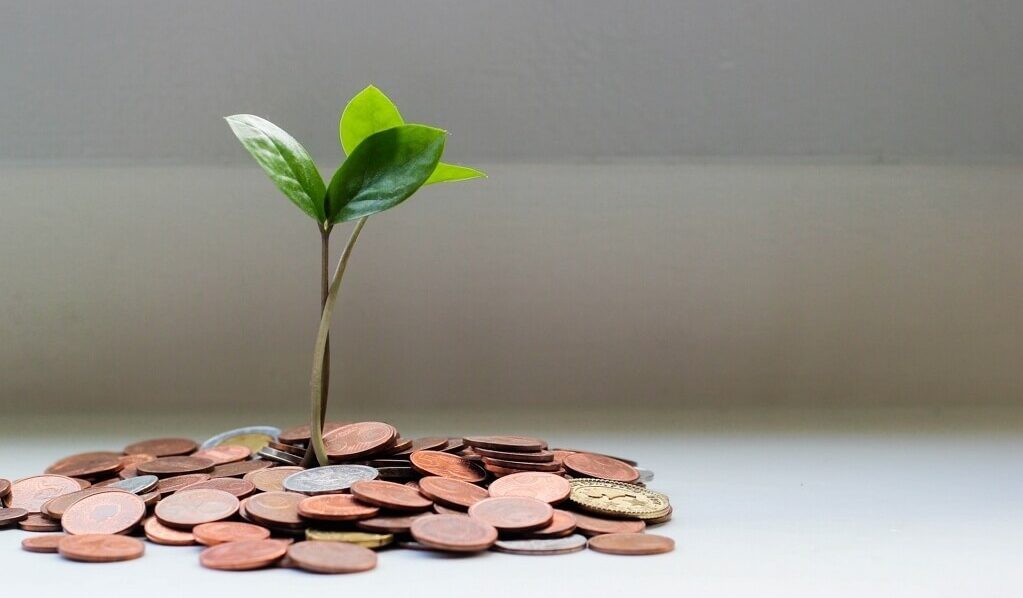
Conclusion
Having the right tools to manage your processes puts you in control and minimizes the risk of business disruption. By investing in CMMS for supply chain management, you can manage your supply chain more efficiently, reduce expenses, and reduce the risks associated with shipping and receiving. CMMS is designed to streamline workflows and save time and money.