Get a Free WorkTrek Demo
Let's show you how WorkTrek can help you optimize your maintenance operation.
Try for freeKeeping assets in good mechanical health is critical for the smooth operation of any facility, in any industry.
By investing in regular inspections, cleaning, and servicing of your assets, you can avoid unexpected breakdowns that lead to downtime and delays, ultimately harming your bottom line.
Yet, many facilities either fail to recognize the importance of proper maintenance or want to improve their approach but don’t know where to start.
We’re here to help.
In this article, we’re going to explain what asset maintenance is, why it’s so important, and share some actionable tips to help you optimize your maintenance strategy.
Let’s get into it!
Asset Maintenance vs Asset Repair
Oftentimes, the terms maintenance” and repair” are used synonymously.
After all, maintenance is all about fixing assets, right?
Well, not exactly.
Asset maintenance is a proactive process to keep your assets in optimal condition and prevent unplanned downtime.
There are several maintenance strategies to choose from:
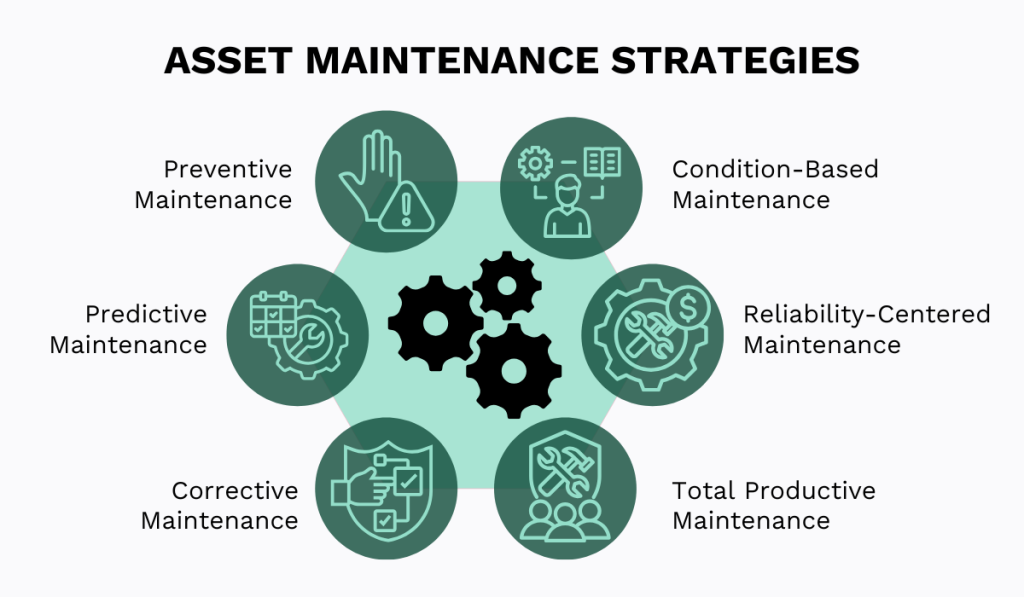
Maintenance activities typically include:
- scheduled inspections to identify potential problems,
- proactive measures such as cleaning, lubrication, calibration, and adjustments,
- running diagnostics to ensure the proper functioning of assets,
- replenishing consumables, and
- conducting safety checks.
In other words, it’s all about avoiding the need for repairs.
Asset repair, on the other hand, is reactive work.
It refers to fixing assets that have already been damaged or experienced failure.
Asset repair entails:
- identifying the cause of failure or malfunction,
- replacing the damaged or failed components,
- fixing faulty parts and
- running diagnostics to confirm the repair was successful.
Asset maintenance is meant to prevent issues, while repair is about correcting them.
And facilities are slowly recognizing that an ounce of prevention is worth a pound of cure.
According to Augury’s 2024 Plant Services Report, proactive maintenance is becoming more widely adopted.
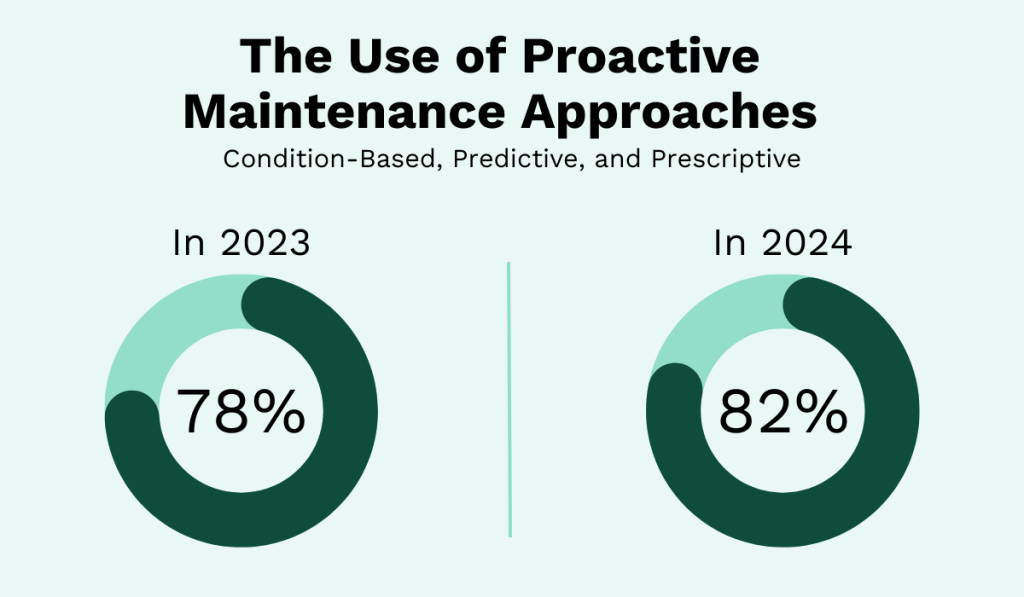
Facilities increasingly notice the value of preventing issues before they arise, so they’re doubling down on maintenance.
But what benefits are they reaping from this effort, exactly?
Keep reading to find out.
Why Is Asset Maintenance Important
In 2023, ABL reported that 43.44% of facilities planned to increase their maintenance budgets.
This number proves that even if consistent asset maintenance requires an investment, it’s still more affordable than fixing a disaster after it has already struck.
But that’s not the only benefit of this proactive approach.
Proper maintenance extends the useful life of your assets, ensures safety at your facility, and makes your operations more efficient.
Let’s explore each of these benefits in more detail.
Prolonging Asset Life
The unfortunate truth about your assets is that no matter how hard you try, you can’t completely stop them from becoming old and outdated.
As technology advances, the old versions of your trusty equipment are bound to become obsolete, and the machines you’ve been using for years will eventually need to be replaced.
However, replacing them might not always be viable, explains Amfab Steel’s Equipment Tech Manager Jeremiah Dotson.
In such scenarios, prioritizing consistent and thorough asset maintenance becomes crucial to extending equipment lifespan.
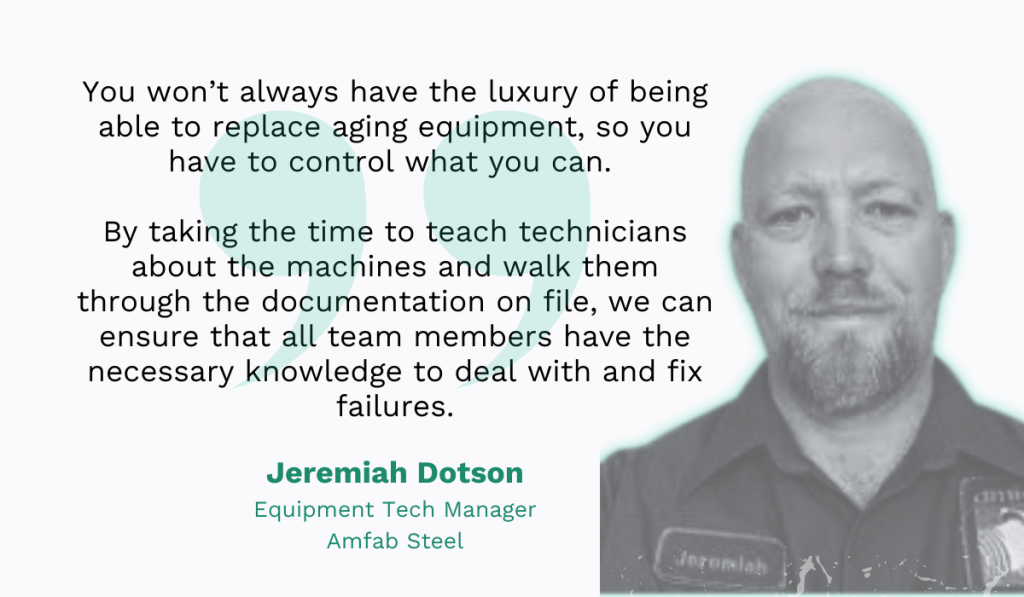
But even if you can afford to replace aging assets, you should not neglect their maintenance.
In fact, you should do the opposite.
That is certainly the mindset of maintenance professionals surveyed for Limble’s State of Maintenance in Manufacturing and Facilities report.
While 69% stated they were planning to combat aging infrastructure by investing in new equipment, 72% favored proactive maintenance as their strategy.
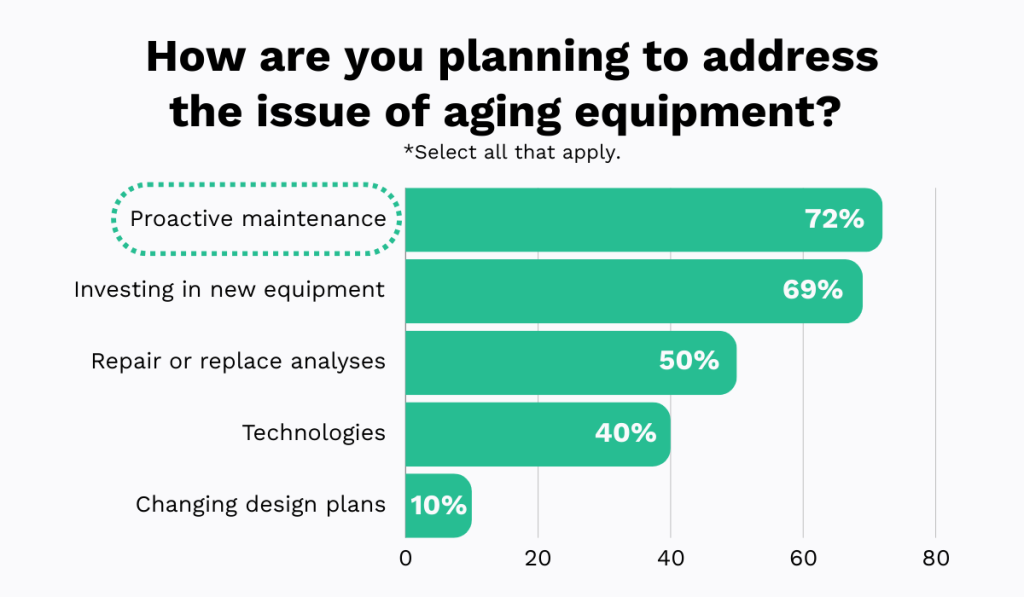
These maintenance professionals are determined to evolve their maintenance strategies and keep their assets operational for as long as possible.
Following in their footsteps can save you more than the money you would have otherwise spent on expensive new machinery.
It also prevents the costs that come with unplanned downtime as you achieve greater operational efficiency.
Improving Operational Efficiency
Good maintenance practices can make a huge difference to your day-to-day operations, in addition to prolonging your assets’ useful life in the long term.
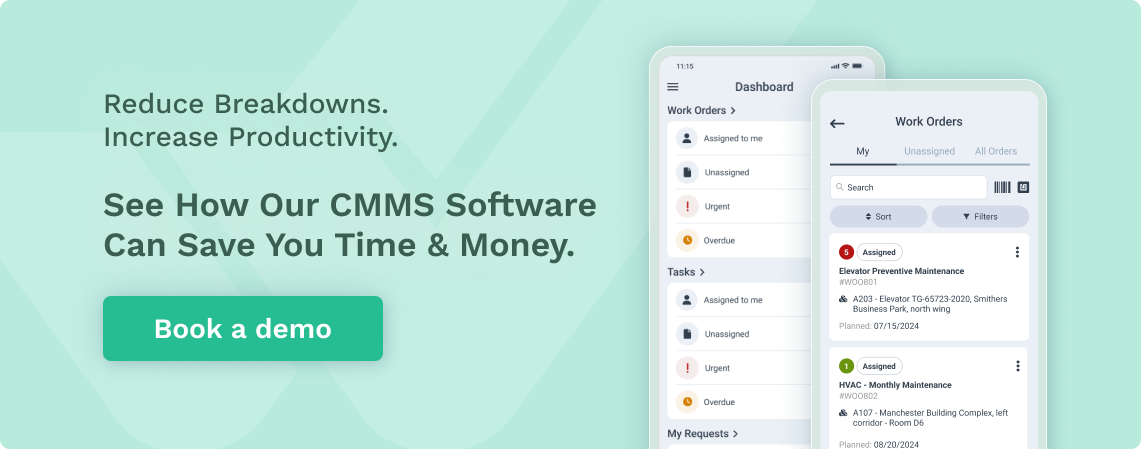
Namely, well-maintained assets perform at their peak, minimizing inefficiencies and ensuring smooth operations.
Sensemore, a company specializing in machinery performance and reliability optimization, agrees and advocates for predictive maintenance.

Let’s say you’re in charge of maintenance operations at a facility that heavily relies on a conveyor belt to move items down the production line.
If you don’t regularly inspect, clean, and lubricate this essential asset, it will wear out and ultimately break down.
This creates a domino effect: production slows, unfinished goods pile up, and workers are left unproductive as the entire production line is disrupted.
Conversely, with a good maintenance plan and schedule, you can be sure that any minor issues will be resolved before they escalate.
Planned shutdowns are a vital part of this.
Yet, the Augury report we mentioned earlier has uncovered that 3 in 10 plants never perform them.
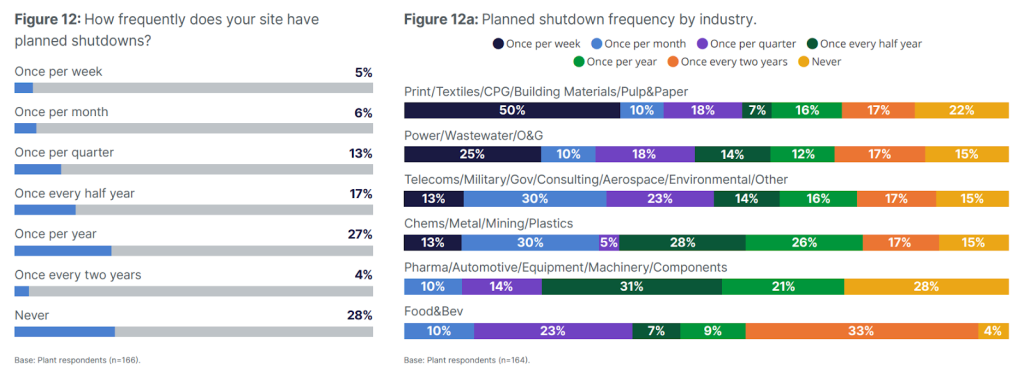
This presents a significant issue, increasing the likelihood of unexpected equipment failures that cascade into costly downtime and emergency repairs.
While planned shutdowns and maintenance may seem inconvenient in the short term, their benefits far outweigh the drawbacks.
Ensuring safety is one of those benefits.
Ensuring Safety at Your Facility
A solid maintenance strategy plays a huge role in keeping your personnel safe, as it helps identify potential hazards and ensures equipment works in line with regulations.
Given that workplace injuries are so common in industries like manufacturing, doing everything you can to prevent them is that much more important.
Just look at Eurostat’s statistics on accidents at work within the EU in 2022.
Manufacturing takes a high third place, accounting for 15.2% of fatal and 18% of non-fatal workplace accidents.
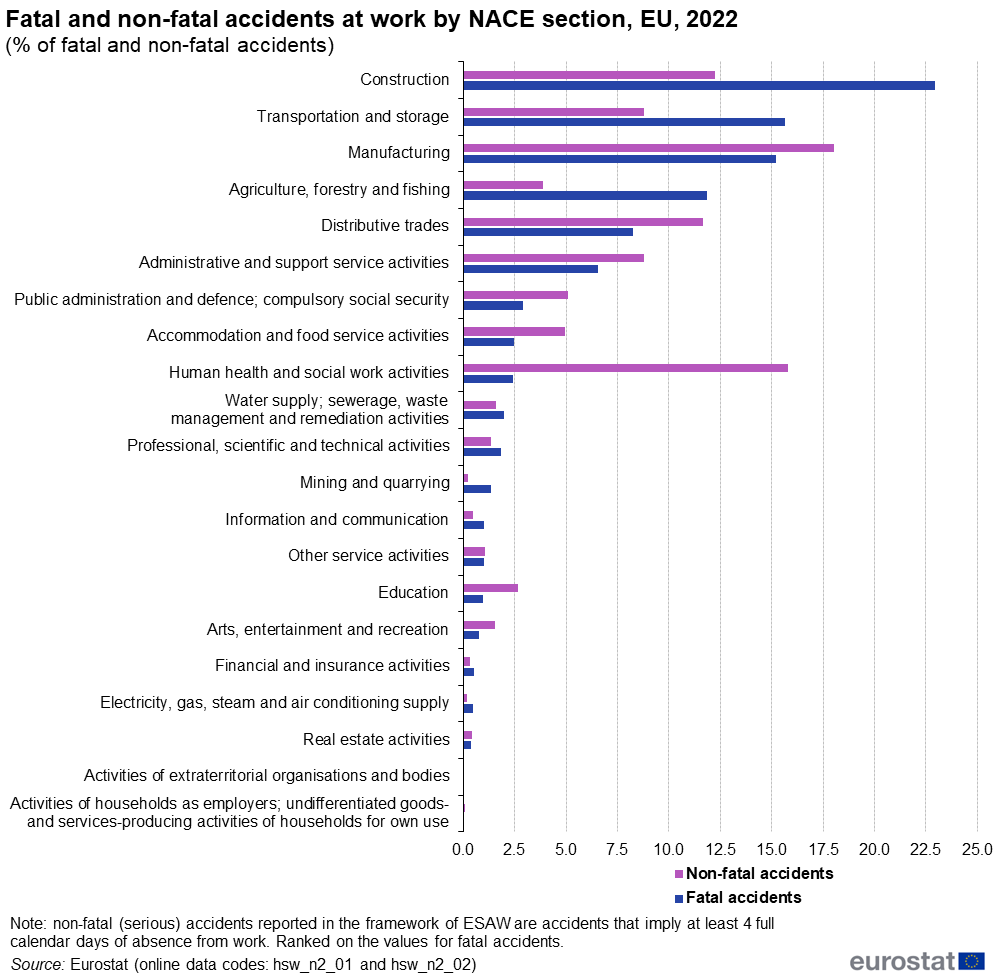
So, how do you ensure your facility doesn’t become part of these undesirable numbers?
Implementing a robust asset maintenance plan is vital, in addition to the obvious—training your personnel to operate equipment safely and identify potential dangers.
This involves making inspections, cleaning, and servicing the equipment at your facility according to a defined schedule a routine.
If you need more motivation, think about some well-known disasters in asset-intensive industries.
Poor maintenance or complete absence of it is what often causes such tragedies.
One such example is the 1988 Piper Alpha disaster, in which the oil platform exploded and collapsed, killing 167 people.
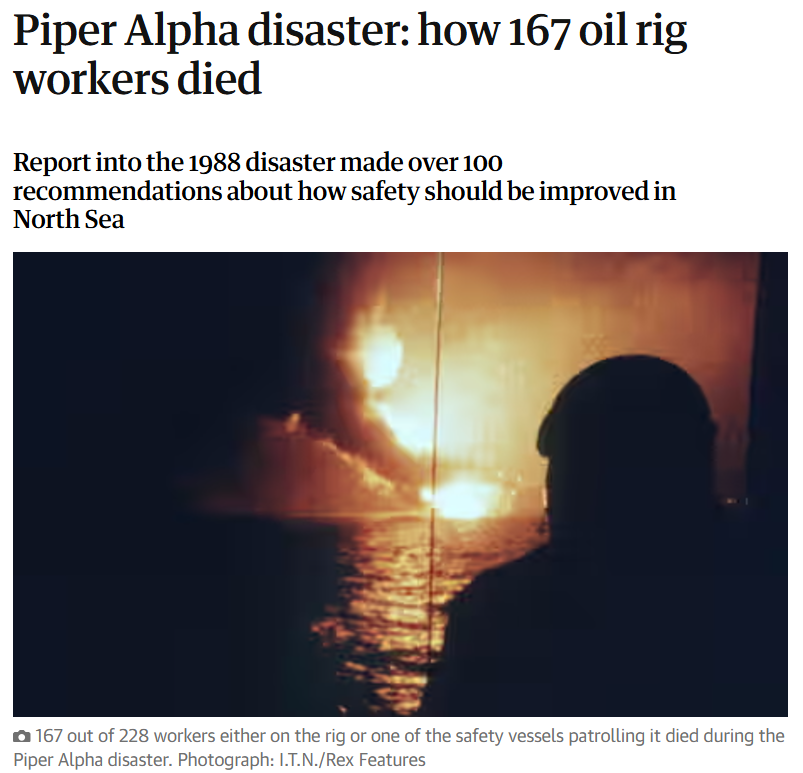
It took more than 3 weeks to extinguish the horrific fire, and due to a lack of physical evidence, it was difficult to establish the cause of the incident.
However, subsequent investigation concluded that the initial leak was caused by simultaneous maintenance on a pump and a safety valve.
It also faulted the rig’s operator, Occidental, for inadequate maintenance protocols and safety procedures, though no criminal charges were filed.
This tragedy teaches an important lesson:
Not only is it crucial to reduce the risk of workplace accidents by performing regular and thorough maintenance—it’s just as important to ensure proper protocols are followed.
Signs You Need a Better Asset Maintenance Plan
Now that you know why regular asset maintenance should be non-negotiable, it’s time to ask yourself:
Are the maintenance practices at my facility the best they can be?”
If you’re not sure how to answer this question, look at some signs indicating there’s room for improvement.
Frequent Unplanned Downtime
Unexpected downtime is a clear indicator that there isn’t enough regular monitoring and preventive maintenance in place.
You can calculate your downtime using one of our free maintenance calculators.
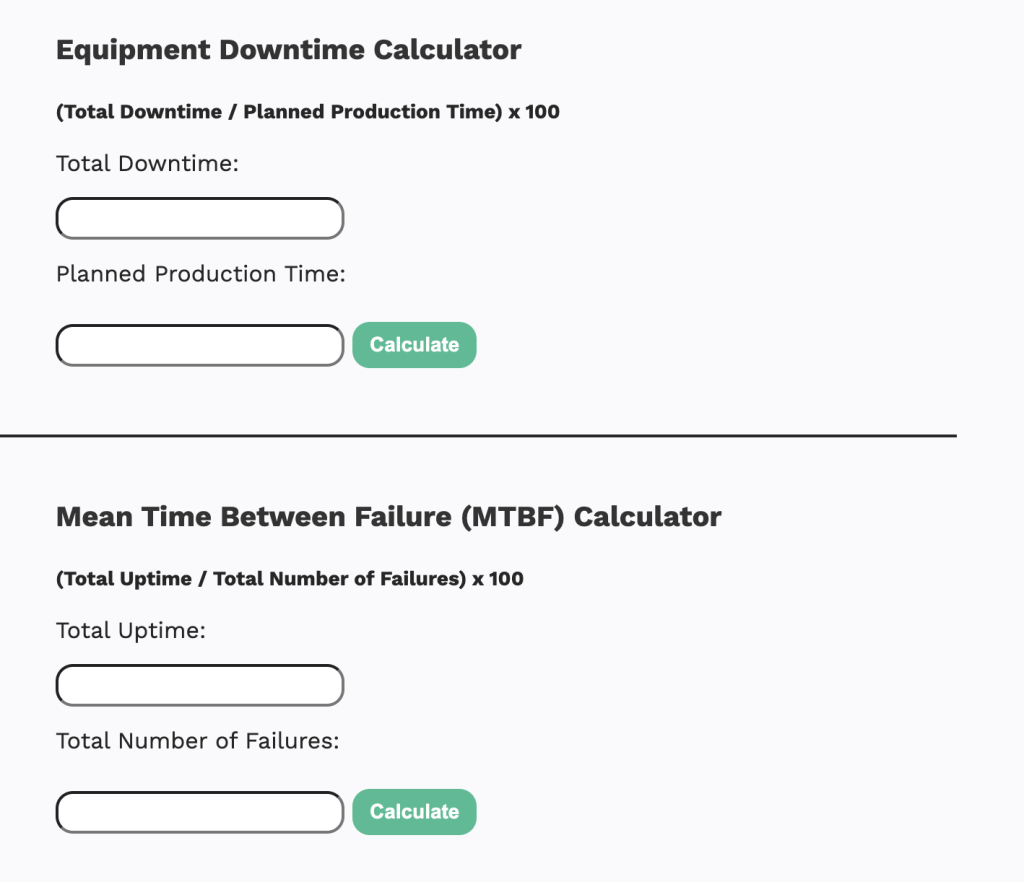
Unfortunately, this is a common issue among various facilities.
Almost 30% of plant facilities say unplanned downtime is their biggest operational challenge.
Since one-third of them rely on run-to-failure as their approach to maintenance, this figure is not surprising.
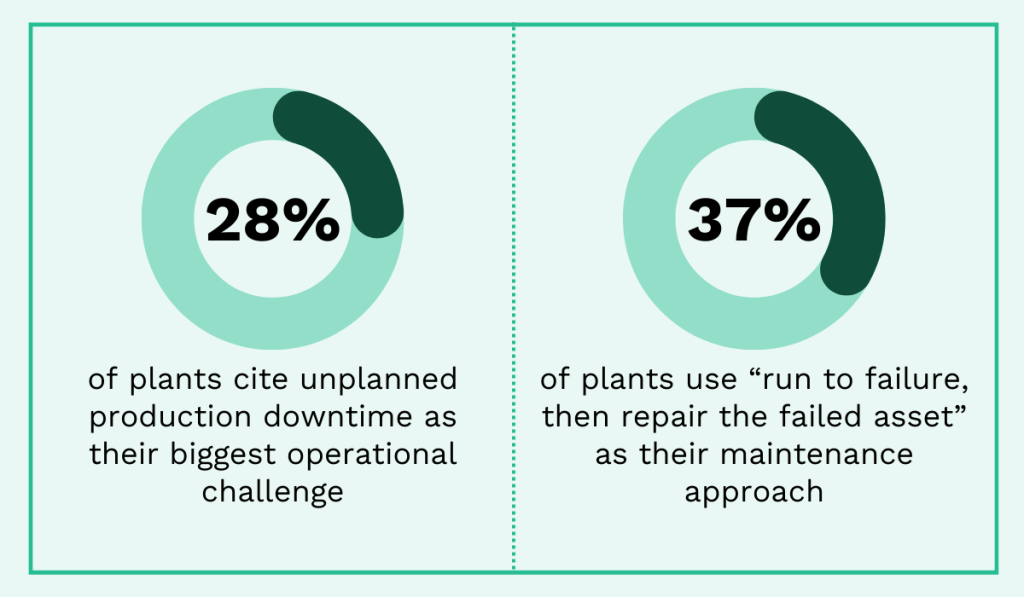
If you’ve ever experienced unplanned downtime, it’s more than just a small inconvenience.
It brings a cascade of disruptions and delays that impact your productivity and profits.
As Erik Schmidt, Resource Development Manager at Johnson Crushers International, Inc., puts it:
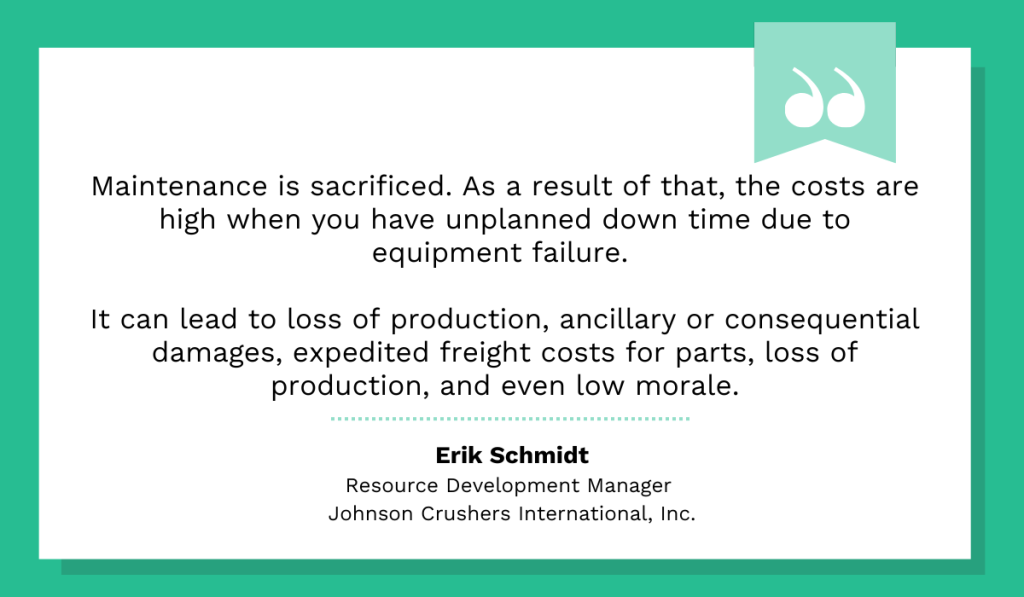
If this scenario resonates, it may be time to reevaluate your maintenance strategy and adopt new practices.
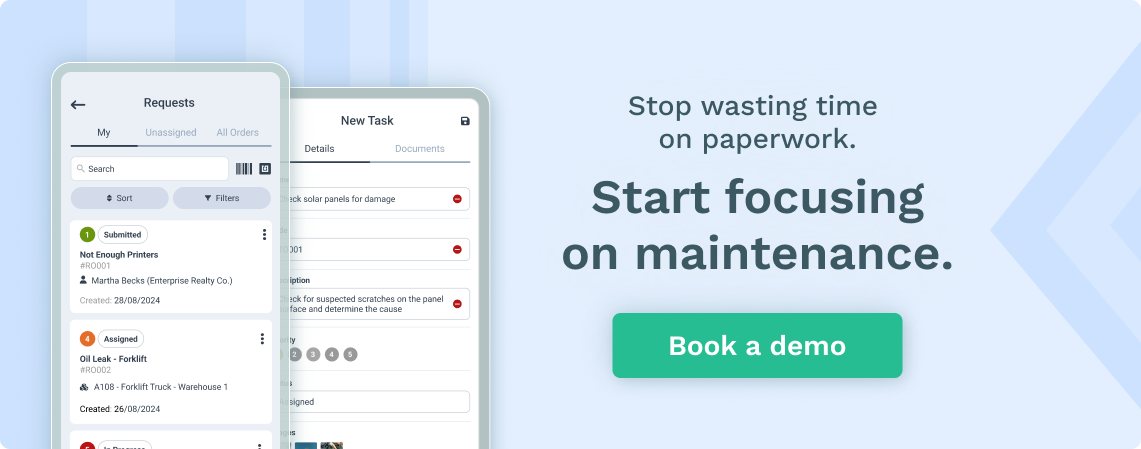
Whichever maintenance strategy you choose, prioritizing proactive measures will undoubtedly minimize unplanned downtime.
Increased Repair Costs
If repair costs at your facility start increasing, this is another red flag to pay attention to.
It could be a sign that your assets are not being maintained properly, so minor issues have room to evolve into major problems that require costly repairs.
Take vacuum pumps, for example.
They are critical in industries where air or gas removal is necessary, and their repair can get pretty expensive.
Gene Ligman, Senior Account Manager at Leybold, an industrial vacuum equipment supplier, breaks down the cost:
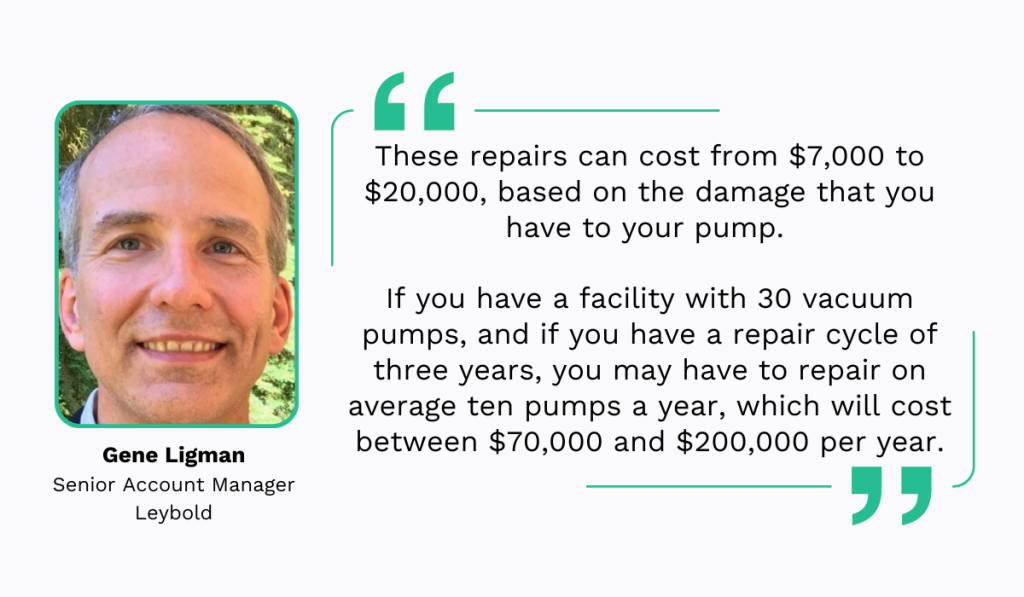
This puts things in perspective and underscores the importance of being proactive with your maintenance.
While consistently facing high repair costs is bound to eat into your profits, maintenance can nip many issues in the bud and protect your bottom line.
Luckily, more and more maintenance professionals recognize this, with cost reduction being the biggest priority in 2024 for almost 30% of them.
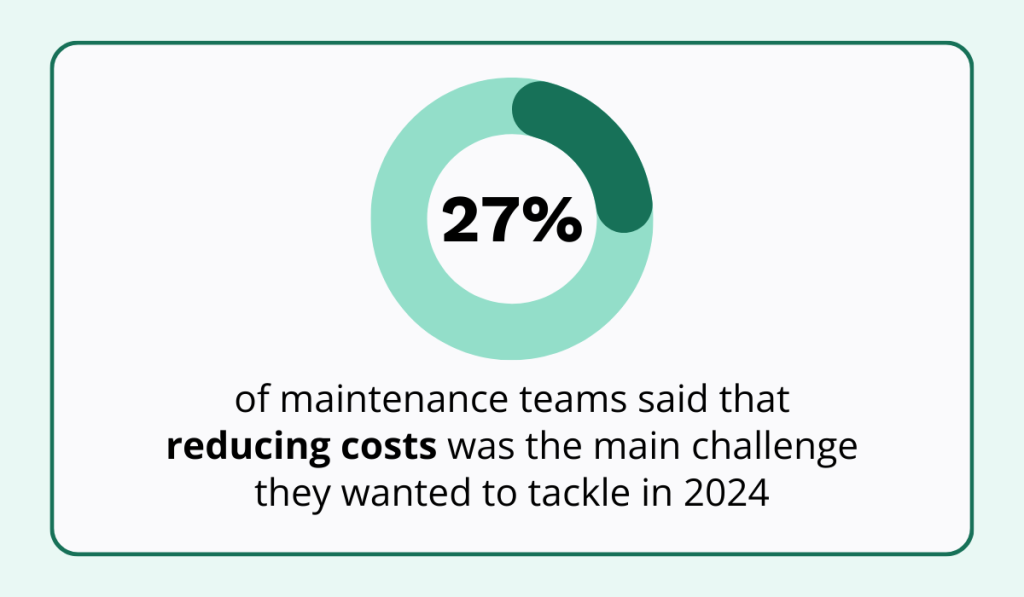
At the same time, facilities are increasing their maintenance budgets.
This suggests that they see the value in investing in maintenance upfront rather than spending huge amounts of money on repairs down the line.
So, if you’re noticing repairs costing you more money than you’re comfortable with, consider following in their footsteps.
What Is the Role of CMMS In Asset Maintenance?
Implementing good maintenance practices is easier said than done, as it requires a shift in mindset and resources.
This is something many maintenance teams struggle with.
Research shows that, for 33.46% of them, planning and scheduling maintenance activities is the biggest challenge.
This raises the question of whether there is a tool that can make the whole process easier and more streamlined.
The answer is: yes, a robust CMMS like WorkTrek.
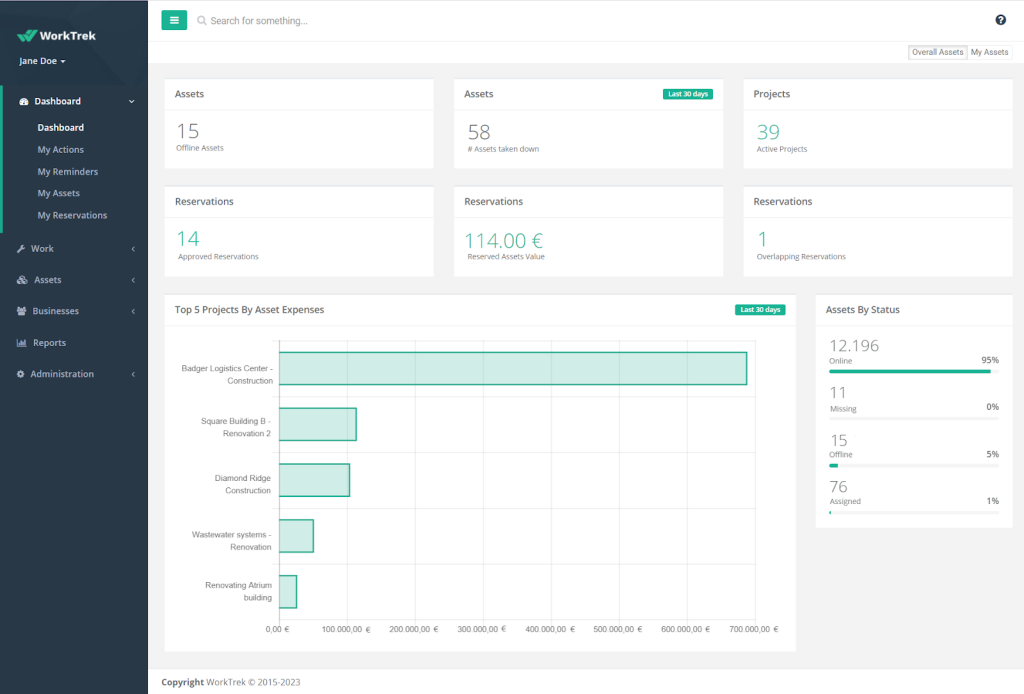
WorkTrek is a feature-rich maintenance management solution that serves as the central nervous system of your operations.
It consolidates the scheduling, tracking, and documentation of all your maintenance activities, making all asset and maintenance data easily accessible to the relevant personnel.
What particularly stands out in this context are WorkTrek’s preventive maintenance capabilities.
Our easy-to-use system allows you to schedule preventive maintenance, complete with SOPs, checklists, photos, and instructions for maintenance workers.
That way, you can be sure that all your assets receive maintenance according to standardized procedures.
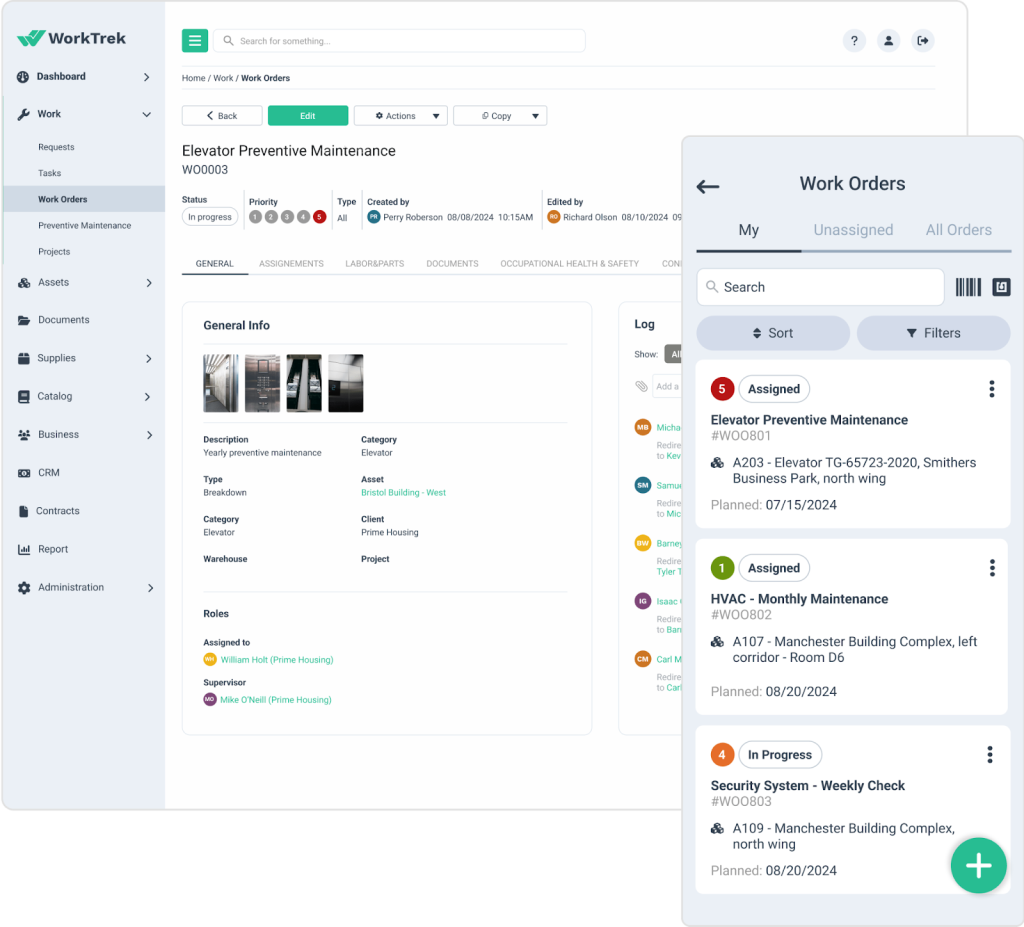
You can also schedule maintenance tasks at regular intervals and generate preventive maintenance work orders based on meter readings.
You no longer have to waste time scheduling tasks manually, allowing you to focus on more strategic initiatives.
And our users’ experiences reflect that:
WorkTrek has been a huge asset to our company. We used to rely on manual processes for task management, service reporting, and work order management but with Worktrek we can now do all of this quickly and efficiently. The software is easy to use and has saved us time & money. I’d highly recommend it!”
— Anne Garcia
Overall, a good CMMS will help you improve efficiency, reduce unplanned asset downtime, and ensure that your assets are always properly maintained.
This makes it an indispensable solution for any facility to streamline its maintenance processes.
Conclusion
Asset maintenance is a process essential for the proper functioning of any facility across different industries.
It helps you make the most of your machinery, keep your operations running smoothly, and create a safe environment for your personnel.
Developing a thorough strategy and investing in the right tools is key to implementing good maintenance practices.
So, take a moment to review your current asset maintenance approach, pinpoint improvement areas, and take the leap.
It will be worth it.