Get a Free WorkTrek Demo
Let's show you how WorkTrek can help you optimize your maintenance operation.
Try for freeKey Takeaways
- Downtime can cost companies between $140 million and $280 million each year.
- CMMS solutions are one of the most effective ways to reduce maintenance backlogs.
- Preventive upkeep strategies help minimize organizations’ environmental impact.
Asset maintenance is as challenging as it is important.
This is why today, we’ll explore some of the most common and pressing obstacles faced by modern upkeep professionals.
However, our goal isn’t just to point out the problems.
We’ll also examine why these issues are particularly problematic and share some actionable tips for overcoming them.
By the end of this read, you’ll be equipped to address these challenges effectively, elevating your maintenance strategies to new heights.
Unplanned Asset Downtime
Proactively scheduling maintenance to address asset problems before they escalate into unplanned downtime is one of the biggest challenges upkeep professionals face.
After all, this is a very costly issue—and it grows more expensive each year.
Jim Davison, National Membership Director at Make UK, a London-based manufacturing advocacy organization, elaborates:
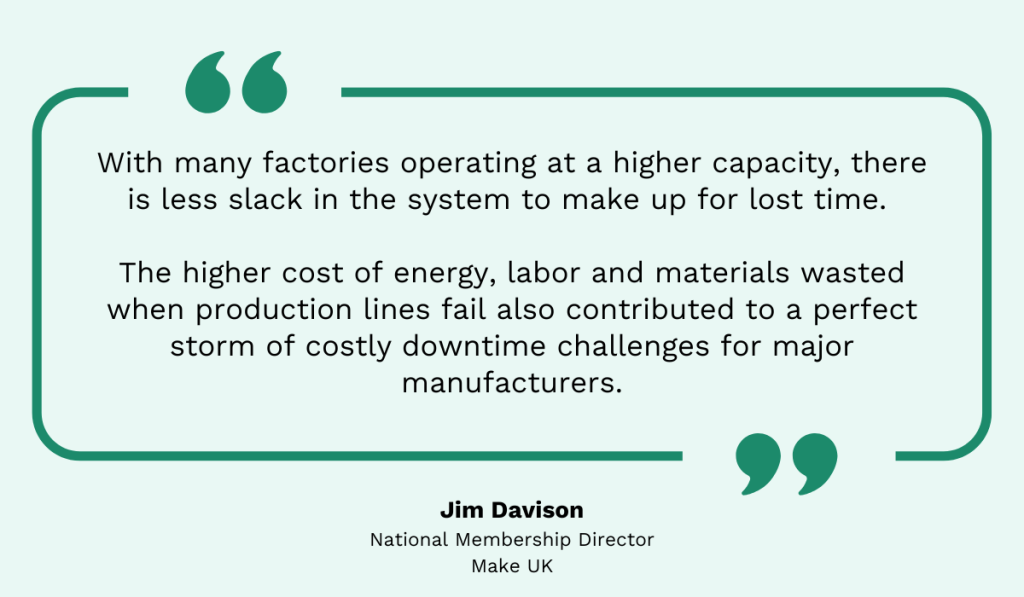
While Davison’s insights focus on the manufacturing industry specifically, downtime impacts all sectors almost equally.
A recent survey by Splunk confirms this.
Retail and manufacturing industries are certainly hit the hardest, with annual downtime costs exceeding $200 million.
However, even in less-affected sectors, costs are steep, surpassing $140 million annually.
This is why maintenance teams are under so much pressure to prevent unscheduled downtime and help maintain operational efficiency.
Luckily, overcoming this challenge is now easier than ever, thanks to the Computerized Maintenance Management Systems (CMMS).
These systems allow users to track the performance, health, and usage of assets.
This, in turn, enables them to schedule service or inspections based on the equipment’s actual condition.
That way, issues get addressed in advance, before they turn into significant operational and financial setbacks.
As shown in the example below, CMMS serves as a digital central control room.
It allows you to access all vital information, like physical location, warranty details, maintenance or downtime history, expenses, and more.

But these solutions don’t just monitor. They also take action.
CMMS can automatically generate preventive maintenance work orders based on specific triggers like usage time, mileage, temperature, or pressure.
That way, it’s even easier to ensure nothing slips through the cracks and that each asset receives timely care.
This is the foundation of effective unplanned downtime prevention.
Maintenance Backlogs
A maintenance backlog refers to the accumulation of upkeep tasks that have been identified, but remain incomplete.
When poorly managed or excessively large, backlogs can lead to significant issues, ranging from unplanned downtime to safety risks.
In some cases, they can even impact an organization’s reputation and customer satisfaction.
OC Transpo, the public transportation operator in Ottawa, Canada, recently faced such a challenge.
Namely, some bus trips went undelivered due to an upkeep backlog in their fleet.
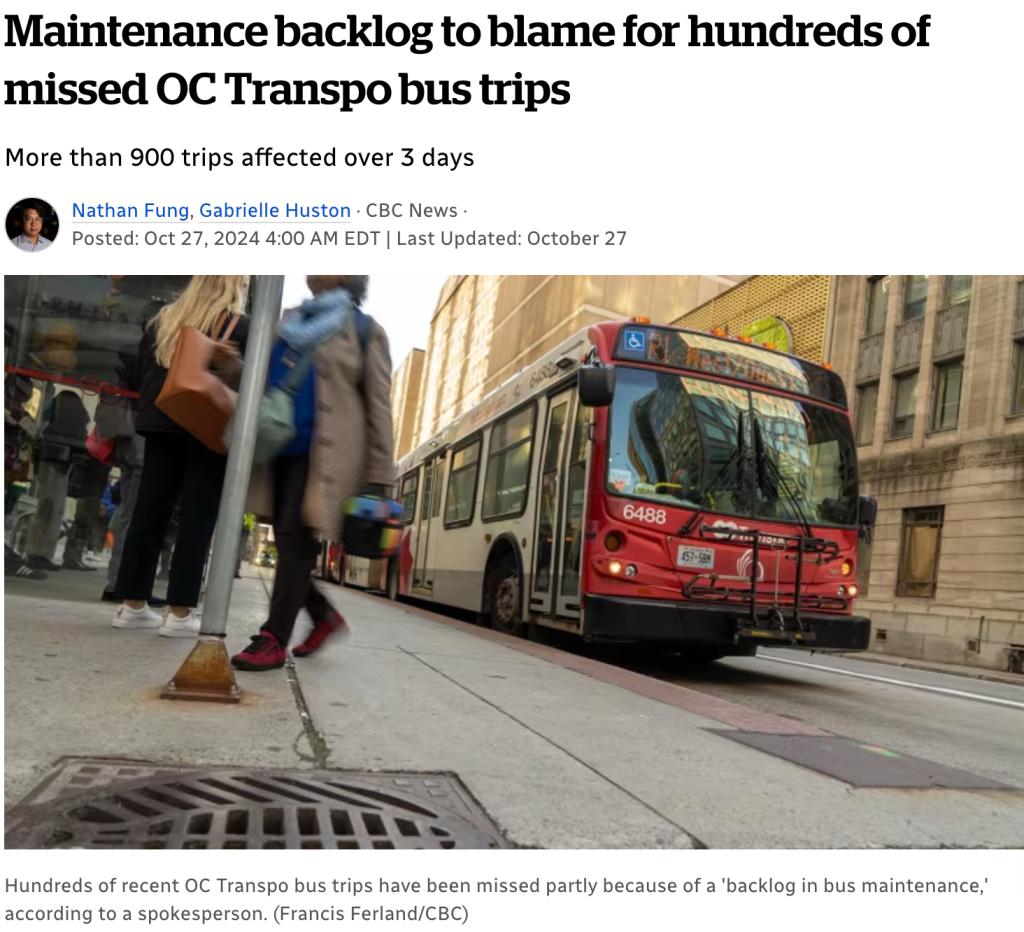
In fact, out of 8,210 planned daily trips, OC Transpo reported to CBC that hundreds were missed within a single week.
For transit riders, this was understandably frustrating, prompting OC Transpo to issue a public apology on X (formerly Twitter).
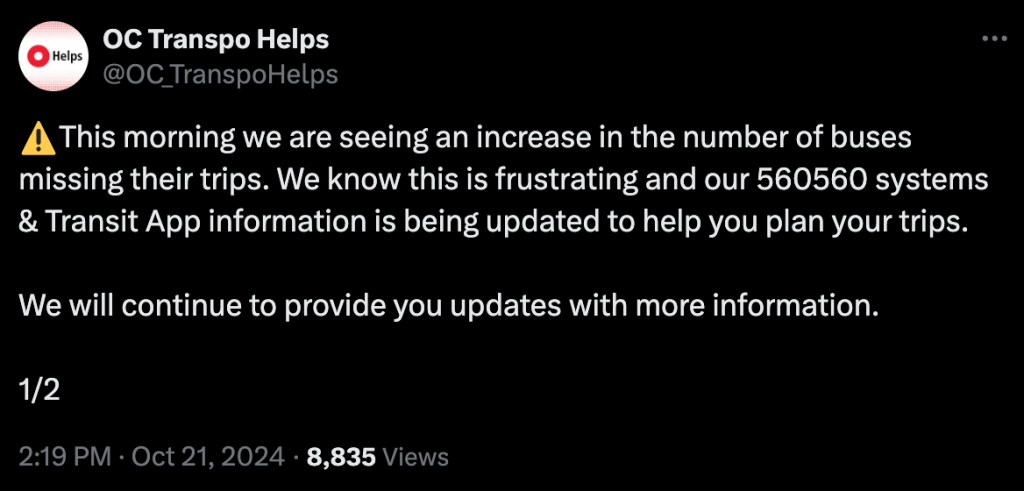
One common cause of backlogs is the reliance on inefficient manual maintenance tracking and planning processes.
This is because paper- or spreadsheet-based record-keeping is highly prone to errors and lacks real-time updates.
Ultimately, that makes it difficult to identify problems, prioritize tasks, and schedule service strategically.
As a result, high-priority repairs often get delayed until they escalate into more serious issues.
However, with CMMS like WorkTrek, this all changes.
Thanks to WorkTrek’s work request/order management feature, monitoring, assigning, and managing tasks has finally become so much simpler and more efficient.
Users can submit requests through various channels—such as the WorkTrek app, email, or request portal—as soon as a problem is detected.
Then, they can track the request’s status in real time, as shown below:
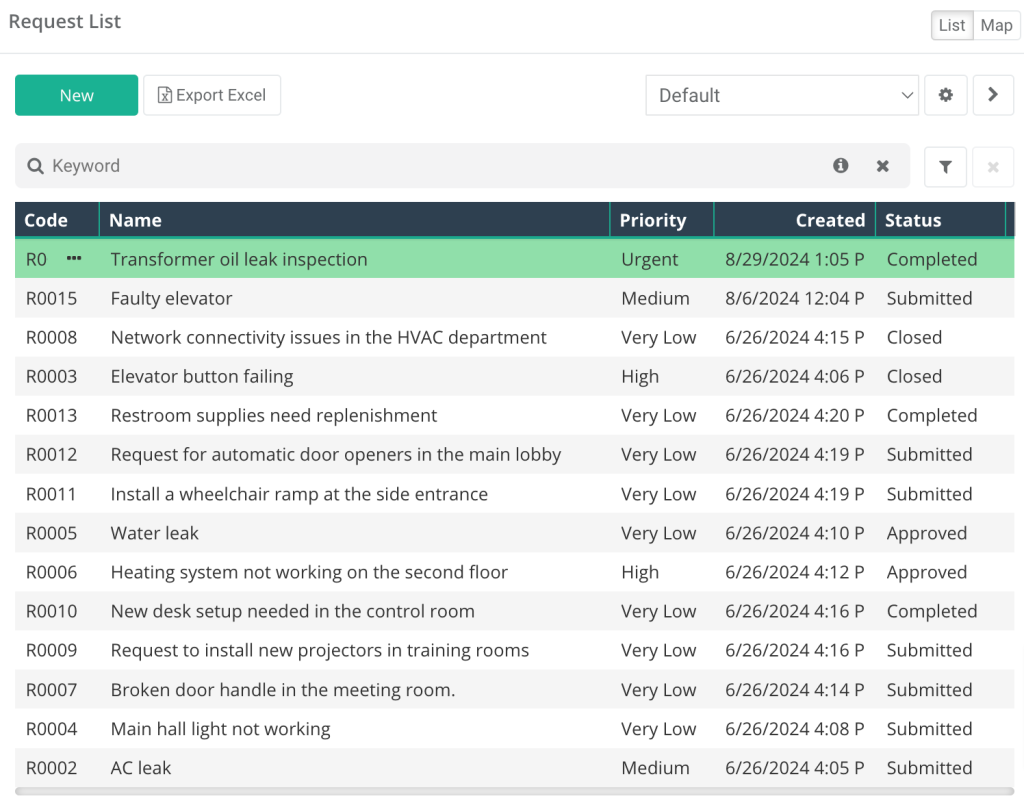
Within the same system, you can also create, assign, and prioritize work orders using highly customizable forms.
This way, you ensure you always capture all the essential information, such as components used, costs incurred, working hours, and even signatures.
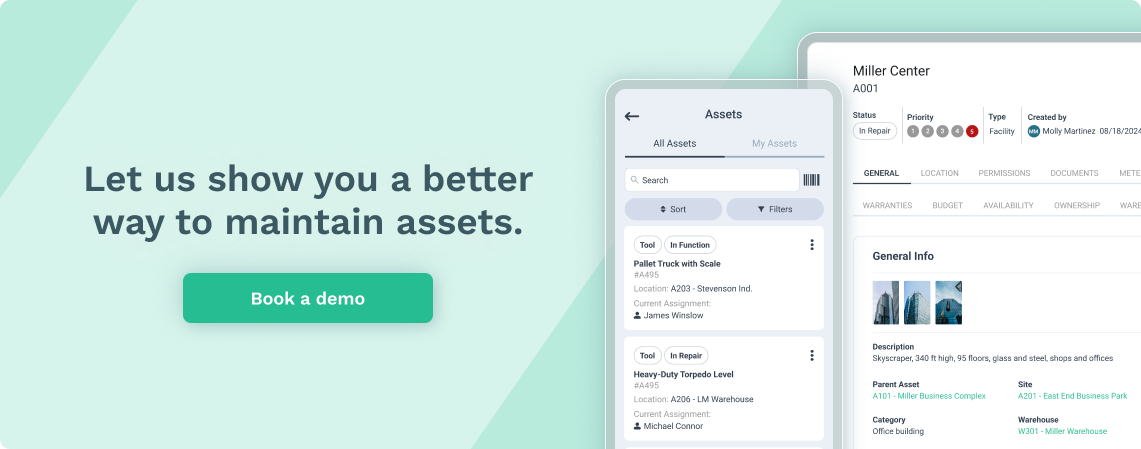
To see how much of the work is actually being finished on time and within budget, check WorkTrek’s intuitive dashboard.
There, you’ll find a brief overview of pending, completed, and overdue tasks, which will help you quickly identify any inefficiencies and avoid an overly large backlog.

The bottom line is this: to solve the issue of mismanaged backlogs, you need an efficient, transparent maintenance planning and scheduling process.
That way, tasks get neatly organized, appropriately prioritized, and—most importantly—completed on time.
Skill Shortages
Another significant contributor to maintenance backlogs and consequent downtime is the shortage of skilled personnel.
Every year, experienced maintenance professionals retire in growing numbers, while equipment and infrastructure become more complex.
As a result, finding qualified personnel to handle the workload has become a significant challenge.
And, according to the U.S. Bureau of Labor Statistics, the need for skilled workers will only continue to expand.
Their projections reveal that employment in installation, maintenance, and repair occupations will grow by 5.0% from 2021 to 2031, adding approximately 304,000 new jobs over the decade.
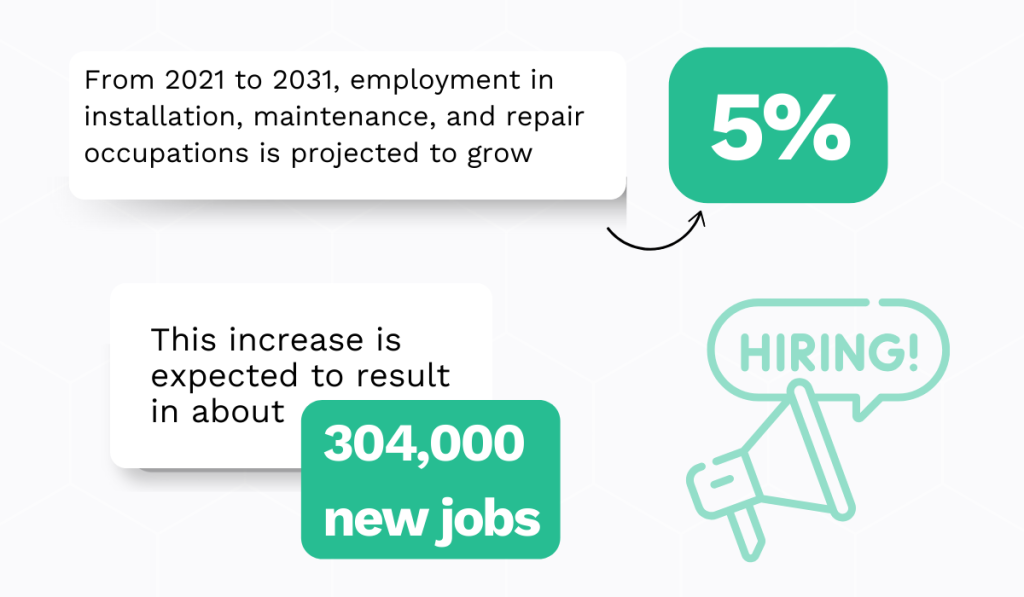
The problem is this: if this demand isn’t fulfilled, maintenance work can’t be done properly, which can have serious consequences for businesses across all industries.
Whether it’s transit agencies needing to cut services, aviation facing safety risks, or auto repair delivering subpar customer experiences, the skills shortage manifests in many different ways.
Addressing this challenge requires a twofold approach:
- maximizing the potential of the existing workforce, and
- finding alternatives for unfilled roles.
The former can be done by investing in training and upskilling your current team to keep them updated on the latest maintenance practices and technologies.
For example, the U.S. Air Force in Middletown, Pennsylvania, recently implemented virtual reality (VR) for this very purpose.
Technical Sgt. Anthony Gambone, leader of the 193rd Special Operations Wing VR program, explains why this technology is highly beneficial:
In short, this allows them to conduct customized training in a safe, time-efficient, and cost-effective way, while ensuring the staff has all the skills to tackle real-world challenges.
The second part of the solution is minimizing dependence on human labor.
This entails automating tasks wherever possible.
For instance, IoT devices and sensors can monitor asset conditions remotely, reducing the need for on-site inspections.
Additionally, CMMS can automatically track inventory levels across multiple locations, as shown in the example below:
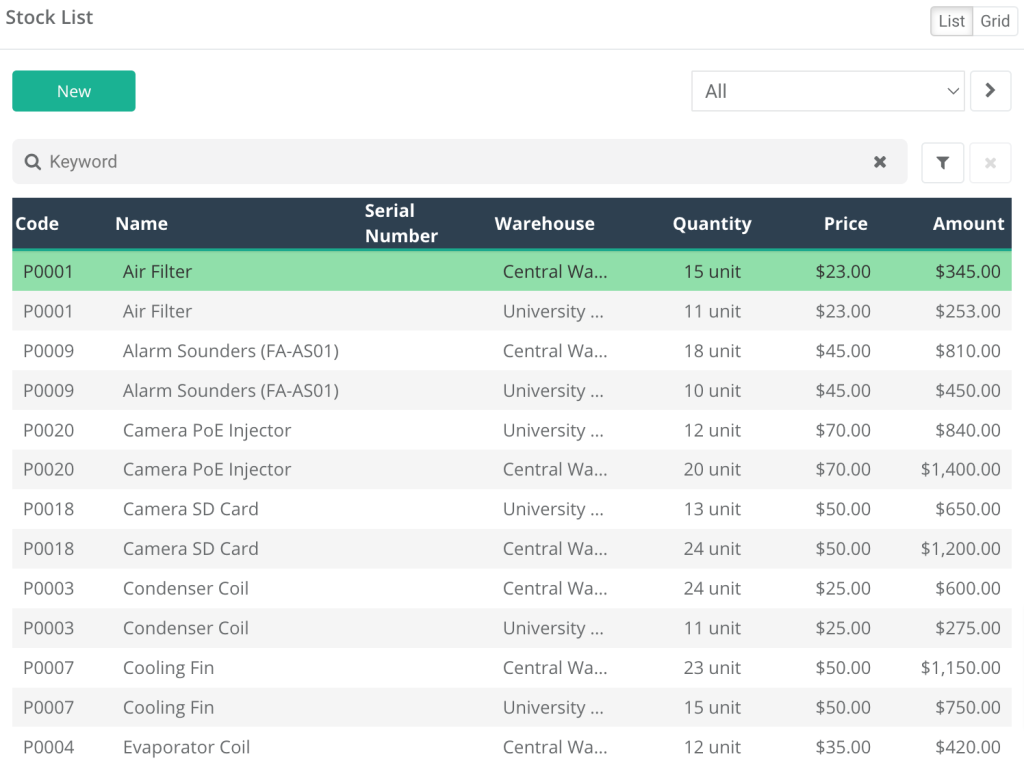
This allows you to minimize time spent on manual inventory checks, data entry, and fixing mistakes.
It’s the easiest, most effective way to maintain uninterrupted operations without reliance on a large team.
Aging Infrastructure
As assets age, their reliability and predictability decline.
That is why more frequent maintenance often becomes necessary.
Additionally, older machines sometimes use components that are no longer standard in design or materials, making them hard and expensive to replace.
All of this not only makes aging assets difficult to maintain but also leads to a variety of safety and operational risks.
In fact, research from the Institution of Mechanical Engineers identifies aging equipment as a leading cause of unplanned downtime across industries.
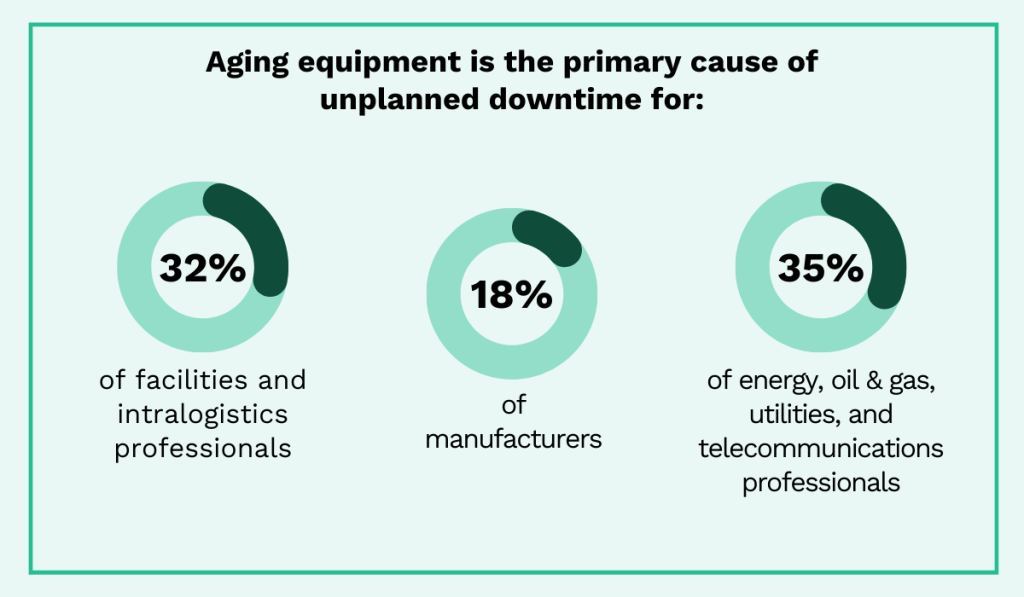
The ideal solution to this challenge would be to replace outdated assets with new ones that meet modern standards.
However, this is rarely financially viable.
Richard Jeffers, Owner of Two6 Services Ltd, a consulting agency focusing on the digitization of manufacturing teams, agrees that outright replacement isn’t the answer for most companies.
Instead, he suggests that maintenance teams hold the key to solving this problem.
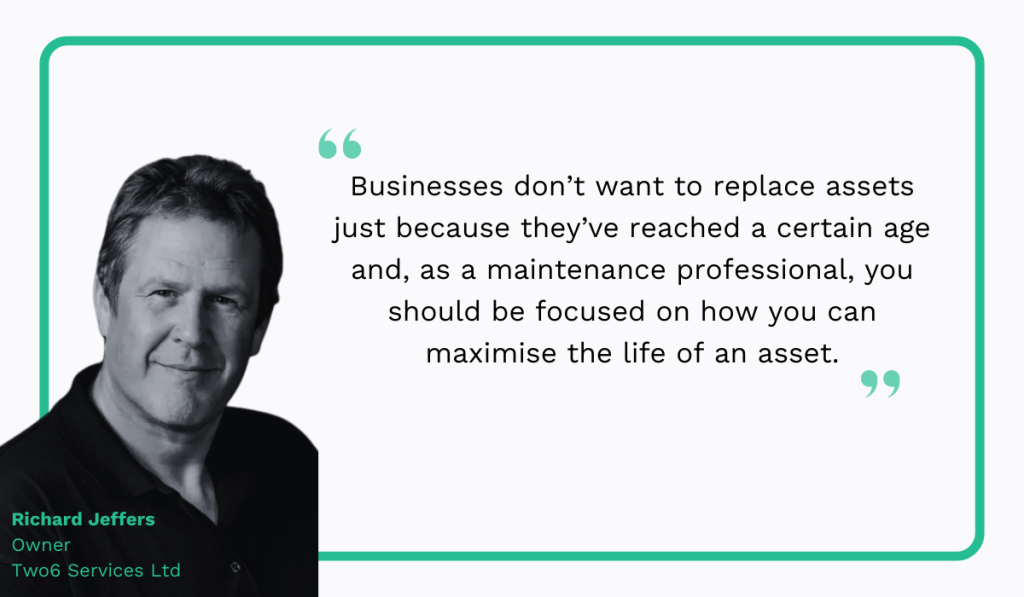
Yes, it’s ultimately up to maintenance personnel to try to increase the lifespan and reliability of existing assets as much as possible.
This is best achieved through regular inspections and condition-based maintenance enabled by the integration of IoT, AI, and CMMS.
IoT sensors provide unprecedented insights into asset health, from speed and vibration to temperature and other vital variables.
AI then takes the data from these sensors and identifies patterns or anomalies, flagging potential problems before they spiral out of control.
Aneesh Goly, President of the Infrastructure IoT company, Smart Structures, provides a specific example:
Armed with these insights, maintenance teams can make smarter decisions and use CMMS to proactively schedule repairs, keeping assets running smoothly and minimizing downtime.
Therefore, there is no need to give up on your older equipment just yet.
With the right combination of tools, you can ensure it keeps meeting your expectations and needs for years to come.
Data Overload
The data generated by various maintenance solutions is incredibly valuable for tracking asset conditions.
However, its sheer volume can often make it difficult to distinguish actionable insights from noise.
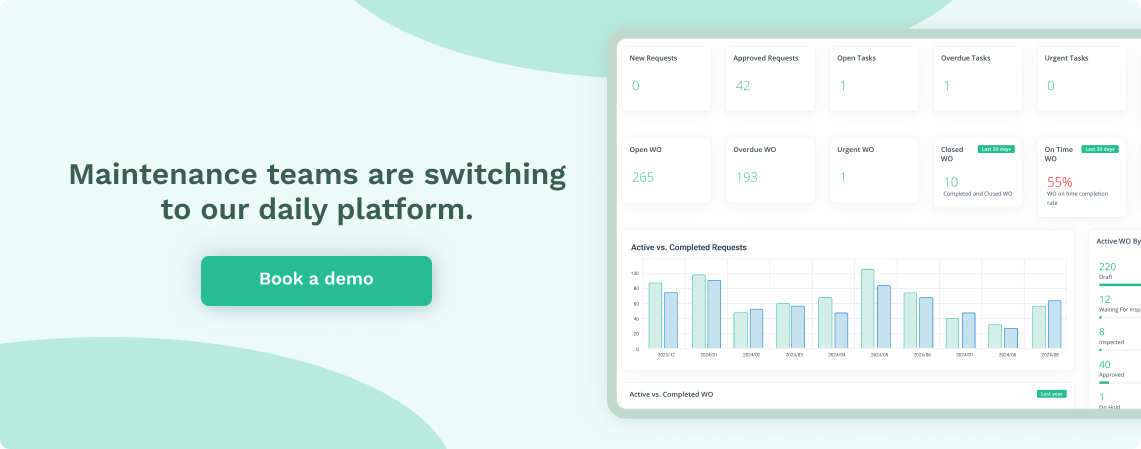
As Philipp Wallner, Industry Manager at MathWorks, the leading developer of mathematical computing software, says, managing this volume of data is no longer feasible for humans alone.
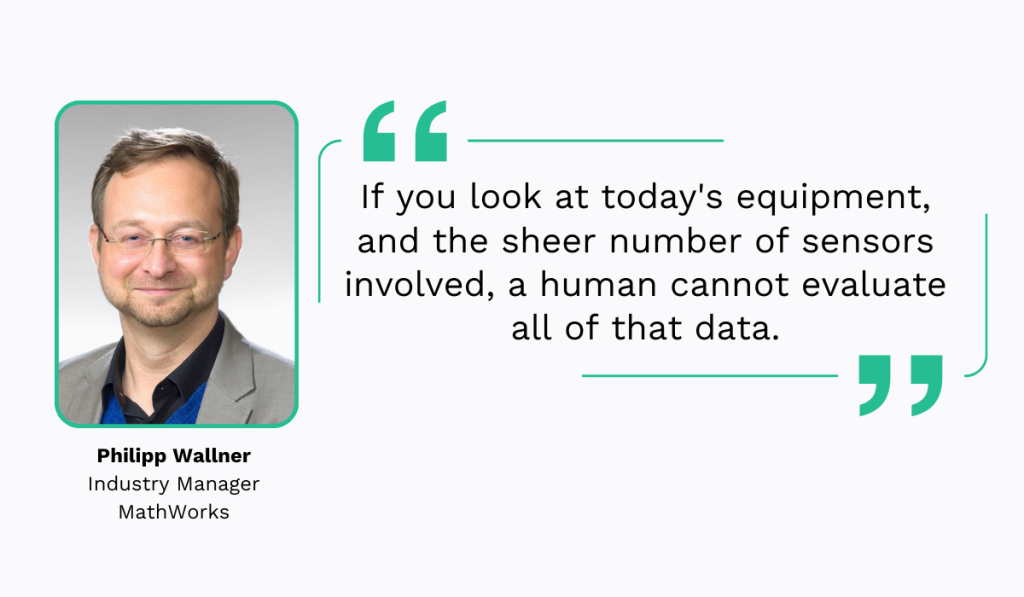
This is a problem because, when your team is drowning in data, the time required to analyze and interpret it increases.
Ultimately, this can lead to a delayed response to maintenance issues, potentially leading to equipment failures, unplanned downtime, and project delays.
This is why it’s essential to find a way to filter through the noise and identify the critical risks that need immediate attention.
The key is finding a digital solution with robust reporting capabilities that can quickly and easily extract meaningful insights from a sea of information.
Therefore, if you’re using or considering any kind of maintenance management solution, take a close look at its reporting features.
Here are some capabilities to look for:
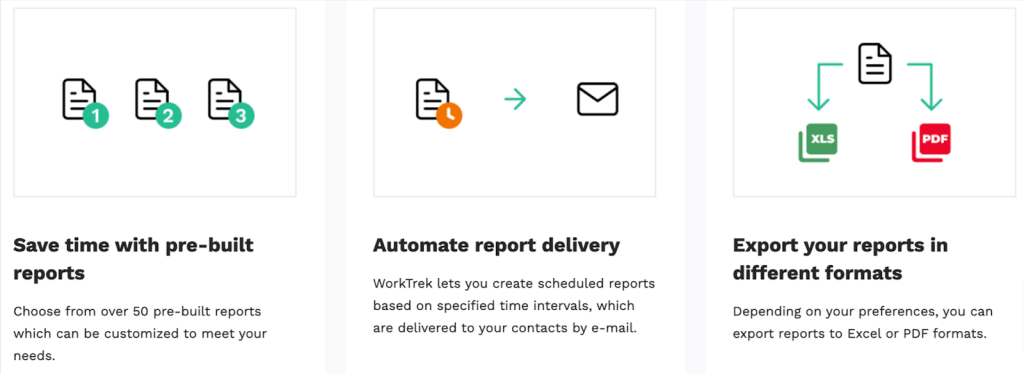
Ideally, the system should be able to analyze a wide range of maintenance metrics (like costs or equipment availability) and include customizable pre-built reports, like in the example below:
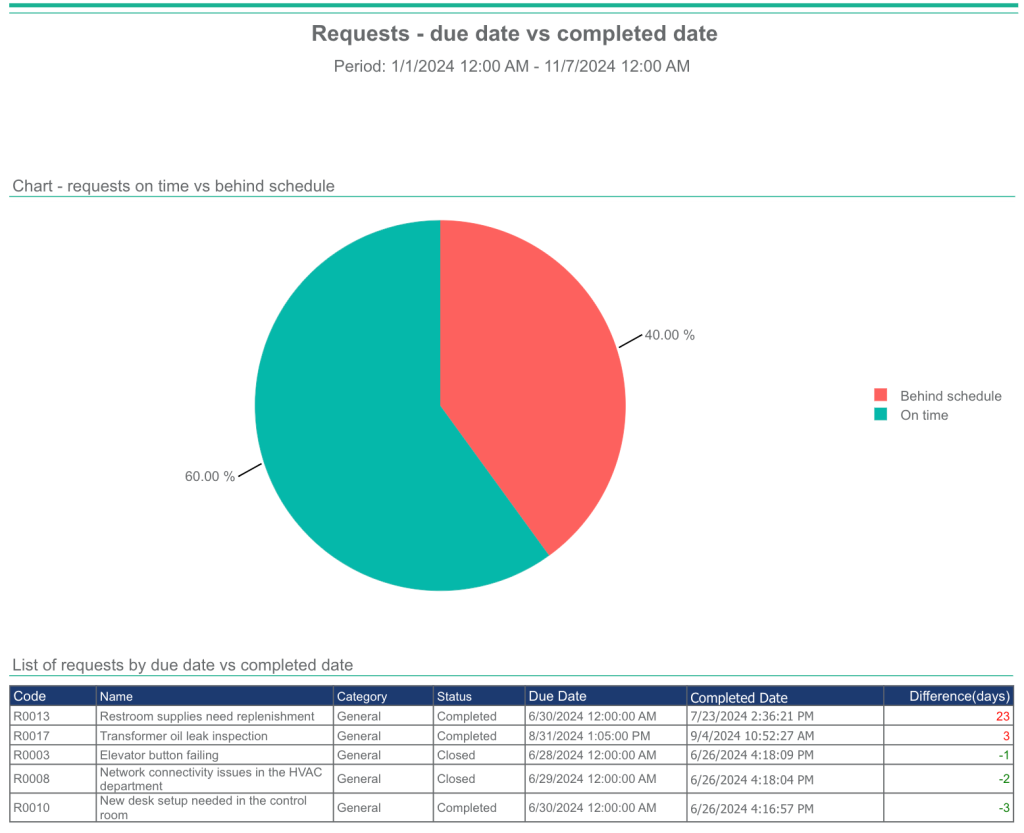
Overall, this simple, yet powerful feature makes all the difference in how you interact with your data.
Instead of sifting through mountains of information, scheduled reports bring actionable insights directly to you—saving time and enabling faster, more informed decision-making.
Environmental Concerns
Asset maintenance can contribute to high energy consumption, water usage, waste generation, and chemical emissions, ultimately causing harm to the environment.
If this isn’t managed properly, it can lead to all sorts of broader problems, such as:
- Noncompliance with laws governing emissions, waste disposal, and pollution control
- Reputational damage
- Safety concerns
To address this challenge, businesses should adopt sustainable practices that minimize their environmental footprint across their maintenance processes, tools, and materials.
There are numerous ways to achieve this.
So, let’s explore some specific examples of how companies are tackling these environmental challenges.
One effective approach is using non-invasive repair processes.
For instance, drainage systems in Australia utilize Quick-Lock, a trenchless pipe repair solution for point repair, pre-lining stabilization, and liner end sealing.
The key benefit of such repair solutions is that they require minimal excavation, significantly reducing environmental impact.
Peter Ados, Managing Director at Leading Civil Solutions, the company tasked with drainage infrastructure repairs at a Victoria airport, praised Quick-Lock for its practical and sustainable benefits.
The second possible solution to upkeep-related environmental concerns involves adopting sustainable maintenance tools.
One example of such a tool is the battery-powered Multi-Purpose Vehicle (MPV) for rail maintenance projects.
Developed in 2021 by Railcare, a Swedish manufacturer of rail maintenance machines, this vehicle is both emission-free and low-noise.
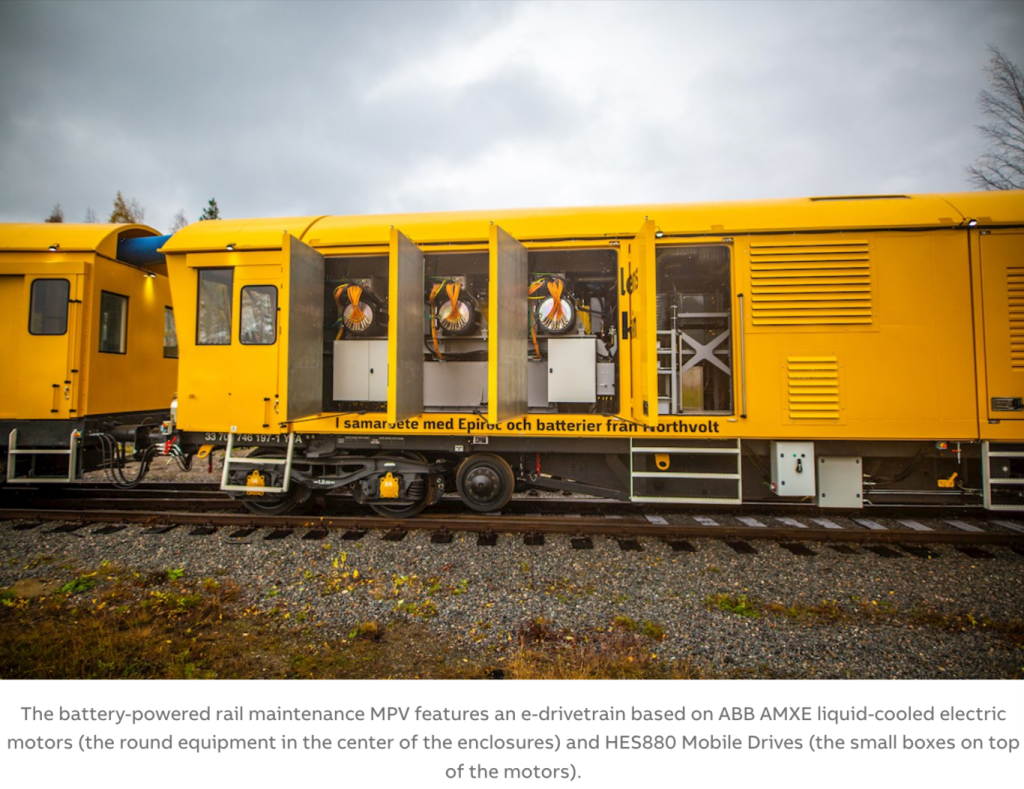
This makes it a highly eco-friendly alternative to traditional diesel-powered vehicles.
Finally, businesses can transform their overall maintenance strategy to be more sustainable.
Preventive or predictive maintenance, for instance, address issues before they escalate, thus reducing unnecessary wear and extending the life of machinery.
This, in turn, decreases the environmental impact associated with spare parts or energy consumption and waste generation.
Siemens even has the numbers to back this up.
They found that predictive maintenance leads to a significant increase in asset lifespan, as well as reductions in inventory, waste, and spare part consumption.
This directly translates into decreased waste generation and a more positive impact on the environment.
All in all, companies now have plenty of options when it comes to mitigating environmental risks associated with their maintenance efforts.
In fact, with a bit of careful planning and a proactive mindset, you can transform this process into a powerful force for environmental good.
Conclusion
There’s no denying that the role of a maintenance professional is becoming more challenging with each passing year.
Labor shortages, aging equipment, and an ever-increasing workload are more than enough to overwhelm anyone.
However, these challenges also bring new opportunities.
They are proof that maintenance is no longer just a reactive function, but a strategic player with the potential to deliver significant value to the organization.
It isn’t just about fixing what’s broken anymore, but about reducing costs, achieving sustainability goals, and fostering innovation.
So, rather than being discouraged by these challenges, embrace them.
With the right tools and mindset, you can overcome them and become one of the key drivers of your organization’s success.