Get a Free WorkTrek Demo
Let's show you how WorkTrek can help you optimize your maintenance operation.
Try for freeKey Takeaways:
- Over 30% of unplanned downtime can be attributed to a lack of the right parts and materials.
- Over 40% of facility management experts find work order progress tracking time-consuming.
- Companies using work order management software can reduce material costs and downtime by 20%.
Keeping up with maintenance work orders can feel like a never-ending battle—lost paperwork, miscommunications, and delays often lead to costly downtime.
Yet many manufacturing and facility management companies still rely on outdated processes, making maintenance more difficult than necessary.
Work order management software changes that in more ways than one.
In this article, we’ll explore the six biggest benefits of making the switch.
Automated Work Order Processing
Work order (WO) management software replaces manual processes, speeds up WO handling, and reduces costly errors.
Take, for example, the simple act of reporting an issue with equipment or infrastructure.
In a manual system, employees or clients must call, email, or even fill out a paper form to submit a maintenance request.
Regardless of the format, these requests can easily get lost, miscommunicated, or delayed as they pass through multiple hands before reaching the right technician.
A missing detail—like an unclear equipment ID—can cause even more back-and-forth, further slowing the repair process.
In contrast, with cloud-based, mobile-friendly software like WorkTrek, submitting a request is as simple as scanning a QR code or tapping a “New Request” in your smartphone app.
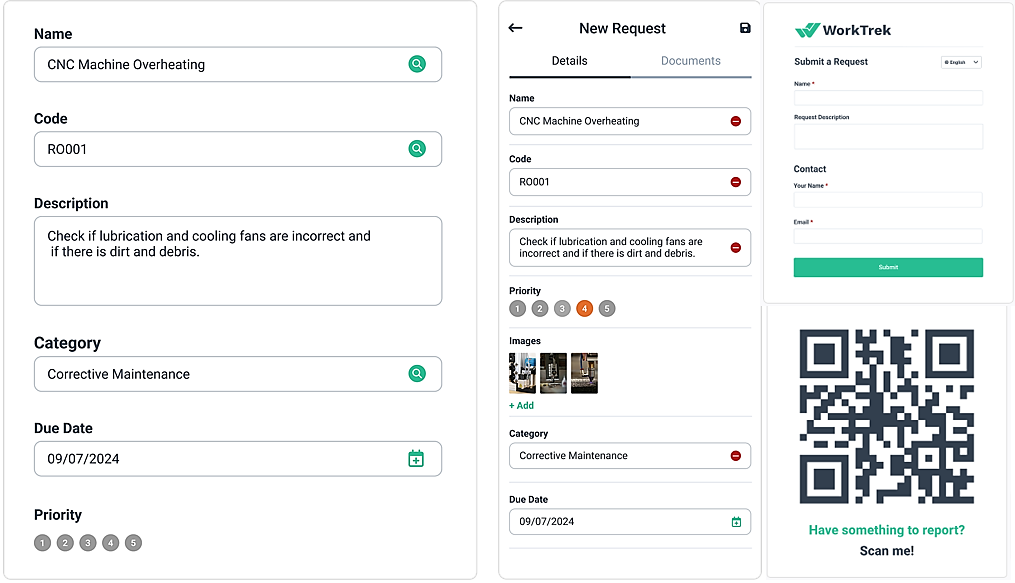
As shown above, users can quickly fill out request details on their mobile devices, describe the issue, and attach photos for added context.
Once submitted, the request is instantly recorded in a central database, triggering a real-time alert for the facility manager.
From there, the manager can review and approve the request, generate a new work order, and assign it to one or more technicians.
Those technicians are immediately notified, and the task appears in their app dashboard, prioritized according to the urgency level (from 1 to 5).
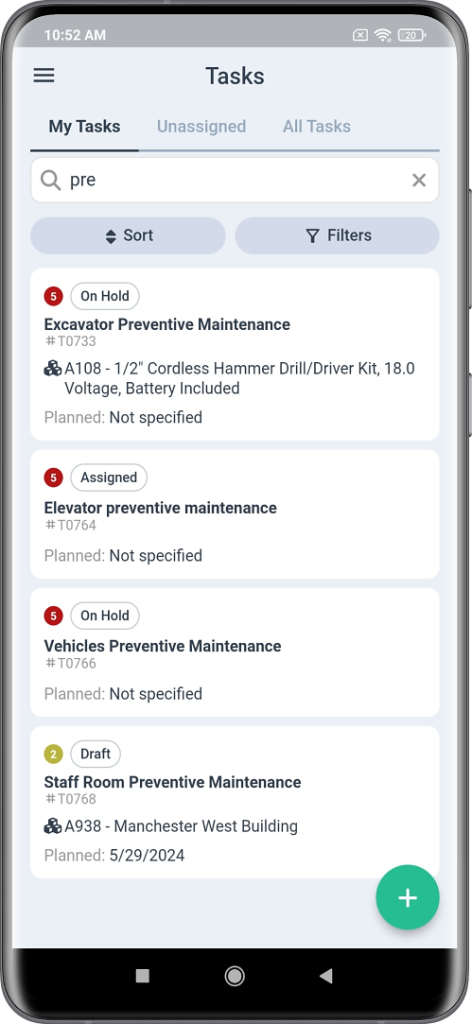
By reviewing the assigned work order, technicians can check which tools and spare parts they need, allowing them to better prepare for the upcoming task.
While executing a work order, the software app keeps field technicians connected to the facility manager.
For example, if they need any clarifications, they can quickly tag a supervisor to assist, like below:
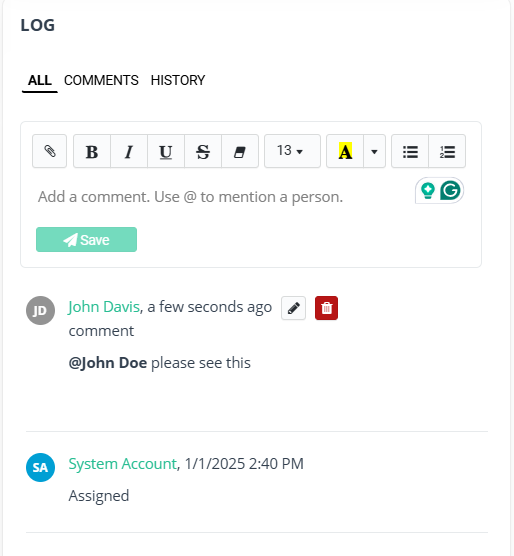
Technicians can also use digital checklists to complete the job according to set procedures.
Once the job is done, they can close the work order and upload photos directly from the site.
Meanwhile, the facility manager can track the progress and status of all work orders in one place, with clear visibility into ongoing, pending, and completed tasks.
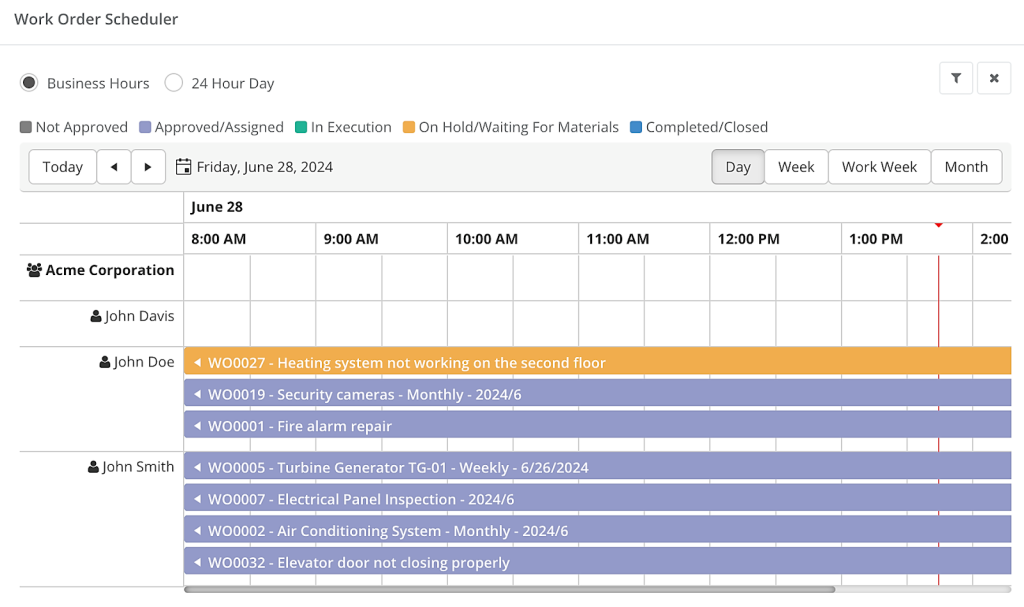
All these automation capabilities make work order processing significantly faster and more efficient.
This is especially important, as JLL Technologies’ report found that over 55% of surveyed facility management experts saw increased work orders in 2024.
At the same time, more than 44% said tracking work order progress remains their most time-consuming task.
With work orders on the rise and manual tracking causing delays, automating work order processing has never been more important.
Optimized Resource Usage
Effective resource management is essential in maintenance operations, and software can address many inefficiencies of manual resource tracking.
Common challenges include the following:
- Technicians spend excessive time traveling between jobs
- Tools and equipment is not where it’s needed
- Spare parts run out unexpectedly
Work order management software eliminates these issues by leveraging real-time tracking to optimize labor, tools, and inventory.
For example, when a new request comes in, the facility manager can quickly check which technicians are available nearby, minimizing unnecessary travel time.
This ensures the right person is sent to the job with minimal delay.
Additionally, the facility manager can monitor assignments and their progress in real time via a centralized dashboard.
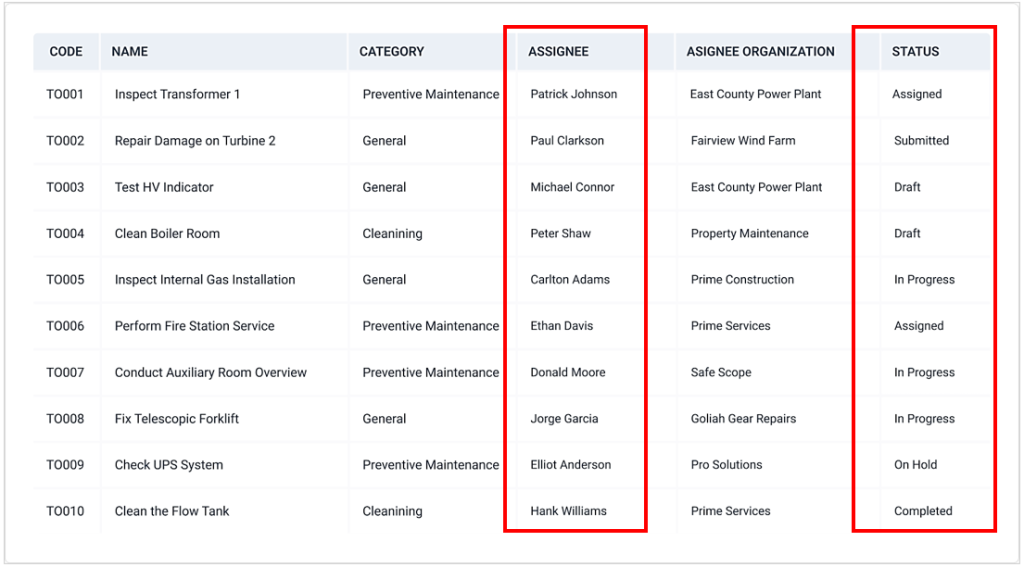
This streamlined task assignment and scheduling allow you to reduce inefficiencies and optimize labor allocation.
This further minimizes risks such as:
- Double-booking technicians on the same task
- Sending multiple technicians separately to the same location
- Overloading individual technicians with too many assignments
Beyond managing labor, work order management software helps track and optimize the distribution of tools, spare parts, and other supplies.
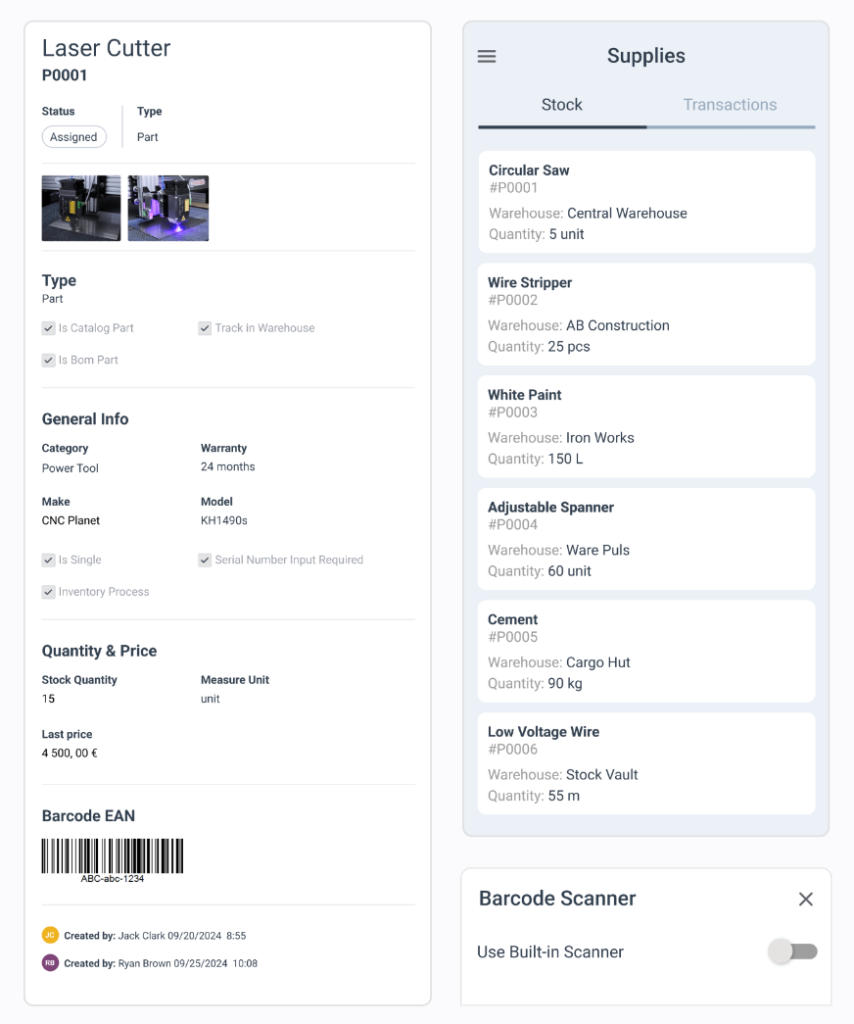
As shown above, the software allows technicians to quickly find and check the availability of tools and equipment they need for maintenance tasks.
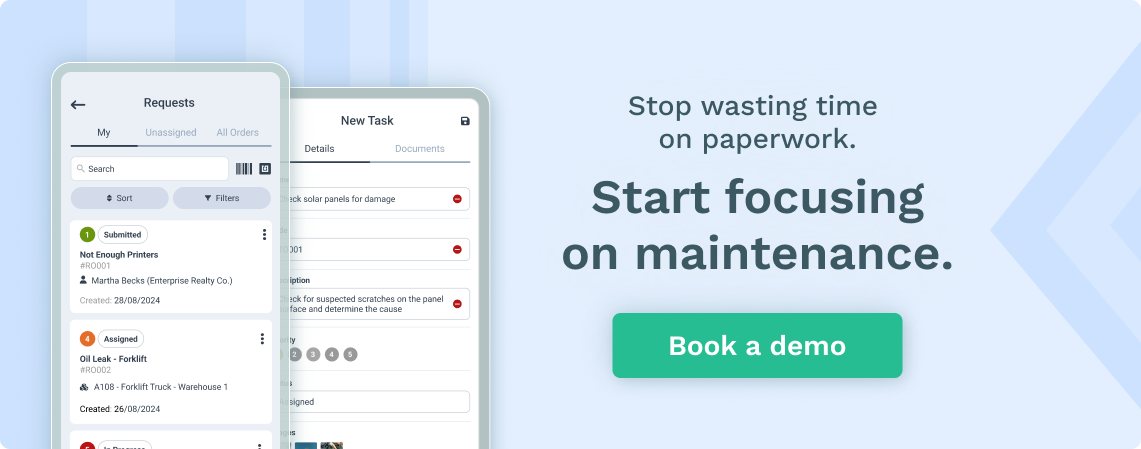
It works the same way with spare parts and materials, giving your team real-time visibility into stock levels.
Needless to say, ensuring your technicians have everything they need before they arrive on-site is crucial.
Equipment failures can lead to costly, unplanned downtime without the right parts.
As Jeff Shiver, CEO of People and Processes Inc., points out:
“Studies have shown as much as 32% of downtime was related to not having the right parts and materials in the storeroom.”
Given this, it’s clear that full visibility into inventory is essential for keeping your facility or plant running smoothly.
Even better, work order software can send automatic alerts when stock levels for critical parts are running low.
You can set minimum thresholds for each item and get real-time notifications when inventory drops below those levels, as illustrated here:
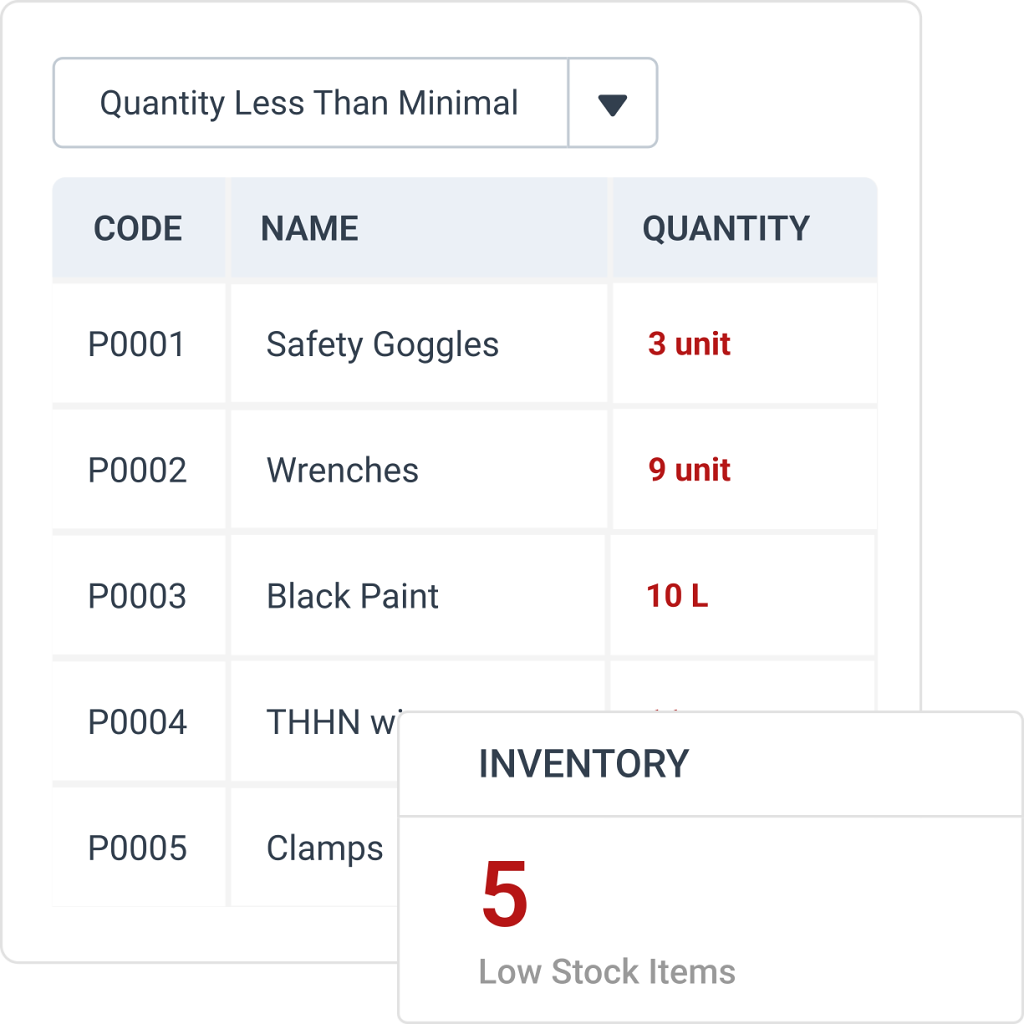
Most work order management software can integrate with your inventory management system and other business platforms.
This ensures that maintenance, inventory, operations, and procurement are all aligned, so you have the right resources available when needed.
Enhanced Accountability
Work order management software can eliminate gaps in responsibility, task ownership, and compliance.
As mentioned earlier, digital work orders ensure that every task is assigned to a specific technician and that it has clear deadlines, required steps, and priority levels.
This way, responsibilities are well-defined, and no work falls through the cracks.
Additionally, technicians and field workers can use work logs to record their activities and time spent on specific tasks, providing managers real-time updates on task progress.
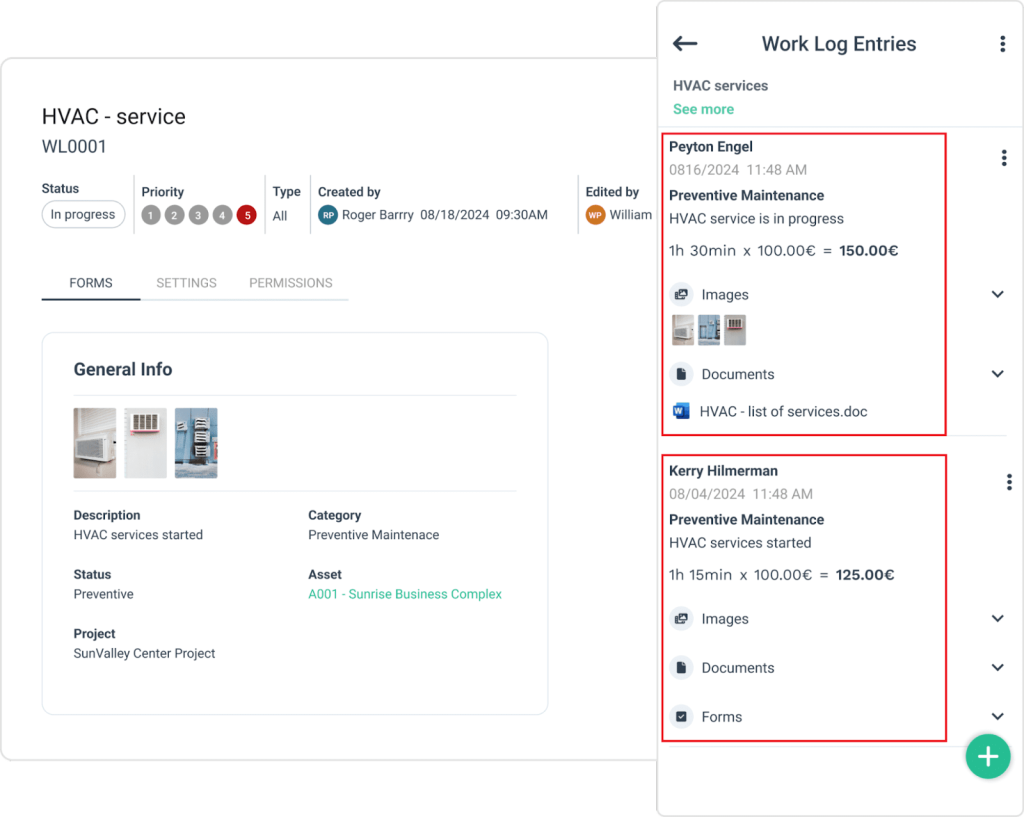
These log entries create a transparent activity record, allowing managers to monitor work progress and address delays before they escalate.
Another accountability-boosting feature is the clock-in/out function, which enables technicians to log their work hours accurately for reporting and billing purposes.
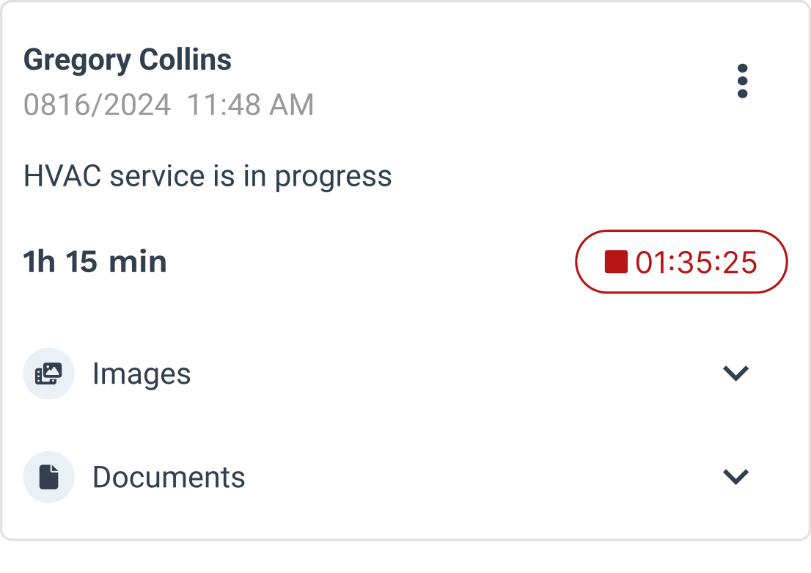
This is further enhanced by expense tracking, which allows users to record all work-related costs directly in the work log, ensuring accurate expense management and reporting.
Beyond improving team accountability, work order management software supports compliance with industry regulations and safety standards.
For instance, digital checklists and forms help verify task completion and ensure adherence to company procedures and industry regulations.
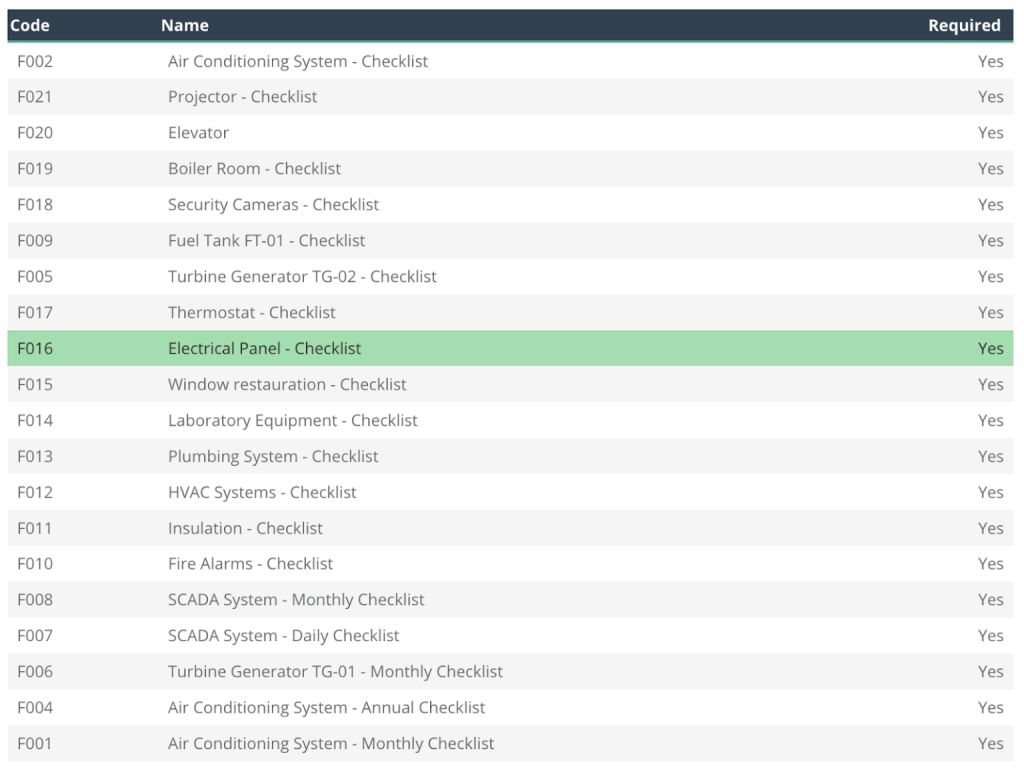
When combined, work log entries, time & expense tracking, and checklists create a clear audit trail of maintenance activities.
With it, you can easily demonstrate adherence to safety protocols and equipment servicing schedules.
Additionally, if a piece of equipment fails inspection or is flagged for other issues, technicians can automatically create a follow-up work order.
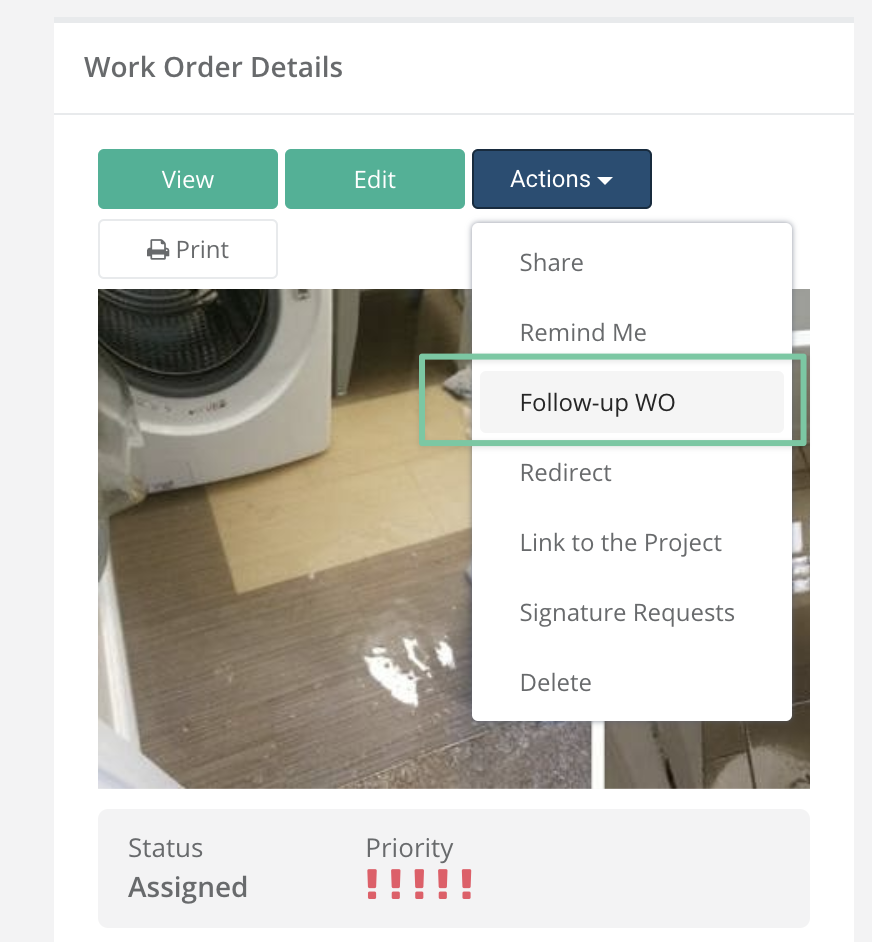
Lastly, work order management software also comes with analytics and reporting features, further enhancing transparency and accountability.
These features combined foster a culture of accountability, ensuring that every task is tracked, documented, and optimized for efficiency and compliance.
Reduced Maintenance Costs
Unplanned repairs and emergency breakdowns are among the biggest drivers of high maintenance costs.
When equipment fails unexpectedly, your organization incurs repair expenses and suffers from lost productivity and costly downtime.
Work order management software helps prevent these issues by allowing you to plan and schedule preventive maintenance, cutting down on operating costs and avoiding costly breakdowns.
Research by BusinessWire confirms this.
Namely, companies using such software experienced an average 20% reduction in material costs and equipment downtime.
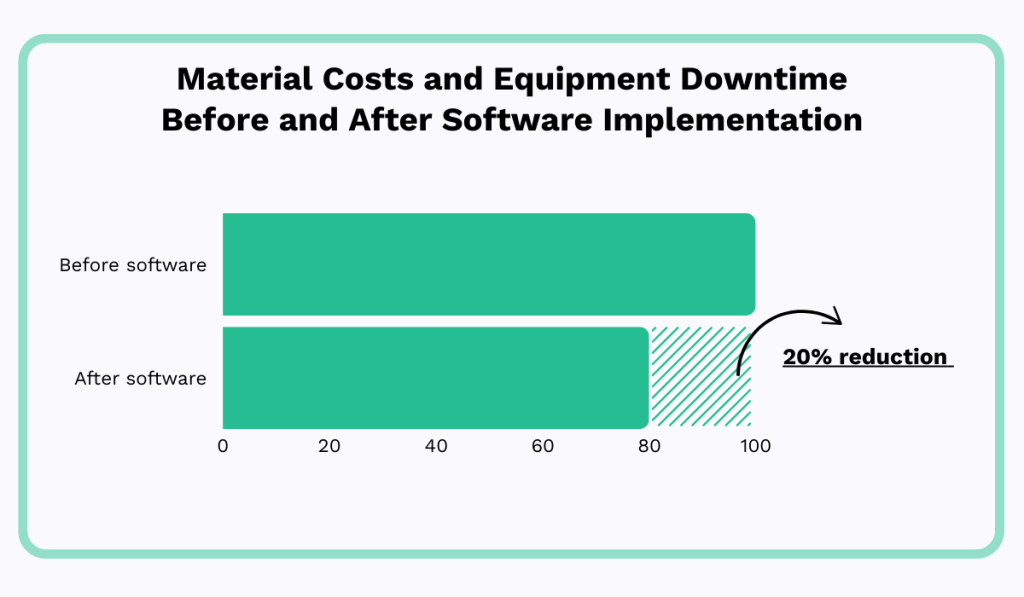
This cost reduction is achieved through combining key software features we’ve already discussed.
For instance, centralized work order scheduling ensures that inspections, preventive maintenance, and part replacements happen on time.
This prolongs asset lifespan and reduces the frequency of major repairs and costly replacements.
Beyond scheduling, work logs and checklists help technicians follow standardized maintenance procedures, minimizing errors that could lead to unexpected breakdowns.
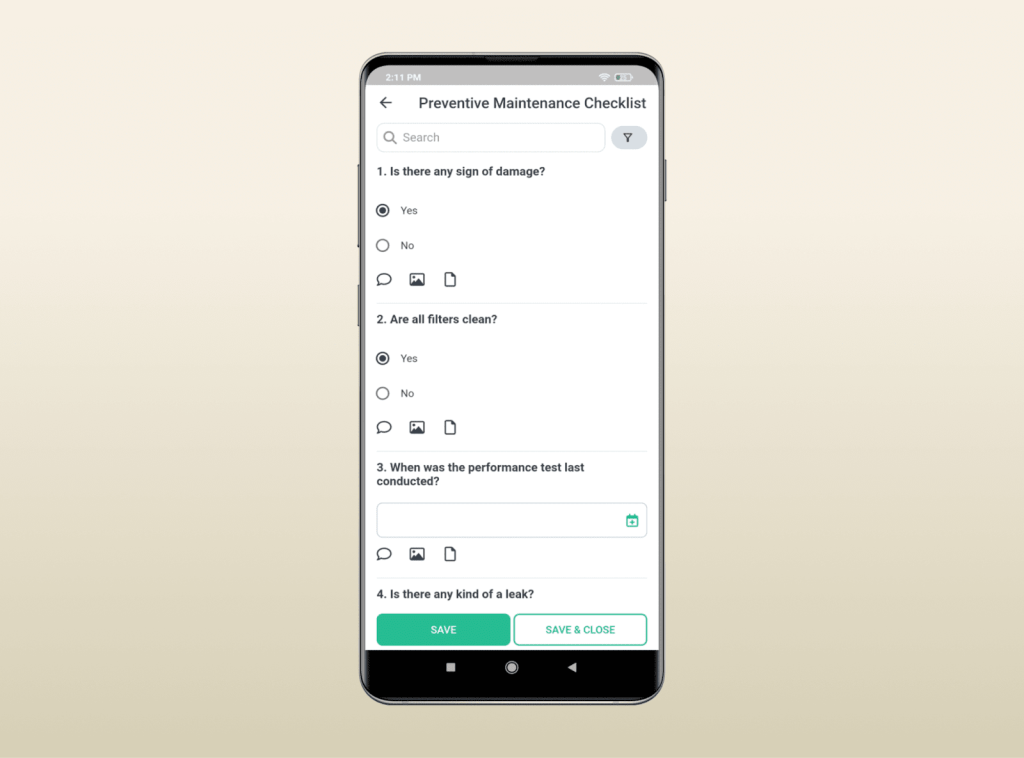
Additionally, inventory tracking prevents over-ordering while ensuring critical tools, components, and materials are always available—avoiding last-minute, high-cost purchases.
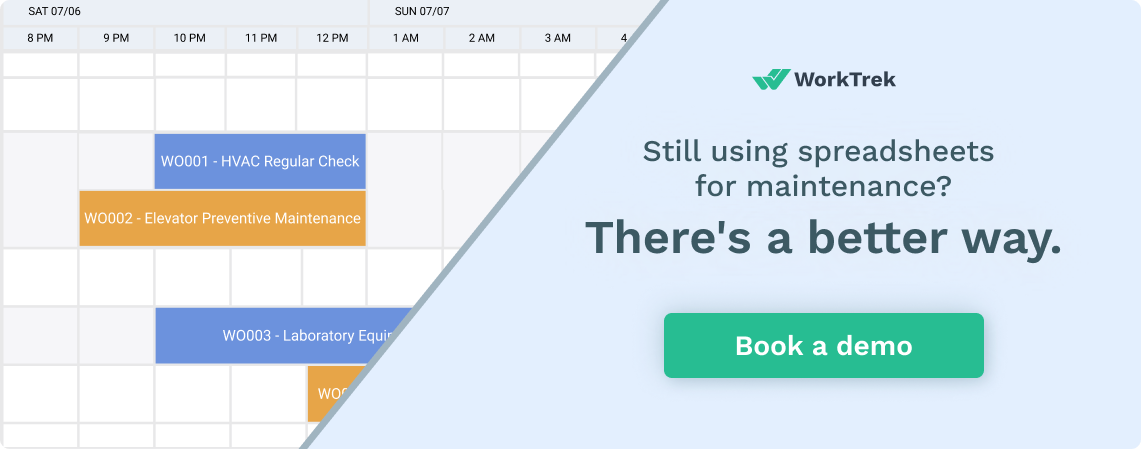
Cost savings also come from better resource allocation.
With real-time tracking, managers can optimize technician workloads, reducing overtime costs and unnecessary callouts.
Lastly, detailed reporting enables you to analyze maintenance spending, spot inefficiencies, and make data-driven decisions to cut costs further.
By combining these capabilities, work order software helps you track, control, and optimize maintenance expenses, driving significant long-term savings.
Improved Customer Response Time
All the benefits we’ve discussed work together to improve response times for service requests, resulting in higher productivity, better service, and increased customer satisfaction.
This applies whether your “customers” are employees within your company or external clients if you provide maintenance services to other businesses.
In either case, work order software automates request submission, approval, and task assignment, significantly reducing response times.
As mentioned above, customers can easily submit service requests using any device with the app installed.
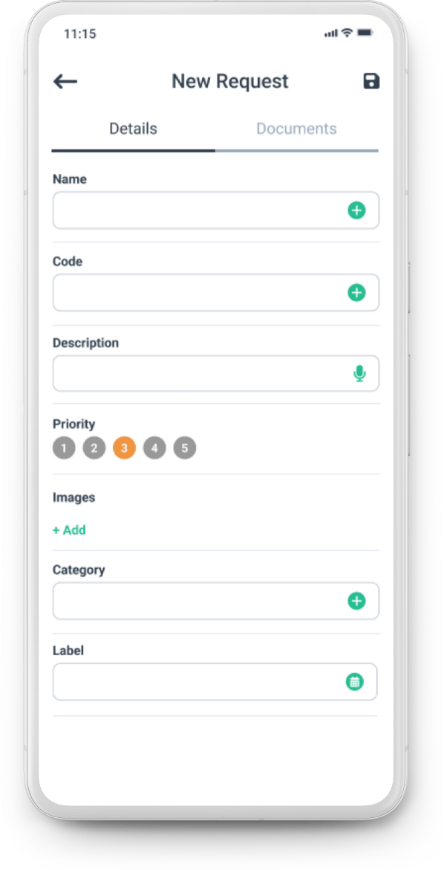
They can describe the problem and attach photos or relevant documentation for more context, ensuring managers receive all the necessary details instantly.
This allows managers to:
- Quickly review and approve requests
- Generate work orders
- Assign tasks to technicians
- Set priorities
Managers can immediately dispatch technicians for high-priority requests, ensuring urgent repairs are addressed without delays.
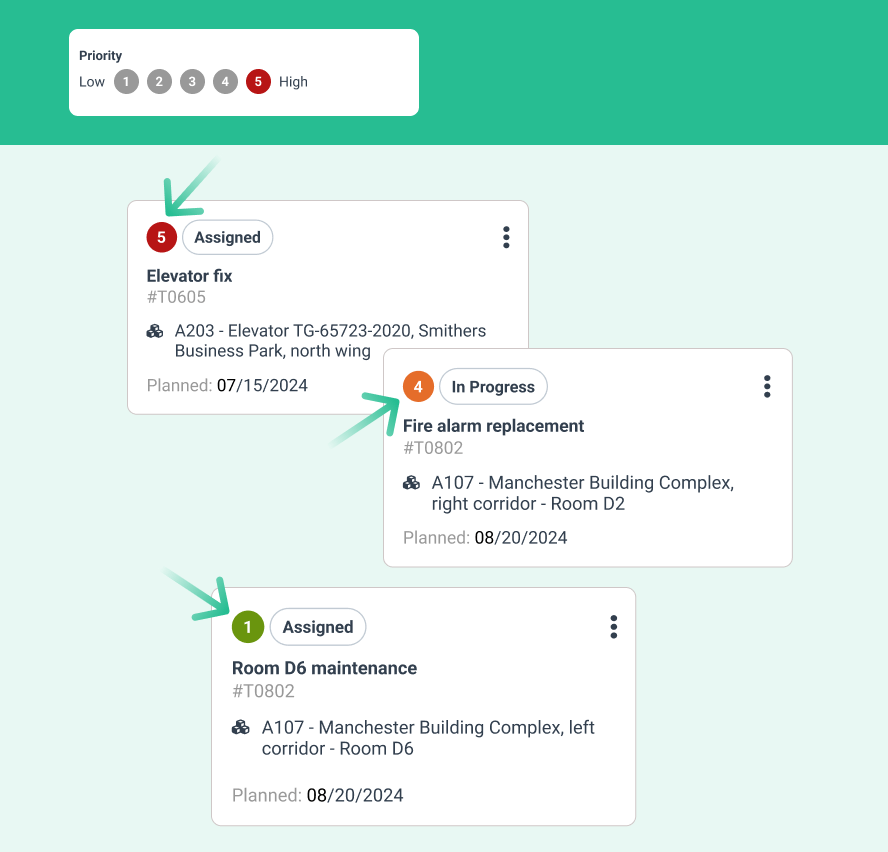
Additionally, your team and customers can track job progress, estimated completion times, and updates through the app—improving transparency and trust.
For facility management companies, this leads to better adherence to Service Level Agreements (SLA).
Managers can monitor response times and ensure maintenance tasks are completed within the agreed SLAs.
Work order management software streamlines request handling and task management, leading to faster responses, better operational reliability, and greater customer satisfaction.
Seamless Adaptation to Your Business Needs
As your business expands, so does the volume of work orders, users, and assets needing maintenance.
Cloud-based software is designed to scale with your business, allowing you to handle more work without any performance issues.
Whether you add new locations, hire more technicians, or handle more service requests, the system seamlessly adapts to your needs.
WorkTrek is one of those systems.
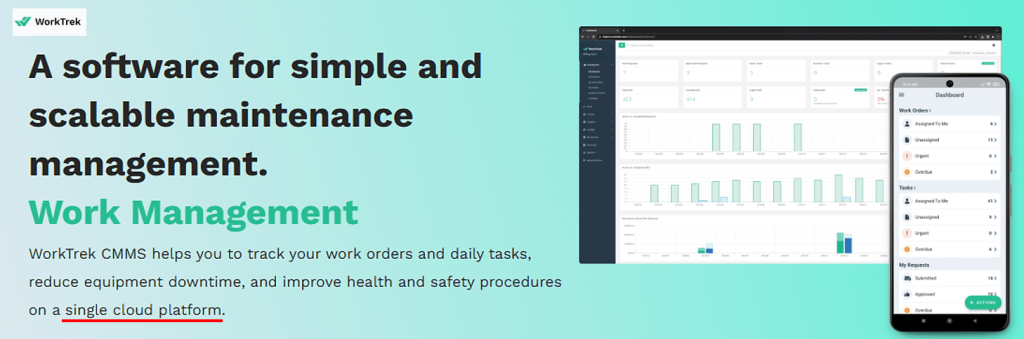
In addition to its strong work order management features, WorkTrek integrates with other business systems, such as ERP, CRM, and inventory management platforms.
These integrations eliminate the need for duplicate data entry and ensure that maintenance, inventory, and procurement functions are in sync.
With all systems connected, you can centralize maintenance data, improving visibility into resource availability, costs, and performance.
This also leads to more detailed and comprehensive work order reports.
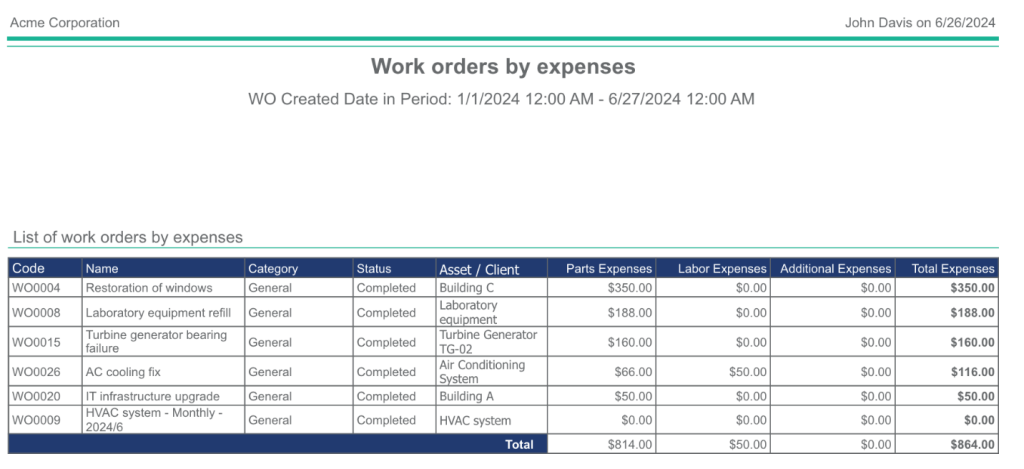
On top of that, mobile access takes work order management to the next level.
With cloud-based software, technicians and managers can process work orders, update job statuses, upload photos, and communicate directly from their mobile devices in real time.
This reduces paperwork, streamlines coordination, and speeds up task completion.
Cloud-based work order management software ensures that your maintenance operations are flexible, efficient, and future-proof by offering scalability, integration, and mobile accessibility.
Conclusion
Work order management software can transform your maintenance operations for the better.
The benefits are clear, from automating workflows and optimizing resource allocation to reducing maintenance costs.
Its scalability and integration capabilities also ensure your system can grow with your business.
Outdated processes just aren’t viable anymore.
Adopting digital work order management is the key to boosting efficiency, saving costs, and preparing your operations for the future.