Get a Free WorkTrek Demo
Let's show you how WorkTrek can help you optimize your maintenance operation.
Try for freeKey Takeaways:
- More than half of facilities rely on reactive maintenance.
- Preventive and predictive maintenance reduce asset failures.
- Over-servicing equipment can lead to damage.
- Skipping maintenance for new assets can void warranties.
Have you ever been told to wait until something breaks to fix it or that new assets don’t need to be maintained regularly?
These widespread misconceptions can lead to inefficient practices and unnecessary downtime.
That’s why today, we’ll debunk six common asset maintenance myths.
The truth will empower you to make smarter decisions for more efficient asset maintenance.
Let’s get started!
Reactive Maintenance Is Enough for Equipment Reliability
Many teams still depend on reactive strategies, believing this ensures equipment reliability.
Also called run-to-failure, this practice is common, with over half of facilities using it to manage their assets.
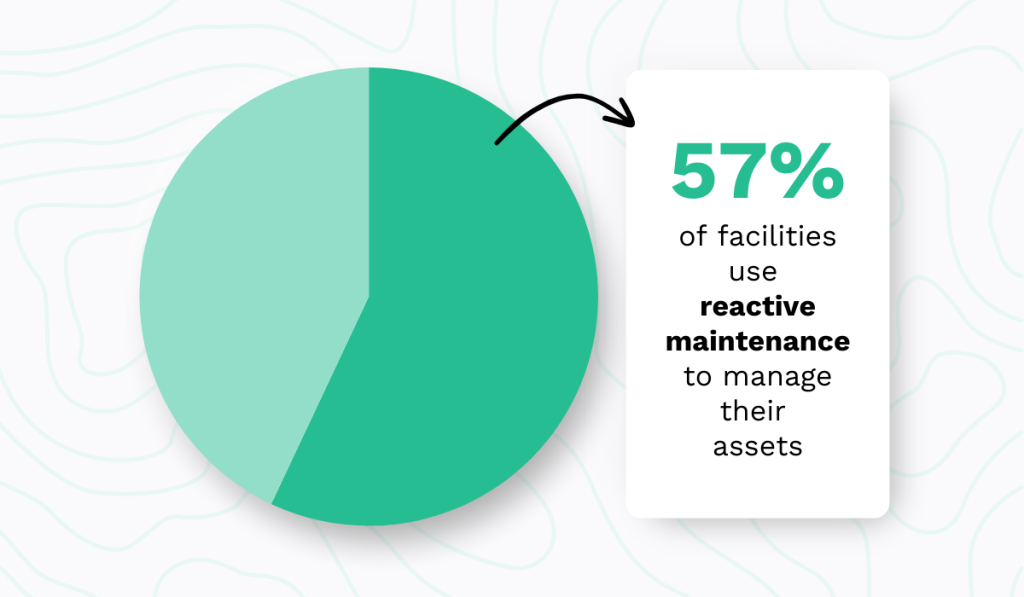
While reactive maintenance can be suitable (and is more recommended) for non-critical, inexpensive assets that are easy to replace, the problem arises when it’s the only strategy.
Unfortunately, the same study reveals that reactive maintenance is the only maintenance program for 5% of facilities.
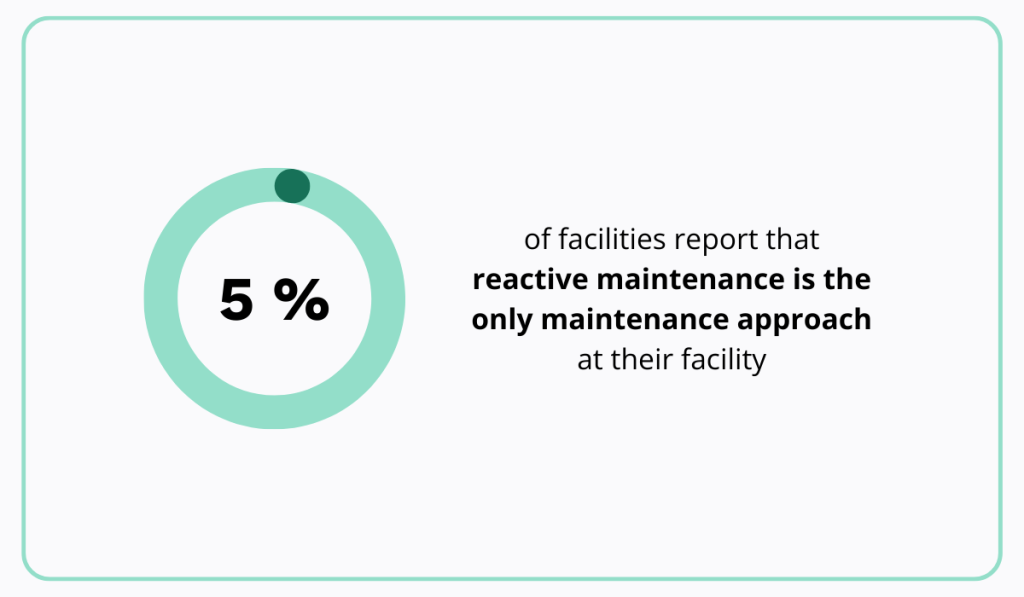
However, relying exclusively on reactive maintenance has significant drawbacks.
Unplanned failures result in costly downtime, repairs, and shorter asset lifespans.
Additionally, sudden breakdowns can create hazardous conditions for workers, especially in environments involving heavy or complex machinery.
Proactive maintenance is a far better solution.
Preventive strategies focus on scheduled upkeep to avoid failures, while predictive maintenance (PdM) uses advanced tools to predict issues before they happen.
Both approaches significantly reduce downtime, extend assets’ life, and create safer working environments.
On top of that, it’s easier to coordinate teams when maintenance is planned and scheduled, as one maintenance manager points out:
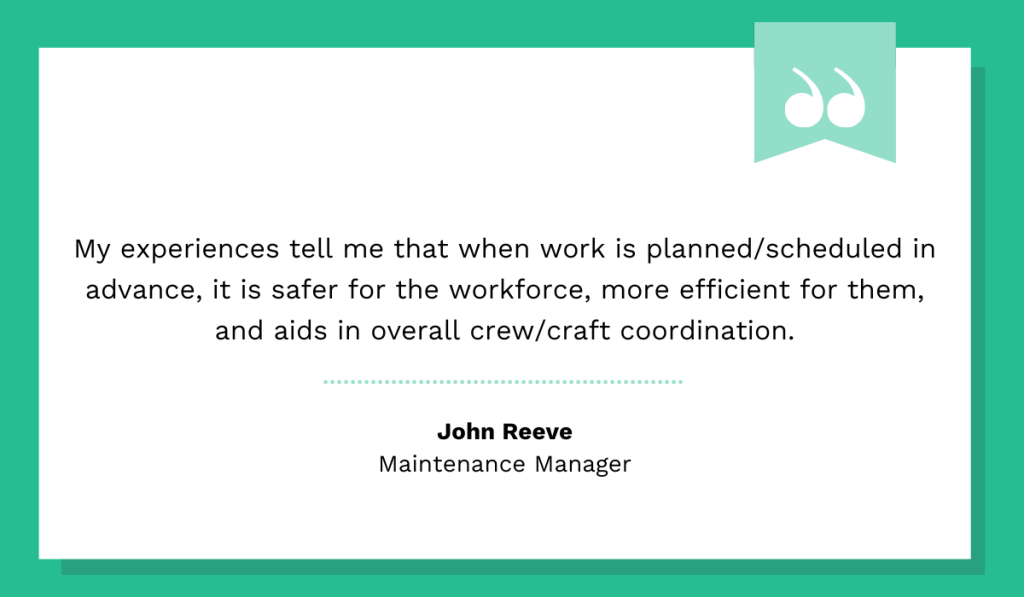
The data also confirms the numerous benefits of proactive maintenance.
A survey by Advanced Technology Services and Plant Engineering Magazine from 2020 found that about 70% of respondents reported lower asset failure risks and downtime when using predictive or preventive maintenance.
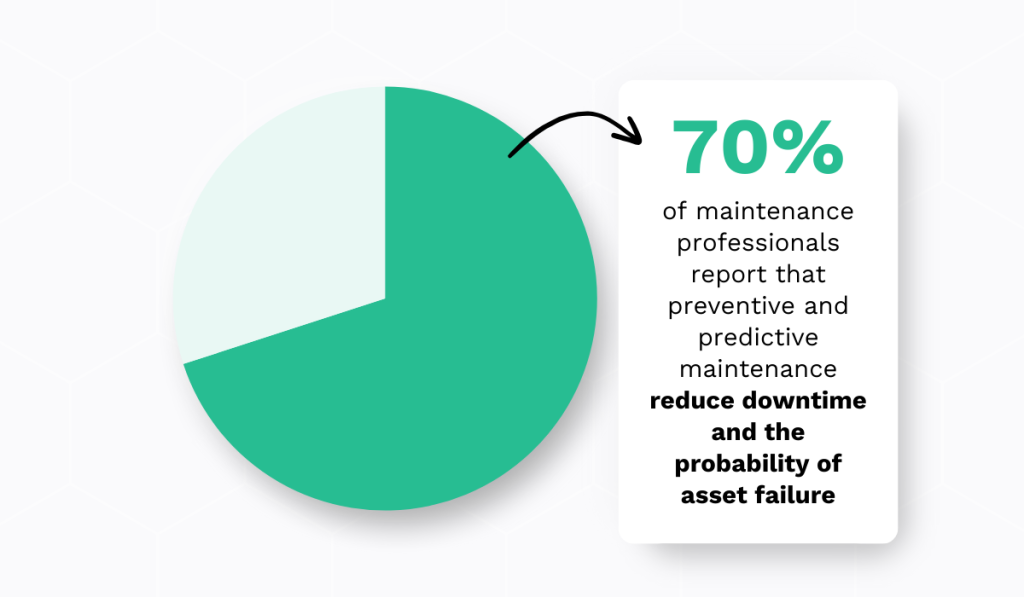
These methods offer a smarter, more efficient path forward, proving that reactive maintenance alone is no longer sufficient for maintaining equipment reliability.
More Maintenance Is Always Better
Some professionals mistakenly believe that more maintenance is always better and that frequent interventions improve equipment performance.
However, over-maintaining assets often has the opposite effect.
Excessive maintenance wastes resources, drives up costs, and even causes unnecessary wear and tear on components, shortening their lifespan.
Duncan Aviation, a privately owned business jet service provider, illustrates this clearly.
In aviation, over-servicing engines by repeatedly topping off oil can damage gearbox seals, causing leaks and visible streaking on engine cowlings.
In this case, over-servicing does more harm than good, unnecessarily grounding aircraft and inflating costs.
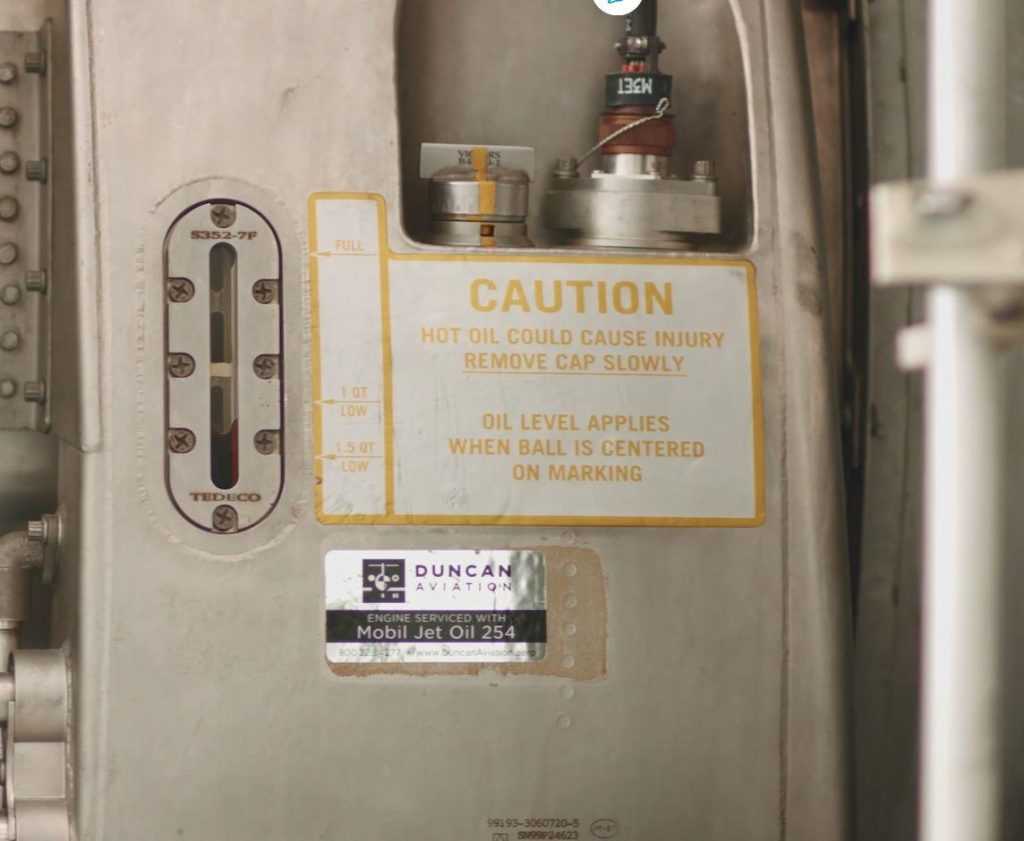
The better approach is data-driven maintenance, where the actual needs of the equipment guide decisions.
Tools like condition monitoring and predictive analytics allow maintenance teams to assess these needs.
Industries like aviation and manufacturing demonstrate the importance of data-driven maintenance.
For instance, GE Aerospace, a world leader in jet and turboprop engines, uses advanced data analytics to avoid unnecessary maintenance and ensure its engines work perfectly.
Patrick Ketelaar, former Principal Engineer at Remote Monitoring & Diagnostics and current GEnx-2B Product Leader, explains their mission:
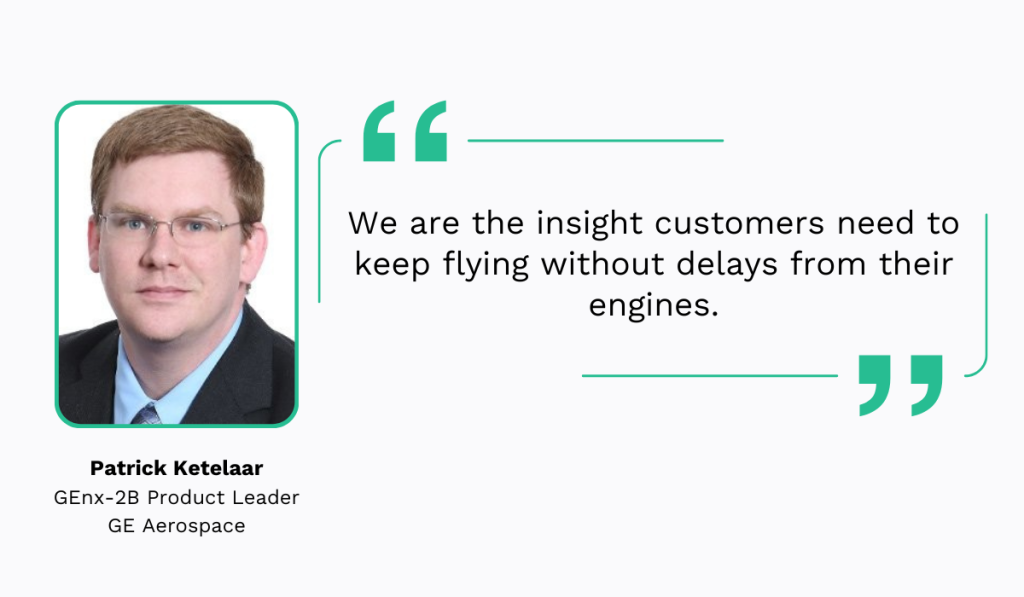
Through real-time monitoring and diagnostics of over 38,000 jet engines, their system identifies potential issues such as abnormal exhaust gas temperatures or oil usage trends.
When issues are detected, they immediately notify their customers (airlines) to act.
This timely and data-driven approach to maintenance prevents the wear and tear caused by excessive maintenance while saving airlines millions of dollars annually.
In the end, the most effective maintenance is not about doing more but about doing what’s needed when it’s needed.
Data-driven strategies help balance the scale.
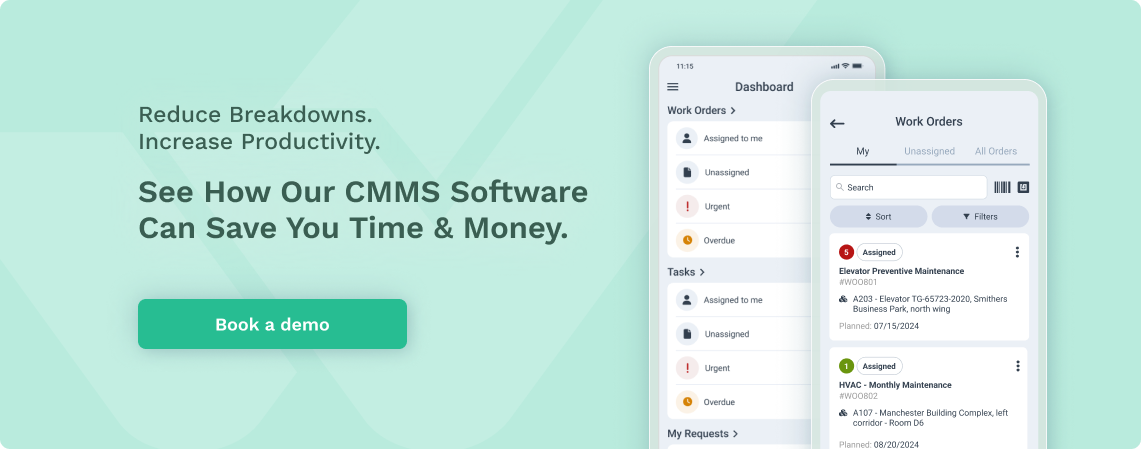
Preventive Maintenance Guarantees Zero Failures
Preventive maintenance is a proven strategy for reducing equipment failures but not eliminating them.
Even with strict schedules and adherence to manufacturers’ guidelines, unforeseen issues can still happen.
For instance, a manufacturing plant might follow rigorous preventive maintenance for its motors but experience an unexpected failure due to electrical surges or material fatigue that weren’t detectable during routine checks.
GE Aerospace brings another example in this context.
In one case, mechanics addressed an issue flagged by routine maintenance (higher than normal nacelle temperatures), but they couldn’t find the cause:
Without knowing specifically what was causing the higher temperature, the issue wasn’t found by mechanics right away.
Fortunately, in this case, continuous data monitoring identified a pressure line leak as the cause of abnormal temperatures.
Once the faulty component was replaced, the engine performance returned to normal.
So, to address the limitations of preventive maintenance, many companies are turning to predictive tools, data analysis, and condition monitoring for more efficient processes.
From telematics in fleets to vibration analysis in wind turbines or thermal imaging in HVAC systems, predictive tools complement preventive maintenance and fill the gaps it cannot address.
Tim Richards, equipment manager at Sargent, a contractor from Maine, highlights this advantage for their company:
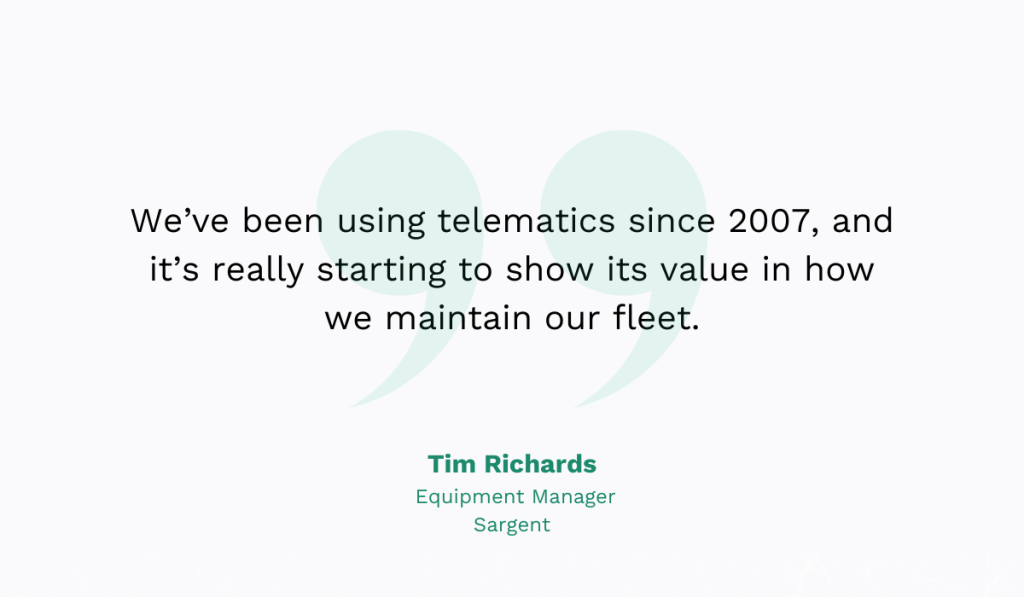
One of Sergent’s key strategies is using HCSS Equipment360, a telematics solution integrated into most of its equipment.
It provides real-time data on machine performance, fault codes, and service intervals, helping them better maintain vehicles and reduce unexpected downtime.
Ultimately, no maintenance strategy can eliminate failures.
However, combining preventive maintenance with predictive tools and condition monitoring is the best defense.
New Assets Don’t Need Maintenance
The belief that new equipment requires no maintenance is a costly misconception.
While it might seem logical that brand-new assets will perform flawlessly, skipping maintenance early on can still lead to unexpected breakdowns, reduced performance, and even warranty voids.
Manufacturers often specify maintenance schedules to honor warranties, making routine maintenance non-negotiable.
And they also look for maintenance records.

So, not following their guidelines and not keeping records could result in repairs or replacements being denied under warranty, increasing your costs significantly.
Take conveyor systems as an example.
Even for a brand-new conveyor belt, regular maintenance is vital.
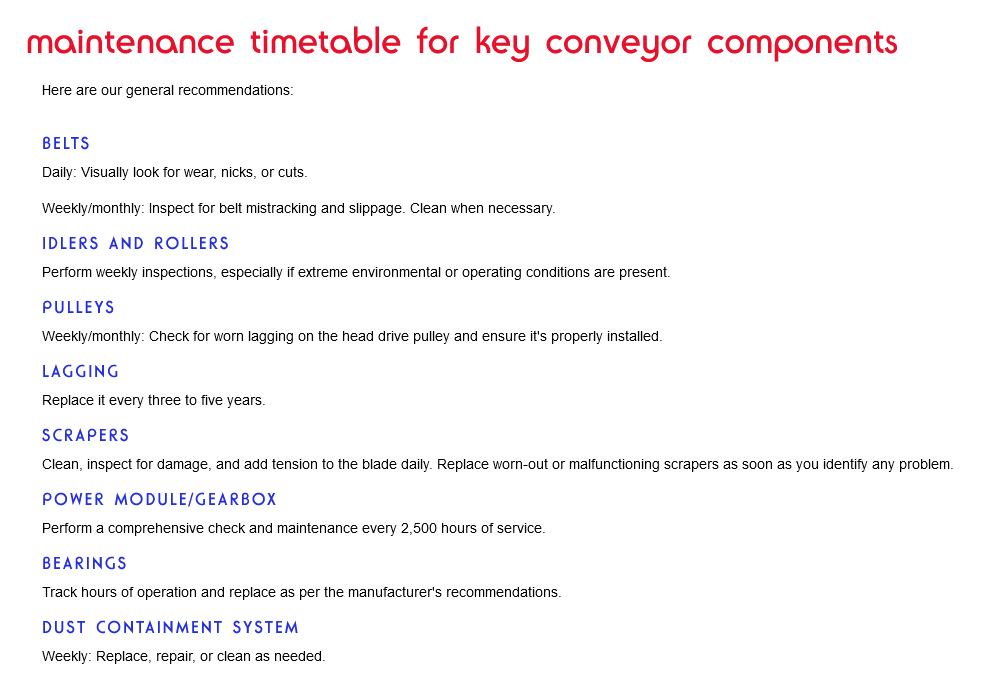
Daily inspections to identify wear, nicks, or cuts in belts are essential to prevent damage.
Weekly or monthly checks for belt mistracking, slippage, and scraper blade tension are also critical to ensure the system functions smoothly.
Refrain from following these steps even if the conveyor system is brand-new could result in early failures, such as misaligned belts causing excessive wear or even catastrophic breakdowns that halt production.
The assumption that “it’s new, so it doesn’t need attention” could cost businesses dearly in downtime and repair expenses.
The truth is that maintenance of new assets should begin even before assets are installed in your facility.
Mark Lamendola, an expert in maintenance management, agrees:
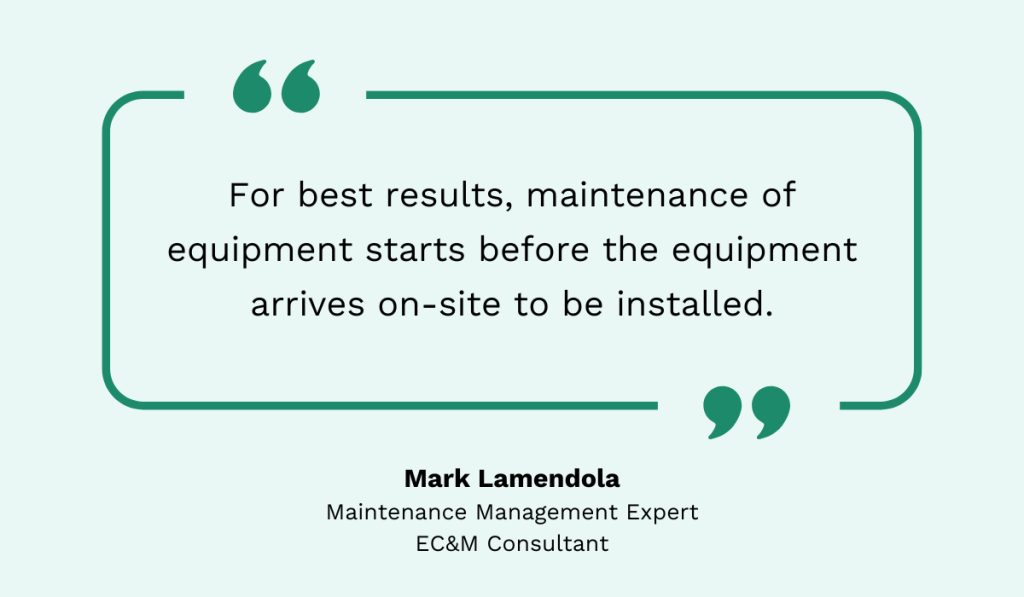
He has preparatory tasks in mind, such as entering assets into a CMMS, scheduling manufacturer-recommended maintenance, and collecting baseline data.
These simple tasks lay the groundwork for effective future maintenance.
For example, performing initial maintenance at start-up will give you a benchmark for detecting performance changes during subsequent checks.
Conversely, lacking it can leave you with baseline data, making it easier to identify abnormal wear trends.
All in all, maintenance from day one protects your investment, ensures compliance with warranties and sets the foundation for a longer and more reliable asset lifecycle.
Don’t skip it.
Spare Parts Should Always Be on Hand
When a machine breaks down and spare parts are unavailable, production halts, costs rise, and downtime can stretch longer than necessary.
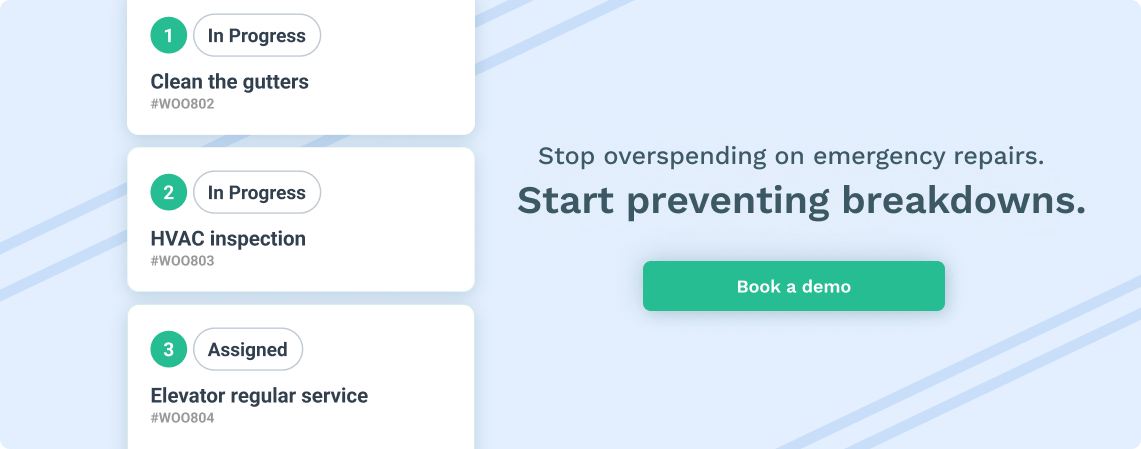
But should you keep a hundred extra bearings or fifty couplings on the shelf, just in case?
Absolutely not.
While critical spares should be available, overstocking ties up capital and increases storage costs.
And yet, many maintenance professionals fall into this trap, as noted by Dr. Anthony Kenneson-Adams, a former Royal Air Force Senior Engineering Officer:
Too often I see 5 years’ worth of bearings or couplings on a shelf while the maintenance manager is struggling to find the budget to buy some other component or service.
The smarter approach is to adopt an optimized inventory strategy based on asset criticality and demand.
Dr. Kenneson-Adams further advises identifying critical assets and establishing true min/max in your storeroom.
Here’s what he suggests:
- Start by identifying your critical assets through an asset criticality assessment.
- Classify spare parts into critical, essential, and non-critical categories.
- Use tools like failure mode and effects analysis (FMEA) or failure reporting and criticality analysis (FRACAS) to prioritize which spares truly need immediate availability.
- Leverage reliability data, such as mean time between failures (MTBF) and mean time to repair (MTTR), to refine stock levels.
- Use inventory management techniques like just-in-time (JIT) and establish clear minimum/maximum thresholds for each spare.
Besides, CMMS like WorkTrek can alert you when inventory levels drop below predefined thresholds.
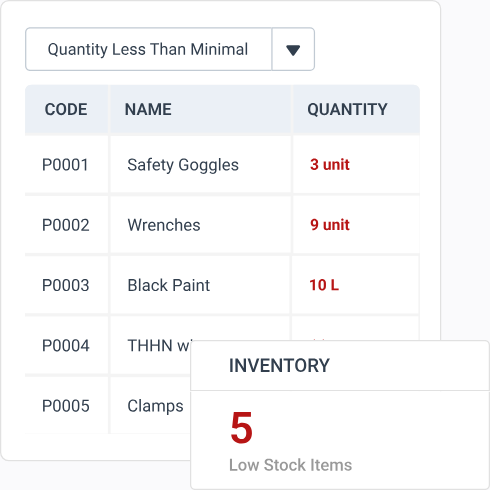
This way, you can streamline inventory management and ensure spare parts are ordered on time.
CMMS also stores all your maintenance data, so you can more accurately predict future spare parts needs.
These helpful CMMS benefits bring us the last myth we must debunk today.
CMMS Isn’t a Necessity
One of the biggest myths in maintenance management is that a computerized maintenance management system (CMMS) is unnecessary.
Many businesses believe they can manage without a CMMS, often due to misconceptions such as:
- Some feel that CMMS solutions are too expensive, especially for small companies.
- Others worry about the time and effort needed to train staff
- Or fear they’ll need costly hardware upgrades.
- Employees may also be reluctant to switch from familiar processes to something new.
- Some believe that CMMS platforms are complex and hard to use.
While these points may seem valid, they’re far from the reality of today’s CMMS solutions.
Implementing a CMMS requires time and resources, but today’s systems are designed to be user-friendly and scalable.
Modern CMMS solutions, especially cloud-based ones like WorkTrek, require minimal infrastructure.
WorkTrek can, for example, be accessed from devices you already have—whether a desktop, tablet, or smartphone.
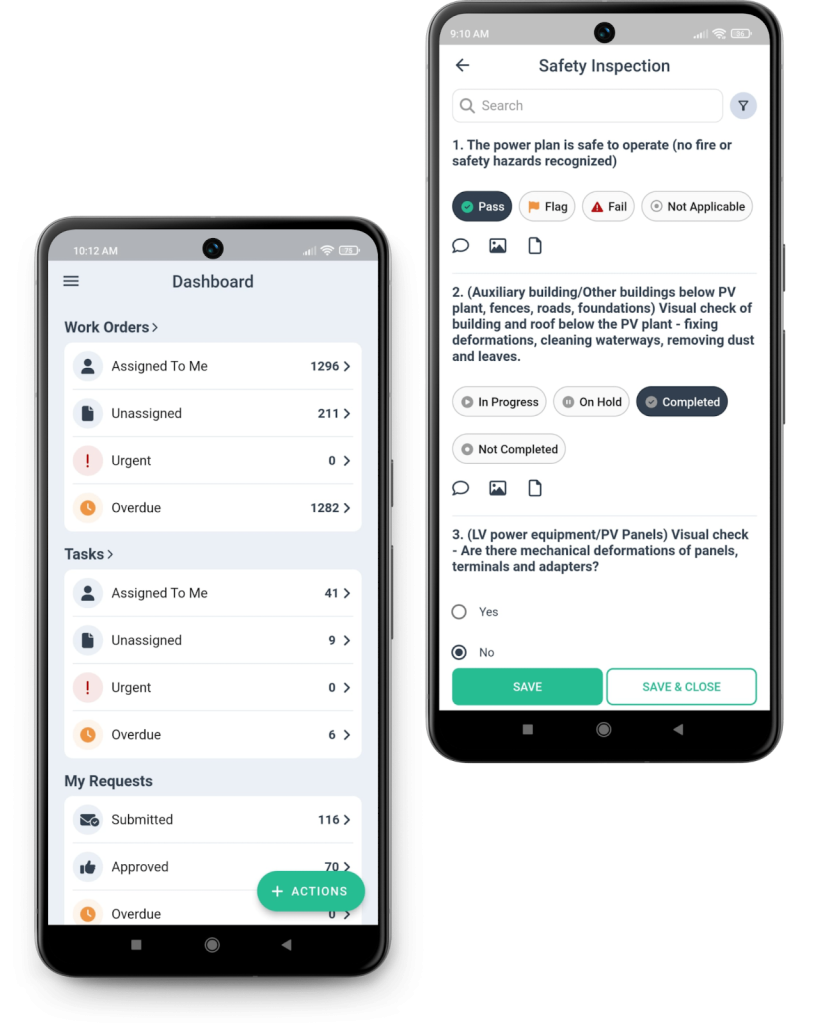
With subscription-based pricing models, the upfront cost is often lower than expected, and companies can pay only for the sets of features they need, making it an affordable option.
The actual value of a CMMS lies in its ability to streamline operations, enhance work order tracking, minimize downtime, and support data-driven decisions.
Additionally, a CMMS lets you easily plan and schedule preventive maintenance.
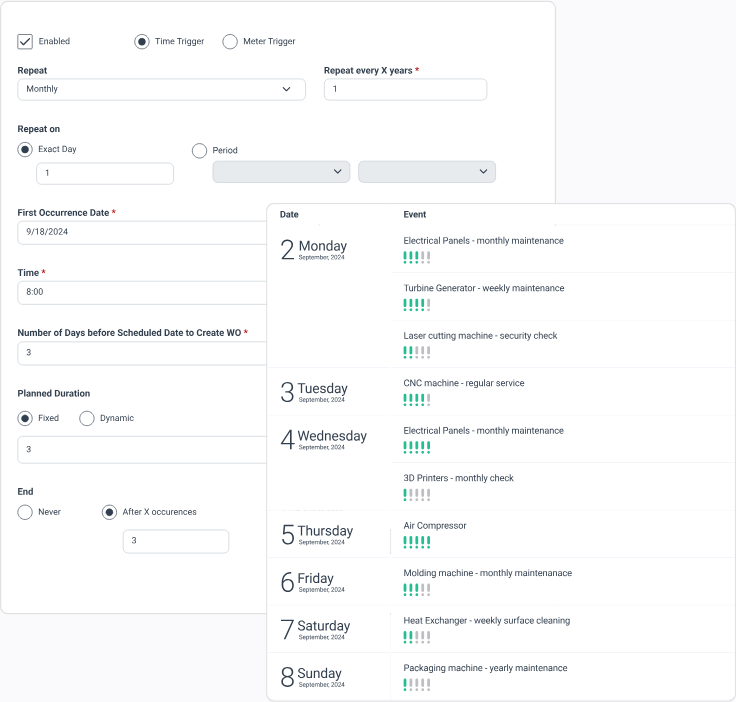
A well-implemented CMMS improves technician safety by providing clear, detailed maintenance instructions, safety hazards, PPE requirements, etc.
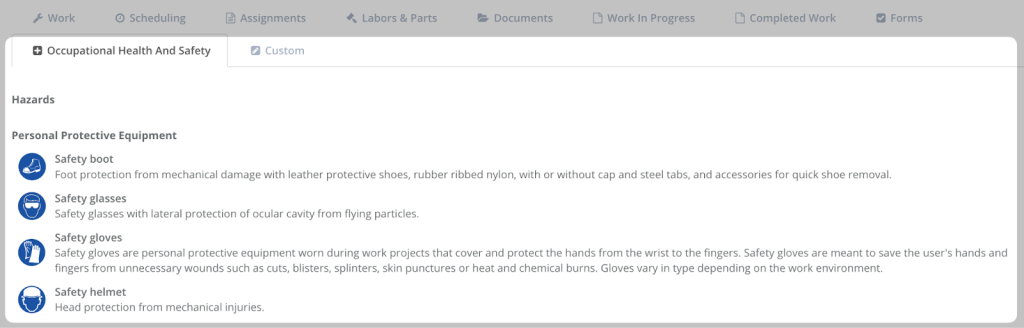
All these benefits together far outweigh the initial investment and effort.
But don’t just take our word for it.
According to the ATS study, 74% of companies using a CMMS say it boosts their productivity.
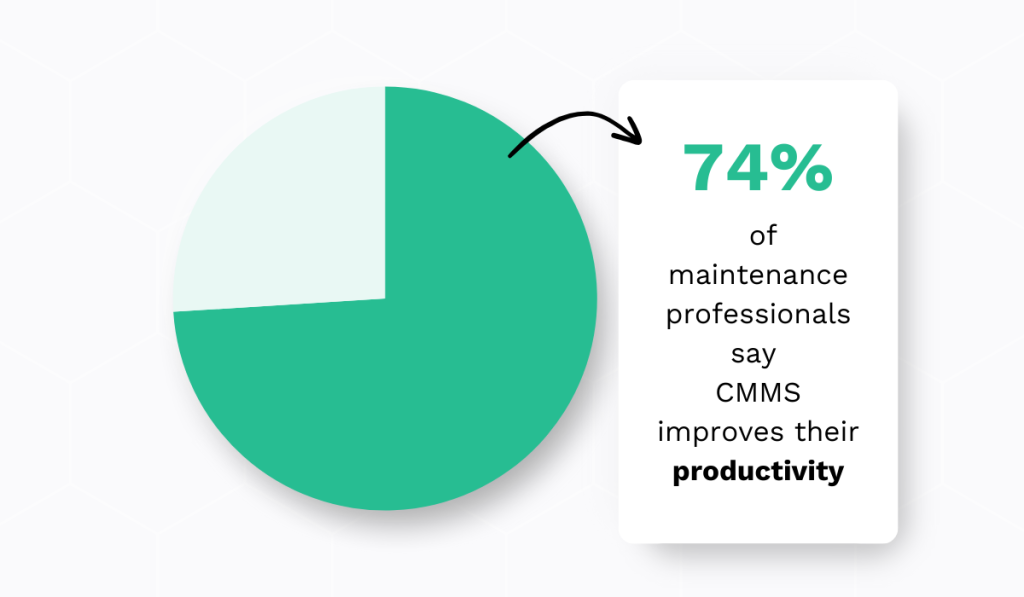
Moreover, at least half of them say that a CMMS improves OEE, overall efficiency, safety, flexibility, usability, and uptime and has good ROI overall.
Given all this, a reliable CMMS is becoming a real necessity.
Conclusion
How many of these asset maintenance myths have you encountered or unknowingly believed?
If even one, it’s time to rethink your approach.
The truth is that effective maintenance strategies don’t just reduce costs—they also create a safer work environment.
It’s time to leave the myths behind and take control of your asset maintenance.