Get a Free WorkTrek Demo
Let's show you how WorkTrek can help you optimize your maintenance operation.
Try for freeFacility maintenance is what maintenance managers do to keep buildings and machines in good shape. It’s an important job. Without it, things can break down and cause big problems. This article covers the different types of facility maintenance.
Illustration: WorkTrek / Data: Camcode
Preventive Maintenance
One type is called preventive maintenance. This means you don’t wait for something to break. Instead, you take care of it regularly to keep it running smoothly. It’s like going to the doctor for checkups, even when you feel fine.
Examples of preventive maintenance include:
- Regularly changing HVAC filters
- Inspecting and tightening electrical connections
- Lubricating mechanical parts like door hinges and motors
- Cleaning and calibrating manufacturing equipment
- Pressure washing exterior surfaces of buildings
- Inspecting the roof and plumbing for leaks
Illustration: WorkTrek / Data: Present Status and Future Growth of Advanced Maintenance Technology and Strategy in US Manufacturing
Preventive maintenance is usually scheduled based on time, meter readings, or other triggers. For example, an HVAC system may be serviced every spring and fall, a generator may be inspected every 200 hours, and light bulbs may be replaced on a set schedule based on expected lifetime.
Preventive maintenance takes time and money upfront. But it can save you from expensive emergencies later. It’s a smart way to make things last longer.
Corrective Maintenance
Corrective maintenance is the opposite. You wait until something breaks, then you fix it.
This is also called “run-to-failure.”
Examples of corrective maintenance include:
- Repairing an HVAC system that stops working
- Replacing a burst pipe or leaking toilet
- Fixing a broken conveyor belt that halts production
- Changing a flat tire on a company vehicle
- Replacing burned-out lights or broken switches
- Patching a pothole in a parking lothnk k
Illustration: WorkTrek / Data: Fluid Life
Corrective maintenance seems cheaper at first, but it’s risky. You never know when something will fail, and it could cause big disruptions. Repairs can also cost more than preventing the problem.
It works best for things that aren’t too critical. You can let them run until they break.
Just don’t rely on this method for everything. It is best used selectively in combination with other proactive maintenance methods.
Predictive Maintenance
Predictive maintenance is high-tech. It uses sensors and computer programs to guess when a failure will happen. Then, you can fix it before it breaks.
Here’s how it works:
- Sensors track things like vibration, heat, and power use
- Computer programs look for patterns that signal trouble
- Maintenance is scheduled at the best time to prevent failure
Analytics tools identify anomalies and forecast the remaining useful life of assets so that maintenance can be scheduled proactively.
Illustration: WorkTrek / Data: Linkedin
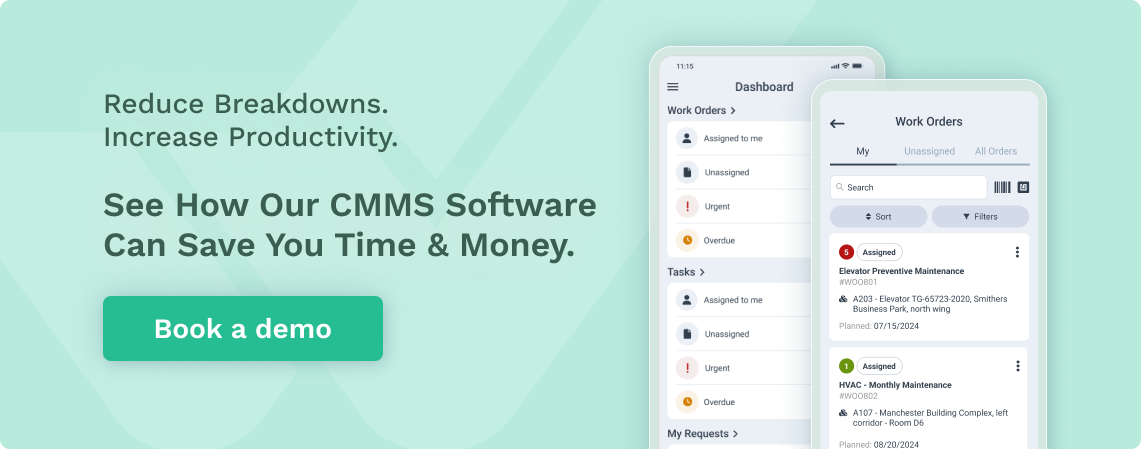
Examples of predictive maintenance include:
- Analyzing vibration data to detect misalignment in rotating equipment before it causes damage
- Using thermal imaging to identify electrical hotspots that indicate loose connections or overloaded circuits
- Monitoring energy usage to detect HVAC performance degradation over time
- Installing sensors on critical pumps to identify seal leaks or bearing wear
- Tracking vehicle mileage and engine data to optimize preventive maintenance schedules
Predictive maintenance can be very effective. But it requires investing in smart technology. It’s best for critical assets that are worth the extra effort.
Predictive maintenance also requires an upfront investment in sensors, data collection, and analysis tools.
To take advantage of the data, a high level of organizational maturity is also needed.
Not all assets are worth instrumenting. Predictive maintenance is best applied to mission-critical assets with a long lifespan.
Condition-Based Maintenance
Condition-based maintenance is similar to predictive maintenance. However, it depends on periodic or continuous assessments rather than advanced analytics to determine when action should be taken.
Maintenance is triggered when equipment performance falls below a pre-defined threshold.
Source: WorkTrek
Examples of condition-based maintenance include:
- Sampling fluids like engine oil and hydraulic fluid to monitor viscosity and contamination levels
- Using ultrasonic testing to measure pipe wall thickness and detect internal corrosion
- Tracking the efficiency of an HVAC chiller to spot refrigerant leaks or heat exchanger fouling
- Doing periodic vibration analysis on pumps and motors to identify developing bearing faults
- Measuring pressure drops in filters to know when they need changing
Condition-based maintenance works on equipment only when needed without the cost and complexity of a predictive maintenance program.
It balances the hands-off approach of run-to-failure with the scheduled preventive maintenance approach.
Condition monitoring can be done with handheld instruments, periodic inspections, or fixed online sensors.
The main advantage of condition-based maintenance is that it aligns maintenance with actual equipment needs. This can prevent unnecessary work before intervention is required.
Reliability-Centered Maintenance
Reliability-centered maintenance (RCM) takes a big-picture view. It looks at each piece of equipment and asks seven key questions:
1. What are the functions and performance standards of the asset?
2. How can it fail to fulfill its functions?
3. What causes each functional failure?
4. What happens when each failure occurs?
5. What are the consequences of the failure?
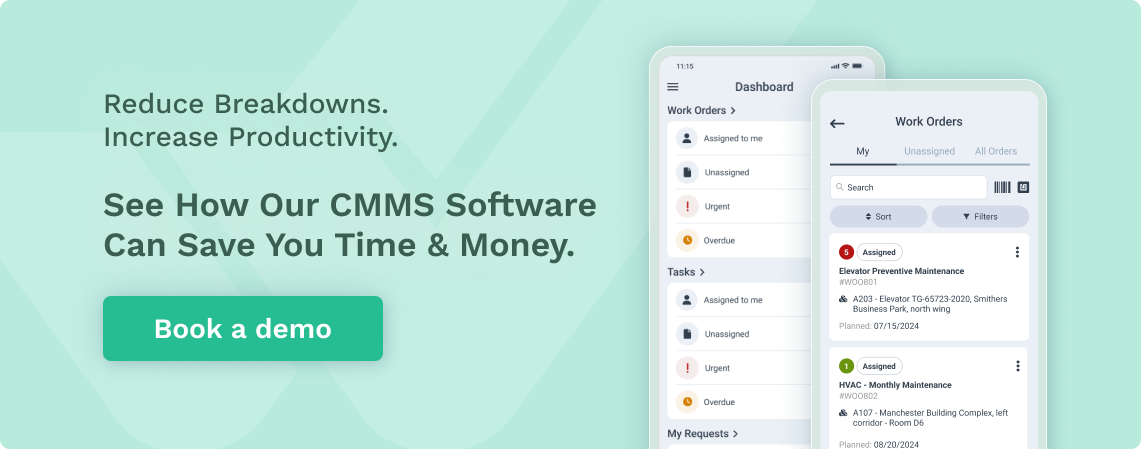
6. What can be done to prevent or predict the failure?
7. What should be done if no proactive task is appropriate?
Source: WorkTrek
RCM uses the answers to create a master plan. The plan mixes preventive, predictive, condition-based, and run-to-failure approaches. Each asset receives the maintenance that best suits it.
For example:
- A spare backup pump can be allowed to run to failure
- A main pump that’s critical to production gets sensors for predictive maintenance
- An easy-to-replace fan gets essential preventive maintenance
- A finicky conveyor belt gets frequent condition checks
RCM takes a lot of work, but it pays off for facilities requiring reliability. It ensures everything is covered.
For instance, a centrifugal pump in an office building may be deemed to have minimal impact if it fails, so it is allowed to run to failure.
But a pump supporting a critical industrial process would be subject to vibration analysis and periodic servicing to prevent disruptions.
RCM produces a comprehensive maintenance plan across all of an organization’s assets.
It is a highly structured approach to determining the right mix of reactive, preventive, predictive, and condition-based maintenance.
Conclusion
So those are the main types of facility maintenance. Each one has its place. Reactive maintenance is cheap but risky. Preventive maintenance reduces failures but might do too much.
Predictive and condition-based maintenance are efficient but require investment. Reliability-centered maintenance gives you the complete package.
Source: WorkTrek
The key is to match the method to your needs. Think about what’s most important for your facility. Is it saving money upfront, preventing disruptions, or extending equipment life?
Let that guide your maintenance mix. With the right blend, you can keep things humming.