Get a Free WorkTrek Demo
Let's show you how WorkTrek can help you optimize your maintenance operation.
Try for freeIndustrial maintenance is surprisingly dynamic, with constant innovations and developments emerging.
This article highlights seven essential facts you need to know about this rapidly changing sector, with support from real-world data, expert insights, and examples.
There’s so much to discover—so let’s get started.
Global Industrial Maintenance Market Should Double In Size By 2031
According to data from Allied Market Research, the global industrial maintenance services market is projected to grow significantly, from $49 billion in 2021 to $85.5 billion by 2031.
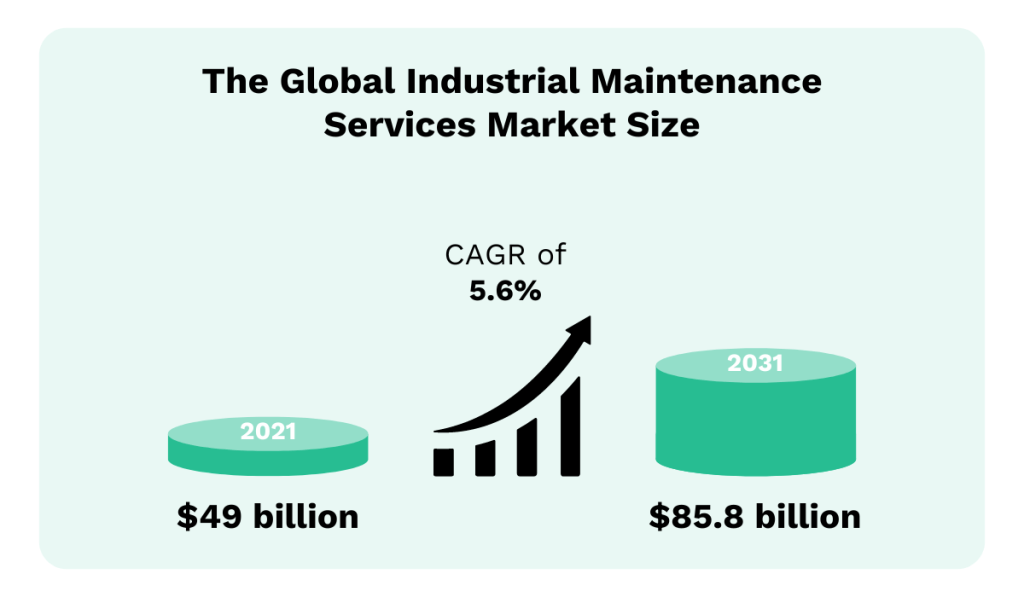
A major factor driving this growth is the increasing complexity of machinery and industrial facilities.
As facilities grow and their equipment becomes more sophisticated, they’re outpacing what internal teams can handle, says Aaron Merkin, CTO of Fortive, an American industrial technology conglomerate.
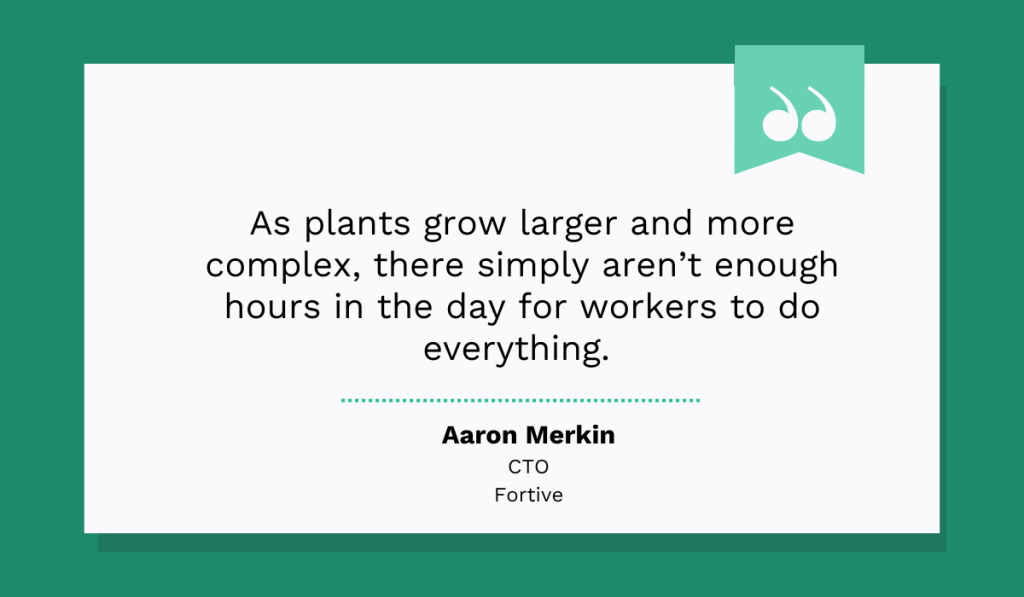
That’s why more and more companies are turning to third-party service providers.
They bring cutting-edge technology like AI and the specialized workforce needed to keep company assets running smoothly.
And when facilities leave upkeep to experts, they can focus on their core activities.
The reason so many industrial businesses are scaling up in the first place is the rise in demand for their services.
This demand is fueled by bigger forces like population growth and globalization, which ramp up the need for everything from electricity to air travel to healthcare services.
To keep up, companies simply must scale up their operations.
Maintenance service providers naturally follow suit. After all, more machines means more upkeep.
Just take New York-based maintenance provider InLine Aviation Group, for example.
They recently introduced a maintenance subscription program called UpAssist, designed to help general aviation companies manage their increasingly complex equipment.
Eric Faulkner, the company’s CEO, highlights how this program will be a huge game-changer for all maintenance directors.
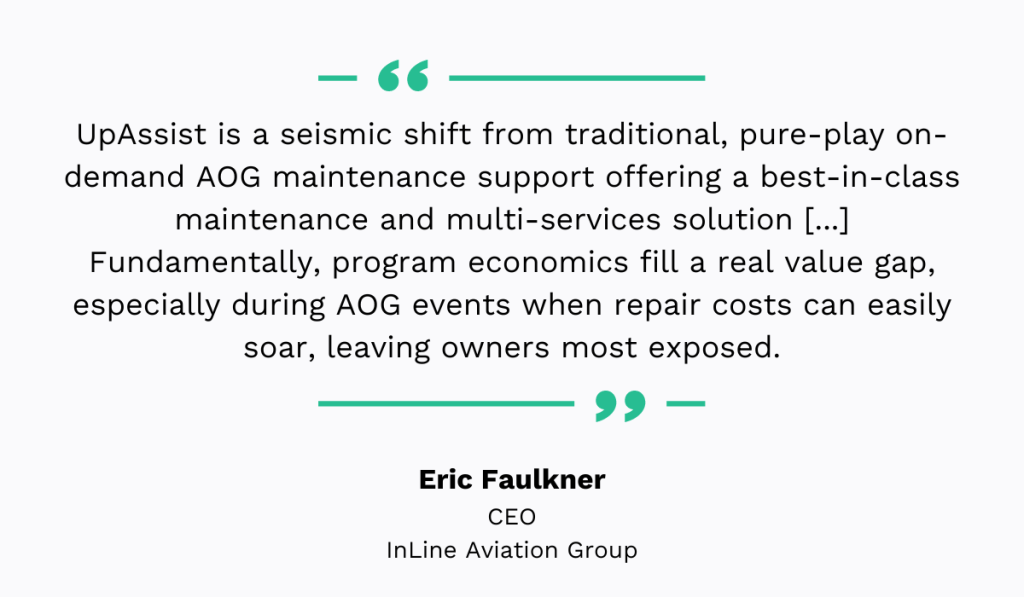
This is just one of many such service providers emerging across all industries.
Overall, as industrial businesses expand, the need for reliable, tech-enabled upkeep services is growing—and the market is responding.
The Aerospace Sector Fuels Industrial Maintenance Growth
The expanding aerospace sector is a key driver of growth in the industrial maintenance services market.
According to Spherical Insights & Consulting, the global aircraft maintenance market is projected to expand significantly, from $88.7 billion in 2023 to $139.4 billion by 2033.
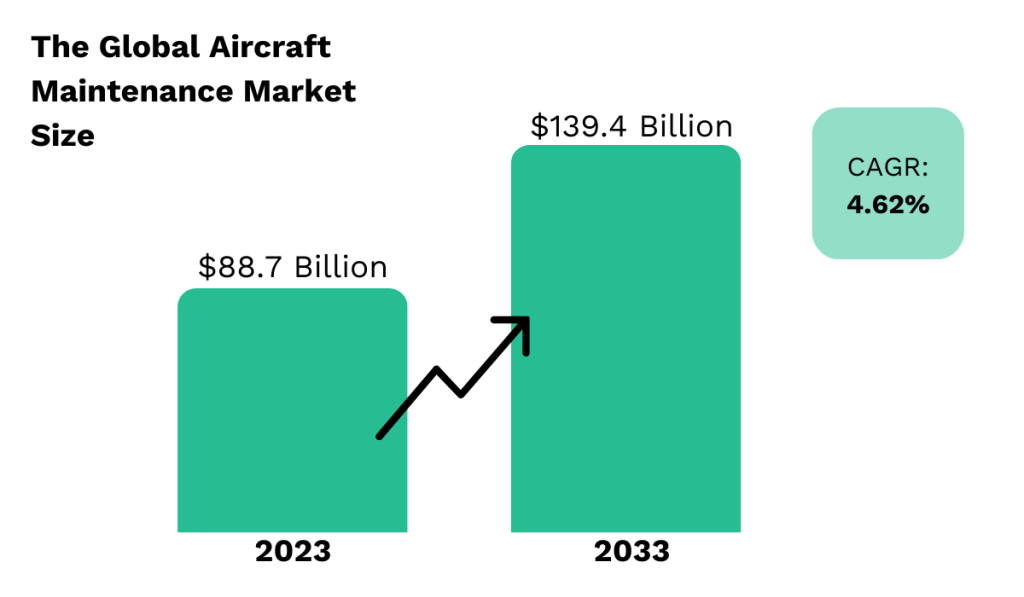
Besides the increase in air travel, what else is fueling this growth?
It’s the rise of Industry 4.0, pushing companies to adopt various advanced technologies to boost the efficiency of their upkeep process.
For instance, Delta Airlines recently became the first U.S. commercial operator to receive FAA approval to use camera-based drones for inspections.
These semi-autonomous drones, or small unmanned aircraft systems (sUAS), are developed to capture images around the airplane without any manual input from a pilot.
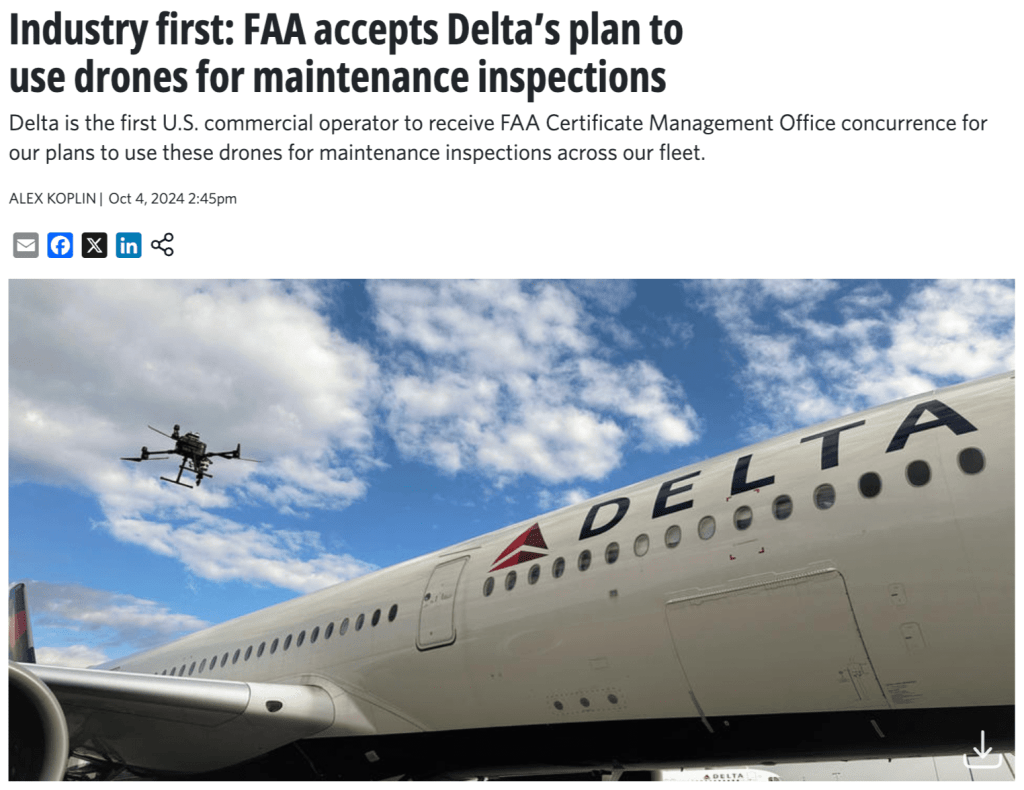
TechOps technicians and inspectors analyze drone images to assess airworthiness before the plane returns to service.
This technology is supposed to reduce the risk of injury for maintenance personnel and is even expected to expedite condition assessments by up to 82%.
As it evolves, it becomes a staple in aircraft upkeep.
In addition to the increased demand for new technologies, aging airliner fleets are another major factor driving the growth of plane maintenance.
Many old airplanes are still in operation and are not yet due for retirement.
However, they require much more frequent and intensive maintenance to stay in service.
As Benjamin Murray, President & CEO of aviation services company Skyservice Business Aviation Inc., points out, even sourcing spare parts for these aging aircraft is challenging.
At the end of the day, whether it’s an old helicopter or a brand-new private jet, the need for aircraft upkeep is constant and expensive.
That’s why it’s no surprise that the aerospace sector has a massive role in expanding industrial maintenance services.
Aircraft Maintenance Workers Remain Too Prone to Injury
From fire hazards and electrical shocks to falls and harmful chemicals; workers are exposed to numerous risks during aircraft upkeep.
Unfortunately, news headlines frequently highlight the dangers involved in the maintenance process.
For example, in 2019, a British Airways employee suffered a severe brain injury and spent three weeks in a coma after falling from a platform in a maintenance hangar.
A subsequent investigation by the Health and Safety Executive (HSE) revealed that the company had failed to assess risks and replace safety barriers properly.
As HSE inspector Sara Lumley, notes, the accident was entirely preventable:
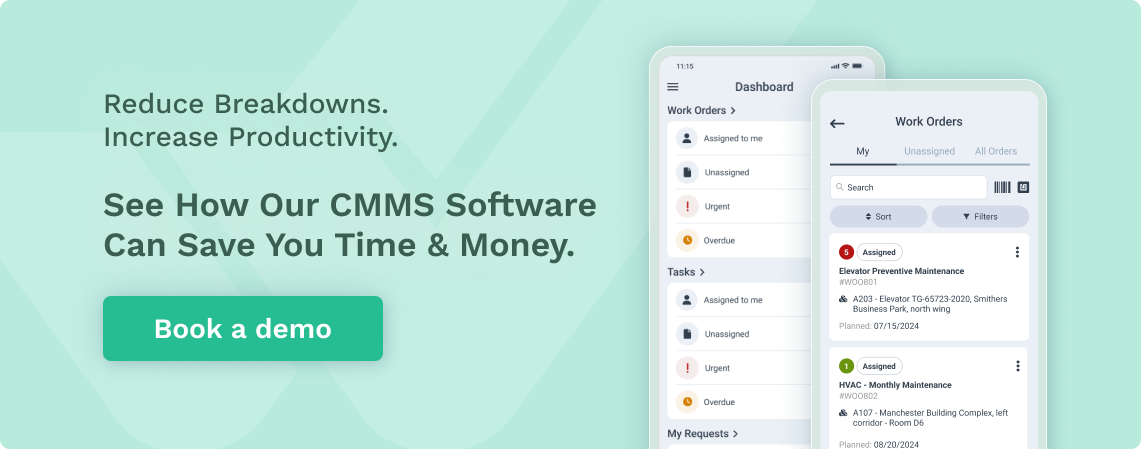
This incident could so easily have been avoided by simply carrying out correct control measures and safe working practices.
Then, there was another incident in Singapore the next year, where a 63-year-old worker at SIA Engineering Company fell from a height while working on an aircraft.
Here, investigators from The Ministry of Manpower (MOM) also found considerable gaps in the company’s work procedures and risk controls.
However, this company is not the only one that has experienced such problems.
In 2021, another accident occurred when a technician’s foot was crushed by a Boeing 737 during a towing operation at Newark Liberty International Airport, resulting in the amputation of five toes.
According to Joseph Czapik, Area Director at U.S.DOL-OSHA, it was United Airlines’ failure to enforce safety standards that led to the incident:
United Airlines could have prevented an employee from suffering a debilitating injury had the company followed its safety procedures for towing a jet weighing as much as 50 tons.
All these stories share a common theme: inadequate safety protocols.
This is a prevalent issue in aircraft upkeep, often stemming from deficiencies in training, communication, or policy enforcement.
However, there are signs of improvement in the industry, with better training, stricter policies, and enhanced risk control practices becoming more widespread.
One promising development comes from AETC Safety, which collaborated with aircraft maintenance experts to roll out a standardized Operational Risk Management (ORM) process.
Col. Will Phillips, director of AETC Safety, believes this will provide technicians with a practical, hands-on tool for assessing and minimizing risks before performing critical tasks.
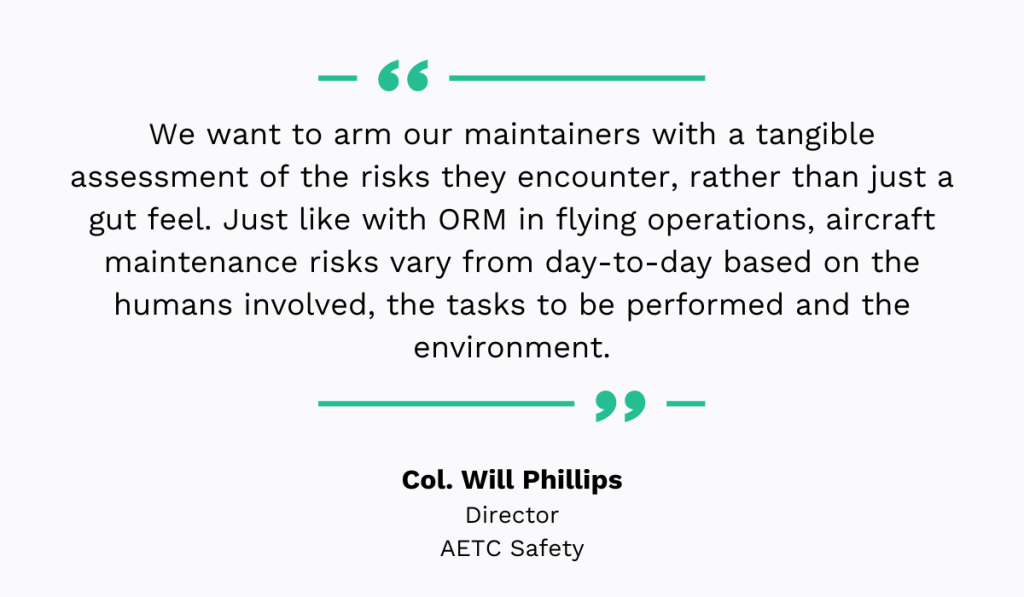
The bottom line is this: aircraft upkeep is and will always be dangerous.
While technological innovations like drones and robots make the process somewhat safer, the human element still plays a significant role.
Workers must exercise caution and follow proper procedures—and it’s up to companies to make sure they do.
Medical Equipment Maintenance is Growing at 10.51% CAGR
Medical equipment maintenance is another sector experiencing significant growth.
According to Precedence Research, based on projections, it will expand from $51.84 billion in 2023 to approximately $155.92 billion by 2034.
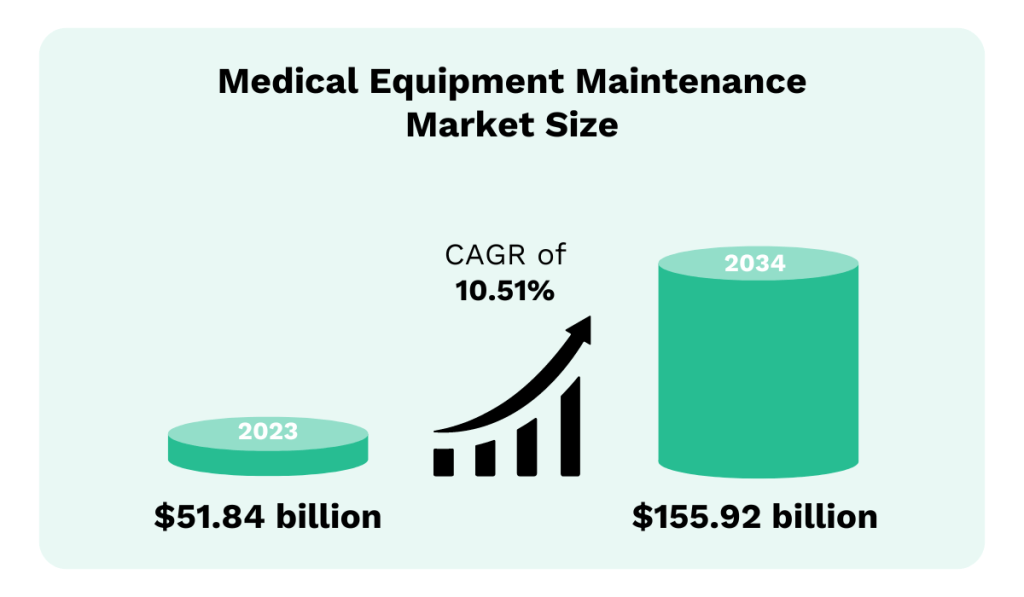
Several growth factors drive this trend and are all closely interconnected.
In a discussion with Outsourcing Pharma, Jiresh Patel, Co-Founder of UptimeHealth, a software startup that provides predictive analytics for medical equipment, explains what they are:
- The increase in the number of medical devices in healthcare
- The growing complexity of equipment
- The rising adoption of IoT and connected devices
Like many other industries, healthcare organizations are scaling up to meet rising demand, which means they are purchasing more equipment.
At the same time, this equipment is getting more complex, making it harder to maintain.
This complexity requires companies to invest more in skilled maintenance technicians who can adequately handle these valuable assets.
In response to these challenges, we see a growing demand for advanced maintenance technologies, particularly IoT systems, because they are designed to make asset monitoring, servicing, and management much more efficient.
Just take GE Healthcare’s OnWatch™ Predict, for example.
This system leverages healthcare IoT technology and AI to analyze real-time asset data and deliver actionable insights to its users.
The solution can track all metrics, from environmental factors (like temperature and humidity) to compressor status, Helium levels, and cryocooler efficiency in MR magnets.
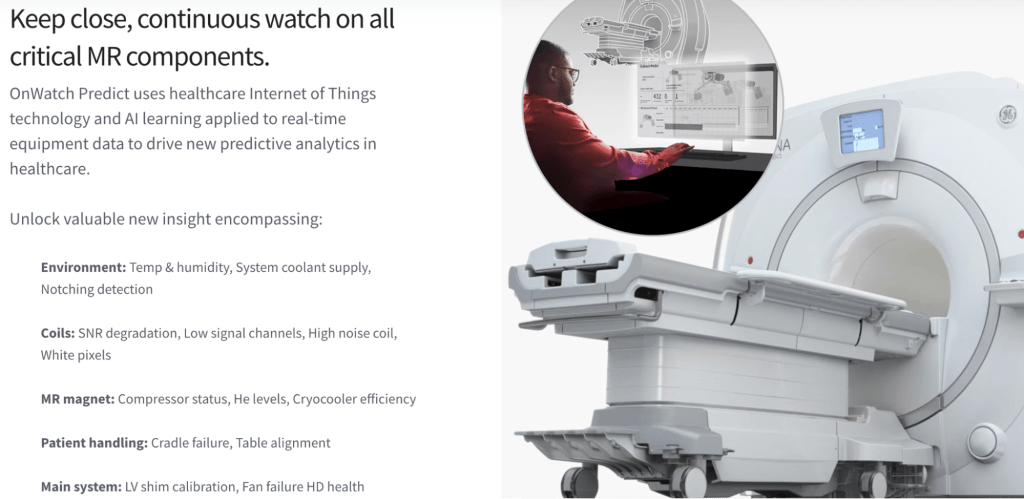
The system analyzes the data and forecasts issues before they occur.
This enables upkeep personnel to make timely repairs and replacements, drastically reducing unplanned downtime.
When you tie all these factors together, it becomes clear why healthcare facilities are expected to invest more and more in maintaining their assets.
It’s simply unavoidable if they want to ensure continued reliability within their operations.
The U.S. Leads in Technological Innovation and Adoption
According to Grand View Research, the U.S. leads in industrial maintenance tech innovation and adoption.
One possible reason for this could be the global competition that pressures U.S. companies to stay ahead.
Countries like Japan, China, and Germany are strong competitors, especially in the automotive, electronics, and aerospace sectors.
U.S. organizations must invest in advanced technologies that ensure equipment reliability and smooth production processes to maintain their edge.
But the competition isn’t just global—it’s local, too.
To put things in perspective, IBIS World reports that, as of 2023, there are over 600,000 manufacturing businesses in the U.S., growing at an average of 1.1% per year since 2018.
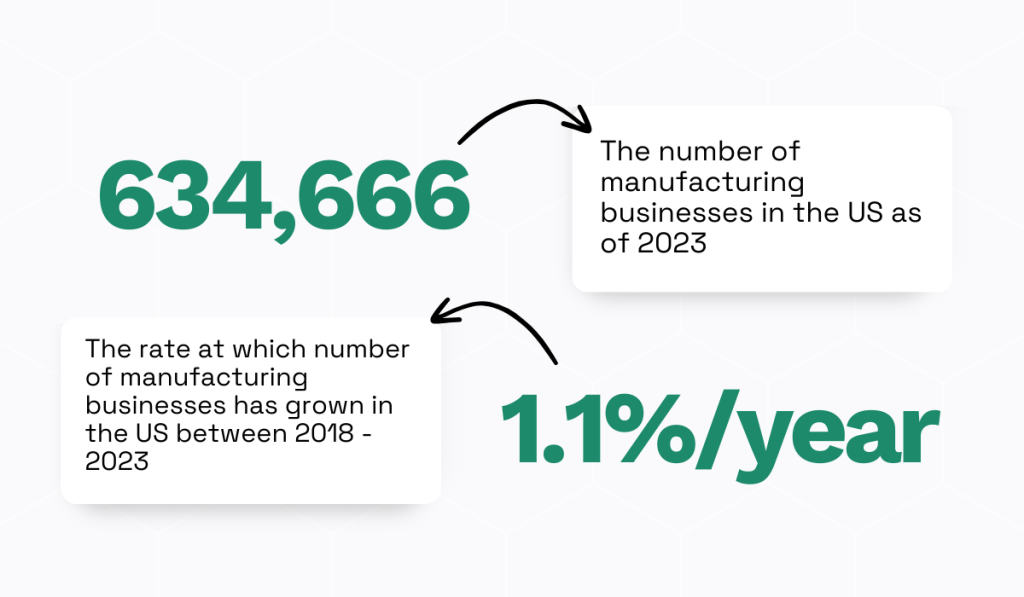
With many new players every year, it’s no surprise the need to innovate and stand out has become almost ingrained in the culture.
The combination of such a mindset and a robust economic infrastructure forces tech leaders to keep innovating.
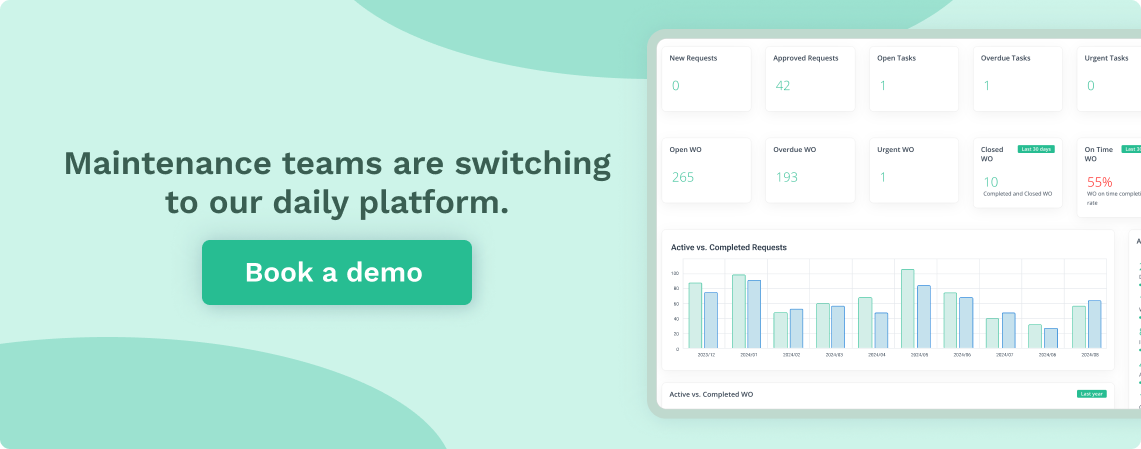
And the industrial maintenance industry is particularly ripe for innovation.
Let’s explore some of the exciting advancements happening in this space.
The Industrial Maintenance Service Market Keeps Innovating
Industrial maintenance innovations are primarily focused on making maintenance more efficient, cost-effective, and faster.
One example comes from CreaForm, which created the first portable, self-positioning 3D laser scanner.
Their 3D handheld scanners are currently used by Fleet Maintenance Facility Cape Breton (FMFCB) to improve ship upkeep and manufacturing.
The devices can capture the details of a ship component with incredible accuracy—up to 0.040mm—which helps the organization create digital twins of complex shapes.
Moreover, the data captured by these scanners can be used to design and 3D print component prototypes.
Below, you can see the quarter turn sector gear prototype FMFCB created using the CreaForm scanner data.
Thanks to this technology, the company saves time and money.
Here’s a quote from Si Thu Naing, supervisor of the Drawing Office within FMFCB’s Naval Architecture subsection:
By streamlining the repair process and reducing downtime, 3D scanning helps FMFCB reduce costs and avoid unnecessary delays due to the supply chain, enabling us to promptly respond to operational requirements of the RCN while ensuring vessels return to service faster.
Now, this is just one example of innovations among many others.
With such groundbreaking technologies entering the field, one thing is certain: the future of this sector should be exciting.
IIoT Is a Leading Trend in Industrial Maintenance
Among all these emerging technologies, the Industrial Internet of Things (IIoT) stands out.
IIoT refers to interconnected sensors, instruments, and other devices that collect, exchange, and analyze asset data to optimize maintenance.
As Rajesh Ramachandran, Global Chief Digital Officer & MD at ABB Process Automation, notes, these systems are most commonly used for predictive maintenance.
Predictive maintenance has always been the topmost critical use case of Industrial IoT, as this is where we see the combination of data, domain expertise, IoT platform, and AI. With a combination of these four critical aspects, predictive maintenance enables manufacturers to predict anomalies in their plants—be it in terms of equipment health, performance, reliability, or operational parameters well in advance.
With IIoT-enabled sensors, upkeep teams gain detailed insights into asset health, allowing them to address equipment problems and prevent unscheduled downtime proactively.
At the same time, they minimize the risk of over-maintenance because upkeep is performed only when necessary.
One example of an IIoT startup is SEW-Eurodrive, which recently showcased its DriveRadar IoT Suite at the Tire Technology Expo 2024.
This solution uses high-precision sensors and advanced machine learning to monitor critical mechanical parameters of industrial gear units.
Its algorithms can pinpoint exactly where issues might arise, providing real-time asset health updates through a web application or mobile app.
Sascha Nagel, Industry Segment and Account Manager at SEW-Eurodrive elaborates:
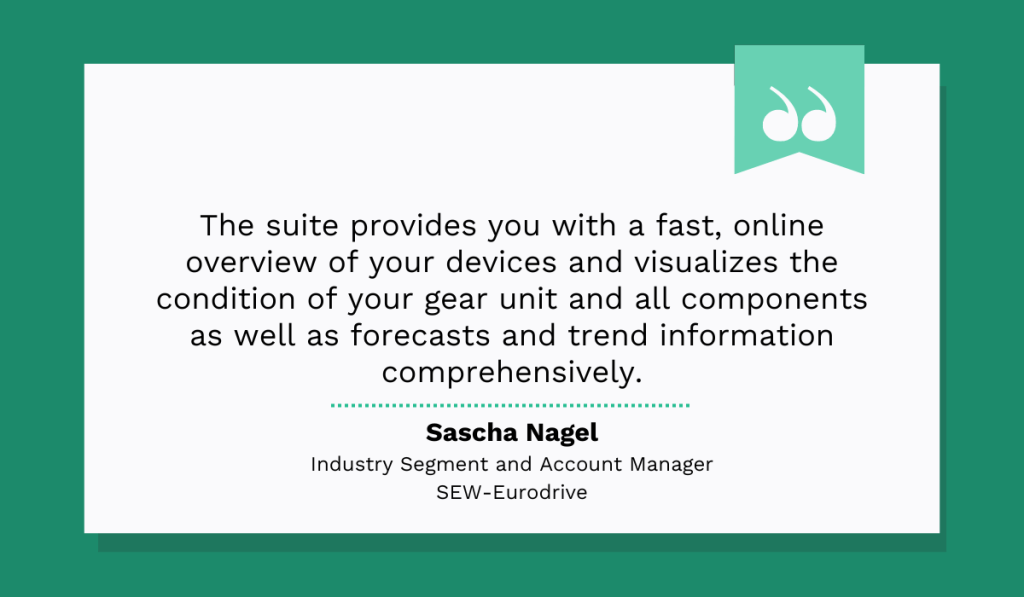
Ultimately, modern industrial facilities must proactively handle equipment failure to maintain smooth operations, and IIoT is ideally suited for this task.
It ensures no data slips through the cracks and provides vigilant, real-time analysis to help maintenance personnel stay one step ahead of potential issues.
Conclusion
The data points to a clear conclusion: industrial maintenance is constantly evolving and will continue to do so.
Because it has to.
As more sophisticated machinery enters industrial ecosystems and competition intensifies, the demand for innovative solutions that drive efficiency becomes more urgent.
After all, organizations simply can’t get anywhere without reliable assets.
The maintenance function has never played such a significant role in securing a company’s success.