Get a Free WorkTrek Demo
Let's show you how WorkTrek can help you optimize your maintenance operation.
Try for freeBusinesses that depend on machinery need to keep them in top shape. Different types of maintenance can help prevent breakdowns, extend machine life, and boost productivity. This article covers machine maintenance types and when to use them.
Machine maintenance strategies include preventive, predictive, and corrective approaches, each suited for specific situations and equipment needs.
Choosing the right maintenance type depends on the machine’s age, usage, and criticality. Some methods focus on fixing issues as they happen, while others aim to stop problems before they start.
Preventive maintenance involves regular check-ups and part replacements to avoid unexpected failures. Predictive maintenance uses data and sensors to spot potential issues early.
Picking the best maintenance plan can cut costs, improve safety, and keep operations running smoothly.
Key Takeaways
- Maintenance strategies help prevent breakdowns and extend machine life
- Different types of maintenance suit various equipment and business needs
- Choosing the right approach can improve efficiency and reduce costs
Understanding Machine Maintenance
Machine maintenance is essential for keeping equipment running smoothly and efficiently.
Regular upkeep, repairs, and inspections are involved to prevent breakdowns and extend machine life.
Proper maintenance helps businesses avoid costly downtime and safety issues.
Definition of Machine Maintenance
Machine maintenance refers to the work done to keep machines functioning well. It includes:
- Regular inspections
- Cleaning and lubricating parts
- Replacing worn components
- Adjusting and calibrating equipment
These tasks aim to prevent problems before they occur. Maintenance can be planned or unplanned, depending on the situation.
Importance of Maintenance
Good machine maintenance plan and practices are important for several reasons:
- Increased productivity
- Improved safety
- Lower repair costs
- Extended equipment lifespan
Regular upkeep helps catch minor issues before they become big problems. This reduces unexpected breakdowns and keeps production running smoothly.
Well-maintained machines also use less energy and produce higher-quality output, which leads to better overall efficiency and customer satisfaction.
Goals of Effective Maintenance
The main goals of effective maintenance are:
- Minimize downtime
- Optimize machine performance
- Ensure worker safety
- Reduce repair and replacement costs
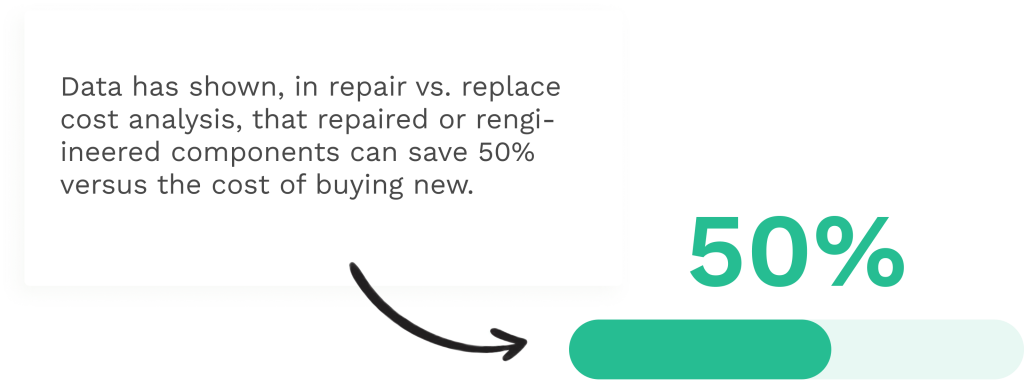
Illustration: WorkTrek / Data: ATS
So which one should you choose? Successful companies often use various maintenance types to achieve these goals, including preventive, predictive, and corrective approaches.
A good maintenance plan balances cost and effectiveness. It aims to keep machines running at peak performance without overspending on unnecessary work.
Regular training for maintenance staff is also important. This ensures they can handle various issues and use the latest maintenance techniques.
Types of Machine Maintenance
Machine maintenance comes in several forms. Each type serves a specific purpose and helps keep equipment running smoothly.
The most effective approaches are preventive and predictive maintenance, while corrective and condition-based maintenance also play an important role.
The main types include preventive, predictive, corrective, and condition-based maintenance.
Preventive Maintenance
Preventive maintenance aims to prevent problems before they start. It involves regular, scheduled upkeep of machines, including cleaning, lubricating, and replacing parts on a set timetable.
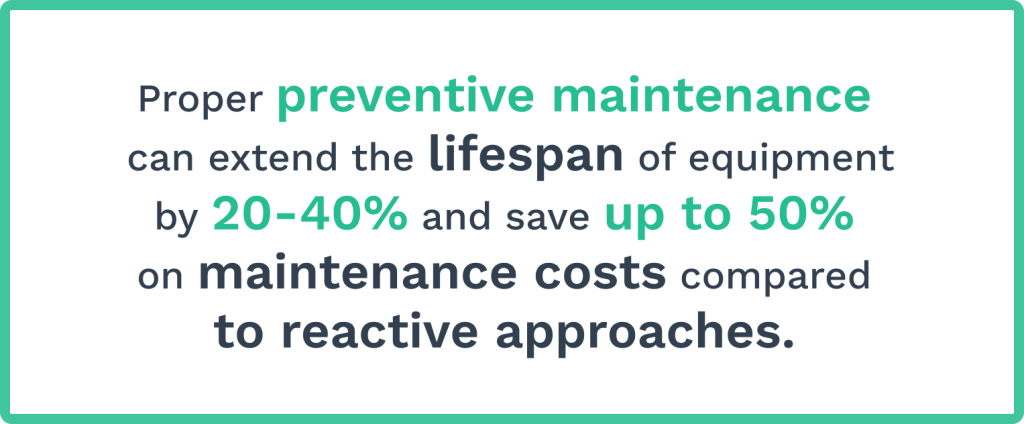
Illustration: WorkTrek / Data: workwize
Preventive maintenance helps extend machine life and reduce unexpected breakdowns. It’s like getting regular oil changes for a car.
Tasks might include:
- Inspecting equipment weekly
- Changing filters monthly
- Calibrating instruments quarterly
This approach can save money in the long run by avoiding costly repairs. It also helps maintain consistent production quality.
Predictive Maintenance
Predictive maintenance uses accurate data to forecast when a machine might fail. It relies on sensors and analytics to spot potential issues early.
This method can be more cost-effective than preventive maintenance. It allows repairs only when needed rather than on a fixed schedule.
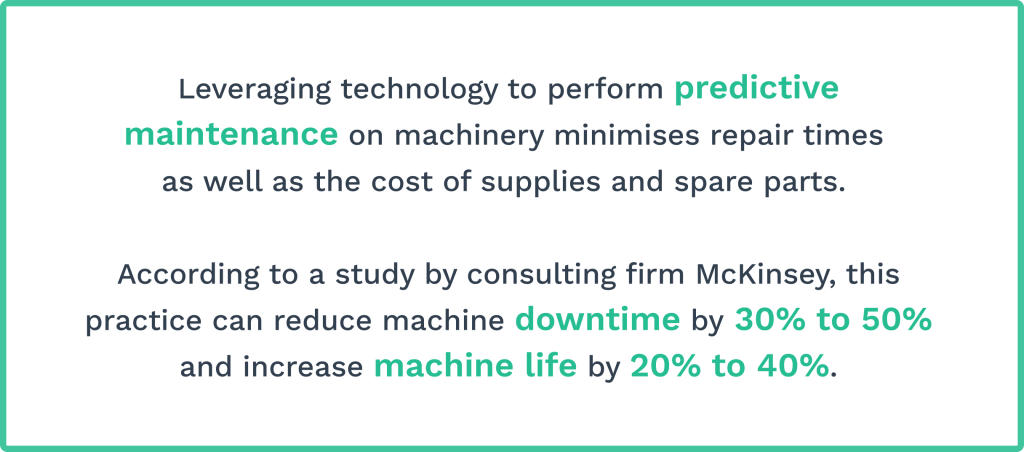
Illustration: WorkTrek / Data: mecalux
Predictive maintenance often uses techniques like:
- Vibration analysis
- Oil analysis
- Thermal imaging
By catching problems early, it can prevent unexpected downtime. This leads to smoother operations and better maintenance activity planning.
Corrective Maintenance
Corrective maintenance, also called reactive maintenance, occurs after a machine breaks down. This approach fixes problems as they occur rather than attempting to prevent them.
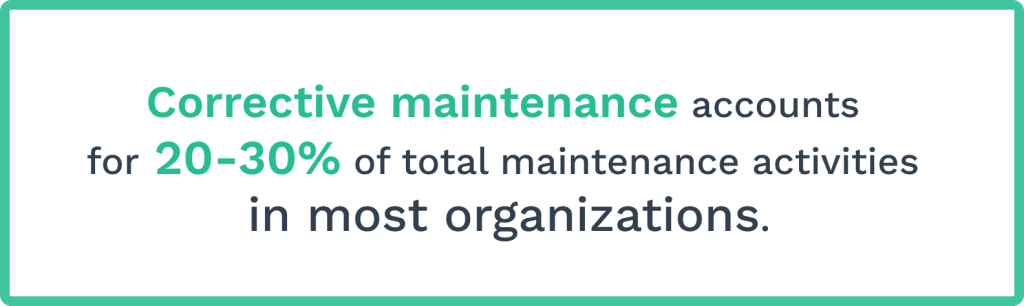
Illustration: WorkTrrek / Data: Camcode
Basic maintenance tasks include replacing light bulbs and changing HVAC filters.
While it might seem cheaper at first, corrective maintenance can lead to:
- Longer downtime
- Higher repair costs
- Unexpected production delays
Corrective maintenance is sometimes used for less critical equipment and is the right maintenance strategy for less critical equipment.
It can be suitable when the cost of failure is low, and repairs are quick and easy.
Condition-Based Maintenance
Condition-based maintenance monitors the actual state of equipment and evaluates the actual condition before performing repairs.
This method is similar to predictive maintenance but focuses more on current conditions. It can involve:
- Continuous monitoring systems
- Regular equipment inspections
- Performance data analysis
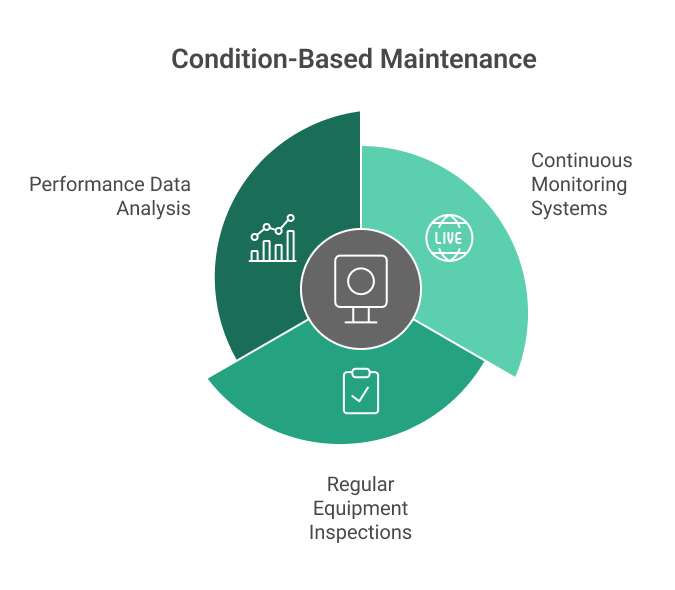
Source: WorkTrek
Condition-based maintenance helps catch issues that scheduled checks might miss. It can benefit critical equipment where failures could be dangerous or costly.
This approach allows for more precise maintenance timing. It can help balance the need for equipment uptime with the cost of maintenance activities.
Preventive Maintenance Strategies
Preventive maintenance aims to keep machines running smoothly and avoid breakdowns. It involves regular upkeep, planned service intervals, and smart parts management.
Routine Maintenance Tasks
Preventive maintenance includes daily, weekly, and monthly tasks. Daily checks might involve inspecting fluid levels, belts, and filters. Weekly tasks often cover lubrication, cleaning, and minor adjustments.
Monthly routines may include more detailed inspections and replacements. These tasks help catch minor issues before they become big problems. Operators play a key role in spotting early signs of wear or damage.
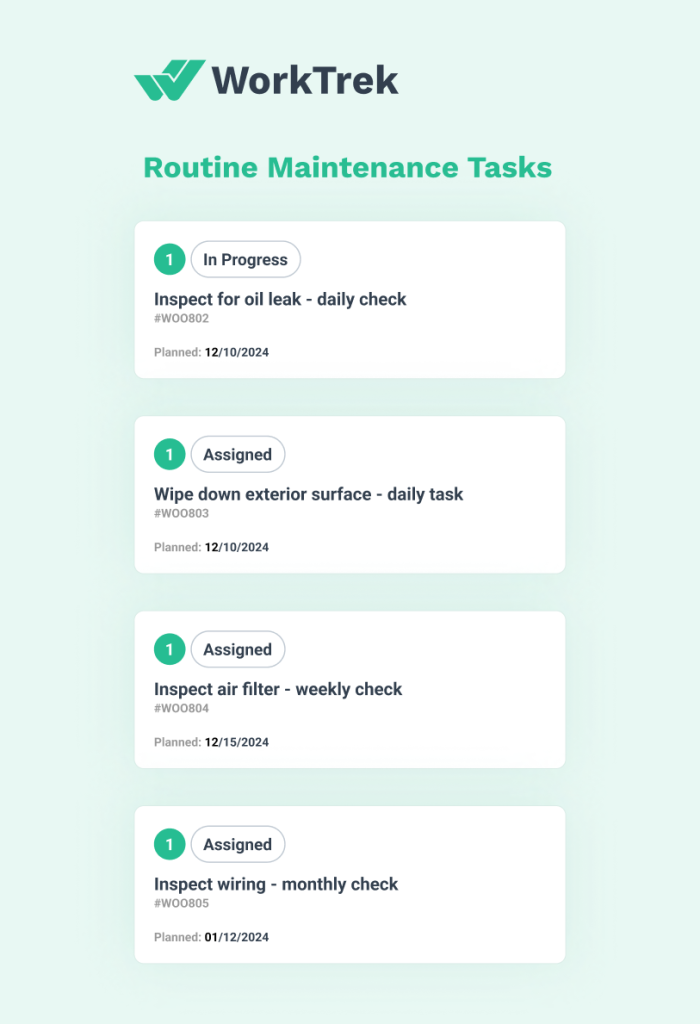
Source: WorkTrek
Checklists are useful tools for tracking routine tasks. They ensure nothing gets missed and create a record of work done. Digital checklists on mobile devices make this process even easier.
Scheduled Maintenance Intervals
Time-based maintenance follows set schedules, which might be based on calendar time or equipment run hours.
For example, an oil change every three months or every 5,000 hours of use.
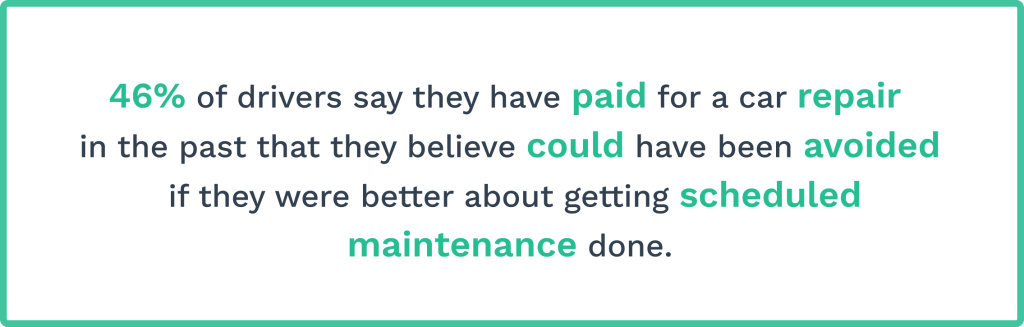
Illustration: WorkTrrek / Data: FinanceBuzz
Usage-based schedules fit equipment that runs irregularly. They focus on actual wear rather than time passed. This approach can save money by avoiding unnecessary service.
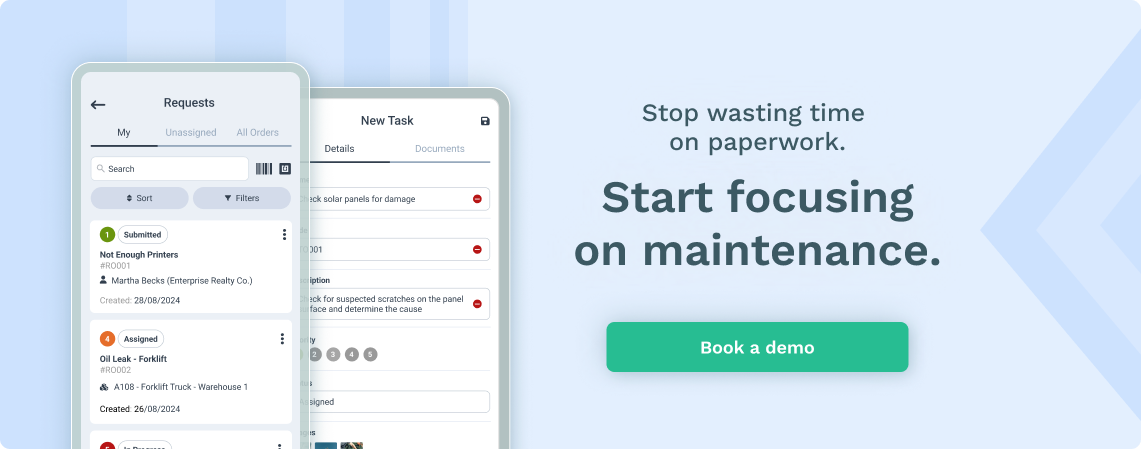
Condition-based maintenance uses sensors to track equipment health. It allows for more precise timing of maintenance tasks. This can extend part life and reduce downtime.
Spare Parts Management
Good parts management is crucial for quick repairs. It involves keeping the right parts on hand without overstocking. A parts inventory system helps track what’s available and what needs ordering.
Critical spares should always be in stock. If not replaced quickly, they could cause long downtimes. Less critical parts can be ordered as needed or kept in smaller quantities.
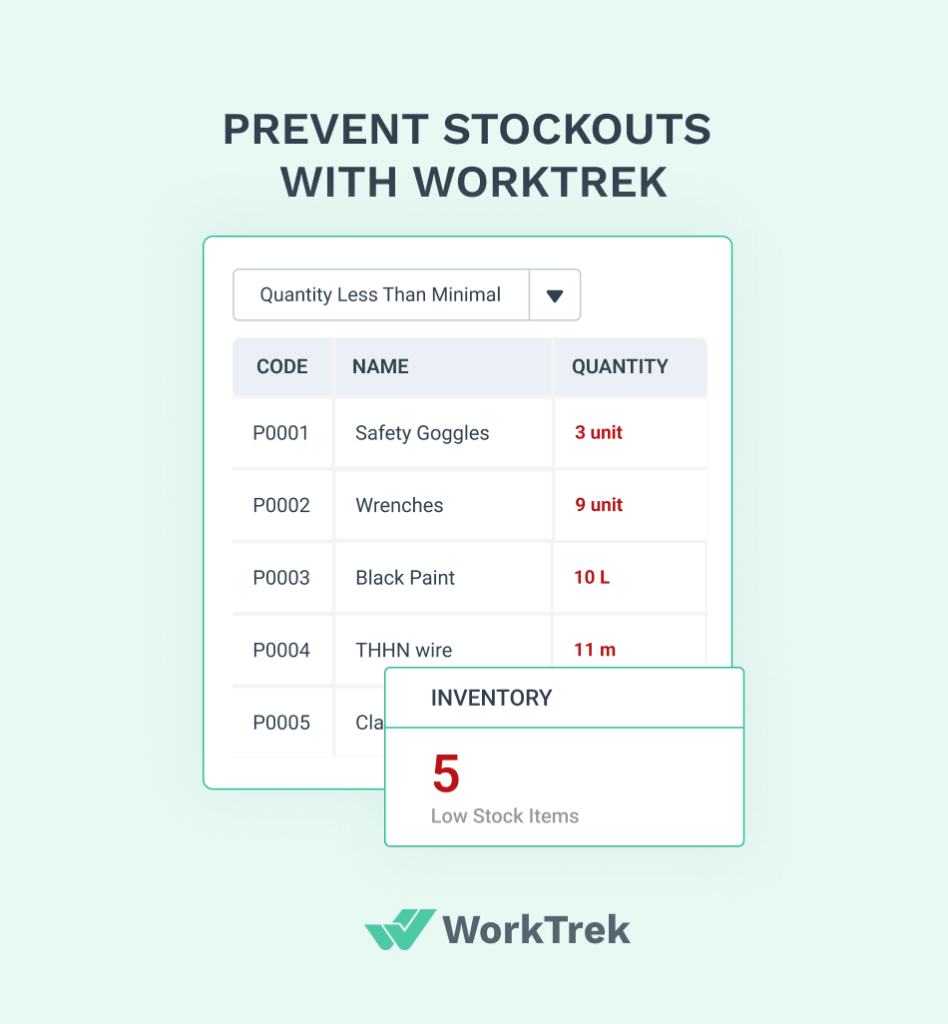
Source: WorkTrek
Regular audits of the parts inventory ensure accuracy and help identify slow-moving parts that might be unnecessary.
Proper parts storage is important to keep them in good condition until needed.
Predictive Maintenance Techniques
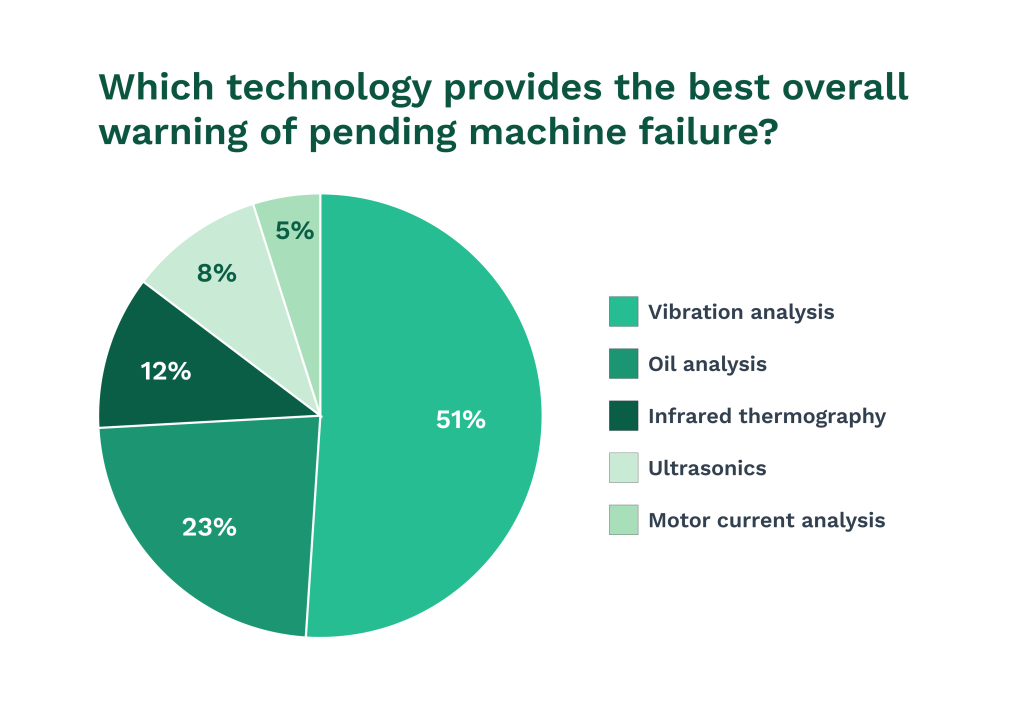
Illustration: WorkTrrek / Data: Reliable Plant
Predictive maintenance uses advanced tools to spot potential equipment issues before they cause problems. These methods help companies save money and avoid unexpected breakdowns.
Vibration Analysis
Vibration analysis is a key predictive maintenance technique. It involves measuring and analyzing machine vibrations to detect problems.
Sensors are attached to equipment to track vibration patterns. Changes in these patterns can signal issues like:
- Loose parts
- Misalignment
- Bearing wear
Vibration analysis works well for rotating machinery, including motors, pumps, and turbines. It can find problems early, giving maintenance teams time to plan repairs.
Special software analyzes the data from vibration sensors. This software compares current readings to normal levels. When vibrations exceed set limits, the system alerts technicians.
Infrared Thermography
Infrared thermography uses heat-sensing cameras to spot equipment issues. These cameras detect temperature differences that might indicate problems.
Common applications include:
- Electrical systems
- Mechanical equipment
- Building inspections
The cameras create thermal images showing hot and cold spots. Unusually hot areas often mean equipment is working too hard or failing.
For example, a hot electrical connection might signal a loose wire. Excess heat could mean low lubricant levels or bearing problems in mechanical systems.
Infrared scans are quick and don’t require equipment shutdowns, making them useful for regular checks without disrupting operations.
Oil Analysis
Oil analysis involves testing oil samples from machinery to check its condition. This method can reveal a lot about equipment health without taking it apart.
Technicians look for:
- Metal particles (signs of wear)
- Contaminants (dirt, water)
- Chemical changes in the oil
Regular oil tests can:
- Extend oil change intervals
- Catch problems early
- Reduce unplanned downtime
Oil analysis works well for engines, gearboxes, and hydraulic systems. It helps companies save money on oil changes and avoid major repairs.
The tests are done in labs using special equipment. Results show trends over time, helping predict when maintenance is needed.
Ultrasonic Testing
Ultrasonic testing uses high-frequency sound waves to detect equipment issues. It can find problems that other methods might miss.
This technique is good for:
- Detecting air or gas leaks
- Checking electrical systems
- Finding bearing problems
Ultrasonic tools pick up sounds humans can’t hear. These sounds can indicate issues like air leaks or electrical arcing.
For bearings, ultrasonic testing can spot problems earlier than vibration analysis. It detects subtle changes in sound that show early wear.
Technicians use handheld devices to scan equipment. The devices convert ultrasonic waves into audible sounds or visual displays for easy interpretation.
Implementing Maintenance Programs
Setting up effective maintenance programs takes planning and effort. Good programs use schedules, training, and metrics to keep machines running smoothly.
Maintenance Planning and Scheduling
Maintenance planning involves determining what work needs to be done and when. It starts with a list of all equipment that needs upkeep and preventive measures.
Planners decide on the right type of maintenance for each machine, which could be preventive, predictive, or corrective.
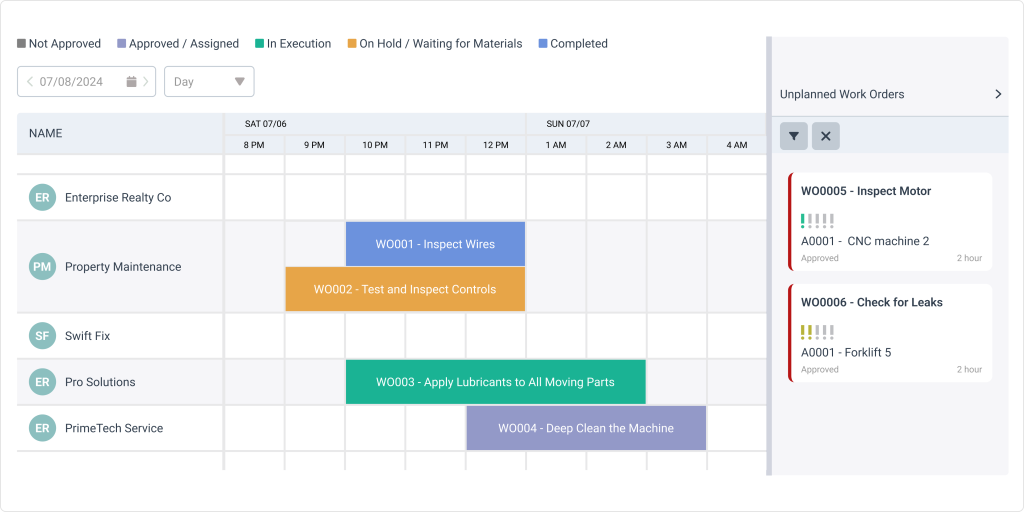
Source: WorkTrek
Next, they create a schedule. This sets times for inspections, part replacements, and repairs. Good schedules balance machine needs with available staff and resources.
Digital tools help track maintenance tasks. These systems send alerts when work is due and record what’s been done.
Maintenance Training Programs
Well-trained staff are key to good maintenance. Training programs teach workers how to:
- Spot signs of wear and damage
- Use diagnostic tools
- Follow safety rules
- Fix common problems
- Work with new technology
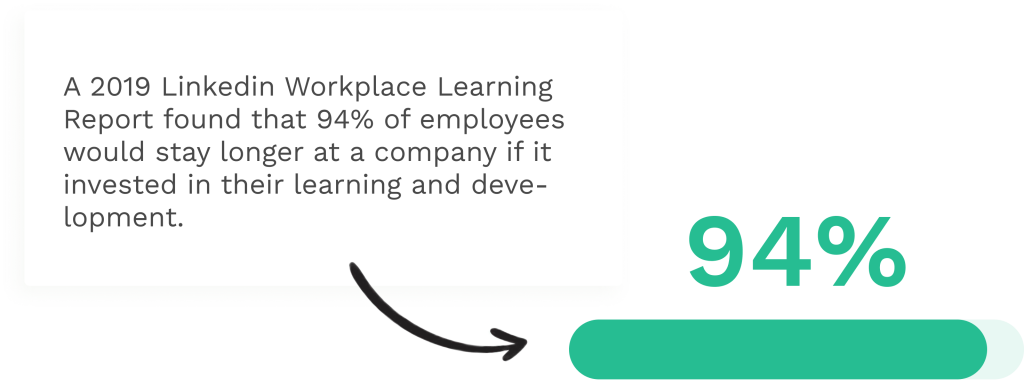
Illustration: WorkTrrek / Data: Alison
Training can happen in classrooms, on the job, or through online courses. It should cover both theory and hands-on practice.
Regular refresher courses keep skills up to date. This is important as machines and methods change over time.
Some companies bring in experts to teach special skills. Others send workers to learn from equipment makers.
Maintenance Performance Metrics
Metrics help track how well maintenance programs are working. Common measures include:
- Downtime: How long machines are out of service
- Mean Time Between Failures (MTBF): Average time a machine runs before breaking down
- Maintenance costs: Money spent on repairs and upkeep
- Work order completion rate: Percent of planned tasks finished on time
Companies use these numbers to spot problems and make improvements. They might adjust schedules or training based on what the data shows.
Regular assessment of these metrics helps refine maintenance approaches. This could mean changing strategies for some equipment or tweaking maintenance timing.
Good metric tracking requires clear records and analysis. Many firms use software to collect and study this data.
Challenges in Machine Maintenance
Keeping machines running smoothly is not without its hurdles. Companies face several key issues when picking the right maintenance strategy. These include balancing resources, adopting new technologies, and following safety rules.
Resource Allocation
Deciding how to use time, money, and people for machine upkeep can be tricky. Companies must figure out:
- How often to check and fix machines
- When to replace old parts
- How many workers to assign to maintenance tasks
It’s a balancing act. Too little maintenance can lead to breakdowns, and too much can waste money. Managers need to find the sweet spot.
Some businesses struggle to attract enough skilled workers. Equipment failures and downtime can cause big problems if not fixed quickly, so having the right people on hand is crucial.
Buying spare parts and tools also requires careful planning. Keeping too many parts in stock ties up cash, but not having parts when needed can stop work.
Technological Integration
New tech can make maintenance more manageable and help detect potential problems. but it’s not always straightforward.
Some challenges are:
- Picking the right software for tracking repairs
- Training workers to use new tools
- Making sure old and new systems work together
CMMS Software like WorkTrek can help you centralize and organize your maintenance plans in a single platform.
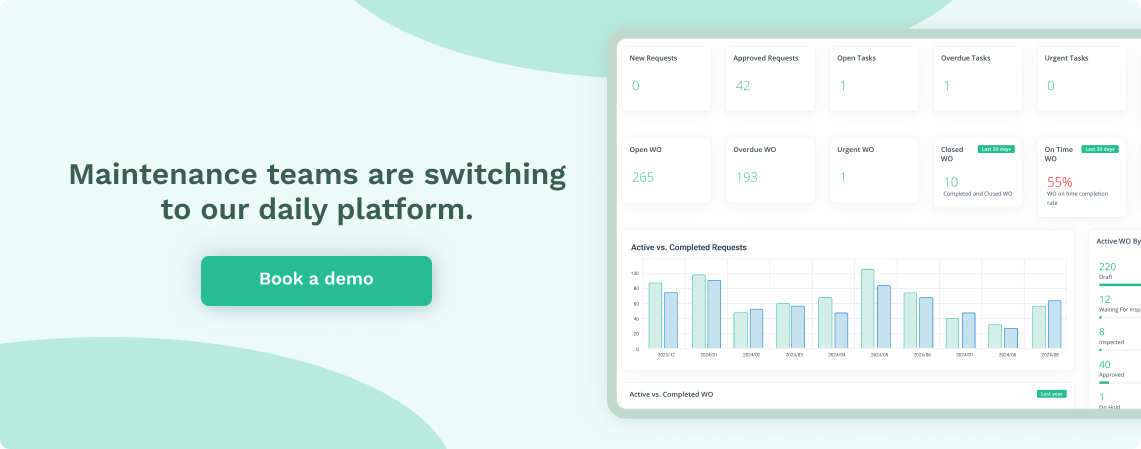
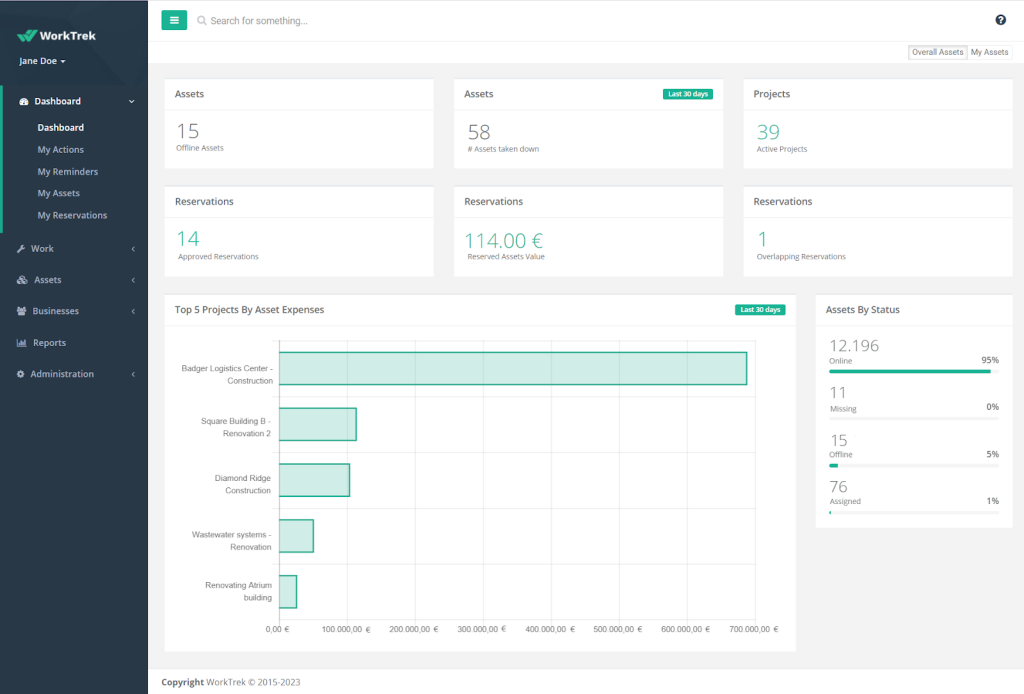
Source: WorkTrek
Smart sensors can spot problems early. However, setting them up and understanding the data takes time and skill.
AI and machine learning offer new ways to predict when machines will break. But these systems need a lot of good data to work well, and getting that data can be difficult.
Mobile apps can help workers do their jobs better. But not everyone finds them easy to use at first.
Safety and Compliance
Keeping workers safe while fixing machines is very important. Some key issues are:
- Following all safety rules
- Giving workers the proper safety gear
- Training everyone on safe ways to work
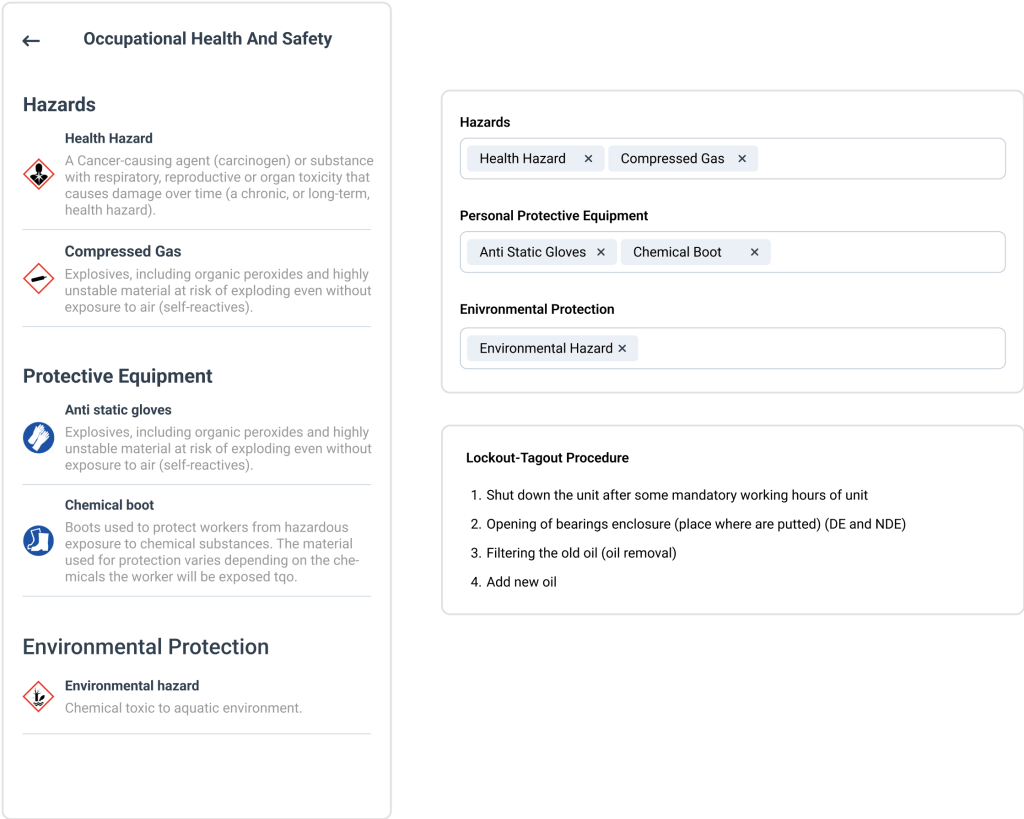
Source: WorkTrek
Safety rules change often, and staying up to date can be difficult. But it’s crucial to avoid accidents and fines.
Some machines have special safety needs. Workers must know how to handle dangerous parts or chemicals.
Companies also need to keep good records. This helps prove they’re following all the rules, but it can also mean more paperwork and time spent on reports.
Environmental rules are getting stricter, too. Businesses must be careful about how they dispose of old parts and fluids.
Emerging Trends in Machine Maintenance
Machine maintenance is evolving rapidly. New technologies such as artificial intelligence (AI) and machine learning are changing how companies care for their equipment. These advances aim to make maintenance more efficient and prevent breakdowns.
Internet of Things (IoT) and Maintenance
IoT devices are transforming machine maintenance. Equipment sensors collect real-time data, helping predict when parts might fail. Companies can fix issues before they cause problems.
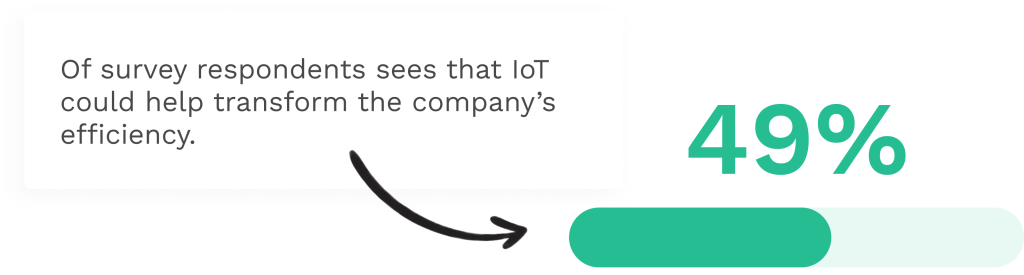
Illustration: WorkTrrek / Data: Fores Interactive
Smart factories are using IoT to track machine health. Sensors measure things like temperature, vibration, and power use. When a machine acts oddly, the system alerts technicians, allowing them to fix small issues quickly.
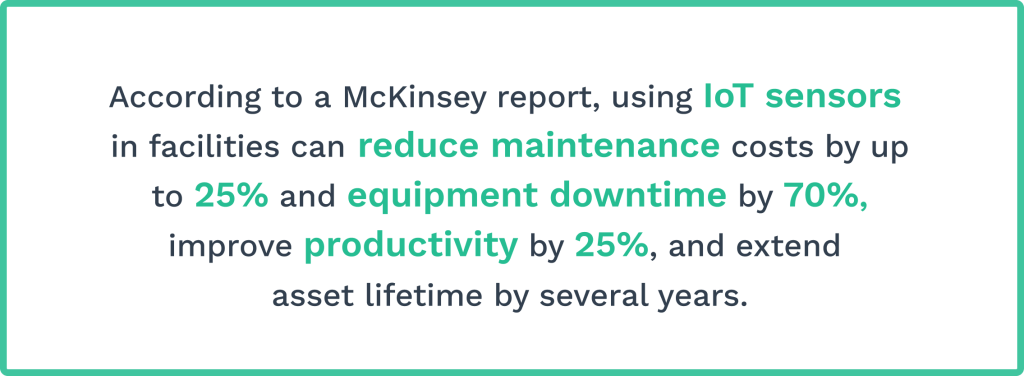
Illustration: WorkTrek / Data: facilio
IoT also helps with inventory. It can track spare parts and automatically order new ones, ensuring they are always on hand when needed.
Automation in Maintenance Processes
Automated systems are taking over routine maintenance tasks. Robots can now do jobs that were once done by hand, freeing up workers for more complex tasks.
Some examples of automation in maintenance:
- Drones that inspect hard-to-reach areas
- Robots that clean and lubricate machinery
- Software that schedules maintenance tasks
These tools make maintenance faster and more accurate. They can work around the clock without getting tired.
3D printing is also changing how companies make spare parts. They can print parts on-site instead of waiting for deliveries.
Data Analytics in Machine Maintenance
Big data helps companies make smarter maintenance decisions, which can result in reduced downtime. They collect information from many sources to spot patterns, which helps predict when machines need care.
Key benefits of data analytics in maintenance:
- Predicting failures before they happen
- Optimizing maintenance schedules
- Reducing downtime and costs
Advanced condition monitoring uses data to track machine health. It can tell when a part is wearing out, letting companies replace parts at the right time—not too early and not too late.
Data also helps companies understand why machines fail, which can help them make better machines in the future.
Selecting the Right Maintenance Approach
Picking the best maintenance strategy is key to keeping machines running well. Companies must consider several factors when deciding.
Equipment type matters a lot. Simple machines might only need basic upkeep, while complex ones often require more advanced care.
Another big factor is the cost of breakdowns.
If failures are costly, predictive maintenance may be worth the investment.
How critical the equipment is also counts. Vital machines need more attention than less important ones.
Here’s a quick guide to help choose:
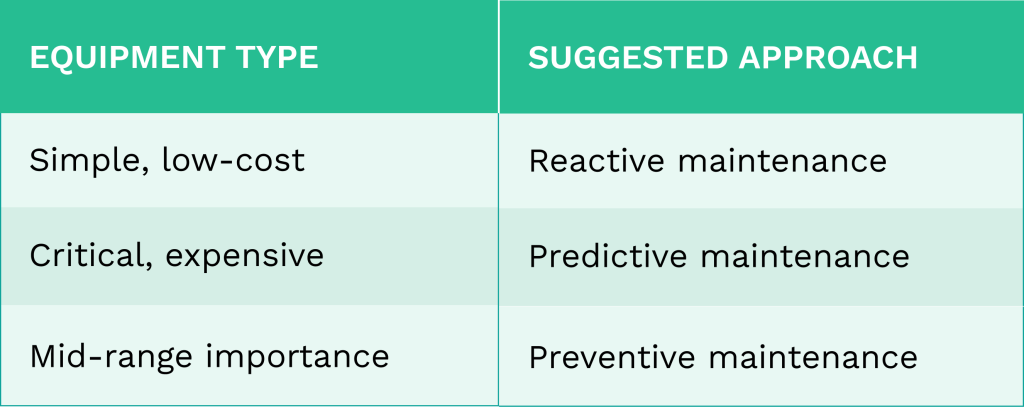
Source: WorkTrek
Budget plays a role, too. Some methods cost more upfront but save money over time.
Maintenance teams should consider their staff’s skills. Complex strategies need trained workers to be effective.
Data helps pick a strategy. Looking at past breakdowns can show what’s needed.
Many companies use more than one method. They might do basic checks on all machines and detailed work on key ones.
The goal is to find a balance. Good maintenance keeps machines running without wasting money.
Summary
Keeping machines running smoothly is super important for any business that relies on equipment. The article broke down the different ways to care for machines – some fix problems before they happen, while others deal with issues as they pop up.
Think of it like caring for your car – you can wait for it to break down or do regular checkups.
Companies need to pick the right approach based on their equipment and budget. Sometimes, the best strategy is a mix of different methods. The bottom line? Good maintenance saves money, keeps workers safe, and helps businesses run without unexpected shutdowns.