Get a Free WorkTrek Demo
Let's show you how WorkTrek can help you optimize your maintenance operation.
Try for freePlanning maintenance is one of the best things you can do for your facility or plant.
Regular planned maintenance prolongs the lifespan of your assets and keeps them healthy, reducing the need for emergency repairs.
It lets you schedule downtime when it best suits your operations, lowering overall maintenance and operational costs.
However, despite these appealing benefits, maintenance planning often needs to catch up.
That’s because maintenance supervisors and planners frequently make these common mistakes.
Today, we will explore the six most dangerous ones.
Don’t worry—we’ll also show you how to avoid them and give examples of companies that did it successfully.
Let’s get started.
Manually Planning Maintenance Activities
Is your planner still relying on spreadsheets in Excel or paper-based logs to do their job?
If yes, you’ll likely encounter errors in your maintenance planning.
This system is prone to them.
Acuity’s research from 2022 showed that 12% of Excel spreadsheets have serious errors and that 12% of people have seen an Excel mistake cost more than £10,000.
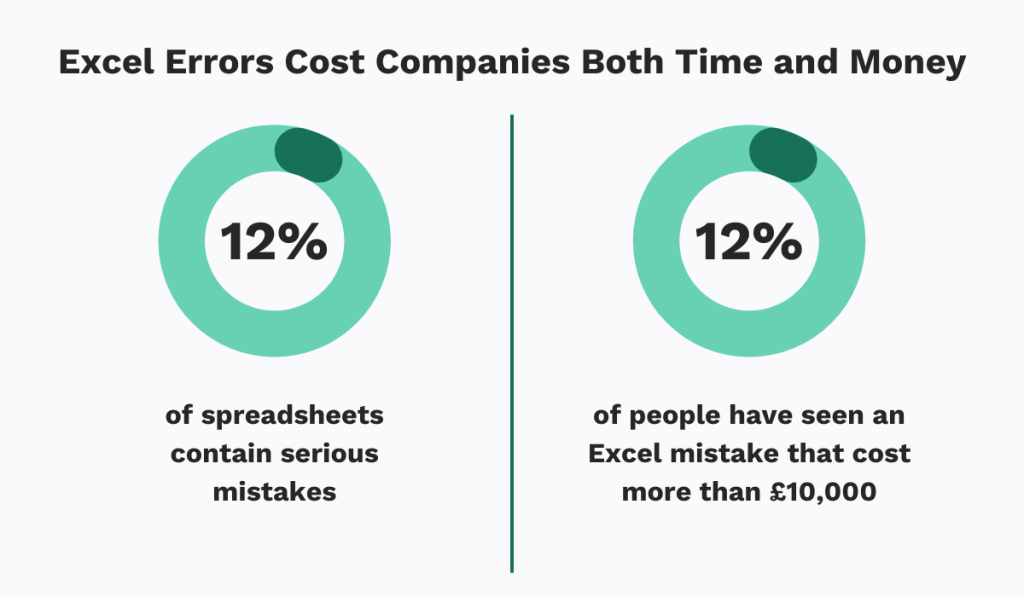
Now, think about this.
One critical task in a maintenance planner’s role is to ensure that all spare parts, tools, and materials are readily available for maintenance.
Let’s say you still keep inventory records in Excel.
If the spreadsheet contains an error, and your planner doesn’t physically check inventory—which would again be a waste of time—the mistake can lead to parts not being available when a technician is scheduled to complete the work.
And that means delays, technician’s idle time, and so on.
So, it’s pretty clear that manually planning maintenance is prone to errors. Not to mention how time-consuming it is to look for information on multiple spreadsheets.
But why go through these headaches when there’s a better solution?
A computerized maintenance management system (CMMS) is the answer.
Let’s look at our own WorkTrek as an example.
First and foremost, WorkTrek is easy to use for maintenance planners, supervisors, managers, and technicians.
Everyone has access to their tasks and schedules.
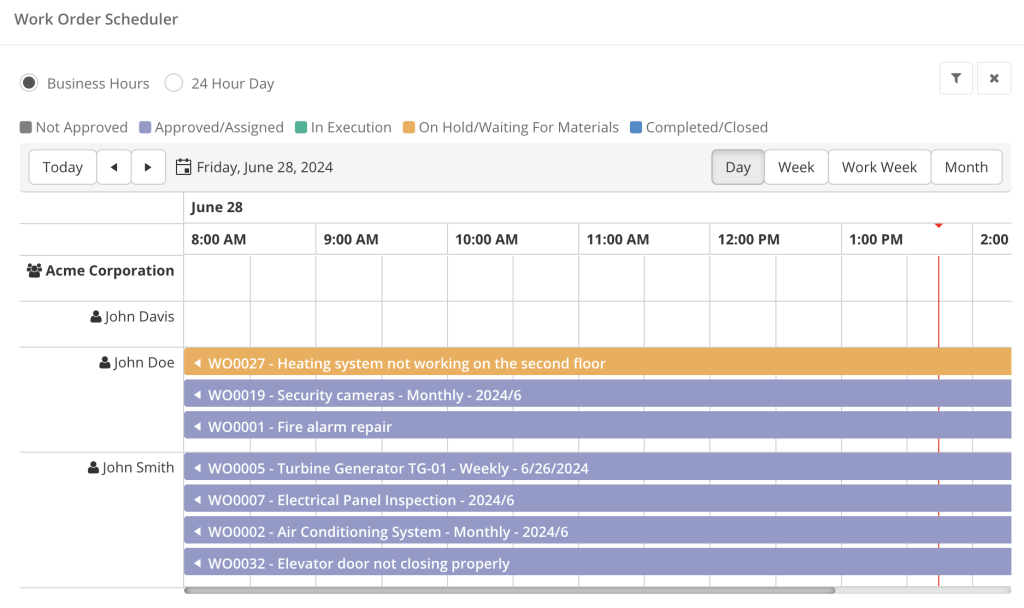
Planners can create, assign, and schedule work orders in one place without endless paperwork.
With all asset data available (including the inventory list), they can often plan a job with just a few clicks.
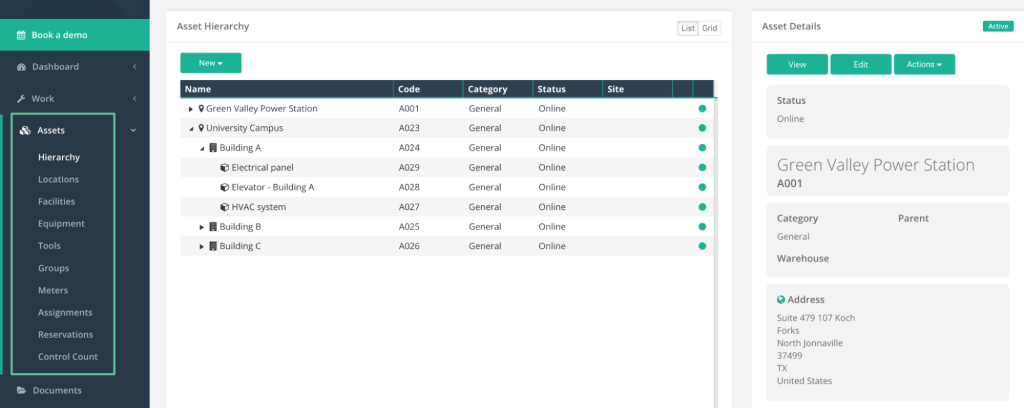
They can also add photos, documents, manuals, and comments to a task, ensuring the technician completes the job precisely as intended.
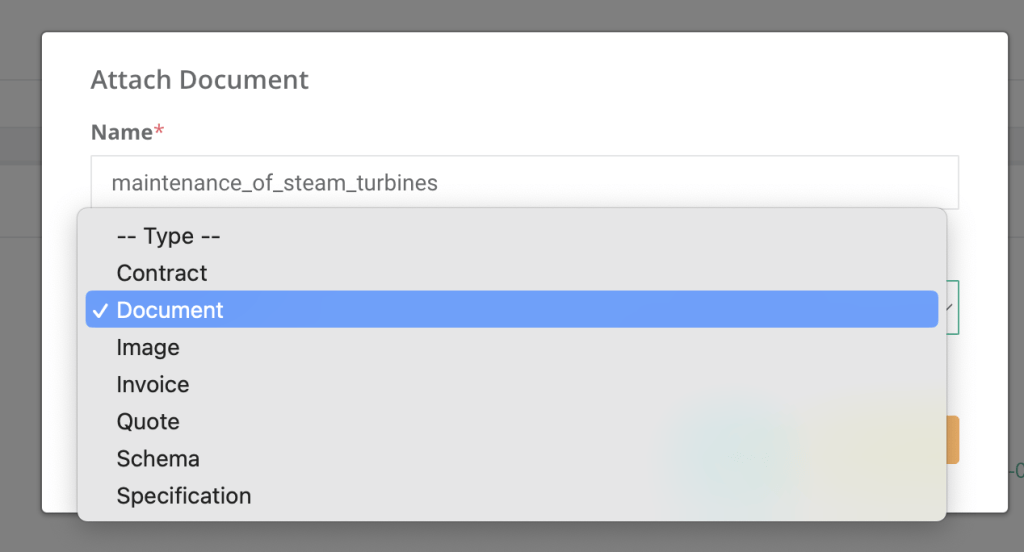
On the other hand, technicians and other employees can quickly submit service requests through WorkTrek’s app or request portal.
The planner can then immediately create work orders and tasks and assign them to the right technician or team using a web or mobile app.
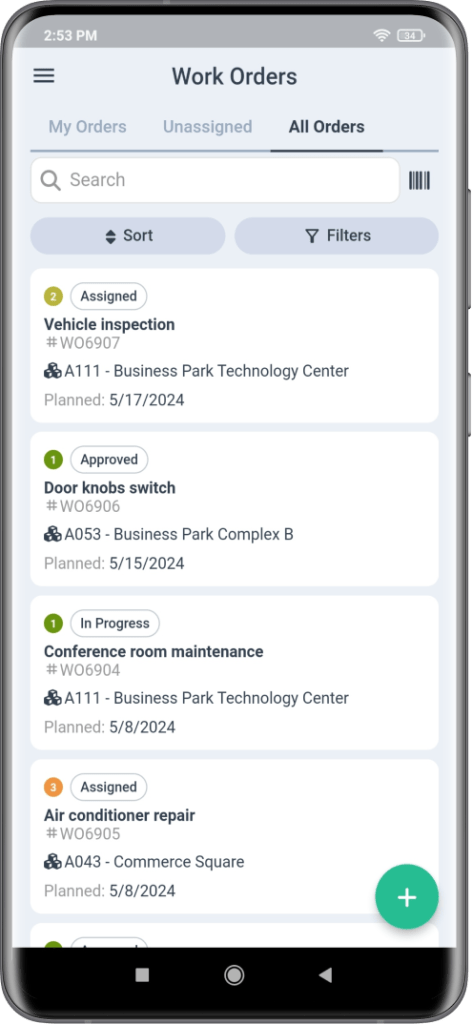
In addition, WorkTrek lets you set specific time intervals for preventive maintenance, schedule inspections, run reports, and much more. In a system like this, data is captured in real time, processes are automated, and there’s no room for mistakes.
So, why stick with manual planning when there’s an easy and convenient way to improve your maintenance planning with automation?
Turning Maintenance Planners into Generalists
Turning your maintenance planner into one is another common mistake in maintenance planning.
After all, a jack of all trades is a master of none.
Burdening your planners with tasks like supervising, troubleshooting, administration, or scheduling distracts them from their primary focus—planning future tasks.
When bogged down with these additional duties, planners can easily get sidetracked.
And you know what that means?
No time to create efficient maintenance plans, leading to poor and inefficient work execution.
MillerCoors (now MolsonCoors), one of the world’s largest brewers, had the same problem.
Their maintenance planning was inefficient because the production department saw maintenance planners as “gofers.”
Brad Simpkins, an asset CARE manager at the time, explained:
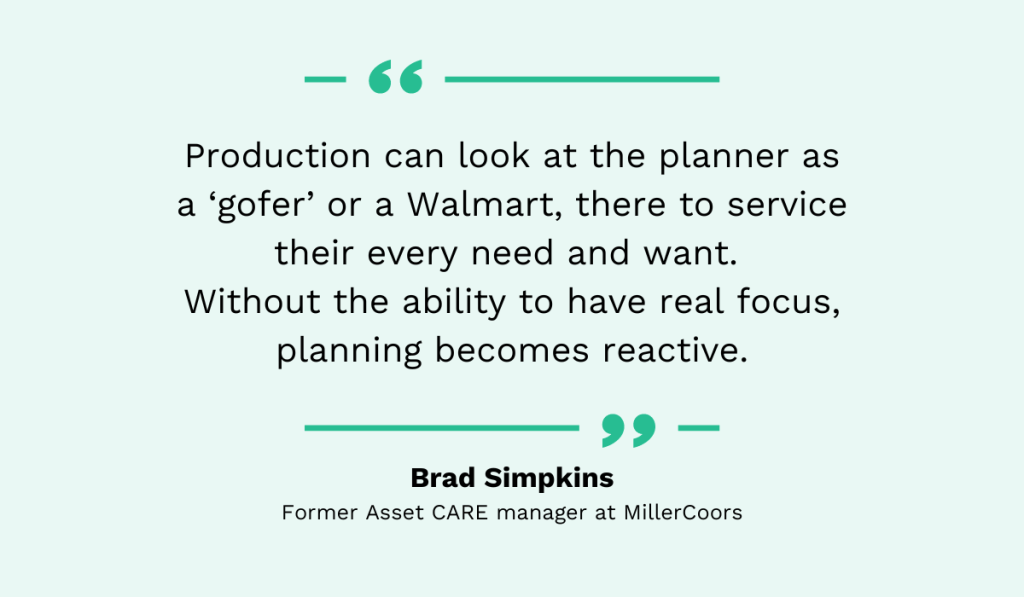
So, their maintenance planners spent lots of time sourcing and storing replacement parts instead of planning future tasks.
But also doing tasks like “buying first-class seats on airplanes to ship a motor,” as Bobby McCall, maintenance manager for packaging operations, added.
Of course, this left no time for planning, and their maintenance remained reactive.
Fortunately, they took action and limited their planners to tasks within their scope of work.
This brought significant results. Planned and scheduled work increased from less than 30% to more than 60%.
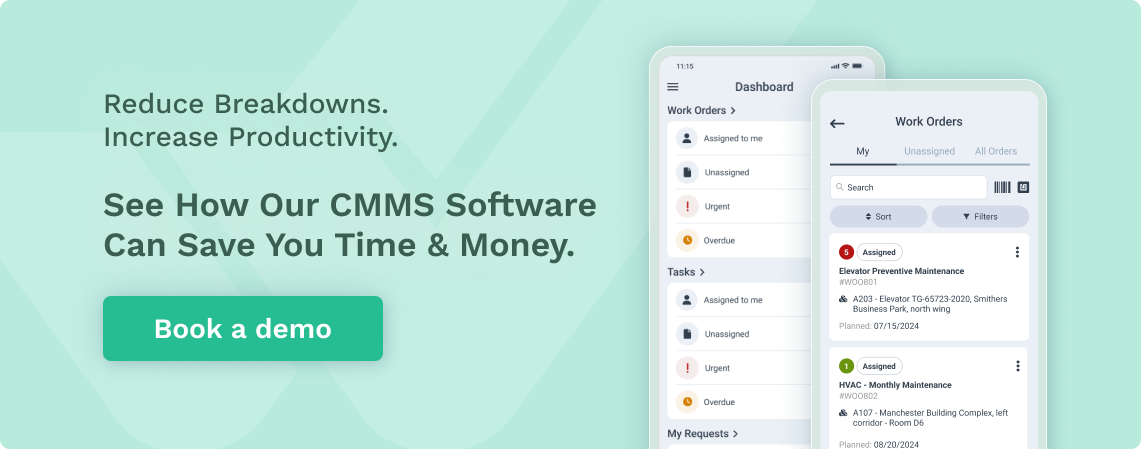
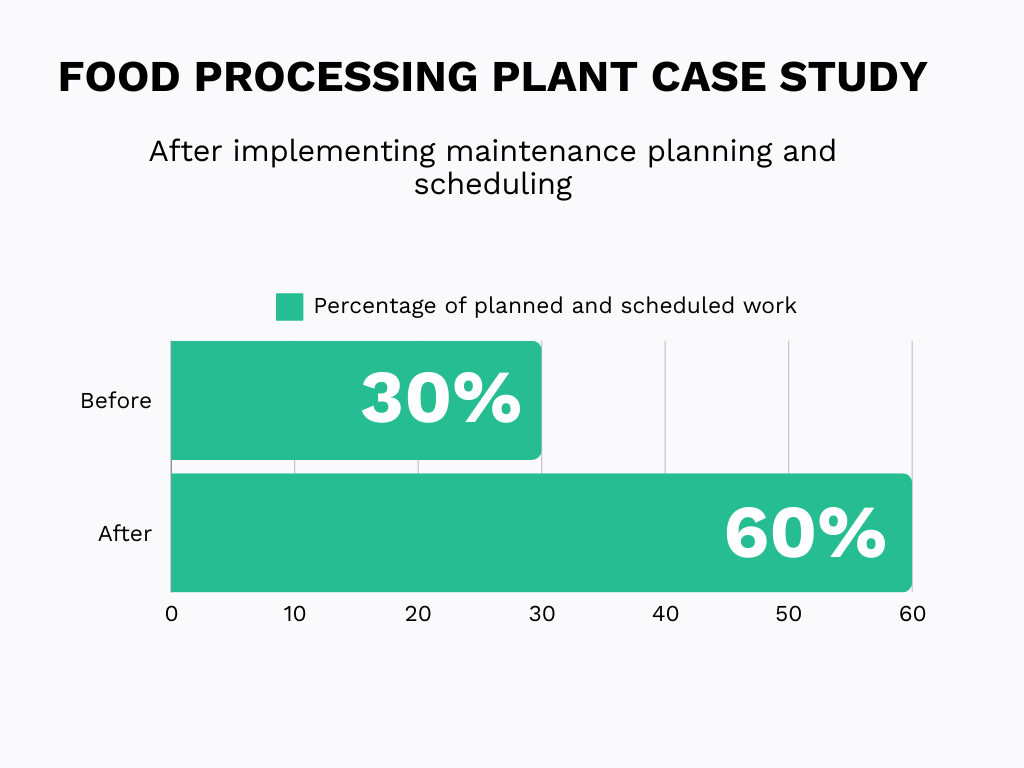
Equipment availability, productivity, and uptime increased, leading to reduced maintenance costs.
Therefore, let your planners do what they do best and remove distractions. It will soon lead to increased planned and scheduled maintenance.
Not Investing In Continuous Development for Planners
Did you appoint a technician as a planner, give them a quick rundown of their new role, and leave them to it?
If yes, you’ve made a big mistake.
Sure, assigning the planner role to a senior technician with maintenance knowledge is a good move. Maintenance planners need technical know-how.
But, technicians who’ve spent years fixing assets might not know how to use the software where historical maintenance data is stored. Or how to order necessary parts from vendors.
So, you need to invest time and effort into training them.
This includes teaching them how to use specific technology, best practices for planning and scheduling, and how to communicate with suppliers.
Erik Hupje, founder of Reliability Academy, highlights more areas that maintenance planners need to learn, or rather, that a manager needs to teach them:
- How to use the CMMS you opted for.
- How the maintenance planning and scheduling process works.
- Where to find equipment information, from checklists to manuals.
- How to create and save job plans.
- How to order spare parts and materials.
- How kitting and staging processes work.
But that’s just the beginning.
The maintenance manager or supervisor should also regularly evaluate the planner’s performance and advise them on what to improve.
This feedback can also uncover if the planner isn’t meeting expectations.
If that happens, Prometheus Group suggests you reassess their fit for the role and analyze whether you have set the planner for success.
So, ask yourself:
- Are you overworking the planner?
- Does one planner have too many assets or technicians to manage?
- Are any issues arising due to poor training or a lack of training?
If the latter is the source of the problem, think of how to improve training. One smart way is to learn directly from equipment manufacturers.
Lee Hillyer, director of global sales—mining at Australian equipment manufacturer McLanahan, explains why:
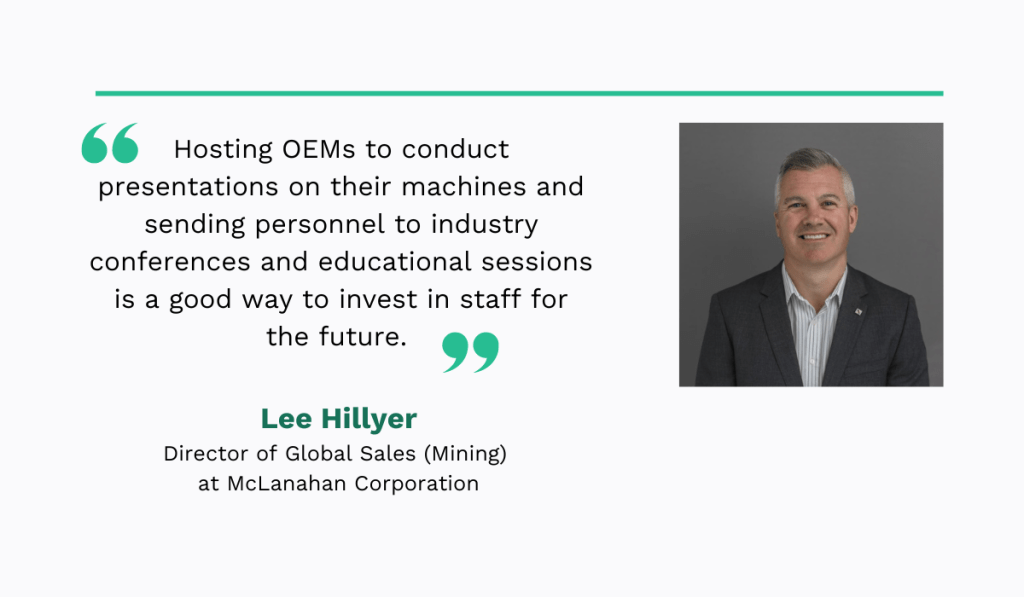
Yes, planners should stay updated on the latest maintenance techniques to prepare more thorough and accurate plans.
And what better way than to hear it from the asset manufacturers themselves?
In short, continually invest in your planners, their development, and their knowledge. Train them properly and teach them how to become better at planning along the way.
When they excel in their role, your maintenance will improve, too.
Relying Only On Manufacturers’ Maintenance Recommendations
Yes, we have just praised how effective it is to educate maintenance personnel directly from OEMs.
Now it’s time to explain why planning maintenance activities shouldn’t be done exclusively based on manufacturers’ recommendations.
We know it sounds contradictory, but let us explain why this is another mistake.
While it is essential to use these recommendations for guidance, it is just as important to consider a specific facility’s operational requirements.
So, as Hillyer from McLanahan, who we already mentioned above, suggests, OEM guidelines should be treated as just a baseline:
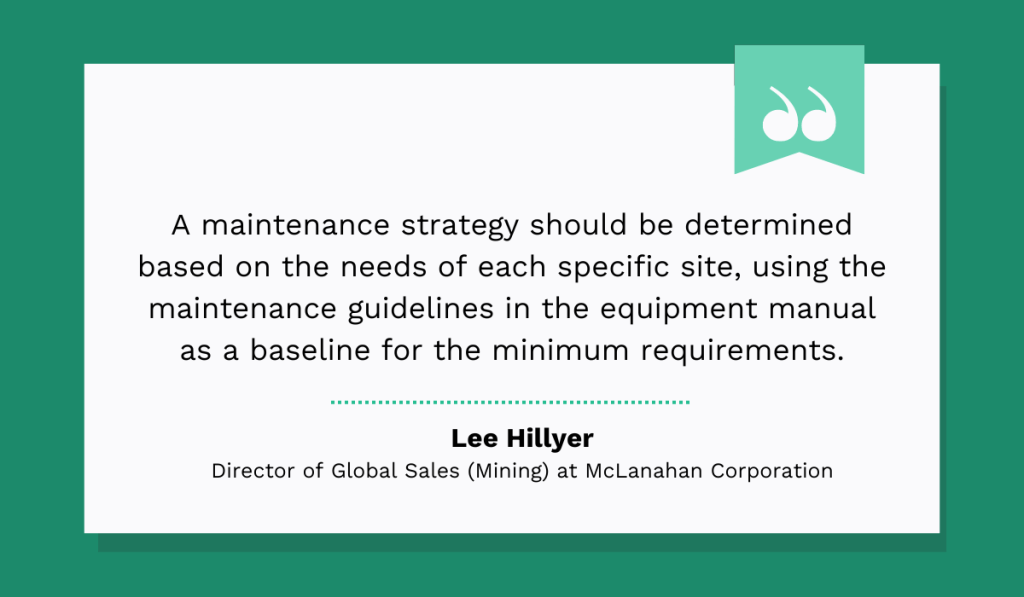
The real goal should be to combine theory (OEM recommendations) and practice.
OEM recommendations are general, and your plant or site is specific. So, think about how your assets are handled and the conditions in which they are used.
Let’s explain this through a simple example—maintenance of a forklift.
If a forklift operates in an environment with dust and debris or is used for heavy lifting continuously, it may require additional maintenance beyond OEM recommendations.
On the other hand, Modla, an online platform for advanced asset analytics, explains that some OEM recommendations assume that their equipment is used in worst-case conditions.
They do that to protect themselves from potential liability and warranty claims.
So, to minimize the risk of equipment failure and associated claims, they provide guidelines that cover even the most extreme conditions.
But, at the same time, that can lead to excessive maintenance for businesses operating in less demanding environments.
This is why some companies, like Harley-Davidson, transitioned to condition-based maintenance to match their specific operating conditions better.
The old process of preventive maintenance was basically to follow the old manuals. In six months, you dump this oil. In a year, you dump this. In two years, you dump this. By bringing in the oil analysis program, we have moved from a time-based system to a condition-based system. That’s low-hanging fruit, and it saved us a ton of money.
By doing so, they optimized their maintenance practices, improved efficiency, and significantly reduced costs.
Therefore, maintenance planners should use manufacturer recommendations as input to create maintenance plans that align with the facility’s needs.
But most importantly, they should consider how the equipment is used in practice.
This, ultimately, truly affects the need for maintenance.
Creating Plans From Scratch Every Time
Creating a new maintenance plan from scratch each time for the same job is a common mistake in the maintenance planning phase.
Jeff Shiver, an expert in the field who helps facilities and plants improve their maintenance, sees this mistake all the time:
In my interviews and data analysis, I search for standard job plans or packages for repetitive maintenance work, especially planned corrective activities resulting from PM inspections and activities frequently repeated on outages. I am often disappointed with the lack of a standard job plan library. It seems that we constantly reinvent the wheel on every outage.
The solution here is simple.
You need a job plan library where your maintenance planners can easily find plans for similar tasks. Here’s an example of a preventive maintenance plan.
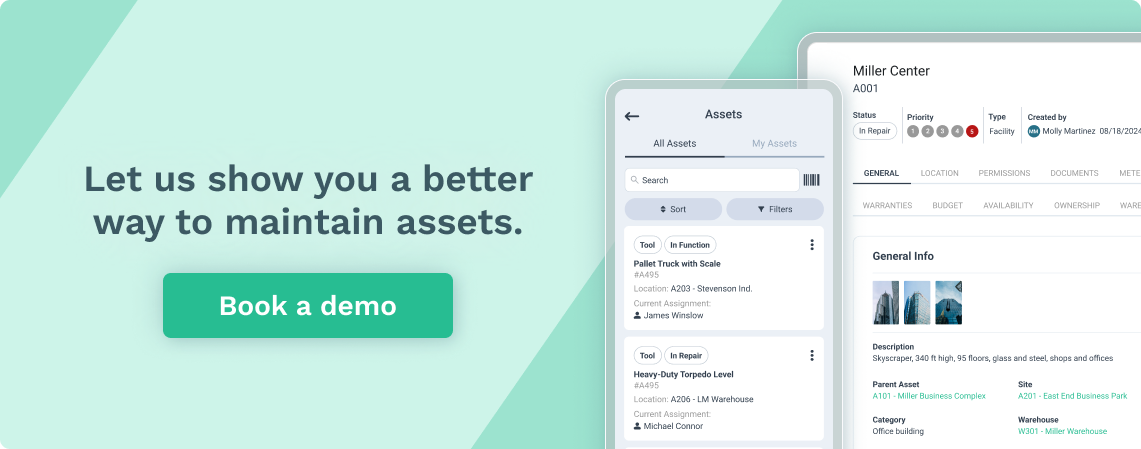
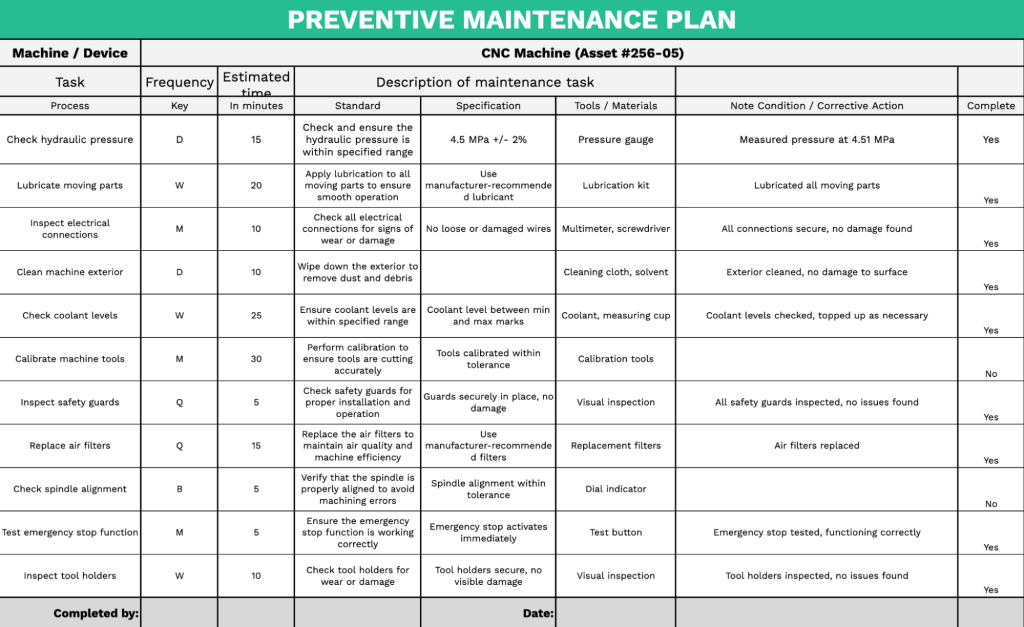
Of course, not every maintenance job is the same, so existing plans shouldn’t just be copied and pasted.
However, your planners can use them as a foundation for new plans, which can be refined for increased effectiveness.
If there isn’t a plan for the same job, should planners create a new one from scratch?
No, they should adjust the existing plans.
Erin Corrigan, former maintenance planner and current SAP PM Master Data Specialist at DuPont, agrees:
But one thing is sure: you can’t have a job plan library without good record keeping.
And this means more than just recording and saving the initial plan.
The essential part is to update the plan after the work is finished to document all feedback and areas for improvement.
When your current maintenance planners find a plan with all these elements in the library, their work will be much easier—and faster.
So, ensure all your maintenance plans are safely stored, and teach your planners to use them!
Ignoring the Findings of Root Cause Analysis
The last mistake we will cover today is ignoring or neglecting root cause analysis (RCA).
In a nutshell, RCA identifies the root causes of problems to prevent them from recurring rather than just reactively fixing symptoms.
One simple but efficient method is the 5 Whys, an example of which you can see below:
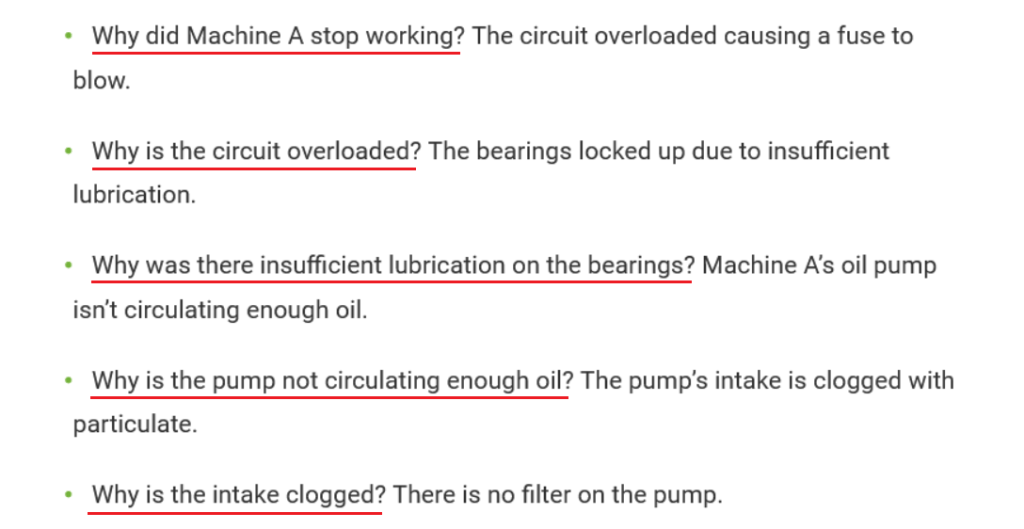
Essentially, you ask “why” five times to dive deep into the root cause of equipment failure.
However, performing RCA is pointless if the findings are ignored.
Despite this, some companies still fall into this trap.
Century Aluminum Ravenswood, which is now closed, was one of them.
Jim Doeffinger, a maintenance manager, described their approach to RCA:
We do some root cause, but it’s all after the fact, and then what do we do with it? ‘This is why it failed.’ Great. What are you going to do to change it? ‘I don’t know. I just wanted to know why it failed.’ It didn’t change anything.
So, even when RCA is conducted, the findings are not shared, no corrective action is taken, and there is no follow-up, so future planning will be poor.
If the core problem isn’t solved, the same issues will repeat, and the same tasks will be planned. Your entire maintenance plan will be off, and you’ll waste time.
Conversely, when the findings of RCA are implemented, you will be much better at planning maintenance.
For starters, knowing the root cause of frequent equipment failures allows better maintenance scheduling to prevent failures before they occur.
Say a machine frequently breaks down due to overheating, and RCA reveals that a malfunctioning cooling system causes the overheating due to clogged filters.
Since you know the root cause, you can plan to clean the filters regularly to prevent this from happening again.
Raytheon’s Facility Services experienced the benefits of RCA first-hand, as their deputy director, Mike Burmood, explained:
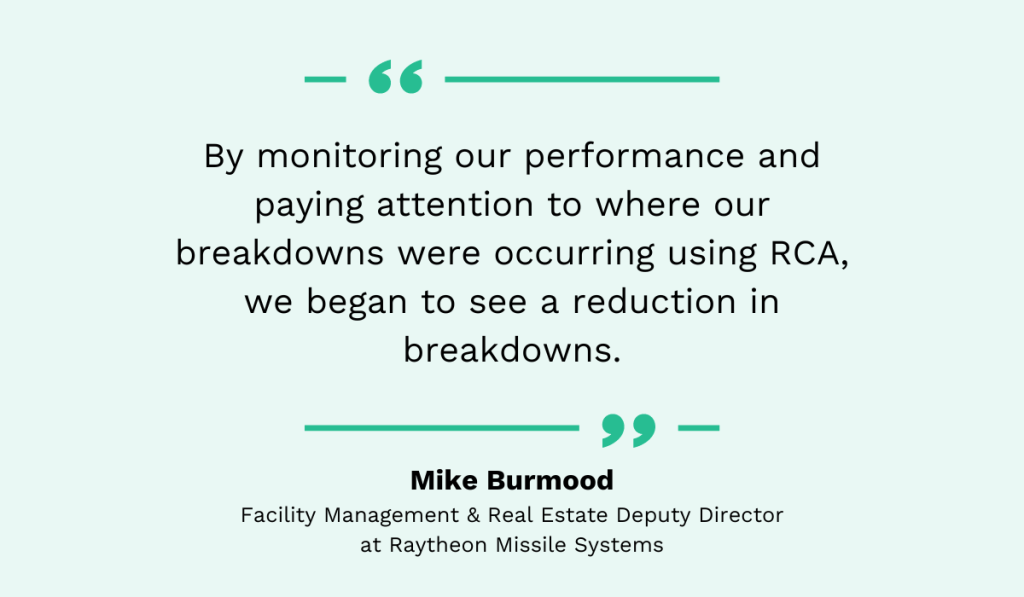
The key takeaway is this: never ignore RCA.
The findings can truly work wonders for your maintenance planning.
In Raytheon’s case, breakdowns decreased to 2% of unplanned work orders, making maintenance more predictable and manageable.
Conclusion
If you recognize yourself in any of these mistakes, it’s time for a change.
Hopefully, we provided enough tips to avoid these common pitfalls of maintenance planning.
We have shown you several companies that were able to fix these mistakes and improve their maintenance planning.
If they did it, you can do it, too!