Get a Free WorkTrek Demo
Let's show you how WorkTrek can help you optimize your maintenance operation.
Try for freeA good maintenance plan is the backbone of successful maintenance operations.
It defines exactly which maintenance tasks must be completed, why, and how.
But what about the “who” and the “when”?
Well, that’s where maintenance scheduling comes in.
Scheduling goes hand-in-hand with your maintenance plan, ensuring all necessary maintenance tasks get completed on time and by the most skilled technicians.
If this sounds important but somewhat overwhelming, don’t worry—we’ll guide you through it.
In this article, we’ll break down each step of the maintenance scheduling process and provide tips on how to best complete it.
1. Reviewing the Maintenance Plan
The first step in maintenance scheduling is reviewing the maintenance plan.
After all, how can you successfully coordinate dozens of maintenance tasks among your technicians if you don’t know what needs to be done and how?
So, take a look at what the maintenance planner has laid out for you.
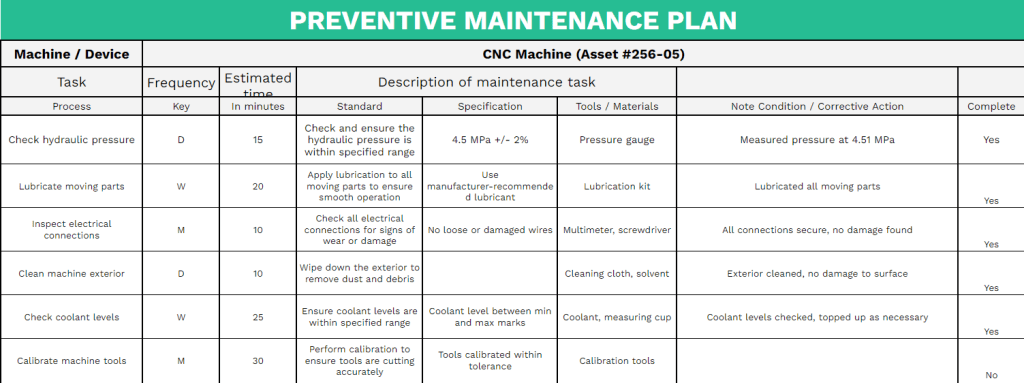
What is the primary objective of the maintenance plan?
Which assets require maintenance, and which tools, parts, and materials will your technicians need to complete the tasks?
Are there any specific safety precautions to keep in mind?
A solid maintenance plan will answer all these questions—and more.
This will allow you to align maintenance tasks with the broader maintenance strategy and keep operations running smoothly at your facility.
At this point, you might be thinking that all of this sounds pretty straightforward.
All you need to do is look at the maintenance plan and assign the outlined tasks to the available technicians.
But research tells us a different story.
According to the 2021 Industrial Maintenance Report, proper scheduling is one of the main challenges blocking the success of maintenance operations.
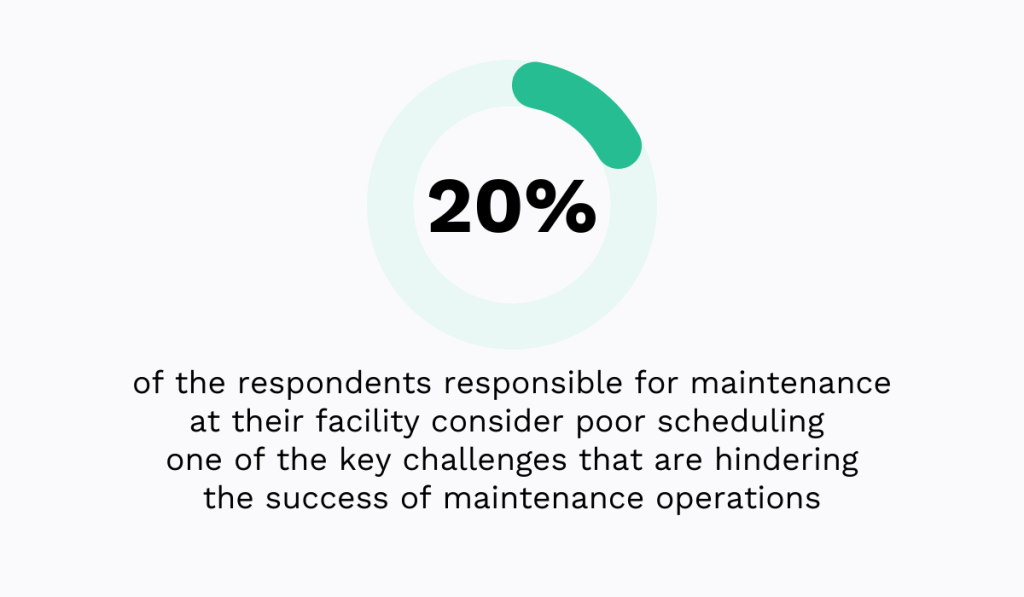
To make matters worse, respondents elaborate that maintenance schedules are rarely followed through.
This further highlights the importance of thoroughly reviewing the maintenance plan instead of just glancing at it and assigning the tasks randomly.
When you have a deeper understanding of the tasks that need to be completed and the reasoning behind them, it becomes easier to develop a strategic and logical schedule.
That is precisely the kind of maintenance schedule that gets followed through and yields the desired results.
2. Confirming Resource Availability
Now that you know which maintenance tasks have to be done, it’s time to confirm that you have all the resources needed to complete them at the ready.
When we say “resources”, we mean all the tools, parts, supplies, safety equipment, documentation, and personnel required to execute the work orders successfully.
Your maintenance planner should ensure that all the necessary resources are readily available—and procure the ones that aren’t—during the planning phase.
Brandon Coombs, Senior VP for Operational Excellence at RS Integrated Supply, a global supply chain solutions provider for MRO, explains:
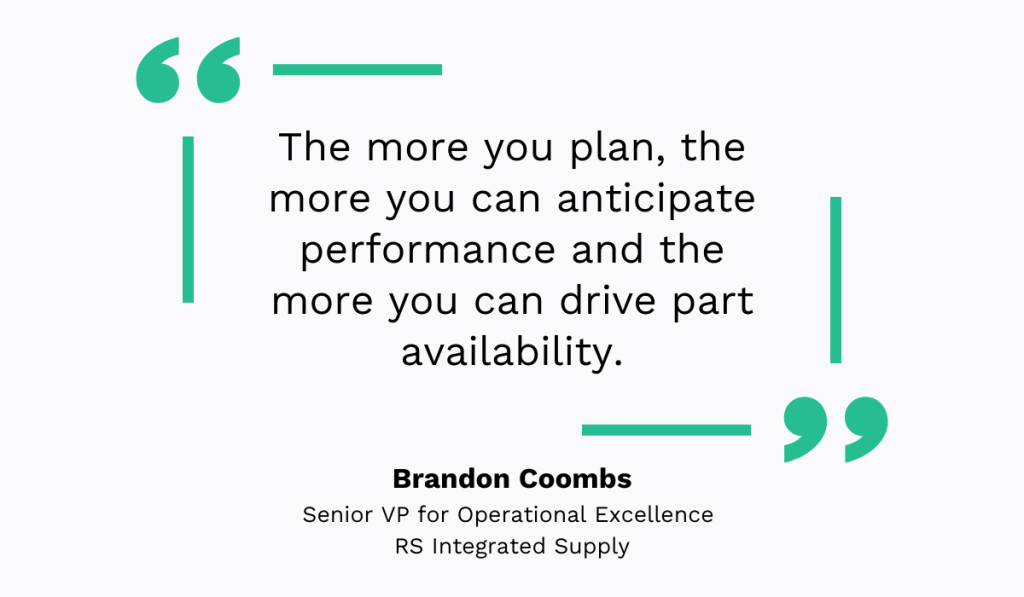
But the reality is that, despite even the most meticulous maintenance planning, circumstances can quickly change and affect the availability of resources.
Perhaps one of the maintenance technicians available for a specific task had to be suddenly relocated to a different facility because a piece of equipment in it unexpectedly broke down.
Or maybe the planner ordered all the spare parts your techs will need on time, but there was a delivery delay.
Scenarios like this are why it’s so important to double- and triple-check resource availability before you start adding maintenance tasks to the schedule.
RS Integrated Supply’s Solutions and Technical Director for UK and Ireland, Richard Jeffers, agrees.
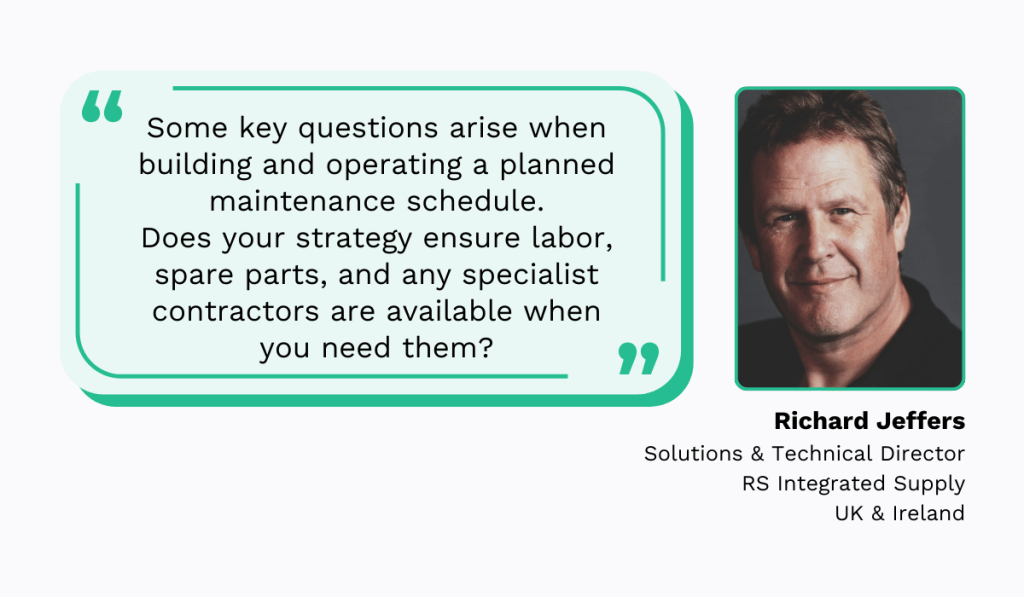
Verifying that all of the resources you’ll need are readily available will ensure that maintenance tasks are performed on time, ultimately preventing unplanned downtime and production delays.
To save you from the tedious and time-consuming process of manually checking resource availability, you can always turn to your CMMS.
Many such solutions come with spare parts and inventory features that will give you a quick overview of the quantities and locations of parts and materials.
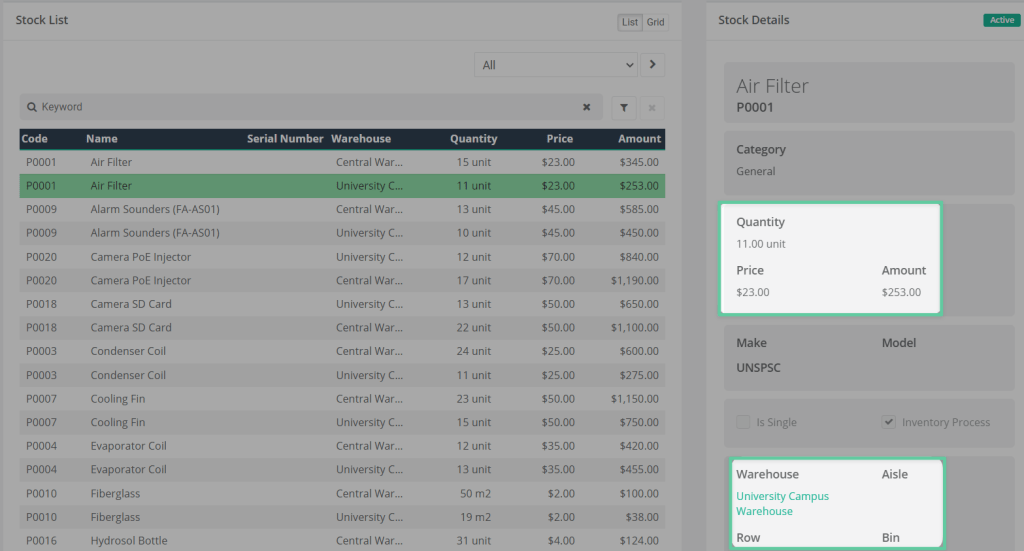
Overall, confirming resource availability during the maintenance scheduling process will help ensure everything is ready for the next step: defining when each task will be performed.
3. Determining When Maintenance Tasks Should Be Performed
Scheduling maintenance tasks at just the right time is a balancing act—more complex than it might seem.
First and foremost, maintenance itself can be time-consuming.
The previously mentioned Plant Engineering report found that, in 2021, facilities spent an average of 33 hours a week on scheduled maintenance.
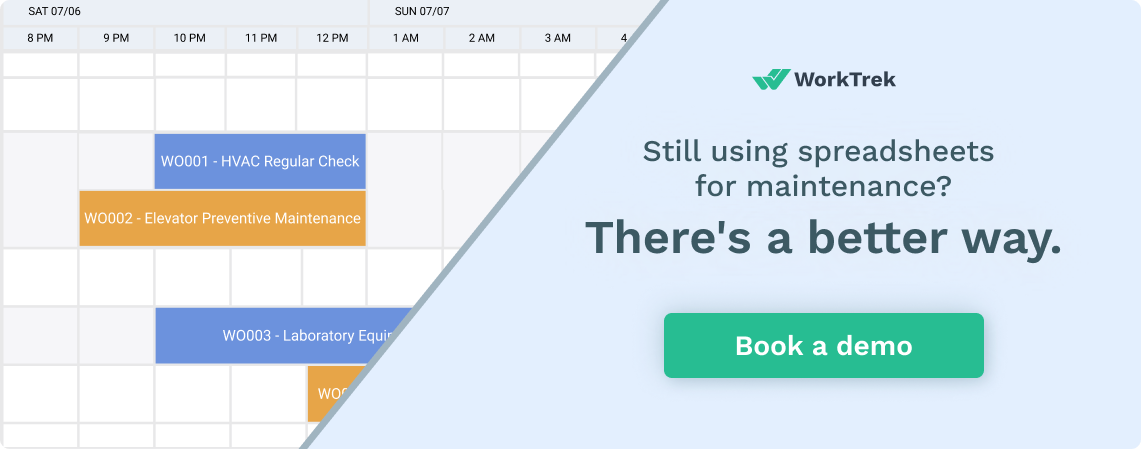
That is 13 hours a week more than a year before.
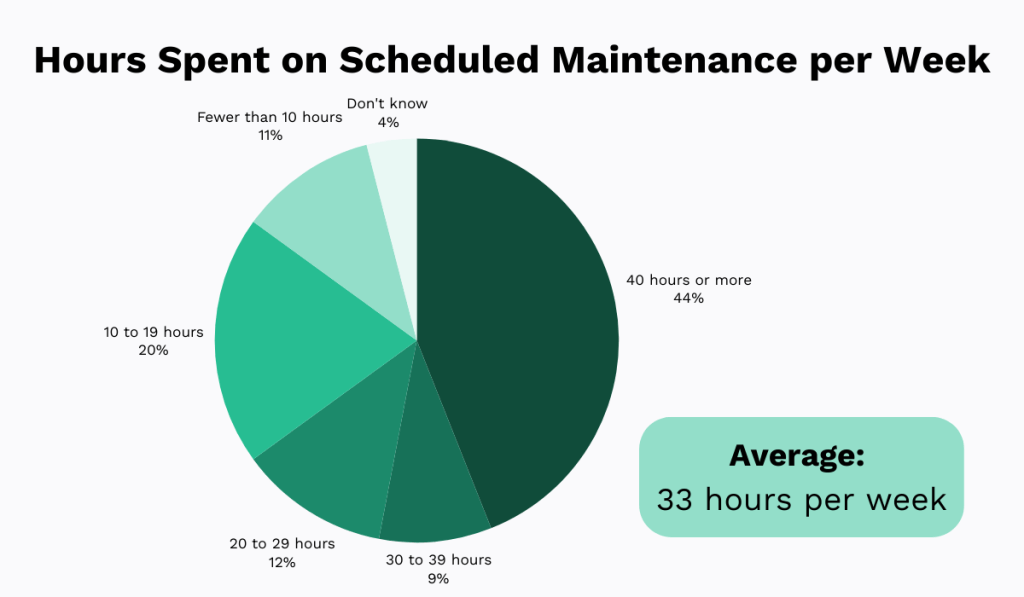
On top of that, there are many moving parts that come into play when determining when specific tasks should be completed.
For example, should you postpone that one task by a couple of days if performing it sooner could disrupt production?
But if you schedule it too late, could you potentially cause damage to the operations?
Yes, and yes, explains Edwin van Dijk, VP of marketing at TrendMiner, a provider of industrial analytics for optimizing production and manufacturing processes.
As you can see, many things have to fall into place to schedule maintenance tasks at just the right time.
It’s helpful to prioritize tasks on criteria such as asset importance and safety to make that challenging feat easier.
Let’s illustrate this point with a real-life example.
George Campbell, Director of Technical Services at a facilities management company, is a seasoned professional designing and implementing preventive maintenance programs for the company’s grocery store and retail clients.
He shares one of his own best practices:
Maintenance scheduling should be guided by how important the asset is to daily operations, giving high priority to safety concerns. For example, air conditioning, refrigeration of perishables, front doors, and generators during storm season would be high priorities for grocery and convenience stores.
Consider the effect of maintenance on your operations.
You wouldn’t want to perform maintenance on the ice cream freezer during a hot summer day when customers are looking for a sweet refreshment, right?
The bottom line is that trying to determine the perfect timing for the performance of maintenance tasks can be challenging.
However, if you consider the asset’s criticality, the availability of the necessary resources, and production schedules, you can get it just right.
4. Assigning Tasks to Appropriate Personnel
Once you’ve determined when specific tasks should be performed, it’s time to assign them to the right maintenance technicians.
Take plenty of time to consider which skills and expertise are required for these tasks.
After all, that’s the only way to ensure they are performed correctly, efficiently, and safely.
Below, you can find some key factors to consider when deciding which technician is the best fit for each assignment.
Technical Skills | The assigned technician should know how the equipment works, and how to inspect, diagnose, and repair issues. |
Specialized Certifications | The assigned technician should have the certifications and safety training required for specific maintenance tasks. |
Knowledge of Tools and Technology | The assigned technician should know how to use the tools and software needed to complete maintenance tasks. |
Level of Experience | The technicians’ level of experience and past performance need to be considered when assigning tasks, with more demanding tasks assigned to those with a higher experience level. |
Physical Ability | The physical capabilities of the technician should be taken into consideration to ensure the task is completed safely, with minimal chances of accident or injury. |
Technician Availability | The technician’s current workload should play a role during task assignments, making sure that the technician isn’t too overloaded to complete the task efficiently and thoroughly. |
Of course, it’s not always easy to ensure that the technician with the necessary skillset, experience, and certifications is available for a specific maintenance task.
Especially if you’re using messy and error-prone spreadsheets to keep track of maintenance activities.
Or even worse—nothing at all.
The findings of Comparesoft’s 2022 CMMS Market Report reveal that this is the case for many maintenance professionals looking to invest in a CMMS.
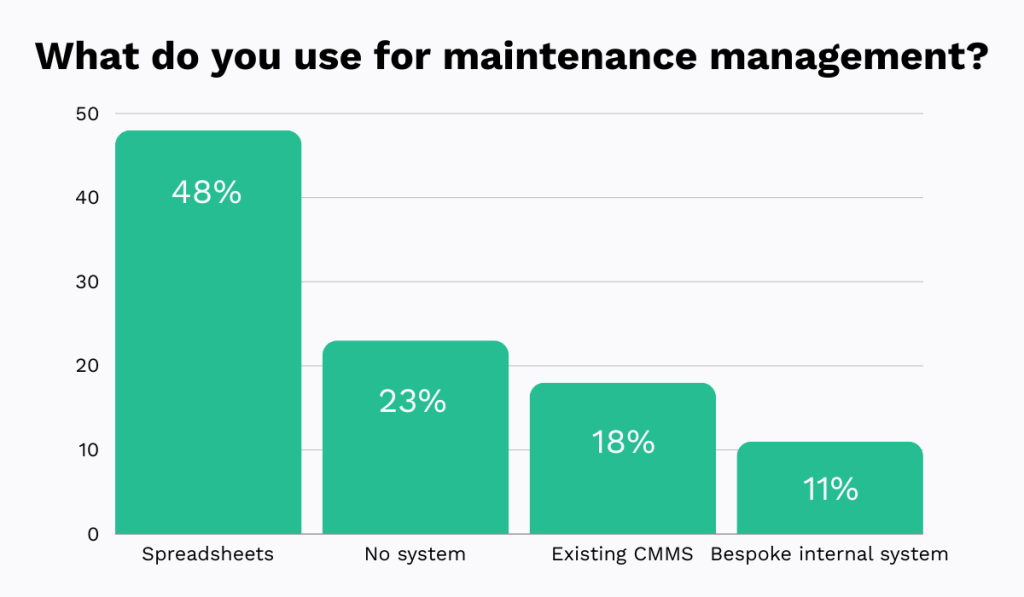
A CMMS is an invaluable tool for streamlining the entire lifecycle of a maintenance task, from creation to completion.
Take our maintenance management system, WorkTrek, as an example.
WorkTrek was designed to make maintenance scheduling a breeze, among other things.
As a scheduler, you can assign tasks to the most suitable technicians in just a few clicks, without having to dig through paperwork or spreadsheets to confirm they’re available when you need them.
Take a look at our Work Order Scheduler below.
It contains crucial details like maintenance task status, task execution time, and assigned technician.
Simply put, everything you need to know at a glance!
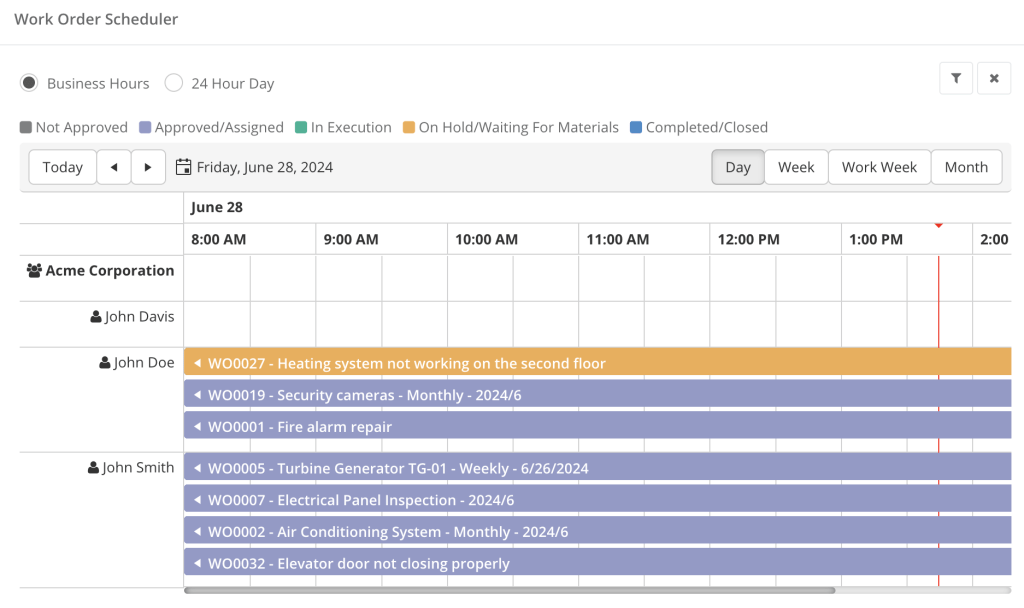
With WorkTrek, technician schedules that need to be shifted around due to oversights and task overlaps become a thing of the past.
So, if you still rely on manual methods for assigning maintenance tasks, consider investing in a solution like this.
Not only will it make your job quicker, easier, and more accurate—it will also significantly benefit your technicians.
Let’s see how.
5. Communicating the Maintenance Schedule
Once the maintenance schedule has been created, the natural next step is to share it with your maintenance technicians.
That way, everyone knows exactly what they’re responsible for and when each task needs to be completed.
But aside from ensuring all critical maintenance tasks are completed on time, having an insight into the maintenance schedule benefits your technicians, too.
Just ask Tim Newman, maintenance manager at Simmons Foods, a supplier of poultry, pet, and animal nutrition products.
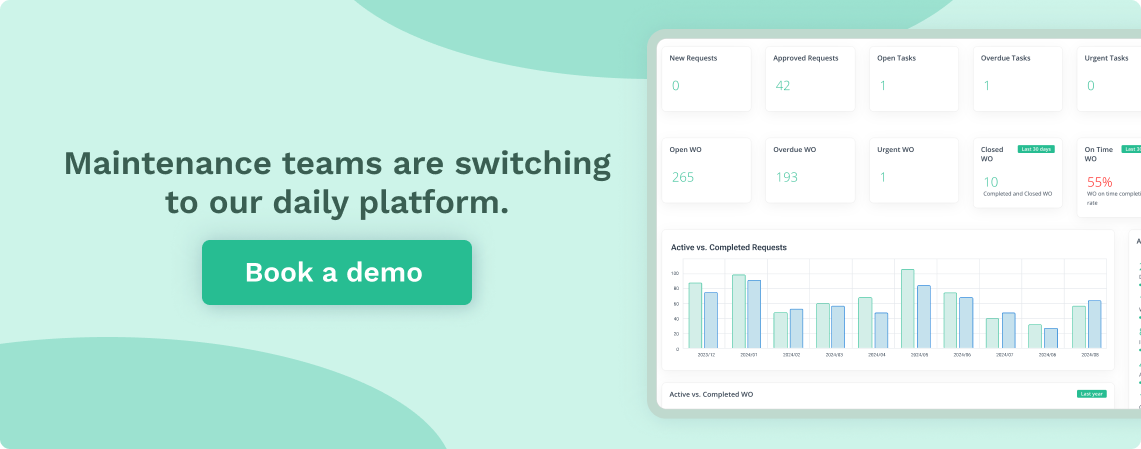
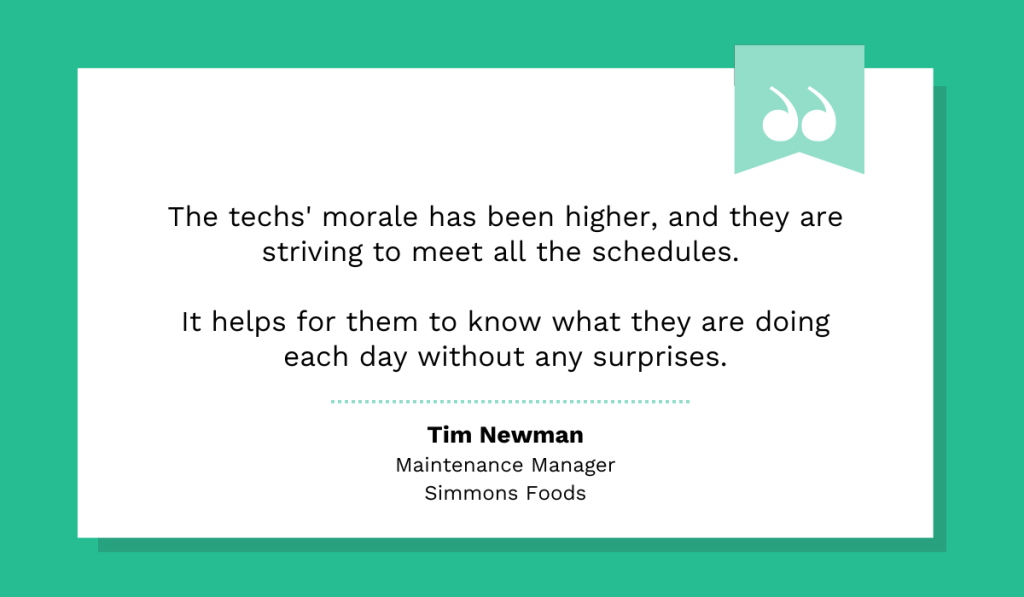
Having access to the maintenance schedule not only helps your technicians prepare for upcoming tasks but also boosts accountability and motivates them to meet deadlines.
The way we see it, making sure that your team has easy access to information about upcoming tasks is key.
Just like you don’t want to have to rifle through mountains of potentially outdated paperwork to check if that one tech with HVAC certification is available, your technicians don’t want to struggle to find out what their next task is.
Yet, this used to be the case at KONE, a global leader in providing and maintaining elevators, escalators, and automatic building doors.
Risto Alaluusua, formerly a lift technician and currently an inspection specialist, recalls the way things worked when he first started at KONE.
I have been with KONE for 25 years, and I remember having to visit the office to find out what was happening.
Nowadays, he explains, things are very different.
With the rise of CMMS, sharing the maintenance schedule with the relevant team members is easier than ever.
WorkTrek, for instance, comes with a mobile app that lets your technicians log in and check what tasks they’ve been assigned to from anywhere, at any time.
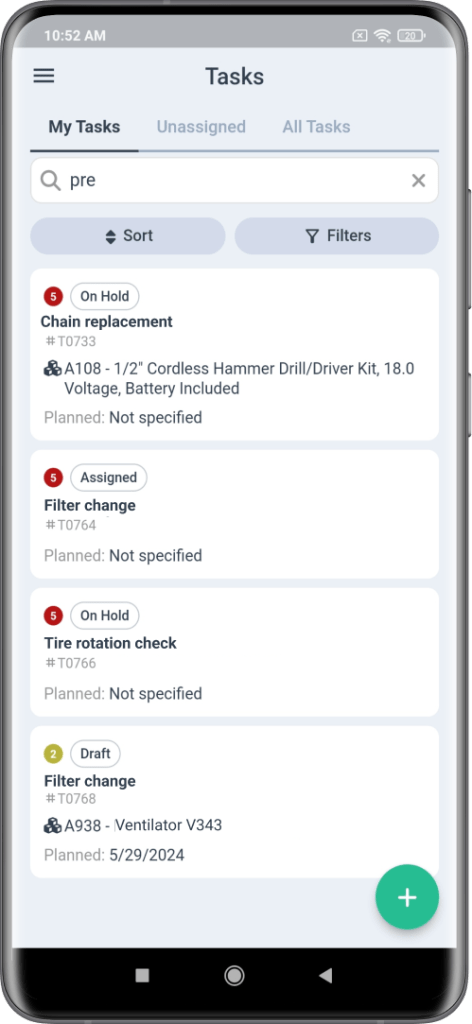
And our users love it, as evidenced by reviews like the one below:
The mobile application is a great tool for our field workers, it allows them to access and manage their tasks on-the-go.
Overall, communicating the maintenance schedule to your team in a timely manner is crucial for ensuring that all tasks are completed according to plan.
And technology like CMMS is there to take that to the next level.
6. Continuously Refining the Scheduling Process
The last step of the maintenance scheduling process actually occurs after maintenance has been completed.
Of course, we’re talking about improving the scheduling process itself.
Even with the help of maintenance management solutions, creating a schedule that works perfectly every single time is pretty much an impossible feat.
For example, an unexpected machine breakdown can shift maintenance timelines and increase the workload for some of your technicians.
And while consistently documenting and reviewing maintenance activities can help you identify any such patterns and improve the scheduling process, this is not the end.
If you truly want to refine the way you schedule maintenance tasks, why not talk directly to the people who complete them?
Below are some of the questions that you can ask them to identify potential issues and gaps in your scheduling process.
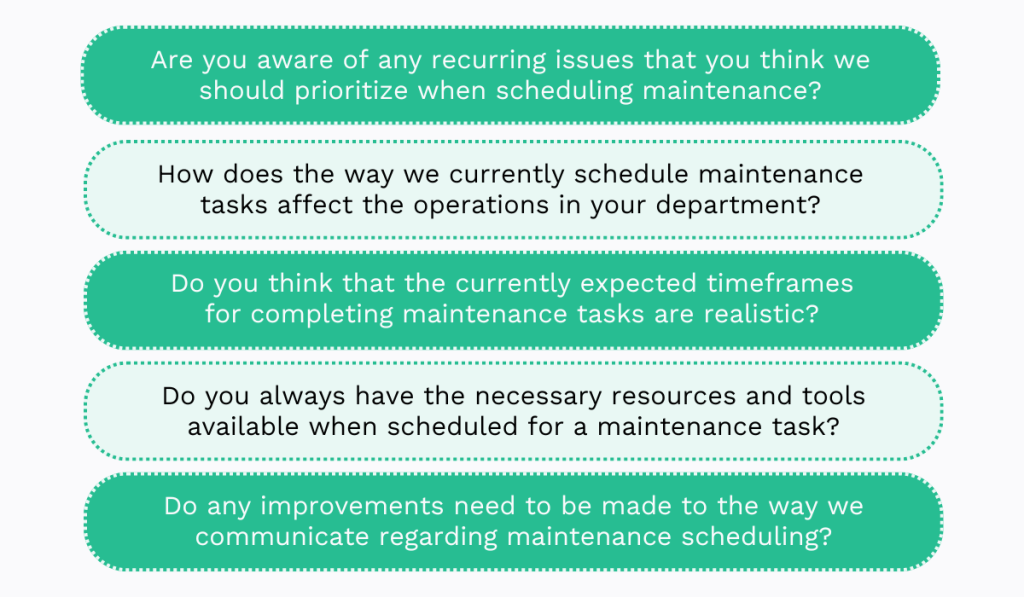
Your maintenance technicians are in the thick of it every day, so any feedback you gather from them will be invaluable.
Let’s say you’ve noticed that your technicians aren’t completing some of the maintenance tasks within the timeframes you’ve allotted for them.
This, naturally, snowballs and leads to unwanted production delays.
Instead of struggling to figure out why that’s the case—and potentially coming to the wrong conclusion—simply ask your technicians for their insights.
That way, you’re opening up the conversation and creating a space where they’ll feel comfortable speaking up going forward.
Consequently, you’ll be able to promptly address the timeframe issue, set more realistic expectations for production, and prevent future delays.
Conclusion
And with that, we conclude our step-by-step process to the maintenance scheduling.
We’ve broken it down into 6 phases, provided tips on how to best tackle each one, and shared some interesting statistics and real-world examples to illustrate the dos and don’ts of it all.
Hopefully, you feel inspired to refine the way you tackle maintenance scheduling—especially in terms of technology.
Relying on a CMMS to help you with this important part of maintenance management is bound to streamline your workflows, increase operational efficiency, and decrease unwanted delays and equipment downtime.
And what’s not to love about that?