Get a Free WorkTrek Demo
Let's show you how WorkTrek can help you optimize your maintenance operation.
Try for freeCMMS Meaning – Introduction
CMMS stands for Computerized Maintenance Management System. It refers to a software application or platform used by organizations to manage and streamline various aspects of maintenance activities, including scheduling, tracking, and reporting on maintenance tasks, resources, and equipment. CMMS software helps organizations optimize the maintenance of their assets, facilities, and equipment to improve efficiency, reduce downtime, and extend the lifespan of assets.
What Does CMMS Mean?
CMMS is software created to help the most modern companies (and those that are not yet modern, but want to try to modernize) manage and control their maintenance operations.
The implementation of a CMMS maintenance software within a company that until now has managed its maintenance activities with pen and paper or Excel sheets, is an operation capable of radically changing its work and obtaining important results with minimal effort (and in a much simpler way.)
At the same time, however, precisely because a CMMS is software dedicated to all types of maintenance, it is important to choose which benefits we want to obtain from our maintenance program.
We may be interested in reporting costs and working hours, planning scheduled maintenance activities, managing the warehouse, creating intervention requests and work orders in a simpler and faster way. And these are just some of the possible benefits of a CMMS maintenance.
This is also why it is good to be clear, when considering the possibility of adopting a CMMS for your maintenance, what benefits this tool will bring to our work.
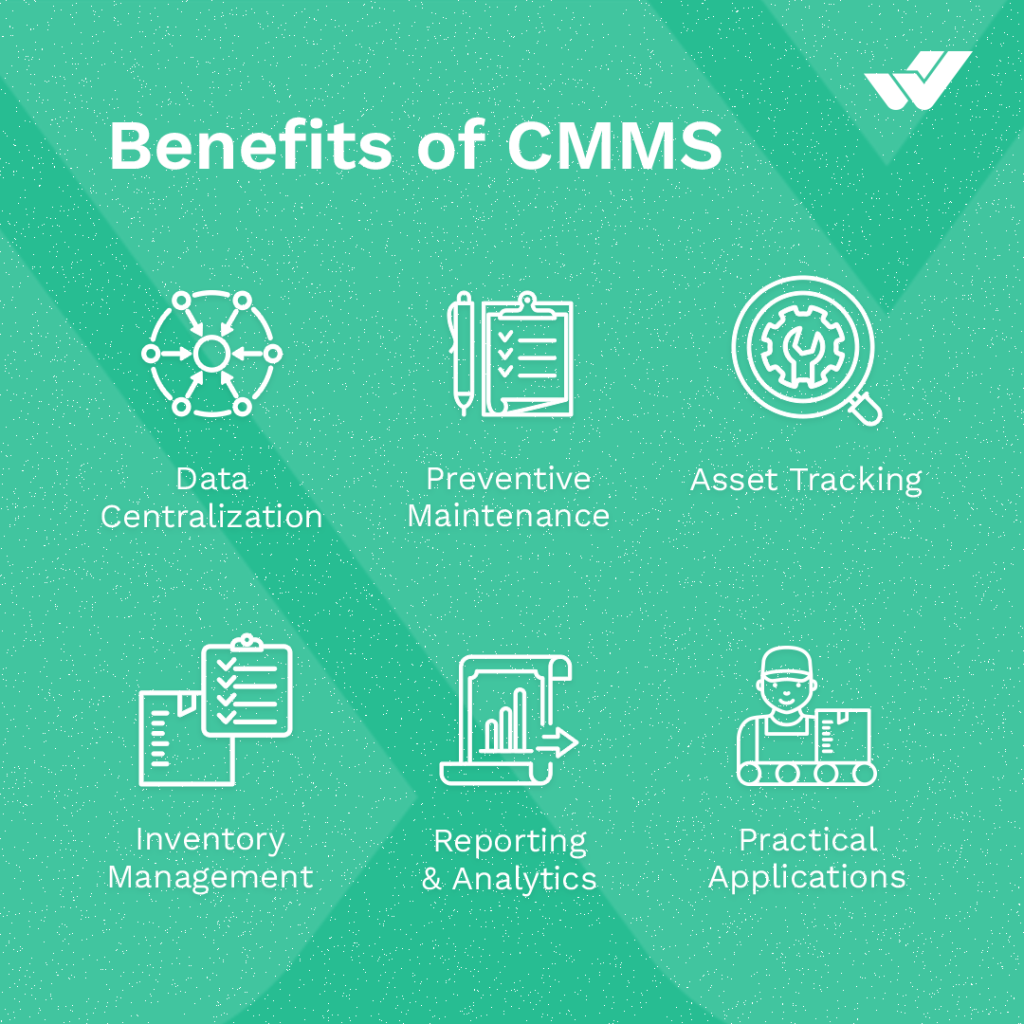
What Does CMMS Software Do and How Does it Work?
The CMMS is a software capable of containing all the maintenance information: from the technical database to the asset sheets, through maintenance plans, requests for technical intervention and work orders. It also allows you to manage all the documentation, the history of interventions and work reports, the spare parts in the warehouse, as well as of course the technicians and suppliers.
Thanks to all this information, it is able not only to help you optimize maintenance processes, but also to provide all the data necessary for a detailed analysis of them, monitoring times, costs and performance thanks to business intelligence systems that analyze the data for you, creating personalized and incredibly detailed reports.
The best CMMS software is also able to automate a large part of these processes, for example by automatically creating work orders or assigning them, always automatically, to the right personnel, based on the indications you have given to the system.
Let’s say for example that you need to plan preventive maintenance interventions based on the working time of a machine. The CMMS is able to generate a new work order every time this time is reached, inform you if spare parts are available in stock, attach the necessary documents and maintenance checklists to ensure that the interventions are carried out in the correct way and finally assign them to the personnel indicated on the basis of the machinery or its location.
This allows you to drastically reduce the costs and management times of your resources, as well as naturally machine downtime, also reducing manual actions and margins of error.
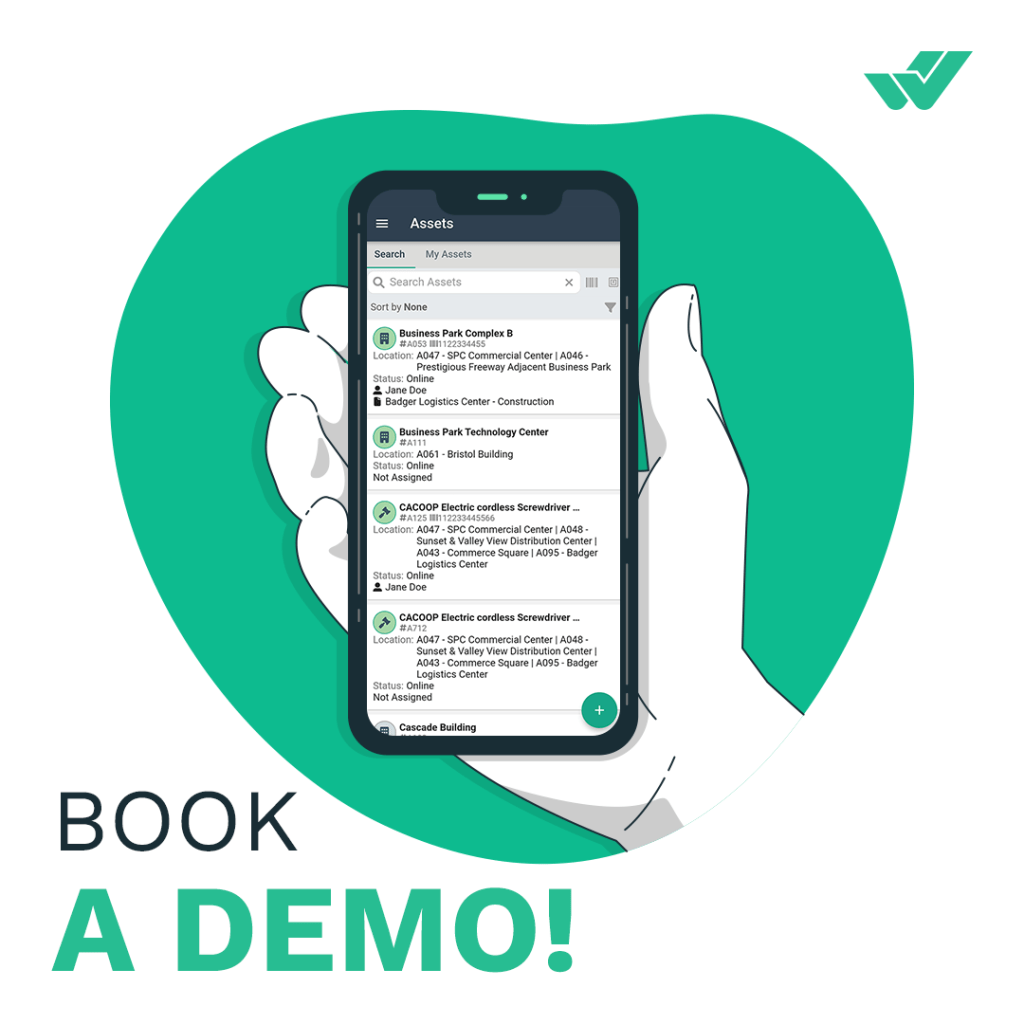
One of the most important features of CMMS systems is the ability to use the mobile app.
Thanks to the mobile app, technicians can take the CMMS for company maintenance with them wherever they go in the field. They will be notified via a simple notification (or an email) when they are assigned a work order, they will be able to consult the documentation, record the intervention times, take advantage of the checklists attached to the work order and add the pieces in just a few taps spare parts used on the final report.
This will allow them not only to cut intervention times, but also to automatically record all data and information relating to the work order within the CMMS system. Once the intervention is completed, they will be able to automatically generate the end of work report, create it directly on their phone and send it to the system (as well as by email to the figures involved).
At this point the CMMS system records the data and sorts them within the platform, where they will be available in real time.
Likewise, the maintenance manager will have a complete view of the progress of maintenance operations, will be able to easily monitor, without any additional action, the work orders carried out and those still to be carried out, as well as analyze the recorded data in real time.
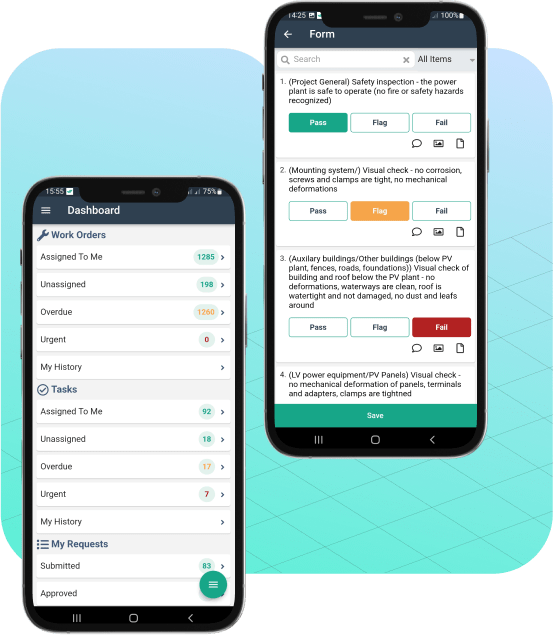
CMMS Meaning
CMMS software is a powerful tool that helps organizations efficiently manage their day-to-day maintenance operations while also facilitating the integration of new maintenance solutions, such as condition monitoring.
CMMS Meaning – Computerized
In the digital age, most processes have moved to computers. It was only a matter of time before the traditional clipboard and pen were replaced by modern technology. Leading CMMS software providers can easily integrate previous hard copy records into computerized interfaces, ensuring no data is lost when transitioning to computerized maintenance management software solutions.
Therefore, in the context of a CMMS, “computerization” refers to the use of computer technology and software to automate, streamline and manage maintenance-related tasks and processes. Computerized CMMS software enables companies to digitize and centralize maintenance management activities, including scheduling maintenance tasks, tracking work orders, managing inventory and spare parts, generating reports, and analyzing maintenance data.
CMMS Meaning – Maintenance
In CMMS (Computerized Maintenance Management System), “maintenance” refers to the process of maintaining, repairing or servicing assets, equipment, facilities or systems within an organization. This includes preventive maintenance (scheduling inspections and tasks to prevent equipment failure), corrective maintenance (repairing or replacing faulty components), predictive maintenance (using data to predict when maintenance is needed), and systems designed to ensure optimal condition for other tasks, activities and asset reliability and longevity.
CMMS Meaning – Management
CMMS plays a key role in helping management plan, schedule and report on maintenance activities. It enables leadership to predict and gain insights into financial reporting, compliance, auditing and other key maintenance performance indicators.
This includes:
- Planning: Plans and schedules maintenance tasks, inspections and repairs to ensure assets are properly maintained and downtime is minimized.
- Resource Allocation: Effectively allocate personnel, equipment, materials and other resources to efficiently carry out maintenance activities.
- Tracking and Monitoring: Monitor the progress of maintenance tasks, track work orders, and record maintenance history to ensure compliance with maintenance plans and standards.
- Reporting and Analysis: Generate reports, analyze maintenance data and identify trends to make informed decisions, optimize maintenance processes and improve asset performance.
- Optimize: Continuously improve maintenance strategies, processes and operations to maximize asset reliability, minimize downtime and reduce maintenance costs.
CMMS Meaning – System
CMMS software is not designed to replace maintenance personnel; rather, it complements existing practices and increases the efficiency with which work is completed. CMMS software integrates seamlessly into current maintenance processes and allows users to tailor functionality to their specific needs.
Therefore, in the context of a CMMS (Computerized Maintenance Management System), “system” refers to a comprehensive software application or platform designed to facilitate the management and optimization of maintenance-related activities within an organization.
This includes:
- Software Platform: A CMMS system consists of software applications accessible through a computer or mobile device that enable users to enter, track, manage and analyze maintenance data and activities.
- Integrated Modules: CMMS systems often include integrated modules or functionality that cover all aspects of maintenance management, including work order management, preventive maintenance planning, asset tracking, inventory management, reporting and analysis, and more.
- Database Infrastructure: CMMS systems rely on database infrastructure to store and organize maintenance-related data such as asset information, maintenance schedules, work orders, historical maintenance records, and inventory levels.
- User Interface: The system provides a user-friendly interface that allows users (including maintenance technicians, supervisors, and managers) to interact with and use the CMMS software effectively. This includes functions such as data entry, task assignment, reporting, and data visualization.
- Automation and Integration: CMMS systems often include automation features to streamline maintenance processes, such as automatic generation of work orders, scheduling, and notifications. In addition, CMMS systems can be integrated with other software applications, such as enterprise resource planning (ERP) systems, asset management software, and IoT devices to facilitate data sharing and collaboration between different departments and systems.
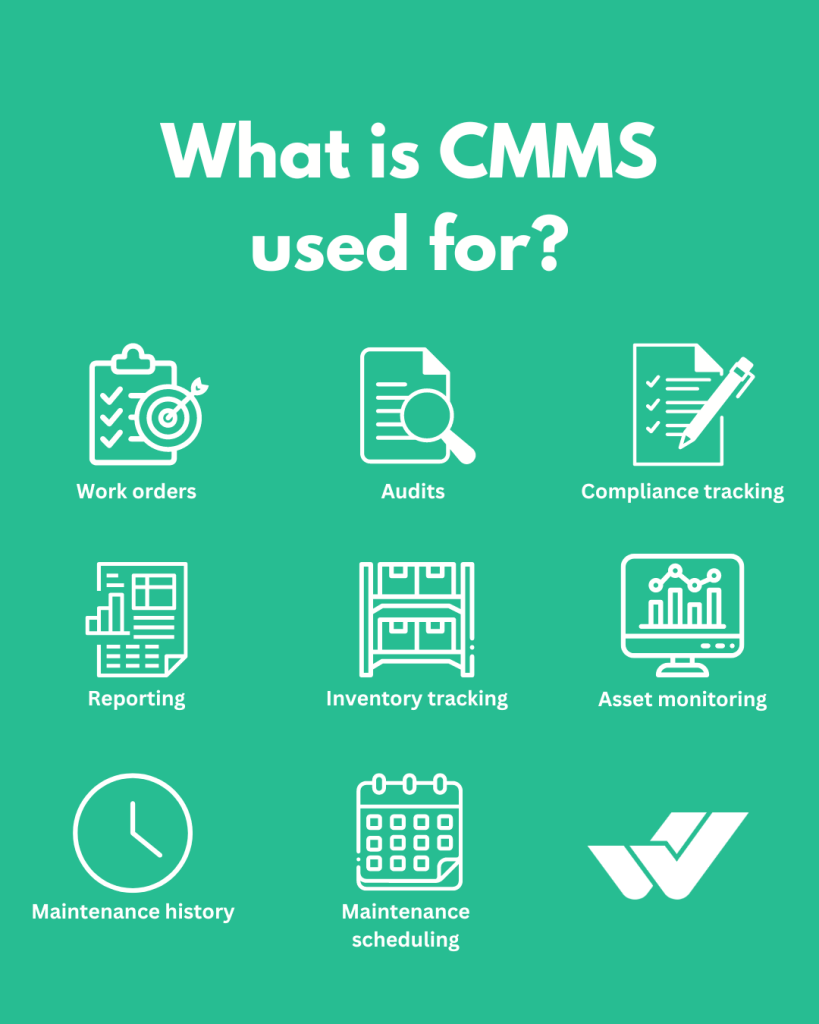
What are the Top 10 Benefits of a CMMS?
The 10 main advantages offered by CMMS software are:
- Plan Maintenance Interventions: Using a CMMS, you can create maintenance plans and execute them individually for each type of equipment. This makes it possible to develop different types of temporary interventions for each plant or group of plants with similar requirements.
- Process Work Orders Immediately: With a centralized system, work orders can be created, prioritized, submitted, and managed in an efficient and often automated manner, reducing the cost of paper documentation and programming.
- Reduce Maintenance Costs: A CMMS can help you track maintenance costs, monitor investments, create shared reports and save money with CMMS when needed.
- Real-time Asset Information: With data continuously collected in a centralized cloud, everyone can instantly get all the information about an asset with just one click, simplifying problem identification and intervention methods;
- Resource Monitoring and Control: To overcome issues related to shortages or excessive material costs, a CMMS allows you to monitor and manage resource inventory and track inventory items, special orders, or miscellaneous movements.
- Accelerate Inspections and Repairs: By constantly monitoring resources, repairs and inspections can be accelerated and unplanned downtime reduced. In fact, a CMMS allows you to view the history of problems and repairs in order to intervene in the shortest possible time.
- Extended Asset Life: Resources that are continuously monitored and maintained in an efficient condition through inspections and planned temporary interventions will naturally extend their useful life.
- Improved Safety: Damaged machinery poses a risk to both the work environment and the operator. The CMMS checks whether the equipment is operating within a specific safety area and signals appropriate intervention if necessary, thus mitigating safety risks.
- Improve System Compliance: Managing security programs and monitoring regulatory compliance is fast and easy. As a result, maintenance audits can be completed in less time, with usable data and time and cost savings.
- Increase the Efficiency of Work Teams: The potential of a central platform can be harnessed to unify the activities of internal teams and coordinate with external partners, resulting in better workflows, better communication between parties and significantly reducing errors.
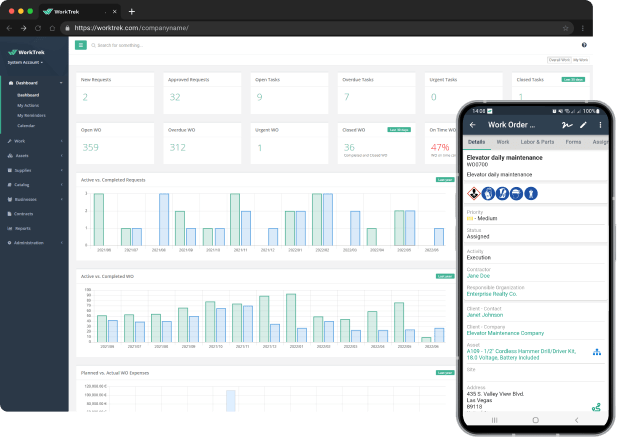
CMMS Meaning – Conclusion
Computerized maintenance management systems (CMMS) are critical to industrial operations. Whether you manage a server farm with mainframes that need regular updates or run a series of warehouses, a CMMS can automate most of your management tasks. It can automatically populate work orders with asset information, trigger alerts based on maintenance schedules, and monitor KPIs to prevent downtime.