Get a Free WorkTrek Demo
Let's show you how WorkTrek can help you optimize your maintenance operation.
Try for freePreventive maintenance program, or planned technical maintenance, consists of intervening on equipment at regular intervals or according to predefined criteria. Its primary objective is to reduce the risk of breakdowns on goods, machinery, and equipment, but it also makes it possible to achieve more general objectives.
This is why most factories and companies seek to increase the share of preventive maintenance implemented compared to corrective maintenance.
To implement a preventive maintenance strategy or plan, it is important to master the main aspects and know which tools can be used.
Read also 10 steps for choosing the right CMMS.
What is the purpose of preventive maintenance program?
Maintenance is carried out according to predetermined criteria, the objective of which is to reduce the probability of failure of an item or the degradation of a service rendered. So, it must make it possible to avoid equipment failures during use. The cost analysis must highlight a gain in relation to the failures it avoids.
Purpose of preventive maintenance:
- Increase the lifespan of equipment
- Decrease the probability of in-service failures
- Reduce downtime in the event of an overhaul or breakdown
- Prevent and also plan costly corrective maintenance interventions
- Make it possible to decide on corrective maintenance under good conditions
- Avoid abnormal consumption of energy, lubricant, spare parts, etc.
- Improving the working conditions of production staff
- Reduce the maintenance budget
- Eliminate the causes of serious accidents
What is the difference between preventive and corrective maintenance?
To summarize, we can say that corrective maintenance solves problems while preventive maintenance seeks to avoid them. Thus, corrective maintenance, sometimes divided between palliative and curative maintenance, occurs when a breakdown occurs on a machine or equipment. Preventive maintenance seeks, by means of checks and routine tasks, to verify that an item is functioning correctly and to identify any faults in its operation before it breaks down.
What are the different types of preventive maintenance?
There are 3 types of preventive maintenance:
- systematic maintenance;
- condition monitoring;
- predictive maintenance.
-
Systematic preventive maintenance:
Preventive maintenance program is carried out according to a schedule established according to the time or the number of units of use (produced). Therefore, even if time is the most common unit, other units can be used such as the number of products manufactured, the length of products manufactured, the distance traveled, the mass of products manufactured, the number of cycles carried out, etc.
This frequency of an intervention is determined by commissioning or after a complete or partial overhaul.
This method requires knowing:
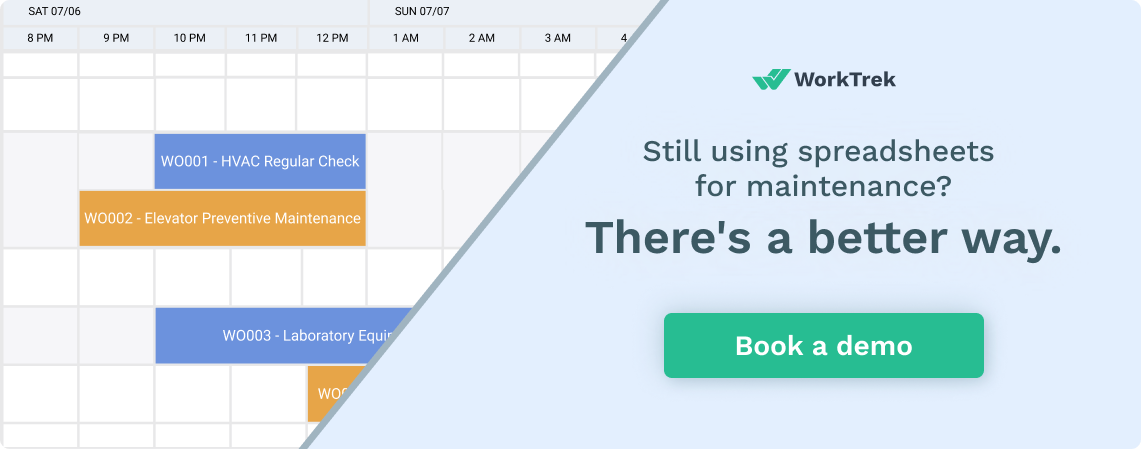
- The behavior of the equipment
- The modes of degradation
- The average time for good operation between 2 failures
Cases of application:
- Equipment subject to current legislation (regulated safety): lifting devices, fire extinguishers, pressure tanks, conveyors, elevators, goods lifts, etc.
- Equipment whose breakdown risks cause serious accidents: all equipment ensuring the public transport of people, planes, trains, etc.
- Equipment with a high cost of failure: elements of an automated production line, processes operating continuously (chemical or metallurgical industries).
- Equipment whose operating expenses become abnormally high during their service life: excessive energy consumption, lighting by used lamps, improper ignition and carburetion (thermal engines), etc.
-
Condition-based preventive maintenance:
Preventive maintenance program is subject to a type of predetermined event (self-diagnosis, sensor information, wear measurement, etc.). Condition-based maintenance is therefore maintenance that depends on experience and involves information gathered in real-time. It is also called predictive maintenance (non-standard term).
The highlighting of weak points characterizes conditional preventive maintenance. Therefore, depending on the case, it is desirable to put them under surveillance and, from there, to decide on an intervention when a certain threshold is reached. But the controls remain systematic and are part of the non-destructive control methods.
All materials are affected. This conditional preventive maintenance is done by relevant measurements of the equipment in operation.
The parameters measured may relate to:
- Oil level and quality
- Temperatures and pressures
- Tension and intensity of electrical equipment
- Vibrations and mechanical play
- Etc.
Some methods, such as vibration analysis or oil analysis, are very rich in terms of the information collected. Their understanding allows informed decisions to be made, which is the basis of conditional preventive maintenance.
-
Predictive maintenance:
Predictive maintenance consists of anticipating future failures on equipment, an object, a system, etc. Concretely, it is a question of anticipating a breakdown or a malfunction thanks to the accumulation of a set of data. Booming in recent years, predictive maintenance has had several advantages. It avoids, for example, the immobilization of a broken-down production system (with the resulting financial repercussions).
Read also 6 steps to implement the work order process.
So, predictive maintenance makes it possible above all to anticipate breakdowns and offers the possibility of intervening while avoiding a much more expensive repair. With predictive technology, maintenance costs are reduced by 10 to 40% and the number of breakdowns is halved. The savings generated result from several consequences:
- Reduced breakdowns and therefore equipment downtime
- Extending their lifespan
- Improving the reliability of equipment and therefore optimizing production
- Better spare parts inventory management
- A reduction in maintenance costs.
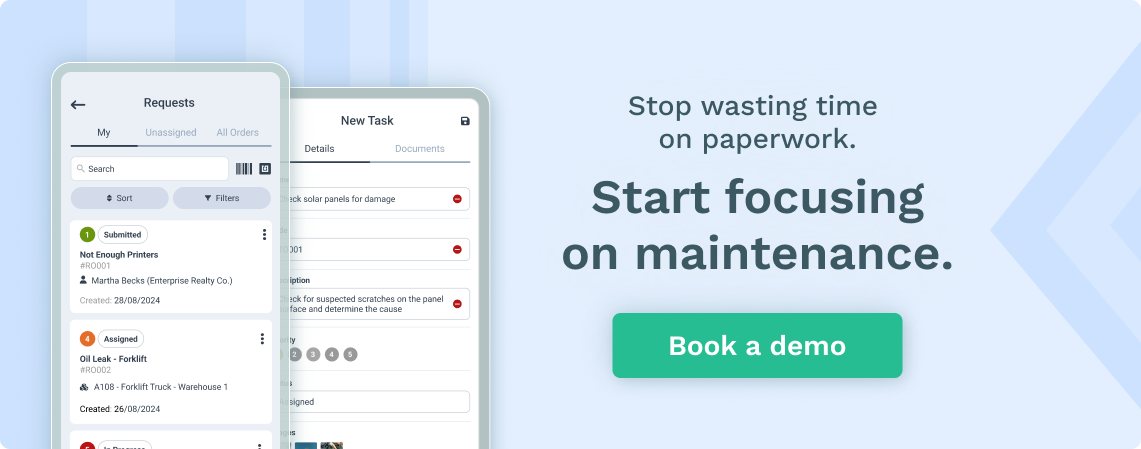
Preventive maintenance operations
Inspections:
Monitoring activities consist of periodically noting anomalies and carrying out simple adjustments that do not require specific tools or stoppage of the production tool or equipment.
Visits:
Monitoring operations which, as part of systematic preventive maintenance, take place according to a determined frequency. These interventions correspond to a list of operations defined beforehand which can lead to the dismantling of components and immobilization of equipment. A visit may result in corrective maintenance action.
Controls:
Compliance checks against pre-established data followed by judgment. Control can:
- Include an information activity
- Include a decision: acceptance, rejection, adjournment
- Lead, like visits, to corrective maintenance operations
Monitoring operations (checks, visits, inspections) are necessary to control the evolution of the real state of the asset. They are carried out continuously or at intervals that may or may not be predetermined, calculated over time, or the number of used units.
Conclusion
Start getting the most out of your assets and save money by pursuing a preventive maintenance strategy. Additional benefits: better organization and ongoing operations.
Although the adoption of preventive maintenance measures requires budgeting for regular service activities, in an industrial setting, it’s usually worth it, especially since when an industrial operation is shut down for unscheduled repairs, it can quickly lead to production stalling or even loss of revenue.
Read also 10 steps for CMMS implementation.