Get a Free WorkTrek Demo
Let's show you how WorkTrek can help you optimize your maintenance operation.
Try for freeRisk-based maintenance prioritizes maintenance tasks based on the risk associated with equipment failure. It is a strategy focused on optimizing resource allocation to enhance asset reliability and extend its useful life.
Risk-based maintenance goes beyond traditional maintenance approaches. It uses data and analysis to decide when and how to maintain assets.
Risk-based maintenance (RBM) aims to optimize resource allocation and minimize the likelihood of costly breakdowns by identifying critical assets and potential failure modes.
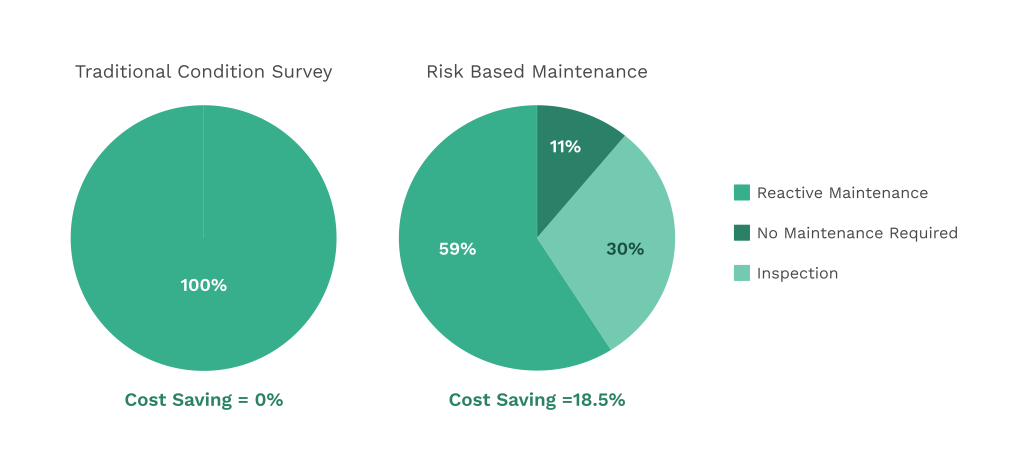
Source: WLC
This approach helps organizations balance the need for equipment reliability with the costs of maintenance activities.
By systematically assessing risk, companies can allocate their resources more effectively, focusing on the most critical assets that pose the highest risk to operations, safety, or financial performance.
RBM involves a continuous cycle of risk assessment, planning, and execution.
It requires gathering data on equipment performance, analyzing failure patterns, and evaluating the consequences of potential failures.
This information is then used to create tailored maintenance plans that address the specific risks associated with each asset.
Key Takeaways
- RBM prioritizes maintenance tasks based on equipment failure risks
- It optimizes resource allocation and improves overall asset reliability
- RBM requires ongoing risk assessment and data-driven decision-making
Fundamentals of Risk-Based Maintenance
Risk-based maintenance focuses on assessing and managing asset risks using maintenance data. Risk-based asset maintenance is a strategic approach that prioritizes resources towards the most critical assets based on their potential risk and consequences of failure.
It aims to optimize maintenance activities and resource allocation based on the potential impact of failure.
Definition of Risk-Based Maintenance
Risk-based maintenance (RBM) is a strategy that uses risk assessment to guide maintenance decisions. It considers how likely equipment will fail and what would happen if it did.
Based on asset health, RBM helps companies decide which assets need attention most. It considers risk probability factors like safety, environmental impact, and financial loss.
This approach differs from fixed schedules. Instead, it adapts maintenance plans based on changing risks.
Evolution of Maintenance Strategies
Maintenance strategies have changed over time. Early methods were reactive, fixing things only after they broke.
Next came preventive maintenance, which used set schedules. This was better but sometimes led to unnecessary work.
Risk-based Maintenance emerged as a more efficient and hybrid approach.
It combines data analysis with expert knowledge to target high-risk areas.
RBM helps companies:
- Save money
- Improve safety
- Increase equipment reliability
It’s part of a shift towards smarter, more flexible maintenance practices.
Benefits of Risk-Based Maintenance
Implementing a risk-based maintenance strategy offers numerous benefits to organizations. By prioritizing maintenance efforts on high-risk assets, businesses can minimize the likelihood of unexpected equipment failures, reduce downtime, and optimize maintenance resources. Some of the key benefits of risk-based maintenance include:
- Improved Asset Reliability and Longevity: By focusing maintenance efforts on critical assets, organizations can ensure they are well-maintained, reducing the risk of asset failure and extending their operational life.
- Reduced Maintenance Costs: Targeting high-risk assets allows for more efficient use of maintenance resources, reducing unnecessary maintenance tasks and overall costs.
- Enhanced Safety and Reduced Risk of Accidents: Properly maintained equipment is less likely to fail unexpectedly, which helps maintain a safer working environment and reduce the risk of accidents.
- Increased Efficiency and Productivity: Minimizing unexpected equipment failures and downtime leads to smoother operations and higher productivity.
- Better Allocation of Maintenance Resources: By identifying and focusing on high-risk assets, organizations can allocate their maintenance resources more effectively, ensuring that the most critical assets receive the attention they need.
- Improved Compliance with Regulatory Requirements: Regular and targeted maintenance helps meet industry regulations and standards and avoid potential fines and legal issues.
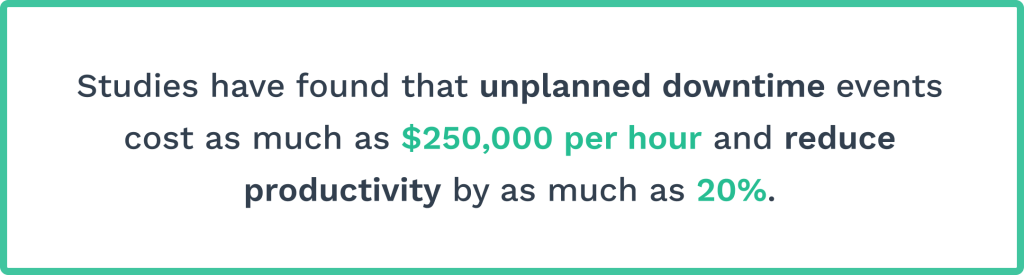
By focusing maintenance efforts on critical assets, organizations can ensure that their most valuable assets are adequately maintained, reducing the risk of asset failure and minimizing the impact of unexpected downtime.
Implementing Risk-Based Maintenance
Implementing risk-based maintenance requires a structured approach. It involves assessing assets, setting criteria, and creating a prioritization system. These steps help focus maintenance efforts where they’re most needed.
Assessment of Assets and Their Failures
The first step is to inspect all equipment, which means checking each machine or part. Teams need to know how often things break and why, and they also need to figure out what happens when asset failures occur.
Risk-based maintenance systems use real data from past breakdowns. This helps predict future problems. Teams should:
• List all assets
• Record failure history
• Note repair costs
• Track downtime
This info helps spot patterns. It shows which assets need more attention.
Risk Evaluation Criteria
Next, teams set up rules to measure risk.
These rules help decide how important each asset is. They look at two main things:
- How likely is it to break?
- What happens if it does break?
Once risks are identified, creating a risk mitigation plan is crucial for preventing asset failures and ensuring maintenance operations’ safety, efficiency, and cost-effectiveness.
Teams might use a scale like this:
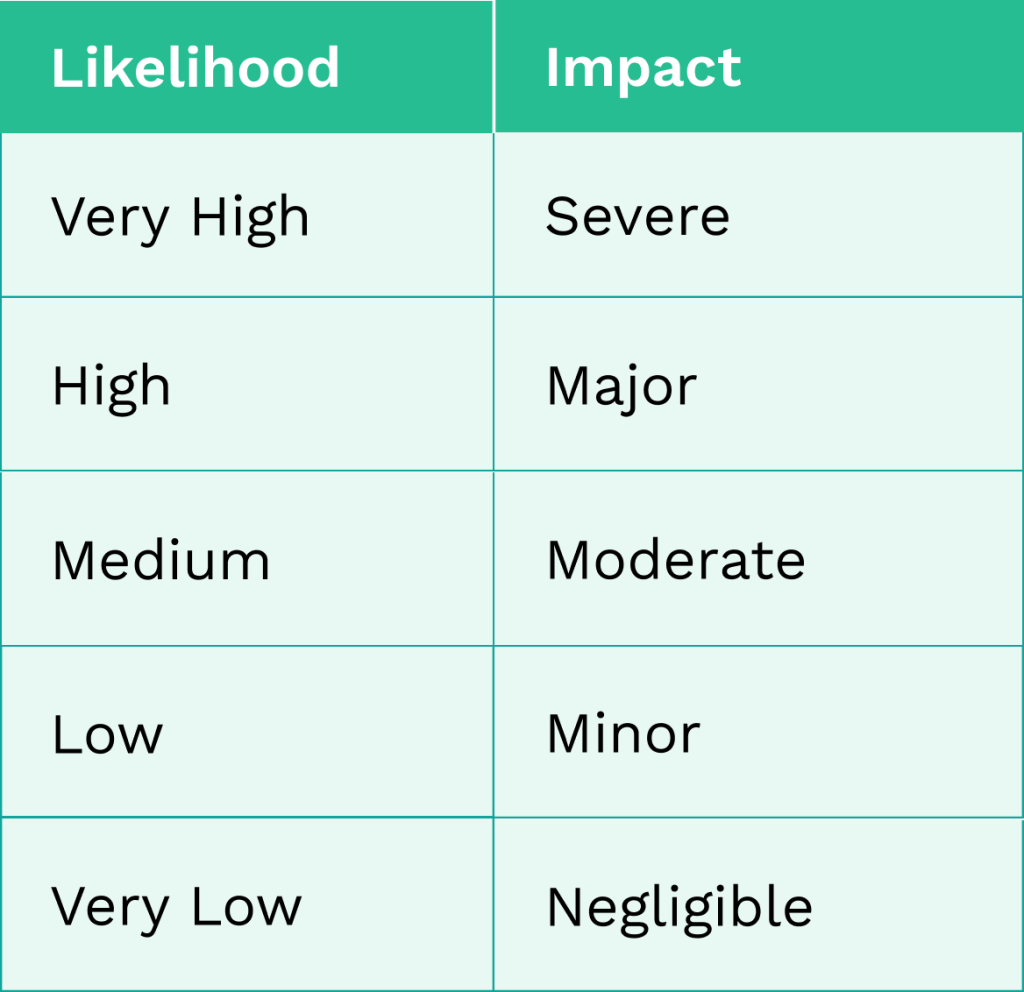
Each asset gets a score for both likelihood and impact. This helps rank them by risk level.
Prioritization Matrix
The last step is making a matrix to rank assets. This tool helps decide where to focus maintenance work. It uses the scores from the risk evaluation.
A simple matrix might look like this:
Impact → Likelihood ↓ | Minor | Moderate | Major |
---|---|---|---|
Low | 3 | 6 | 9 |
Medium | 2 | 5 | 8 |
High | 1 | 4 | 7 |
Assets with lower numbers get more attention. This helps with planning and using resources wisely. Teams can focus on high-risk items first.
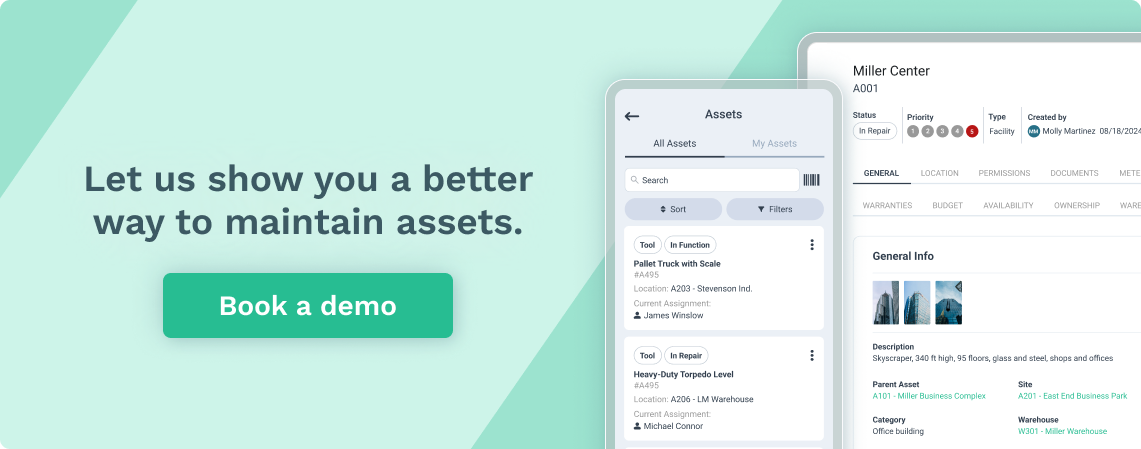
The matrix guides maintenance schedules and helps decide what checks to perform. High-risk assets might need more frequent or detailed inspections.
Creating a Risk-Based Maintenance Plan
Creating a risk-based maintenance plan involves several steps, each designed to optimize maintenance efforts and ensure the reliability of critical assets. Here’s a structured approach to developing an effective maintenance plan:
- Collect Data on Equipment and Assets: Gather comprehensive data on all equipment, including failure histories, maintenance costs, and other relevant information. This data forms the foundation of the risk assessment process.
- Conduct a Risk Assessment: Evaluate the potential risks associated with each asset. This involves identifying possible failure modes, their likelihood, and the consequences of such failures.
- Develop a Maintenance Strategy: Based on the risk assessment, create a maintenance strategy that addresses the identified risks. This strategy should outline specific maintenance tasks and their frequency.
- Assign Risk Scores to Each Asset: Use the risk assessment data to assign risk scores to each asset. These scores should reflect both the probability of failure and the potential impact of that failure.
- Prioritize Maintenance Tasks Based on Risk Levels: Rank maintenance tasks according to their risk scores. The maintenance schedule should prioritize high-risk assets.
- Schedule Maintenance Tasks and Allocate Resources: Develop a detailed maintenance schedule that includes all prioritized tasks. Allocate maintenance resources, such as personnel and tools, to ensure timely and effective execution of the plan.
- Review and Update the Maintenance Plan Regularly: Continuously monitor the effectiveness of the maintenance plan. Regular reviews and updates are essential to adapt to changing conditions and new data.
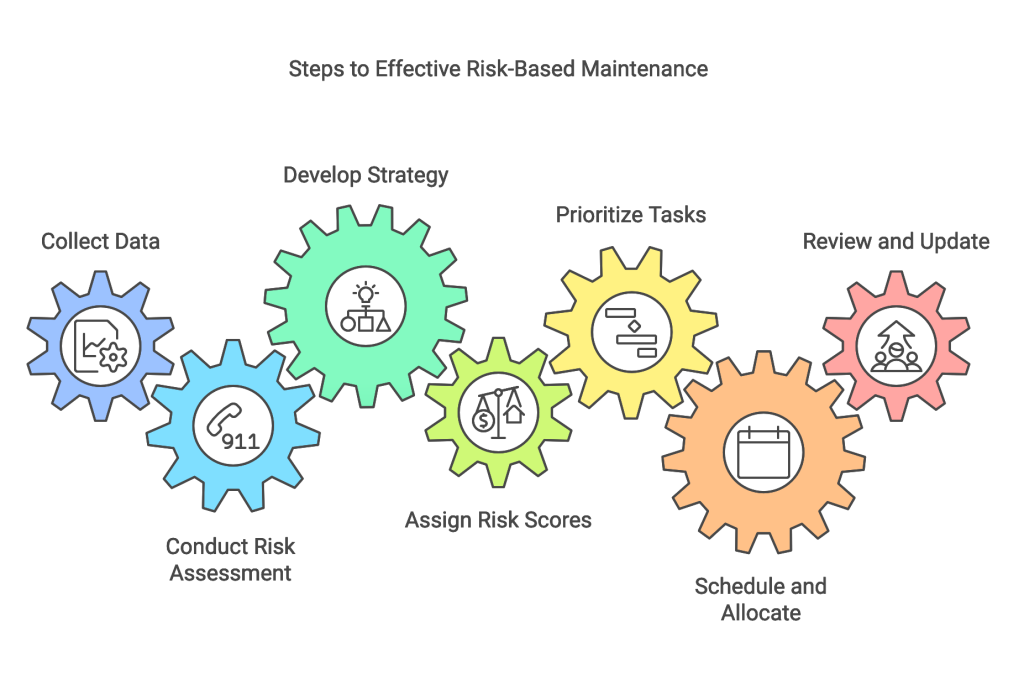
Source: WorkTrek
A well-structured risk-based maintenance plan can help organizations optimize maintenance efforts, reduce downtime, and improve efficiency.
By systematically addressing risks, companies can ensure their maintenance strategy is both proactive and effective.
Risk Management in Maintenance
Risk management is a key part of maintenance planning. It helps teams focus on the most critical assets and potential problems. This approach can save time and money while keeping equipment running smoothly.
Integration with Asset Management
Risk-based maintenance works hand in hand with asset management. Teams look at each piece of equipment and consider what could go wrong. They ask questions like:
- How likely is a breakdown?
- What would happen if it failed?
- How much would it cost to fix?
This information helps create a risk score for each asset. High-risk items receive more attention, and maintenance efforts are optimized across the facility to lower failure risks.
Regular checks and data collection are vital. They help spot issues before they become big problems. This proactive stance can prevent costly breakdowns and keep operations running smoothly.
Balancing Costs and Risks
Finding the right balance between maintenance costs and risks is tricky. Too much maintenance wastes money, while too little leads to breakdowns.
Risk-based maintenance helps find the sweet spot. It uses data to make smart choices about where to spend time and money. Here’s how it works:
- Identify critical assets
- Assess risks for each
- Plan maintenance based on risk levels
- Track results and adjust as needed
This method often leads to cost savings. It cuts down on unnecessary work while focusing on what matters most. Over time, it can boost reliability and cut overall maintenance costs.
But it’s not just about saving money. It’s about using resources wisely to keep everything running safely and efficiently.
Planning and Scheduling in RBM
Risk-based maintenance (RBM) relies on a risk-based maintenance approach involving careful planning and smart resource use. It focuses on fixing equipment based on how likely it is to break and how bad that would be.
Maintenance Planning
RBM planning starts with examining each piece of equipment. Teams check its age, use, and history of problems. They also consider what would happen if it broke down.
Next, they rank equipment by risk.
The highest-risk items receive the most attention, which helps avoid surprise breakdowns.
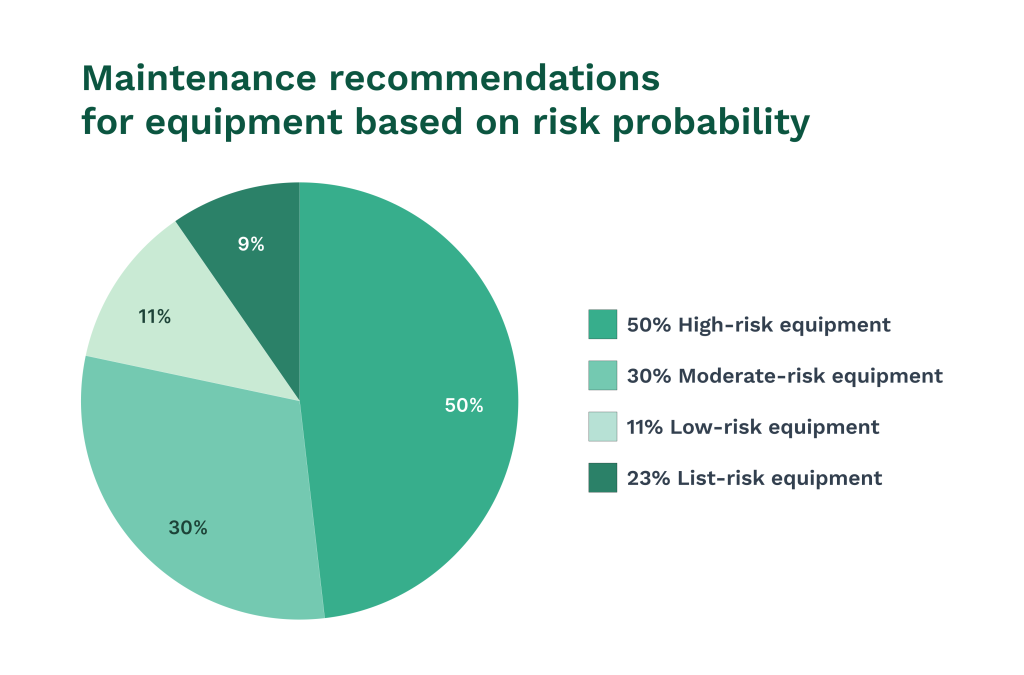
Illustration: WorkTrek / Data: blyPro
Teams then make a schedule. They decide when to check, fix, or replace each item. The plan changes as new information comes in.
Regular reviews keep the plan current, ensuring it matches the facility’s current risks and needs.
Resource Allocation and Optimization
RBM helps use maintenance resources wisely. It puts money and people where they’re needed most.
High-risk equipment receives more care, meaning more frequent checks or faster repairs. Low-risk items receive less attention, saving time and money.
Teams balance the cost of maintenance against the cost of failure. They aim to spend just enough to prevent big problems.
RBM also helps plan for parts and tools. It shows what might be needed soon so teams can be ready.
By focusing on risk, RBM maximizes every maintenance dollar and labor hour, resulting in fewer breakdowns and less wasted effort.
This approach is also ideal when organizations with limited resources reduce unplanned downtime.
Tools and Techniques
Risk-based maintenance uses specific tools and technologies to assess risks and predict equipment failures. These methods help maintenance teams make data-driven decisions and focus their efforts on critical assets.
Risk Assessment Tools
Risk assessment tools help identify and measure potential risks to equipment and systems. One common tool is the Failure Mode and Effects Analysis (FMEA).
FMEA looks at how equipment might fail and what impacts those failures could have.
Another helpful tool is the Risk Matrix. This visual aid helps classify risks based on their likelihood and severity. It uses color codes to show which risks need immediate attention.
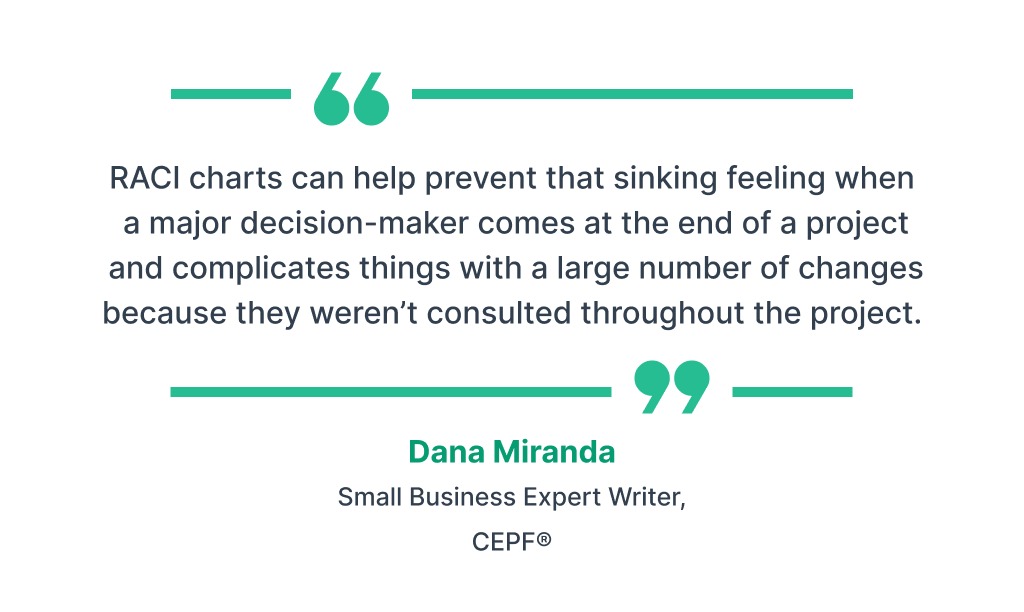
Fault Tree Analysis is also valuable. It maps out the chain of events that could lead to failure, helping teams understand complex systems and find ways to prevent problems.
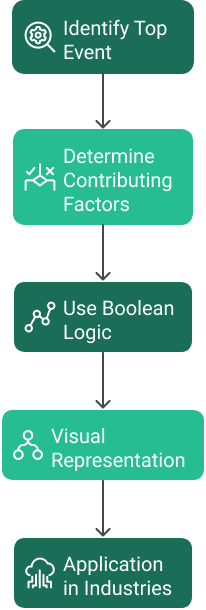
Source: WorkTrek
Predictive Maintenance Technologies
Predictive maintenance uses advanced tech to spot problems before they happen. Vibration analysis is a key method. It detects unusual vibrations in machines, which can signal upcoming failures.
Oil analysis is another important technique. It checks oil samples for signs of wear or contamination. This can reveal issues inside engines or other moving parts.
Infrared thermography uses heat-sensing cameras to find hot spots in equipment. These hot areas can point to electrical problems or excessive friction.
Ultrasonic testing helps detect leaks or cracks. It uses sound waves to find issues that can’t be seen with the naked eye.
Key Performance Indicators
Key Performance Indicators (KPIs) help measure the success of risk-based maintenance strategies. They provide data to assess maintenance effectiveness and drive improvements.
Measuring Maintenance Effectiveness
Mean Time to Repair (MTTR) is a crucial KPI for maintenance teams. It measures the average time needed to fix equipment after a failure. A lower MTTR indicates more efficient repair processes.

Source: WorkTrek
Mean Time Between Failure (MTBF) tracks the average time between equipment breakdowns. Higher MTBF values suggest better reliability and maintenance practices.

Source: WorkTrek
Preventive maintenance effectiveness measures how well-scheduled maintenance prevents breakdowns. It compares planned maintenance to unplanned repairs.
Work order performance tracks the completion rate and timeliness of maintenance tasks. This KPI helps identify bottlenecks in the maintenance process.
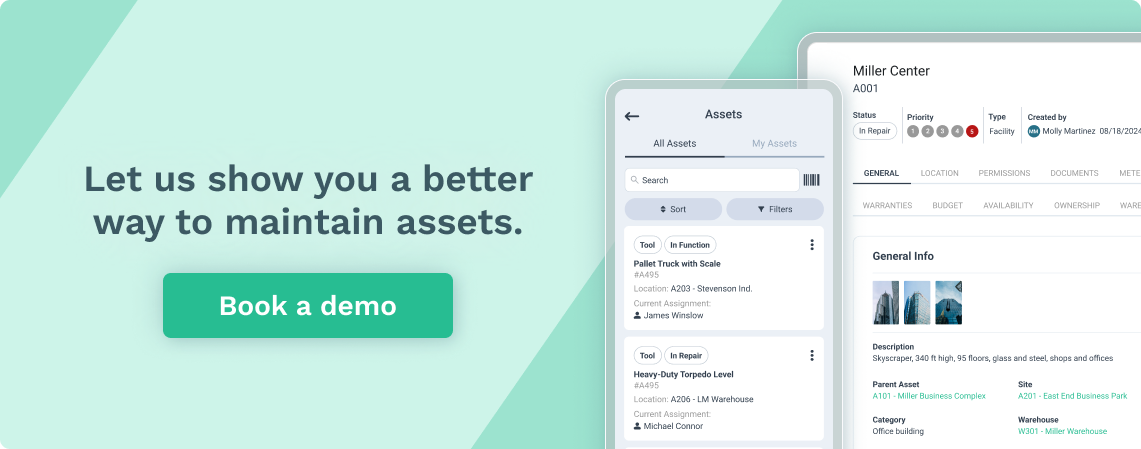
Improvement and Benchmarking
Asset maintenance costs provide insight into the financial impact of maintenance strategies. Tracking these costs helps identify areas for potential savings.
Reliability metrics, such as equipment uptime and availability, show how well maintenance efforts keep assets running. Higher reliability often translates to improved productivity.
Risk assessment accuracy compares predicted failure probabilities to actual outcomes. This KPI helps refine risk models over time.
Benchmarking KPIs against industry standards or past performance highlights areas for improvement. Regular review of these metrics drives continuous enhancement of maintenance practices.
Case Studies
Risk-based maintenance has proven effective across various industries. Companies have seen improvements in safety, cost savings, and equipment reliability.
Gulf Coast Chemical Plant
A chemical plant on the Gulf Coast implemented RBM for their fixed equipment, piping, and pressure relief devices. The results were significant:
- 65% reduction in inspection requirements
- Projected $3.2 million reduction in maintenance costs over 10 years
- Estimated $4.6 million in risk reduction savings over 10 years
- Potential for $8 million in savings over 10 years by increasing turnaround intervals
BPD Refinery
A 130,000 BPD refinery in the United States implemented an RBI program using RBMI software:
- Reduced risk exposure by $5.1 million per year
- Optimized inspection and maintenance plans, saving $1.2 million annually
- Significantly reduced the risk of loss of containment incidents
Dutch Utility Company
A utility company in the Netherlands conducted a Proof of Concept (PoC) for RBM:
- Applied to over 13,000 assets in electrical and gas systems
- Results showed more efficient and effective maintenance practices
- Most assets required less frequent maintenance
- Some assets maintained the same level or increased maintenance based on ambient conditions
- The company deemed the PoC successful and decided to implement RBM across the entire organization
Core Builder Machine Case Study
A study on a core builder machine demonstrated the benefits of integrating RBM with Cost of Unreliability (COUR) techniques:
- Maintenance intervals for critical components were optimized:
- Heater: reduced from 24 days to 6 days
- Roll: reduced from 48 days to 13 days
- Conveyor: reduced from 48 days to 23 days
- Maintenance costs decreased from $468,442 to $95,483 – a reduction of 79% in maintenance costs
These case studies demonstrate that RBM can significantly improve maintenance efficiency, cost reduction, and risk mitigation across various industries.
Lessons Learned
Companies found clear communication key to success. Teams needed to understand the new risk-based approach, and training staff on risk assessment methods was crucial.
Data quality proved vital. Accurate equipment histories and failure data were essential for good decision-making. Some firms had to improve their data collection first.
Many learned to start small and scale up. Beginning with pilot projects on critical equipment helped refine the process, allowing for adjustments before full implementation.
Flexibility was important. Risk profiles changed over time.
Successful companies regularly review and update their risk assessments.
Challenges and Solutions
Implementing risk-based maintenance comes with hurdles, but there are ways to overcome them. Companies can address common obstacles and improve their maintenance strategies over time.
Overcoming Implementation Barriers
Resistance to change is a major challenge when adopting risk-based maintenance. Staff may be used to old methods and hesitant to learn new ones.
To address this, companies should provide clear training and show the new system’s benefits.
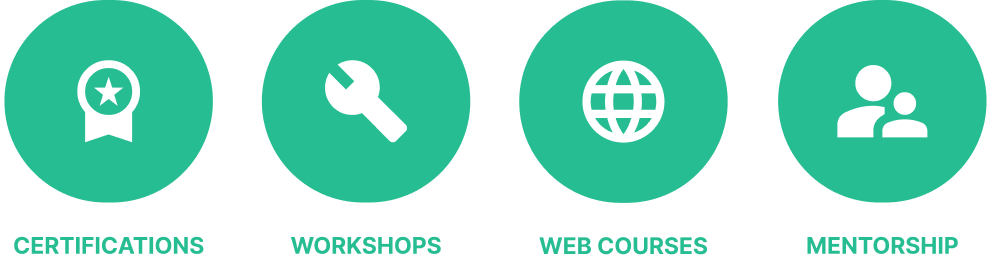
Data quality issues can hinder risk assessments. Incomplete or inaccurate data leads to poor decisions. The solution is to invest in reliable data collection tools and processes.
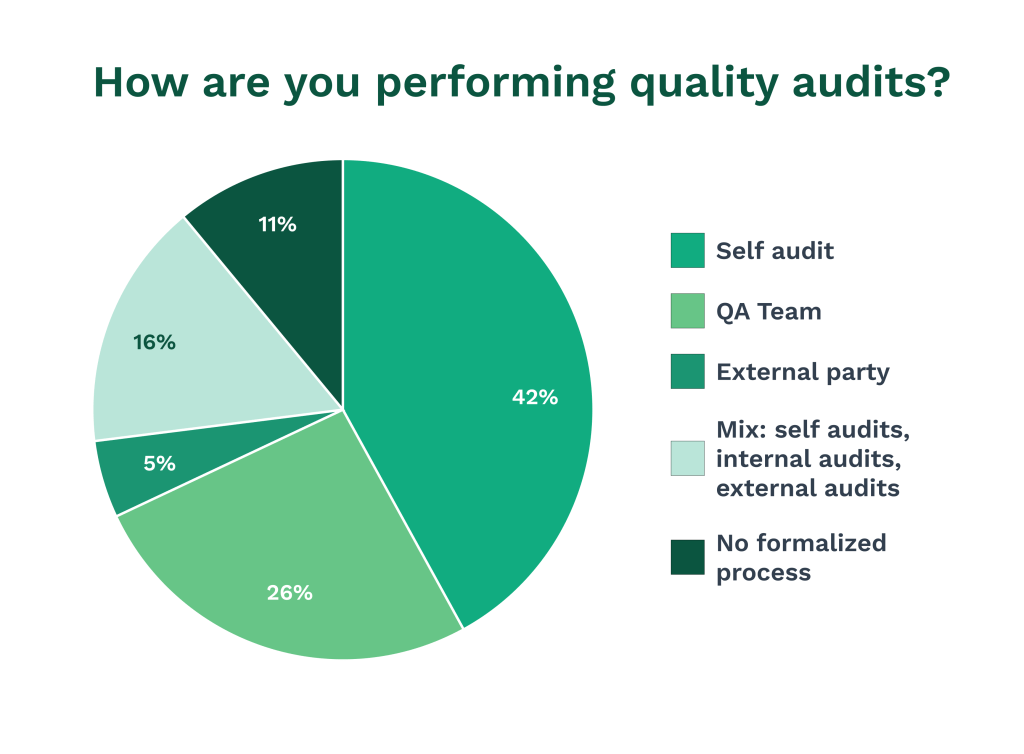
Resource constraints often limit implementation. Companies may lack time, money, or expertise. To overcome this, start with small pilot projects and gradually expand. Seek help from outside experts if needed.
Continuous Improvement and Adaptation
Risk-based maintenance needs ongoing refinement. Regular process reviews help identify areas for improvement. Set up feedback loops to gather input from maintenance teams and equipment operators.
Technology changes rapidly, so maintenance strategies must keep pace. Stay updated on new tools and techniques. Attend industry conferences and network with peers to learn best practices.
Adjusting to changing business needs is crucial. As production demands shift, so should maintenance priorities. Build flexibility into the risk assessment process for quick updates when conditions change.
Measuring success helps drive improvement. Track key performance indicators like equipment uptime and maintenance costs. Use this data to fine-tune the risk-based approach over time.
Conclusion
Risk-based maintenance (RBM) is a smart way to maintain equipment. It considers how likely things are to break and how bad it would be if they did.
RBM helps companies focus on what’s most important. This allows them to spend their time and money wisely on the machines that need it most.
This method uses data to make choices. It’s not just guessing or following a set schedule. RBM looks at accurate information about each piece of equipment.
Companies that use RBM can avoid big problems. They fix things before they break down, keeping the workplace safer and preventing costly shutdowns.