Get a Free WorkTrek Demo
Let's show you how WorkTrek can help you optimize your maintenance operation.
Try for freeKey Takeaways
- A CMMS simplifies maintenance management and reduces downtime.
- Automated spare parts alerts prevent repair delays.
- Inspection records identify recurring issues and ensure safety.
- Predictive maintenance boosts uptime by 10-20% using advanced technology.
Does it feel like your equipment is breaking down more than it should?
Perhaps you want to reduce downtime, cut costs, or keep your team focused on proactive tasks instead of scrambling to fix issues.
Whatever the reason, streamlining repairs and maintenance could be the key to running a smoother, more efficient operation.
In this article, we’ll cover five powerful ways to achieve this.
Combining all five will maximize your equipment’s lifespan and see notable improvements in efficiency, safety, and cost savings.
Let’s dive in!
Adopt a CMMS
Centralizing and automating maintenance tasks is essential to simplifying your workload, and that’s where a computerized maintenance management system (CMMS) truly helps.
A CMMS brings all aspects of maintenance management under one roof—from work orders and asset history to task scheduling and inventory tracking.
This level of organization is why 72% of maintenance professionals rely on a CMMS to streamline operations.
Take our own CMMS, WorkTrek, as an example.
It’s packed with features to streamline your maintenance tasks, making it easier to track equipment information and maintenance history all from a single cloud platform.
You can have every asset’s manual, safety requirements, and checklists accessible instantly.
That information lets you easily plan future maintenance tasks and schedule preventive maintenance based on time intervals or meter readings.
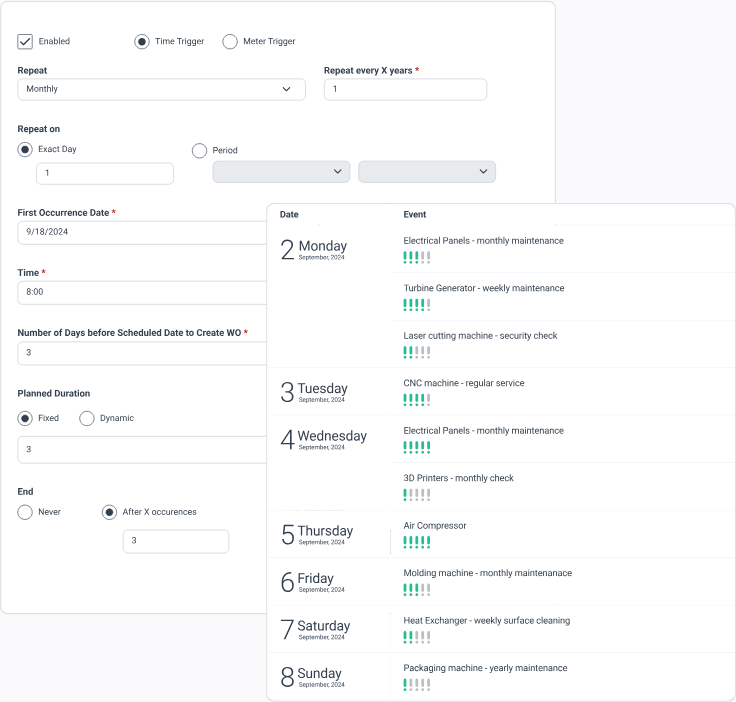
Moreover, thanks to our mobile CMMS, technicians can access information from the field, see exactly what’s needed for a repair, follow step-by-step instructions, and use the correct safety gear.
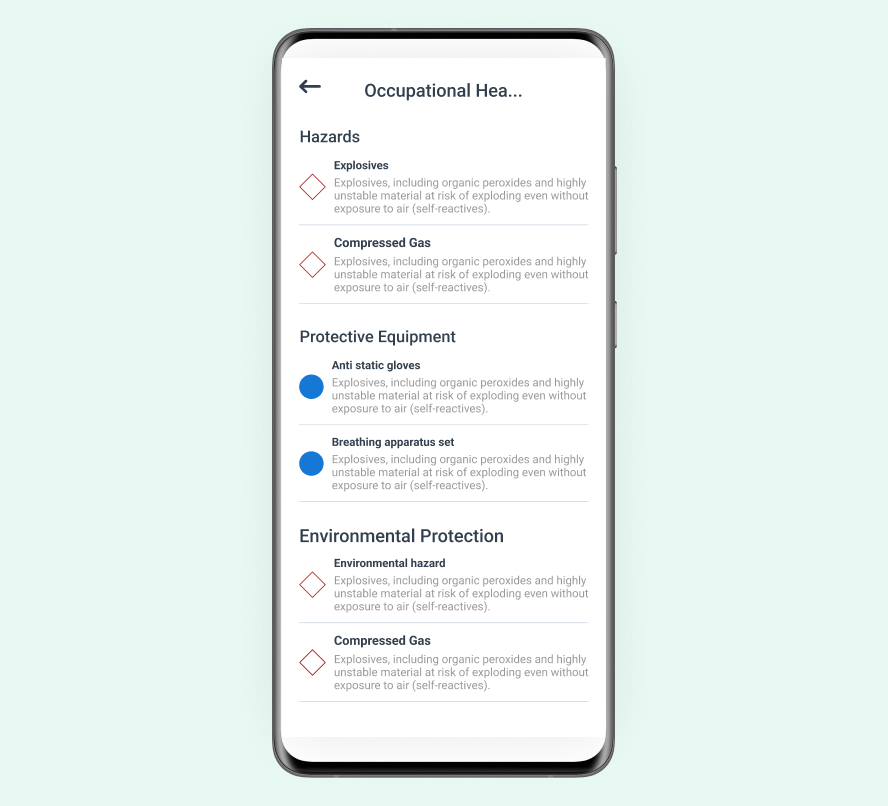
They can also quickly text a colleague if they need specific information or to troubleshoot a problem.
With this level of automation and organization, repairs and maintenance tasks are completed accurately and on schedule.
Besides this more operational maintenance workflow improvement, a CMMS can also help you make important decisions based on accurate data.
Let’s take budgeting as an example.
With WorkTrek, you can generate detailed reports on how much each work order costs.
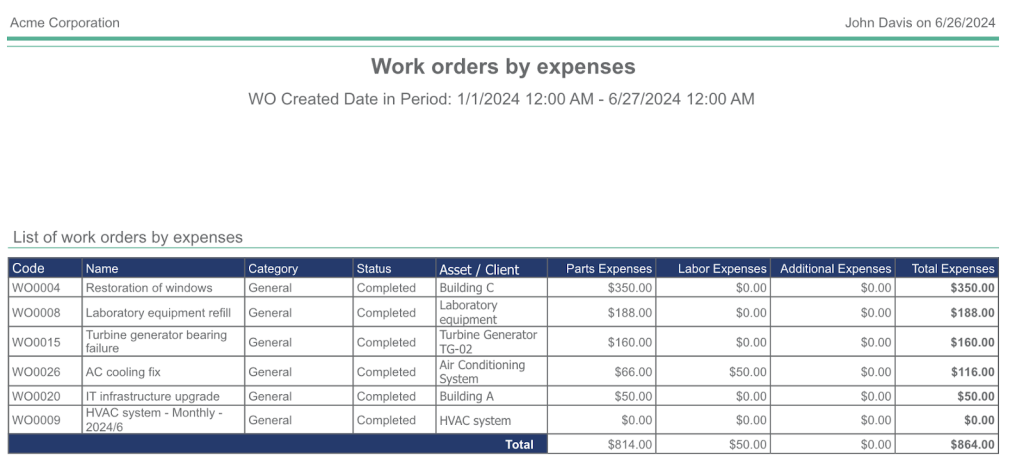
Then, you can analyze this data to understand spending patterns, budget more accurately, and avoid overspending on maintenance.
All in all, when you adopt a good CMMS with features that span from work order management and preventive maintenance scheduling to reporting and analytics, you streamline every maintenance step.
Organize Your Spare Parts Management
As you’ve likely experienced firsthand, nothing brings a repair to a standstill faster than a missing part.
Waiting for the correct part doesn’t just waste valuable time—it can also increase costs.
The shipping expenses skyrocket due to expedited shipping needs, and purchasing in smaller quantities increases prices per unit.
Moreover, as waiting for parts prolongs equipment downtime, it disrupts production schedules, ultimately impacting your facility’s bottom line and customer satisfaction.
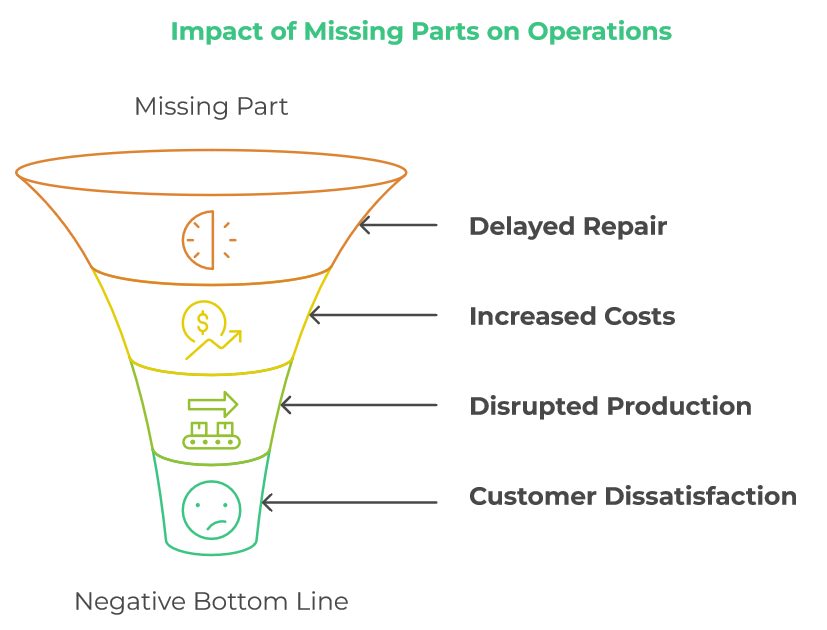
That’s why a well-managed parts inventory is essential.
To minimize downtime and prevent delays, maintain an organized inventory of frequently used parts and emergency spares.
Maintenance experts like Johan Romieu from Sanofi swear by this approach, claiming it can be a game-changer.
With the right parts, repairs stay on schedule, and your team can avoid scrambling for components.
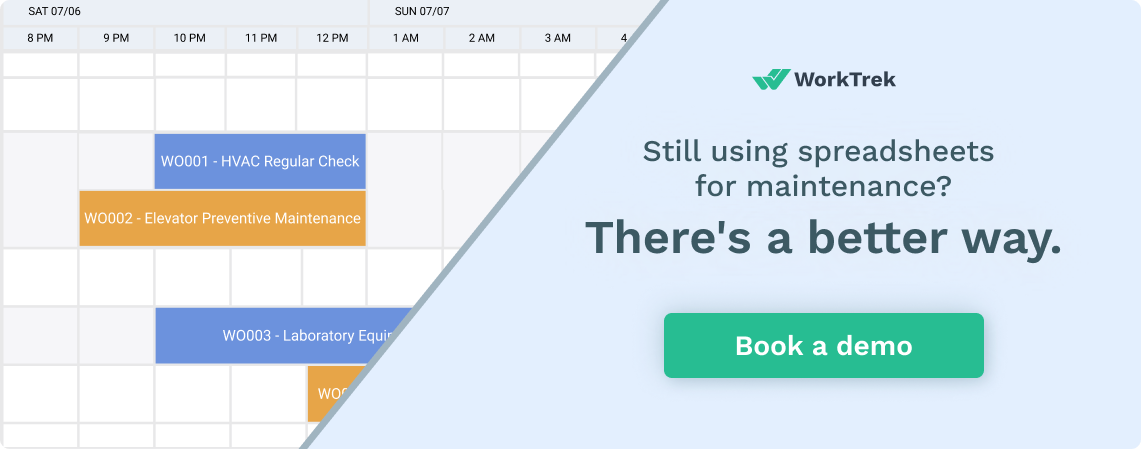
You can take spare parts management one step further by automating the reordering process.
With a CMMS, you can track parts usage and get automatic alerts when stock runs low, so you’re never caught without a crucial component.
For example, in WorkTrek, you can set low-stock alerts that notify you when inventory levels fall below a specified threshold.
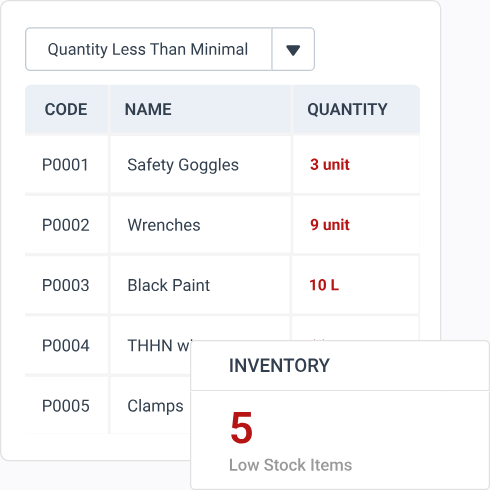
This way, you can stay stocked and carry out maintenance repairs more efficiently.
WorkTrek’s inventory capabilities extend beyond alerts and reordering.
Using barcodes or QR codes, you can track parts, access their histories across different warehouses, and even search by specific serial numbers for faster identification.
A CMMS also provides insights into parts consumption per machine or work order.
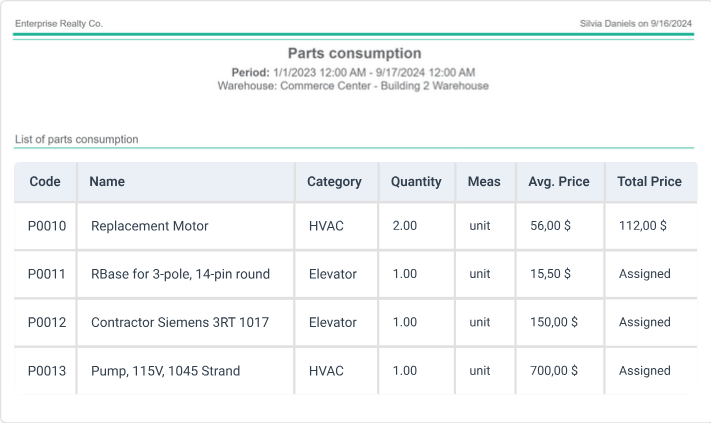
With this data, you have better control over spare parts costs and can streamline your maintenance process.
So, make sure to rethink how you manage your spare parts!
Conduct Regular Machinery Inspections
One of the simplest yet most powerful ways to streamline repairs and maintenance is by establishing a routine inspection schedule.
Routine checking and cleaning of your equipment keeps it in optimal condition, but you will also be more likely to notice potential problems before they grow.
For instance, an inspection might reveal an unusual noise from a machine—an early indicator of a mechanical issue you can address before it leads to a breakdown.
Beyond cost savings, regular inspections also help ensure the machinery is safe.
Dale Golgart from KPA, safety management and workforce compliance software, agrees:
Poorly maintained machines can lead to safety hazards and all sorts of incidents, so it’s crucial to stay ahead of these risks.
To make the inspection process thorough and consistent, develop a standardized checklist for each type of equipment.
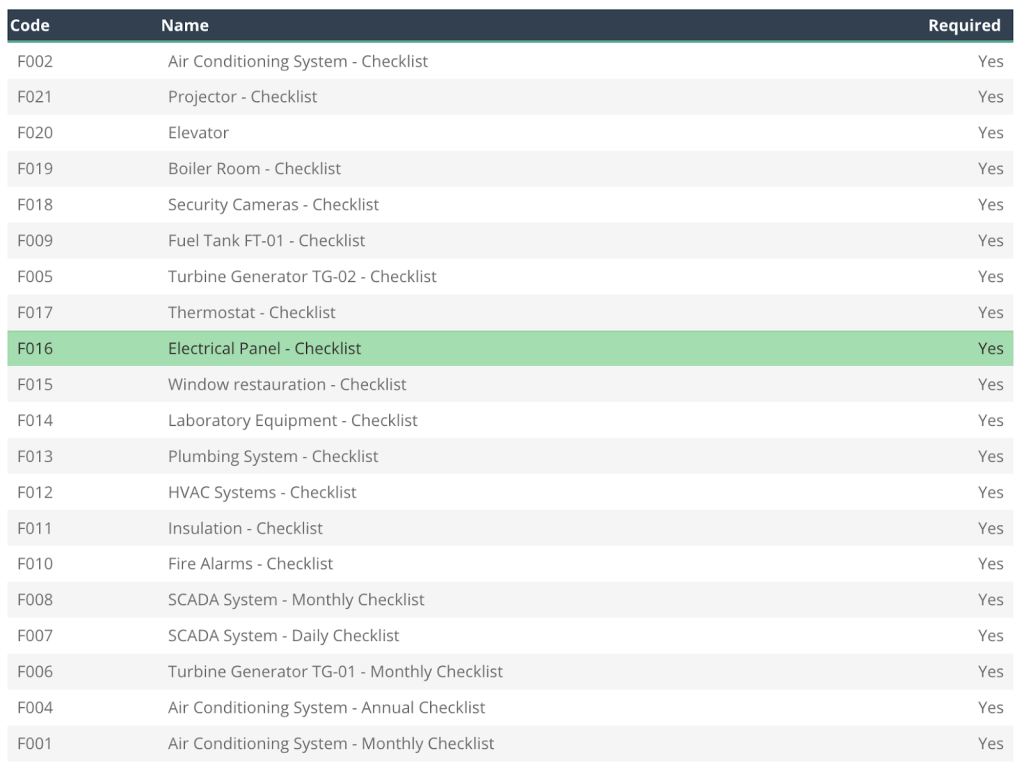
This checklist should outline what needs to be checked, like oil levels or filters, and specify how often these checks should be performed.
Some machines require oil checks every week, while others need them monthly.
To determine the best timeframe, follow the manufacturer’s maintenance manual.
This matters for multiple reasons, some mentioned in the quote by Tyler Smith, Product Manager at Volvo.
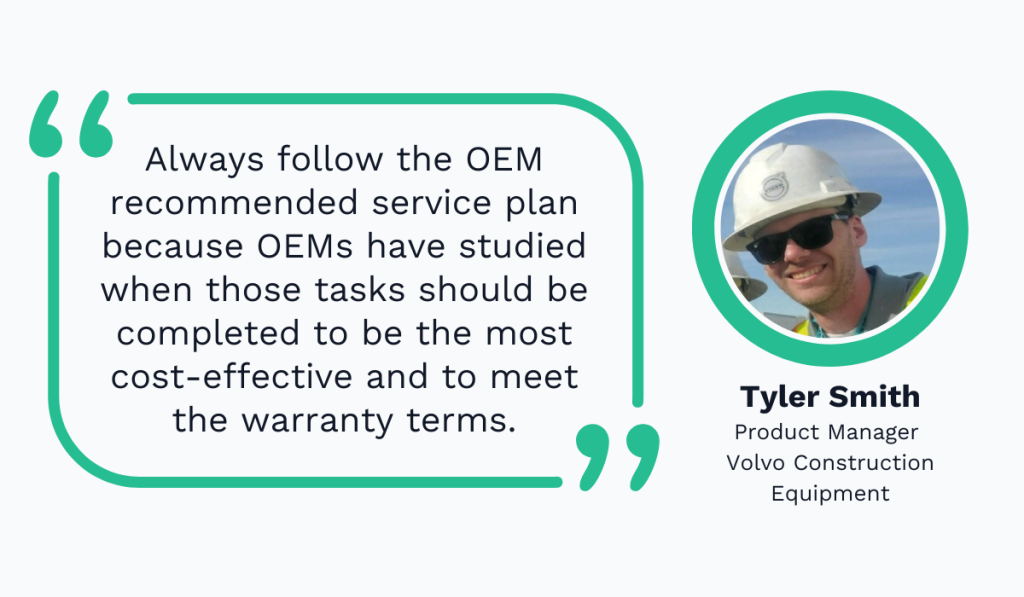
Keeping detailed records of each inspection is as important as the inspection itself.
Recording findings, actions taken, and repairs completed create a dependable history of each machine’s condition, which can guide future maintenance.
Karthik Preyeswary, Senior Inspector Engineer at DEMIRS, highlights the importance of this practice:
Therefore, document each inspection.
It will be easier to detect recurring issues and identify which machines need more frequent maintenance or replacement.
Additionally, detailed records support regulatory compliance, protecting your facility from potential liabilities.
Train Staff in Preventive Maintenance Practices
Preventive practices streamline maintenance, while reactive ones disrupt it.
Therefore, train your maintenance team on preventive practices.
When each team member knows how to handle basic tasks—like lubrication, cleaning, and regular inspections—small issues don’t escalate into major, disruptive problems.
To ensure your preventive maintenance training is effective, focus on these key areas:
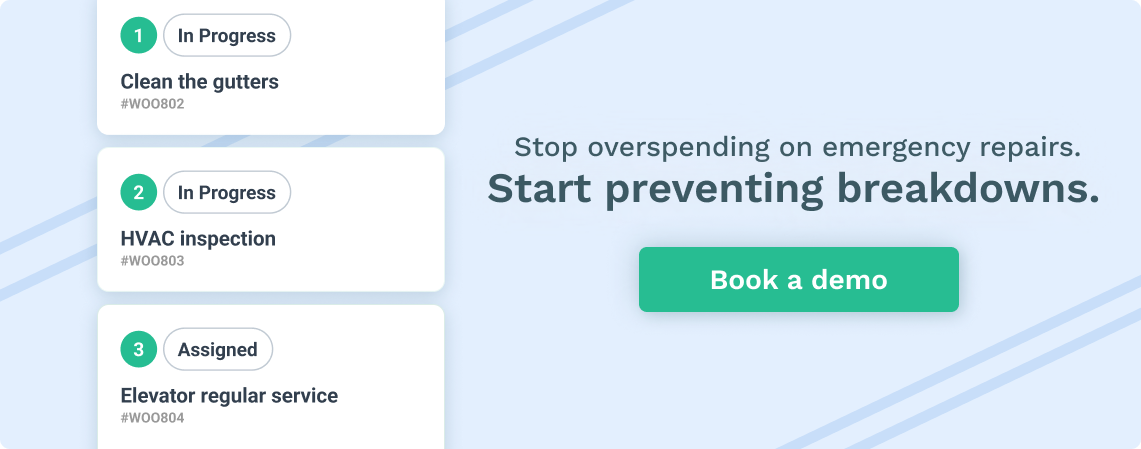
- Make sure your staff understands workplace safety practices, so they can work safely and avoid accidents.
- Provide core training on how your facility’s equipment works and what each component does.
- Teach staff to recognize early signs of trouble and how to troubleshoot problems quickly.
- Allow staff to work with actual equipment, building confidence and giving them real-world experience.
- Keep your team updated on the latest tools and techniques in maintenance to ensure they are using the best methods.
However, training alone isn’t enough; it must be accompanied by a cultural shift from reactive, last-minute repairs to planned, preventive maintenance.
Joe Kuhn, a seasoned plant manager and industry coach, highlights that many facilities still operate in a “reactive mode,” where the team feels comfortable “saving the day” when equipment breaks down.
Yet, moving toward preventive maintenance demands changing that mindset, which doesn’t happen overnight.
According to Kuhn, the key to this shift is building a proactive culture “one positive experience at a time:”
Culture changes one experience at a time. So, all you have to do today is create one new positive experience. Hey, today we’re going to plan the schedule and kit one job we’re going to have. We’re going to anticipate downtime for our detractors to wrench time. We’re going to get this thing done in eight hours, we’re going to turn it over to production and everything’s going to be okay.
This involves finding small, consistent preventive maintenance methods until they become second nature.
For example, start with a single job: schedule it, prepare the tools and parts in advance, and complete it without delays.
Completing one preventive task like this creates a small “win,” showing the team the value of maintenance planning and attention to detail.
Over time, these small wins add up, gradually creating a reliable maintenance culture.
So yes, you need a good training program, but persistence is the real key.
Consistently and gradually promoting a collective preventive mindset will lead to more engaged staff who perform maintenance efficiently and take ownership of keeping the facility running smoothly.
Implement Predictive Maintenance Technologies
Predictive maintenance (PdM) is a level-up from preventive maintenance and another good practice for streamlining repairs.
With various technologies like IoT sensors, data analytics, and artificial intelligence (AI) that monitor your equipment’s real-time condition and by analyzing critical data points, PdM can forecast potential failures before they occur.
It’s preventive maintenance but based on more data.
Tim White, a former reliability engineer and current engineering consultant at XMPro, highlights the importance of using machine learning models for detecting anomalies.
For example, event intelligence platforms can process data from various sources—including digital twins—to identify patterns and provide immediate alerts.
This means your maintenance team can act swiftly, guided by prescriptive analytics that not only notifies them of potential issues but also offers solutions for addressing them.
Facilities that have adopted PdM report impressive results.
Deloitte’s research shows it can boost equipment uptime by 10-20%.
Therefore, it’s not surprising that 47% of facilities cite improved uptime as their main reason for implementing PdM.
These numbers, along with the predictive maintenance market valuation data, indicate that an increasing number of facilities are adopting predictive maintenance to improve operational reliability.
And how could they not, since this type of maintenance bridges the gap between routine upkeep and emergency response?
All things said, there’s no better way to streamline maintenance than with the machines’ insights.
Conclusion
As someone deeply familiar with the challenges of maintenance management, you know that every minute of uptime counts.
Whether adopting a CMMS, streamlining spare parts management, or leveraging predictive maintenance, each approach can significantly increase it.
By implementing these five methods, you’ll shift from reactive to proactive maintenance and create a culture that supports your efforts. In the end, these practices do more than streamline repairs—they build a more resilient and productive facility.
If you want to achieve that, rethink how you maintain today and take the first step toward a better future!