Get a Free WorkTrek Demo
Let's show you how WorkTrek can help you optimize your maintenance operation.
Try for freeAre you running a fleet of commercial motor vehicles or trying to streamline the process of vehicle inspection reports? Do you manage commercial vehicles, struggle with compliance with federal regulations, and want to improve the visibility of your equipment?
Two critical components are at the core of this operation: Electronic Logging Devices (ELD) and Driver Vehicle Inspection Reports (DVIR).
Motor carriers play a crucial role in maintaining compliance with federal regulations that ensure the safety of their fleet through diligent use of ELDs and DVIRs. These devices are essential for the repair and maintenance of commercial motor vehicles in accordance with the Federal Motor Carrier Safety Administration (FMCSA) standards.
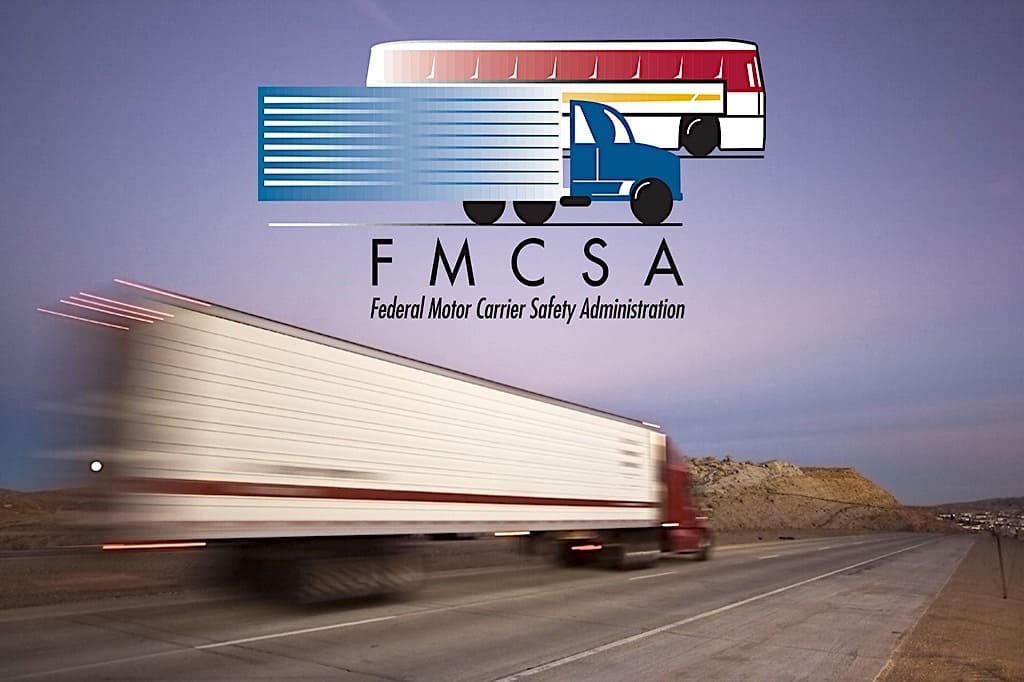
Source: Idealease
What is an ELD?
ELDs are mandated in many countries, and they track driving hours to ensure compliance with Hours of Service regulations. DVIRs, on the other hand, are required for any commercial motor carrier to improve the safety of the fleet.
This article explores how integrating vehicle data from ELDs and other data devices can streamline DVIR processes, improving compliance, safety, and operational efficiency in the transportation industry.

Source: ForwardThinking
A Deep Dive into Electronic DVIRs Technology
The Genesis and Evolution of ELDs
Government regulations have made electronic Logging Devices (ELDs) commonplace in the transportation industry. They are designed to provide fleet managers with rich data sets to improve compliance, report defects, and overall fleet efficiency.
In the United States, the Federal Motor Carrier Safety Administration (FMCSA) mandated using ELDs for most commercial vehicles through the ELD Final Rule, effective December 2017. Similar mandates have been adopted in other jurisdictions, recognizing the critical role of ELDs in promoting road safety and compliance to enhance the process for driver vehicle inspection reports.
Understanding the Technical Fabric of ELDs for commercial motor vehicle defects
While an ELD connects directly to the vehicle’s data port to automatically record a driver’s driving hours and activity, the functionality extends beyond just time tracking. ELDs can log a variety of data points essential for comprehensive fleet management, including but not limited to:
- Date, time, and GEO location information
- Engine hours and vehicle miles
- Driver identification and log-in/log-out times for truck driver
- Vehicle and motor carrier identification
- Real-time driver status (On-duty, Off-duty, Sleeper Berth, Driving)
This data supports compliance with HOS regulations and provides a wealth of information that can be analyzed to optimize fleet operations, improve fuel efficiency, and enhance overall fleet safety.
One of the benefits of ELDs is that they can automate the detection of some vehicle defects using data from the CAN bus of the vehicle. Using this data, fleet managers can automate both the notification and scheduling of mechanical issues.
If you take the next step and part an ELD device with Work Order Management Software, Fleet Managers can automatically generate work orders and assign them to mechanics when a fault is detected.
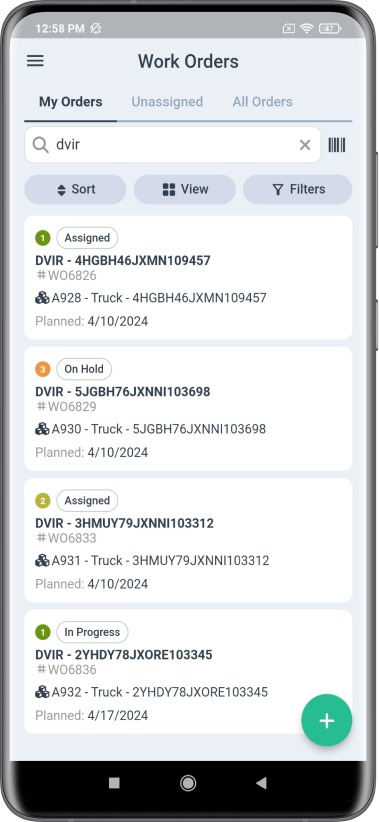
Source: WorkTrek
ELDs and Fleet Management Optimization
The integration of ELDs into fleet management systems has improved the experience for fleet managers. They include:
- Roadside inspections
- Integration with fleet management software
- DVIR form
- Automating corrective action
- Streamlining DOT roadside inspections for commercial motor vehicle
- Reducing the overhead associated with managing inspected commercial motor vehicles
- Reducing the time needed for vehicle inspections
- Reducing the time needed for a driver’s vehicle inspection report
- Better compliance with existing federal law
The real-time data collected by ELDs enabled fleet managers to closely monitor vehicle and driver performance, identify improvement areas, and make data-driven decisions.
For instance, analyzing driving hours and break patterns can help optimize routes and schedules, reduce idle times, and improve customer service. If you want to increase driving efficiency even further, look at route optimization products that streamline the driving experience.
Additionally, the data can be instrumental in scheduling preventive maintenance, reducing downtime, and extending the lifespan of fleet vehicles.
Furthermore, if you can pair ELD devices with a WorkOrder Management system such as WorkTrek, you can provide automated work-order creation and full visibility of the repair process.
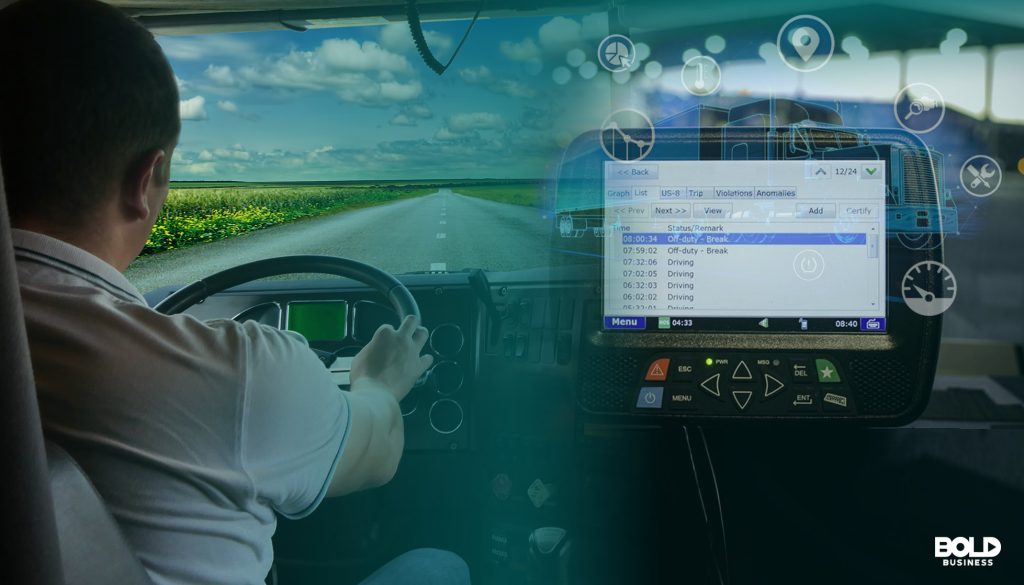
Source: Bold Business Insights
Navigating the Challenges and Embracing the Future
Despite the clear benefits, there have been a lot of challenges in the industry in adopting ELD technology. Privacy concerns, the cost of implementation, and the learning curve for technology adoption are some of the issues that organizations face.
However, the industry continues to evolve, with manufacturers and regulatory bodies working together to address these concerns and enhance the effectiveness of ELD systems.
Looking forward, integrating ELDs with other technological advancements, such as artificial intelligence, machine learning, and the Internet of Things (IoT), promises to further revolutionize fleet management.
These integrations could lead to even more sophisticated data analysis capabilities, predictive maintenance, and enhanced driver safety measures.
Comprehensive Overview of Driver Vehicle Inspection Report (DVIR)
What is a Driver vehicle inspection report (DVIR)
Driver Vehicle Inspection Reports (DVIR) are a critical component of the transportation industry’s fleet management and safety protocols.
The primary goal of a DVIR is to ensure that vehicles are maintained in good working order and any issues are addressed promptly to prevent accidents, breakdowns, completed repairs, and unplanned downtime.
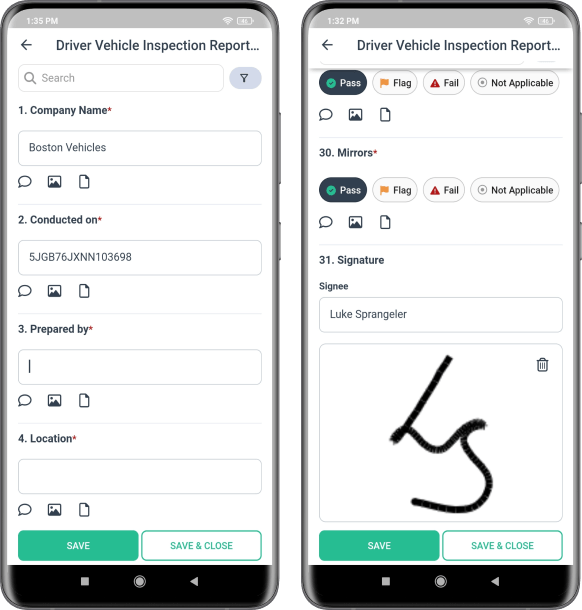
Source: WorkTrek
Legal Mandates Surrounding DVIR
Transportation regulatory authorities, such as the Federal Motor Carrier Safety Administration (FMCSA) in the United States, mandate the conduct of DVIRs.
These regulations stipulate that commercial vehicle operators must conduct both pre-trip and post-trip inspections of their vehicles and report the condition of various components, including brakes, steering mechanisms, lighting devices, tires, and more.
The regulatory framework ensures that all commercial vehicles on the road meet minimum safety standards, protecting not just the drivers but all road users.
The DVIR Process: A Step-by-Step Breakdown
The DVIR process involves several key steps designed to assess the condition of the vehicle systematically:
-
Pre-Trip Inspection: Before starting a trip, drivers are required to check the vehicle’s overall condition, focusing on critical safety components.
-
Monitoring During Use: While ELDs primarily monitor driving hours, drivers should also be observant of any signs of malfunction or degradation in vehicle performance during operation and note these for further inspection.
-
Post-Trip Inspection: A thorough inspection is conducted at the end of a trip. This includes checking the engine, tires, lights, brakes, and other critical systems.
-
Reporting and Documentation: Any issues found during the pre-trip or post-trip inspection must be documented in the DVIR.
-
Review and Follow-up: Maintenance personnel review the DVIR and address any reported issues.
-
Record Keeping: Completed DVIRs are kept on record for a minimum of 3 months,.
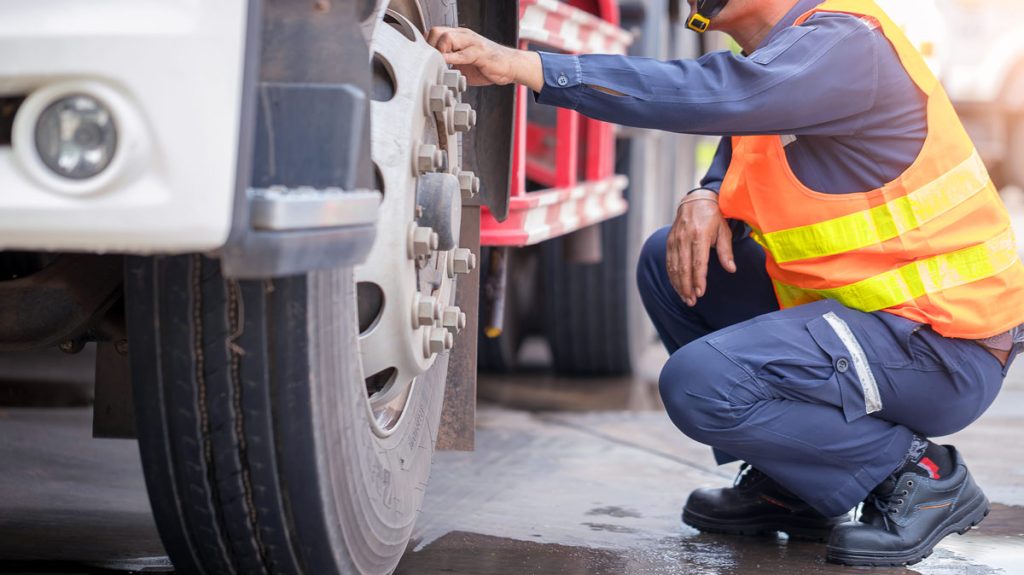
Source: Geotab
Conclusion
While there are numerous benefits to integrating ELD devices with DVIR processes, there are also several challenges that you need to be aware of.
These can include technical hurdles related to data compatibility and integration, training staff to effectively use new tools and interpret data, and ensuring that data privacy and security measures are maintained.