Get a Free WorkTrek Demo
Let's show you how WorkTrek can help you optimize your maintenance operation.
Try for freeYou’re in the field, ready to update a work order—but your software won’t let you.
No mobile access. No real-time updates.
Now, the job stalls, and the frustration builds.
That’s what happens if your work order management software doesn’t have the right features.
But when it does, work orders become faster to create, assign, track, and complete.
So, what are the must-have features for seamless and efficient work order management?
Let’s break them down.
Automated Work Order Creation
Are you manually creating work orders for every maintenance task?
That’s a recipe for wasted time.
According to a Smartsheet report, over 40% of workers spend at least a quarter of their week on repetitive tasks like data entry and email management.
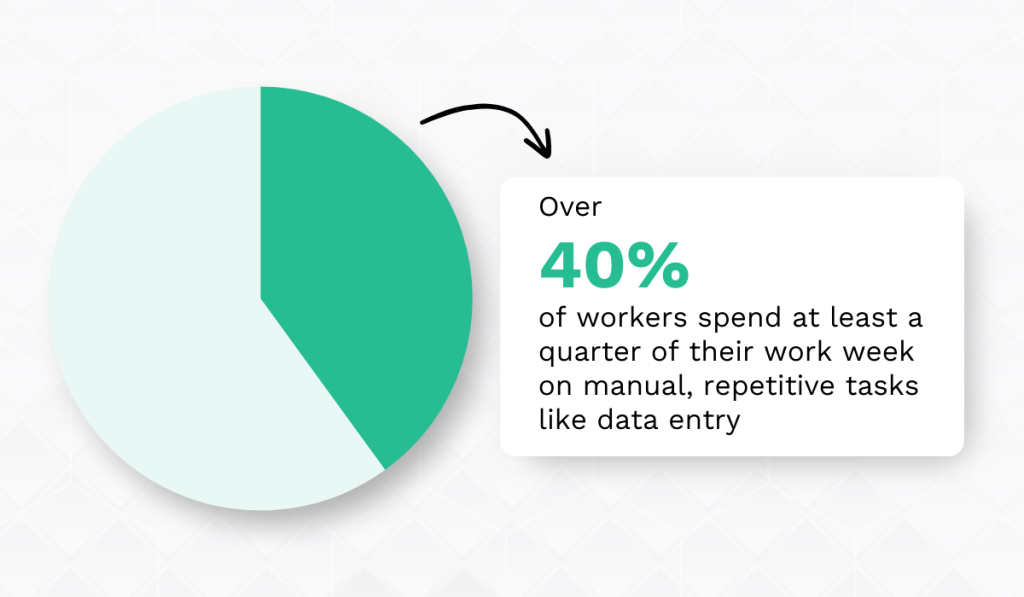
And work order creation is exactly that—endless, repetitive data entry.
The right work order management software eliminates this by automating work order creation.
With solutions like WorkTrek, you can set up recurring work orders based on different factors.
For starters, you can schedule preventive maintenance tasks daily, weekly, monthly, or yearly.
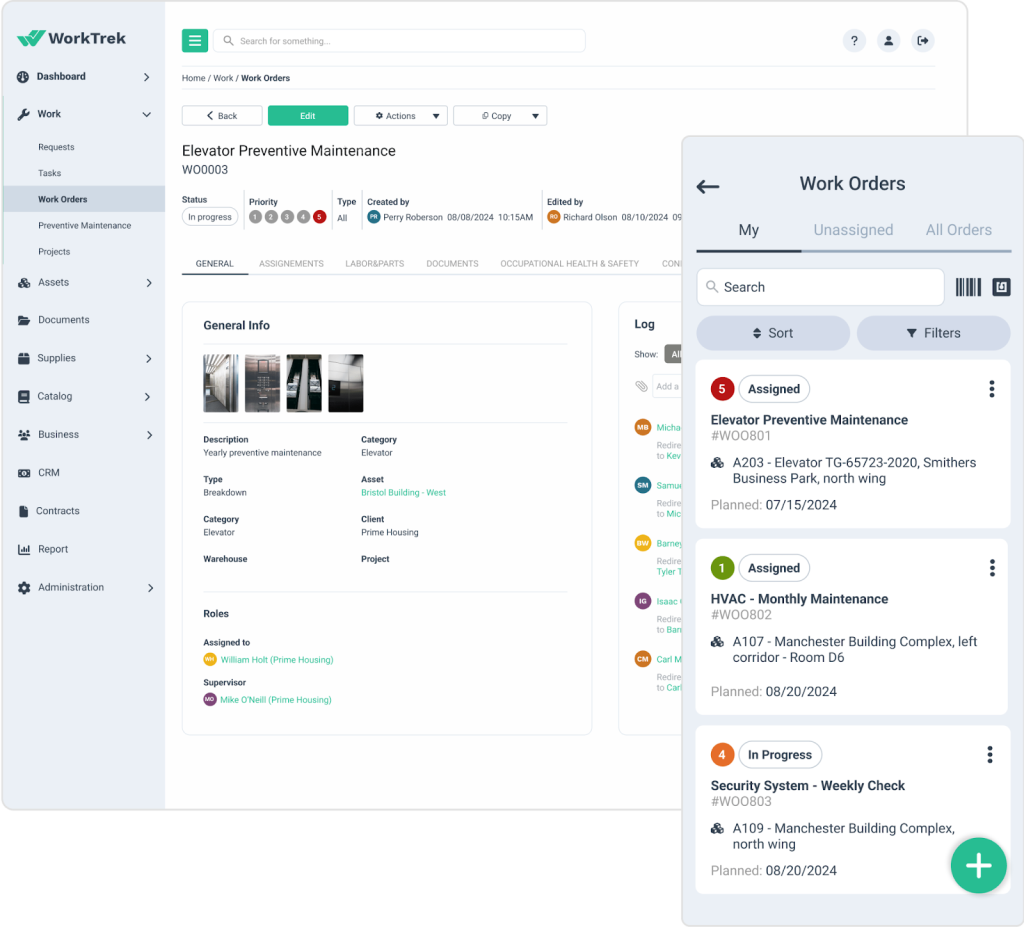
Additionally, if an asset reaches a specific number of operating hours, the system can automatically trigger a work order.
For example, you could set up a forklift’s maintenance schedule to generate a work order every 500 hours of operation, like in the example below:
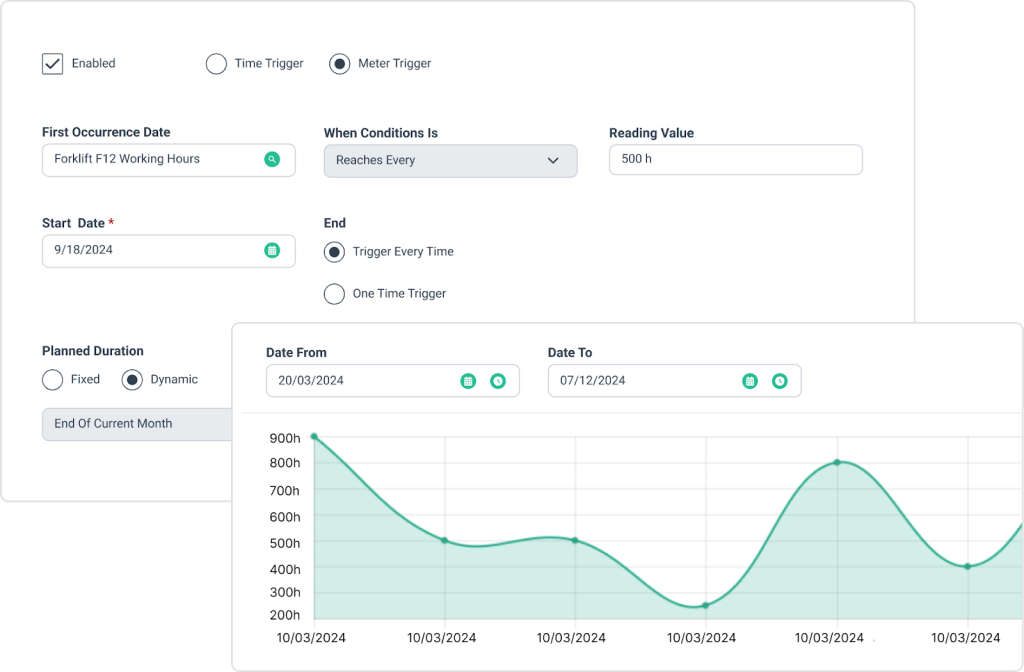
Some systems integrate with meters and sensors, allowing maintenance to be scheduled based on real-time data, such as asset temperature, vibration, or pressure.
If a preventive maintenance check identifies an issue, the system can automatically create a follow-up work order, ensuring no problems slip through the cracks.
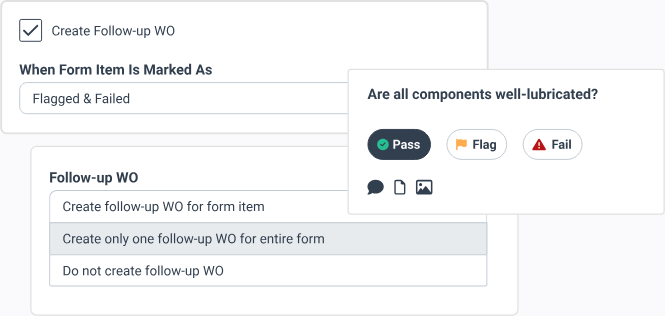
The right automation settings help reduce redundant tasks, minimize missed service requests, and allow the team to focus on critical maintenance.
Increased efficiency, reduced downtime, and longer asset lifespans all result from a feature that should be non-negotiable in any work order management software.
Easy Scheduling
Creating a work order is just the first step.
The real challenge is making sure it gets scheduled at the right time, with the right technician, and with the necessary resources.
Work orders pile up without a proper scheduling system, technicians become overbooked, and critical repairs are delayed.
Unfortunately, statistics show that scheduling inefficiencies remain one of the biggest pain points in maintenance operations.
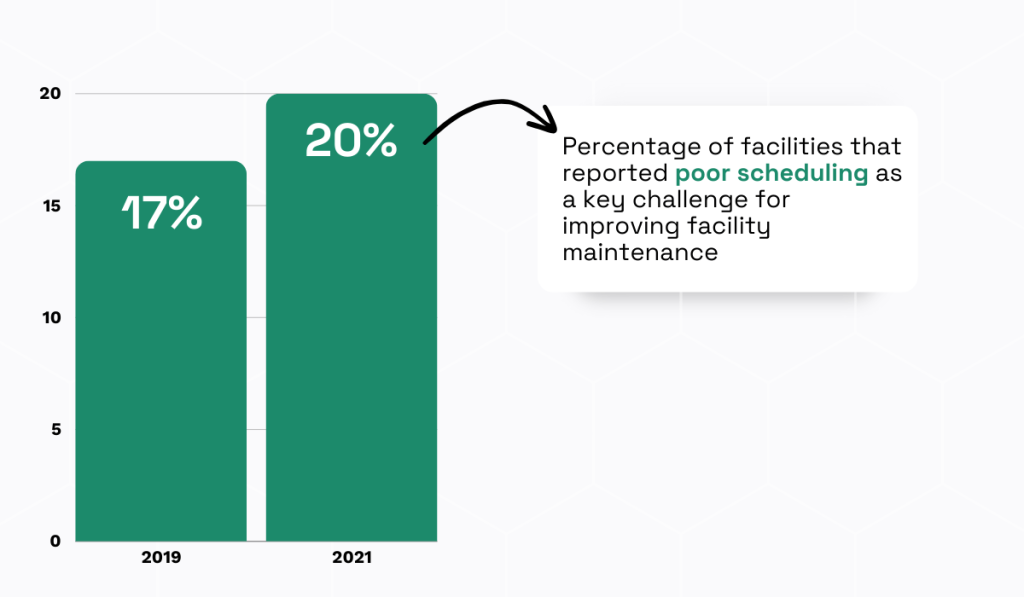
But it doesn’t have to be that way.
A well-designed work order management system makes scheduling simple and efficient.
Instead of manually matching technicians to tasks or shuffling through spreadsheets to check availability, you can assign jobs in just a few clicks.
For example, with a work order scheduler like the one below, you can see all assigned tasks in one place, including maintenance status, execution time, and the responsible technician.
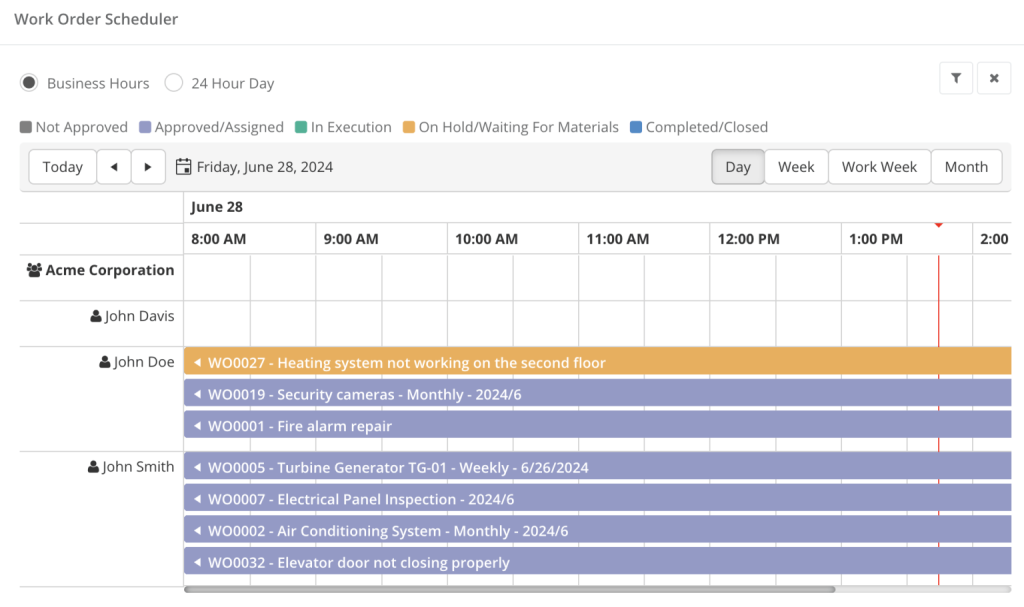
And if you need a broader view, you can switch between different formats.
A list format allows for quick sorting, a calendar provides a clear timeline of upcoming tasks, and a location-based view of work orders helps assign jobs more efficiently.
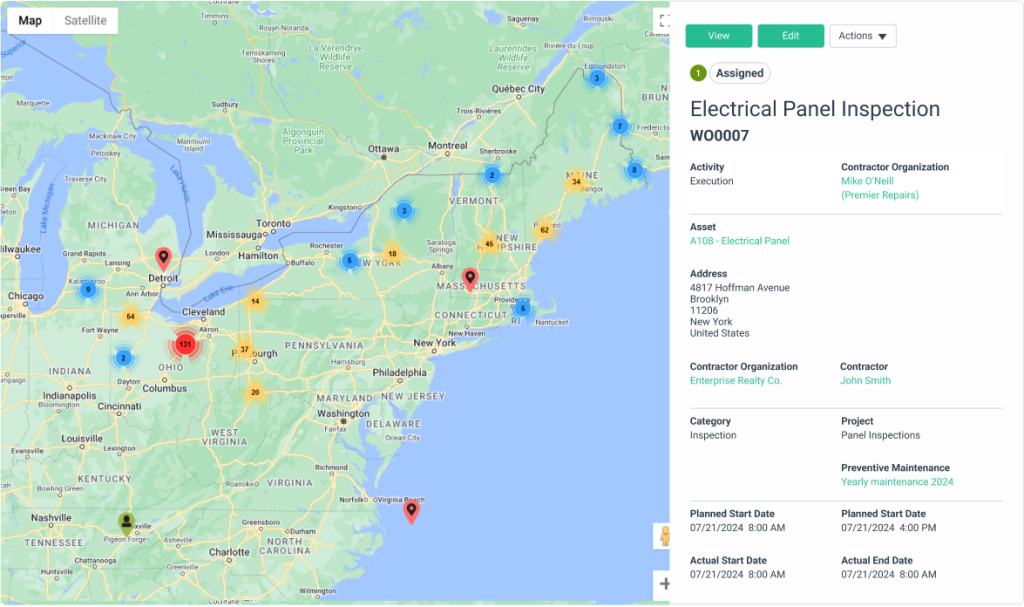
For example, if a technician is already working near a broken-down asset, you can quickly send them to the next job, reducing travel time and improving response rates.
All in all, a flexible scheduling system ensures that high-priority tasks don’t get lost and that maintenance teams stay productive, making it another essential feature for any work order management software.
Mobile Access
If your team can’t update work orders from the field, you’re already falling behind.
But when your software is mobile-friendly, everything changes.
Field workers and technicians can log job details, track parts, sign work orders, and update statuses—all from their phones.
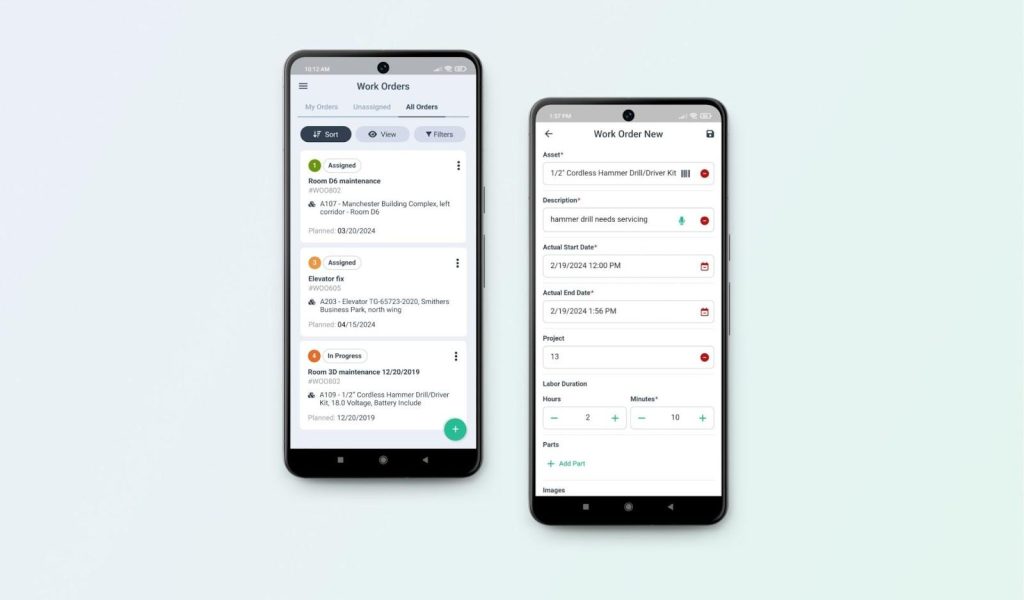
Some systems even offer offline access, allowing work orders to be updated in areas with poor connectivity and synced later.
Moreover, with mobile access, anyone can create a work request the moment they spot an issue, either through the app, a request portal, or email.
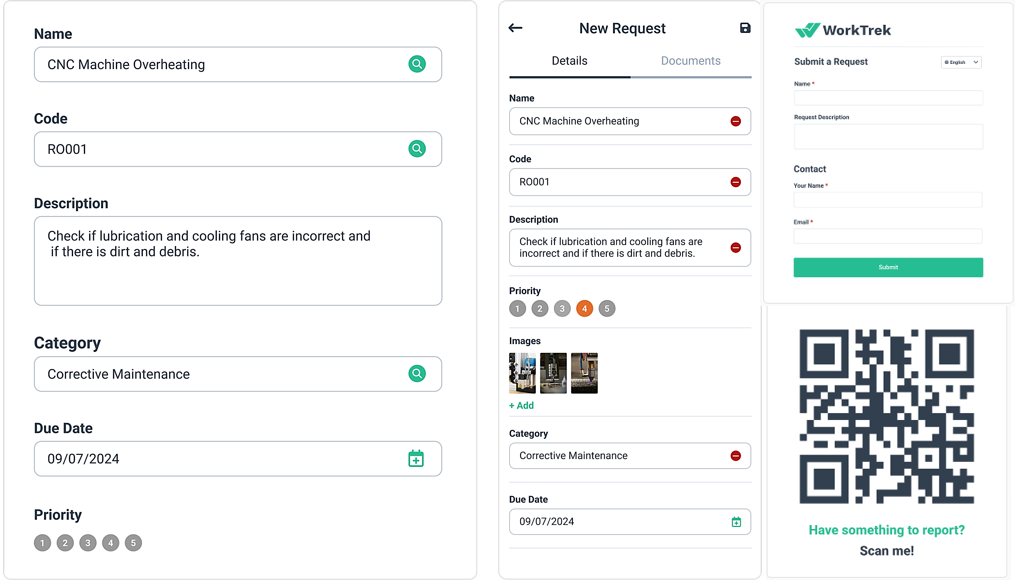
Then, the office can immediately create and assign a work order, ensuring the problem is fixed immediately.
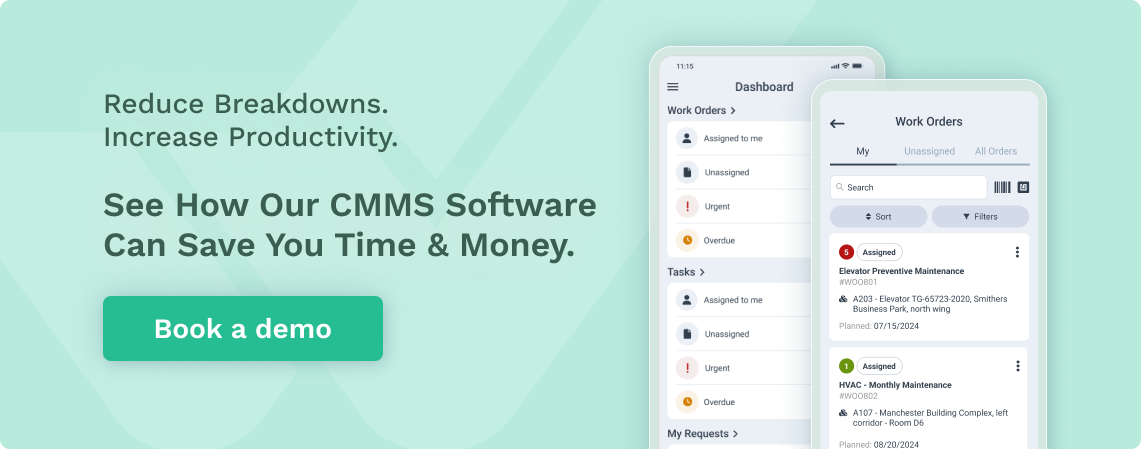
When it’s time to get the job done, technicians can check their phones for instructions, safety requirements, and part details.
They can even clock in and out, providing precise time tracking that helps with future scheduling.
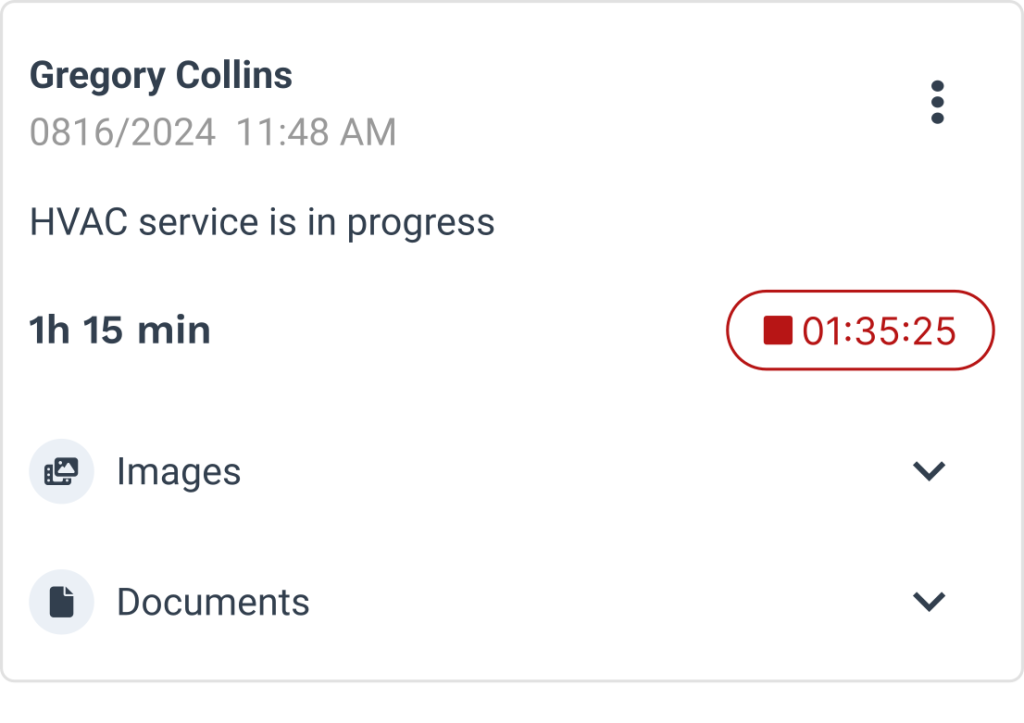
Plus, the supervisor can track the job getting completed in real-time.
Once a repair is complete, marking it as done is just as easy. That means fewer miscommunications and faster response times.
Most importantly, mobile access keeps your team connected no matter where they are.
Digital Work Order Documentation
Paperwork slows everything down.
Lost documents, illegible handwriting, and missing signatures create confusion and compliance risks.
Digital work order documentation eliminates these issues by keeping everything—work orders, images, instructions, and records—in one centralized system.
With modern software, users can:
- Upload photos of issues directly from the field
- Attach safety guidelines and step-by-step instructions
- Collect digital signatures for approvals or job completion
Take digital signatures, for example.
Whether a contractor signs off on completed work or a client approves a repair, everything is documented instantly.
Instead of chasing down paperwork, signatures can be stored within the system, allowing authorized users to approve tasks with just a click.
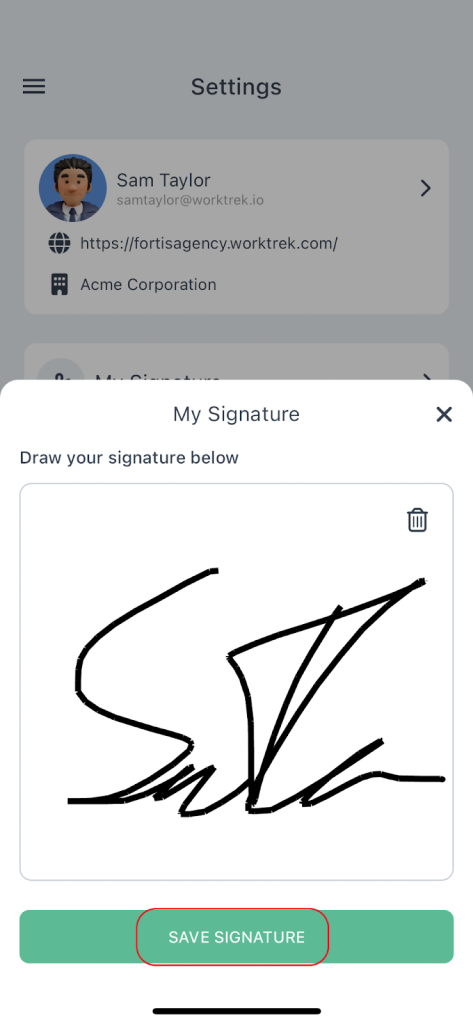
This kind of documentation also improves accountability and compliance.
In the case of an audit, for instance, every work order and approval is just a search away.
Digital documentation also helps technicians in the field.
If they’re troubleshooting an issue, they can quickly check past maintenance records to see what was done previously—reducing guesswork and repeat problems.
The benefits of digital documentation over paper are clear.
The key is choosing software that makes the process seamless.
Centralized Inventory Management
What happens when a technician gets assigned a job only to arrive and find that the necessary part isn’t in stock?
The job stalls, downtime increases, and costs rise.
But with centralized inventory management, you can avoid this entirely.
For starters, all assets, inventory, and spare parts are tracked in one place.
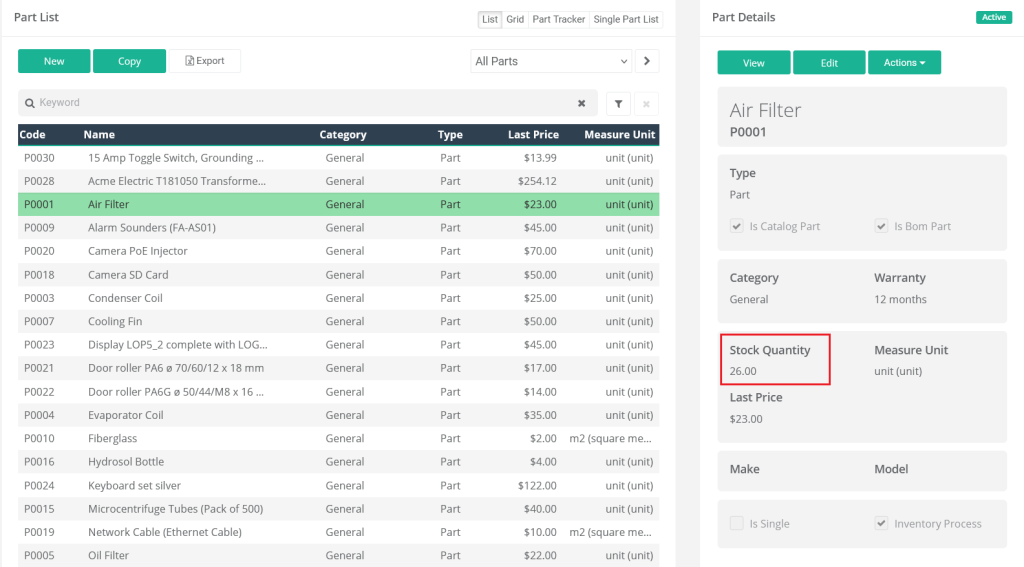
When you create a work order, you can immediately see which parts are needed and where they’re located—no more guesswork or wasted trips.
Plus, since spare parts and materials are directly linked to work orders, the system automatically updates inventory in real-time whenever a part is used.
You can also set stock level thresholds so that when a part runs low, the system alerts you to order it before it’s too late.
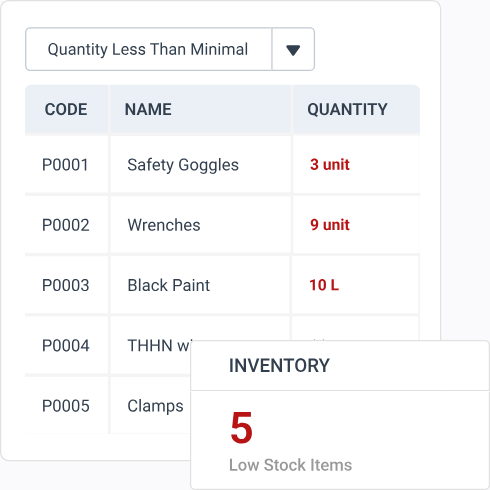
Some software even automatically generates purchase orders, ensuring stock is replenished without manual intervention.
The result is a clear, up-to-date view of your inventory, making it easier to plan and schedule maintenance without unexpected delays.
Customizable Workflows
No two maintenance operations run the same way.
Some teams need multi-step approvals before closing a work order, while others want automatic task assignments based on location or priority.
That’s why customizable workflows are a must-have feature.
With a flexible work order system, you can:
- Automate approvals to match compliance requirements
- Trigger follow-up tasks based on inspection results
- Set up different processes depending on the type of work order (corrective, preventive, inspection, etc.)
For example, a facility managing highly regulated equipment may require supervisor approval before marking a work order as complete.
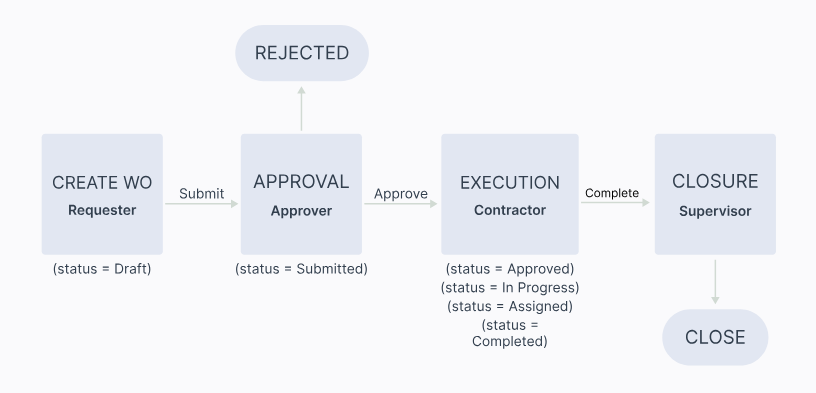
Meanwhile, a fleet maintenance team might automate work orders for vehicles that reach a certain mileage threshold.
By tailoring workflows to fit specific operational needs, teams can speed up processes, reduce errors, and ensure work is completed consistently—without manual oversight.
Customizable workflows mean more efficiency, less guesswork, and a maintenance process that works as needed.
Automated Notifications
A work order is assigned, but the technician doesn’t see it in time.
Maintenance delays add up without clear communication, leading to higher costs and equipment failures.
That’s where automated notifications help.
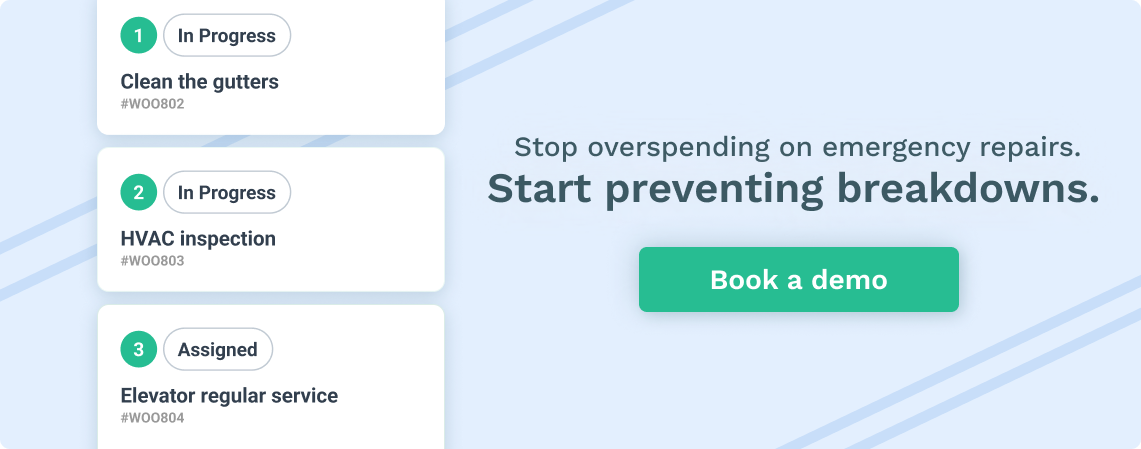
They instantly alert the right people at the right time—whether it’s a technician getting a new task, a manager seeing an update, or a supervisor being notified when a job is completed.
These alerts can be sent via email, SMS, or in-app notifications (such as reminders), ensuring everyone stays informed in real-time.
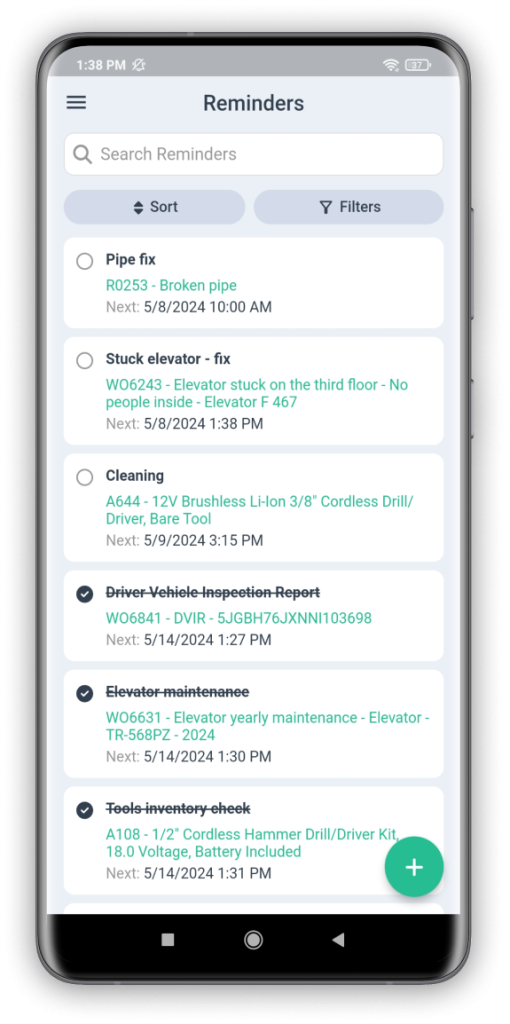
Users can also customize notification settings to prevent overload, ensuring only the most relevant alerts are sent to the right people.
Many systems also include an @mention feature, allowing users to tag teammates directly within a work order.
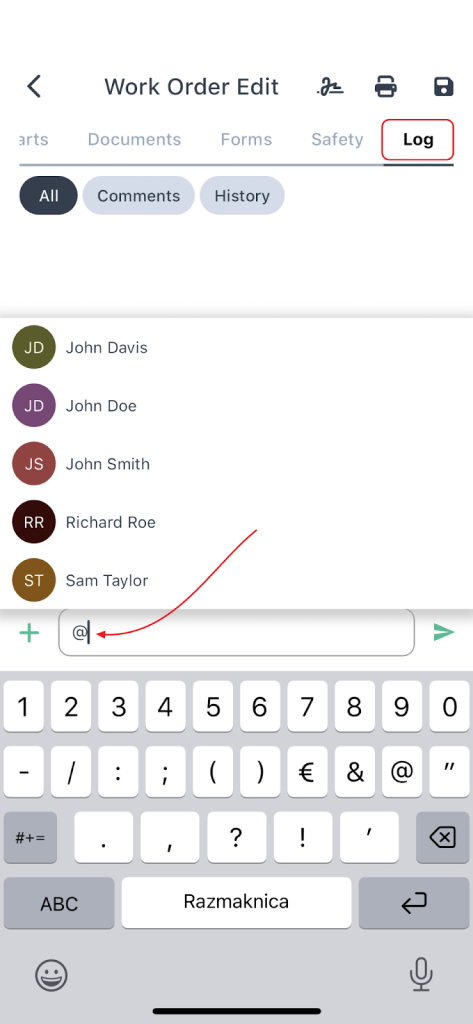
This makes it easy to ask for clarification, confirm completion or request approval—all while automatically notifying the right person.
In a large manufacturing plant, for example, automated alerts can also notify supervisors when equipment inspections reveal issues, allowing them to schedule repairs before a minor problem turns into a costly failure.
All in all, by keeping communication fast, seamless, and in real-time, teams reduce delays, prevent missed assignments, and resolve issues more efficiently.
This is a feature you simply can’t go without.
Detailed Reporting
Detailed reporting turns maintenance data into actionable insights, helping teams optimize operations and reduce costs.
It’s no wonder that this is another feature good work order management software must have.
A strong reporting system tracks work order completion times, recurring issues, asset performance, and labor costs from one dashboard.
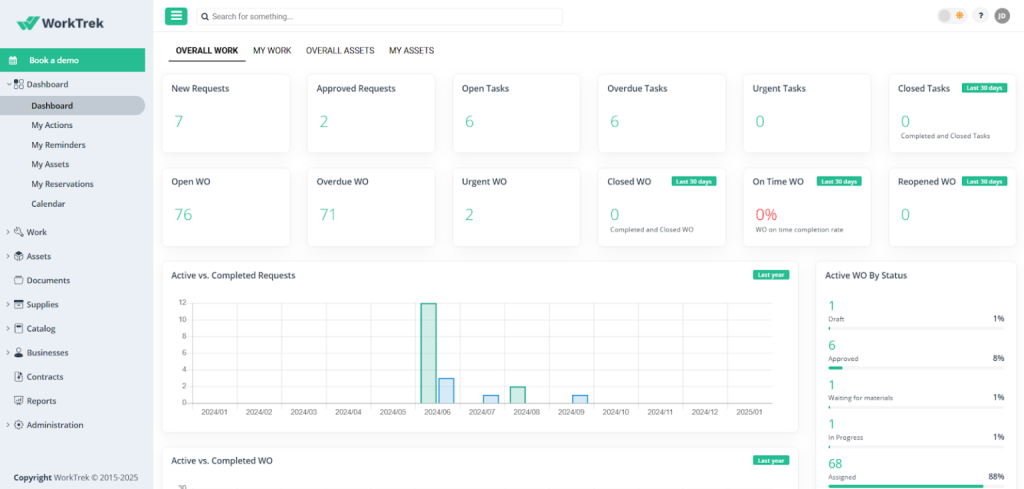
This allows managers to spot inefficiencies, adjust maintenance schedules, and plan budgets more effectively.
For instance, a facility might notice that certain assets require frequent emergency repairs.
With this insight, they can shift toward preventive maintenance strategies, reducing downtime and repair expenses.
However, robust work order management software should also generate various reports, including work orders per expense, per parts used, and more.
Here is an example of one such report:
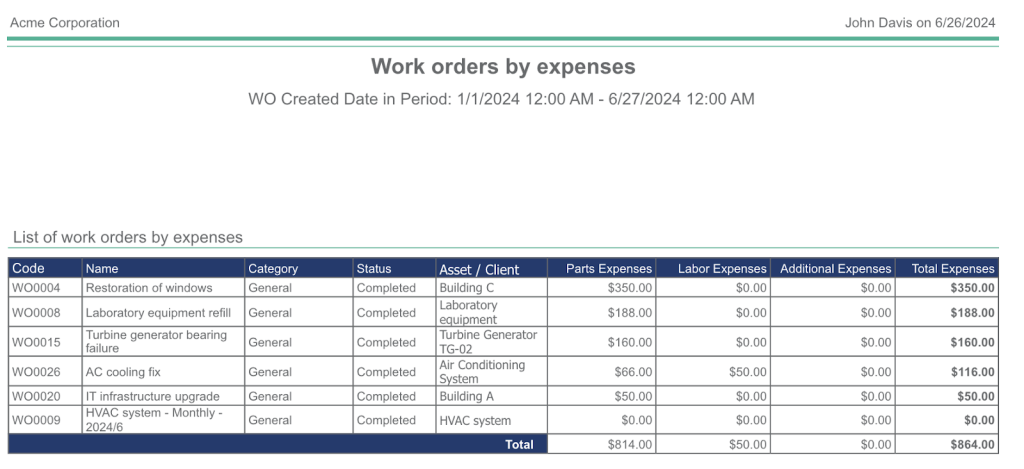
With this clear data, you can plan your budget better, and fine-tune your maintenance strategy.
So, choose software with strong reporting capabilities to gain full visibility into maintenance operations, make data-driven decisions, and cut unnecessary costs.
Integration With Other Systems
Maintenance management doesn’t happen in isolation.
Work order management software should integrate with other business systems, such as ERP, accounting, HR, and IoT platforms, to maximize efficiency.
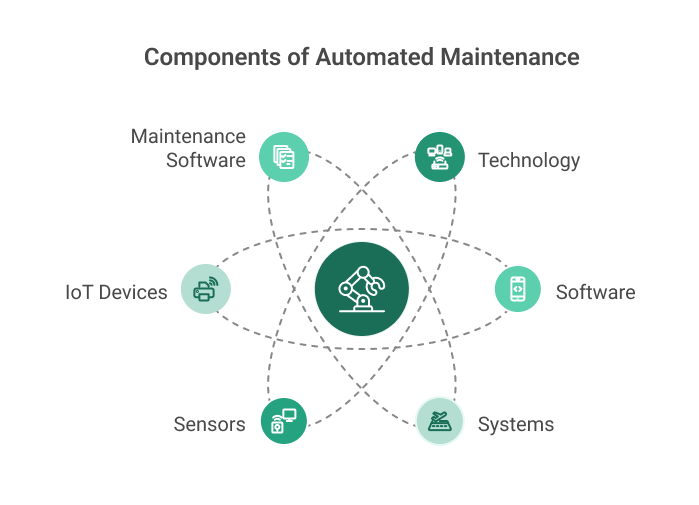
For example, ERP integration ensures that maintenance costs, labor hours, and spare parts usage are automatically recorded in financial systems, eliminating manual data entry and improving budget tracking.
IoT integration allows real-time monitoring of equipment—if a sensor detects abnormal temperature or vibration, the system can trigger a work order before a failure occurs, preventing costly downtime.
Other useful integrations include accounting software to streamline expense tracking and HR systems to link maintenance tasks with employee schedules, certifications, or labor cost analysis.
The need for seamless integration becomes even clearer when you consider real-world challenges.
Take this small fabric maintenance company, for example:
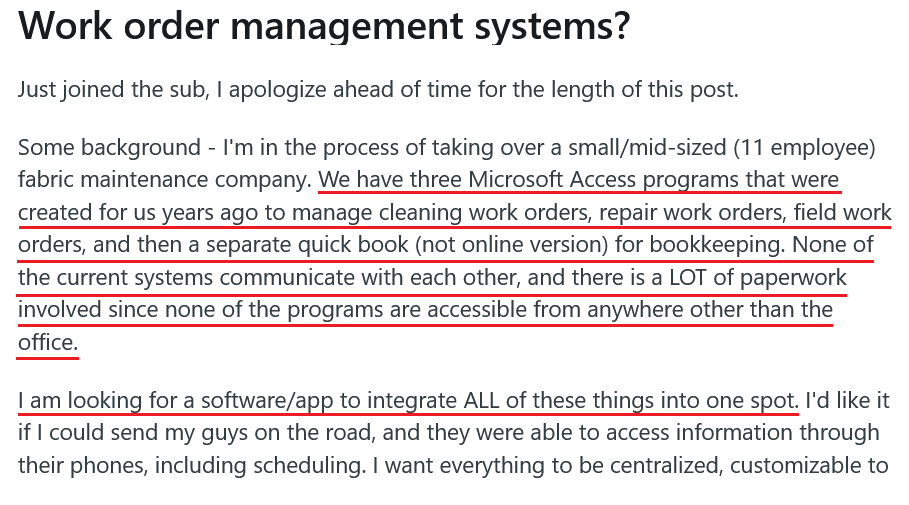
For years, they have been dealing with systems for work orders, bookkeeping, and scheduling that don’t communicate with each other.
The right work order management software would centralize everything.
It lets field technicians access work schedules, work orders, and even process payments from their phones while syncing with accounting and payroll systems.
All in all, by choosing software with strong integration capabilities, you can centralize data and improve cross-department collaboration.
That reduces costs and makes operations across the company more efficient.
So, think about this feature when choosing a system for your business!
Conclusion
Work orders shouldn’t be a source of delays, confusion, or wasted time.
Instead, work order management software should transform maintenance from reactive chaos to proactive efficiency—cutting downtime, saving costs, and keeping teams productive.
But not all software is built the same.
Does yours have the features to keep up?
If not, it might be time for an upgrade—before inefficiencies cost you more than time.
Try WorkTrek for free to see if it matches your needs.