Get a Free WorkTrek Demo
Let's show you how WorkTrek can help you optimize your maintenance operation.
Try for freeUnderstanding Failure Mode and Effects Analysis (FMEA) can help mitigate risks and optimize performance in any industry. This powerful tool helps identify where and how a process might fail and what the repercussions could be.
In our guide, we’ll explore the basics of FMEA, showcase its application across sectors, and reveal how you can leverage it to maintain control over potential setbacks.
In short, FMEA is a robust and systematic approach for identifying and evaluating potential failures in systems, products, or processes utilized across various industries to enhance performance, reliability, and safety.
There are three main types of FMEA: Design FMEA (DFMEA) for product reliability, Process FMEA (PFMEA) for manufacturing processes, and System FMEA (SFMEA) for overall system analysis; all contribute to identifying potential failures and mitigating risks. Effective implementation of FMEA involves assembling a cross-functional team, prioritizing risks using the Risk Priority Number method, and continuously updating the FMEA document to reflect changes in design or process, thus fostering ongoing improvements.
Understanding FMEA: A Comprehensive Overview
Source: Intelex Blog
Failure Mode and Effects Analysis (FMEA) systematically identifies and assesses potential system, product, or process failures. The goal is proactively tackling possible issues to enhance the system or process’s performance and reliability.
Originating from practices developed by the U.S. military in the 1940s, its consistent use attests to its effectiveness across various sectors. It is typically applied during new product design stages when adapting existing products for alternative applications or while devising control plans that accommodate process changes.
The value of FMEA persists well into a product or service’s operational life cycle—not only at inception—and this application breadth is explored extensively within the literature on effect analysis. A notable text delving into different approaches surrounding FMEA is ‘Failure Mode and Effect Analysis: FMEA From Theory to Execution’ by D. H. Stamatis.
This work elaborates on diverse methodologies related to failure mode analysis, offers detailed glossaries pertinent to key terms involved with these methods, and describes how ISO 9000:2000 standards and Six Sigma principles can be integrated within a practical FMEA framework.
Failure Mode and Effects Analysis (FMEA) systematically identifies and assesses potential system, product, or process failures. The goal is proactively tackling possible issues to enhance the system or process’s performance and reliability.
Originating from practices developed by the U.S. military in the 1940s, its consistent use attests to its effectiveness across various sectors. It is typically applied during new product design stages, when adapting existing products for alternative applications, or while devising control plans that accommodate process changes.
Source: ASQ
Types of FMEA analyses
FMEA analyses are divided into three key types:
- Design FMEA (DFMEA): This analysis centers on a product’s reliability, probing for potential risks before the manufacturing stage begins. It scrutinizes failure modes and their root causes in terms of likelihood.
- Process FMEA (PFMEA): This type zeroes in identifying potential failures within the manufacturing process and their origins. It aims to devise methods that either prevent or lessen these prospective issues.
Conversely, PFMEAs serve as tools for carefully evaluating manufacturing and assembly procedures by pinpointing likely process-related shortcomings and devising solutions. In contrast, SFMEAs examine all system components— design and production processes—to detect possible failures, ensuring overall systemic dependability.
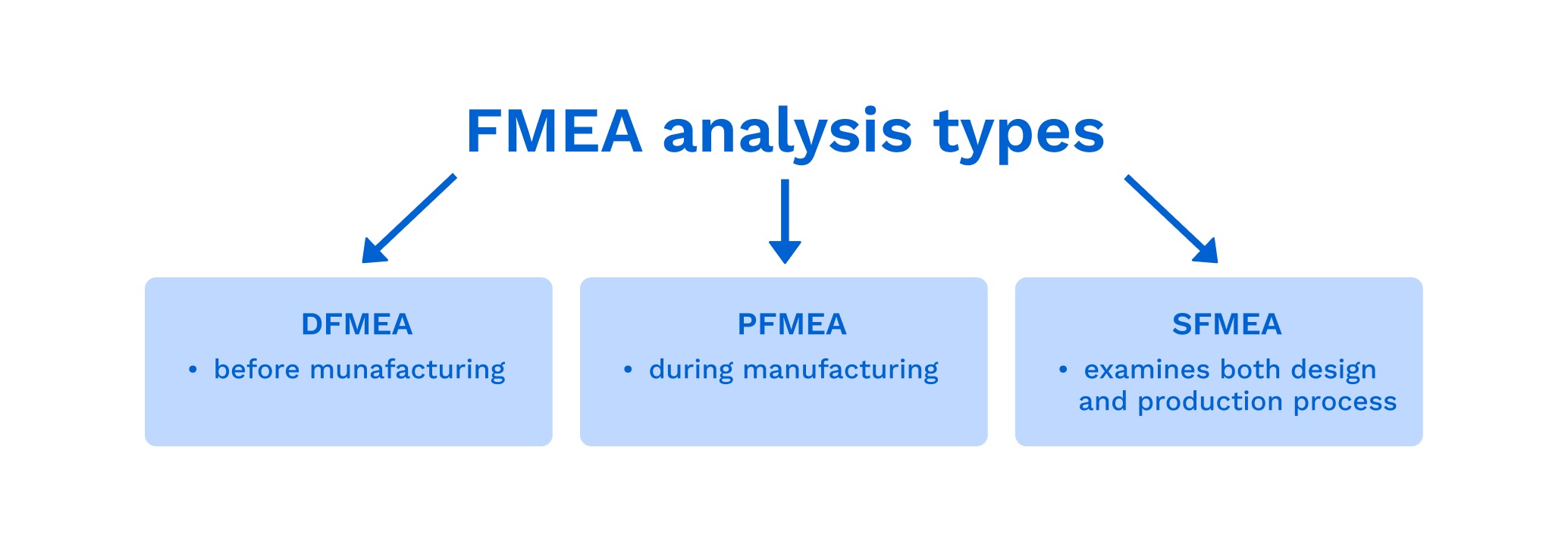
Key Components of FMEA
Failure Modes and Effects Analysis (FMEA) methodology utilizes concepts such as failure modes, the effects of those failures, and a system for ranking risks to address potential issues that could arise in design or processes.
Conducting an FMEA analysis focuses on exploring the repercussions of various failures by evaluating their severity, occurrence rates, and detectability.
Central to FMEA’s goals is directing appropriate corrective measures to mitigate or eradicate instances of failure. It emphasizes prioritization based on criticality first.
Within this framework lies the Risk Priority Number (RPN) strategy that plays a pivotal role in identifying and ordering these possible concerns according to urgency. It involves utilizing scores ranging from 1, indicating minimal risk, up to 10, reflecting very high risk—evaluation typically undertaken by specialists forming part of a dedicated DFMEA team during this assessment procedure.
In its capacity as an instrument for managing risks, FMEA is an evolving record detailing presently acknowledged risks alongside interventions applied towards their mitigation—all contributing to progressive improvement within relevant domains.
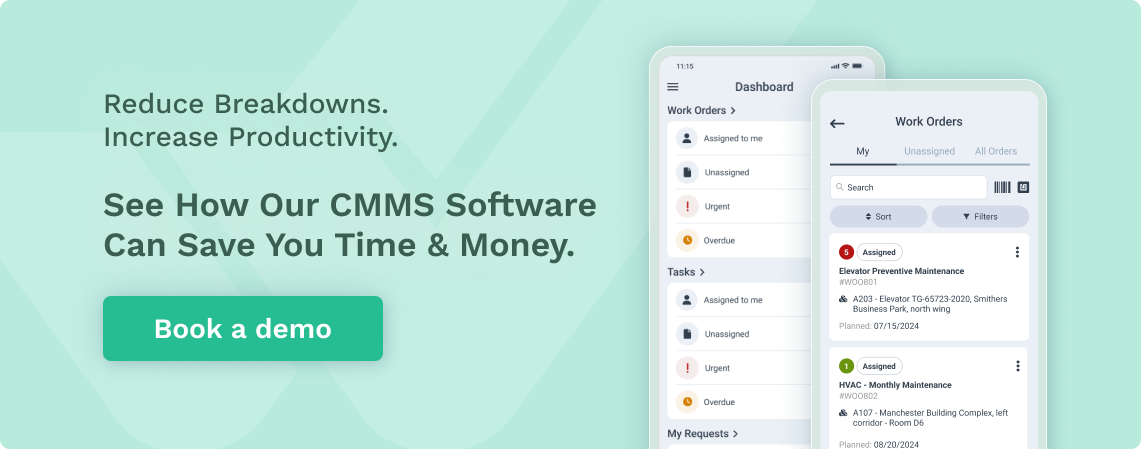
Implementing FMEA in Various Industries
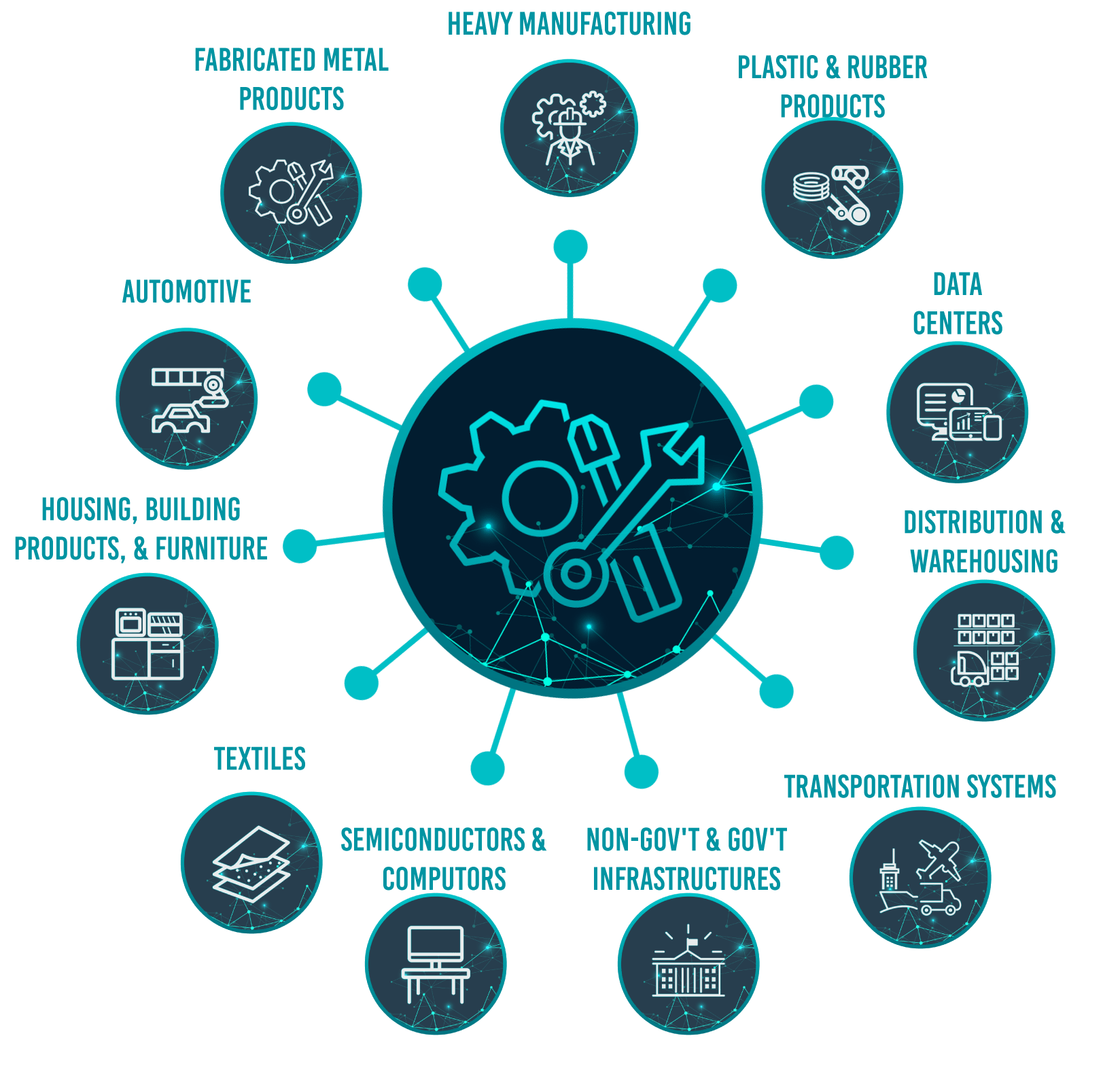
Source: Industrial Manufacturing
In the automotive industry, FMEA is a critical tool for assessing the robustness of new car models, mainly focusing on crucial components such as engines and brakes to ensure their reliability. Similarly, the aerospace sector applies FMEA methodologies to evaluate aircraft designs, where it plays a significant role in identifying potential failure modes, contributing to enhanced overall safety and performance.
FMEA’s versatility extends to various sectors, including:
- Semiconductor manufacturing: FMEA is used to pinpoint flaws within crucial manufacturing processes.
- Food processing: FMEA helps detect issues related to contamination or improper handling.
- Medical devices: FMEA enhances the service and maintenance of devices for safety and reduces potential failures.
- Telecommunications: FMEA is used to improve service processes and address network and billing errors.
FMEA is a versatile instrument applied throughout various sectors to proactively identify and address potential failure points, enhancing product and process safety, efficacy, and dependability. An example of its application showcases the breadth of its utility in mitigating such risks.
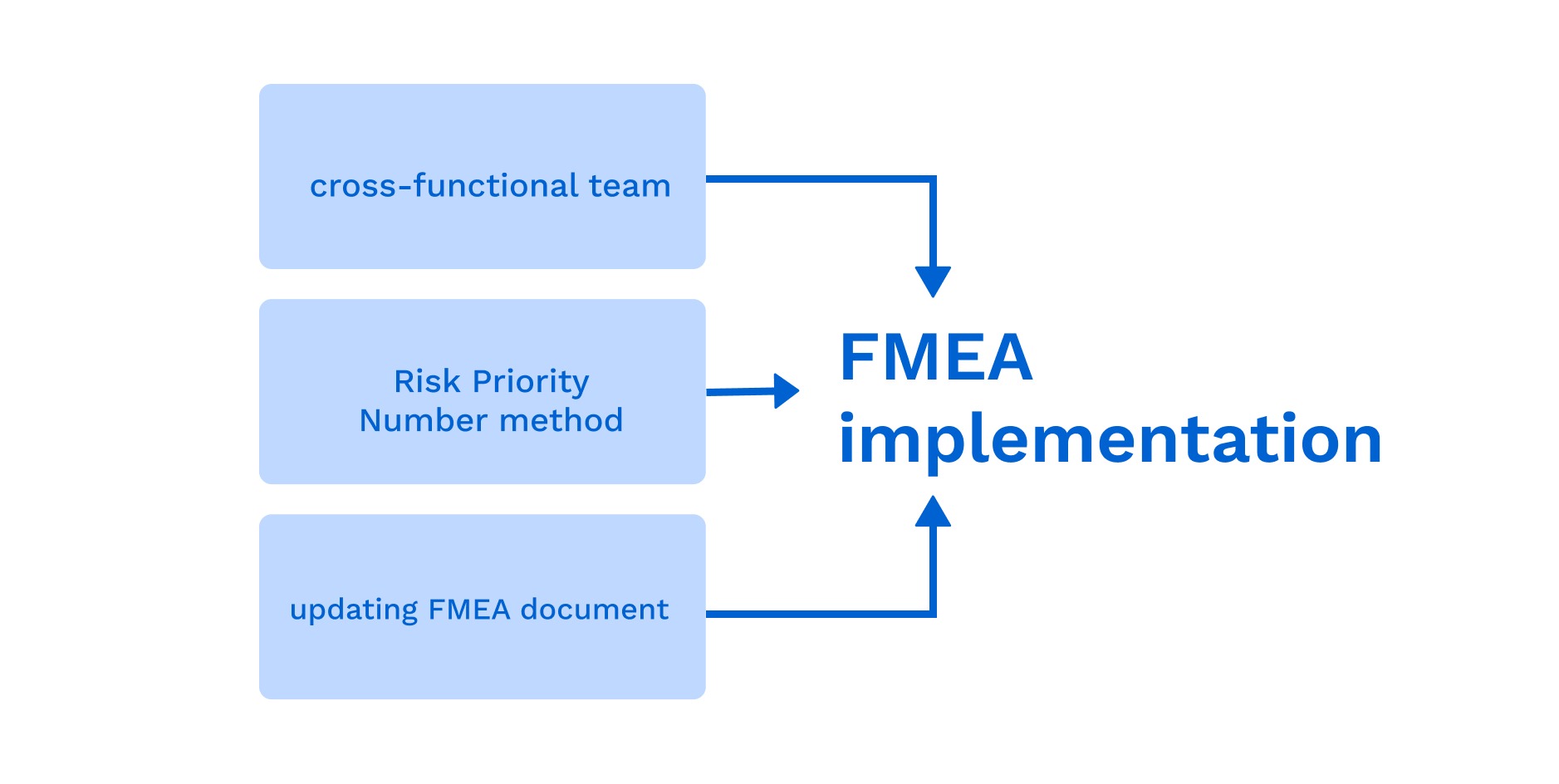
Source: WorkTrek
The FMEA Process: A Step-by-Step Guide
The initiation of the Failure Mode and Effects Analysis (FMEA) process involves a series of well-defined steps.
- The formation of a multidisciplinary FMEA team.
- Starting the FMEA early in the design phase to ensure effectiveness.
- Segmenting the analysis into smaller segments if it is too broad for practical examination.
- Engaging in an extensive brainstorming session with the FMEA team to list all potential failure modes for each component.
- Analyzing how each potential failure could impact the end product or downstream process stages.
These procedures are designed to perform a thorough mode and effects analysis, considering potential failures and their impacts on processes or products.
Every identified possible failure mode is meticulously recorded within an organized framework known as an FMEA table. Failures that score highest based on Risk Priority Numbers (RPNs) are flagged for immediate attention, leading to strategizing action plans for them specifically.
Subsequently, detailed control plans defining responsibility and timelines regarding actions meant to prevent or lessen these failures’ occurrence rate—consistently incorporating re-evaluation post-implementation phases—are developed, aimed at monitoring enhancement efficacy over time.
Sorce: Spicemix
Risk Assessment with RPN
The Risk Priority Number (RPN) is a crucial metric for evaluating the significance of potential failures identified through an FMEA analysis. It is derived by multiplying three factors: severity, occurrence, and detection ratings for each possible failure. This aids in efficiently prioritizing and mitigating prospective risks.
For every potential failure under scrutiny, specific ratings are given for its severity, how often it may occur, and the probability of detecting it before it leads to issues.
- The severity rating reflects the degree to which the failure affects product performance.
- The likelihood that a particular failure will happen is expressed via an occurrence rating.
- Detection rating measures how well one can identify a pending issue or malfunction
Assigning these criteria-based values for assessing risks linked with various failures within products helps stakeholders tackle them systematically.
To illustrate further, numerical scores between 1 (least severe/likely/detectable) and 10 (most severe/likely/detectable) represent severeness levels of impact on functionality, frequency
estimates regarding said event materializing into actuality—and gauging our capability at
pinpointing such discrepancies beforehand respectively—to eventually calculate this risk
quantification factor when multiplied together.
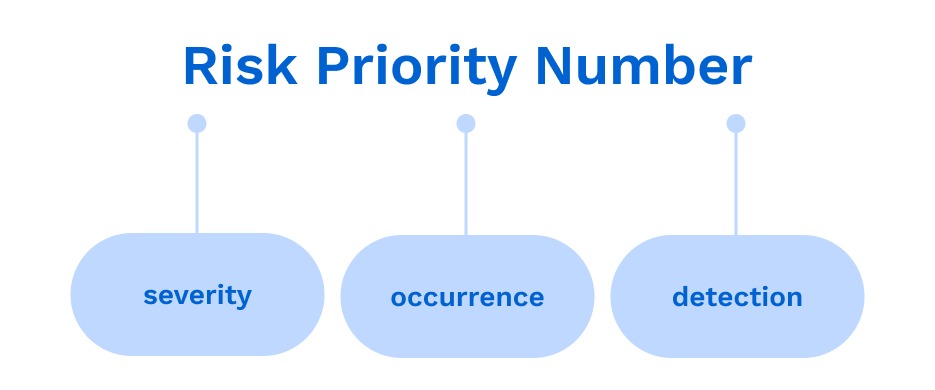
Source: WorkTrek
Prioritizing and Mitigating Risks
Within the framework of FMEA, a risk ranking table determines when corrective actions should be taken by evaluating the severity of potential failures, their likelihood of occurrence, and the effectiveness of their detection methods. Corrective measures are initiated for issues that register within specific RPN thresholds or exhibit particularly high levels of severity to ensure prompt attention to significant concerns.
Alterations in product design or attributes necessitate modifications to DFMEA action plans so they align with updated risk assessments. The continual updating process maintains the FMEA document as an active tool in managing risks effectively, ensuring control and action plans remain relevant and up-to-date following any changes made.
Source: Centraleyes
FMEA Examples and Case Studies
FMEA has played a critical role across different sectors by bolstering design processes and minimizing problems within systems. In the software sector, for example, deploying FMEA resulted in enhanced design procedures and fewer system issues.
FMEA also benefits the automotive industry, improving vehicle safety measures and lowering the chances of widespread product recalls.
Process FMEAs have been essential in reducing unforeseen machine stoppages and protecting against production capacity loss by scrutinizing existing processes. The transportation and logistics industries have leveraged FMEAs to boost operational efficiency, refine processes, and mitigate logistical hurdles.
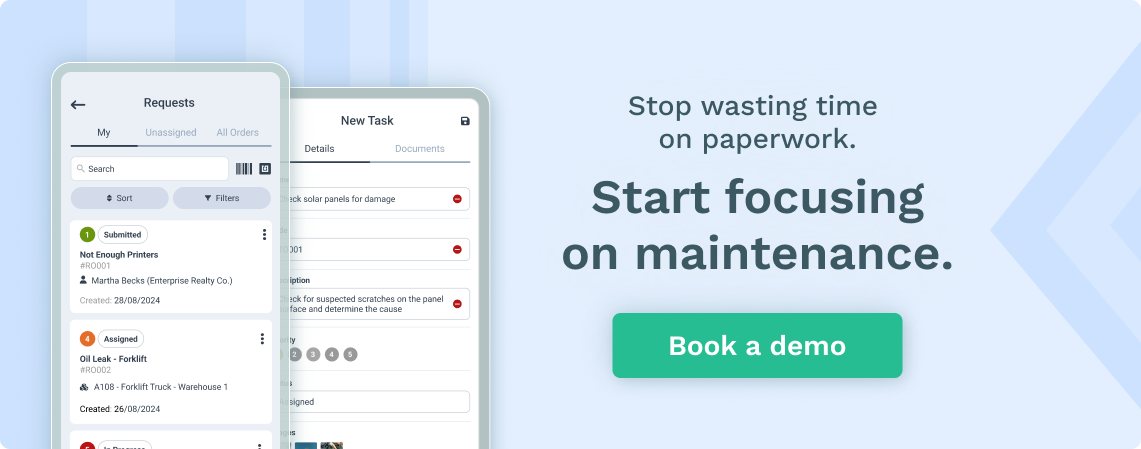
Source: Riskconnect
FMEA Tools and Techniques
Failure Modes and Effects Analysis (FMEA) methodologies include various tools, such as software programs, process flow diagrams, and databases cataloging standard failure modes.
FMEA applications facilitate the pinpointing of probable points of failure within an organization’s processes. They also rank associated risks and execute preventive actions to improve quality control.
These advanced programs provide an array of risk evaluation instruments, historical record-keeping functions, automated alerts for users, personalized report generation options, and capabilities for team collaboration from remote locations.
Integration capabilities enable FMEA systems to work harmoniously with Enterprise Resource Planning (ERP) frameworks and Quality Management Systems (QMS), ensuring aligned operations across business platforms.
The trend toward cloud-based FMEA solutions is growing because they offer convenient access from anywhere at any time and remain current in their assurances regarding data security.
Automated features built into these systems reduce manual labor by streamlining entries related to data capture tasks, computation or estimation efforts regarding risk severity levels assessments, and report preparation processes necessary for strategic planning sessions.
In conjunction with software utilities employed early during analysis, process flowcharts help map every component involved within the operational sequences, thereby supporting thorough evaluations carried out under FMEA guidelines.
Creating detailed records identifying recurring patterns linked to different types of failures, their origins, and potential consequences optimizes the efficiency of analysis by drawing upon established corporate wisdom accumulated over time.
Source: Advance Innovation Group
FMEA Best Practices and Common Pitfalls
Defining a precise scope for FMEA activities can optimize the discussion process and improve outcomes. Incorporating various viewpoints from stakeholders such as cross-functional teams and customers in the FMEA initiative can broaden the analysis’s depth.
By motivating active engagement from individuals on both the business and technical sides, you fortify the integrity of the FMEA procedure while ensuring its uniform execution across different sectors.
Employing software designed for FMEAs may result in the following:
- Heightened productivity
- More efficient workflows
- Better quality control measures
- Diminished labor expenses related to conducting an FMEA
Incorporating changes in supply chain inputs into your FMEA worksheets is essential to consider how they might influence system risks. Vigilance against common errors is crucial. Depending exclusively on Risk Priority Number (RPN) thresholds may not lead to effective risk management because it could make teams prioritize achieving lower scores over mitigating risks effectively.
Selecting a suitable risk ranking table hinges upon organizational context and specific qualities inherent in product or process design details. Choices around these specifications should be made by those performing analyses or decision-makers within an organization.
Source: Entrepreneur
FMEA and Its Connection to Risk Management
While separate fields, risk management and failure modes and effects analysis (FMEA) are interrelated practices that utilize a common language and aim to enhance reliability. FMEA aids in risk management by offering vital knowledge for pinpointing potential failures and evaluating their impact as part of a broader risk management approach.
Key failure modes and their impacts are incorporated into the FMEA assessment, drawing on well-established risk management procedures. The interplay between technology, risk management, and FMEA significantly shapes their evolution.
Cutting-edge software designed for FMEA leverages predictive analytics and artificial intelligence capabilities to amplify the detection of risks across company operations.
Source: Ipkeys
FMEA Resources and Further Learning
Individuals aiming to expand their knowledge of FMEA have various resources. Such materials cover an extensive array consisting of:
- Books
- Articles
- Courses
- Videos
- Online Training and Resources
These mediums deliver in-depth information on the methodologies, applications, and optimal practices associated with FMEA.
The detailed content available within these FMEA resources comprises articles, case studies, and scholarly publications. These elements provide perspectives into how FMEA has been applied practically, as well as recent research developments and actual case studies that can act as beneficial educational references for novices and seasoned experts.
Summary
This guide thoroughly examines the Failure Mode and Effects Analysis (FMEA), elaborating on its diverse forms, essential elements, and implementation across different fields. We dissect the systematic approach to FMEA, discuss how Risk Priority Numbers (RPN) aid in evaluating risks, and outline methods for ranking and addressing those risks.
By looking at real-world examples and analyses from various industries, we’ve observed FMEA’s effectiveness when applied practically. This article considered several techniques employed within FMEA and best practices to adhere to—while also cautioning against typical mistakes—all framed within the larger context of risk management strategies. We intend this document to be a foundational tool for deepening your grasp of FMEA principles while fostering Study in this field.