Get a Free WorkTrek Demo
Let's show you how WorkTrek can help you optimize your maintenance operation.
Try for freeThe food and beverage industry has to deal with many levels of complexity. Downtime is costly, and food safety and quality management are key to the health and safety of customers. Regulatory compliance issues and audits can be time-consuming. Keeping up with all these processes and associated documentation and data requires effective maintenance management systems and real-time insight into operating conditions.
Using CMMS in the food and beverage industry
With the advent of cloud-based software, food and beverage processors are increasingly using CMMS (Computerized Maintenance Management System) software to achieve this goal, which not only enables workforce management but also centralizes and aggregates data from multiple source data. By integrating with software across the enterprise, such as SCADA (Supervisory Control and Data Acquisition) systems or ERP (Enterprise Resource Planning) systems, and connecting to condition monitoring sensors, modern maintenance software is changing the way maintenance teams work.
Performing maintenance based on asset health improves the effectiveness and efficiency of maintenance planning. For example, analytics software can identify issues as data from condition monitoring sensors comes in, and a CMMS can aggregate condition monitoring alerts. Maintenance teams can then respond instantly when and where they are needed most. Data-driven maintenance decisions can reduce unplanned downtime and overall maintenance costs. Combined with machine-installed sensors, today’s software solutions can reduce the risk of recalls, streamline compliance processes, and maximize asset availability.
Read also 20 benefits of CMMS for businesses
In addition to maintaining equipment, food, and beverage processors must monitor the safety and nutritional quality of their products. You must comply with the proper handling and storage of raw materials and finished products. To avoid waste, effective inventory management is essential. Standardized processes and workflows ensure the safety of food and beverages produced and the safety of workers during production.
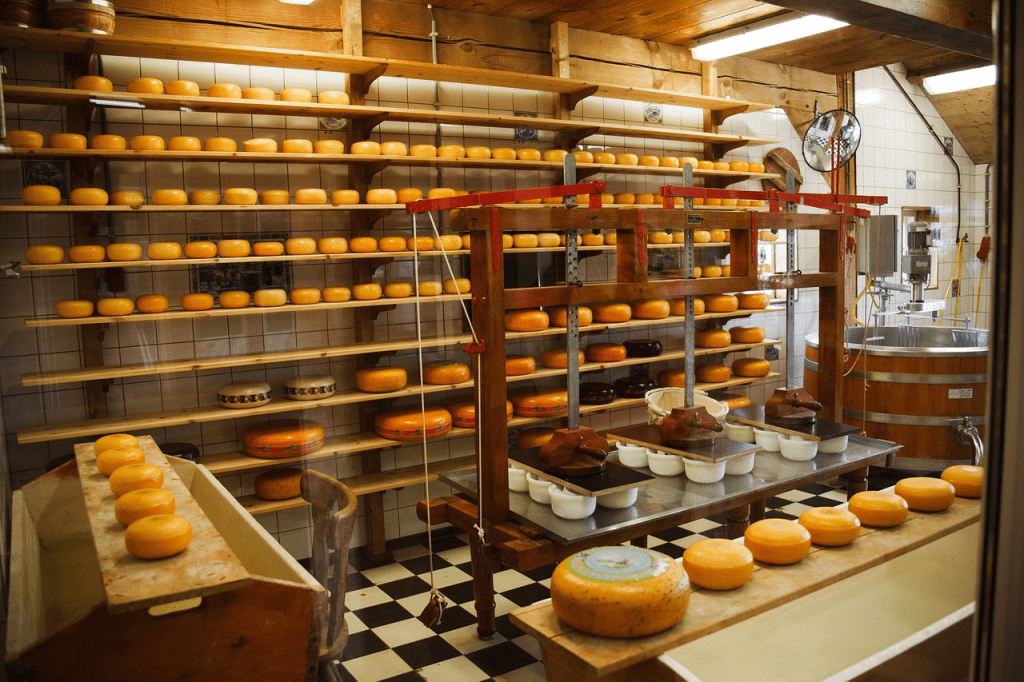
Benefits of CMMS for the food and beverage industry
The integration of software and sensors opens up new possibilities. Many food and beverage processing plants use SCADA systems to monitor their production lines in real-time. A CMMS can collect SCADA data and combine it with automatically generated condition monitoring alerts to help teams respond quickly and make informed decisions about equipment repairs. The integration of multiple data sources enables faster and better maintenance decisions and maximizes the use of maintenance resources. With staffing constraints faced by many organizations today, the ability to remotely monitor assets using sensors is beneficial.
Planning And Management Of Industrial Maintenance
How to achieve effective maintenance management?
Effective maintenance management should primarily focus on eliminating failures through good control and analysis. Then you have to work hard to ensure and extend the life of your equipment, especially those that play an important role in your plant’s production process.
In addition to containing and reducing breakdowns, it is also important to implement a preventive maintenance strategy. When we act before failures occur, we can increase equipment reliability and reduce costs.
In this way, resources can be gradually shifted from corrective maintenance to preventive and predictive maintenance. The latter is maintenance based on the analysis of certain variables of the equipment that can tell us when a machine is about to break down.
What are the most common challenges industrial companies face in managing asset maintenance?
We often find that organizations are very focused on dealing with failures, but not actively managing them or analyzing them thoroughly to prevent them from happening again.
On the other hand, we have found that in most cases there is a clear lack of time and resources to design and implement a good preventative maintenance program. This prevents companies from prioritizing preventive actions, which are always less costly than corrective actions.
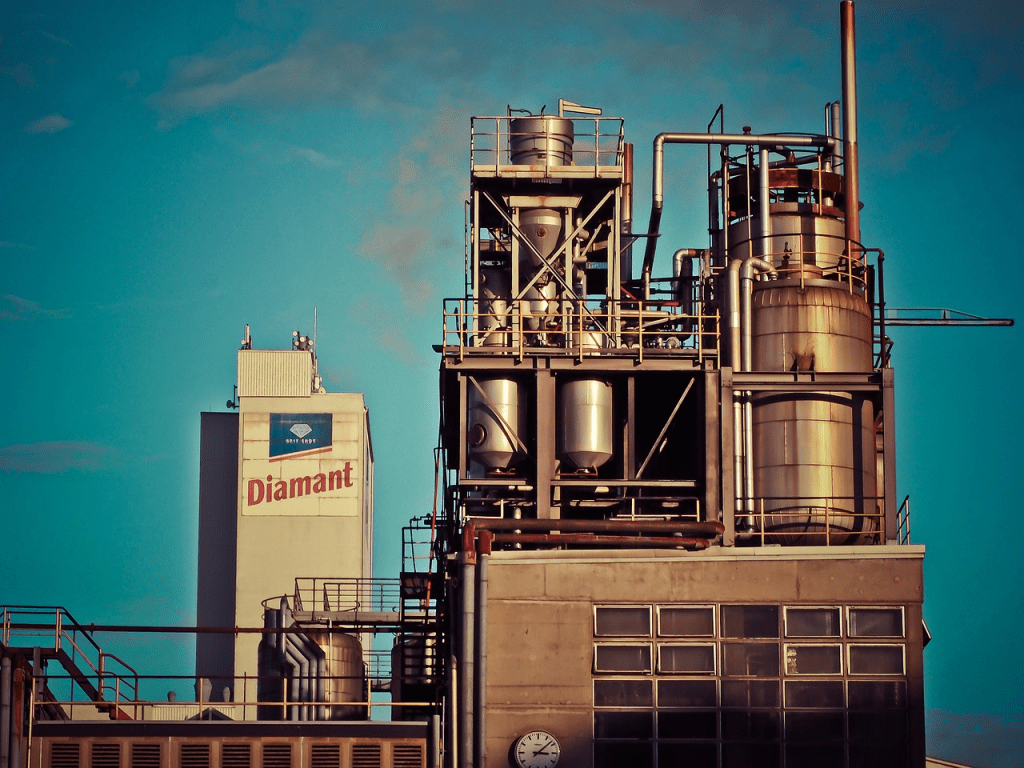
Implementation Of CMMS Software
What are the key benefits of implementing CMMS software in an industrial business?
CMMS software enables industrial companies to collect, manage, and store vast amounts of data about plant maintenance processes. This enables organizations to easily visualize relevant information in real time and make decisions more effectively and quickly.
Additionally, CMMS solutions help companies focus on the most important issues, keep maintenance costs to a minimum, and manage spare parts efficiently.
What are the initial concerns of industrial companies when introducing CMMS software?
Most importantly, the solution was implemented but not used. After all, CMMS software is only useful if you know how to use it effectively and take advantage of all CMMS features. It does nothing by itself; it must be an aid to good management.
What factors should be considered when choosing a CMMS?
When choosing a CMMS for Food and Beverage Industry, we should look for a solution that is powerful, easy to use, intuitive, user-friendly, and simple. It is more important than ever that it is cross-platform and includes versions for mobile devices.
Finally, and interestingly, a CMMS can be connected to other production and quality management software to provide a global view of the plant.
Supercharge your maintenance with WorkTrek CMMS!
Book a WorkTrek demo to see how a CMMS can help your business.
Try for freeFood Sector
In the specific case of the food sector, the needs for innovation and digital transformation derive mainly from two needs: to improve one’s performance and optimize processes (as in any other sector) and to respond effectively to the requirements of regulations and regulatory provisions. Process improvement is reported as a priority by most companies, while it is a fact that the food sector has to juggle multiple rules and standards, some mandatory, others optional, but still challenging.
This is how the interweaving of documentation, practices, and registrations begins, necessary to meet the requirements of European standards, such as the Food Law CE 178/2002, the ISO 9001 standard for Quality Management Systems, the HCCP system, also incorporated in ISO 22000 for food safety management systems, ISO 22005 for traceability systems in the food and feed chain and, finally, GMP good manufacturing practices. This list is certainly not exhaustive, but indicative of the main peculiarities of the sector. The entire “company ecosystem” is involved, with rules for the management of human resources and training, risk analysis, product quality levels, process monitoring, and so on.
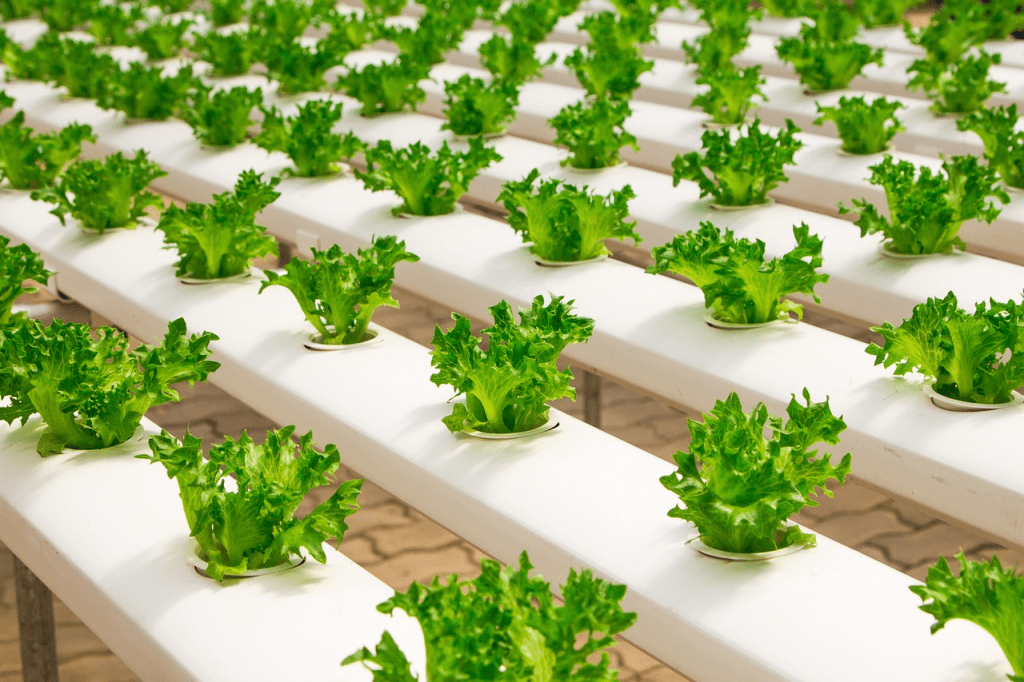
Read more about, European standards and Food law.
The process of managing the production infrastructure necessary for the manufacturing, packaging, and transport of food and materials and objects in contact with food is no exception. In reality, the obligation of correct maintenance arises upstream of the food sector, as also envisaged for Health and Safety at Work, which in a certain sense represents the basic level from which to start. There are many more steps to take.
In fact, maintenance is also a key activity for product quality, process efficiency, and – especially in the food sector – product safety.
This is how, in order to achieve truly remarkable results, technology becomes an indispensable tool for these production realities. Many companies have already implemented a computerized maintenance process management system (CMMS).
See also, how to implement CMMS software.
Food Industry Problems
Equipment reliability
Without regular maintenance, equipment failure, human error or measurement errors can affect throughput and profits.
Food waste management
Machine failure or failure not only disrupts production but also increases food waste.
Asset management decisions
While absolutely necessary, without easy access to asset history and maintenance data, management may not be able to allocate upfront funding for asset replacement.
Managing food safety regulations
Many food companies find it difficult to demonstrate FDA, USDA, and ISO 22000 compliance with the required documentation.
Maintenance operations
Spreadsheet-based work order management has limitations and is extremely inefficient when workloads are high.
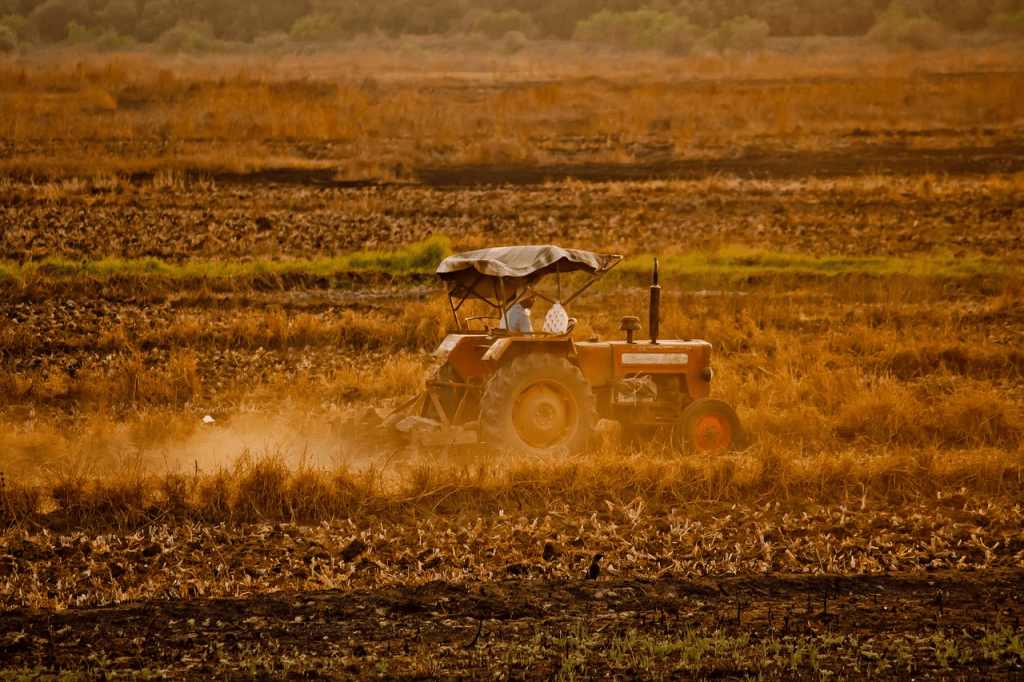
What Are Some Common Tasks In Food And Beverage Manufacturing?
Because food and beverages are consumables and contamination can be life-threatening, many manufacturing tasks involve the safe handling and processing of raw materials and final products.
Raw material handling
For example, most ingredients are perishable, requiring precise and careful management of ingredient sourcing, transport, storage, dates, and labeling. Safe processing and minimizing waste requires ensuring that inventory is properly ordered, used, and stored.
Combination process
The next stage usually involves tasks such as washing produce, cutting meat and vegetables, and mixing them with spices and other items to make food. It is important that processed foods remain consistent in taste, appearance, and quantity from batch to batch.
Much food production is done in batches and labeled accordingly, so if something goes wrong, a recall can be initiated to warn consumers of a potential problem.
Packaging and storage
Once the finished product is ready, it needs to be packaged into properly sized-containers for sale. Available in single-serving packs, family packs, or bulk packs. Regardless of size, effective packaging protects food and beverage products from contamination and spoilage and communicates a company’s brand and reputation.
Regulations and oversight
Many tasks in food and beverage manufacturing are related to compliance and regulation due to potential risks to human health. Ensuring food is produced in a safe, compliant, and hygienic manner can reduce the likelihood of foodborne illness. Employees must keep equipment and surfaces clean and sanitized and comply with all FDA and state regulations.
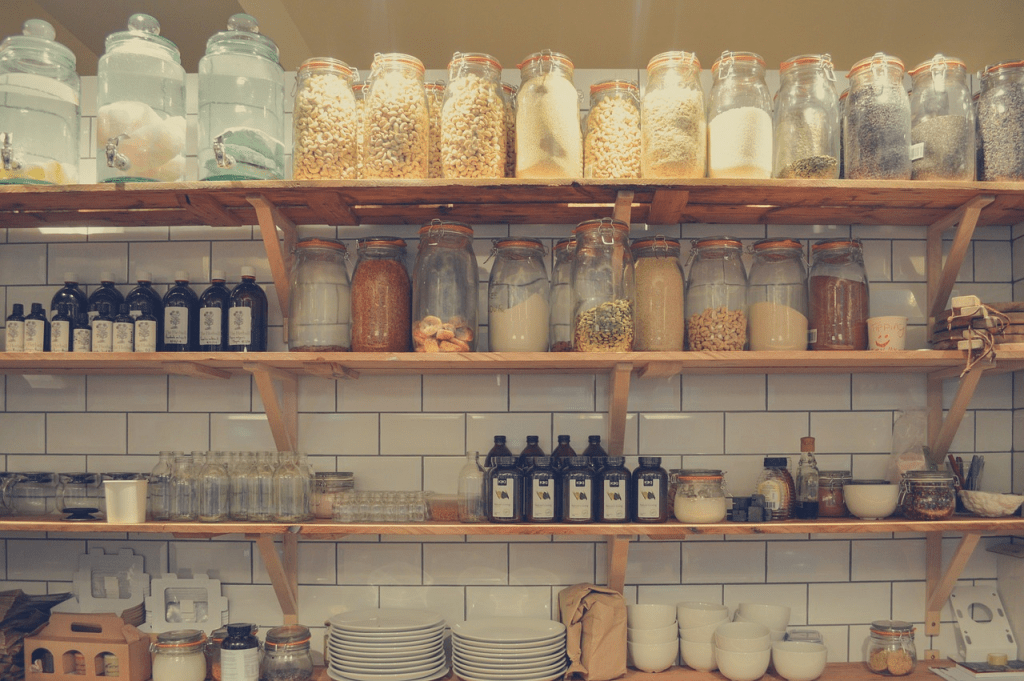
What Are The Benefits Of CMMS For Food Processing and Packaging?
Comply with food safety regulations
There are many agencies that regulate the food industry. To ensure that food manufacturers comply with health and safety regulations, these companies conduct inspections and audits. A compliance CMMS is capable of storing detailed documents such as safety manuals, standard operating procedures, and critical equipment and asset records. Just a few clicks (or one if you’re using a mobile device) are enough to retrieve the relevant data needed to demonstrate compliance. With a CMMS for food manufacturing, you can even create custom reports for inspectors and auditors.
Maintenance to reduce food waste
In addition to affecting production, disruptions in the food manufacturing process can also create a lot of waste. Food that cannot be processed on time due to malfunction or equipment failure must be discarded for health and safety reasons. CMMS for Food and Beverage Industry reduces the likelihood of equipment failure by ensuring regular preventive maintenance. This helps maintenance teams work more efficiently and reduce waste. Access to real-time information also enables employees to track inventory levels more efficiently, which helps prevent over-ordering.
Maximize equipment reliability
To be successful, food manufacturers need reliable equipment. Any disruption in food processing can severely impact production and, more importantly, profits. To maximize equipment reliability, regular preventive maintenance is required. CMMS for Food and Beverage Industry allows users to efficiently plan, schedule, and document preventive maintenance activities on any piece of equipment. Maintenance software helps maximize uptime and keep equipment running at its best.
Make smarter asset management decisions
Access to a comprehensive history of each asset, including data on failures and repairs, helps management make more informed asset management decisions. For example, each asset has an average lifespan, and budgets typically allocate funds for replacement when the asset reaches the end of its lifespan. However, with regular preventive maintenance and few unplanned repairs, assets can live well beyond their average lifespan. Management may choose to defer equipment replacement and allocate available funds to other urgent matters.
Modernize your maintenance process
If you’re still using spreadsheets to organize maintenance operations, it’s time for a change. While spreadsheets have limited functionality, CMMS software features offer task automation, data centralization, detailed analysis, advanced reporting, and more. Most reputable maintenance software solutions offer the ability to access the program on any web-based device, including mobile. Maintenance staff can easily manage work orders, work requests, and parts inventory while on the go. Dashboard functionality in CMMS software enables organizations to graphically view real-time data for a range of key performance indicators (KPIs) at any time. This allows management to keep their finger on the pulse of the organization, identify trends, and drive efficiencies.
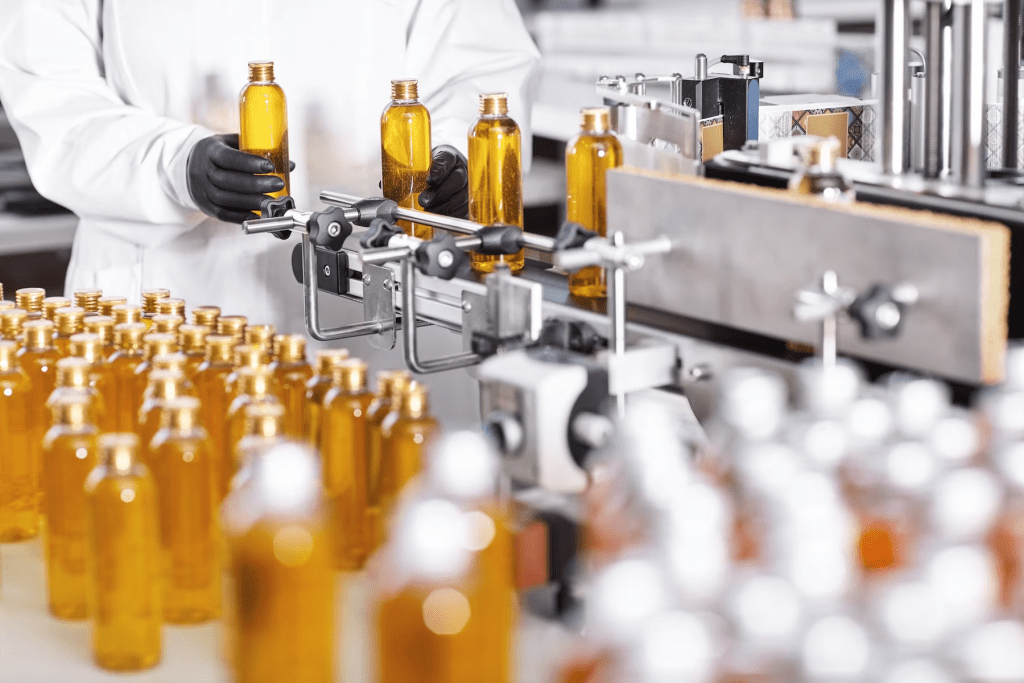
Conclusion
CMMS for Food and Beverage Industry offers you the opportunity to improve and enhance your goals in the industry. The industry’s demand for products, supply, and distribution, and the cost of delivering pharmaceuticals to each customer are high.
Every CMMS employee can deliver work to clients with the highest reliability, conduct inspections, and execute preventive programs to ensure the best quality. A CMMS is not only for managing but also for controlling your industry clients.
In the industry, the price and quality of the products are very high. CMMS is an application that can only be used after repeated projections. A corrective prevention program can help you improve and eliminate this condition. In order to produce a product, you need to spend some time before starting work.