Get a Free WorkTrek Demo
Let's show you how WorkTrek can help you optimize your maintenance operation.
Try for freeIntroduction
CMMS play an irreplaceable and indispensable role today. Previously, maintenance tasks required more time and effort and required extensive documentation such as work cards, clipboards, and maintenance logs. The use of a CMMS has several advantages, the most prominent of which is the saving of workers’ time, which they can use for something more important and thus boost their productivity.
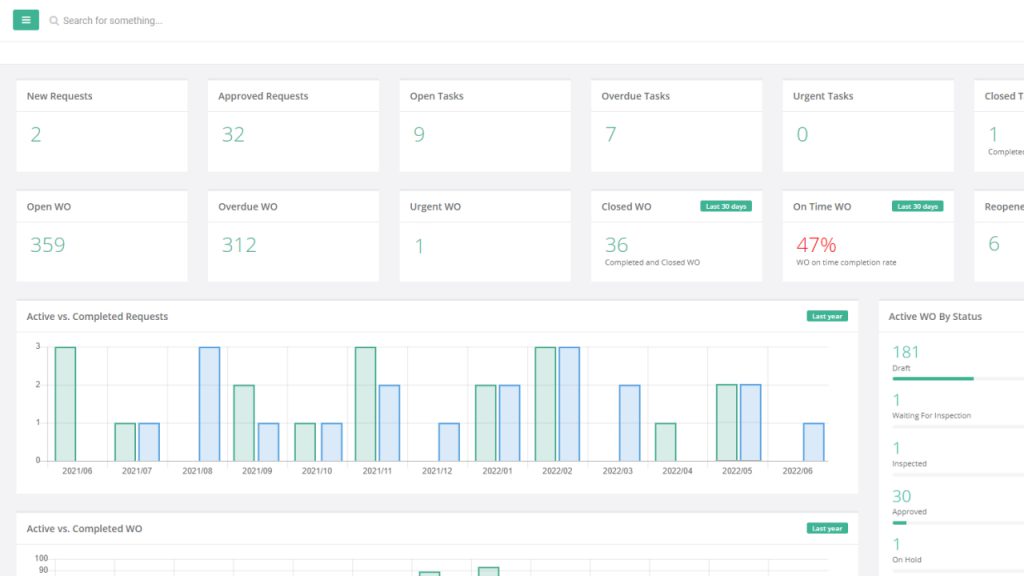
Reasons Why Your Company Needs a CMMS
CMMS Boost Employee Productivity: Companies thrive when they stay one step ahead of their competitors. To achieve this, they must use time efficiently and increase employee productivity, thereby increasing company profits.
Managers and officials can use computerized maintenance management systems to easily monitor employee work progress and assign new tasks remotely while gaining insight into work orders. This creates an efficient way to manage operations and quickly identify all types of issues that arise in management.
CMMS Helps Improve Asset Management: Managing and monitoring multiple assets across large industries is a fairly complex and time-consuming task. Companies miss opportunities to identify and solve problems.
Preventive maintenance is the function of monitoring assets to detect and correct any problems early before a major failure occurs. Companies can now ensure that their equipment is regularly maintained and in good condition.
CMMS Optimizes and Simplifies Maintenance Operations: Computerized maintenance management systems are designed to reduce manual intervention and increase operational automation.
A centralized system ensures that all data is stored in one place, making analysis easier and providing managers with valuable insights. The main benefit of automating operations is that a CMMS increases the overall productivity of assets and employees. Optimizing certain tasks ensures operations are monitored and regular maintenance is performed to prevent equipment failure.
CMMS Helps Save Money: Companies often lose significant time and money due to equipment failures that impact production and operations. This problem is caused by not maintaining the equipment properly and performing most of the operations manually, which is not an efficient approach.
A reliable solution is a computerized maintenance management system as a smart device for management and production. The software makes it easy to track individual devices and monitor their performance. This helps identify problems and prevent potential failures before they become serious problems.
CMMS can Improve Your Business with Data-Driven Decisions: Traditional asset management methods can be outdated and provide inaccurate insights because most data is stored in physical records.
The software uses advanced algorithms to provide accurate data insights so facility managers can make data-driven decisions with ease. Data-driven reporting provides a holistic view of resource allocation and production. Companies can identify patterns and opportunities to solve major problems in production and improve business efficiency while reducing downtime and costs.
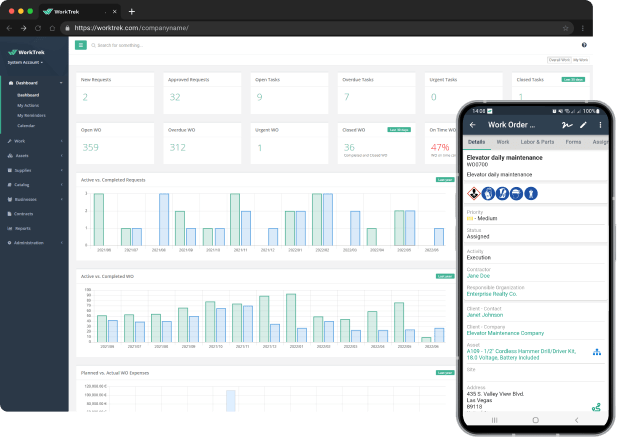
What is Business Productivity?
Business productivity is the efficiency and effectiveness with which a company uses its resources to achieve its goals. It is a measure of the output or results achieved relative to the inputs or resources consumed in the process.
The most important aspects of business productivity include:
Efficiency: The ability to achieve desired results with minimal resources, time and effort. This includes optimizing processes, eliminating waste and reducing inefficiencies to maximize output.
Effectiveness: The extent to which business activities and programs contribute to achieving organizational goals. This involves focusing on activities that deliver value and are aligned with strategic priorities.
Quality: The standard of excellence or satisfaction achieved by a product, service, or process. Effective processes lead to high-quality results that help increase customer satisfaction, loyalty, and retention.
Innovation: The ability to introduce new ideas, products, services, or processes to increase productivity, competitiveness, and performance. Innovation drives company growth, differentiation and sustainability.
Employee Engagement and Satisfaction: The extent to which employees are motivated, committed and satisfied with their roles. Engaged and satisfied employees are more productive, creative, and loyal, thereby contributing to overall business success.
Customer Satisfaction and Loyalty: How satisfied customers are with a company’s products, services, and experiences. Satisfied customers are more likely to make repeat purchases, recommend the company, and drive sales growth.
Financial Performance: A company’s ability to generate sales, profitability, and return on assets. Efficient companies manage costs effectively, maximize revenue streams, and achieve sustainable financial performance over time.
By continually improving processes, leveraging CMMS, empowering employees, and focusing on creating value for customers, companies can increase productivity and achieve long-term success.
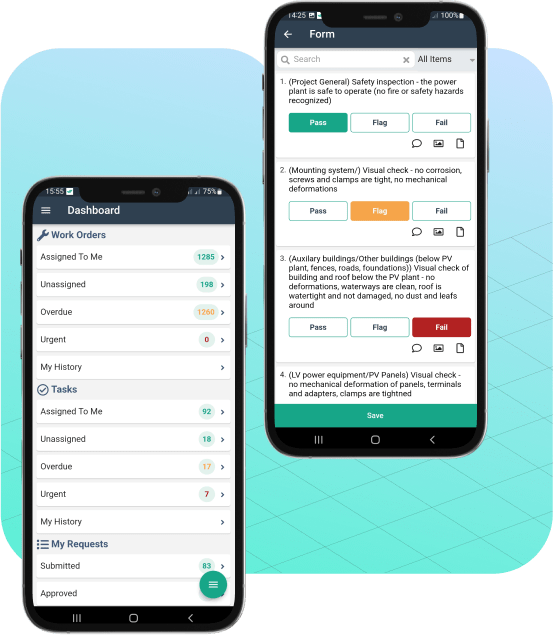
How to Boost Productivity With a CMMS?
Boosting productivity with a CMMS (Computerized Maintenance Management System) requires leveraging the software’s features and capabilities to streamline maintenance processes, optimize resource utilization, and improve overall operational efficiency. Here are a few strategies for achieving this goal:
Simplify Work Order Management: Automate and simplify work order creation, assignment, and tracking with a CMMS. Implement standardized workflows and templates to ensure consistency and efficiency in handling maintenance requests and tasks.
Implement a Preventive Maintenance Program: Use a CMMS to plan and manage preventive maintenance tasks based on equipment reliability data, manufacturer recommendations, and regulatory requirements. Implementing a preventive maintenance program can help minimize unplanned downtime, extend asset life, and improve overall reliability.
Simplify Inventory Management: Track inventory, manage spare parts, and optimize purchasing processes with a CMMS. Implement inventory optimization techniques, for example, setting reorder points, conducting regular audits, and using supplier management tools to ensure adequate inventory levels and minimize stock-outs.
Leverage Mobile Capabilities: Leverage CMMS mobile apps to enable maintenance technicians to access work orders, update task status, and record field maintenance activities. Mobile capabilities increase technician productivity by enabling real-time communications, reducing paperwork, and speeding up response times.
Enable Predictive Maintenance: Use a CMMS to implement a predictive maintenance strategy that leverages data analytics and predictive algorithms to predict equipment failures and proactively plan maintenance. Predictive maintenance helps detect problems before they cause costly downtime, allowing for timely intervention and optimal resource allocation.
By implementing these strategies and effectively leveraging CMMS capabilities, companies can increase productivity, optimize maintenance operations, and achieve operational excellence.
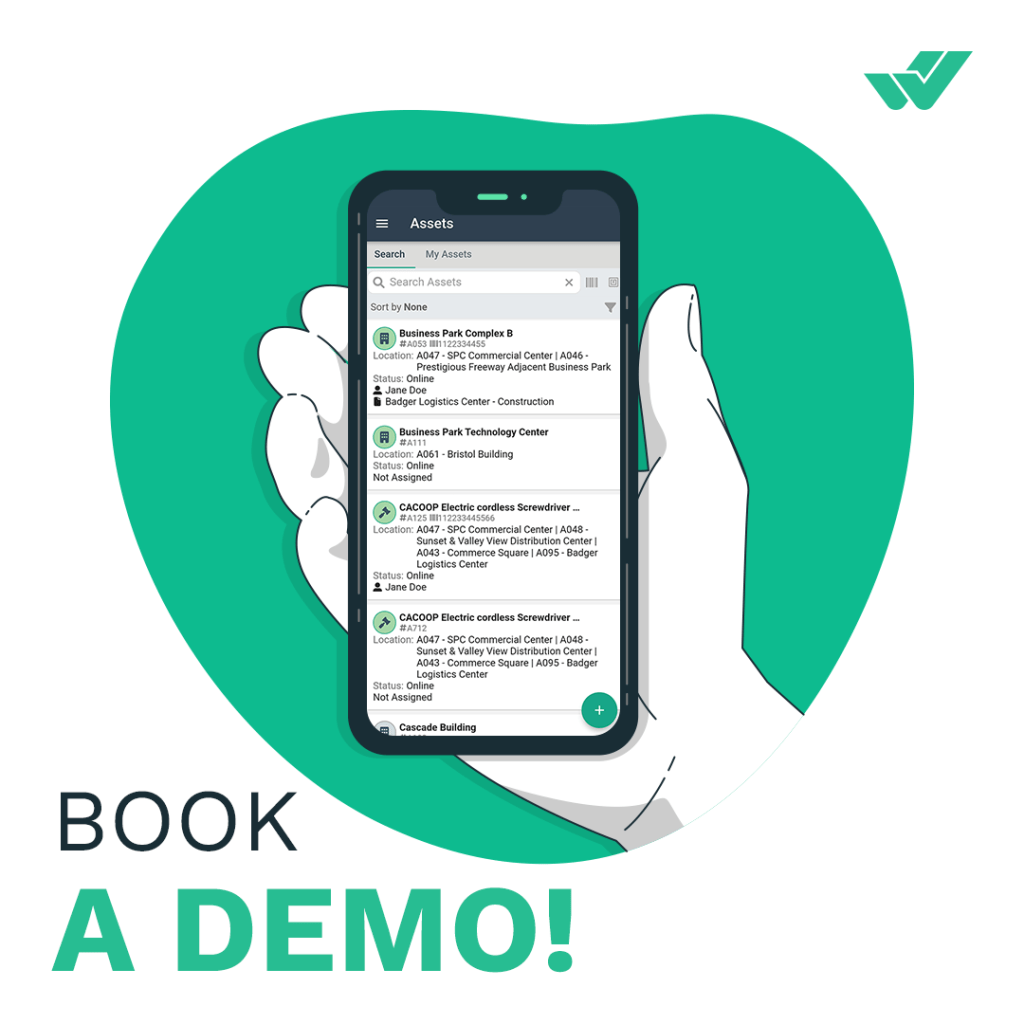
How Does a Mobile CMMS Boost Productivity?
In the rapidly evolving digital age, facility managers are constantly looking for innovative solutions to optimize facility operations and increase productivity. Mobile CMMS (Computerized Maintenance Management System) is one such transformative solution that has revolutionized the facilities management landscape.
A mobile CMMS can significantly boost productivity in a number of ways:
Real-Time Access: With a mobile CMMS, maintenance technicians have real-time access to work orders, asset information and maintenance history, no matter where they are. This eliminates the need to return to a desktop computer or office to retrieve information, allowing technicians to stay productive on the go.
Improved Communication: Mobile CMMS enables seamless communication between technicians, supervisors, and administrators through instant messaging, notifications, and alerts. Technicians can collaborate effectively, share updates, and request help when needed, improving teamwork and productivity.
Reduce Paperwork: A mobile CMMS eliminates manual paperwork and data entry by allowing technicians to record maintenance activities, take photos and update asset information directly from their mobile devices. This simplifies administrative tasks, reduces errors and saves time.
Barcode and QR Code Scanning: Many CMMS mobile apps support barcode and QR code scanning capabilities, allowing technicians to quickly identify assets, access relevant information, and easily update asset data. This increases the efficiency and accuracy of asset management and maintenance tasks.
Improved Task Management: A mobile CMMS provides technicians with a centralized platform to effectively manage and prioritize their tasks. Technicians can view assigned work orders, review task details, and organize workload to maximize productivity and complete tasks on time.
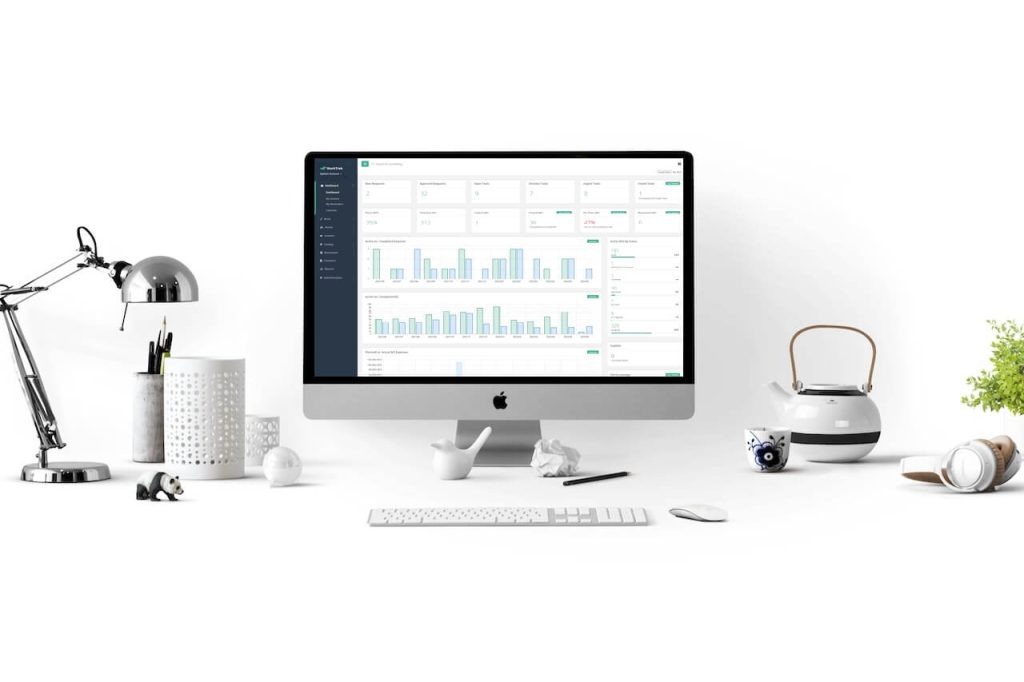
What are the Top 10 Benefits of a CMMS?
The 10 main advantages offered by CMMS software are:
Plan Maintenance Interventions: Using a CMMS, you can create maintenance plans and execute them individually for each type of equipment. This makes it possible to develop different types of temporary interventions for each plant or group of plants with similar requirements.
Process Work Orders Immediately: With a centralized system, work orders can be created, prioritized, submitted, and managed in an efficient and often automated manner, reducing the cost of paper documentation and programming.
Reduce Maintenance Costs: A CMMS can help you track maintenance costs, monitor investments, create shared reports and save money when needed.
Real-time Asset Information: With data continuously collected in a centralized cloud, everyone can instantly get all the information about an asset with just one click, simplifying problem identification and intervention methods;
Resource Monitoring and Control: To overcome issues related to shortages or excessive material costs, a CMMS allows you to monitor and manage resource inventory and track inventory items, special orders, or miscellaneous movements.
Accelerate Inspections and Repairs: By constantly monitoring resources, repairs and inspections can be accelerated and unplanned downtime reduced. In fact, a CMMS allows you to view the history of problems and repairs in order to intervene in the shortest possible time.
Extended Asset Life: Resources that are continuously monitored and maintained in an efficient condition through inspections and planned temporary interventions will naturally extend their useful life.
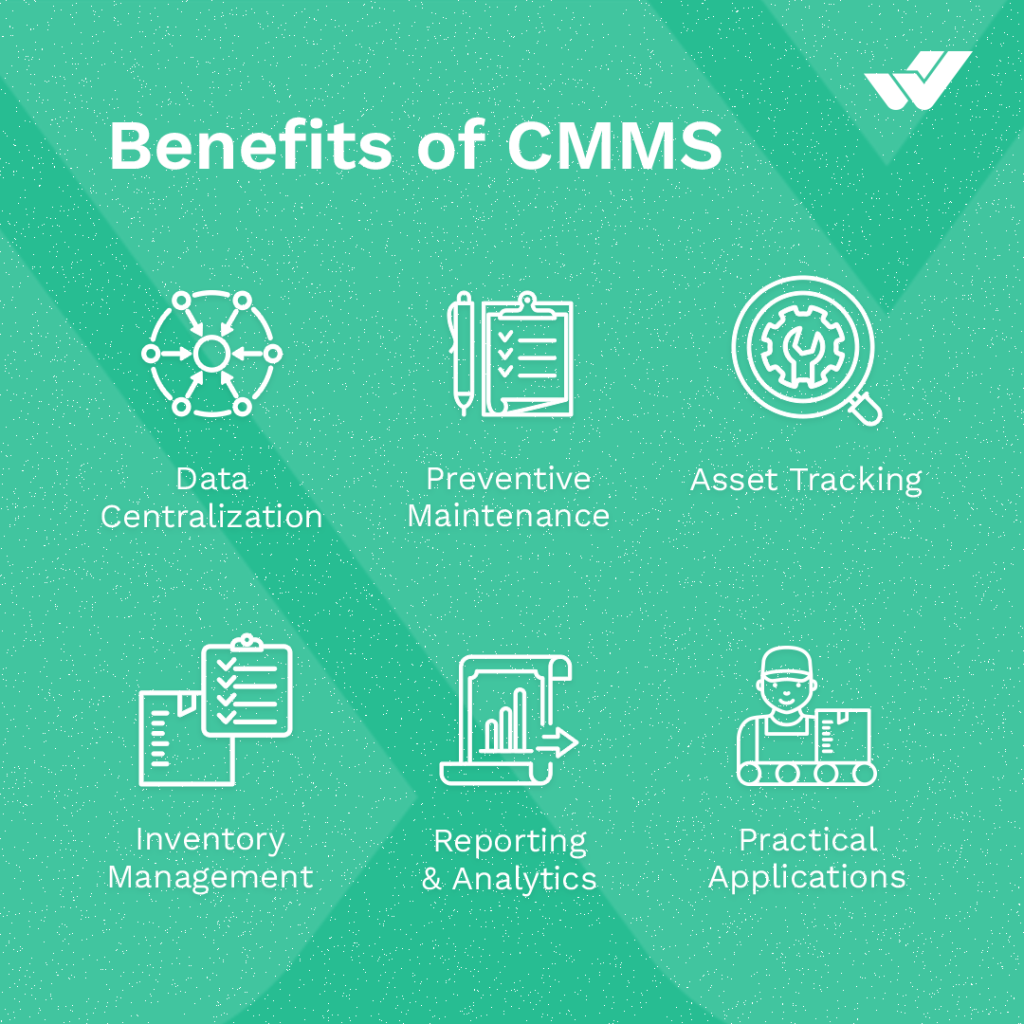
Boosting Productivity with CMMS – Conclusion
Implementing CMMS software can bring significant benefits to companies looking to increase productivity, reduce operating costs, and ultimately increase return on investment (ROI). CMMS solutions streamline maintenance operations and minimize equipment downtime by leveraging advanced features and capabilities such as predictive maintenance scheduling, real-time monitoring, and data-driven analytics. Efficient allocation of resources, improved equipment lifecycle management and regulatory compliance further contribute to cost savings and operational efficiency.
Contact WorkTrek today to learn more about our services!