What is Time-Based Maintenance?
Time-based maintenance (TBM) is a preventative maintenance strategy that schedules maintenance activities at predetermined intervals based on elapsed time, operating hours, or cycles, regardless of the asset’s actual condition.
It operates on the principle that equipment failures can be prevented by performing maintenance tasks at regular intervals before the equipment is likely to fail.
Unlike reactive maintenance (which waits for equipment to fail before taking action) or condition-based maintenance (which monitors the actual condition of the asset to decide when maintenance is needed), time-based maintenance follows a fixed schedule determined by historical data, manufacturer recommendations or industry standards.
Key Characteristics of Time-Based Maintenance:
Time-based maintenance is characterized by several important features that distinguish it from other maintenance approaches. Managing maintenance activities effectively through scheduling and tracking is crucial for ensuring timely interventions and optimal equipment performance:
- Predetermined Intervals: Maintenance activities are scheduled at specific intervals, which may be based on calendar days, operating hours, production cycles, or distance traveled.
- Preventive Nature: It aims to prevent failures before they occur rather than fixing equipment after it has already failed.
- Standardized Procedures: Time-based maintenance typically follows standardized procedures for each maintenance task.
- Documentation and Record-Keeping: Detailed records are maintained for all scheduled maintenance activities, including dates, tasks performed, parts replaced, and technician information.
- Independent of Equipment Condition: Maintenance is performed regardless of whether the equipment shows signs of deterioration or not.
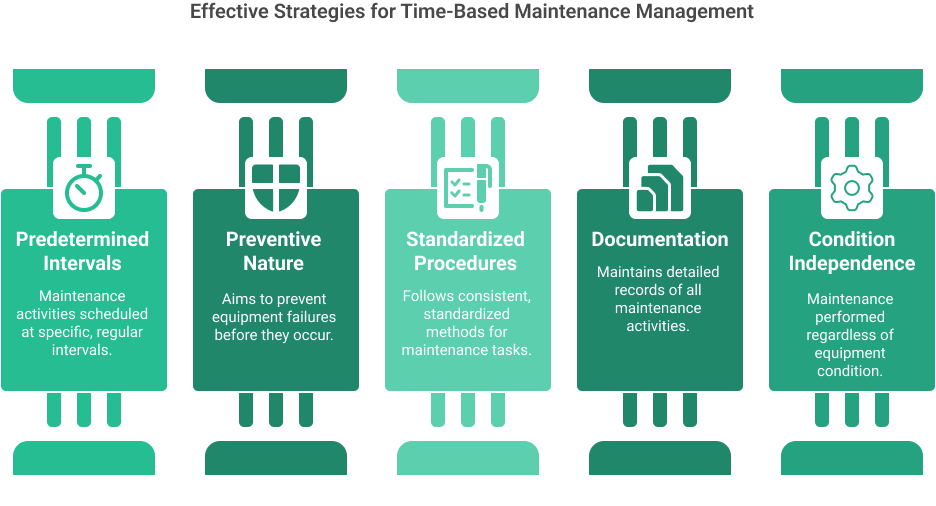
Types of Time-Based Maintenance:
Time-based maintenance can be categorized into several types based on the trigger for maintenance activities:
- Calendar-Based Maintenance: Scheduled according to calendar time (daily, weekly, monthly, quarterly, or annually).
- Usage-Based Maintenance: Triggered by accumulated usage such as operating hours, mileage, number of cycles, or production count.
- Regulatory-Driven Maintenance: Performed to comply with industry regulations, safety standards, or legal requirements.
- Seasonal Maintenance: Conducted at specific times of the year, often in preparation for seasonal changes or operational demands.
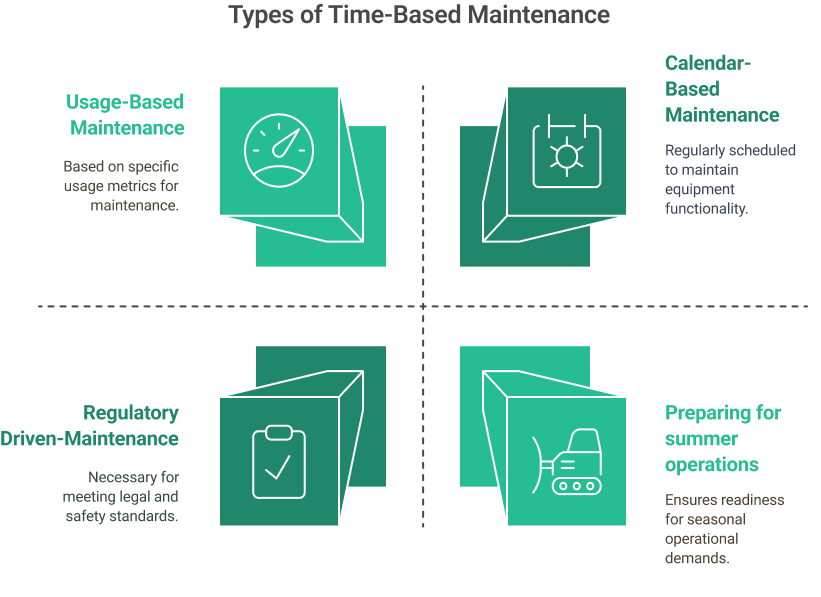
Types of Maintenance
Maintenance strategies are essential for ensuring the longevity and reliability of equipment. Several types of maintenance approaches exist, each with its methodology and benefits. Understanding these strategies helps organizations choose the best approach for their specific needs.
- Preventive Maintenance: Preventive maintenance is a proactive approach involving performing routine maintenance tasks at fixed intervals to prevent equipment failure. This strategy identifies and addresses potential issues before they escalate into major problems. Preventive maintenance can be further divided into two subcategories:
- Time-Based Maintenance: This involves performing maintenance tasks at predetermined intervals, regardless of the equipment’s condition. It relies on historical maintenance data and manufacturer recommendations to set these intervals. Typical examples are routine maintenance tasks, such as oil changes or filter replacements.
- Condition-Based Maintenance: Unlike time-based maintenance, this approach involves performing maintenance tasks based on the actual condition of the equipment. It uses inspections and monitoring tools to assess when maintenance is needed, ensuring that tasks are performed only when necessary.
By implementing preventive maintenance, organizations can reduce the risk of unexpected equipment failures, enhance reliability, and extend the lifespan of their assets.
Predictive Maintenance
Predictive maintenance takes a more advanced approach by using sensors, IoT devices, and machine learning algorithms to predict when equipment will likely fail.
This strategy involves analyzing data from various sources, including sensors, maintenance records, and equipment performance data, to accurately forecast maintenance needs.
Predictive maintenance aims to identify potential issues before they become significant problems, allowing for timely interventions.
Organizations can reduce downtime, increase efficiency, and improve overall equipment performance by leveraging predictive maintenance tools.
This data-driven approach enhances reliability and optimizes maintenance schedules, ensuring that resources are used effectively.
Equipment Best Suited for Time-Based Maintenance
Time-based maintenance is not universally optimal for all equipment types. It works best for:
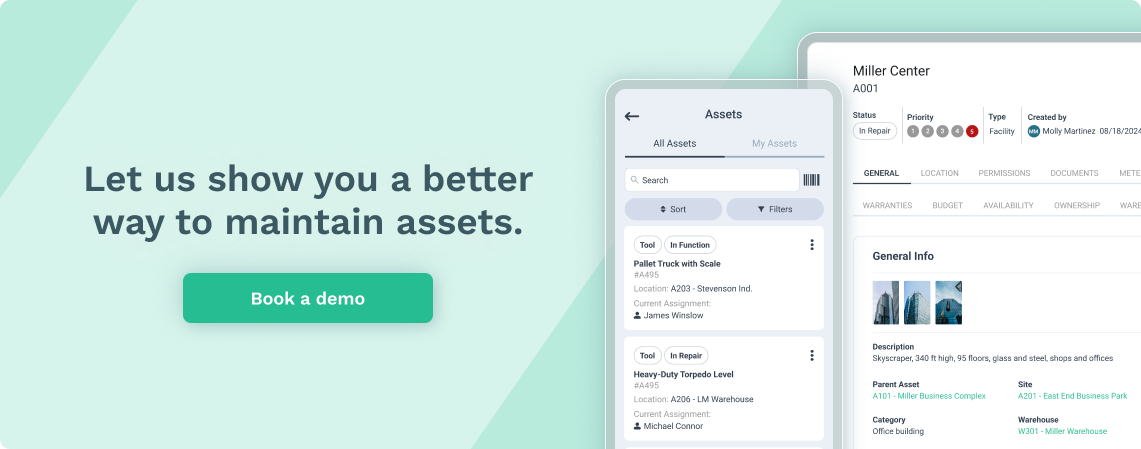
- Equipment with Predictable Wear Patterns: Machinery where components deteriorate relatively consistently and predictably.
- Critical Safety Systems: Equipment where failure could result in safety hazards, such as fire protection systems, emergency generators, and safety valves.
- Regulatory-Controlled Equipment: Assets subject to strict regulatory requirements that mandate periodic inspections and maintenance.
- Simple Mechanical Systems: Equipment with straightforward, well-understood and predictable failure mechanisms.
- Low-Cost, Non-Critical Assets: When the cost of preventive maintenance is significantly lower than the consequences of failure.
- Equipment with Clear Manufacturer Guidelines: Assets with detailed maintenance schedules provided by manufacturers based on extensive testing and field experience.
- Equipment with Limited Monitoring Capabilities: Older equipment without sensors or systems to enable condition monitoring.
- Equipment Operating in Stable Conditions: Machines operating under consistent loads and environmental conditions.
Examples of equipment well-suited for time-based maintenance include:
- HVAC systems (seasonal inspections and filter changes)
- Vehicles (oil changes, tire rotations)
- Pumps and motors with consistent operation
- Elevators and escalators
- Fire extinguishers and sprinkler systems
- Lighting systems (bulb replacements)
- Basic conveyors and material handling equipment
- Standard electrical panels and circuit breakers
Benefits of Time-Based Maintenance
Time-based maintenance offers several significant benefits that make it a valuable strategy for many organizations:
- Reduced Downtime: Time-based maintenance helps minimize unexpected equipment failures by performing maintenance tasks at fixed intervals, reducing downtime, and increasing equipment availability.
- Improved Equipment Reliability: Regular maintenance tasks can identify and address potential issues before they escalate, enhancing overall equipment reliability and performance.
- Increased Efficiency: Time-based maintenance streamlines maintenance activities, making planning and executing tasks easier. This efficiency reduces the time and resources required for maintenance.
- Cost Savings: Time-based maintenance can lead to significant cost savings by preventing unexpected breakdowns and extending the lifespan of equipment. Reduced downtime and fewer emergency repairs also contribute to lower maintenance costs.
- Improved Safety: Regular maintenance tasks help identify and mitigate potential safety hazards, reducing the risk of accidents and ensuring a safer working environment.
Adhering to a structured maintenance schedule can reap these benefits, ensuring that organizations’ equipment operates smoothly and efficiently.
Best Practices for Time-Based Maintenance
Implementing an effective time-based maintenance program requires attention to several key practices:
1. Establish Optimal Maintenance Intervals
The foundation of effective time-based maintenance is setting appropriate intervals for maintenance activities. To establish optimal intervals:
- Consult Manufacturer Recommendations: Begin with the manufacturer’s suggested maintenance schedules based on testing and design specifications.
- Analyze Historical Data: Review equipment failure history to identify patterns and adjust intervals accordingly.
- Consider Operating Environment: Factor in environmental conditions such as temperature, humidity, dust, and vibration that might accelerate wear.
- Evaluate Criticality: More critical equipment may warrant more frequent maintenance intervals to minimize the risk of failure.
- Incorporate Regulatory Requirements: Ensure compliance with industry regulations and standards that may dictate minimum maintenance frequencies.
2. Develop Comprehensive Maintenance Procedures
For each maintenance task, develop detailed procedures that:
- Clearly outline all steps required to complete the maintenance task
- Specify tools, parts, and materials needed
- Include safety precautions and personal protective equipment requirements
- Provide troubleshooting guidance for common issues
- Include verification steps to confirm the work was performed correctly
3. Implement Effective Planning and Scheduling
Proper planning and scheduling are crucial for time-based maintenance:
- Create a Master Maintenance Schedule: Develop a long-term schedule of all maintenance activities for all equipment.
- Balance Workload: Distribute maintenance tasks evenly to avoid overwhelming maintenance staff.
- Coordinate with Operations: Schedule maintenance during planned downtime or low-production periods when possible.
- Build in Flexibility: Allow for adjustments due to unexpected breakdowns or operational demands.
- Establish Priority Systems: Create clear guidelines for prioritizing competing maintenance tasks.
4. Train and Develop Maintenance Personnel
Ensure maintenance staff are properly trained:
- Provide equipment-specific training for technicians
- Cross-train staff to increase flexibility and knowledge-sharing
- Regularly update training as equipment and procedures change
- Develop troubleshooting skills to handle unexpected issues
5. Document and Analyze Maintenance Activities
Thorough documentation enables continuous improvement:
- Record All Maintenance Activities: Document date, time, tasks performed, parts used, and technician information.
- Track Key Performance Indicators: Monitor metrics such as MTBF, MTTR, and maintenance costs.
- Conduct Regular Analysis: Review maintenance records periodically to identify patterns, recurring issues, or opportunities for improvement.
- Implement Continuous Improvement: Use analysis results to refine maintenance intervals and procedures.
6. Integrate with Other Maintenance Strategies
Time-based maintenance works best when combined with other maintenance approaches:
- Complement with Condition Monitoring: Use inspections or monitoring for critical equipment to verify that the time-based schedule is appropriate.
- Implement Reliability-Centered Maintenance: For complex systems, use RCM analysis to determine which components are best suited for time-based maintenance.
- Incorporate Predictive Technologies: When economically justified, supplement time-based maintenance with predictive technologies.
7. Regularly Review and Update the Maintenance Program
A time-based maintenance program should evolve:
- Periodically reassess maintenance intervals based on actual equipment performance
- Update procedures to incorporate new techniques or best practices
- Adjust the program based on changes in equipment usage or operating conditions
- Review and revise the program after significant equipment failures or near-misses
Challenges and Limitations of Time-Based Maintenance
While time-based maintenance offers numerous advantages, it also comes with certain challenges and limitations:
- Over-Maintenance: Performing maintenance tasks at fixed intervals can sometimes lead to excessive maintenance, where tasks are performed unnecessarily. This can waste time and resources, leading to higher maintenance costs.
- Under-Maintenance: Conversely, time-based maintenance can also result in under-maintenance if the intervals are too long. This can lead to equipment failures and unplanned downtime, as maintenance tasks are not performed frequently enough.
- Limited Flexibility: Time-based maintenance can be inflexible, making it challenging to adjust maintenance schedules in response to changing equipment conditions or operational requirements. This rigidity can hinder the ability to respond to unexpected issues.
- Difficulty in Establishing Optimal Maintenance Intervals: Determining the best intervals for maintenance tasks requires significant data analysis and expertise. Setting optimal intervals can be challenging without accurate historical maintenance data and a thorough understanding of equipment performance.
- Limited Consideration of Equipment Condition: Time-based maintenance does not account for the actual condition of the equipment. This can lead to unnecessary maintenance tasks or missed opportunities, as the strategy relies solely on fixed schedules rather than real-time data.
Despite these challenges, time-based maintenance remains a valuable strategy when implemented correctly. Organizations can optimize their maintenance programs and achieve better results by understanding their limitations and integrating them with other maintenance strategies.
Using a CMMS to Manage Time-Based Maintenance
A Computerized Maintenance Management System (CMMS), is an invaluable tool for implementing and managing an effective time-based maintenance program. Here’s how a CMMS supports time-based maintenance:
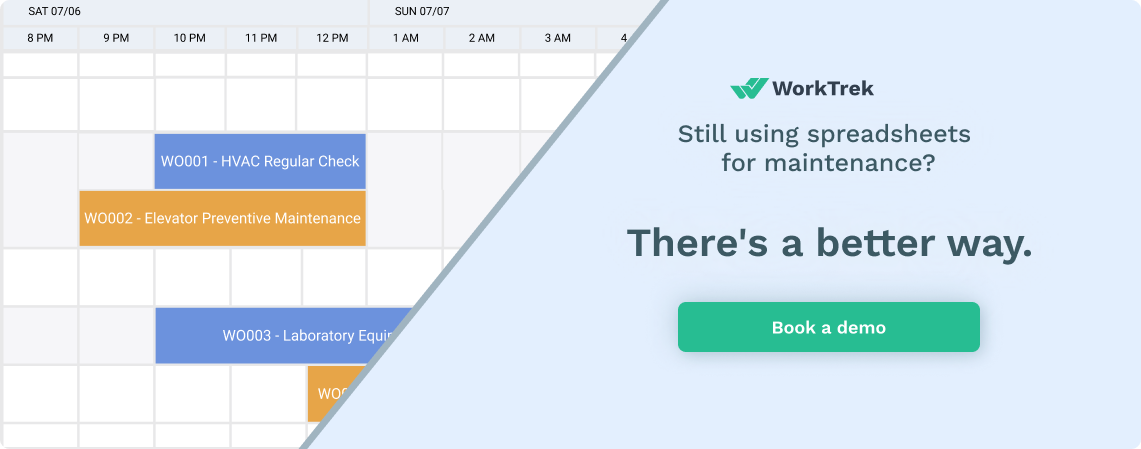
1. Automated Scheduling and Work Order Generation
A CMMS can dramatically improve the efficiency of time-based maintenance by:
- Automatically Generating Work Orders: Creating work orders based on predefined maintenance schedules without manual intervention.
- Setting Up Recurring Maintenance: Establishing maintenance tasks that repeat at specified intervals (daily, weekly, monthly, quarterly, or yearly).
- Scheduling Based on Multiple Triggers: Configuring maintenance schedules based on calendar time, equipment runtime hours, production counts, or other metrics.
- Providing Advance Notifications: Alerting maintenance supervisors and technicians about upcoming scheduled maintenance tasks.
- Managing Task Dependencies: Ensuring prerequisite tasks are completed before dependent tasks are scheduled.
2. Asset and Equipment Management
A CMMS provides a centralized database for all equipment information relevant to maintenance:
- Equipment Registry: Maintaining a comprehensive inventory of all assets with detailed specifications.
- Maintenance History: Recording all maintenance activities performed on each piece of equipment.
- Component Tracking: Managing individual components and subassemblies with different maintenance schedules.
- Documentation Repository: Storing equipment manuals, procedures, and warranty information.
- Location Tracking: Mapping equipment locations for efficient routing of maintenance personnel.
3. Resource Management
Effective time-based maintenance requires careful allocation of resources, which a CMMS helps manage:
- Personnel Scheduling: Assigning qualified technicians to appropriate maintenance tasks based on skills and availability.
- Parts and Inventory Management: Ensuring necessary parts are available for scheduled maintenance activities.
- Tool and Equipment Tracking: Managing specialized tools needed for maintenance tasks.
- Vendor and Contractor Management: Coordinating with external service providers for specialized maintenance activities.
4. Data Collection and Analysis
A CMMS enables data-driven decision-making through:
- Maintenance Metrics: Tracking key performance indicators such as compliance with scheduled maintenance, MTBF, MTTR, and maintenance costs.
- Failure Analysis: Recording failure modes and causes to inform maintenance interval adjustments.
- Cost Tracking: Monitoring labor hours, part costs, and downtime associated with maintenance activities.
- Trend Analysis: Identifying patterns in equipment performance and maintenance requirements over time.
- Reporting: Generating standard and custom reports to communicate maintenance performance to stakeholders.
5. Continuous Improvement of Maintenance Schedules
A CMMS facilitates the refinement of time-based maintenance programs through:
- Maintenance Optimization: Analyzing actual failure data against maintenance schedules to optimize intervals.
- Lifecycle Analysis: Tracking equipment throughout its lifecycle to inform replacement or overhaul decisions.
- Maintenance Effectiveness Evaluation: Assessing whether scheduled maintenance is preventing failures as intended.
- Compliance Monitoring: Ensuring adherence to regulatory requirements and internal maintenance standards.
6. Implementation Best Practices for CMMS in Time-Based Maintenance
To maximize the benefits of a CMMS for time-based maintenance:
- Start with Clean Data: Ensure equipment information, maintenance schedules, and procedures are accurate before implementation.
- Standardize Coding Systems: Develop consistent naming conventions and classification systems for equipment, tasks, and failure modes.
- Integrate with Other Systems: Connect the CMMS with enterprise systems such as ERP, inventory management, and condition monitoring.
- Implement Mobile Access: Provide maintenance technicians with mobile access to the CMMS for real-time work order management and data entry.
- Train Users Thoroughly: Ensure all users understand how to use the CMMS properly for their respective roles.
- Establish Clear Workflows: Define processes for work order management, from creation to closure, with appropriate approvals and quality checks.
- Regularly Audit Data Quality: Monitor and maintain data accuracy in the CMMS to ensure reliable analysis and decision-making.
By leveraging a CMMS to manage time-based maintenance, organizations can significantly improve maintenance efficiency, reduce unplanned downtime, extend equipment life, and optimize maintenance resources. The systematic approach enabled by a CMMS transforms time-based maintenance from a simple calendar-based activity into a sophisticated, data-driven strategy for asset management.
Get a Free WorkTrek Demo
Let's show you how WorkTrek can help you optimize your maintenance operation.
Try for free