Get a Free WorkTrek Demo
Let's show you how WorkTrek can help you optimize your maintenance operation.
Try for freeDFMEA stands for Design Failure Mode and Effects Analysis. Engineers and product developers use it to find and fix potential design problems before they become real issues.
DFMEA is a systematic approach to identify, evaluate, and prevent possible failures in product designs. This process helps companies make safer, more reliable products. It examines each part of a design and asks “What could go wrong here?” and “How bad would it be if it did?”
Illustration: WorkTrek / Quote: Coast
DFMEA is part of the larger FMEA family of risk management techniques. While FMEA can be used for many things, DFMEA focuses on product design. It’s often used in automotive, aerospace, and electronics industries, where product failures could have serious consequences.
Overview of DFMEA
DFMEA stands for Design Failure Mode and Effects Analysis. It’s a key tool in product development and quality control.
DFMEA is a type of Failure Modes and Effects Analysis (FMEA) that focuses on identifying potential failures in product design before they occur.
The main goal of DFMEA is to improve product safety and reliability. It does this by finding weak points in the design early on.
DFMEA follows a step-by-step process:
- Define the scope
- Identify potential failure modes
- Assess the effects of failures
- Rate the severity of the issues
- Determine the likelihood of failures
- Evaluate detection methods
Companies use DFMEA to manage risk in their product designs. It helps them spot problems that could lead to safety issues or product recalls.
DFMEA can be done at different levels. It can look at a whole system or focus on individual components.
Source: WorkTrek
The process involves teamwork. Engineers, designers, and quality experts often work together on DFMEA.
DFMEA can help companies save money and protect their reputation. It also helps prevent costly mistakes and ensures better product quality.
Objectives and Benefits of DFMEA
DFMEA aims to identify potential failure modes in a product’s design before it reaches production. This proactive approach helps catch issues early.
A key objective is to improve product quality. By spotting problems in advance, companies can make design changes to prevent failures.
DFMEA also focuses on customer satisfaction. It helps create more reliable products that meet user needs and expectations.
Risk mitigation is another important goal. The process evaluates the severity, occurrence, and detection of potential failures, allowing teams to prioritize the most critical risks.
Some benefits of DFMEA include:
• Reduced warranty costs
• Fewer design changes late in development
• Improved safety and reliability
• Better compliance with regulations
DFMEA uses a Risk Priority Number (RPN) to rank failure modes. This helps teams decide where to focus their efforts for maximum impact.
Source: WorkTrek
Effective risk management is a significant advantage of DFMEA. It provides a structured way to address potential issues before they become real problems.
Prevention is at the heart of DFMEA. By considering possible failures, teams can design safeguards and controls to prevent issues from occurring.
Components of DFMEA
How does DFMEA work? DFMEA consists of several key elements that identify and assess potential design failures. These components help teams analyze risks and prioritize improvement efforts.
Severity, Occurrence, and Detection
Source: WorkTrek
Severity measures how serious the effects of a failure could be. It’s usually rated on a scale of 1 to 10, with ten being the most severe.
Occurrence measures how often a failure might occur. Like severity, the scale is set from 1 to 10.
Detection rates how easy it is to spot a failure before it reaches the customer. This is also measured on a 1-10 scale.
These three factors help teams understand the overall risk of each potential failure mode. They form the basis for calculating the Risk Priority Number.
Risk Priority Number (RPN)
The Risk Priority Number (RPN) is a key metric in DFMEA. It’s calculated by multiplying Severity, Occurrence, and Detection scores.
RPN = Severity × Occurrence × Detection
A higher RPN suggests a more critical issue that needs attention. For example:
- Low RPN (1-100): Lower priority
- Medium RPN (101-500): Moderate priority
- High RPN (501-1000): High priority
Teams use the RPN to prioritize which issues to address first. This helps focus resources on the most critical problems.
Potential Failure Modes
Potential failure modes are how a design could fail to meet its intended function. These might include:
- Component breakage
- Software glitches
- Electrical short circuits
- Material degradation
Teams brainstorm and list all possible ways the design could fail. This step requires creativity and a deep understanding of the product.
It’s important to consider both obvious and less obvious failure modes. Sometimes, seemingly minor issues can lead to significant problems later on.
Potential Effects of Failure
This component examines what could happen if a failure occurs. The effects can range from minor inconveniences to serious safety hazards.
Examples of potential effects include:
- Product malfunction
- Customer dissatisfaction
- Safety risks
- Regulatory non-compliance
Source: WorkTrek
Teams rate the severity of each effect. This helps prioritize which failures need the most attention.
Understanding the potential consequences helps teams make informed decisions about design improvements.
Potential Causes of Failure
Identifying potential failure modes is crucial for prevention. Common causes might include:
- Poor material selection
- Manufacturing defects
- Environmental factors
- Design flaws
Teams analyze each failure mode to determine its root causes. This often involves asking “why” multiple times to investigate the issue further.
Understanding causes helps teams develop effective preventive actions. It also aids in risk reduction and improving detection methods for similar issues in the future.
By addressing root causes, teams can significantly reduce the likelihood of failures occurring.
Executing the DFMEA Process
The DFMEA process involves several key steps to identify potential design failures. A systematic approach and cross-functional collaboration are essential for effective risk assessment and mitigation.
Cross-Functional Team Formation
A diverse team is crucial for a successful DFMEA. It typically includes engineers, quality specialists, and representatives from production and service departments.
The team brings together varied expertise and perspectives, which helps identify a wide range of potential issues.
Regular meetings and clear communication channels are established. These ensure that all team members can contribute effectively throughout the process.
Identification of Potential Risks
The team reviews the design thoroughly. They consider all components, functions, and interactions within the system to help reduce system failure.
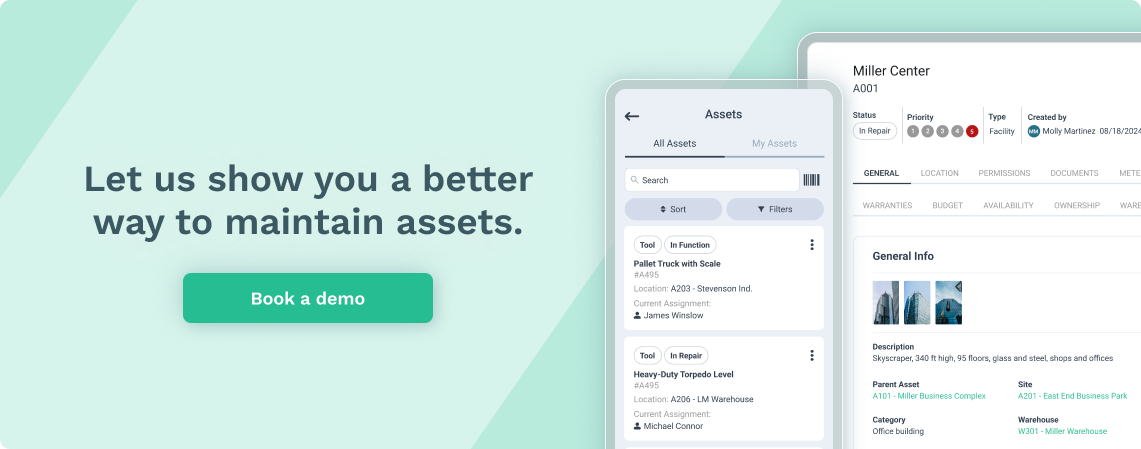
Source: WorkTrek
Brainstorming sessions are conducted to identify possible failure modes. These sessions encourage open discussion and creative thinking.
Each potential failure is documented, along with its possible causes and effects. This creates a comprehensive list of risks to be evaluated.
Historical data and lessons from previous projects are also considered. This helps identify risks that may not be immediately apparent.
Evaluation and Prioritization of Risks
Each identified risk is assessed based on three factors:
- severity
- Occurrence
- Detection.These factors are typically rated on a scale of 1 to 10.
The Risk Priority Number (RPN) is calculated by multiplying these three factors. This provides a quantitative measure for prioritizing risks.
Risks with higher RPNs are given priority for mitigation. However, the team also considers the severity of consequences independently.
A matrix or table is often used to visualize the risk assessment results. This helps quickly identify the most critical areas for improvement.
Risk Control Measures
For each prioritized risk, the team develops control measures. These include both prevention and detection controls.
Prevention controls aim to reduce the likelihood of failure occurrence. They may involve design changes, material improvements, or process modifications.
Detection controls focus on identifying failures before they reach the customer. These may include inspection methods, testing procedures, or monitoring systems.
The team considers the feasibility and effectiveness of each proposed measure. Cost-benefit analysis is often performed to ensure efficient resource allocation.
Implementation and Monitoring of Corrective Actions
An action plan for implementing the chosen control measures is developed. This plan includes responsibilities, timelines, and resource requirements.
The team regularly tracks implementation progress and uses CMMS tools like WorkTrek to ensure timely task completion.
Illustration: WorkTrek / Data: Pinterest
After implementation, the effectiveness of the control measures is evaluated. This may involve testing, data collection, and analysis.
If necessary, the team adjusts the control measures based on the results. This iterative process ensures continuous improvement in design reliability.
The DFMEA document has been updated to reflect the implemented changes. This document serves as a valuable reference for future projects and continuous improvement efforts.
DFMEA in Different Industries
Design Failure Mode and Effects Analysis (DFMEA) is used across various industries to improve product safety and reliability. Its application varies based on industry-specific needs and regulations.
In the automotive industry, DFMEA is crucial for producing safer vehicles. Car manufacturers use it to analyze brake systems, engines, and other critical components, helping prevent potential failures that could lead to accidents.
The aerospace sector relies on DFMEA to ensure aircraft safety. Engineers analyze every part, from wings to landing gear, to identify possible failures. This thorough approach helps maintain high safety standards in aviation.
Healthcare uses DFMEA to design medical devices and equipment. It helps identify risks in devices like pacemakers or X-ray machines. This process is vital for patient safety and meeting strict medical regulations.
In the defense industry, DFMEA is used to develop reliable military equipment. It helps analyze potential failures in weapons systems, vehicles, and communication devices.
Illustration: WorkTrek / Quote: Agilian
This ensures equipment performs well in challenging conditions.
Industrial applications of DFMEA include:
- Manufacturing machinery
- Chemical processing plants
- Power generation systems
By using DFMEA, these industries can create safer, more efficient products and processes.
DFMEA Throughout the Product Lifecycle
Design Failure Mode and Effects Analysis (DFMEA) plays a key role in every stage of a product’s life. It helps catch issues early, boosts quality, and cuts costs. Let’s look at how DFMEA works in different phases.
Product Design and Development
In this phase, DFMEA is crucial for identifying potential failure modes before they become real problems. Engineers use it to spot weak points in the design.
They look at each part and ask:
- How might this fail?
- What would happen if it did?
- How likely is it to fail?
This helps them make the product safer and more reliable. They can fix issues on paper, which is much cheaper than fixing them later.
DFMEA also guides testing plans. It shows which parts need extra checks, saving time and money by focusing efforts where they matter most.
Manufacturing and Assembly Processes
As the product moves to production, DFMEA shifts focus. Now, it examines how the manufacturing process might cause failures.
Teams check:
- If parts fit together right
- If assembly steps might damage components
- If variations in the process could lead to defects
This helps improve productivity and product quality. It can lead to changes in how things are made or put together.
DFMEA also helps pick the right equipment. It shows where precision matters most, guiding choices about machines and tools.
Post-Market Surveillance
DFMEA doesn’t stop when the product ships. It’s a key tool for tracking real-world performance.
Teams use it to:
- Analyze customer complaints
- Spot trends in product returns
- Guide updates and fixes
This ongoing review helps improve each product version and feeds back into the design process for new products.
DFMEA, in this phase, can catch issues that slipped through earlier checks. It’s a vital part of continual improvement and maintaining product safety.
Integrating DFMEA with Other Quality Tools
Illustration: WorkTrek / Data: EZO CMMS
DFMEA works best when combined with other quality management tools. This approach creates a more robust quality assurance system.
One key tool to pair with DFMEA is design review. Design reviews allow teams to evaluate DFMEA findings and make improvements before production begins.
Design verification is another important integration process. It helps confirm that DFMEA recommendations have been properly implemented.
DFMEA results can inform quality control measures. Teams can focus QC efforts on areas identified as high-risk during the DFMEA process.
Corrective and preventive actions often stem from DFMEA findings. These actions address potential failures before they occur in real-world use.
When guided by DFMEA, reliability testing becomes more targeted. Engineers can design tests to evaluate specific failure modes identified in the analysis.
Regularly updating the DFMEA enhances continuous improvement. As new information emerges, teams can refine their analysis and mitigation strategies.
By combining DFMEA with these tools, organizations create a comprehensive approach to quality management. This integration helps ensure safer, more reliable products.
Common Challenges and Best Practices
Design Failure Mode and Effects Analysis (DFMEA) involves several key challenges. Teams must avoid common mistakes, implement effective prevention and detection strategies, and foster collaboration to maximize results.
Avoiding Common Mistakes
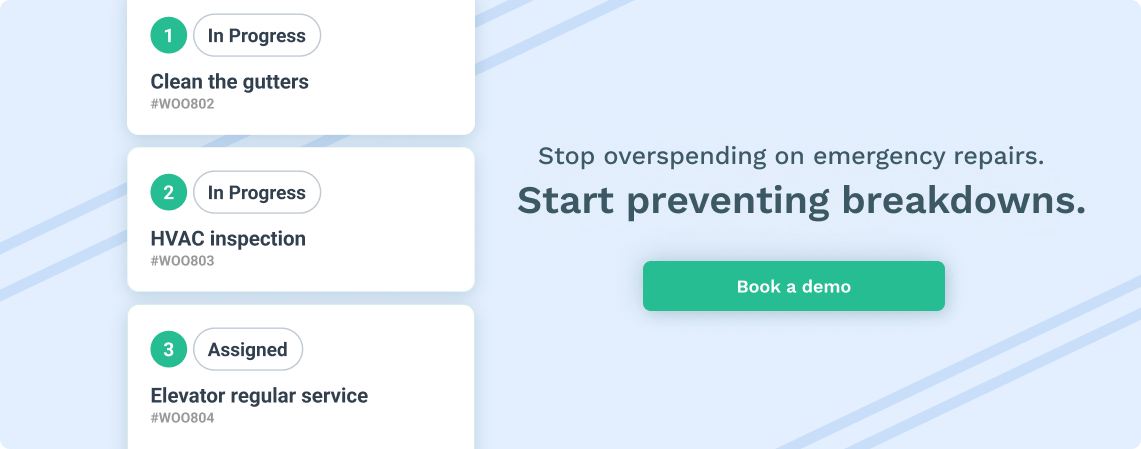
Several pitfalls can hinder DFMEA implementation. One frequent error is focusing too narrowly on known issues while overlooking potential new failure modes. This can lead to incomplete risk assessments.
Another mistake is assigning unrealistic severity ratings. Teams may underestimate or exaggerate the impact of certain failures, skewing the analysis.
Inadequate root cause analysis is also problematic. Failure to dig deep enough into underlying causes can result in ineffective prevention measures.
Teams should use clear, specific language when describing failure modes and effects. Vague descriptions make it difficult to develop targeted solutions.
Incorporating Prevention and Detection Strategies
Effective DFMEA processes emphasize both prevention and detection controls. Prevention controls aim to prevent failures from occurring. These may include design changes, material upgrades, or improved manufacturing processes.
Detection controls help identify failures quickly if they do occur. Examples include sensors, quality checks, and testing procedures.
Teams should prioritize prevention over detection when possible. It’s better to avoid failures than to catch them after the fact.
A balanced approach is key. Robust prevention and detection strategies work together to minimize risks and improve product reliability.
Maximizing Team Collaboration
Illustration: WorkTrek / Data: UC Today
Cross-functional teams are essential for effective DFMEA. Including members from design, manufacturing, quality, and service departments provides diverse perspectives on potential failures.
Clear communication is crucial. Team members must share information openly and listen to different viewpoints.
Regular meetings help keep everyone aligned. These sessions allow for updates on progress and discussion of new insights.
Assigning clear roles and responsibilities ensures all aspects of the analysis are covered. This prevents important tasks from falling through the cracks.
Decision-making should be collaborative. Encouraging input from all team members leads to more comprehensive risk assessments and mitigation strategies.
DFMEA Documentation and Reporting
Proper documentation and reporting are crucial for an effective DFMEA process. Clear records help teams track issues, prioritize actions, and make informed decisions to improve product designs.
DFMEA Template Usage
A well-structured DFMEA template is essential for consistent documentation. The template typically includes columns for:
- Item/Function
- Potential Failure Mode
- Potential Effects
- Severity Score
- Potential Causes
- Occurrence Rating
- Current Controls
- Detection Score
- Risk Priority Number (RPN)
Teams fill out each column systematically, ensuring all potential failure modes are captured and evaluated. A standardized template helps maintain consistency across different projects and facilitates easier comparison and analysis.
Generating Action Items
Action items are concrete steps to address identified risks. They emerge from the DFMEA analysis and focus on high-risk areas.
To generate effective action items:
- Prioritize based on RPN scores
- Focus on failure modes with high severity or occurrence ratings
- Consider detection improvements for hard-to-detect issues
- Assign responsible team members and deadlines
Regular reviews of action items ensure progress and help update the DFMEA as designs evolve.
Making High-Priority Recommendations
High-priority recommendations target the most critical risks identified in the DFMEA. These recommendations should:
- Address failure modes with the highest RPN scores
- Focus on reducing the severity or occurrence of potential failures
- Suggest improved detection methods for critical issues
- Consider the cost-effectiveness and feasibility of implementation
Teams should present these recommendations clearly, backed by data from the DFMEA analysis. Prioritizing recommendations helps decision-makers allocate resources effectively and tackle the most pressing design concerns first.
Advanced DFMEA Topics
Software tools, systematic risk assessment, and regulatory compliance can enhance design failure mode and effects analysis (DFMEA), which helps improve product design and reliability.
Leveraging Software Tools
Software tools streamline the DFMEA process and boost efficiency. These programs offer templates, databases, and automated calculations. They help teams track changes, collaborate remotely, and generate reports quickly.
Many DFMEA software options integrate with other design tools. This integration allows for real-time updates as designs change and helps maintain consistency across different analyses.
Illustration: WorkTrek / Data: SelectHub
Some advanced features include:
- Customizable risk matrices
- Automatic risk priority number (RPN) calculations
- Failure mode libraries
- Visual mapping of system functions
These tools often provide data analytics capabilities. Teams can spot trends and focus on high-risk areas more easily.
Adopting a Systematic Approach to Risk Assessment
A systematic approach to risk assessment in DFMEA ensures thorough analysis. It starts with breaking down the product into its components and system functions.
Teams then identify potential failure modes for each function. They assess the severity, occurrence, and detection of each failure mode. This assessment leads to calculated risk priority numbers (RPNs).
Key steps in systematic risk assessment include:
- Function analysis
- Failure mode identification
- Effect analysis
- Cause analysis
- Control evaluation
Teams prioritize actions based on RPNs and other factors. They develop and implement risk mitigation strategies, and regular reviews ensure the effectiveness of these actions.
Standards and Regulatory Compliance
DFMEA plays a crucial role in meeting industry standards and regulatory compliance. Many sectors have specific DFMEA requirements or guidelines.
For example, the automotive industry uses the AIAG-VDA FMEA standard, and medical device manufacturers must comply with ISO 14971 for risk management.
Compliance often involves:
- Documenting the DFMEA process
- Using standardized severity and occurrence ratings
- Implementing traceability measures
- Conducting regular reviews and updates
Teams should stay updated on relevant standards and adapt their DFMEA processes to meet changing regulations. This approach ensures products meet safety and quality requirements.