Get a Free WorkTrek Demo
Let's show you how WorkTrek can help you optimize your maintenance operation.
Try for freeComputerized maintenance management systems (CMMS).
If you want to know some interesting facts about it, you’ve come to the right place.
Today, we’ll walk you through key statistics and insights about computerized maintenance management systems (CMMS).
You’ll see how the market is evolving, why more companies are adopting this technology, and how it can benefit your maintenance operations.
The Global CMMS Market Size Is Projected to Reach US $4,2 Billion by 2033
Future Market Insights reveals that the CMMS market is expected to grow significantly over the next ten years.
More precisely, it is projected to grow from US $1,636.2 million in 2023 to US $4,215.1 million by 2033, with a growth rate of 9.1% per year.
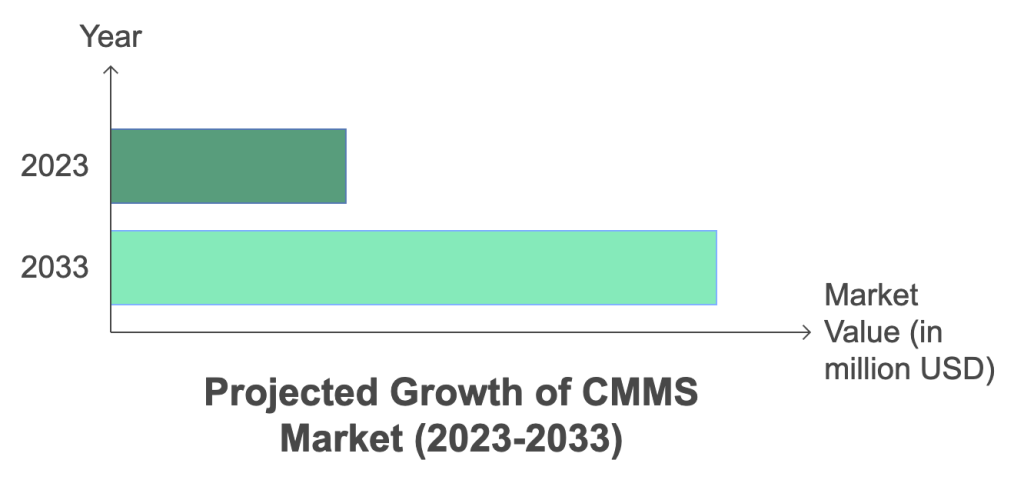
To put this into perspective, from 2018 to 2022, the growth rate was just 7.0%.
So, what’s driving this rapid demand?
It’s simple: industries need their machines to run smoothly and last longer, and they need better visibility to the work being performed, which is what CMMS offers.
With downtime costing millions per hour, businesses are turning to CMMS to track work orders, monitor performance, and make smarter decisions faster.
Another reason for this growth is the general shift toward automation and digital solutions.
Gone are the days when maintenance logs were kept with pen and paper.
With CMMS, everything is organized digitally, giving businesses more control over their operations.
Plus, as digital tools are used more widely, CMMS is becoming more affordable and user-friendly, opening the doors for small and medium businesses to join in.
Finally, a modern CMMS can integrate with IoT sensors to analyze real-time data and automatically schedule maintenance based on predictive insights, further reducing downtime and improving asset management.
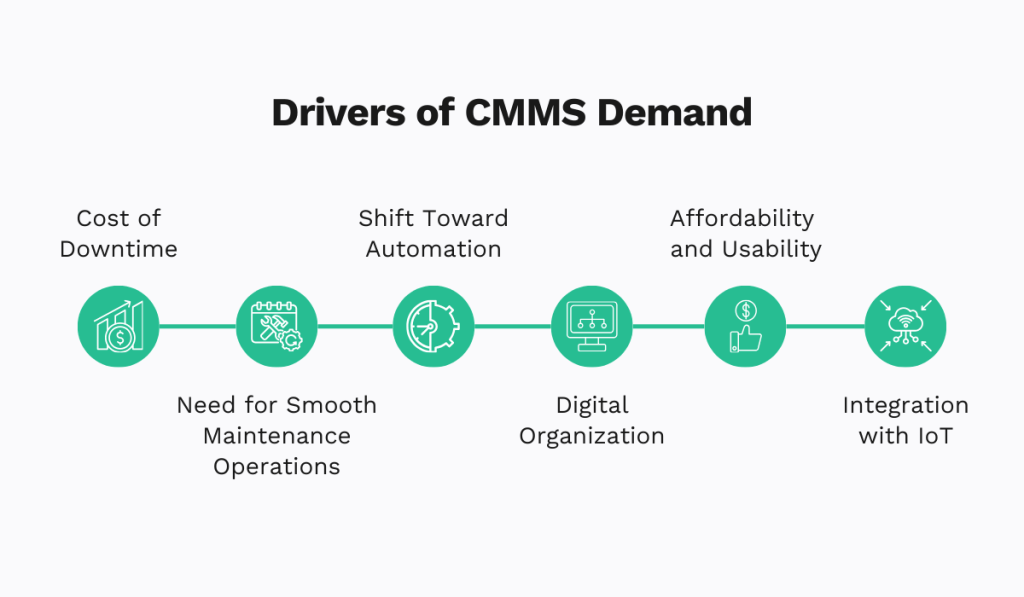
Considering all these factors, it’s easy to see why more companies are jumping on board and investing in CMMS.
The CMMS Market Contributes 20% to the Global Asset Management Market
CMMS now makes up one-fifth of the global asset management market, and that number is telling.
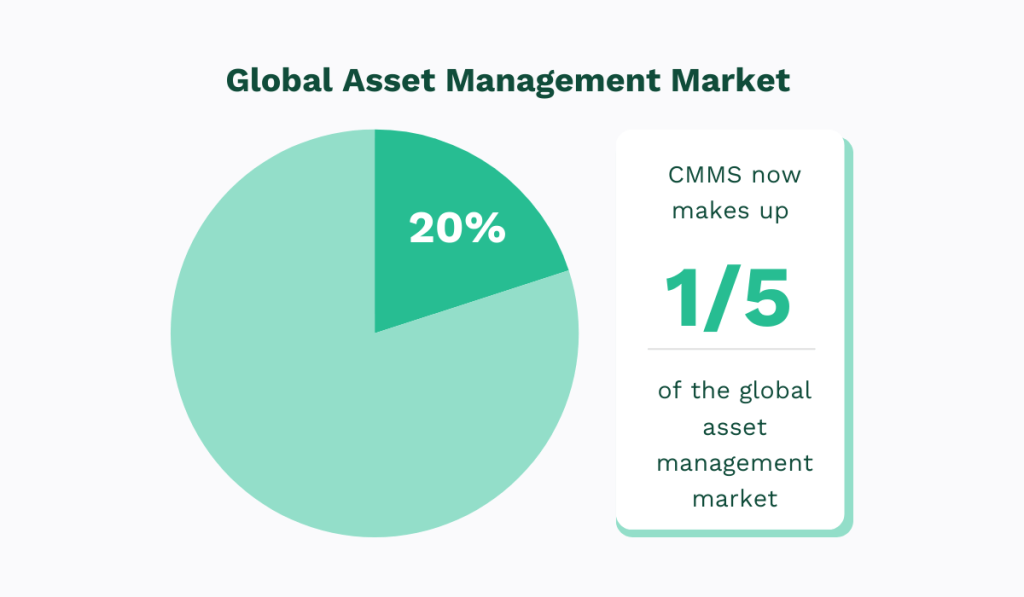
This shows how vital these systems are for managing and maintaining physical assets.
If you’re in an industry where your equipment’s uptime is crucial—manufacturing, construction, or utilities—CMMS is a game-changer.
It ensures that preventative maintenance happens on time, which means fewer breakdowns and more efficient use of your assets.
In the long run, this extends the lifespan of your machinery and saves you money.
This 20% share shows a trend toward software-based solutions for managing extensive equipment inventories.
Companies realize that spreadsheets and manual tracking just don’t cut it anymore.
With CMMS, everything is in one place, making it easier to manage work orders, track asset histories, and plan for future maintenance needs.
This trend highlights the growing recognition of CMMS as a critical tool for companies that want to stay competitive and efficient.
72% of Companies Use CMMS for Organizing Maintenance
This statistic comes from the State of Maintenance Report 2024 by Upkeep, which surveyed maintenance supervisors and managers from mostly small to mid-sized companies.
On why they use CMMS, 72% of maintenance professionals answered that they primarily use it to organize their maintenance activities and data in one place.
This makes perfect sense.
Juggling work orders, service history, parts inventory, and asset conditions using different systems or, worse, manually, is chaotic and inefficient.
With CMMS, it’s the opposite.
Take our very own CMMS, WorkTrek, as an example.
It centralizes everything: maintenance tasks, documents, service history, spare parts inventory, asset conditions, and expenses.
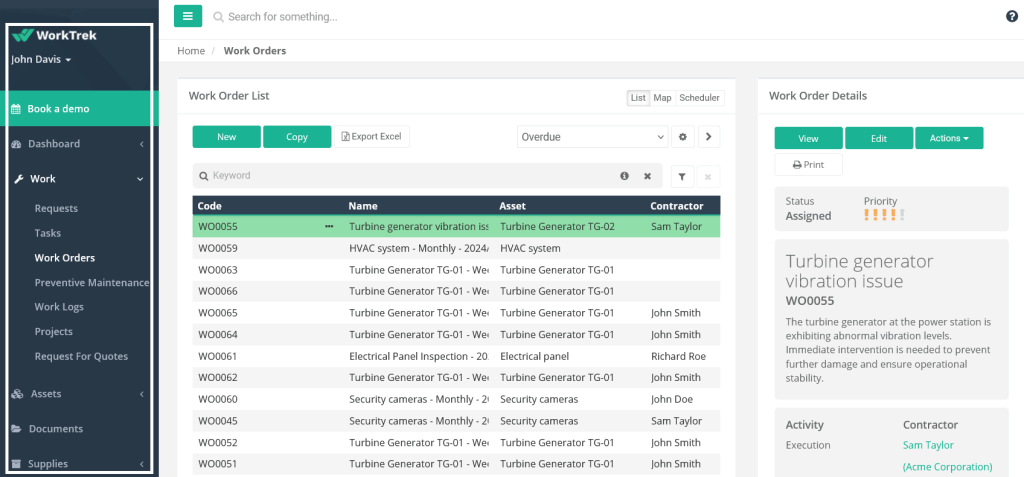
From one central dashboard, you can easily schedule and assign tasks, track progress, and generate detailed reports.
When everything is in one place, it’s easier to manage, which saves you time and minimizes errors.
It really can’t get more organized than this!
28% of Maintenance Professionals Say Reduced Unplanned Downtime Is the Biggest Benefit of CMMS
Another key finding from the State of Maintenance Report is that 28% of maintenance professionals believe reducing unplanned downtime is the biggest benefit of CMMS.
It’s easy to see why when we know that unplanned downtime is a huge pain point for many companies. Unfortunately, this pain point occurs way too often.
Namely, research shows that over two-thirds of industrial companies experience at least one unplanned outage a month.
However, with the help of a CMMS, that can be reduced.
Maintenance teams can easily stay on top of their maintenance strategy, schedule preventive maintenance more accurately, and even monitor assets in real time to predict failures before they cause costly breakdowns.
As you will soon learn, the latter is growing in popularity across industries.
48% of CMMS Users Have a Predictive Maintenance Regime
Even in 2022, 48% of CMMS users have already implemented a predictive maintenance regime.
This statistic comes from the CMMS Market Report and Insights by Comparesoft, which analyzed data from 119 CMMS buyers.
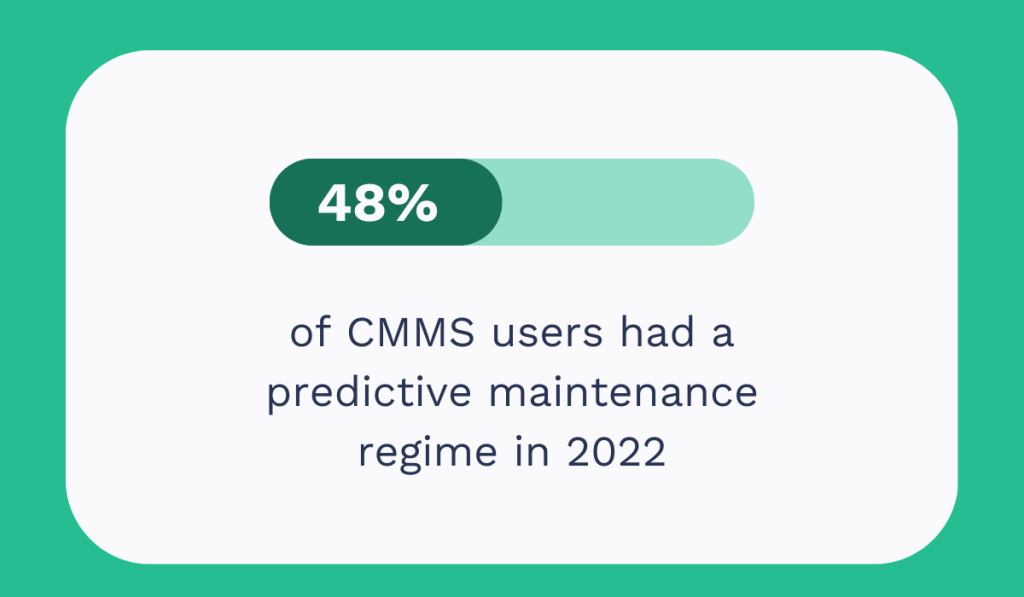
This shows that almost half of CMMS users are tapping into advanced capabilities to optimize their maintenance strategies further.
Predictive maintenance allows CMMS to analyze equipment data and identify patterns that indicate potential issues, letting maintenance teams fix problems before they cause downtime.
As more companies adopt Industry 4.0 and IoT technologies, CMMS solutions that connect with sensors to gather real-time data are becoming necessary.
With nearly half of users already using predictive maintenance by 2022, it’s clear that this trend is set to grow, making these capabilities a must-have for any future-focused CMMS.
21% of CMMS Users Are Interested Only in Core CMMS Functions
Not surprisingly, the same Comparesoft report revealed that only 21% of companies were interested in core CMMS functions like asset tracking, job logging, and work order management.
With so many companies already adopting predictive maintenance, it makes sense that most users expect more from their CMMS.
The majority (79%) are looking for additional features such as service management analytics, parts management, health and safety compliance, and integration with sensors for predictive maintenance.
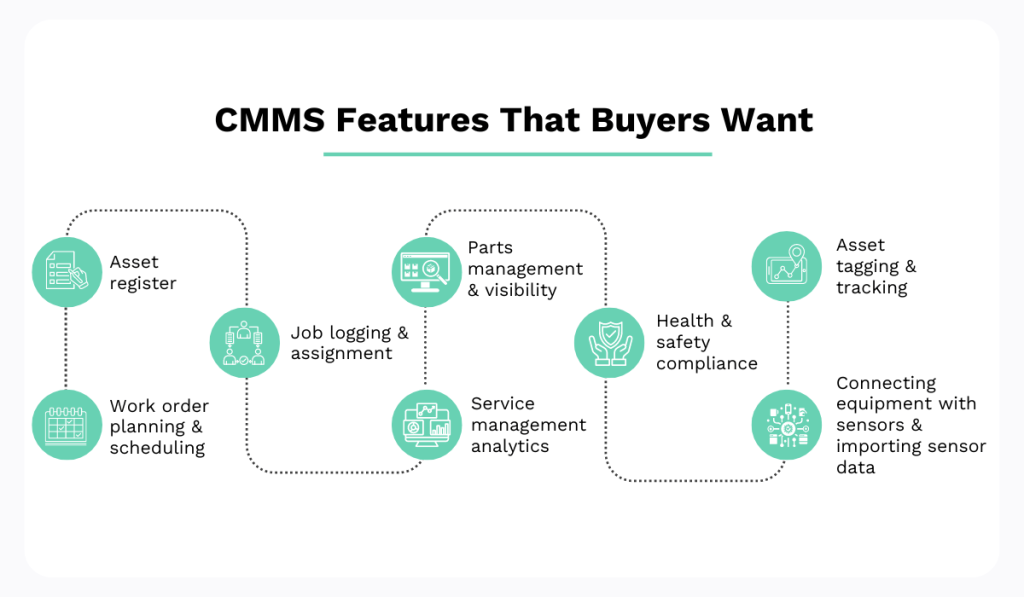
Why is this significant?
It highlights that the needs of modern maintenance teams are evolving and that CMMS providers must continuously innovate to stay competitive.
It’s no longer enough just to offer basic tracking and scheduling features.
As digital technologies and IoT become standard, maintenance teams expect their CMMS to integrate with equipment monitoring software, collect sensor data, and automate maintenance activities.
This reinforces the idea that predictive maintenance is becoming a “must-have”.
58% of Users Who Sought a CMMS in 2022 Used Spreadsheets
In 2022, more than half of potential CMMS buyers still relied on spreadsheets, while 28% weren’t using any maintenance management system, according to Comparesoft.
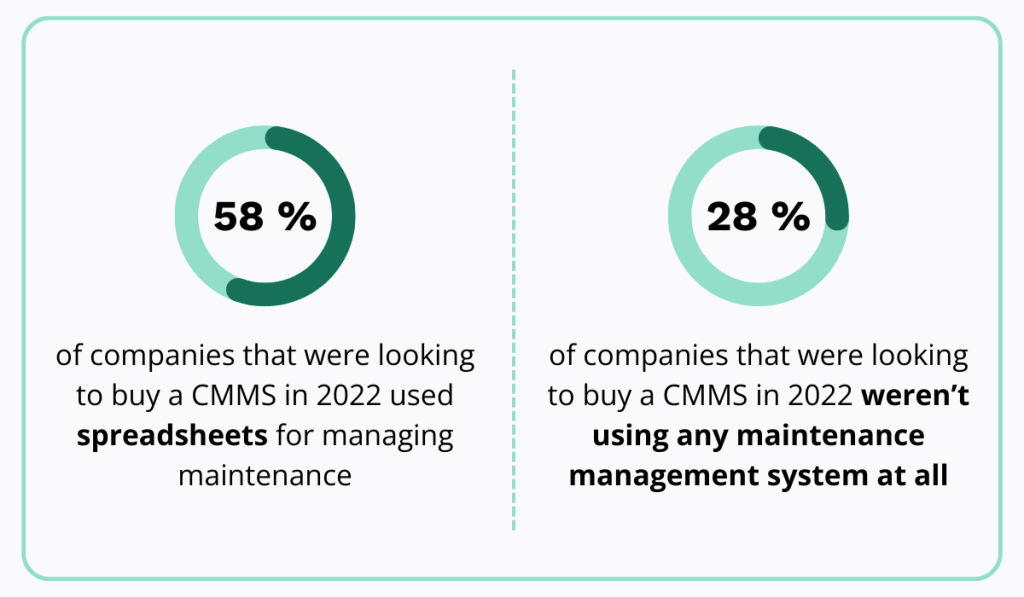
This data highlights a stark contrast between past practices and the future direction of maintenance management.
It is easier for companies to adopt CMMS if they are already managing their maintenance somehow, than not at all. Because they can quickly become aware of the drawbacks of their approach.
While spreadsheets were once the go-to tool, their limitations are becoming increasingly apparent.
They are time-consuming, error-prone, and need more automation and advanced tracking features that a CMMS offers.
With a CMMS, maintenance teams can automate tasks, track service history, and manage assets from a single platform—efficiencies that spreadsheets simply cannot match.
The growing demand for CMMS shows that more companies are moving away from outdated methods, investing in systems that handle everything from basic asset tracking to predictive maintenance.
And you’re about to learn the key reason why this shift matters.
74% of Maintenance Professionals Say Their CMMS Improves Productivity
Spreadsheets alone cannot significantly improve productivity, but CMMS can.
And this statistic proves it.
In 2020, Advanced Technology Services (ATS) partnered with Plant Engineering Magazine to survey the state and common trends in industrial maintenance across U.S. manufacturing plants.
Regarding software use, they found that CMMS improves productivity for 74% of maintenance professionals.
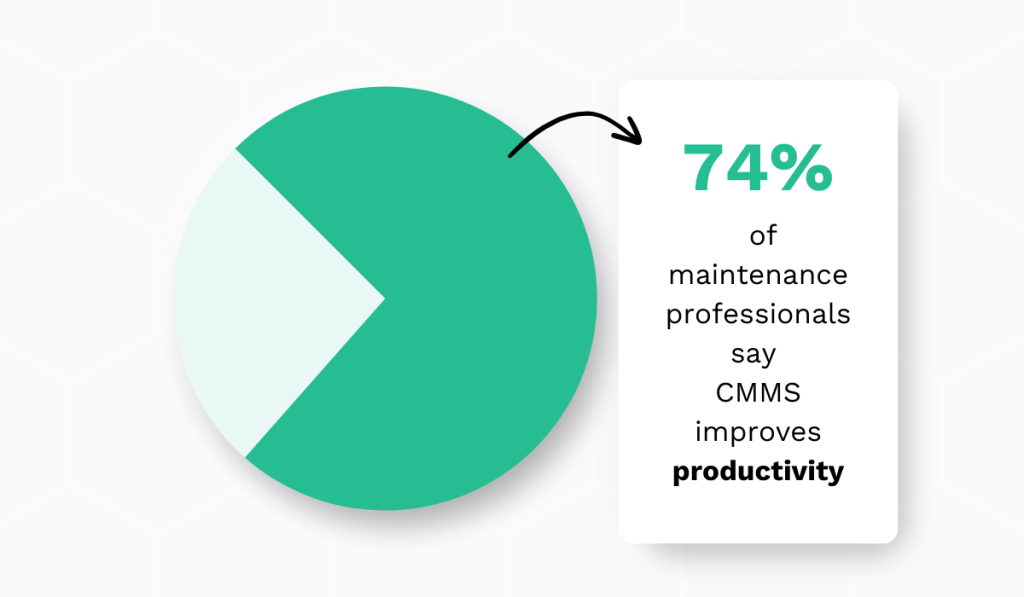
This statistic highlights how much a well-implemented CMMS can impact day-to-day operations.
Here are some ways CMMS can boost your productivity:
- Automate and standardize work order creation, assignment, and tracking.
- Schedule and manage preventive maintenance tasks based on equipment data.
- Track inventory levels, manage spare parts, and optimize purchasing.
- Use mobile apps to access and update work orders in the field.
- Implement predictive maintenance using data analytics and algorithms.
When you switch from manually managing tasks to an automated CMMS, the boost in efficiency is clear. That’s why so many maintenance professionals notice a significant productivity gain.
7% of Maintenance Managers Say That Poor CMMS Data Quality Is the Biggest Challenge They Face
But even with all its benefits, a CMMS isn’t flawless.
According to ABL’s 2023 Global Maintenance Manager Report, 7% of maintenance managers cited poor data quality as their biggest challenge in using CMMS.
While this number might seem small, it points to a serious problem.
A CMMS is only as good as the data entered into it.
If the data—like equipment details, maintenance history, or performance metrics—is incomplete or incorrect, it can lead to mistakes, delays, and inefficiencies.
For instance, wrong model numbers or missing manufacturer information can delay repairs or cause the wrong parts to be ordered, leading to increased downtime.
The report further reveals the root cause of this issue: inadequate change management processes, where updates about equipment changes or repairs aren’t properly recorded.
Luckily, there is a solution to this challenge.
Stuart Murray, Head of Technical at ABL Group Company, suggests that maintenance teams can solve this by collecting accurate data, using standardized processes, and implementing continuous improvement strategies:
Ultimately, it’s not the CMMS itself that causes problems—it’s how we use it. Ultimately, a CMMS can only be as effective as the information it holds.
Conclusion
These nine statistics tell a clear story—adopting a CMMS can take your operations to the next level.
As long as you use it properly, it will keep your maintenance organized, boost productivity, and reduce downtime.
With rising demand for predictive maintenance and improved efficiency, now is the time to embrace this technology.
You’ll need to if you want to stay competitive. As more companies adopt CMMS to streamline processes and reduce costs, sticking to outdated methods could leave you struggling to keep up.