Get a Free WorkTrek Demo
Let's show you how WorkTrek can help you optimize your maintenance operation.
Try for freeEquipment that you depend on for your business needs regular maintenance to thrive. By maintaining machines regularly, companies can reduce unexpected breakdowns, ensure smooth operations, and minimize downtime. Understanding the benefits of machine maintenance is important. This article will answer the following questions: Why is it important to maintain your machines and equipment regularly?
This proactive approach not only safeguards investments but also enhances the performance and efficiency of equipment.
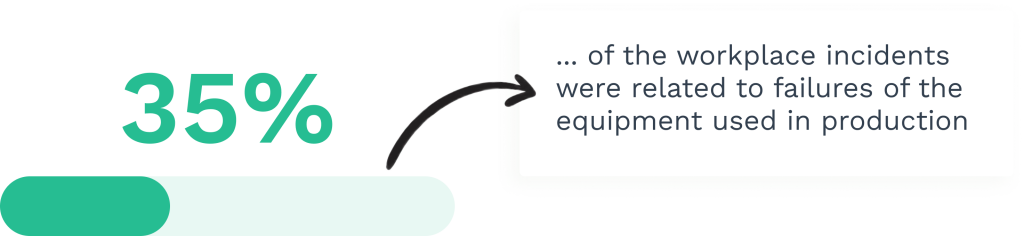
Illustration: WorkTrek / Data: CleanLink
Keeping machines in top condition helps extend their lifespan, providing better returns on investment.
Regular checks and servicing can also maximize product quality by preventing issues that may lead to defects or inconsistencies in production.
Ignoring regular maintenance work can lead to higher repair costs and significant downtime, impacting profitability.
Moreover, adhering to safety standards becomes easier when machines are well-maintained, thus reducing risks in the workplace.
Consistent maintenance ultimately supports a more sustainable and efficient operation.
Key Takeaways
- Regular maintenance reduces breakdowns and downtime.
- Proper upkeep extends machine lifespan and boosts quality.
- Maintenance ensures safety and cuts long-term costs.
The Fundamentals of Machine Maintenance
Machine maintenance ensures equipment functions efficiently. It involves different activities designed to keep machines in top condition.
Routine Inspections: Regular checks can catch small issues before they become big problems. Inspections look at wear and tear, oil levels, and mechanical performance.
Cleaning and Lubricating: Machines should be cleaned and lubricated to reduce friction. This prevents damage and keeps them running smoothly.
Parts Replacement: Old or worn-out parts must be replaced to avoid unexpected breakdowns. It’s important to use quality parts to maintain performance.
Proactive vs. Reactive Maintenance: Proactive maintenance plans in advance to prevent potential issues, while reactive maintenance deals with problems after they occur. Proactive methods, such as preventive maintenance, help avoid costly downtime and reduce emergency repairs.
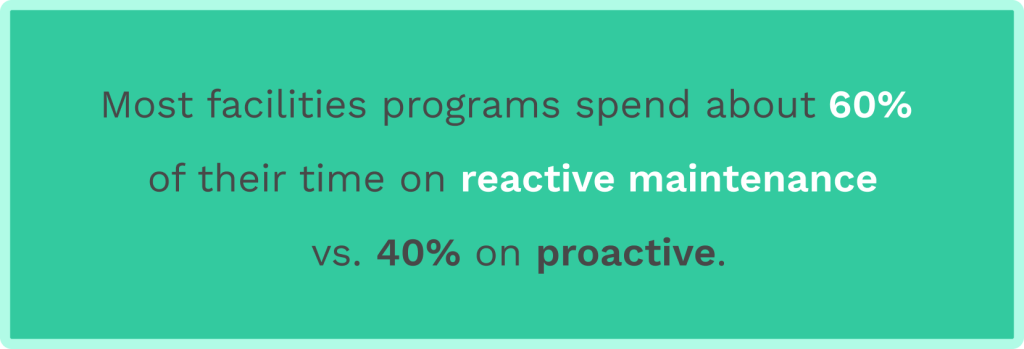
Illustration: WorkTrek / Data: ServiceChannel
Schedule and Frequency: Maintenance should be scheduled based on how often machines are used. A time-based approach ensures regular check-ups.
Common Tools: Use the right tools, from wrenches to CMMS software like WorkTrek for precise maintenance tasks.
This fundamental approach to machine maintenance helps increase lifespan, boost efficiency, and reduce the risk of unexpected failures. Regular attention to these fundamentals ensures machinery remains reliable and productive.
Extending Machine Lifespan
Regular maintenance is key to extending machinery’s lifespan. Focusing on preventing wear and tear and being consistent with regular inspection and lubrication can significantly improve machines’ durability and functionality.
Preventing Wear and Tear
Machines in constant use are prone to wear and tear, which can lead to breakdowns.
By investing time in daily checks, operators can spot issues before they escalate. Steps like tightening loose parts or replacing worn components early can help maintain the machine’s health.
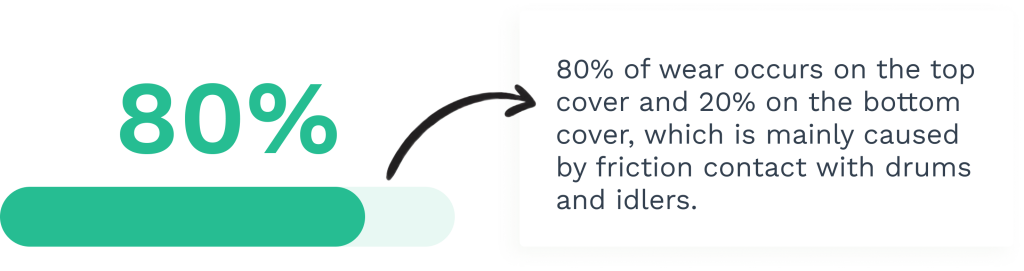
Illustration: WorkTrek / Data: Fenner Dunlop
Keeping machines clean is also crucial. Dust and debris can cause significant harm over time. Ensuring a clean environment can prevent damage and maintain efficiency. Regular cleaning schedules make a big difference in machine performance.
Operators should also follow operating guidelines. Overloading a machine or misusing it can shorten its lifespan. Training sessions to ensure operators understand the correct use of equipment are highly beneficial.
Regular Inspection and Lubrication
Inspections help identify minor issues before they become costly problems. It’s important to check for unusual noises, vibrations, or leaks during inspections.
A detailed inspection log can help track the machine’s condition over time.
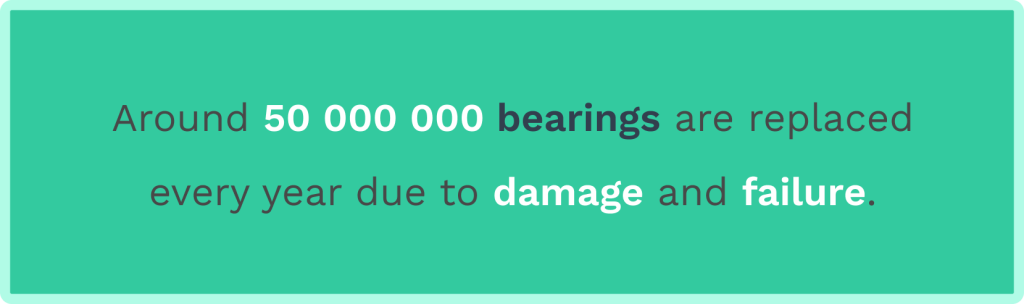
Illustration: WorkTrek / Data: CBM Connect
Lubrication reduces friction between moving parts, essential in preventing unnecessary wear. It is vital to use the right lubricant for each specific component.
Each machine part might need a different oil or grease, and using the wrong kind can cause damage. Use the manufacturer’s recommendation and only use high-quality lubricants.
Maintenance technicians should schedule regular lubrication sessions to ensure effective operation. It is advisable to follow the manufacturer’s guidelines for lubrication intervals.
A property lubricated machine will last longer and reduce energy usage, saving you money.
Enhancing Performance and Efficiency
Machines need regular maintenance to perform at their best. It focuses on precise calibration and alignment while optimizing operational parameters to boost efficiency.
Calibration and Alignment
Calibration ensures that machines operate with the highest accuracy possible. It involves adjusting machinery to meet specified standards defined by the manufacturers.
Regular calibration can prevent errors leading to product defects, thus saving time and costs.
For example, a well-calibrated machine minimizes deviations, ensuring precise measurements and outputs.
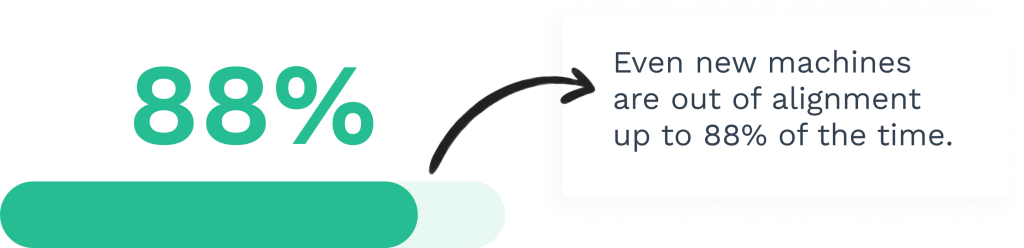
Illustration: WorkTrek / Data: API
Alignment, however, ensures all parts of the machine are correctly positioned. Similar to when your car is out of alignment, misalignment can cause vibrations and excessive wear. This can reduce the machine’s lifespan.
Properly calibrated and aligned machines are less likely to break down, ensuring continuous productivity.
Optimizing Operation Parameters
Optimizing operation parameters is fine-tuning the machine’s settings to match its tasks. This includes adjusting speed, temperature, and pressure for optimal performance.
By doing so, machines can operate more efficiently, using energy wisely and minimizing waste.
Data analysis can help identify ideal operating conditions. When machines are set up with precision, they produce higher-quality outputs with less material loss.
Operators play a key role in observing and adjusting these parameters.
Consistently reviewing and optimizing can significantly improve machine efficiency and reduce maintenance costs.
Keeping a close eye on these settings is essential for achieving peak performance and reducing machine downtime.
Ensuring Safety Standards
Safety is another important reason to maintain your machinery regularly.
It helps in pinpointing potential hazards before they become major issues and ensures compliance with safety regulations, thus maintaining a safe work environment.
Identifying Potential Hazards
Routine inspections and maintenance help in spotting potential dangers early on. This includes checking for worn-out parts, loose connections, and other issues that could lead to malfunction.
By addressing these problems promptly, the risk of accidents can be minimized.
Using maintenance checklists can be effective in identifying hazards.
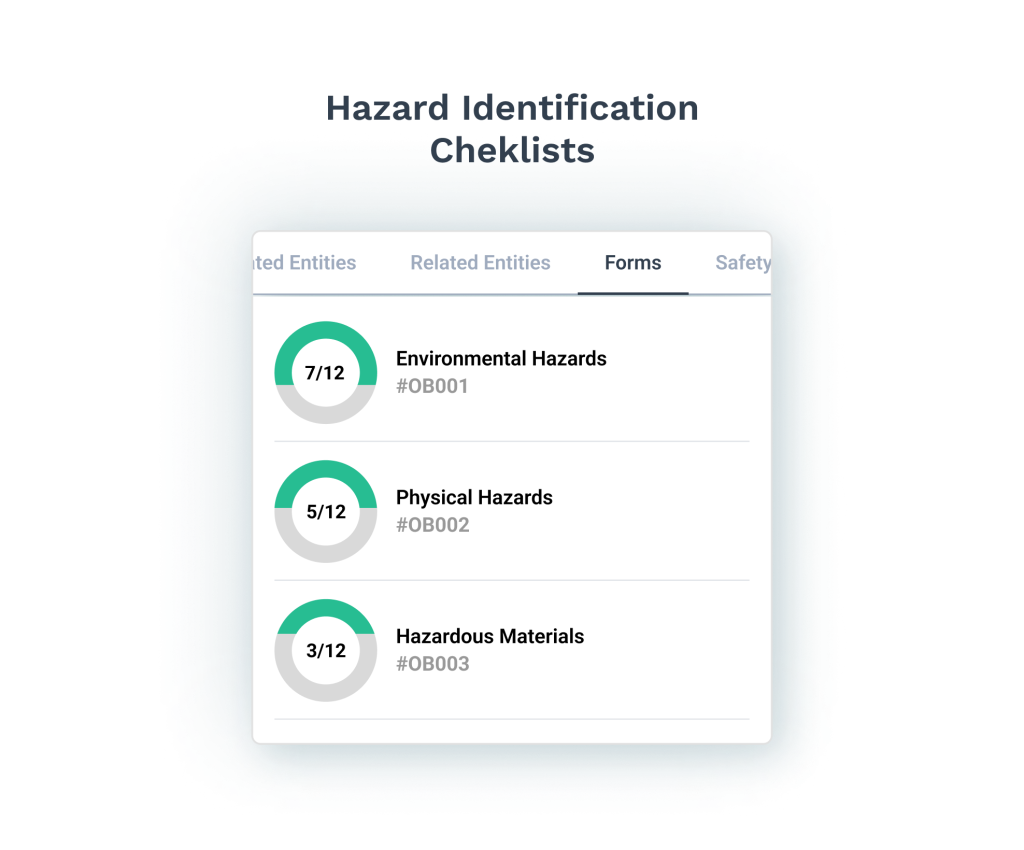
Source: WorkTrek
These maintenance checklists should cover all critical components of the equipment’s life, ensuring nothing is overlooked.
Make safety training part of your regular training regiment for maintenance personnel.
Compliance with Safety Regulations
Adhering to safety regulations is essential for any organization operating machinery.
Regulations like those from the Occupational Safety and Health Administration (OSHA) set the standards for workplace safety.
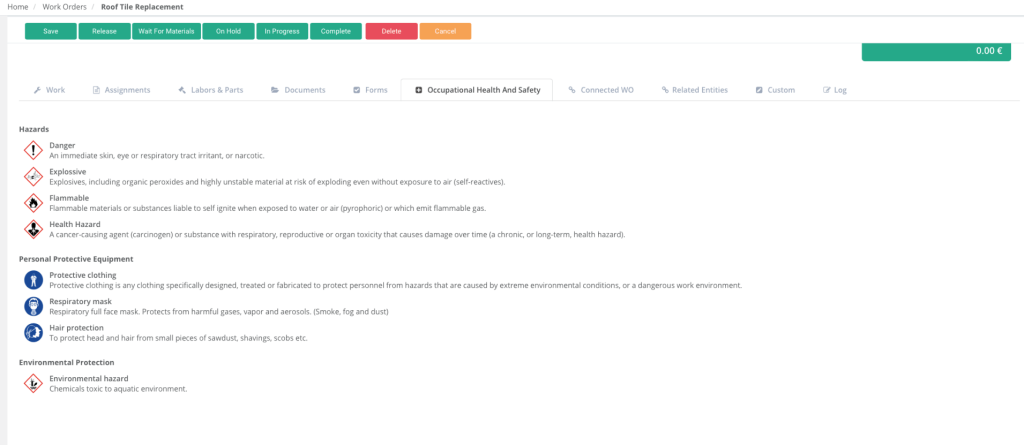
Source: WorkTrek
Regular maintenance helps comply with these standards.
Don’t forget to be diligent about record keeping. It serves as proof of compliance and can be helpful during safety audits.
If you are still keeping manual paper records, consider WorkTrek CMMS, which can help you digitize and automate your records.
Companies protect their employees and avoid potential legal issues and fines by ensuring that equipment meets all regulatory requirements.
Reducing Costs and Downtime
Regular machine maintenance can significantly decrease repair expenses and reduce downtime. Businesses can improve efficiency and save money by minimizing repair costs, scheduling maintenance properly, and selecting the right maintenance strategy.
Minimizing Repair Expenses
Businesses should focus on proactive maintenance strategies to minimize repair expenses. Regular inspections help identify potential issues before they escalate into costly repairs, and addressing problems early on can reduce unexpected breakdowns.
Training staff to handle basic equipment checks can also lower costs. Skilled employees can perform routine tasks and identify problems without needing external technicians. Implementing a computerized maintenance management system (CMMS) keeps track of past maintenance activities and predicts future needs, ensuring that machines are serviced promptly.
Source: WorkTrek
Investing in high-quality spare parts is another way to reduce expenses. Maintaining an organized inventory ensures that necessary parts are available when needed, preventing delays that might otherwise lead to increased costs. Keeping spare parts on hand helps maintain consistent production efficiency and minimizes costly downtimes.
Planning Maintenance Schedules
Properly planning maintenance schedules can reduce downtime. Scheduling maintenance during off-peak hours ensures minimal disruption to operations.
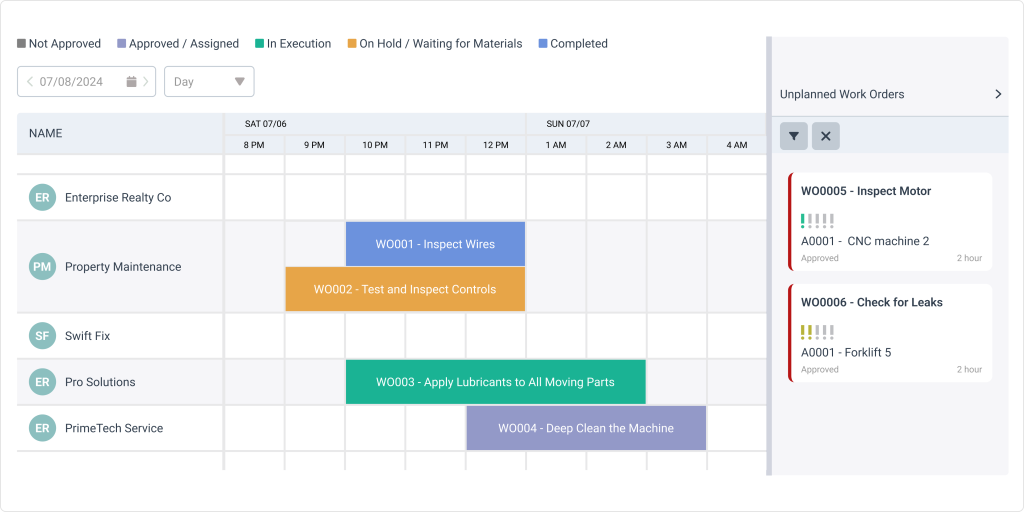
Source: WorkTrek
By aligning maintenance activities with production schedules, businesses can avoid unnecessary interruptions.
Predictive maintenance techniques allow businesses to forecast when equipment might need attention. This technique uses data analysis to predict potential failures, allowing for timely interventions.
Tracking metrics like the mean time between failures (MTBF) provides insight into machine reliability and helps plan maintenance accordingly.
Establishing clear maintenance procedures and documenting them guarantees consistency and adherence to schedules. Regularly reviewing and updating these plans helps adapt to any changes in operations or equipment needs, ensuring continued efficiency and minimized downtime.
Maximizing Product Quality
Proper machine maintenance can create high product quality. Consistent routines help achieve stable production rates and lower defect rates, which are crucial for maintaining a reliable output.
This helps businesses meet customer expectations and regulatory standards.
Consistency in Production
Regularly serviced machines maintain a steady performance, directly impacting production consistency.
Well-maintained equipment operates smoothly, reducing unexpected breakdowns. This minimizes downtime and keeps the production line running efficiently.
For example, ensuring machinery like mixers and pasteurizers are in top condition in the dairy industry can prevent texture or taste variations.
This consistency is vital for maintaining brand trust and customer satisfaction. Regular checks and timely repairs help achieve this.
Furthermore, maintaining a stable production environment helps prevent product size or weight variability. Consistent calibration and cleaning procedures ensure each product meets the set standards without deviation.
Reduction of Defect Rates
Regular maintenance significantly reduces defect rates by identifying issues before they lead to failures.
When components such as filters, belts, and seals are checked routinely, they are less likely to cause product defects due to wear and tear.
Defects can lead to serious compliance issues in sectors like pharmaceuticals. Ensuring machines like tablet presses and coating machines are in excellent condition minimizes the risk of faulty products reaching the market.
Routine maintenance helps spot problems, reducing waste from defective batches.
Investing in preventative measures reduces the need for costly recalls or batch rejections. This proactive approach to maintenance ensures high-quality standards are consistently met, benefiting both production processes and end-users.
Environmental Considerations
Regular maintenance of machinery plays can minimize environmental impact. It enhances energy efficiency and reduces waste, both of which are significant contributors to a more sustainable operation.
Energy Efficiency
Proper maintenance ensures that machinery runs at optimal efficiency, reducing the amount of energy consumed during operation.
For instance, well-maintained industrial gearboxes can significantly decrease their environmental impact using less energy.
When machines are energy efficient, less fuel or electricity is required, reducing emissions and a smaller carbon footprint.
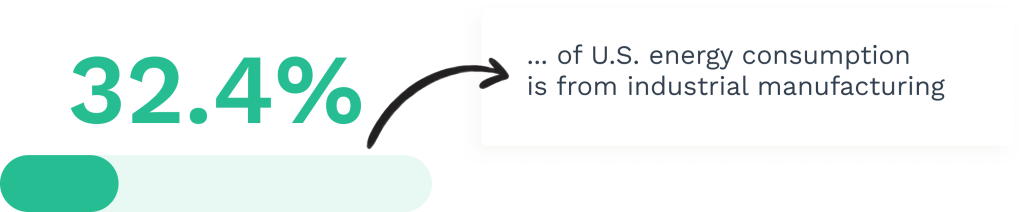
Illustration: WorkTrek / Data: Rockwell Automation
A neglected machine often works harder to perform the same tasks, consuming more energy. This increased energy use raises operating costs and increases greenhouse gas emissions.
By routinely checking and servicing machines, companies can identify and correct inefficiencies. This leads to smoother operations and enhances the lifespan of the equipment.
Waste Reduction
Maintenance also plays a key role in waste reduction. Regular inspections and adjustments can prevent part breakdowns and reduce the need for unnecessary replacements.
Fewer parts end up as waste, which, in turn, decreases the demand for raw materials.
Moreover, failing to maintain equipment can result in complete shutdowns or malfunctions, causing spoilage and increased waste production.
Companies can ensure continuous operation by keeping machines in good condition, minimizing production halts and material wastage.
Preventive maintenance strategies focus on repairing and adjusting components before they fail. This approach conserves resources and supports a more environmentally friendly operation.
Leveraging Technological Advancements
Modern technology offers a wealth of solutions for maintaining machinery more efficiently. Smart monitoring systems and predictive maintenance tools reduce downtime and improve performance.
Adoption of Smart Monitoring Systems
Smart monitoring systems provide real-time data about equipment conditions. These systems use sensors to track temperature, vibration, and other vital indicators.
Source: WorkTrek
When anomalies are detected, alerts can be sent immediately, allowing for quick action to prevent potential issues.
Implementing smart systems helps maintain consistent operation and extends the machinery’s lifespan.
Data collected over time can help identify patterns of wear and tear. This insight enables more informed decisions about equipment use and maintenance scheduling, ultimately enhancing overall efficiency and safety.
Integration with Predictive Maintenance
Predictive maintenance uses data analytics and machine learning to foresee when a machine might fail.
By analyzing historical and real-time data, predictive tools calculate the optimal time for maintenance before a breakdown occurs.
Integrating these technologies into maintenance schedules can result in significant cost savings. Addressing issues before they escalate reduces unexpected downtime and minimizes repair costs.
This approach also allows businesses to schedule maintenance during non-peak times, ensuring production remains uninterrupted and efficient.
These technological advancements enable a more proactive approach, reducing the stress and costs of unexpected machinery failures.
Workforce Skill Development
Focusing on training and fostering proactive habits enables efficient upkeep and minimizes downtime.
Training for Maintenance Procedures
Training empowers maintenance workers with the skills needed for tasks.
Programs that include classroom instruction and hands-on practice help workers understand various maintenance techniques.
For example, operator maintenance skills development often emphasizes learning through doing, which can help employees quickly identify and fix equipment issues.
Offering certifications and regular workshops ensures the team stays updated on the latest technology and practices.
Cross-training employees also provides backup for critical roles. By investing in comprehensive training, organizations can maintain high standards of equipment reliability and ensure safety.
Fostering a Culture of Proactivity
Creating a proactive workforce culture encourages employees to address issues before they escalate.
Encouraging regular maintenance checks and open communication helps identify potential problems early.
Employees should feel empowered to report irregularities, knowing their input contributes to overall efficiency.
Rewarding proactive behavior reinforces the importance of this approach. Teams that regularly perform preventative maintenance, such as routine equipment checks, help reduce unexpected breakdowns.
Adopting a culture where proactive measures are valued leads to a more reliable and efficient operation, benefiting the entire organization.
Concluding Thoughts on Regular Maintenance
As this article outlines, regular maintenance is vital for keeping machinery in top condition. By servicing machines frequently, businesses can avoid unexpected breakdowns, reduce repair costs, and minimize downtime.
A well-maintained machine has a longer lifespan. It operates more efficiently, leading to better productivity and reduced wastage. Regular checks include inspections, testing, and adjustments.
These steps ensure that any small issues are dealt with before they become major problems.
Benefits of Regular Maintenance:
- Extended lifespan
- Increased efficiency
- Reduced repair costs
- Minimized safety risks
It’s important to schedule these maintenance routines and stick to the schedule. Consistency is key in preventing significant problems.
When conducted properly, maintenance helps machines run at optimal levels, leading to savings in both time and resources.