Get a Free WorkTrek Demo
Let's show you how WorkTrek can help you optimize your maintenance operation.
Try for freeIf you are running a business, you need to keep your equipment running. There are two main approaches to maintenance: planned and unplanned.
Planned maintenance involves regular, scheduled upkeep.
Unplanned maintenance happens when something breaks unexpectedly. This article compares the differences between unplanned and planned maintenance.
Planned maintenance costs less and is more efficient than unplanned maintenance. It helps prevent breakdowns and extends the life of equipment. On the other hand, unplanned maintenance can lead to costly downtime and rushed repairs.
Companies that use planned maintenance often see better results. They can budget for repairs, schedule work during off-hours, and avoid emergencies.
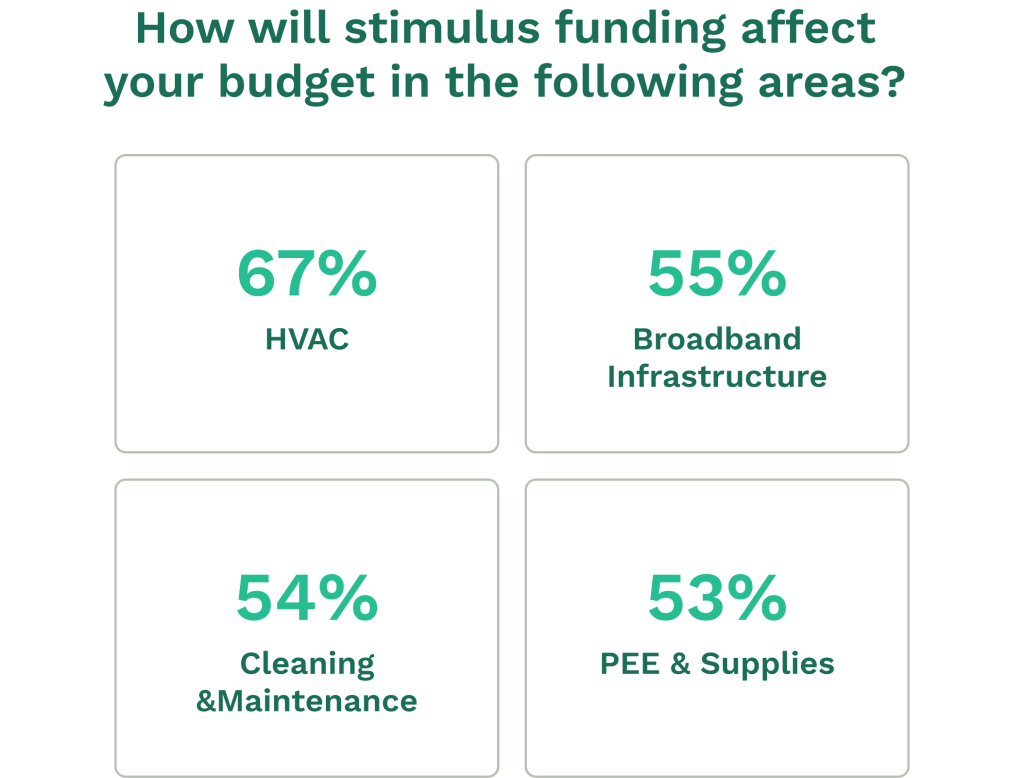
Unplanned maintenance can disrupt work and create stress for employees. Both types have their place, but a good balance is key.
Key Takeaways
- Regular upkeep prevents costly breakdowns and extends equipment life
- Planned maintenance allows for better budgeting and scheduling
- A mix of planned and unplanned maintenance strategies optimizes operations
Understanding Maintenance: Definitions and Differences
Maintenance strategies play a crucial role in keeping equipment and systems running smoothly. There are two main approaches: planned and unplanned maintenance.
Each has its characteristics and impacts on operations.
Defining Planned Maintenance
Planned maintenance is a proactive approach based on analyzing equipment’s historical performance. It involves scheduled tasks to prevent breakdowns and extend the life of assets.
This is usually when maintenance organizations are diligent about performing preventive maintenance.
Types of planned maintenance include:
- Preventive maintenance: Regular checks and repairs
- Predictive maintenance: Using data to forecast issues
- Scheduled maintenance: Set times for upkeep tasks
Benefits of planned maintenance:
- Reduced unexpected failures
- Improved equipment lifespan
- Better budget control
- Minimized production disruptions
Organizations can schedule planned maintenance during off-peak times to limit its impact on operations.
Defining Unplanned Maintenance
Unplanned maintenance refers to repairs or fixes performed after equipment breaks down unexpectedly. It’s a reactive approach to address sudden failures.
Types of unplanned maintenance:
- Reactive maintenance: Fixing equipment after it fails
- Emergency maintenance: Urgent repairs to prevent safety issues or major losses
- Corrective maintenance: Addressing problems found during inspections
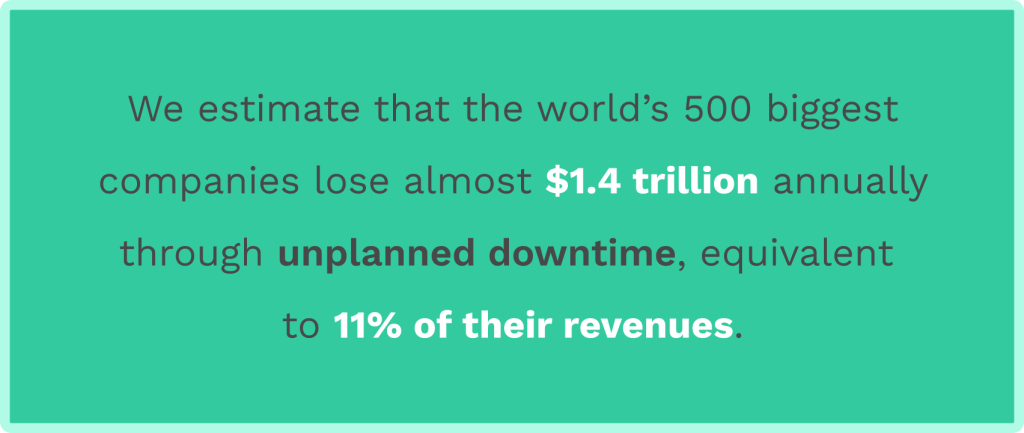
Unplanned maintenance often leads to:
- Production delays
- Higher repair costs
- Increased safety risks
- Shorter equipment lifespan
While sometimes unavoidable, excessive unplanned maintenance can indicate poor maintenance practices.
Planned vs. Unplanned Maintenance: Key Differences
The main differences between planned and unplanned maintenance lie in timing, approach, and outcomes.
Timing:
- Planned: Scheduled in advance
- Unplanned: Occurs unexpectedly
Approach:
- Planned: Proactive, preventive
- Unplanned: Reactive, corrective
Cost:
- Planned: Generally lower, more predictable
- Unplanned: Often higher, unpredictable
Downtime:
- Planned: Shorter, controlled
- Unplanned: Longer, disruptive
Resource allocation:
- Planned: Efficient use of staff and parts
- Unplanned: May require emergency resources
Effective maintenance strategies often combine both approaches, focusing on increasing planned maintenance to reduce unplanned events.
Assessing the Impact of Maintenance Types
Maintenance types have far-reaching effects on business operations. They influence productivity, costs, efficiency, and asset longevity differently.
Impact on Productivity
Unplanned maintenance often leads to sudden equipment breakdowns, which cause unexpected downtime and production losses. Workers may sit idle while repairs are made.
Planned maintenance, on the other hand, can be scheduled during off-hours, minimizing disruptions to normal operations. This type of maintenance is cost-effective and reduces problems in the long run.
It allows for better resource allocation and smoother workflows.
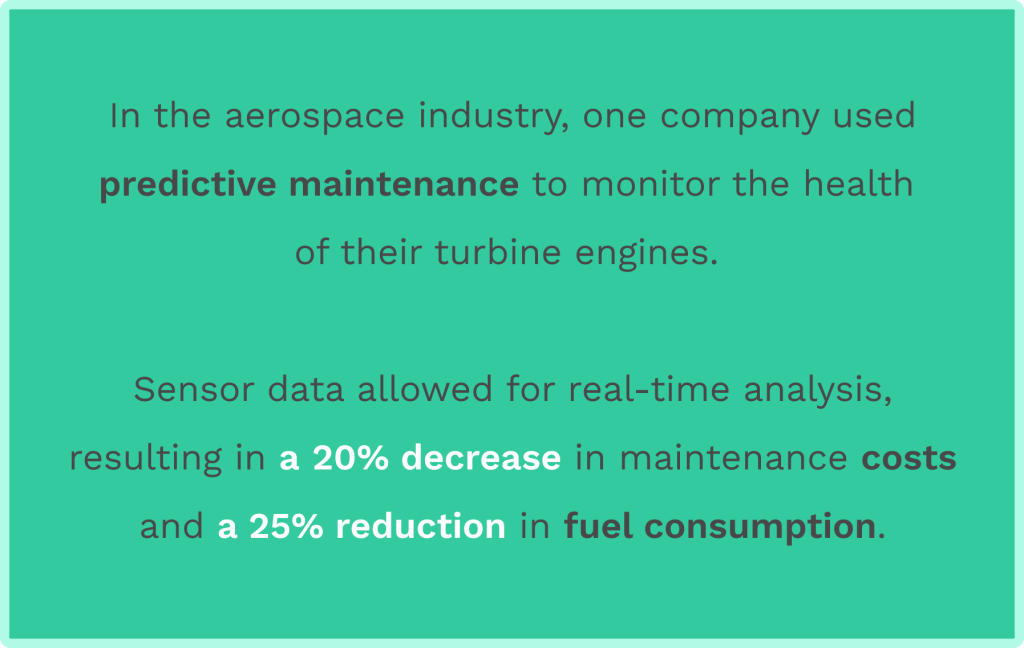
Regular upkeep prevents major failures, resulting in more consistent production output. Employees can focus on their core tasks instead of dealing with frequent breakdowns.
Impact on Maintenance Costs
Unplanned maintenance typically costs more than planned maintenance. Emergency repairs often require rush orders for parts, and technicians may need overtime pay.
Planned maintenance allows for bulk purchasing of supplies, saving you money on parts.
Also labor costs are lower as work is done during regular hours.
Preventive measures catch small issues before they become big problems, reducing the need for costly major repairs or replacements.
Impact on Efficiency and Operational Efficiency
Unscheduled maintenance disrupts normal processes. It can cause a ripple effect of delays throughout operations. This leads to decreased overall efficiency.
Planned maintenance improves operational efficiency, allows for better coordination between maintenance and production teams, and allows for more effective resource allocation.
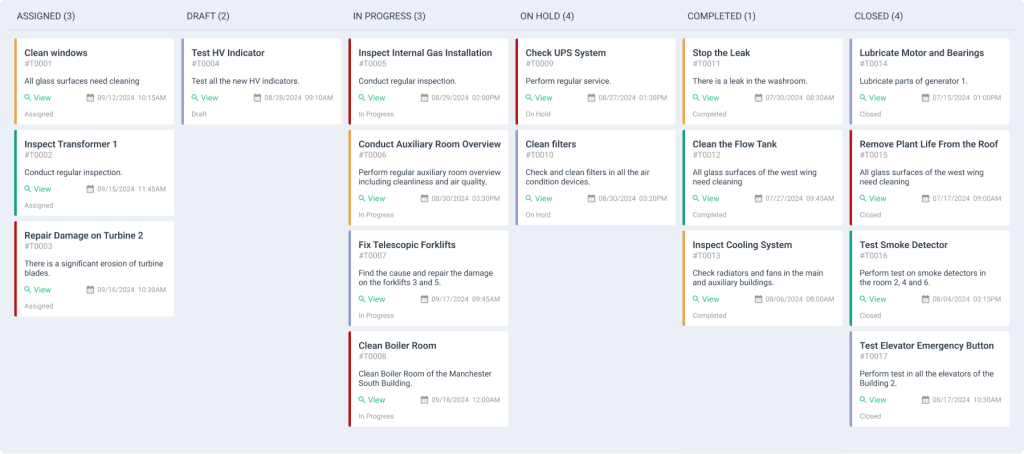
Regular upkeep ensures equipment runs at optimal levels. This leads to improved energy efficiency and reduced waste. Tracking planned vs. unplanned maintenance helps identify areas for process improvement.
Impact on Asset Life
Reactive maintenance often shortens asset lifespans. Equipment forced to run until failure suffers more wear and tear, which can lead to premature replacement.
Planned maintenance extends asset life. Regular inspections catch issues early. Timely repairs and part replacements prevent major breakdowns.
Proper upkeep ensures equipment operates within design parameters. This reduces stress on components and prolongs useful life. Well-maintained assets often retain higher resale value.
Executing Maintenance Tasks
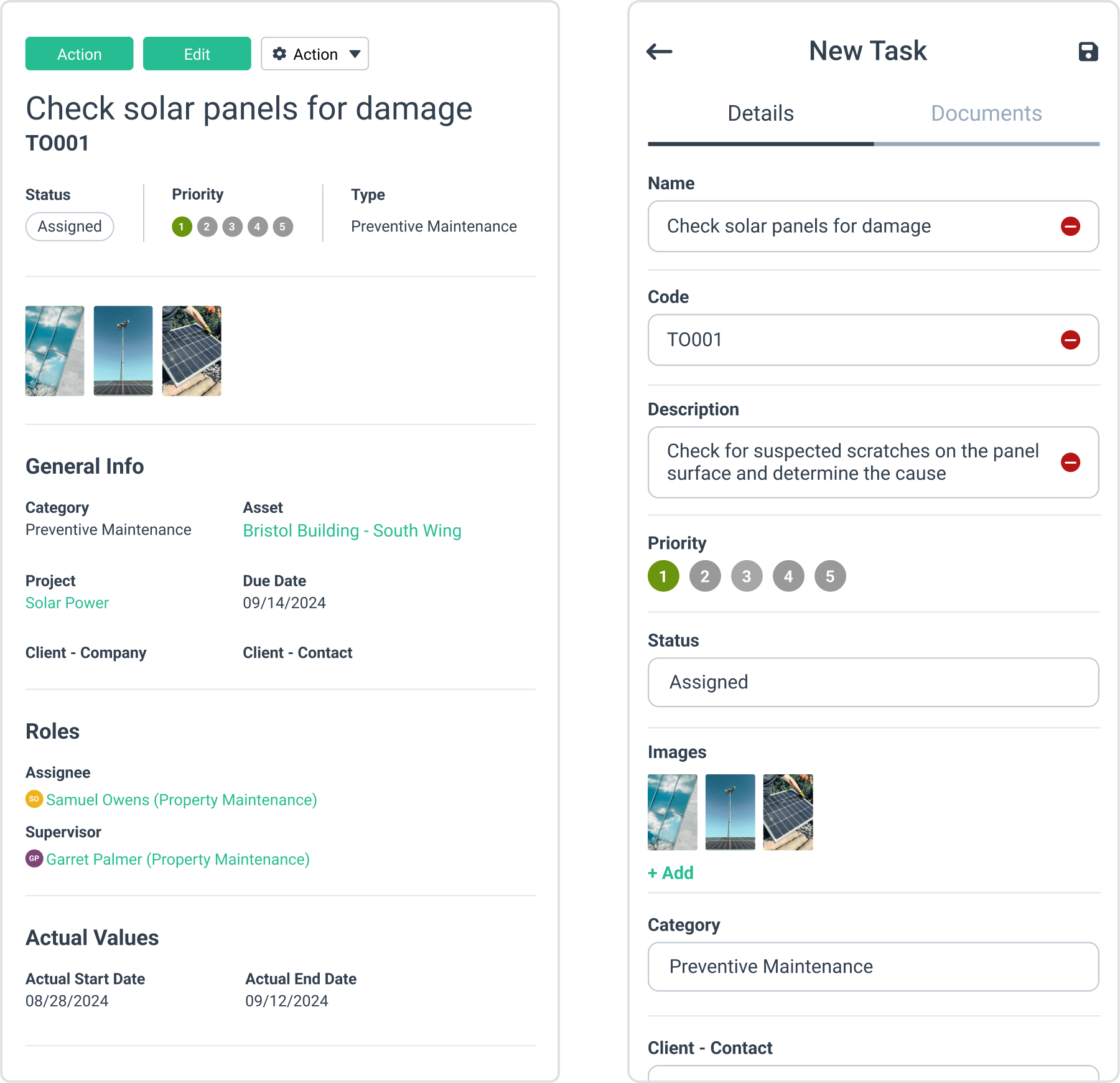
Maintenance tasks vary in their timing, approach, and goals. Some are planned, while others happen in response to sudden issues.
Different types of maintenance serve unique purposes in keeping equipment running smoothly.
Conducting Preventive Maintenance
Planned preventive maintenance involves regular, scheduled checks and upkeep. Technicians inspect equipment, replace worn parts, and perform tune-ups, helping to prevent breakdowns before they occur.
Common preventive tasks include:
- Lubricating moving parts
- Tightening loose components
- Cleaning filters and sensors
- Updating software
Teams often use checklists to ensure they complete all necessary steps. Depending on equipment needs, they may schedule these tasks daily, weekly, or monthly.
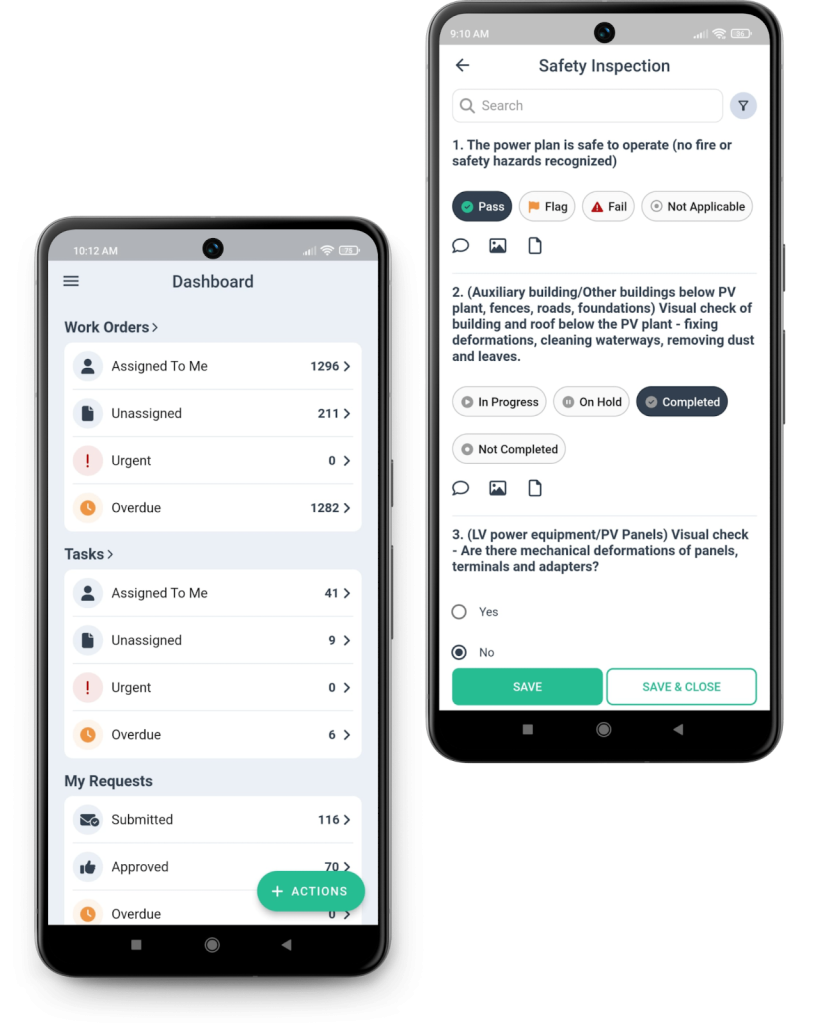
Preventive maintenance reduces unexpected downtime and extends machine life. It allows companies to plan for maintenance costs and staff time. This approach is key for keeping production lines running smoothly.
Responding to Unplanned Failures
Unplanned maintenance occurs when equipment suddenly breaks down. Teams must act fast to fix the issue and restart production.
Steps in addressing unplanned failures:
- Assess the problem
- Gather needed tools and parts
- Make repairs quickly
- Test the fix
- Return equipment to service
These events often lead to costly downtime. They may require overtime work or rush-ordered parts. Unplanned repairs can also cause safety risks if not handled properly.
To minimize unplanned failures, companies aim to shift more maintenance to preventive methods. They track failure patterns to predict and prevent future breakdowns.
Incorporating Corrective and Prescriptive Maintenance
Corrective maintenance fixes issues found during inspections or regular use.
It addresses problems before they cause major failures. This might include adjusting settings or replacing minor parts.pers
Prescriptive maintenance uses data to suggest the best fix for a problem. It relies on sensors and AI to analyze equipment performance. This method helps teams make smart choices about repairs.
Both approaches aim to reduce downtime and extend equipment life. They bridge the gap between preventive work and unplanned repairs.
These methods allow companies to catch issues early and better plan for future maintenance needs.
Special Considerations
Maintenance strategies vary across industries and situations. External factors and human elements play key roles in shaping practical approaches.
Maintenance in Different Industries
Planned maintenance is critical for manufacturing, where equipment downtime can be costly. Regular checks on production lines help prevent unexpected breakdowns.
In healthcare, strict schedules ensure medical devices are always ready for use. Hospitals often use a mix of planned and reactive maintenance for critical equipment.
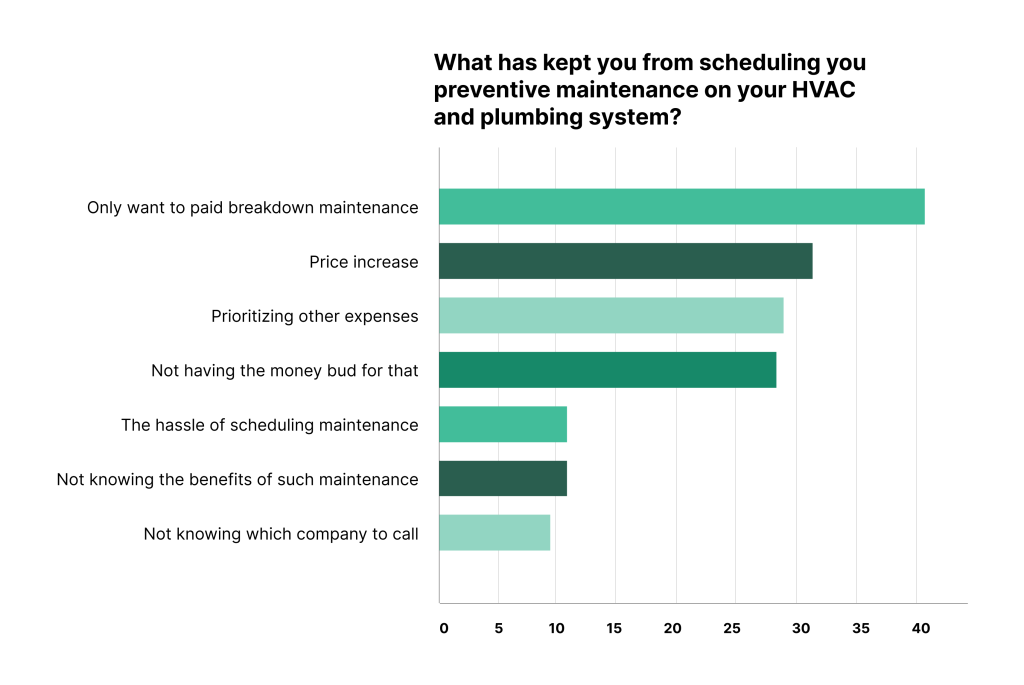
HVAC systems in commercial buildings need routine care to maintain air quality and energy efficiency. Facility managers typically follow set maintenance schedules for these systems.
Considering Human Error in Maintenance
Human errors can lead to unplanned maintenance needs. Proper training reduces mistakes in equipment operation and repair.
Clear procedures and checklists help technicians avoid oversights. Regular audits can spot common errors and guide improvements.
Some companies use digital tools to guide maintenance tasks, lowering the risk of human error. These systems can prompt specific steps and record actions taken.
Evaluating External Factors Affecting Maintenance
Weather conditions impact outdoor equipment maintenance schedules. Harsh environments may require more frequent checks and repairs.
Supply chain issues can affect spare parts availability, forcing changes to maintenance plans. Having a network of suppliers helps manage this risk.
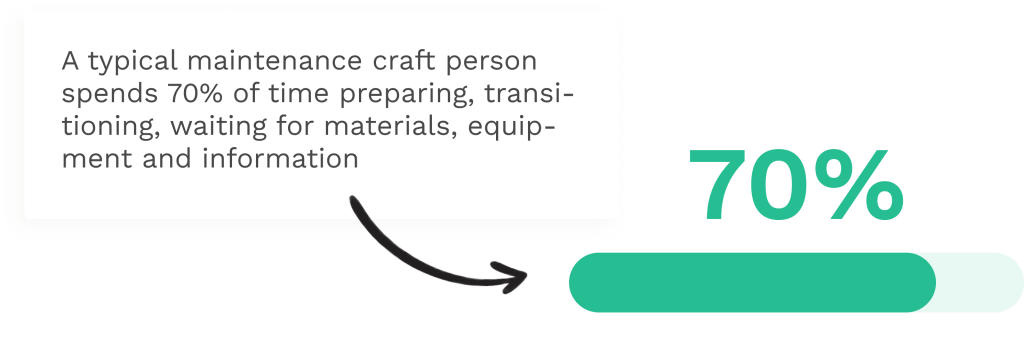
Regulatory changes may demand updates to maintenance practices. Industries like aviation must adapt quickly to new safety rules.
Economic factors influence maintenance budgets. Companies often adjust their maintenance percentage based on financial conditions.
Comparative Analysis in Various Settings
A study of 100 factories compared planned vs. unplanned maintenance approaches:
- Planned maintenance reduced downtime by 30-50%
- Unplanned repairs cost 3-5 times more on average
- Facilities using planned strategies saw 15-25% higher equipment lifespan
In the transportation sector, airlines with robust inspection schedules had 40% fewer flight delays than those relying on breakdown maintenance.
Retail chains that implemented planned maintenance for refrigeration units saw a 25% drop in food spoilage costs compared to stores using reactive approaches.
Summary
In conclusion, balancing planned and unplanned maintenance is essential for efficient and cost-effective operations.
With its proactive approach, planned maintenance minimizes unexpected failures, reduces costs, and extends equipment lifespan. It allows businesses to optimize resource allocation, schedule repairs during off-hours, and maintain smooth workflows.
Conversely, unplanned maintenance, while sometimes unavoidable, can disrupt productivity and lead to higher expenses. Companies should strive to prioritize planned strategies while incorporating flexibility for unforeseen events.
By leveraging preventive and predictive maintenance techniques, organizations can reduce downtime, enhance operational efficiency, and ensure the longevity of their assets. A thoughtful maintenance strategy is key to long-term success.