Get a Free WorkTrek Demo
Let's show you how WorkTrek can help you optimize your maintenance operation.
Try for freeKeeping equipment running smoothly is key for any business. Proactive maintenance helps catch problems before they happen, saving money and time in the long run. This guide to proactive maintenance will answer that question.
Proactive maintenance involves regular checks and fixes to prevent breakdowns. It’s different from fixing things only when they break. Many companies now use this method to keep their machines working well.
This guide will explain how to start a proactive maintenance plan. We’ll cover the steps, tools, and tips you need.
By the end, you’ll be ready to improve your maintenance approach.
Key Takeaways
- Regular checks and fixes prevent costly breakdowns
- Proactive maintenance saves time and money for businesses
- Tools and planning are needed for successful proactive maintenance
Understanding Proactive Maintenance
Proactive maintenance efforts aim to prevent equipment failures before they occur. It involves regular inspections, repairs, and replacements to keep machines running smoothly.
This approach differs from reactive maintenance, which only fixes problems after breakdowns happen. Proactive maintenance helps reduce costs by preventing unexpected failures, minimizing downtime, and improving operational efficiency.
There are several types of proactive maintenance:
The most common type is implementing preventive maintenance strategies.
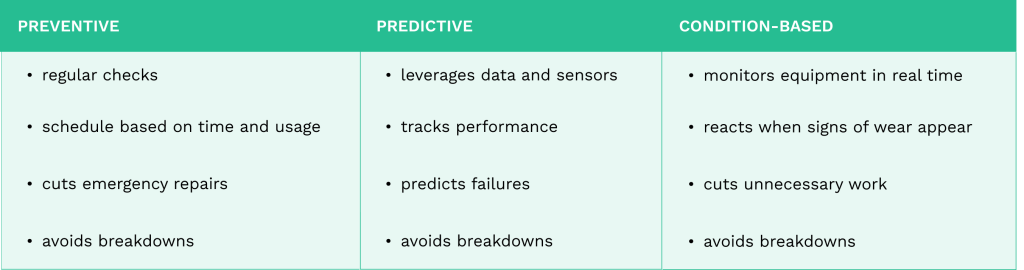
It involves scheduled upkeep based on time or usage, such as changing the oil every 5,000 miles or inspecting a machine monthly. The goal is to reduce costly emergency repairs for the most critical assets.
Predictive maintenance, also called smart maintenance, uses data and sensors to forecast when issues might arise.
This allows teams to fix problems just before they cause failures.
Condition-based maintenance monitors equipment in real time. It triggers repairs when specific indicators show potential issues.
Implementing proactive maintenance requires planning and resources. Organizations need to:
- Identify critical equipment
- Create maintenance schedules
- Train staff on procedures
- Use proper tools and software
Proactive maintenance practices can extend equipment life and improve reliability by focusing on prevention.
It helps businesses avoid costly breakdowns, improve maintenance practices, reduce maintenance costs, and maintain consistent operations.
Benefits of Proactive Maintenance
Proactive maintenance offers many advantages for facilities and equipment. It helps prevent unexpected breakdowns and extends the life of assets.
Reduced Downtime
One key benefit of a proactive maintenance plan is reduced downtime. Fixing small issues early can avoid major failures that stop operations.
Cost Savings
Another plus is cost savings. While upfront costs may be higher, proactive maintenance saves money in the long term. It cuts emergency repair expenses and replacement costs.
Improved Safety
Improved safety is a crucial advantage. Well-maintained equipment is less likely to malfunction in ways that could harm workers.
Energy Efficiency
Energy efficiency often increases with proactive upkeep. Properly maintained systems use less power and run more smoothly.
Improve Asset Lifespan
Asset lifespan gets a boost, too. Regular care and timely repairs help equipment last longer before needing replacement.
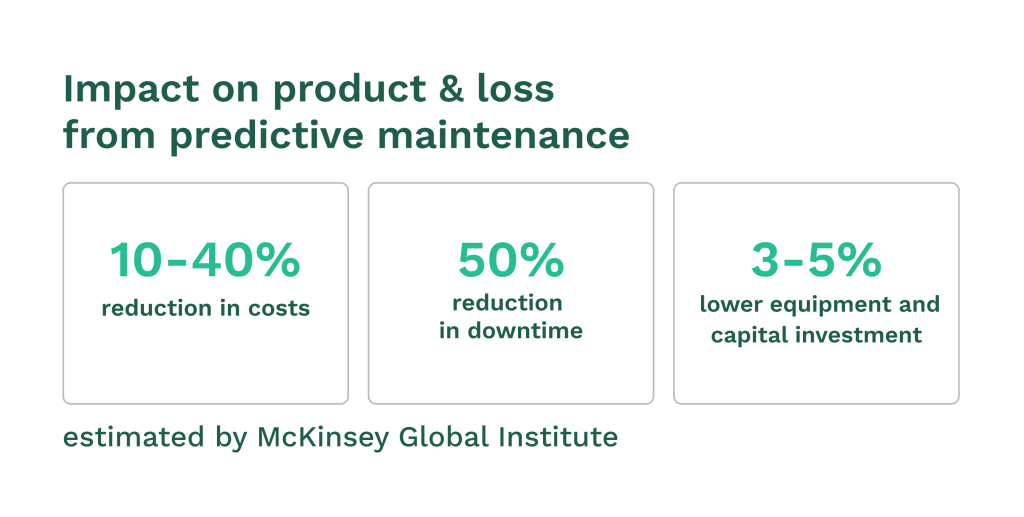
Improve Planning
Proactive approaches also enhance planning. Maintenance can be scheduled at convenient times, minimizing disruptions to normal operations.
Tracking Maintenance Data
Better data collection is an added perk. Tracking maintenance activities provides insights for future improvements and budgeting.
Improved Equipment Reliability
Lastly, proactive maintenance improves product quality. Well-maintained equipment is more likely to produce consistent, high-quality outputs.
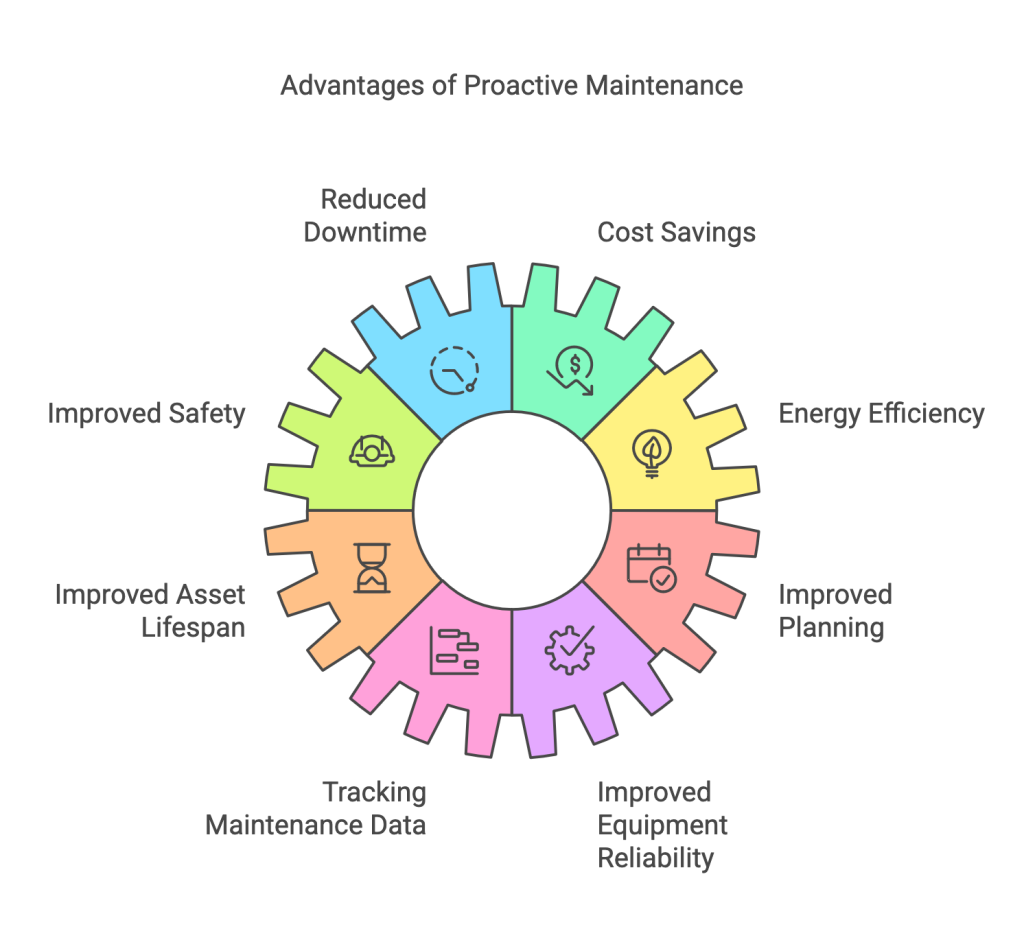
Key Elements of Proactive Maintenance
Proactive maintenance focuses on preventing equipment failures before they occur. It uses data analysis, scheduling, and monitoring to keep systems running smoothly.
Predictive Maintenance Techniques
Predictive maintenance uses data to forecast when equipment might fail. It relies on sensors and advanced analytics to track machine health.
Key predictive techniques include:
- Vibration analysis
- Oil analysis
- Thermography
- Acoustic monitoring
These methods help spot issues early. For example, vibration analysis can detect loose parts or misalignments, and oil analysis reveals contaminants that could damage engines.
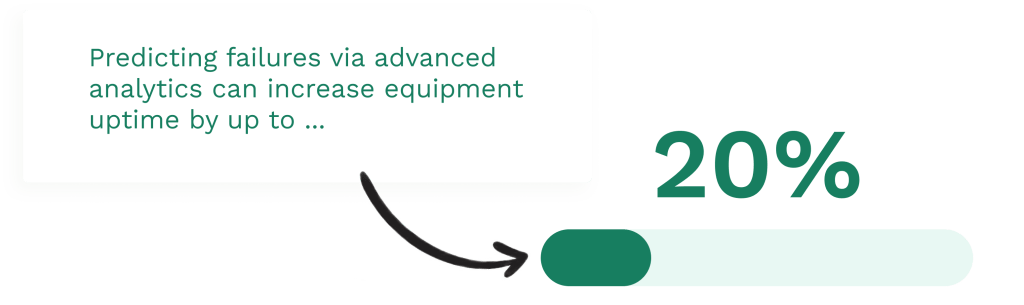
Predictive maintenance reduces unplanned downtime and cuts costs by avoiding unnecessary repairs. Companies can plan maintenance at the best times, causing less disruption.
Preventative Maintenance Scheduling
Preventative maintenance follows a set schedule. It aims to keep equipment in good shape through regular upkeep.
Common preventative tasks include:
- Cleaning and lubricating parts
- Replacing worn components
- Calibrating instruments
- Checking safety systems
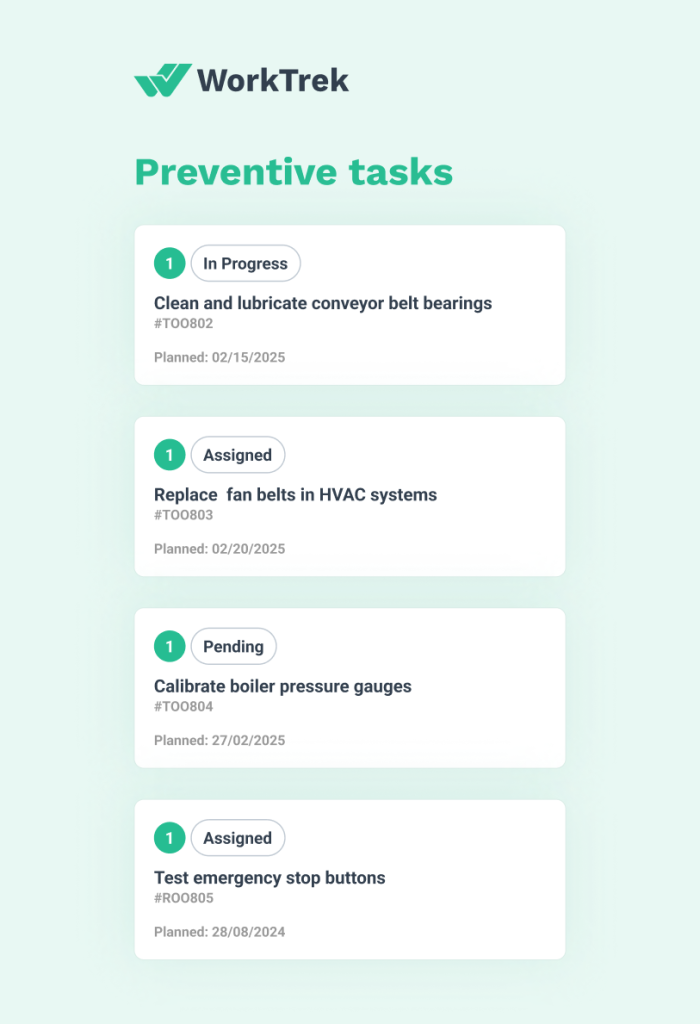
Effective scheduling balances maintenance needs with production demands. It often uses manufacturer guidelines and past performance data.
Digital tools help manage complex maintenance schedules. They can track multiple assets and send alerts when service is due.
Condition Monitoring
Condition monitoring tracks equipment performance in real-time. It uses sensors to measure temperature, pressure, and vibration.
Key benefits of condition monitoring include:
- Early detection of problems
- Improved safety
- Better energy efficiency
- Extended equipment life
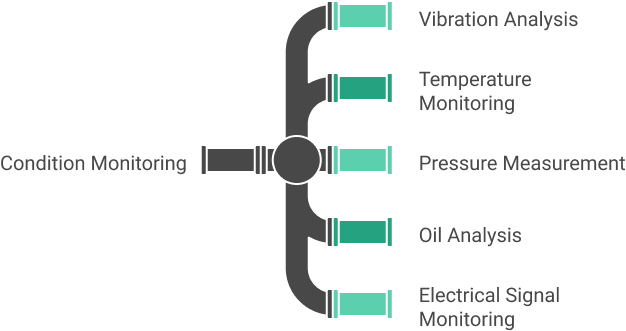
Modern systems collect data using the Internet of Things (IoT), allowing remote monitoring and quick response to issues.
Condition monitoring helps fine-tune maintenance plans. It shows which parts need attention and when leading to more efficient resource use and less waste.
Implementing Proactive Maintenance
Putting a proactive maintenance plan into action takes careful planning and execution. It involves creating a solid strategy, training staff, choosing the right tools, and using data to make smart choices.
Establishing a Maintenance Plan
A good maintenance plan is key to being proactive. Start by making a list of all equipment and assets. Give each item a priority based on its importance to your operations. Set up a schedule for regular checks and upkeep.
Use preventive maintenance strategies to stop problems before they start. This can include things like:
- Cleaning and lubricating machines
- Replacing worn parts
- Checking for signs of wear
Make sure to keep detailed records of all maintenance tasks. This will help track patterns and spot recurring issues.
Training Maintenance Personnel
Well-trained staff are crucial for proactive maintenance. Teach your team about the equipment they’ll be working on and show them how to spot early signs of trouble.
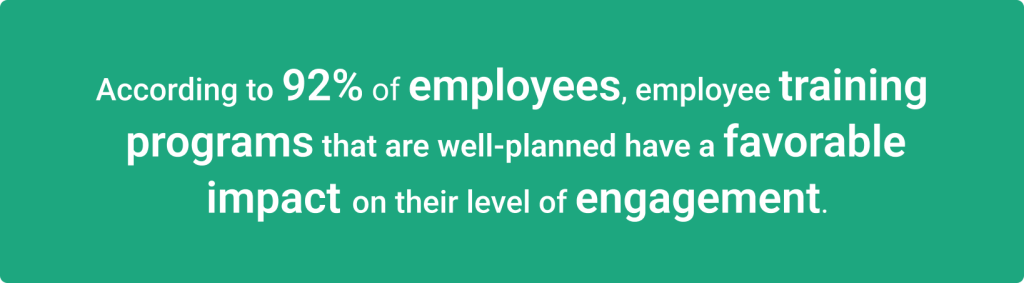
Give hands-on training for maintenance tasks. This helps staff feel more confident in their work. Set up regular refresher courses to keep skills sharp.
Encourage a culture of proactive thinking. Reward staff who find and fix issues early. This helps everyone stay focused on preventing problems, not just fixing them.
Selecting the Right Tools and Technology
The right tools can make proactive maintenance much easier. Invest in a computerized maintenance management system (CMMS) like WorkTrek. This software helps track maintenance tasks, schedules, and equipment history.
Consider using sensors and IoT devices to monitor equipment health. These can give early warnings of potential issues. Some helpful tools include:
- Vibration sensors
- Temperature monitors
- Oil analysis equipment
Choose tools that fit your specific needs and budget and improve maintenance performance. Make sure they can work together and share data easily.
Data Analysis and Decision-Making
Collecting historical maintenance data is just the first step. The real value comes from analyzing it and making smart choices. Look for patterns in equipment performance and failure rates.
Use this info to adjust your maintenance schedule and improve operational efficiency. You might find some machines need more frequent checks, while others can go longer between services.
Set up alerts for when data shows potential problems. This lets you act fast to prevent breakdowns. Over time, you’ll build a predictive maintenance model that can spot issues before they happen.
Keep improving your process. Review your data regularly and adjust your plan as needed. This will help make your proactive maintenance even more effective over time.
Proactive Maintenance Strategies
Proactive maintenance aims to prevent equipment failures before they occur. It uses data, analysis, and systematic approaches to optimize asset performance and reliability.
Risk-Based Maintenance
Risk-based maintenance prioritizes maintenance tasks based on the potential impact of equipment failure. This strategy focuses resources on critical assets that pose the highest risk to operations, safety, or the environment.
Key elements of risk-based maintenance include:
- Asset risk assessment
- Failure mode analysis
- Probability and consequence evaluation
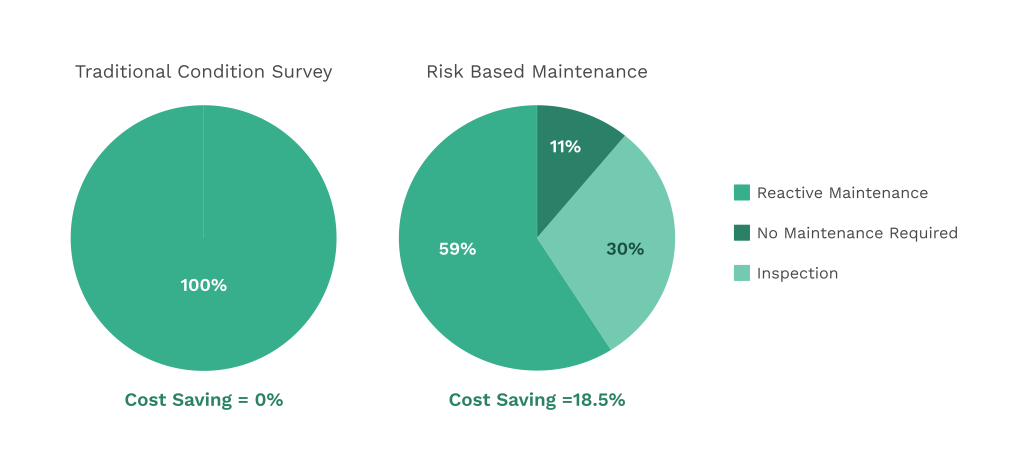
Organizations use risk matrices to categorize assets and determine appropriate maintenance intervals. High-risk equipment receives more frequent inspections and preventive work.
This approach helps companies:
- Reduce downtime of critical systems
- Optimize maintenance budgets
- Improve safety and regulatory compliance
Implementing risk-based maintenance requires thorough asset knowledge and ongoing risk evaluations.
Reliability-Centered Maintenance
Reliability-centered maintenance (RCM) is a systematic method for identifying each asset’s most effective maintenance tasks. It aims to preserve system functions while minimizing costs.
RCM involves:
- Defining system functions
- Identifying potential failures
- Analyzing failure modes and effects
- Selecting optimal maintenance tasks
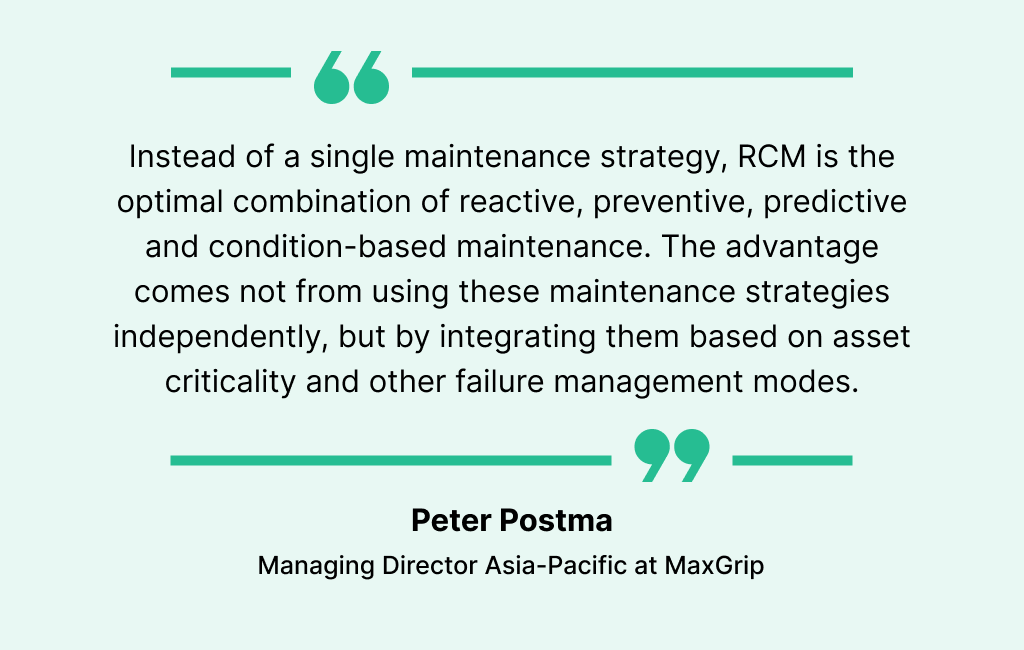
This strategy helps determine whether preventive, predictive, or run-to-failure approaches suit each asset. RCM considers factors like:
- Equipment criticality
- Failure patterns
- Maintenance costs
- Operational impact
By applying RCM, organizations can extend asset lifespans and reduce unnecessary maintenance work.
Total Productive Maintenance
Total Productive Maintenance (TPM) is a holistic approach that involves all employees in maintaining equipment. It aims to eliminate breakdowns, defects, and accidents.
TPM principles include:
- Autonomous maintenance by operators
- Planned maintenance schedules
- Quality maintenance to prevent defects
- Early equipment management
- Continuous improvement initiatives
This strategy empowers front-line workers to perform basic maintenance tasks, freeing up specialists for more complex work. TPM fosters a culture of shared responsibility for equipment reliability.
Benefits of TPM:
- Improved equipment effectiveness
- Reduced maintenance costs
- Enhanced product quality
- Increased employee engagement
Implementing TPM requires strong leadership support and employee training programs.
Computerized Maintenance Management Systems
Computerized Maintenance Management Systems (CMMS) like WorkTrek are software tools that help organize and streamline maintenance operations. They are important in proactive maintenance strategies.
Key CMMS features:
- Work order management
- Asset tracking and history
- Inventory control
- Preventive maintenance scheduling
- Data analysis and reporting
CMMS software enables maintenance teams to:
- Plan and schedule work efficiently
- Track equipment performance trends
- Generate detailed maintenance reports
- Manage spare parts inventory
CMMS tools centralize maintenance data and support data-driven decision-making. They help identify recurring issues, optimize maintenance intervals, and improve asset reliability.
Maintenance Metrics and Performance Indicators
Tracking the right metrics helps companies improve their maintenance processes. These indicators measure efficiency, costs, and the impact of maintenance activities on overall operations.
Key Performance Indicators (KPIs)
Maintenance KPIs are crucial for measuring success. Common KPIs include:
- Mean Time Between Failures (MTBF)
- Mean Time To Repair (MTTR)
- Overall Equipment Effectiveness (OEE)
- Planned Maintenance Percentage (PMP)
MTBF shows how long equipment runs between breakdowns. A higher MTBF means better reliability. MTTR measures repair speed. Lower MTTR indicates faster repairs.
OEE combines availability, performance, and quality to gauge equipment productivity. PMP tracks the percentage of planned vs. unplanned maintenance work.
These KPIs help teams spot trends, set goals, and make data-driven decisions. Regular tracking allows for quick adjustments to improve maintenance strategies.
Return on Investment (ROI) in Maintenance
ROI measures the financial benefits of maintenance activities. It compares maintenance costs to the savings or increased production it generates.
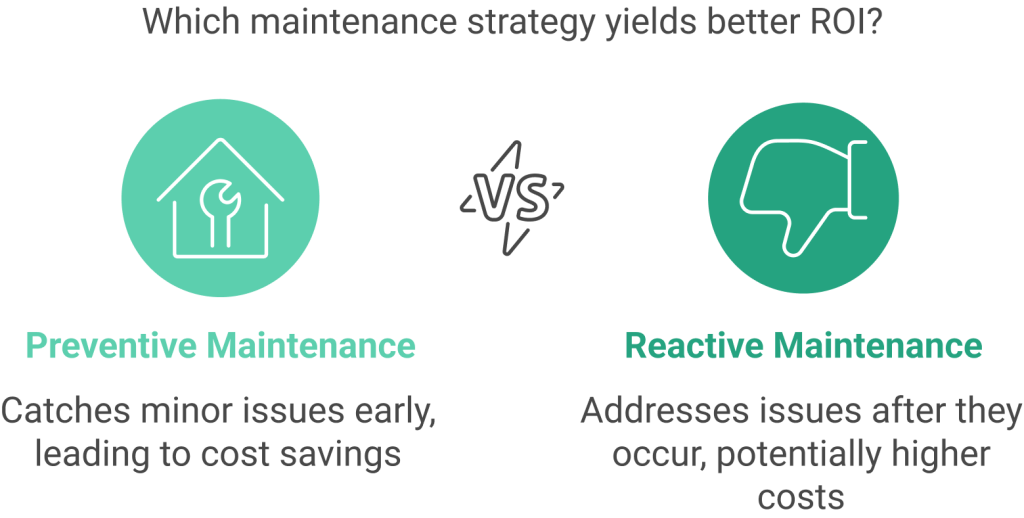
To calculate maintenance ROI:
- Add up all maintenance costs (labor, parts, tools)
- Estimate savings from reduced downtime and extended equipment life
- Divide savings by costs and multiply by 100 for percentage
For example, if $50,000 in maintenance costs leads to $150,000 in savings:
ROI = ($150,000 / $50,000) x 100 = 300%
This shows a strong return on the maintenance investment. Tracking ROI helps justify maintenance budgets and proves the value of proactive strategies.
Maintenance Costs and Savings
Maintenance costs include:
- Labor costs (wages, training)
- Parts and materials
- Tools and equipment
- Contractor fees
Savings come from:
- Reduced downtime
- Longer equipment life
- Lower energy costs
- Fewer emergency repairs
- Improved asset management
Tracking these numbers helps balance spending and savings. Finding the right mix of preventive and reactive maintenance is key.
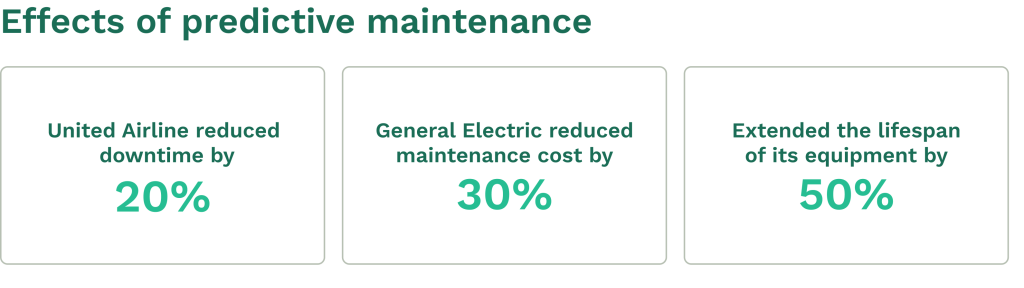
Companies can use cost per production unit to compare maintenance spending across different areas. This metric shows which equipment or processes need more attention.
Regular cost analysis helps teams find ways to cut waste and improve efficiency. It also supports better budget planning for future maintenance needs.
Challenges and Considerations in Proactive Maintenance
Proactive maintenance brings many benefits but also presents unique hurdles. When implementing this approach, companies must carefully weigh resource needs, costs, cultural shifts, and operational impacts.
Resource Allocation
Implementing proactive maintenance strategies requires careful resource planning. Companies need to invest in skilled personnel and advanced tools. This often means hiring specialists or training existing staff.
New technologies like sensors and data analysis software are essential. But they come with a learning curve. Maintenance teams need time to master these tools.
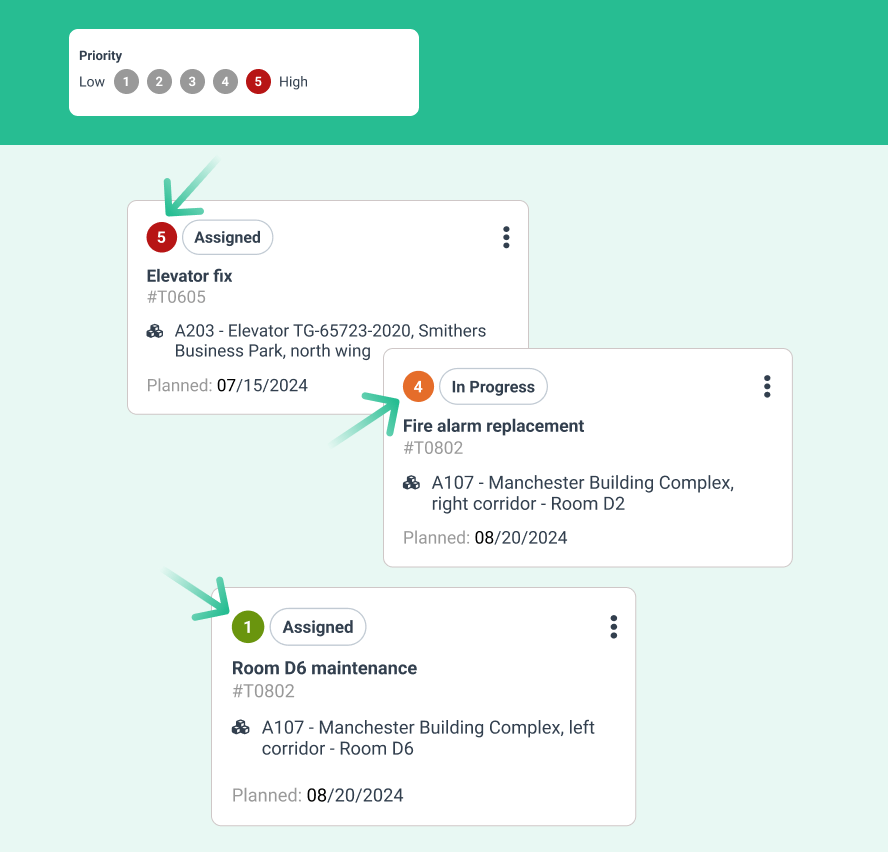
Managers must balance maintenance tasks with other priorities. This can be tricky when resources are limited. Proper scheduling and task prioritization become crucial.
Upfront Costs versus Long-Term Savings
Proactive maintenance demands significant upfront investment. Companies need to purchase monitoring equipment, software, and training programs. These costs can be substantial.
The promise of future savings is appealing. Reduced breakdowns and extended equipment life offer long-term benefits. But, it can take time to see a return on investment.
Budget-conscious organizations may struggle with initial expenses. Decision-makers need to weigh short-term costs against potential long-term gains. This requires detailed financial analysis and forecasting.
Cultural and Organizational Changes
Shifting to proactive maintenance often requires a cultural transformation. Traditional reactive approaches are deeply ingrained in many organizations, and changing this mindset can be challenging.
Employees may resist new procedures and technologies. They might see proactive measures as unnecessary or disruptive. Clear communication and training are essential to overcome these barriers.
Leadership must champion the change. They must explain the benefits and set clear expectations, which helps create buy-in across all levels of the organization.
Balancing Maintenance and Production
Finding the right balance between maintenance activities and production needs is crucial. Excessive maintenance can disrupt operations and reduce output, while too little maintenance risks equipment failure and costly downtime.
Scheduling becomes complex. Maintenance teams must work around production schedules, which requires close coordination between departments.
Predictive technologies can help optimize this balance. They allow for more precise timing of maintenance activities. However, implementing these systems takes time and expertise.
Managers must constantly evaluate the impact of maintenance on production goals and adjust strategies as needed to maintain efficiency.
Case Studies
Proactive maintenance has transformed operations across various sectors. Real-world examples show its impact on efficiency, cost savings, and equipment reliability.
According to a recent McKinsey & Company study, organizations implementing proactive maintenance report up to a 28% reduction in maintenance costs.
Conclusion and Best Practices
Proactive maintenance is a key strategy for keeping facilities and equipment running smoothly. It helps prevent unexpected breakdowns and extends asset lifespans.
To implement effective proactive maintenance:
- Create a detailed maintenance schedule
- Train staff on proper maintenance procedures
- Use condition monitoring tools
- Keep accurate maintenance records
Regular inspections are crucial. Check equipment frequently for signs of wear or damage and address small issues before they become big problems.
Prioritize critical assets. Focus proactive efforts on equipment essential for operations or expensive to replace.
Leverage technology. CMMS software can help track maintenance tasks, schedule work orders, and analyze data.
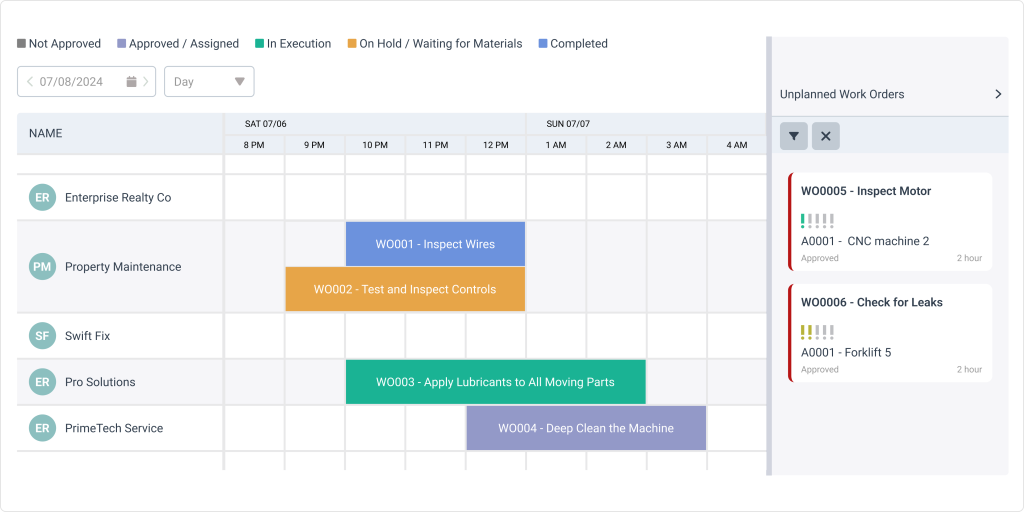
Continuously improve processes. Review maintenance data regularly to identify trends and refine procedures.
Involve equipment operators. They often notice early warning signs of issues. Encourage them to report concerns promptly.
Stay up-to-date on best practices. Maintenance techniques evolve, so ongoing learning is important.
With a robust, proactive maintenance program, facilities can boost reliability, cut costs, and improve overall performance.