Search results for: task
Category
Announcements
CMMS
Compliance & Control
Enterprise Asset Management
Facility Management
Fleet
Operations & Maintenance
Product Updates
Uncategorized
CMMS
Essential Tasks To Track In Your CMMS
Computer Maintenance Management System (CMMS) is specialized maintenance management software that performs a series of advanced functions and essential tasks, including operations and maintenance activity tracking and other management features. The CMMS makes it easier for maintenance departments to keep a database of the equipment for which they are responsible, by planning, monitoring, and logging […]
Make your work easier.
Try for free.
Book a demo
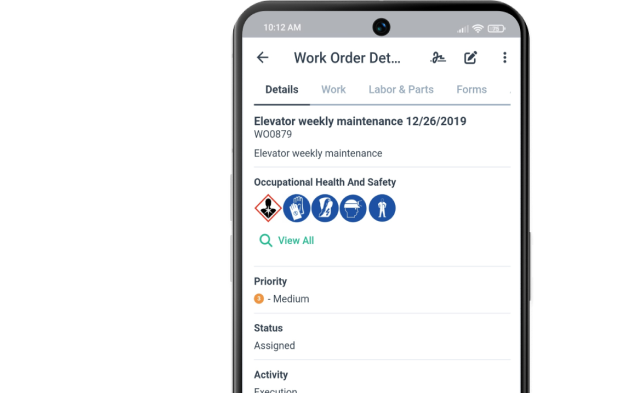